1027
As we did a robot
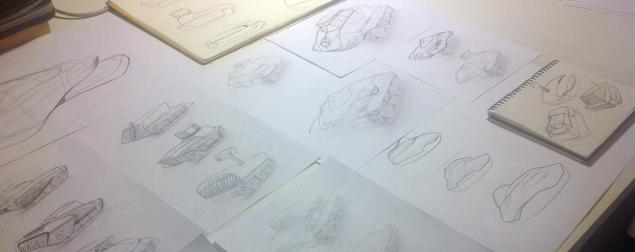
Dear friends! I want to show off a little to share our experience in developing the robot body-guard on the crawler.
Large images under the cut.
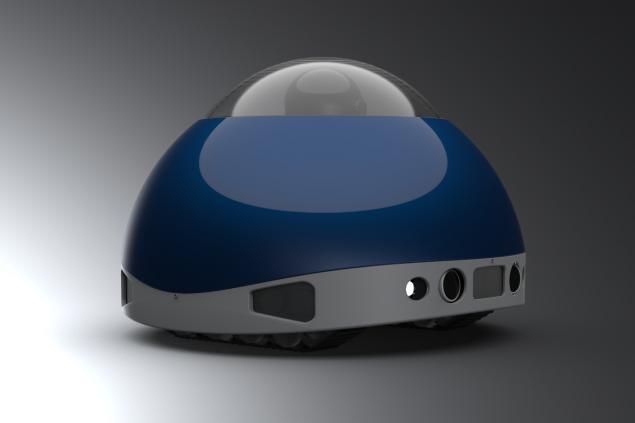
In matters of security, there should be places where it is impossible to look. Set the camera on every corner is not always possible (and not always "afford"), and to avoid "blind spots", even when seemingly full coverage is not always possible. And the human factor and does not worth mentioning.
Therefore, to patrol objects abound difficult terrain and lots of potential blind spots - vacation homes, shopping and business centers, warehouses - are increasingly offering special use robot guards.
So, equipped with motion sensors, temperature, smoke, etc., as well as a video camera robot can be controlled from your smartphone, and when an alarm is triggered - first check what is really dangerous happened at the facility, and even then make a decision - whether to cause a rapid response.
Task to develop housing and mount chassis for this robot on the basis of available electronic components and chassis purchased by large-scale radio-controlled tank and was put in front of us - the industrial design studio FORMA a >. General concept and development of electronic components involved in the company X-Turion.
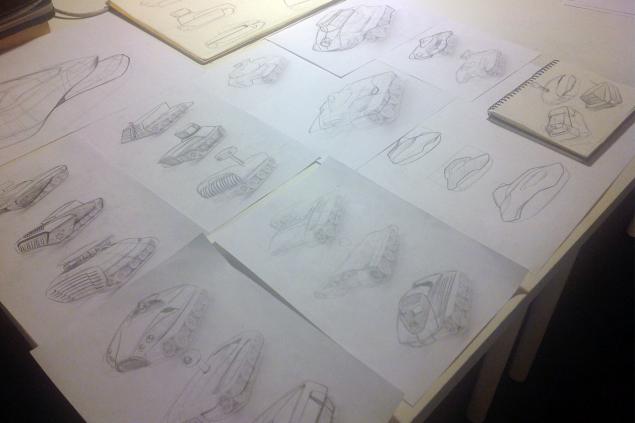
Work began with the collection of general information on Robotics similar class. Identified stylistic trends, selected materials and manufacturing techniques, and then began preliminary search. Of the proposed more than three dozen options was chosen one direction - friendly and simple form, the most distant from the tank style, which became the basis for further development. The result - a very simple appearance, practical and inconspicuous housing securely hides a sophisticated electronics and mechanics. Compartment for additional equipment behind resolved in the style of classic zadnemotornyh "Fiat". The cap for the main camera is made of transparent polycarbonate. The shape of the robot and used for its manufacture materials must ensure that the furniture or expensive equipment will not be damaged by them, and the little children who have to like this robot because it reminds favorite cartoon characters, can neither hurt about it yourself, or easily "hurt" it.
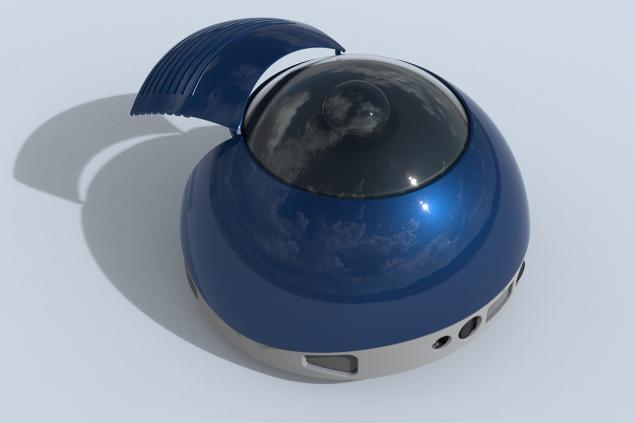
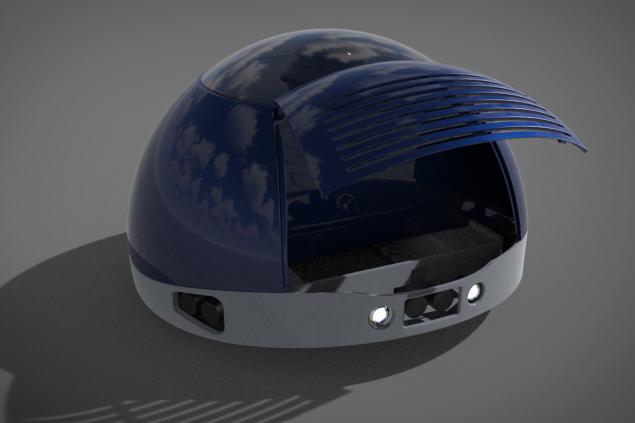
Dimensions of the first embodiment determines the size provided by the customer chassis, developed on the basis of three-dimensional model of the prototype is already too long - 500 mm in diameter, to prototype it was expensive. Therefore, the studio staff made themselves on the basis of body fitness ball with a polyester resin and reinforcing mesh. Transparent cap was molded Plexiglas. Prototype development of conceptual and information retrieval to the final finishing of the layout took 5 months. Chassis layout is shown at CeBIT 2014 in Hanover.
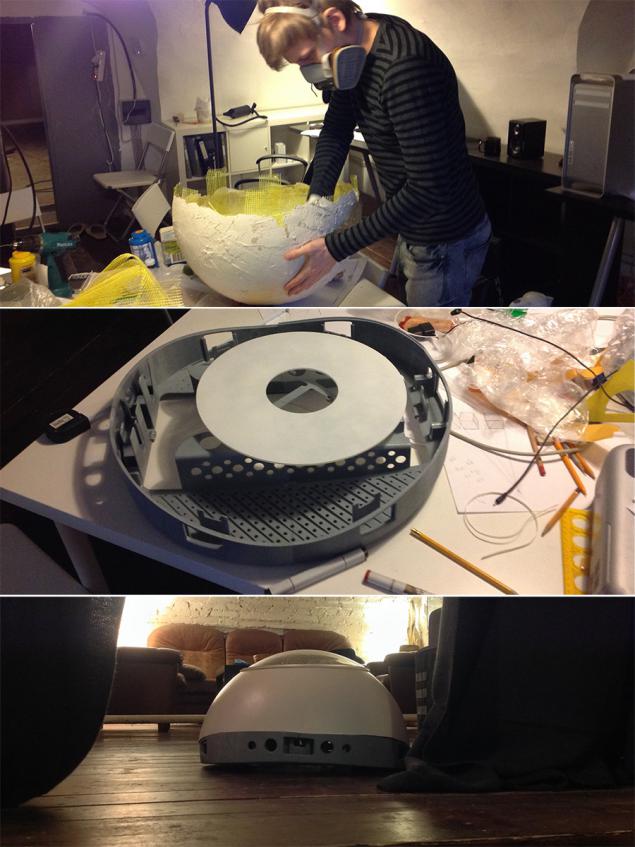
Testing the first prototype revealed a number of shortcomings that have been eliminated in the course of further work. The diameter of the robot decreased to 350 mm, now it is appropriate to look not only at large sites, but also at home.
The basis of the robot has laid down a new chassis that acts as a load-bearing structure, where fixed motor, battery pack, card, wireless module. Also mounted on the chassis of the lower housing part (manufacturing technology - injection molding, is designed to form a two-component mold). On the resulting assembly installs all necessary sensors and a stereo pair. Patterned rubber spacers allow to install different versions of the main chamber.
Actually, the chassis and the lower part of the body:
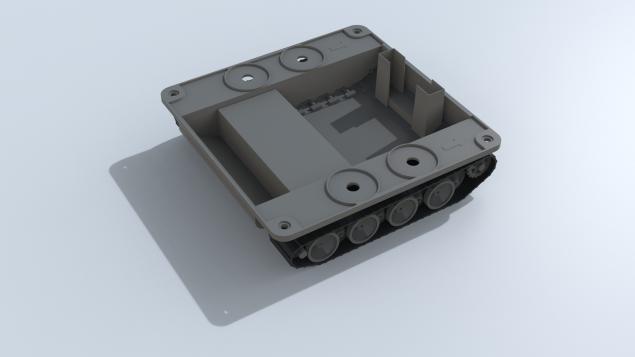
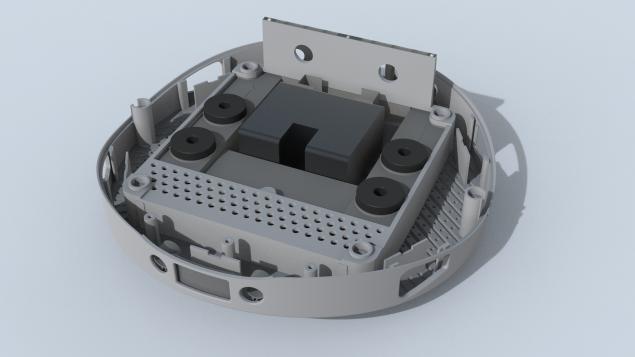
The next step is added to the camera stand and plate that separates the bay for additional equipment. Metal elements are made of stainless steel with thickness 0, 75 mm, laser cut and bent into the desired configuration.
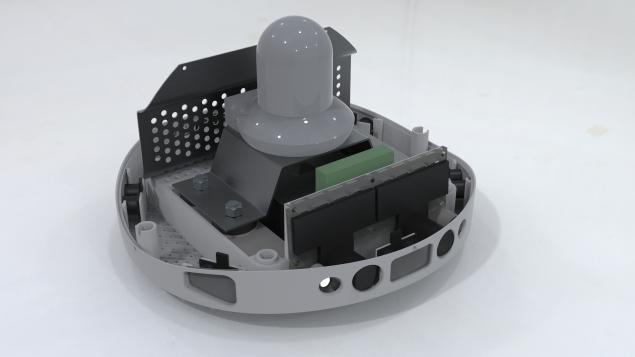
Painting in a wide range of colors available in both mass and only the front surface. In addition, the upper edge is painted matt black to minimize glare. The plastic cap is glued over the camera in a groove in the upper part of the housing. Two assemblies are attached to each other by 6 main rotor and four additional.
Thus, in less than a couple of months we have been designed from the ground up design and design documentation fully ready for mass production of a practical and efficient robot.
Graphic materials taken from the site studio FORMA .
Source: geektimes.ru/post/248942/