754
Volgograd student came up with 3D-printer
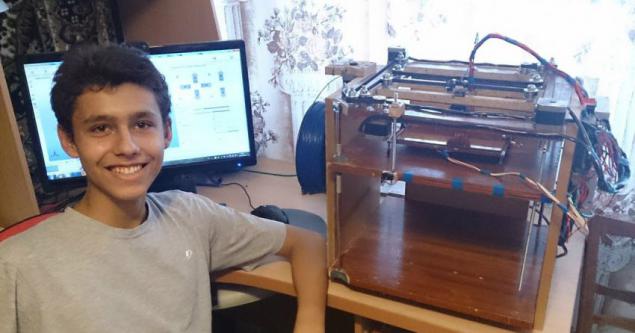
VolgoBot based on the achievements of the popular project RepRap, but has an original design. "I use technology Fused deposition modeling (FDM), when the plastic is fed into a bar in the thermal head, it melts and is applied in layers on the desktop, gradually forming part. In my printer thermal head is moved horizontally, XY axis using a clever positioning mechanism called H-Bot, simply put, is when the design is only one belt. Desk, in turn, goes along the vertical axis Z, gradually falling during the press ", - says Michael. As print media he plans to use any appropriate technology requirements: melt at temperatures up to 300 degrees, allocate a minimum of harmful substances, does not clog the thermal head. For example, it is ABS plastic, PLA, Neylon, Polywood (wood imitation).
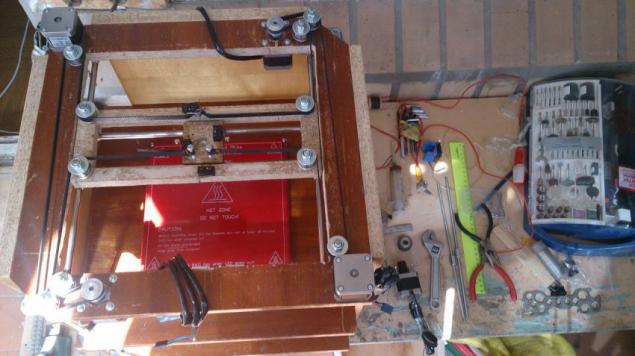
VolgoBot name chosen in honor of the city on the Volga, where he lives Michael. Now in the assembly stage is VolgoBot №0. His mission - to print the items to VolgoBot №1 and give life to the next 3D-printers. "I'm almost finished assembly can only Teflon tube for feeding the rod in the thermal head, which" races "in the mail. While engaged in setting and calibration electronics mechanics, "- says Michael.
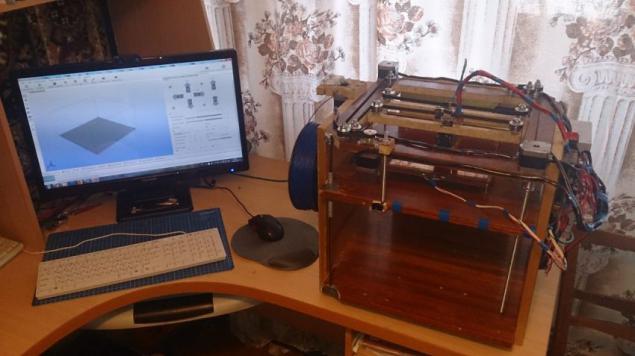
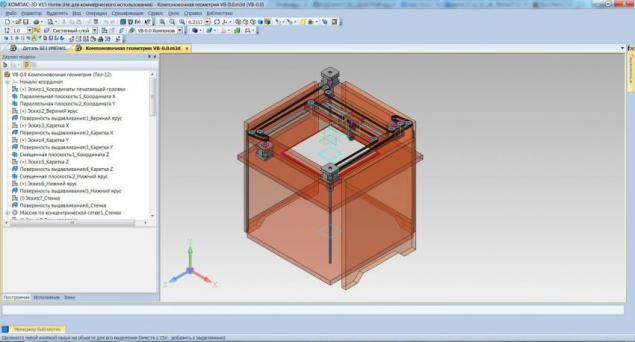
Before you begin to develop your own 3D-printer, Michael has studied the structure of existing models. To gain experience he modeled in KOMPAS-3D printer Prusa Mendel i2 (developer Josef Prusa).
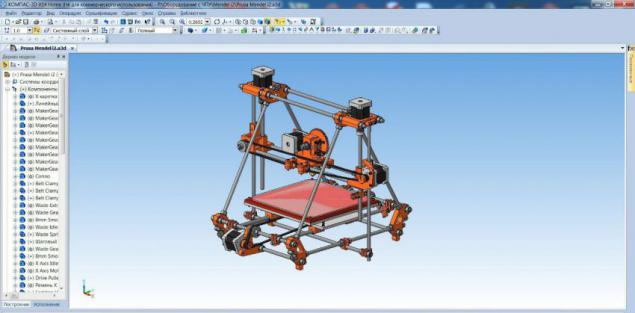
Michael knew many CAD-systems, but believes that his choice is KOMPAS-3D: «It is much more convenient for me and dearer." His familiarity with the system, he began with a training version of KOMPAS-3D LT, and now enjoys a full-featured KOMPAS-3D Home.
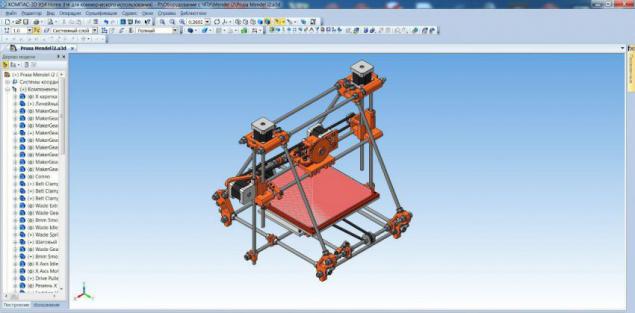
Source: ascon.ru