1189
How to make a wood chipper with your hands
Each owner of your own plot, be it a country house or a small cottage with a vegetable garden knows that to maintain order is sometimes very difficult. The problem of waste disposal to the private sector is particularly acute, and if organic can be stored in a compost pit and plastic bottles to landfill, what with the abundance of woody litter? After opilki fruit trees or building is a lot of unnecessary branches, boards and lumber. Leave them on the wood and burn very long and troublesome. Specifically for such cases they invented the wood chipper. The new device is quite expensive, but fortunately, to make the wood chipper with your hands is not so difficult as it might seem at first glance.
The purpose and principle of operation
The wood chipper will be indispensable for any vacationer. With him no longer need to light fires to burn sawn-off tree branches or to think, what to do with waste after harvesting, stems, tops, roots, etc. of Any organic solid waste machine processed into chips and swarf, which subsequently will serve as an excellent material for high quality compost or solid fuel boilers. So, in one fell swoop, you solve several problems: waste disposal, saving space and time, you will get an endless source of material for fertilizers and fuel for the winter.
Anyway, the wood chipper is very useful on the farm, but factory mechanisms are prohibitively expensive, so we offer to save money and do it yourself. Most encouraging, there is no need to "reinvent the wheel" — it is necessary only correctly replicate the design of the factory of the device using available parts.
But before you start, you first need to thoroughly study and understand the principle of operation of the machine. Otherwise you will not be able to make a correct drawing and to make it a reality. The device of the chopper just to ugliness is the engine shaft with the cutting elements, frame, protective shell and the receiving compartment through which the material falls inside. Because this unit will get quite heavy, it is better to set on two-wheeled base to easily move around the site.
The principle of operation of the apparatus is as follows: the motor rotates and drives the shaft by means of chain or belt. When you put branches or stalks of plants into the receiving box, the cutting elements are severed into smaller pieces that go on the other side of the device. Very similar to an ordinary kitchen grinder.
Device isolitaire how to choose a pattern and purchase the components of the future, unless it is necessary to define its purpose, that is, what exactly (or more often) it will shred thick branches of fruit trees, small Board, or the remains of plants after harvest. Depends on the output device, type of his work and, consequently, the cost of the necessary details.
The engine of the chipperFor garden shredders you can use gasoline or electric engines. Each of them has its own peculiarities of use. For example, a gasoline engine can process large thick branches, also it is valued for its mobility. Machine with electric motor, on the contrary, must always be near a power source, but it takes up much less space than gasoline. It is easy and convenient to use, but will not handle very large objects due to low power.
What should pay attention when choosing the engine for garden shredder:
The knives of the chopperthe Second important part of the chopper – cutting elements or knives. Their design depends on the type and operation of the mechanism, and also the amount of recycled material. So, a simple disc with blades will grind into dust only fragile branches, combination designs can shred thick branches and give the same small chips, there are those that pulverized wood chips with a length of 2-10 cm If you are planning to use recycled material for solid fuel boilers, it is better to choose the latter option.
Since our aim is to copy one of the factory models of chopper, consider the knives used for their production:
Disc knife – is intended for processing of small branches up to a thickness of 2 cm, stems of plants and herbs.
Milling system – knives, arranged in a similar way, you can chop a branch with a thickness of about 8 cm. the Only mandatory condition is that the lumber must be dry. Otherwise, lumps of bark and wet wood chips will clog the cutter and the mechanism will stop working.
Milling turbine knife is one of the most common and convenient options. This design can shred any branches, regardless of the thickness and the degree of humidity.
Unfortunately, the models of knives to do on their own is almost impossible, therefore, to improvised devices were invented by their cutting elements: nouvo-disc design, set of saws, and duhvalova system with 8 knives.
Drawing of a grinderto make a grinder for wood, is not enough just to buy the parts, it is necessary to have a professional plumbing skills. The whole process takes place in three stages – the creation of a drawing, preparation of materials and assembling the device.
Since we are not going to invent anything new, the basis of the drawing can take any suitable model of the chopper, and the rest to add at your discretion. To create a drawing you can use a special computer program AutoCAD.
The main components of the mechanism we have described above, but this is only a General view. The most important thing you should pay attention to when creating the drawing – the location of the knives and their angle of cut. Consider the design of crusher with two shaft cutting element.
So, the shafts will be located between the plates and each shaft will have 3-4 knife. For attaching cutting elements to better use the bolts, shifting them with respect to the Central part of the shaft. The shaft rotates freely thanks to the 4 bearings that are fixed on the plates. The synchronicity of the movement of the shafts provide 2 gears, which drives the motor. To transmit torque, use a strap or chain to choose from. Depending on the dimensions of the blades and the diameter of the raw material you are going to grind, vary the interval between the shafts.
If you use the motor to 4 kW, its number of revolutions is 2500-2800 rpm Be a good indicator for disc mechanism, designed for fine twigs and plant stems. Two-shaft mechanism must be powerful, so the speed should be reduced.
The images below are drawings of the wood chipper with 2 shafts, each of which has 3 knives:
The disc model looks a lot easier mainly due to the simple design of the knives.
The drawing can display the disc diameter, number of blades and their location. The more blades, the finer will be raw output. The drive can be positioned vertically or at an angle.
The frame is attached to the stud with circular saws. Often, these devices use a belt to drive, so the shaft pin and two pulley.
Most of the materials needed to build a chopper, you can buy at the car store agricultural equipment or a hardware store, but some items need to order or make yourself. It needs to be able to work as a grinder and welder.
Twin-shaft shredderWork on creation of twin-shaft shredder consists of the following phases of Assembly of the frame and a receiving compartment, the creation of a chopping drum with knives, Assembly of the drum and the motor.
Materials needed:
The first step is to make the frame. To do this cut from a shaped tube 4 details: 2 – 40 cm, 2 – 80 cm. Welding machine clamp the short piece between the long right angle to make a frame. The distance between the two internal cross members shall be such that they could stand the grinding drum.
To later shredder can be moved, it is necessary to fit the wheels. On the frame lock 2 strut, which then will keep the axle and wheels.
Engine Assembly:
When the frame is ready, you can assemble a milling drum. To make the shaft, take a square billet for 4 knives or round, for 3. From a square piece file out the tips, making them round, so they went into the bearings. If you use the round billet, hone its Central part, making 3 flat slice of a knife.
Sami knives can be easily made of spring KAMAZ. Cut desired slice of the springs, align it if necessary, heating in the forge and repeatedly struck with a hammer. Will descalate detail and let cool. The knives make holes for the bolts. Sharpen the knives on the machine, by choosing the angle of the cutting edge of 35-45.
Attach the blades to the shaft and mark the fixing points. Drill holes in the intended locations and make them in the thread. To make the milling drum, take two plates – this will be wall. The welder cut holes in them for the bearings and abrade the edge. If you can not do this step yourself, you can go to the locksmith shop or the enterprise. Install inside the bearings.
Bolts attach the lining to the metal wall. Insert the shafts into the bearings and secure them. Connect the threaded metal wall studs and fix them with nuts. It only remains to make the receiving compartment through which the timber to get inside. To do this, take sheet metal and make 4 of the same workpiece in the form of a parallelepiped. Find the narrow side of each blank, back from her by 5 cm and fold the edge. Bend the remaining three blanks do in the opposite direction. Assemble the box and make sure that the workpiece tightly adjoin each other. Join the edges by welding or self-locking rivets. At the base on the curved sides of the drill locations for the mounting holes.
Install all the gathered design on the frame and secure it with the bolts. Put the engine and pull the drive element (chain or belt). In the last turn and install lock box. Close all internal parts with a protective cover to the rotating mechanisms has not got the chips and COP.
The Assembly of the wood chipper in the video below will help you to more fully represent, how is the whole process:
SUBSCRIBE to OUR youtube channel that allows you to watch online, download from YouTube free video about the recovery, the rejuvenation of man. Love for others and ourselves, as the feeling of high vibrations — an important factor for improvement .
Put LIKES and share with your FRIENDS!
www.youtube.com/channel/UCXd71u0w04qcwk32c8kY2BA/videos
Disc pulperIn contrast to twin-shaft, disc grinder requires far fewer parts, time and effort during Assembly.
Materials needed:
Progress:
Of stainless steel make the frame. Place the engine into the frame. On top of the engine install reflective shield out of sheet metal. The reflective shield cut a hole for the shaft.
The disc drill a hole for mounting on the shaft and a small slot for fixing the knives.
Assemble the disc with the knife and set it inside. Make a box out of sheet metal by the above instructions and install it on the chopper.
As you can see, nothing complicated, the main thing is to get all the necessary parts. Homemade wood chipper with two shafts has great power and is intended for processing of large branches. The size of the chip can be controlled from 2 cm to 8 cm depending on the number of knives on one shaft. published
Source: dachnaya-zhizn.ru/izmelchitel-drevesiny-svoimi-rukami
The purpose and principle of operation
The wood chipper will be indispensable for any vacationer. With him no longer need to light fires to burn sawn-off tree branches or to think, what to do with waste after harvesting, stems, tops, roots, etc. of Any organic solid waste machine processed into chips and swarf, which subsequently will serve as an excellent material for high quality compost or solid fuel boilers. So, in one fell swoop, you solve several problems: waste disposal, saving space and time, you will get an endless source of material for fertilizers and fuel for the winter.
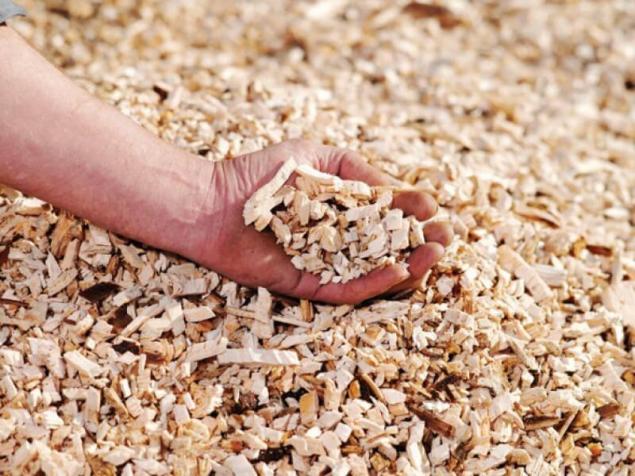
Anyway, the wood chipper is very useful on the farm, but factory mechanisms are prohibitively expensive, so we offer to save money and do it yourself. Most encouraging, there is no need to "reinvent the wheel" — it is necessary only correctly replicate the design of the factory of the device using available parts.
But before you start, you first need to thoroughly study and understand the principle of operation of the machine. Otherwise you will not be able to make a correct drawing and to make it a reality. The device of the chopper just to ugliness is the engine shaft with the cutting elements, frame, protective shell and the receiving compartment through which the material falls inside. Because this unit will get quite heavy, it is better to set on two-wheeled base to easily move around the site.
The principle of operation of the apparatus is as follows: the motor rotates and drives the shaft by means of chain or belt. When you put branches or stalks of plants into the receiving box, the cutting elements are severed into smaller pieces that go on the other side of the device. Very similar to an ordinary kitchen grinder.
Device isolitaire how to choose a pattern and purchase the components of the future, unless it is necessary to define its purpose, that is, what exactly (or more often) it will shred thick branches of fruit trees, small Board, or the remains of plants after harvest. Depends on the output device, type of his work and, consequently, the cost of the necessary details.
The engine of the chipperFor garden shredders you can use gasoline or electric engines. Each of them has its own peculiarities of use. For example, a gasoline engine can process large thick branches, also it is valued for its mobility. Machine with electric motor, on the contrary, must always be near a power source, but it takes up much less space than gasoline. It is easy and convenient to use, but will not handle very large objects due to low power.
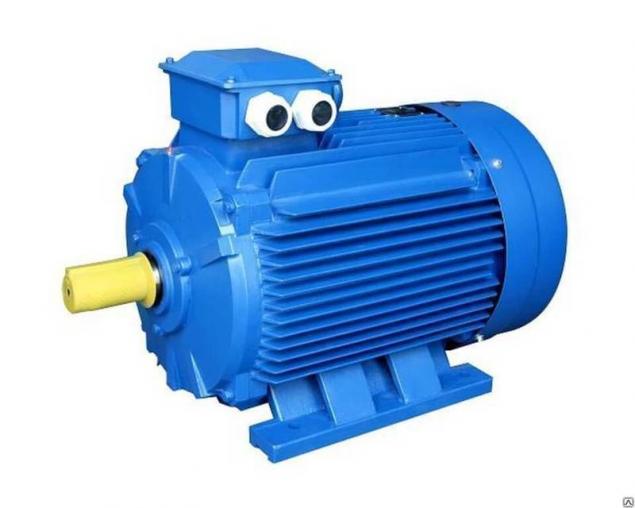
What should pay attention when choosing the engine for garden shredder:
- power up to 1.5 kW will be enough to grind branches with a thickness up to 2 cm;
- more powerful engines in the 3-4 kW is able to shred branches with a diameter of about 4 cm and is suitable for gardeners;
- the engine of 6 kW and more will cope with thick branches 10-15 cm, and may be appropriate for owners of large farms and farms.
The knives of the chopperthe Second important part of the chopper – cutting elements or knives. Their design depends on the type and operation of the mechanism, and also the amount of recycled material. So, a simple disc with blades will grind into dust only fragile branches, combination designs can shred thick branches and give the same small chips, there are those that pulverized wood chips with a length of 2-10 cm If you are planning to use recycled material for solid fuel boilers, it is better to choose the latter option.
Since our aim is to copy one of the factory models of chopper, consider the knives used for their production:
Disc knife – is intended for processing of small branches up to a thickness of 2 cm, stems of plants and herbs.
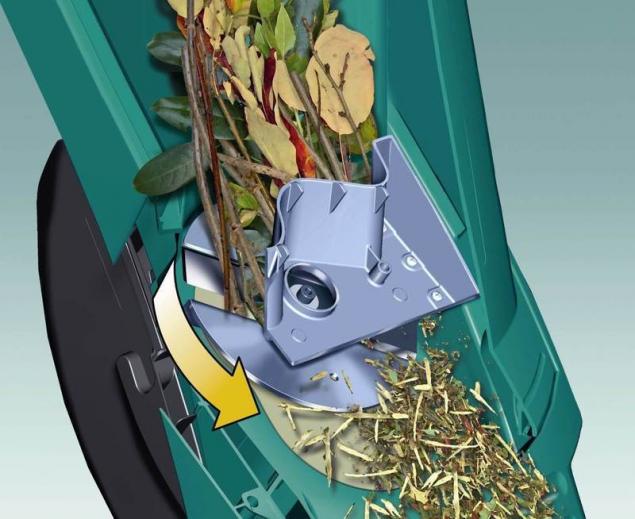
Milling system – knives, arranged in a similar way, you can chop a branch with a thickness of about 8 cm. the Only mandatory condition is that the lumber must be dry. Otherwise, lumps of bark and wet wood chips will clog the cutter and the mechanism will stop working.
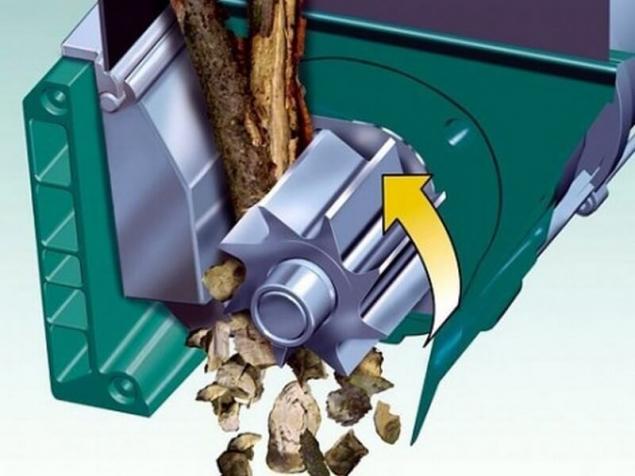
Milling turbine knife is one of the most common and convenient options. This design can shred any branches, regardless of the thickness and the degree of humidity.
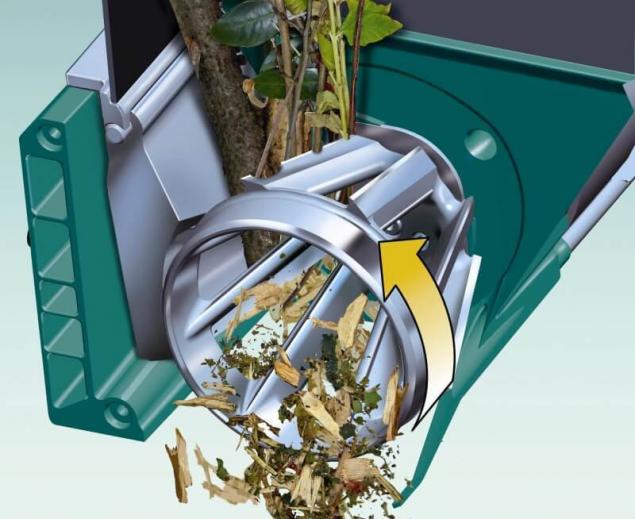
Unfortunately, the models of knives to do on their own is almost impossible, therefore, to improvised devices were invented by their cutting elements: nouvo-disc design, set of saws, and duhvalova system with 8 knives.
Drawing of a grinderto make a grinder for wood, is not enough just to buy the parts, it is necessary to have a professional plumbing skills. The whole process takes place in three stages – the creation of a drawing, preparation of materials and assembling the device.
Since we are not going to invent anything new, the basis of the drawing can take any suitable model of the chopper, and the rest to add at your discretion. To create a drawing you can use a special computer program AutoCAD.
The main components of the mechanism we have described above, but this is only a General view. The most important thing you should pay attention to when creating the drawing – the location of the knives and their angle of cut. Consider the design of crusher with two shaft cutting element.
So, the shafts will be located between the plates and each shaft will have 3-4 knife. For attaching cutting elements to better use the bolts, shifting them with respect to the Central part of the shaft. The shaft rotates freely thanks to the 4 bearings that are fixed on the plates. The synchronicity of the movement of the shafts provide 2 gears, which drives the motor. To transmit torque, use a strap or chain to choose from. Depending on the dimensions of the blades and the diameter of the raw material you are going to grind, vary the interval between the shafts.
If you use the motor to 4 kW, its number of revolutions is 2500-2800 rpm Be a good indicator for disc mechanism, designed for fine twigs and plant stems. Two-shaft mechanism must be powerful, so the speed should be reduced.
The images below are drawings of the wood chipper with 2 shafts, each of which has 3 knives:
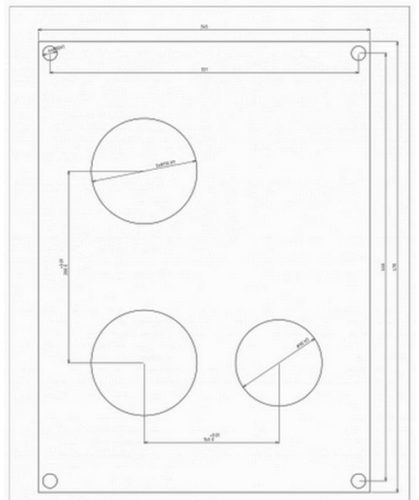
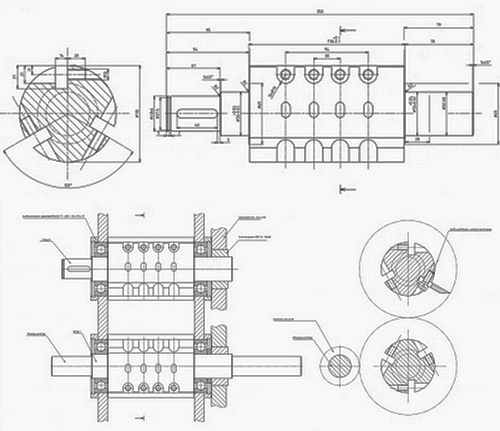
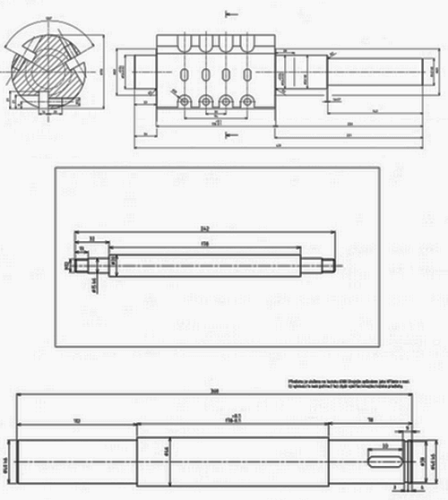
The disc model looks a lot easier mainly due to the simple design of the knives.
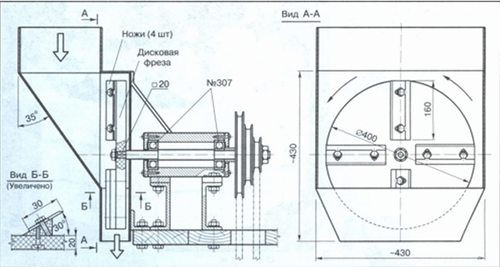
The drawing can display the disc diameter, number of blades and their location. The more blades, the finer will be raw output. The drive can be positioned vertically or at an angle.
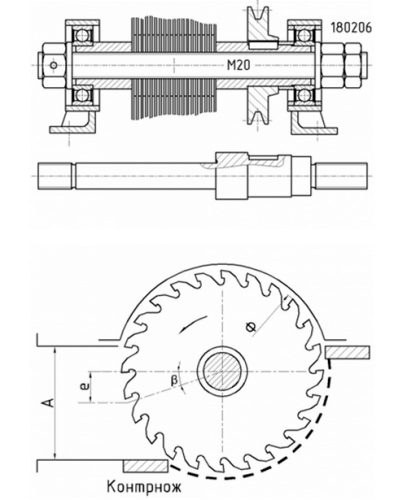
The frame is attached to the stud with circular saws. Often, these devices use a belt to drive, so the shaft pin and two pulley.
Most of the materials needed to build a chopper, you can buy at the car store agricultural equipment or a hardware store, but some items need to order or make yourself. It needs to be able to work as a grinder and welder.
Twin-shaft shredderWork on creation of twin-shaft shredder consists of the following phases of Assembly of the frame and a receiving compartment, the creation of a chopping drum with knives, Assembly of the drum and the motor.
Materials needed:
- engine;
- plate 10 mm – 2 PCs;
- gear – 2 PCs;
- pulley — 1 piece;
- shaft for blades – 2 PCs;
- bearings with fasteners– 5 PCs;
- knives;
- profiled tube;
- sheet metal (thickness 2 mm).
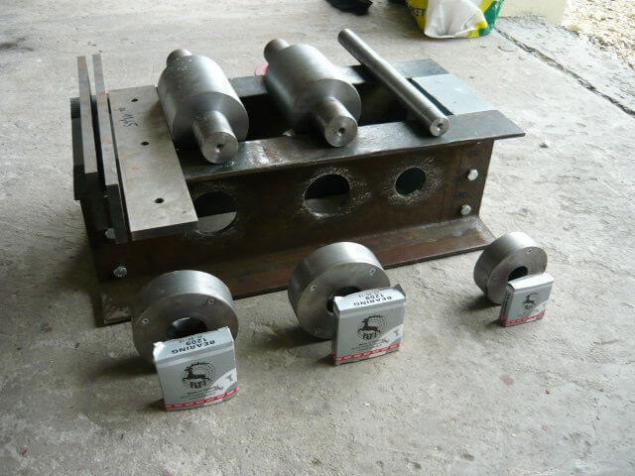
The first step is to make the frame. To do this cut from a shaped tube 4 details: 2 – 40 cm, 2 – 80 cm. Welding machine clamp the short piece between the long right angle to make a frame. The distance between the two internal cross members shall be such that they could stand the grinding drum.
To later shredder can be moved, it is necessary to fit the wheels. On the frame lock 2 strut, which then will keep the axle and wheels.
Engine Assembly:
When the frame is ready, you can assemble a milling drum. To make the shaft, take a square billet for 4 knives or round, for 3. From a square piece file out the tips, making them round, so they went into the bearings. If you use the round billet, hone its Central part, making 3 flat slice of a knife.
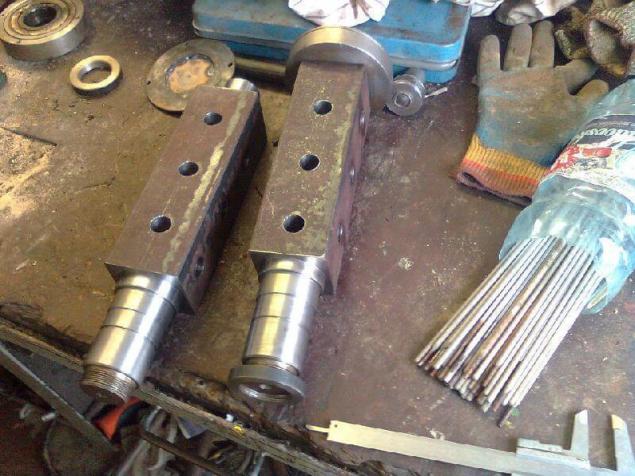
Sami knives can be easily made of spring KAMAZ. Cut desired slice of the springs, align it if necessary, heating in the forge and repeatedly struck with a hammer. Will descalate detail and let cool. The knives make holes for the bolts. Sharpen the knives on the machine, by choosing the angle of the cutting edge of 35-45.
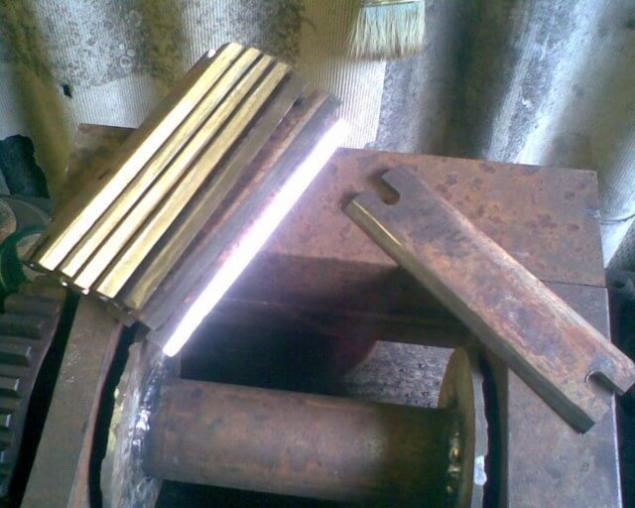
Attach the blades to the shaft and mark the fixing points. Drill holes in the intended locations and make them in the thread. To make the milling drum, take two plates – this will be wall. The welder cut holes in them for the bearings and abrade the edge. If you can not do this step yourself, you can go to the locksmith shop or the enterprise. Install inside the bearings.
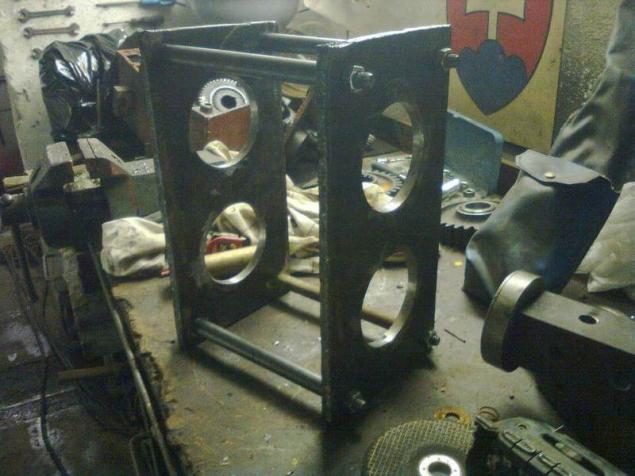
Bolts attach the lining to the metal wall. Insert the shafts into the bearings and secure them. Connect the threaded metal wall studs and fix them with nuts. It only remains to make the receiving compartment through which the timber to get inside. To do this, take sheet metal and make 4 of the same workpiece in the form of a parallelepiped. Find the narrow side of each blank, back from her by 5 cm and fold the edge. Bend the remaining three blanks do in the opposite direction. Assemble the box and make sure that the workpiece tightly adjoin each other. Join the edges by welding or self-locking rivets. At the base on the curved sides of the drill locations for the mounting holes.
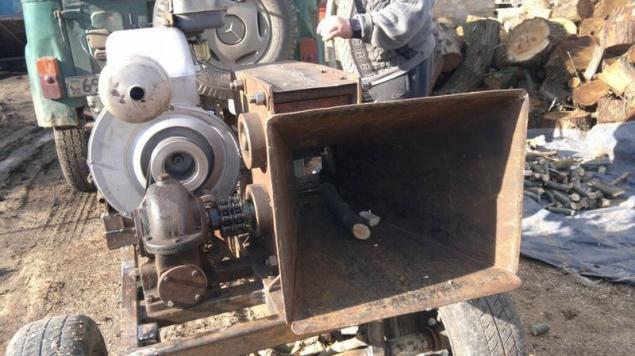
Install all the gathered design on the frame and secure it with the bolts. Put the engine and pull the drive element (chain or belt). In the last turn and install lock box. Close all internal parts with a protective cover to the rotating mechanisms has not got the chips and COP.
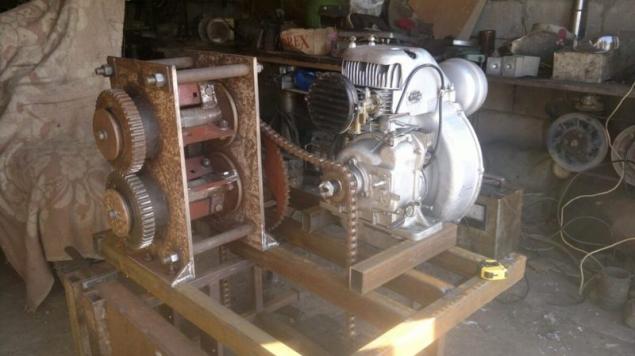
The Assembly of the wood chipper in the video below will help you to more fully represent, how is the whole process:
SUBSCRIBE to OUR youtube channel that allows you to watch online, download from YouTube free video about the recovery, the rejuvenation of man. Love for others and ourselves, as the feeling of high vibrations — an important factor for improvement .
Put LIKES and share with your FRIENDS!
www.youtube.com/channel/UCXd71u0w04qcwk32c8kY2BA/videos
Disc pulperIn contrast to twin-shaft, disc grinder requires far fewer parts, time and effort during Assembly.
Materials needed:
- motor;
- knives;
- profiled tube;
- sheet metal to create the disk;
- sheet metal 2 mm in thickness for the protective shell and the receiving compartment.
Progress:
Of stainless steel make the frame. Place the engine into the frame. On top of the engine install reflective shield out of sheet metal. The reflective shield cut a hole for the shaft.
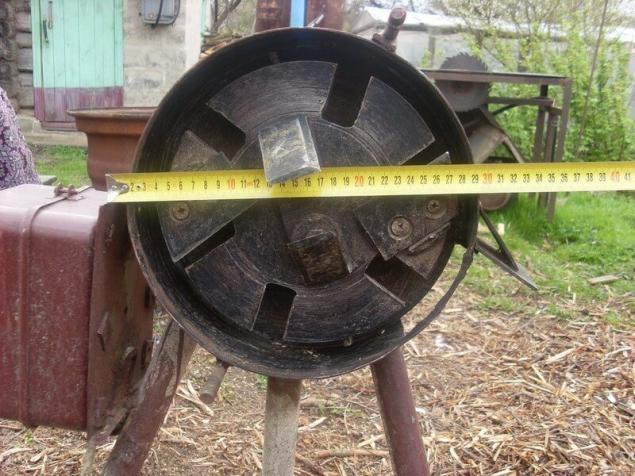
The disc drill a hole for mounting on the shaft and a small slot for fixing the knives.
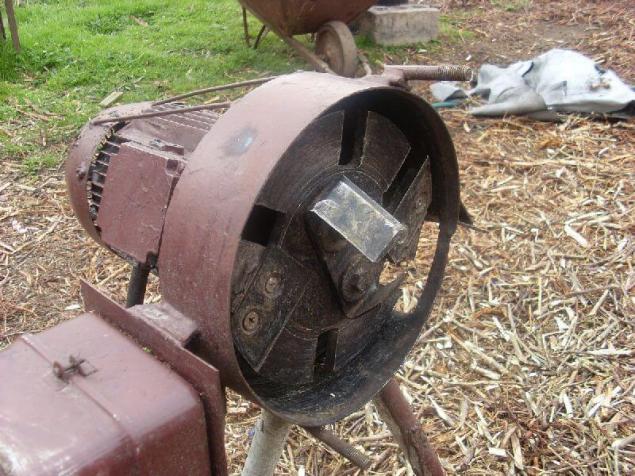
Assemble the disc with the knife and set it inside. Make a box out of sheet metal by the above instructions and install it on the chopper.
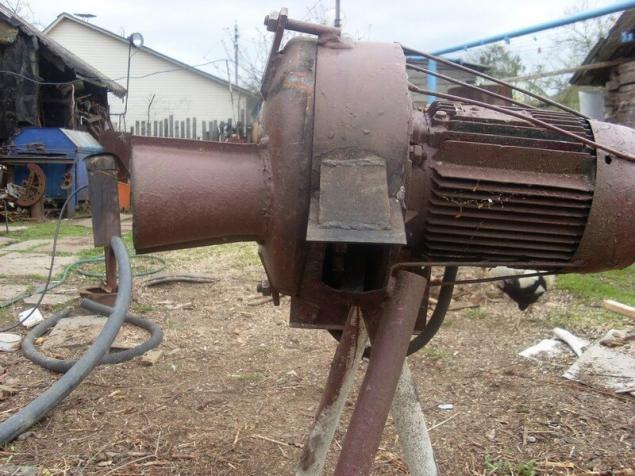
As you can see, nothing complicated, the main thing is to get all the necessary parts. Homemade wood chipper with two shafts has great power and is intended for processing of large branches. The size of the chip can be controlled from 2 cm to 8 cm depending on the number of knives on one shaft. published
Source: dachnaya-zhizn.ru/izmelchitel-drevesiny-svoimi-rukami
Mini-sauna for the home and garden: how to make a barrel with their hands
What to do if you were attacked by Viper