696
The use of hybrid drives in construction machinery
Hybrid designs that use unusual forms of energy use in the future to reduce fuel consumption and increase productivity. Any thing of mixed origin or composition can be called a hybrid. In a narrower sense, the hybrid is one functioning node, which combines heterogeneous technologies.
Under this definition fit and is known for dozens of years hydrostatic and diesel-electric drives, because they are combined mechanical, hydraulic or electrical methods of energy transfer, but in practice, such designs are rarely called hybrid. Common is the use of the term "hybrid" to refer to innovation of modern mixed (heterogeneous) technologies of energy use in heavy machinery and trucks. A more specific definition is given by the Caterpillar: "the Hybrid is the car fitted with equipment able to recover, accumulate and emit energy during work."
However, in accordance with this definition some of the machines are equipped with innovative mixed energy technologies, technically should be excluded from the class "hybrid", for example crawler dozer Cat D7E, because its Electromechanical transmission does not recovers, does not accumulate and does not give the stored energy, as well as several models of front wheel loaders: Cat 966K XE Hybrid John Deere 644K, John Deere 944K, which is recuperated and used for useful work energy that turn into cars into heat and dissipated, but the energy is not accumulated.
In this article, we will use the term "hybrid car" quite broadly, implying that any car that "use a mix of technology transfer (and conversion) of energy not normally used in the technique of this type or size," or, in other words, "unusual uses for this technology and energy technology."
The fundamental principles of hybrid technology
In addition to definitions, it is useful to recall two more concepts commonly encountered when considering hybrid technologies: regenerative braking and motor-generator.
Regenerative braking – in the broadest sense is a physical process of slowing or stopping the motion of the mass, e.g. moving front-end loader, rotating superstructure of an excavator or the descending boom of the excavator, and convert the kinetic energy into another form of energy that can be accumulated or used immediately to perform useful work. The energy of inertia of the mechanical movement is used to actuate the motor running in generator mode or motor operating as a hydraulic pump. When operating construction equipment – excavators, loaders – the processes of acceleration and deceleration are repeated in each cycle every few tens of seconds, and that's a huge potential for saving energy and therefore fuel.
The motor-generator converts electrical energy and can operate as motor and generator. It is connected with the internal combustion engine (ice) in such a way that, working motor, can increase the power of the engine or can help to operate the hydraulic pumps, thus reducing the load on the engine and saving fuel. Working as generator, motor-generator feeds current to the other motors of the machine or charges the accumulating device, such as a battery or a capacitor (a device that is able to quickly accumulate and give large amounts of electricity).
Note also that when working on a hybrid drive noise the machine is much lower than when working on the engine and it is very important for the environment.
Classic cars with hybrid drives Hydraulic excavator Komatsu HB215LC-1 is an example of an electric hybrid design, which is recuperated and accumulated kinetic energy of the braking rotating superstructure. Unlike conventional excavators, which use a hydraulic motor of a turn, the construction used Komatsu motor rotation. If motor rotation is not included and is not powered, it rotates under the action of the inertia of the rotating superstructure of the machine acts as a generator and brakes the movement of the superstructure. The current generated is sent to the storage capacitor via the current Converter. The energy from the capacitor can then be used either to power the electric motor of the turning mechanism, as a subsidiary – to create acceleration when turning, either to power the motor-generator operating as a motor and adds 60 HP to power the engine and help the engine faster to gain momentum, and actuating the hydraulic actuator.
In the hybrid excavator Cat 336E H, the official premiere of which took place at the Bauma exhibition in April 2013, regenerative braking is used otherwise for storing kinetic energy by the hydraulic method. When the operator releases the lever for turning the superstructure and motor rotation ceases to receive power from the hydraulic pump due to the inertia of rotation of the superstructure rotation motor is driven and begins to work as a pump, and add-in slow motion.
In conventional excavators, the oil flow from the hydraulic motor turn (now working as a pump) stops off hydraulic system creates resistance in the circuit, the result stops the motor rotation. During this process, the so-called "hydrostatic braking", the kinetic energy is converted into heat. However, the excavator mod. Cat 336E H, the oil flow is directed through a "Valve energy recovery turn" (Swing Energy Recovery Valve) charging nitrogen accumulator: the oil compresses the gas in the battery. Thus, kinetic energy of inertia rotation is accumulated for beneficial use, but at the expense of resistance to oil flow, it impedes the motor rotation. Allegedly, the fuel consumption of the hybrid model is reduced to 25% compared with the traditional machine with the power drive, and the performance of the hybrid model is not inferior to models with the ice.
Another design, allowing the use of braking energy of the superstructure in turn, is implemented in the excavator ZH200 Hitachi New Generation (released in 2011). In this model, there are two hydraulic motor of rotation of the superstructure (one electrical and one hydraulic), the condenser and the motor-generator.
In the braking process, the rotating of the superstructure rotation motor acts as a generator and charges the capacitor, which then powers the electric motor rotation, helping the motor turn faster to turn the add-in. As stated, the motor-generator is connected to the pumps and regulates the amount of electric power accumulated in the capacitor, that is, the motor-generator can charge the capacitor, and help the engine to operate the hydraulic pumps. The claimed improvement in fuel economy hybrid models – up to 20%.
Hybrid drive for excavator Kobelco SK-80H-2 (in 2010 released on the Japanese market) is different in that it combines elements of electrical and hydraulic systems. The design has a generator which is driven from the internal combustion engine, the generator charges the capacitor and the Nickel-metal-hybrid battery via the DC / DC Converter. Accumulated energy is channeled through an inverter that converts current to power four electric motors. Three of them result in movement of the pump, feeding hydraulic circuit boom, stick/ dipper and movement. The fourth electric motor directly operates the turning mechanism of the superstructure and, when functioning as a generator (during braking pivoting of the add-in) that charges the capacitor and the battery.
In addition, Kobelco construction uses a pair of electric motor/ hydraulic pump, which drives the boom through a separate hydraulic circuit, and, when the boom is lowered, the kinetic energy of deceleration of the movement of the boom is used for oil feed circuit of the boom to drive the hydraulic pump, which in this case works as a motor. Hydraulic pump/ motor in turn drives the connected electric motor, which here acts as a generator. The generated electric current (as current from the electric motor turn the add-in) is supplied to the battery and the capacitor. Allegedly, in some cases, the whole machine can run only on electricity with the engine off, in result, saves a significant amount of fuel and reduces noise, which is especially important when working in areas with dense residential development.
The main component of the parallel hybrid drive loader L220F Hybrid (2008) is a "combined starter-alternator" (Integrated Starter Generator ISG) located between the engine and the transmission and associated with a modern battery that has many times more capacity compared to conventional lead-acid battery.
Up to 40% of the time the engine wheel loader is idling. The hybrid drive allows you to turn off the engine when it is not needed, and make and quickly output to the operating speed via the starter-generator is receiving power from the battery. Starter-generator adds to the power of the internal combustion engine to 67 HP, the battery is then replenished by regenerative braking of the loader. Fuel efficiency of the hybrid loader is 10% compared to classical models.
In drive mod. John Deere 644К Hybrid motor-generator driven by the internal combustion engine used to power a single electric motor through a DC / DC Converter with liquid cooling. Torque from the motor is transmitted to the automatic transmission of simplified construction (without torque Converter and a reversible transmission, because the electric motor itself can carry out the reverse – rotate in the opposite direction) and normal to the axis. In the car uses regenerative braking when the braking time of the mechanical transmission rotates the electric motor, which operates in the generator mode, the energy is accumulated and can be used with motor-generator "to drive the hydraulic and fuel economy", as stated in the documents of the company. For storage of recovered energy in construction is also used braking resistor liquid-cooled. The company already takes orders for the supply of these machines.
In an electric hybrid drive Eaton, used commercial trucks, motor-generator located between the clutch and the transmission. When braking energy is recuperated, the inertia of the mass of the truck rotates the mechanical part of the transmission, and the motor-generator operates in a generator mode, energy is stored in lithium-ion batteries. Then, the electronic control system utilizes stored energy to drive the motor-generator operating in motor mode, which in turn either increases the torque of the internal combustion engine, either directly drives the truck (moving off) without the involvement of DVS.
In all the above described machines, the drive recovers, stores and uses the braking energy, that's why we call them classic.
Electromechanical design of hybrid Diesel-electric drive used in a great quarry equipment for quite some time. A new breakthrough has been the development of drives of this type with the advent of electronic control systems.
In the frontal wheel loaders LeTourneau tens of years used diesel-electric drive. The engine drives the alternator, which is converted to DC using silicon of triode thyristor and is supplied to the power four electric motors on the wheels. When braking these huge machines (operating weight mod. LeTourneau-2350 reaches 266,6 t) the normal brakes turn kinetic energy into heat through friction. However, in models of the second generation introduced "Hybrid drive technology with a dial-up rocket motor" (Switched Reluctance Hybrid Technology Propulsion System) with regenerative braking system that converts up to 90% of the huge kinetic energy into electric current by means of electrical motors in the construction of which no brushes and uses a bipolar transistor with insulated gate and with liquid cooling. This is a very simple and rugged design, almost maintenance-free.
According to the manufacturer, the regenerative braking system allows you to stop the car without using the normal brakes, thereby increasing their life. It is argued that the hybrid system allows to save up to 45% of fuel compared to previous generation models. Description of how the accumulated energy is used for useful work, is not given. Says only that the wheel motors can rotate the wheel back and forth to work in the modes of motor and generator, they are smaller, saving power, equal to the electric motors of the first generation.
On a similar principle built drive dump truck mod. Cat 795F AC (2010): internal combustion engine drives the generator, and a motor-wheel can work in generator mode to recover braking energy.
Diesel-electric drive, the underlying hybrid loaders LeTourneau second generation is not new. But the diesel-electric drive of front wheel loaders of a smaller size, and the John Deere 944K electric drive dozer the Cat D7E – design completely original and innovative.
Actuator mod. John Deere 944K has the design of similar hybrid trucks from LeTourneau, only it uses two motor-generator driven by the internal combustion engine, which in turn provide power supply for electrical drives, four motor wheels. In mod. 944К recuperated kinetic braking energy of the machine: the motors of the wheels are in generators. Then allegedly "recovered energy back to the crankshaft of the internal combustion engine, helping the engine cope with the load and reducing fuel consumption, also this energy is used in other machine systems".
In an Electromechanical drive dozer the Cat D7E, in contrast to the classical "hybrid" drive, there is no energy recovery. Raise the cockpit of a 27-ton bulldozer Cat D7E (launched on the market in 2009) – and immediately see components that are not typical for tracked vehicles, such as a generator, which is driven from the internal combustion engine produces 235 HP, power and propulsion instead of a conventional torque Converter automatic transmission. The generator produces AC voltage of 480 V, which is then converted or constant current, or a frequency-controlled alternating current, the latter is applied to power two large electric motors, mechanically connected to the part of the mover, which provides the usual differential side gear Caterpillar. DC voltage 340 In the feed liquid pump and air conditioning machines. The company cites this figure: the fuel efficiency of hybrid models increased to 30% in comparison with a car with a standard drive for the same power.
Hydraulic hybrids was Developed by company Eaton hybrid "Auxiliary hydraulic actuator for moving off" (Hydraulic Launch Assist) includes a conventional power drive of the truck is connected through the gearbox with a hydraulic pump/ motor. When braking the kinetic energy of the car's mass is converted into hydraulic energy due to rotation of the hydraulic pump/ motor operating as a pump that pumps hydraulic oil into the high pressure accumulator. As stated in the description, it accumulates about 70% of the available energy. Hydraulically stored energy (without the aid of ice) can be used to disperse the truck until you run out of battery power, thereby reducing fuel consumption, or can be used to increase the torque of the internal combustion engine to increase the rate of acceleration of the truck.
In the design of the drive Run Wise 3-Gear System Parker engine truck is used to drive the hydraulic pump/ motor, which first charges the accumulator high pressure. The battery then feeds the hydraulic motors of the hydrostatic drive of the wheels of the truck. On the "bottom rung" of the hydrostatic drive, the truck speeds up to 40 km/h, and the "top" up to 70 km/h the internal combustion engine, composed of the hydrostatic drive works on rpm just above idle. At speeds above 70 km/h dump truck is provided directly from the internal combustion engine via a mechanical transmission. When the truck makes frequent stops, pumps/ motors, hydraulic drive working mode of the pumps, providing regenerative braking and charging the accumulator.
In the design of hybrid drive 24-ton wheel front loader Cat 966K XE features the mechanical force components (torque Converter) and the components of the hydrostatic drive a hydraulic motor/ pump, two flow capacities are connected to a planetary gear that provide "maximum efficiency of transmission" as it is written in the documentation of Caterpillar. The change speed transmission is stepless. It seems that the drive is able to recover braking energy by using the hydraulic actuator, this energy is then used to create a flow in the hydraulic system, as claimed, "in the contours of the working equipment or the drive of the cooling fan, whereby the internal combustion engine (290 HP) operates at a lower speed." Fuel savings of up to 25% compared to previous models. Mod. HEH 966К released on the market in the first quarter of 2013.
In the sector of mining equipment, Caterpillar is developing hybrid drives for mining hydraulic excavator Cat 6120H FS electric rope shovel Cat 7495, which recuperated braking energy by turning the add-in and lowering the boom.
Company Joy Global, the owner of the company LeTourneau, has developed a diesel-electric rope excavator P&H 2650, which, according to the company, hybrid technology borrowed from the front-end loader LeTourneau. published
P. S. And remember, just changing your mind — together we change the world! ©
Source: www.os1.ru/article/technology/2013_11_A_2013_11_18-17_15_37/
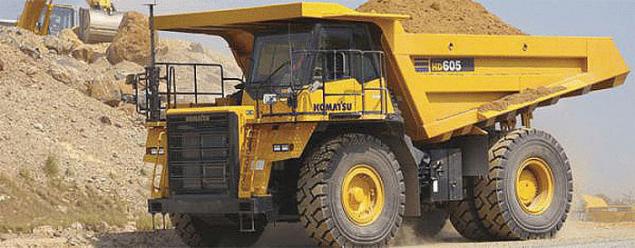
Under this definition fit and is known for dozens of years hydrostatic and diesel-electric drives, because they are combined mechanical, hydraulic or electrical methods of energy transfer, but in practice, such designs are rarely called hybrid. Common is the use of the term "hybrid" to refer to innovation of modern mixed (heterogeneous) technologies of energy use in heavy machinery and trucks. A more specific definition is given by the Caterpillar: "the Hybrid is the car fitted with equipment able to recover, accumulate and emit energy during work."
However, in accordance with this definition some of the machines are equipped with innovative mixed energy technologies, technically should be excluded from the class "hybrid", for example crawler dozer Cat D7E, because its Electromechanical transmission does not recovers, does not accumulate and does not give the stored energy, as well as several models of front wheel loaders: Cat 966K XE Hybrid John Deere 644K, John Deere 944K, which is recuperated and used for useful work energy that turn into cars into heat and dissipated, but the energy is not accumulated.
In this article, we will use the term "hybrid car" quite broadly, implying that any car that "use a mix of technology transfer (and conversion) of energy not normally used in the technique of this type or size," or, in other words, "unusual uses for this technology and energy technology."
The fundamental principles of hybrid technology
In addition to definitions, it is useful to recall two more concepts commonly encountered when considering hybrid technologies: regenerative braking and motor-generator.
Regenerative braking – in the broadest sense is a physical process of slowing or stopping the motion of the mass, e.g. moving front-end loader, rotating superstructure of an excavator or the descending boom of the excavator, and convert the kinetic energy into another form of energy that can be accumulated or used immediately to perform useful work. The energy of inertia of the mechanical movement is used to actuate the motor running in generator mode or motor operating as a hydraulic pump. When operating construction equipment – excavators, loaders – the processes of acceleration and deceleration are repeated in each cycle every few tens of seconds, and that's a huge potential for saving energy and therefore fuel.
The motor-generator converts electrical energy and can operate as motor and generator. It is connected with the internal combustion engine (ice) in such a way that, working motor, can increase the power of the engine or can help to operate the hydraulic pumps, thus reducing the load on the engine and saving fuel. Working as generator, motor-generator feeds current to the other motors of the machine or charges the accumulating device, such as a battery or a capacitor (a device that is able to quickly accumulate and give large amounts of electricity).
Note also that when working on a hybrid drive noise the machine is much lower than when working on the engine and it is very important for the environment.
Classic cars with hybrid drives Hydraulic excavator Komatsu HB215LC-1 is an example of an electric hybrid design, which is recuperated and accumulated kinetic energy of the braking rotating superstructure. Unlike conventional excavators, which use a hydraulic motor of a turn, the construction used Komatsu motor rotation. If motor rotation is not included and is not powered, it rotates under the action of the inertia of the rotating superstructure of the machine acts as a generator and brakes the movement of the superstructure. The current generated is sent to the storage capacitor via the current Converter. The energy from the capacitor can then be used either to power the electric motor of the turning mechanism, as a subsidiary – to create acceleration when turning, either to power the motor-generator operating as a motor and adds 60 HP to power the engine and help the engine faster to gain momentum, and actuating the hydraulic actuator.
In the hybrid excavator Cat 336E H, the official premiere of which took place at the Bauma exhibition in April 2013, regenerative braking is used otherwise for storing kinetic energy by the hydraulic method. When the operator releases the lever for turning the superstructure and motor rotation ceases to receive power from the hydraulic pump due to the inertia of rotation of the superstructure rotation motor is driven and begins to work as a pump, and add-in slow motion.
In conventional excavators, the oil flow from the hydraulic motor turn (now working as a pump) stops off hydraulic system creates resistance in the circuit, the result stops the motor rotation. During this process, the so-called "hydrostatic braking", the kinetic energy is converted into heat. However, the excavator mod. Cat 336E H, the oil flow is directed through a "Valve energy recovery turn" (Swing Energy Recovery Valve) charging nitrogen accumulator: the oil compresses the gas in the battery. Thus, kinetic energy of inertia rotation is accumulated for beneficial use, but at the expense of resistance to oil flow, it impedes the motor rotation. Allegedly, the fuel consumption of the hybrid model is reduced to 25% compared with the traditional machine with the power drive, and the performance of the hybrid model is not inferior to models with the ice.
Another design, allowing the use of braking energy of the superstructure in turn, is implemented in the excavator ZH200 Hitachi New Generation (released in 2011). In this model, there are two hydraulic motor of rotation of the superstructure (one electrical and one hydraulic), the condenser and the motor-generator.
In the braking process, the rotating of the superstructure rotation motor acts as a generator and charges the capacitor, which then powers the electric motor rotation, helping the motor turn faster to turn the add-in. As stated, the motor-generator is connected to the pumps and regulates the amount of electric power accumulated in the capacitor, that is, the motor-generator can charge the capacitor, and help the engine to operate the hydraulic pumps. The claimed improvement in fuel economy hybrid models – up to 20%.
Hybrid drive for excavator Kobelco SK-80H-2 (in 2010 released on the Japanese market) is different in that it combines elements of electrical and hydraulic systems. The design has a generator which is driven from the internal combustion engine, the generator charges the capacitor and the Nickel-metal-hybrid battery via the DC / DC Converter. Accumulated energy is channeled through an inverter that converts current to power four electric motors. Three of them result in movement of the pump, feeding hydraulic circuit boom, stick/ dipper and movement. The fourth electric motor directly operates the turning mechanism of the superstructure and, when functioning as a generator (during braking pivoting of the add-in) that charges the capacitor and the battery.
In addition, Kobelco construction uses a pair of electric motor/ hydraulic pump, which drives the boom through a separate hydraulic circuit, and, when the boom is lowered, the kinetic energy of deceleration of the movement of the boom is used for oil feed circuit of the boom to drive the hydraulic pump, which in this case works as a motor. Hydraulic pump/ motor in turn drives the connected electric motor, which here acts as a generator. The generated electric current (as current from the electric motor turn the add-in) is supplied to the battery and the capacitor. Allegedly, in some cases, the whole machine can run only on electricity with the engine off, in result, saves a significant amount of fuel and reduces noise, which is especially important when working in areas with dense residential development.
The main component of the parallel hybrid drive loader L220F Hybrid (2008) is a "combined starter-alternator" (Integrated Starter Generator ISG) located between the engine and the transmission and associated with a modern battery that has many times more capacity compared to conventional lead-acid battery.
Up to 40% of the time the engine wheel loader is idling. The hybrid drive allows you to turn off the engine when it is not needed, and make and quickly output to the operating speed via the starter-generator is receiving power from the battery. Starter-generator adds to the power of the internal combustion engine to 67 HP, the battery is then replenished by regenerative braking of the loader. Fuel efficiency of the hybrid loader is 10% compared to classical models.
In drive mod. John Deere 644К Hybrid motor-generator driven by the internal combustion engine used to power a single electric motor through a DC / DC Converter with liquid cooling. Torque from the motor is transmitted to the automatic transmission of simplified construction (without torque Converter and a reversible transmission, because the electric motor itself can carry out the reverse – rotate in the opposite direction) and normal to the axis. In the car uses regenerative braking when the braking time of the mechanical transmission rotates the electric motor, which operates in the generator mode, the energy is accumulated and can be used with motor-generator "to drive the hydraulic and fuel economy", as stated in the documents of the company. For storage of recovered energy in construction is also used braking resistor liquid-cooled. The company already takes orders for the supply of these machines.
In an electric hybrid drive Eaton, used commercial trucks, motor-generator located between the clutch and the transmission. When braking energy is recuperated, the inertia of the mass of the truck rotates the mechanical part of the transmission, and the motor-generator operates in a generator mode, energy is stored in lithium-ion batteries. Then, the electronic control system utilizes stored energy to drive the motor-generator operating in motor mode, which in turn either increases the torque of the internal combustion engine, either directly drives the truck (moving off) without the involvement of DVS.
In all the above described machines, the drive recovers, stores and uses the braking energy, that's why we call them classic.
Electromechanical design of hybrid Diesel-electric drive used in a great quarry equipment for quite some time. A new breakthrough has been the development of drives of this type with the advent of electronic control systems.
In the frontal wheel loaders LeTourneau tens of years used diesel-electric drive. The engine drives the alternator, which is converted to DC using silicon of triode thyristor and is supplied to the power four electric motors on the wheels. When braking these huge machines (operating weight mod. LeTourneau-2350 reaches 266,6 t) the normal brakes turn kinetic energy into heat through friction. However, in models of the second generation introduced "Hybrid drive technology with a dial-up rocket motor" (Switched Reluctance Hybrid Technology Propulsion System) with regenerative braking system that converts up to 90% of the huge kinetic energy into electric current by means of electrical motors in the construction of which no brushes and uses a bipolar transistor with insulated gate and with liquid cooling. This is a very simple and rugged design, almost maintenance-free.
According to the manufacturer, the regenerative braking system allows you to stop the car without using the normal brakes, thereby increasing their life. It is argued that the hybrid system allows to save up to 45% of fuel compared to previous generation models. Description of how the accumulated energy is used for useful work, is not given. Says only that the wheel motors can rotate the wheel back and forth to work in the modes of motor and generator, they are smaller, saving power, equal to the electric motors of the first generation.
On a similar principle built drive dump truck mod. Cat 795F AC (2010): internal combustion engine drives the generator, and a motor-wheel can work in generator mode to recover braking energy.
Diesel-electric drive, the underlying hybrid loaders LeTourneau second generation is not new. But the diesel-electric drive of front wheel loaders of a smaller size, and the John Deere 944K electric drive dozer the Cat D7E – design completely original and innovative.
Actuator mod. John Deere 944K has the design of similar hybrid trucks from LeTourneau, only it uses two motor-generator driven by the internal combustion engine, which in turn provide power supply for electrical drives, four motor wheels. In mod. 944К recuperated kinetic braking energy of the machine: the motors of the wheels are in generators. Then allegedly "recovered energy back to the crankshaft of the internal combustion engine, helping the engine cope with the load and reducing fuel consumption, also this energy is used in other machine systems".
In an Electromechanical drive dozer the Cat D7E, in contrast to the classical "hybrid" drive, there is no energy recovery. Raise the cockpit of a 27-ton bulldozer Cat D7E (launched on the market in 2009) – and immediately see components that are not typical for tracked vehicles, such as a generator, which is driven from the internal combustion engine produces 235 HP, power and propulsion instead of a conventional torque Converter automatic transmission. The generator produces AC voltage of 480 V, which is then converted or constant current, or a frequency-controlled alternating current, the latter is applied to power two large electric motors, mechanically connected to the part of the mover, which provides the usual differential side gear Caterpillar. DC voltage 340 In the feed liquid pump and air conditioning machines. The company cites this figure: the fuel efficiency of hybrid models increased to 30% in comparison with a car with a standard drive for the same power.
Hydraulic hybrids was Developed by company Eaton hybrid "Auxiliary hydraulic actuator for moving off" (Hydraulic Launch Assist) includes a conventional power drive of the truck is connected through the gearbox with a hydraulic pump/ motor. When braking the kinetic energy of the car's mass is converted into hydraulic energy due to rotation of the hydraulic pump/ motor operating as a pump that pumps hydraulic oil into the high pressure accumulator. As stated in the description, it accumulates about 70% of the available energy. Hydraulically stored energy (without the aid of ice) can be used to disperse the truck until you run out of battery power, thereby reducing fuel consumption, or can be used to increase the torque of the internal combustion engine to increase the rate of acceleration of the truck.
In the design of the drive Run Wise 3-Gear System Parker engine truck is used to drive the hydraulic pump/ motor, which first charges the accumulator high pressure. The battery then feeds the hydraulic motors of the hydrostatic drive of the wheels of the truck. On the "bottom rung" of the hydrostatic drive, the truck speeds up to 40 km/h, and the "top" up to 70 km/h the internal combustion engine, composed of the hydrostatic drive works on rpm just above idle. At speeds above 70 km/h dump truck is provided directly from the internal combustion engine via a mechanical transmission. When the truck makes frequent stops, pumps/ motors, hydraulic drive working mode of the pumps, providing regenerative braking and charging the accumulator.
In the design of hybrid drive 24-ton wheel front loader Cat 966K XE features the mechanical force components (torque Converter) and the components of the hydrostatic drive a hydraulic motor/ pump, two flow capacities are connected to a planetary gear that provide "maximum efficiency of transmission" as it is written in the documentation of Caterpillar. The change speed transmission is stepless. It seems that the drive is able to recover braking energy by using the hydraulic actuator, this energy is then used to create a flow in the hydraulic system, as claimed, "in the contours of the working equipment or the drive of the cooling fan, whereby the internal combustion engine (290 HP) operates at a lower speed." Fuel savings of up to 25% compared to previous models. Mod. HEH 966К released on the market in the first quarter of 2013.
In the sector of mining equipment, Caterpillar is developing hybrid drives for mining hydraulic excavator Cat 6120H FS electric rope shovel Cat 7495, which recuperated braking energy by turning the add-in and lowering the boom.
Company Joy Global, the owner of the company LeTourneau, has developed a diesel-electric rope excavator P&H 2650, which, according to the company, hybrid technology borrowed from the front-end loader LeTourneau. published
P. S. And remember, just changing your mind — together we change the world! ©
Source: www.os1.ru/article/technology/2013_11_A_2013_11_18-17_15_37/
In Denmark one day with the help of wind generated electricity more than is required country
What is it like 14 years living alone on the island away from the mainland (10 photos)