450
Slow down and stock up: recovery systems in modern cars
Any braking regular braking system is wasted on air heating energy. And the volume of these "expenses" are well known to all city drivers. The difference in fuel consumption when driving around town and on country road with no stops, on average, one and a half times, and even more. To prevent unnecessary loss of tried a long time, but the main problem is the irreversibility of combustion engines is strongly impedes this.
To prove the necessity of regenerative braking, i.e. one in which energy machine again accumulated to be used for overclocking and did not need anyone. The effectiveness of the scheme since the 60-ies checked on the railroad. But there are locomotives, and the energy returns immediately to the network. Machines this method is not very suitable due to the absence of most of these motors...
And since cars go on rails, and locations of deceleration and acceleration is also not very hard to predict. Therefore, the method used in some metro stations, the location of stop points on the hills that allows you to accelerate at the expense of the store of potential energy and slow down due to the rise – also not popular. Except that places bus stops have traditionally tried to place on the roller coaster...
The flywheel in a vacuumHistorically, the first recovery system for machines with internal combustion engine system with mechanical accumulation of energy in the rotating flywheel. Such systems were used mainly on construction equipment, where the large rotating part was used as the energy storage and power delivery was via hydraulic or electrical systems.
But the scope of this kind of technology has remained narrow in the first place it was large excavators and cranes, often port. To make the system more compact and to install on the car just never occurred to any method of implementation rested on the low energy cost and high price of the device.
At an oil price of less than $ 4 per barrel to introduce something similar on the transport have no one to come to mind, and even after the first oil crises, the stock of modernization of the internal combustion engine is more than the overlap needs to save fuel. Volvo even had a system on the model 260 in 1980, but the power of about 10 kilowatts with a steel flywheel has not met expectations, and the program was phased out.
The leap in technology in the 80-ies helped to create a more efficient system of energy storage at the flywheel, eliminating the root problem – the probability of explosive destruction of the flywheel. Solved the problem simply: did the flywheel threads that the destruction was slow. But placing it in vacuum container and the use of gas bearings is allowed to store energy for a very decent period to several days, although most such systems are designed for a short work cycle, the energy input to the flywheel to her spending a few minutes or even seconds.
So, for example, racing KERS in Formula 1. There are practical examples of its implementation for conventional serial machines, such as Porsche and Ferrari. But in practice is likely to spread, such a system does not get it. Along with such advantages as very high capacity and high power savings, the shortcomings will remain and the gyroscopic effect, and the relatively high losses in the drive, and in the suspension of the flywheel. As a result, the application of this technology has remained oncospecific, and while prospects for change are seen, the development of purely electrical methods of energy storage while there is a better and remarkable power density flywheel storage until needed.
The potential benefit in system reliability is also unlikely to be in demand, reliability and ease now not held in high esteem. The only really promising and the destination for this technology are the buses. For example, Optare Solo with flywheel drive FlyBus or delivery trucks and garbage trucks that make stops every few hundred meters. The FlyBus system or FlyBrid's version of "for all" made by an engineering company Rikardo, in cooperation with Torotrak, developer of the toroidal variable-speed drives of high power.And here again appears on the horizon, a Swedish company. In the version used of the Volvo S60 in 2011, the capacity of the system was 80 kilowatts, weight – 60 kg, and the momentum of the flywheel about 60 thousand revolutions per minute. Judging by these indicators, it is possible to increase the capacity of the system to "sport" values, because the speed of the rotors can be even higher than 100 thousand in a minute, but then again, judging by the lack of a hybrid in the model range of the company, experiments with cars was considered unsuccessful.
Liquid and gas under pressure,a Few more promising is the pneumohydraulic system recovery, the most known to us as the Peugeot Hybrid Air. It is a well-established scheme, while the real machine is not so widely known. It's in the first place... the garbage trucks.
Dozens of cars with the Bosch system and Eaton for over ten years operated in the United States, and their hybrid drive has proved reliable and inexpensive. The essence of this installation is in the power of the motor, which when braking is pumping the working fluid in the large accumulator tube with compressed gas. When accelerating car gas displaces the liquid, the liquid turns the same motor and helps to save fuel. The system has no expensive batteries, and it resource is very large. Power of motors too high, and cost, on the contrary, very low.One catch: the accumulator has a large size and weight, and really his energy is enough for one or two cycles of acceleration and braking, mileage without the inclusion of DVS is only a few kilometers for passenger cars and hundreds of meters for the truck. When used on buses or trucks this system allows to completely abandon the use of traditional brakes, the hydraulic motor can slow the car down to a complete stop. This hydro-pneumatic recuperator even surpasses the electrical system, those with low speed of rotation of the wheels no longer effective.
An additional advantage is the ability to store energy for a long time, hours or days. In contrast to flywheels, which, after ten minutes lose a substantial portion of the stored power. Unfortunately, the ambitious plans of the company Peugeot was perceived cool new shareholders from Chinese Dongfeng and partners in the development of the system from Ford. But judging by the news, it is Chinese Dongfeng trucks can be the next mass media this technology.
The regenerative braking is usedthe Main competitor of these is definitely interesting, but has a number of schema constraints is a classical electric circuit with an electric motor, batteries or supercapacitors.
Conventional electrical braking and recuperation good is the fact that used on the railway about 60 years and worked through. All structural layout with synchronous, asynchronous and commutator motors are well known and calculated. Energy is transferred back to the supply grid, stored in batteries or supercapacitors and can be used over a long time.
The main problem of electric brakes is that they do not combine with combustion engines, and for the efficient use of electricity had to combine the conventional internal combustion engine and all the paraphernalia of electric car batteries and traction motor – in one mechanism. The resulting hybrids are usually just called "hybrids." And despite the complexity and high weight of such a scheme, at the moment it is the only commercially used in the automobile industry and is already very popular.
Hybrids at the moment are the most promising direction of development of the car from the point of view of reducing fuel consumption, and the progress in development of batteries and the development of so-called "rechargeable hybrids", which is essentially intermediate between pure electric cars and hybrids makes them an important element in the evolution of personal transport.
In 1997 came the first production Toyota Prius, which is currently the most popular hybrid car and a trendsetter in its class. In her scheme, decided to use electric motors of low power and inexpensive Nickel metal hydride battery is also low power, and to compensate for these shortcomings gave the car a very complex drivetrain with many modes of operation of the internal combustion engine, electric motor and generator. The success of this scheme heavily influenced the development of similar technologies from other manufacturers. Now the number of car models with hybrid drive has exceeded two dozen.
The main challenge for electric braking on the Autonomous machine remains in the current limit, charging of the battery. She just can't quickly "absorb" all the energy capable of producing electric motors.
The complexity of the capacity of the electrical system recuperation also need to be attributed to the main disadvantages of the scheme. And increase the power of electric motors and converters is given expensive, especially if their weight must be kept to a minimum and efficiency is maximum. But the advantages outweigh the disadvantages, and the number of hybrids multiplied. Gradually increasing the power of the motors, and therefore the brake power of such systems. The batteries on the new projects are mainly Li-ion, able to store much more energy and charging much faster, become more powerful and the motors.
And of course, electrical braking is applied and "pure" electric vehicles, because it can significantly increase their range. And the resource of brake mechanisms it increases. We have seen in practice that regenerative braking on the Tesla with its powerful motors and batteries is much more efficient than the weaker hybrids, allowing you to use mechanical brakes only when the most rapid deceleration. Later the same braking is used will allow to refuse of disc brakes on cars, and I hope this time we will see. published
P. S. And remember, only by changing their consumption — together we change the world! © Join us at Facebook , Vkontakte, Odnoklassniki
Source: www.kolesa.ru/article/tormozit-i-zapasat-sistemy-rekuperacii-v-sovremennyh-mashinah-2015-11-19
To prove the necessity of regenerative braking, i.e. one in which energy machine again accumulated to be used for overclocking and did not need anyone. The effectiveness of the scheme since the 60-ies checked on the railroad. But there are locomotives, and the energy returns immediately to the network. Machines this method is not very suitable due to the absence of most of these motors...
And since cars go on rails, and locations of deceleration and acceleration is also not very hard to predict. Therefore, the method used in some metro stations, the location of stop points on the hills that allows you to accelerate at the expense of the store of potential energy and slow down due to the rise – also not popular. Except that places bus stops have traditionally tried to place on the roller coaster...
The flywheel in a vacuumHistorically, the first recovery system for machines with internal combustion engine system with mechanical accumulation of energy in the rotating flywheel. Such systems were used mainly on construction equipment, where the large rotating part was used as the energy storage and power delivery was via hydraulic or electrical systems.
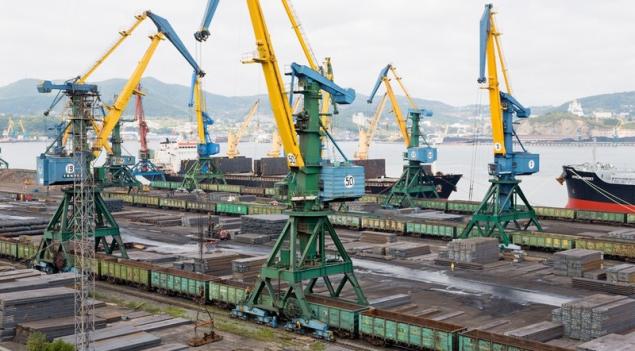
But the scope of this kind of technology has remained narrow in the first place it was large excavators and cranes, often port. To make the system more compact and to install on the car just never occurred to any method of implementation rested on the low energy cost and high price of the device.
At an oil price of less than $ 4 per barrel to introduce something similar on the transport have no one to come to mind, and even after the first oil crises, the stock of modernization of the internal combustion engine is more than the overlap needs to save fuel. Volvo even had a system on the model 260 in 1980, but the power of about 10 kilowatts with a steel flywheel has not met expectations, and the program was phased out.
The leap in technology in the 80-ies helped to create a more efficient system of energy storage at the flywheel, eliminating the root problem – the probability of explosive destruction of the flywheel. Solved the problem simply: did the flywheel threads that the destruction was slow. But placing it in vacuum container and the use of gas bearings is allowed to store energy for a very decent period to several days, although most such systems are designed for a short work cycle, the energy input to the flywheel to her spending a few minutes or even seconds.
So, for example, racing KERS in Formula 1. There are practical examples of its implementation for conventional serial machines, such as Porsche and Ferrari. But in practice is likely to spread, such a system does not get it. Along with such advantages as very high capacity and high power savings, the shortcomings will remain and the gyroscopic effect, and the relatively high losses in the drive, and in the suspension of the flywheel. As a result, the application of this technology has remained oncospecific, and while prospects for change are seen, the development of purely electrical methods of energy storage while there is a better and remarkable power density flywheel storage until needed.
The potential benefit in system reliability is also unlikely to be in demand, reliability and ease now not held in high esteem. The only really promising and the destination for this technology are the buses. For example, Optare Solo with flywheel drive FlyBus or delivery trucks and garbage trucks that make stops every few hundred meters. The FlyBus system or FlyBrid's version of "for all" made by an engineering company Rikardo, in cooperation with Torotrak, developer of the toroidal variable-speed drives of high power.And here again appears on the horizon, a Swedish company. In the version used of the Volvo S60 in 2011, the capacity of the system was 80 kilowatts, weight – 60 kg, and the momentum of the flywheel about 60 thousand revolutions per minute. Judging by these indicators, it is possible to increase the capacity of the system to "sport" values, because the speed of the rotors can be even higher than 100 thousand in a minute, but then again, judging by the lack of a hybrid in the model range of the company, experiments with cars was considered unsuccessful.
Liquid and gas under pressure,a Few more promising is the pneumohydraulic system recovery, the most known to us as the Peugeot Hybrid Air. It is a well-established scheme, while the real machine is not so widely known. It's in the first place... the garbage trucks.
Dozens of cars with the Bosch system and Eaton for over ten years operated in the United States, and their hybrid drive has proved reliable and inexpensive. The essence of this installation is in the power of the motor, which when braking is pumping the working fluid in the large accumulator tube with compressed gas. When accelerating car gas displaces the liquid, the liquid turns the same motor and helps to save fuel. The system has no expensive batteries, and it resource is very large. Power of motors too high, and cost, on the contrary, very low.One catch: the accumulator has a large size and weight, and really his energy is enough for one or two cycles of acceleration and braking, mileage without the inclusion of DVS is only a few kilometers for passenger cars and hundreds of meters for the truck. When used on buses or trucks this system allows to completely abandon the use of traditional brakes, the hydraulic motor can slow the car down to a complete stop. This hydro-pneumatic recuperator even surpasses the electrical system, those with low speed of rotation of the wheels no longer effective.
An additional advantage is the ability to store energy for a long time, hours or days. In contrast to flywheels, which, after ten minutes lose a substantial portion of the stored power. Unfortunately, the ambitious plans of the company Peugeot was perceived cool new shareholders from Chinese Dongfeng and partners in the development of the system from Ford. But judging by the news, it is Chinese Dongfeng trucks can be the next mass media this technology.
The regenerative braking is usedthe Main competitor of these is definitely interesting, but has a number of schema constraints is a classical electric circuit with an electric motor, batteries or supercapacitors.
Conventional electrical braking and recuperation good is the fact that used on the railway about 60 years and worked through. All structural layout with synchronous, asynchronous and commutator motors are well known and calculated. Energy is transferred back to the supply grid, stored in batteries or supercapacitors and can be used over a long time.
The main problem of electric brakes is that they do not combine with combustion engines, and for the efficient use of electricity had to combine the conventional internal combustion engine and all the paraphernalia of electric car batteries and traction motor – in one mechanism. The resulting hybrids are usually just called "hybrids." And despite the complexity and high weight of such a scheme, at the moment it is the only commercially used in the automobile industry and is already very popular.
Hybrids at the moment are the most promising direction of development of the car from the point of view of reducing fuel consumption, and the progress in development of batteries and the development of so-called "rechargeable hybrids", which is essentially intermediate between pure electric cars and hybrids makes them an important element in the evolution of personal transport.
In 1997 came the first production Toyota Prius, which is currently the most popular hybrid car and a trendsetter in its class. In her scheme, decided to use electric motors of low power and inexpensive Nickel metal hydride battery is also low power, and to compensate for these shortcomings gave the car a very complex drivetrain with many modes of operation of the internal combustion engine, electric motor and generator. The success of this scheme heavily influenced the development of similar technologies from other manufacturers. Now the number of car models with hybrid drive has exceeded two dozen.
The main challenge for electric braking on the Autonomous machine remains in the current limit, charging of the battery. She just can't quickly "absorb" all the energy capable of producing electric motors.
The complexity of the capacity of the electrical system recuperation also need to be attributed to the main disadvantages of the scheme. And increase the power of electric motors and converters is given expensive, especially if their weight must be kept to a minimum and efficiency is maximum. But the advantages outweigh the disadvantages, and the number of hybrids multiplied. Gradually increasing the power of the motors, and therefore the brake power of such systems. The batteries on the new projects are mainly Li-ion, able to store much more energy and charging much faster, become more powerful and the motors.
And of course, electrical braking is applied and "pure" electric vehicles, because it can significantly increase their range. And the resource of brake mechanisms it increases. We have seen in practice that regenerative braking on the Tesla with its powerful motors and batteries is much more efficient than the weaker hybrids, allowing you to use mechanical brakes only when the most rapid deceleration. Later the same braking is used will allow to refuse of disc brakes on cars, and I hope this time we will see. published
P. S. And remember, only by changing their consumption — together we change the world! © Join us at Facebook , Vkontakte, Odnoklassniki
Source: www.kolesa.ru/article/tormozit-i-zapasat-sistemy-rekuperacii-v-sovremennyh-mashinah-2015-11-19
30 photos-sketches from the life of naturalist photographers
16 books for the fulfillment of desires in 2016 year