7881
For all the good paying body (8 photos)
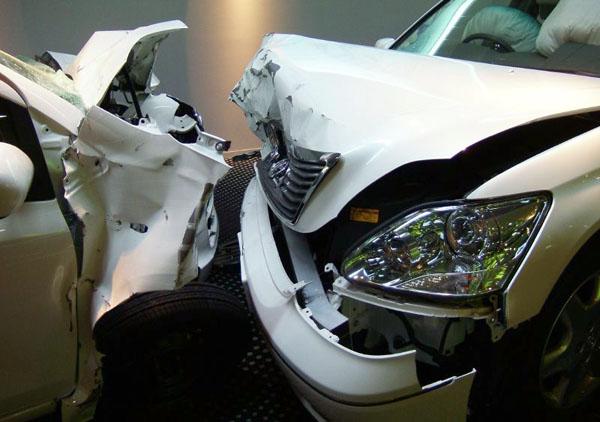
Every driver wants his car was fast, comfortable, reliable, economical and safe. His desires are understandable, but internally contradictory. Something always have to sacrifice: to improve certain qualities to pay other deterioration. While most "extreme" is physical strength.
Lose weight, to save
Economy depends on the mass of the vehicle. After the oil crisis of the 70s of the twentieth century, cars have become much easier. This was facilitated by, on the one hand, the development of processing techniques have become, the use of computer modeling, which helped precisely calculate the load on each part of the body or part. On the other hand, the prices for oil, vehicles had to "lose weight" in order to save on fuel.
More accurate data and the emergence of more and more new alloys allowed to do many of the details are thinner and lighter. For example, much thinner steel exterior body panels: the front wings, the outer door leaf. In principle, the reliability of the car will not be harmed. Galvanized metal technology have resulted in not the worst, and now even better results on the stability of the body to corrosion.
However, after heavy hail car is likely to be similar to a golf ball - all in a small dimple. But this is a so-called force majeure, provided all such situation is impossible. If before the vehicle resist corrosion due to metal thickness (thicker metal rusted longer), it is now galvanized steel allows to give a guarantee against rust up to 12 years until "consumed" a thin layer of zinc deposited on the surface. Of course, in the absence of chipping and damage from foreign objects.
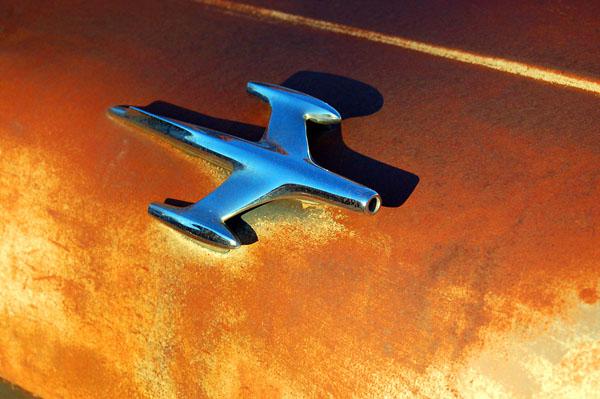
On modern cars rust galvanized metal saves
True, the bodywork paint has become more fragile. And the cause is the desire to get a car that meets the requirements of environmental protection legislation. Modern automotive paint in many respects superior to paint the mid-1950s: there are many colors, additives "metallic", "pearl", "chameleon". But the most significant - is the absence in the harmful lead additives. But these supplements provide automotive paint chipping resistance emergence.
Air emissions of lead compounds have been so significant that today a return to lead additives in paint and can be no question. The company aims at achieving the chemical industry, which at one time managed to make less harmful dyes and colors more vivid and varied. Now the task is to make the paint resistant to damage.
Soft body for accidents
Savings program have gone on to strengthen the superstructure cab, creating a so-called "protective cells". The great achievement of Engineers began crumple zones and the creation of powerful, virtually non-deformable superstructure cab.
The use of different kinds of metal (more durable and softer), the use of computer modeling of deformation of the superstructure of the front and rear has allowed modern cars to gain more points in terms of security. They no longer get 2-4 stars in the mid-1990s, and 3-5 stars for adult occupant safety by the method of EuroNCAP - European independent organization conducting its own testing of passive safety (ie safety in case of accidents) cars. For example, the Citroën C5 car in a frontal crash test with serious deformation of the front end all roof rack minimally displaced or deformed, and thus the space inside the cabin and did not decrease the risk of injury is reduced. By the way, the American method of crash test simulates a collision at lower speeds. Therefore, the European technique is more indicative assessment of progress in building a safe car.
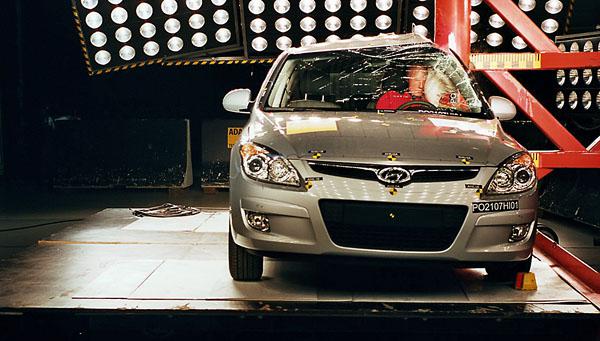
Crash test by the method of EuroNCAP Hyndai i30 received four out of five stars for adult occupant safety, but only two out of four stars for pedestrian safety.
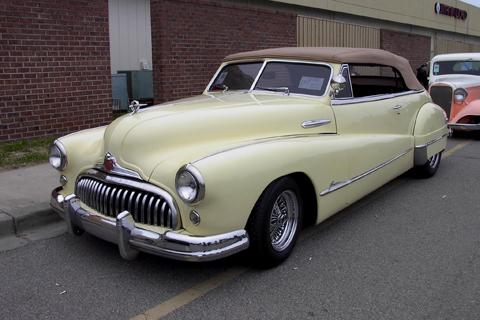
Cars 60s compared to today were much more durable and damaged in collisions, respectively, less. But because of this, the whole force of the blow accrue to the driver and passengers. The modern design represents the maximum plastic - that is irreversible deformation of the body and parts of the car: the hood folded into a neat "accordion" in order not to break the windshield and do not damage the passenger side rails of the body (body bearing beams) effectively extinguish blow, putting in predetermined locations. But the saved lives of drivers and passengers are evidence that the decision to sacrifice the strength of the car, making it vulnerable places, justified.
Pedestrian safety has also become a concern for engineers. In order to shoot down was inflicted minimal damage, actively implemented a "soft" engine hood, frameless wiper and soft bumpers. For example, in a Peugeot 308 to increase the distance between the hood and the engine, so that the collision of a car and a pedestrian softer hood can no longer bend and, therefore, it is better to repay the force of impact. As a result - 3 out of 4 stars for pedestrian safety. This is better than the larger cars Peugeot, and the other cars a class above.
These results were achieved due to the sloping, like minivans, sloping hood and windshield. Of course, such hoods often deformed by negligence, wipers are more expensive, and bumpers though can take the old form in a collision at speeds up to 5 km / h, but in case of accidents, even small, require a minimum of painting. But this is a deliberate decision engineers - a reaction to the demand of public organizations to make "socially responsible" cars.
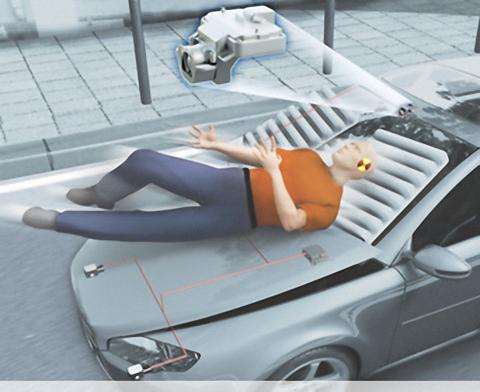
Jaguar engineers at the present generation XK, instead of increasing the distance between the hood and the engine, using a system of sensors Pedestrian Sensing collision with a pedestrian in front of the car and the special hardware engine hood with pyrotechnical. At the moment of impact on the sensor signals triggered pyro cartridge and lift the hood, increasing the distance between the hood and the engine, and the fall pedestrian on the engine compartment lid significantly softened.
Not all manufacturers are going to meet the desires of consumers. For example, the discontent of car owners is how to install airbags in most European cars squib with the folded airbag is installed under the front panel. To airbag can unfold, from the inner side panels made incisions oslablinyuschie part of the panel surface. When expanded by the airbag tears a large and expensive interior panel. The same situation with side airbags mounted in the seat back. Only a few low-end models, for example, Peugeot Partner, Renault Logan, Lada Kalina, provide for disclosure of the front passenger air bag through a separate small "flap" in the front panel, which can be easily replaced after an accident.
Aluminum debut
Innovation is not always offered by the engineers that improve virtually all the characteristics perceived positively by buyers. So was, for example, using the suspension components made of aluminum - a strong and lightweight material. Made of aluminum alloy suspension arms provide the reduction of so-called unsprung mass and thus improves handling, comfort and safety of the car.
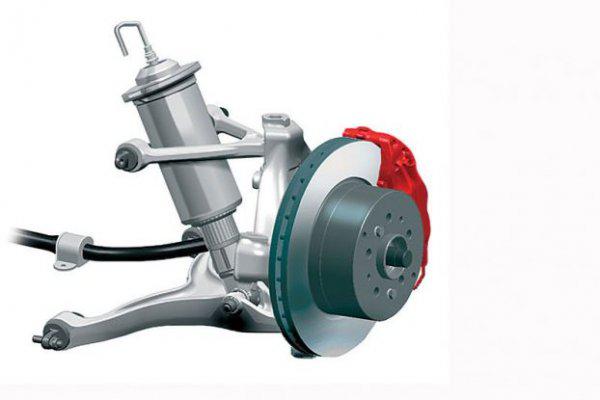
However, for aluminum and its alloys are characterized by "metal fatigue" - a sharp change in the properties of the metal, making it very fragile. Suspension components made of aluminum alloys after a certain amount of work in excess of the threshold strength of the metal can simply break. Details of steel, losing strength, are deformed so that it is not dangerous to the same threshold, which occurs after the "metal fatigue" of the steel and its alloys is considerably higher.
In order to prevent the operation of aluminum suspension parts above the norm, they were made with a single node regularly replaceable elements suspension - ball bearings, sometimes with silent blocks or other plugs that can be replaced after a certain mileage (every 40-60 thousand kilometers) . But such details and work on replacing them proved costly. To meet the consumers, many car manufacturers, obzavedshiysya in the second half of the 1990s suspension parts made of aluminum and its alloys, in this decade heirs received no details of the "winged" metal.
There is also a very interesting situation when the car became more fragile. For example, the story of the introduction of the cast alloy wheels. Started racing with their application, where it is very important weight of each node and details. Soon, these solutions have been used on road cars. But it was rather an aesthetic need.
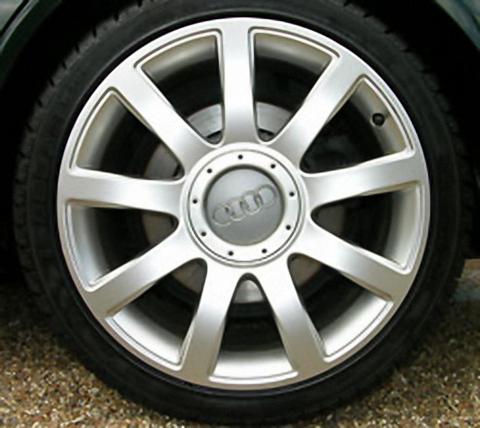
Audi RS4 - an extreme version of the model A4. Specialists has been significantly redesigned undercarriage of the car. The car is equipped with beautiful, large diameter alloy wheels with low-profile tires. Wanting to reduce unsprung weight and stiff suspension make for extremely precise reactions of the car, the engineers at the end of their "improvements" came to a serious increase in the load on the suspension of the car.
The desire of buyers to get beautiful wheels make the car more vulnerable. When zooming in on the curb, hit a deep hole standard steel forged wheels are deformed. But so the wheels can be relatively easy to return to the previous form. Restore the form of alloy wheels in the deformation is possible only on a special machine. If the load exceeds a certain threshold, there is a possibility that the crack alloy wheel, in this case no longer continue to move at a wheel, or it can not be repaired.
What's next?
Engineers and designers are constantly working hard to find the optimal combination of safety, environmental cleanliness, efficiency, comfort and reliability of the car.
In the future, the paint may become softer, less susceptible to stone chips. Today promising techniques for painting on Nissan's possible to obtain paint, not only more resistant to slight scratches, but also self-healing. Shallow surface scratches on the paint themselves "delayed" in a few days.
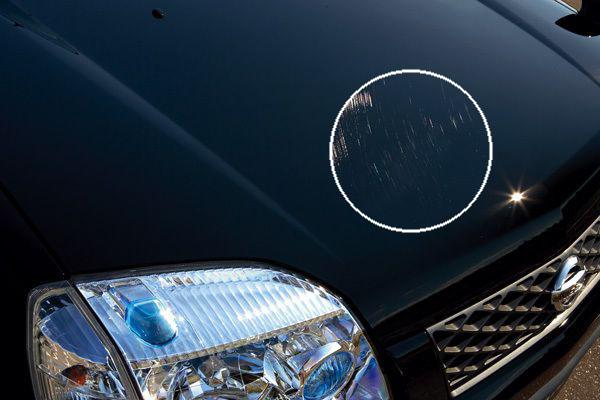
Nissan's engineers have managed to create a paint Scratch Guard Coat, which, thanks to special additives, does not harden completely dries. This feature allows you to retain the ability to drag the paint in the affected areas.
Hardly cars become harder to do again, to small accident leaves no residue. But nothing prevents to make the car more "maintainable" to damaged parts easier to change. For example, right now the leading manufacturers of headlights are mounted on an easy to replace plastic emphasis that when you hit a headlight broken and quenched blow, leaving the entire headlamp expensive.
Automakers is not yet possible to satisfy all the requirements for modern cars. We have to choose the most important and focusing on them, continue to try to create the perfect car.