488
Technology ecology: how the toxic emissions of the internal combustion engine is converted into "fragrance of violets"
Adsorbents and catalysts, probes and filters, reservoirs and honeycomb ceramic is a whole mini-plant for processing chemical waste is hidden under the hood of a modern car with the engine running on hydrocarbon fuels. Today we will touch on the technologies developed in harmony with the requirements of rapidly changing environmental standards, we will understand how neytralizuya toxic emissions of the internal combustion engine and try to assess the prospects for survival of this segment of the market, given current global trends.
At the end of last year the German government announced that by 2050, cars with internal combustion engines will remain, that soon became one of the reasons for the country's accession to the international Alliance ZEV (Zero-Emission Vehicle), the ambitious aim of which is radically reducing the level of greenhouse gas emissions on a global scale. For the producers of vehicles on hydrocarbon fuels is a more than clear call that clearly identifies a key priority of survival is the development of effective means to reduce the toxicity of automobile emissions.
And why, in fact, to neutralize the exhaust gases – you ask? As known from the school course of chemistry in the combustion of any organic fuel to form carbon dioxide and water. But carbon dioxide is not the most dangerous product of the reaction occurring in the chamber of the internal combustion engine. First: the fuel does not burn completely and the combustion process is accompanied by formation of very toxic substances such as carbon monoxide (co), and, simultaneously, large amounts of unburned until the end of hydrocarbons (arenes – to paraffins). Second, the process of burning actively involved nitrogen (N2) from the air and impurities contained in the gasoline – sulfur, etc. In turn, the emissions of nitrogen oxides (NOx) cause acid rain, smog, and now widely produced ozone holes. No less a danger to human health and all living things represent and byproducts of combustion containing sulphur compounds. Here we note that in the U.S. special attention to the problem focus on the concentration of NOx in exhaust gas, generating in the result of decomposition under the influence of sunlight the infamous California photochemical smog.
Catalytic Converter
As we know, again from a school program catalysts – substances that speed up chemical reactions, but not joining them. A perfect example is precious metals. Three-way catalytic Converter with a composition of palladium (Pd), platinum (Pt) and rhodium (Rh) covers the ceramic honeycomb thin layer. The total area of the surface of the coating such honeycomb is, on average, up to 20 000 sq. m. (!) Such an impressive area improves the contact of the exhaust gases with noble metals, which, based on the single Converter takes only 2-3 grams. Unit Converter burn residuals of carbon monoxide and decomposes a portion of unburned hydrocarbons to carbon dioxide and water. Harmful oxides NOx to atmospheric nitrogen regenerates the rhodium.
The working catalyst temperature is 400-800°C, so the inner pieces of structure units are made of thermally stable ceramic – silicon carbide or cordierite. The problem often faced by engineers in determining the optimal location of the catalyst. The fact that output working temperature mode of the latest need some time and a cold engine emits virtually untreated mixture. The question is, whether to arrange the catalytic Converter closer to the engine, where it will be faster to warm up, or closer to the muffler, where the device will operate in a more benign temperature regime.
Most modern cars are equipped with systems of neutralization and in this regard, it is not necessary to leave your car on the lawn with dried grass – the case of the Converter, red-hot after a trip, may cause ignition of the grass with aggravating consequences. It is not advisable to start the engine by way of towing, as this may cause the fuel getting to the catalytic Converter, the subsequent detonation, accompanied by the destruction of the ceramic honeycomb.
Adsorption of nitrogen oxides
Catalytic Converter LNT (Lean NOx Trap) is one of the examples of modern systems are designed to reduce nitrogen oxides in exhaust gases of diesel engines. Accumulation of oxides in the body contributes to the adsorbent is a barium oxide or the like. At the moment when the Converter is completely filled, the computer gives the command to the enrichment of the air-fuel mixture fed into the combustion chamber. At first glance, it's crazy, because a mixture in which a lot of fuel and little air, dramatically increases the concentration of toxic carbon monoxide in the exhaust gases. In fact, it is slightly different scenario: inside LNT catalyst carbon monoxide reacts with nitrogen oxides, decomposing them to harmless molecular nitrogen N2 and conditionally harmless carbon dioxide. At the moment when the Converter is fully cleaned of NOx from the engine goes to normal operating mode. As you know, to talk about the economy of periodic pereobulsya mixture would not be true, but if it comes to such priority as the clean environment, the inclusion of the duty cycle of these components is justified.
What is a lambda probe
Effective neutralization involves the optimal concentration of oxygen. If the mixture is excessively lean, i.e. there is a shortage of fuel due to the prevailing air, the NOx concentration in the exhaust gases increases. Enrichment of the mixture under these conditions is not accompanied by complete burning of fuel and in the exhaust will increase the concentration of carbon monoxide not oxidized hydrocarbons. To maintain the optimum oxygen balance used lambda probe is a sensor that monitors the oxygen level in the exhaust manifold of the engine.
If the excess air ratio, representing the ratio of the volume of air to the volume of the mixture λ > 1, the mixture of “poor”, if λ < 1 – enriched. Lambda probe is a kind of fuel cell with platinum electrodes with an electrolyte of Zirconia. One of the electrodes of the sensor communicates with the outboard air containing an oxidizer (oxygen), and the other electrode with the exhaust gases. “Fuel” for the cell is unburned gasoline. The enrichment of the mixture, the voltage at the sensor increases, which serves as a signal to the computer for supplying commands to the lean condition.
Lambda probe — fuel cell with two platinum electrodes and electrolyte of Zirconia. And the electrodes, and an electrolyte permeable to oxygen. Inside the probe is fed air from outside, which is heated heating element. If the mixture is rich and the exhaust contains little oxygen, the O2 concentration inside the probe becomes much more than the outside. Therefore oxygen from outside air passes through the electrodes and the electrolyte as ions, causing the electric current in the external circuit. As soon as molecules of oxygen appear in the exhaust (in lean mixtures), the concentration is equalized, and the voltage drops sharply.
Exhaust gas recirculation
Nitrogen is very inert, and in order to enter into the desired reaction it is necessary either to compress or heating. The first and the second condition is satisfied in the cylinder of the diesel engine (for gasoline units, this is not true because the compression ratio is much lower). Lowering the temperature in the cylinder may reduce the concentration of nitrogen oxides in the exhaust. With this function, the cope system of exhaust gas recirculation EGR, the first modification which was installed back in the 1970-ies on diesel trucks in the United States. Using a special valve exhaust gases are mixed with exhaust air and sent back into the cylinder. Part of the heat accompanying the combustion of the mixture assume the inert gases, causing the temperature in the combustion chamber is reduced.
The injection of urea
When environmental standards come into its own, comes to the aid of urea. Nitrogen oxides superbly restored to molecular nitrogen reacts with ammonia (NH3). Another thing is that keeping on Board of toxic gas is impossible. As an alternative to storing ammonia chemical engineers suggested the use of urea ((NH2)2CO) is injected into the exhaust tract of the vehicle separate portions. In “tandem” with the exhaust gases, the urea comes in a special catalytic Converter, where is transformed into ammonia required for the decomposition of NOx to nitrogen and water. The described technology is called selective catalytic SCR (Selective Catalytic Reduction), and uncomfortable to our ears the word "urea" in this technology have replaced the sonorous AdBlue. Although, if you look, AdBlue is only 32,5% pure (NH2)2CO in distilled water.
As you can see, environmental standards have been a powerful stimulus in creating an entire field of chemical industry, and the owners of “urea” diesel engines have to fill the car with diesel fuel and AdBlue consumption, which is very noticeable and is up to 6% of the volume of used fuel.
Before the portion of exhaust gases back into the cylinder it must be cooled, which can be used as a liquid cooling loop and air, or both. The figure shows the recirculation system of the truck Scania.
Diesel particulate filters
Neutralize to accepted norms require not only a gaseous mixture of exhaust gas and solid particles. Such microscopic particles of soot, ranging in size from 10 to 1 µm are emitted during acceleration familiar to us all overloaded Trucks. Familiar sight. Can you imagine the “healing” effect, which is this intensely spewing smog has on our lungs. Soot in the exhaust, and NOx is mainly a problem of diesel engines, since diesel fuel is quite a heavy oil fraction containing unsaturated compounds. This helps to ensure that the concentration of carbon in the diesel fuel higher than gasoline, and hence soot during combustion will stand out more.
To cope with the problem allows high-temperature resistant ceramics. It works like this. Up to a point special ceramic filters DPF (Diesel Particulate Filter) to adsorb soot from the exhaust, and after accumulating to a certain limit, the engine is translated into a special mode of operation in which the temperature of the gases in the exhaust system increases up to 600 °C, which taking into account the existing system allows oxygen to oxidize the soot, and then output through the exhaust pipe. In order not to subject the DPF to the damaging effects of high temperatures, some manufacturers cover the ceramic surface with a thin layer of platinum functions as a catalyst. The PSA group engineers (Peuqeot-Citroen) have proposed to add diesel fuel additives based on cerium (Ce), which allows to reduce the temperature of soot oxidation to 450 °C. And it is quite comparable to conventional exhaust gas temperature. In countries where work standards Euro 5 since 2011, all diesel cars have DPF filters.
Low-voltage hybrid
The owners of vehicles with engines, for hydrocarbon fuels is getting harder to squeeze existing technological solutions in the framework of continuously tightening environmental regulations. Current trends more clearly define the transition to hybrid solutions. One of them on the basis of low voltage hybrid (48V) suggested Bosch. And such low-voltage systems in the near future will allow “hybridizing” many existing models of cars.
Despite the attractiveness offered by the engineers of innovation from the point of view of environmental impact, the final cost of the internal combustion engine, and the car itself, “burdened” green technologies enough to significantly increase. Therefore, if the trend will continue in the foreseeable future, the use of internal combustion engines against the background of promoting and improving the infrastructure of electric vehicles will be simply ineffective. published
P. S. And remember, only by changing their consumption — together we change the world! ©
Join us in Facebook , Vkontakte, Odnoklassniki
Source: geektimes.ru/company/dronk/blog/275958/
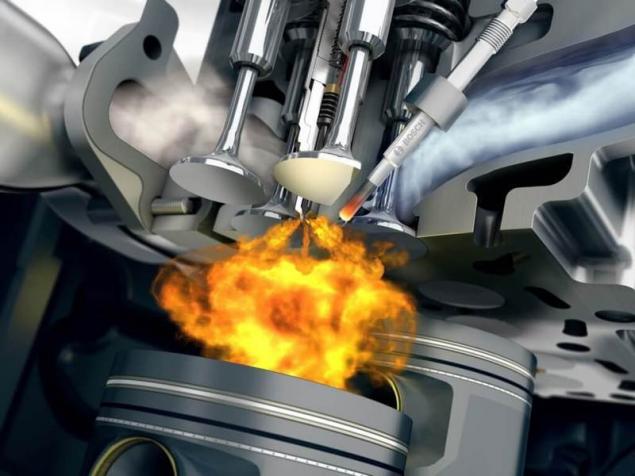
At the end of last year the German government announced that by 2050, cars with internal combustion engines will remain, that soon became one of the reasons for the country's accession to the international Alliance ZEV (Zero-Emission Vehicle), the ambitious aim of which is radically reducing the level of greenhouse gas emissions on a global scale. For the producers of vehicles on hydrocarbon fuels is a more than clear call that clearly identifies a key priority of survival is the development of effective means to reduce the toxicity of automobile emissions.
And why, in fact, to neutralize the exhaust gases – you ask? As known from the school course of chemistry in the combustion of any organic fuel to form carbon dioxide and water. But carbon dioxide is not the most dangerous product of the reaction occurring in the chamber of the internal combustion engine. First: the fuel does not burn completely and the combustion process is accompanied by formation of very toxic substances such as carbon monoxide (co), and, simultaneously, large amounts of unburned until the end of hydrocarbons (arenes – to paraffins). Second, the process of burning actively involved nitrogen (N2) from the air and impurities contained in the gasoline – sulfur, etc. In turn, the emissions of nitrogen oxides (NOx) cause acid rain, smog, and now widely produced ozone holes. No less a danger to human health and all living things represent and byproducts of combustion containing sulphur compounds. Here we note that in the U.S. special attention to the problem focus on the concentration of NOx in exhaust gas, generating in the result of decomposition under the influence of sunlight the infamous California photochemical smog.
Catalytic Converter
As we know, again from a school program catalysts – substances that speed up chemical reactions, but not joining them. A perfect example is precious metals. Three-way catalytic Converter with a composition of palladium (Pd), platinum (Pt) and rhodium (Rh) covers the ceramic honeycomb thin layer. The total area of the surface of the coating such honeycomb is, on average, up to 20 000 sq. m. (!) Such an impressive area improves the contact of the exhaust gases with noble metals, which, based on the single Converter takes only 2-3 grams. Unit Converter burn residuals of carbon monoxide and decomposes a portion of unburned hydrocarbons to carbon dioxide and water. Harmful oxides NOx to atmospheric nitrogen regenerates the rhodium.
The working catalyst temperature is 400-800°C, so the inner pieces of structure units are made of thermally stable ceramic – silicon carbide or cordierite. The problem often faced by engineers in determining the optimal location of the catalyst. The fact that output working temperature mode of the latest need some time and a cold engine emits virtually untreated mixture. The question is, whether to arrange the catalytic Converter closer to the engine, where it will be faster to warm up, or closer to the muffler, where the device will operate in a more benign temperature regime.
Most modern cars are equipped with systems of neutralization and in this regard, it is not necessary to leave your car on the lawn with dried grass – the case of the Converter, red-hot after a trip, may cause ignition of the grass with aggravating consequences. It is not advisable to start the engine by way of towing, as this may cause the fuel getting to the catalytic Converter, the subsequent detonation, accompanied by the destruction of the ceramic honeycomb.
Adsorption of nitrogen oxides
Catalytic Converter LNT (Lean NOx Trap) is one of the examples of modern systems are designed to reduce nitrogen oxides in exhaust gases of diesel engines. Accumulation of oxides in the body contributes to the adsorbent is a barium oxide or the like. At the moment when the Converter is completely filled, the computer gives the command to the enrichment of the air-fuel mixture fed into the combustion chamber. At first glance, it's crazy, because a mixture in which a lot of fuel and little air, dramatically increases the concentration of toxic carbon monoxide in the exhaust gases. In fact, it is slightly different scenario: inside LNT catalyst carbon monoxide reacts with nitrogen oxides, decomposing them to harmless molecular nitrogen N2 and conditionally harmless carbon dioxide. At the moment when the Converter is fully cleaned of NOx from the engine goes to normal operating mode. As you know, to talk about the economy of periodic pereobulsya mixture would not be true, but if it comes to such priority as the clean environment, the inclusion of the duty cycle of these components is justified.
What is a lambda probe
Effective neutralization involves the optimal concentration of oxygen. If the mixture is excessively lean, i.e. there is a shortage of fuel due to the prevailing air, the NOx concentration in the exhaust gases increases. Enrichment of the mixture under these conditions is not accompanied by complete burning of fuel and in the exhaust will increase the concentration of carbon monoxide not oxidized hydrocarbons. To maintain the optimum oxygen balance used lambda probe is a sensor that monitors the oxygen level in the exhaust manifold of the engine.
If the excess air ratio, representing the ratio of the volume of air to the volume of the mixture λ > 1, the mixture of “poor”, if λ < 1 – enriched. Lambda probe is a kind of fuel cell with platinum electrodes with an electrolyte of Zirconia. One of the electrodes of the sensor communicates with the outboard air containing an oxidizer (oxygen), and the other electrode with the exhaust gases. “Fuel” for the cell is unburned gasoline. The enrichment of the mixture, the voltage at the sensor increases, which serves as a signal to the computer for supplying commands to the lean condition.

Lambda probe — fuel cell with two platinum electrodes and electrolyte of Zirconia. And the electrodes, and an electrolyte permeable to oxygen. Inside the probe is fed air from outside, which is heated heating element. If the mixture is rich and the exhaust contains little oxygen, the O2 concentration inside the probe becomes much more than the outside. Therefore oxygen from outside air passes through the electrodes and the electrolyte as ions, causing the electric current in the external circuit. As soon as molecules of oxygen appear in the exhaust (in lean mixtures), the concentration is equalized, and the voltage drops sharply.
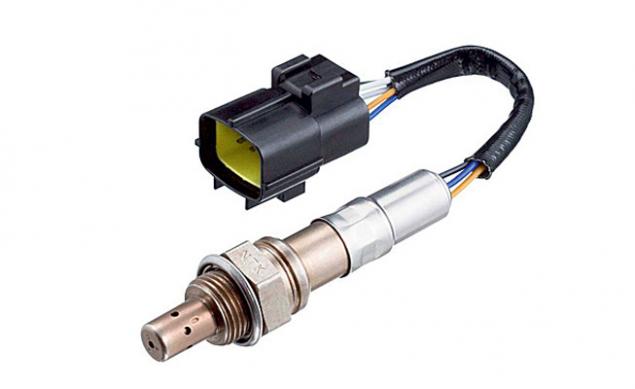
Exhaust gas recirculation
Nitrogen is very inert, and in order to enter into the desired reaction it is necessary either to compress or heating. The first and the second condition is satisfied in the cylinder of the diesel engine (for gasoline units, this is not true because the compression ratio is much lower). Lowering the temperature in the cylinder may reduce the concentration of nitrogen oxides in the exhaust. With this function, the cope system of exhaust gas recirculation EGR, the first modification which was installed back in the 1970-ies on diesel trucks in the United States. Using a special valve exhaust gases are mixed with exhaust air and sent back into the cylinder. Part of the heat accompanying the combustion of the mixture assume the inert gases, causing the temperature in the combustion chamber is reduced.
The injection of urea
When environmental standards come into its own, comes to the aid of urea. Nitrogen oxides superbly restored to molecular nitrogen reacts with ammonia (NH3). Another thing is that keeping on Board of toxic gas is impossible. As an alternative to storing ammonia chemical engineers suggested the use of urea ((NH2)2CO) is injected into the exhaust tract of the vehicle separate portions. In “tandem” with the exhaust gases, the urea comes in a special catalytic Converter, where is transformed into ammonia required for the decomposition of NOx to nitrogen and water. The described technology is called selective catalytic SCR (Selective Catalytic Reduction), and uncomfortable to our ears the word "urea" in this technology have replaced the sonorous AdBlue. Although, if you look, AdBlue is only 32,5% pure (NH2)2CO in distilled water.
As you can see, environmental standards have been a powerful stimulus in creating an entire field of chemical industry, and the owners of “urea” diesel engines have to fill the car with diesel fuel and AdBlue consumption, which is very noticeable and is up to 6% of the volume of used fuel.
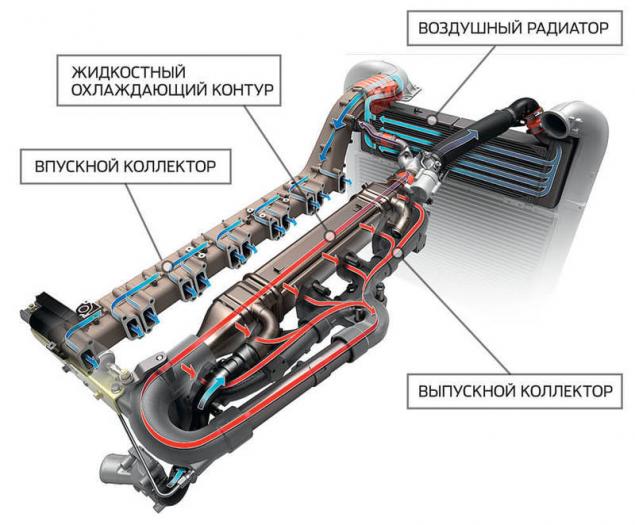
Before the portion of exhaust gases back into the cylinder it must be cooled, which can be used as a liquid cooling loop and air, or both. The figure shows the recirculation system of the truck Scania.
Diesel particulate filters
Neutralize to accepted norms require not only a gaseous mixture of exhaust gas and solid particles. Such microscopic particles of soot, ranging in size from 10 to 1 µm are emitted during acceleration familiar to us all overloaded Trucks. Familiar sight. Can you imagine the “healing” effect, which is this intensely spewing smog has on our lungs. Soot in the exhaust, and NOx is mainly a problem of diesel engines, since diesel fuel is quite a heavy oil fraction containing unsaturated compounds. This helps to ensure that the concentration of carbon in the diesel fuel higher than gasoline, and hence soot during combustion will stand out more.
To cope with the problem allows high-temperature resistant ceramics. It works like this. Up to a point special ceramic filters DPF (Diesel Particulate Filter) to adsorb soot from the exhaust, and after accumulating to a certain limit, the engine is translated into a special mode of operation in which the temperature of the gases in the exhaust system increases up to 600 °C, which taking into account the existing system allows oxygen to oxidize the soot, and then output through the exhaust pipe. In order not to subject the DPF to the damaging effects of high temperatures, some manufacturers cover the ceramic surface with a thin layer of platinum functions as a catalyst. The PSA group engineers (Peuqeot-Citroen) have proposed to add diesel fuel additives based on cerium (Ce), which allows to reduce the temperature of soot oxidation to 450 °C. And it is quite comparable to conventional exhaust gas temperature. In countries where work standards Euro 5 since 2011, all diesel cars have DPF filters.
Low-voltage hybrid
The owners of vehicles with engines, for hydrocarbon fuels is getting harder to squeeze existing technological solutions in the framework of continuously tightening environmental regulations. Current trends more clearly define the transition to hybrid solutions. One of them on the basis of low voltage hybrid (48V) suggested Bosch. And such low-voltage systems in the near future will allow “hybridizing” many existing models of cars.
Despite the attractiveness offered by the engineers of innovation from the point of view of environmental impact, the final cost of the internal combustion engine, and the car itself, “burdened” green technologies enough to significantly increase. Therefore, if the trend will continue in the foreseeable future, the use of internal combustion engines against the background of promoting and improving the infrastructure of electric vehicles will be simply ineffective. published
P. S. And remember, only by changing their consumption — together we change the world! ©
Join us in Facebook , Vkontakte, Odnoklassniki
Source: geektimes.ru/company/dronk/blog/275958/