As the robot DRC-HUBO from South Korea won the DARPA Robotics Challenge
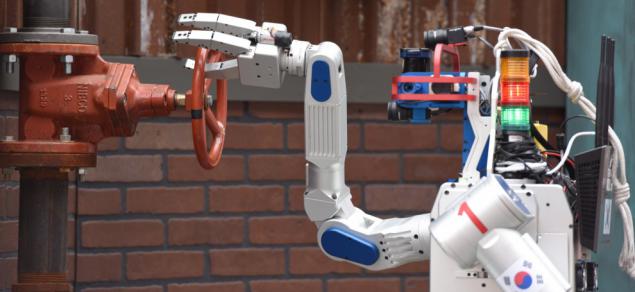
On Saturday, the team Korean leading scientific and technological institute (KAIST) of South Korea won the DARPA Robotics Challenge (DRC) in Pomona (CA), when their robot adaptable Humanoid DRC-HUBO , победил 22 other robots from five different countries and won the top prize of $ 2 million.
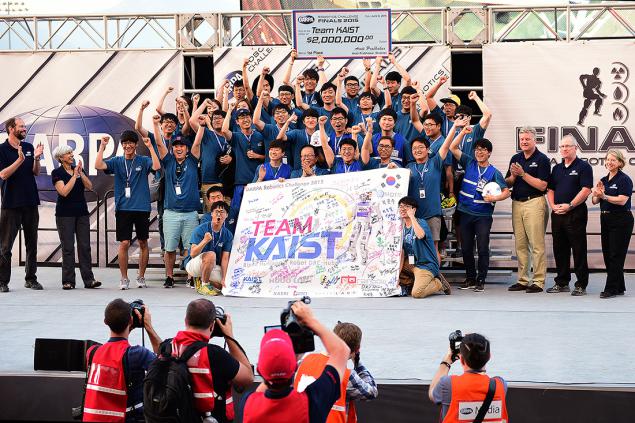
The ability to transform itself from a two-legged walking robot in the car on wheels has been instrumental in getting the award. Many robots have lost balance and fell to the ground, opening the door or by working with a drill. But do not DRC-HUBO
Moving on two legs [robot] is still not stable - said Jung Ho Oh, a professor of mechanical engineering at the Korea's leading scientific and technological institute, head of the team KAIST. - If one thing went wrong - the result can be catastrophic.
Blockquote>
![]()
He said that the humanoid robot has advantages when working in the company of people, but he wanted to develop a design that minimizes the risk of falls, "I thought about many things, and it was very simple - the wheel on your lap".
< DRC-HUBO can change your posture, standing on two legs, walk, reach for objects, which are high, and the move to a more stable position on your lap.
< DARPA have decided to organize DRC after the incident in Fukushima in Japan, hoping to advance in the field of robotics. At соревнование DRC Finals were invited to the team, developing semi-autonomous robots and human operators have to work together on disaster simulation environment. Robots by universities and companies to compete very different in size and shape, some of them are robots with legs, wheels, as well as hybrids.
![]()
< DRC-HUBO was the winner because it was able to perform all eight tasks without errors in the shortest time (44 min. 28 sec). Other teams also performed well, but because of delays in their robots lost time. Among the best - team Tartan Rescue , its CHIMP - a robot with legs and Track, which was able to return to the job after the fall; < Momaro from the team the University of Bonn - simple and elegant machine on wheels, with a rotating head with two hands; < RoboSimian from the NASA Jet Propulsion Laboratory, with four legs and movements napominayuschimim yoga; < ATLAS Teams from the IHMC - a large electric humanoid robot developed by Boston Dynamics
![]()
DRC-HUBO performs the task of closing the valve. Please note that the upper part of his body is rotated 180 degrees. I>
Flexibility - is the most important, - said the manager of DARPA and organizer DRC Jill Pratt meeting with journalists, commenting on the design of robots. - The robot, which is able to change the configuration from using the feet to the use of the wheels, can have a more complicated design and more weight, but it will give you this flexibility.
Blockquote>
Professor O is an internationally recognized expert on the humanoid robot. He and his students from the KAIST in Daejeon (South Korea) to improve HUBO its platform for several generations. Below is a video that is already several years: when the professor makes Personal HUBO 2:
To DRC Finals he decided to significantly modify the robot to prepare it for possible jobs. The master class after the event about the professor said that DRC-HUBO "is no different, it's just a humanoid robot." But in fact his team KAIST carefully consider every detail. He estimated the cost of each robot at approximately $ 500,000 and $ 1 million. The following are the main features that have helped DRC-HUBO to cope with the tasks of:
< 1. Wheels on the knees: DRC-HUBO has wheels on both knees and feet on the rollers. The wheels allow the robot to move quickly and steadily. Moving along the ground, it uses optical sensors on the legs to measure distance using optical flow.
![]()
< 2. Powerful engines: as well as SCHAFT - a robot, who won the preliminary competition DARPA and приобретенный by Google , DRC-HUBO is a very powerful engines (they had 33 with 31 degrees of free movement). Due to the specialized engine and cooling (fans and blades), the robot can use a voltage of 3-4 times higher than indicated in the specifications of the engine, with a maximum rate of 30 amperes in some cases.
< 3. Compatibility: team wanted to make a robot compliant force-torque sensors without the use of conventional and automatic regulator (feared that it would lead to instability). Therefore, a special amplifier is transferred to the problem of compatibility of the engine driver.
![]()
< 4. Rotary Torso: DRC-HUBO Mauger rotate the upper part of his body 180 degrees. This means that the knees of the robot can be deployed to one side and watch it at the same time capable of the opposite (you try it!). This ability not only works when he is, but when he is on his knees. The robot used this opportunity in several tasks when needed: to drive the vehicle, punched the wall, move through the rubble and up the stairs.
< 5. Long arms: team members KAIST have realized that the hand HUBO 2 is too short for some tasks, so they made a long, swiveling 7 degrees. They also hid all the cables inside, so they do not catch on surrounding objects. Each hand can hold the weight up to 15 kg, and has an "adaptable gripper", which may miss the hard and soft items.
![]()
< 6. Simplified sensing: Instead of filling your head sensors, stereoscopic cameras and lidar, which constantly scan their environment (the technology uses a robot ATLAS, for example), DRC-HUBO is a simplified vision system; Operators rely on the normal cell most of the time, and lidar attached to the actuator, scans the surrounding environment only when necessary. In fact, the robot is not the head - "only the eyes," said one of the students KAIST
< 7. Power: when the engine requires more power, the main power supply system may not be able to provide enough energy to important components of the machine. To avoid this, the team used a super capacitor, which supplies energy to computers, transmission channels, and some sensors and gyroscopes, even if the main power system fails.
< 8. Special software: command uses the real-time OS for Linux Xenomai and a special motion control framework, which is called PODO (the development of KAIST ). It also involves modeling environment Gazebo. The team has developed their software with a focus on low bandwidth and unstable connection between the operators and the robot.
![]()
Now let's take a closer look DRC-HUBO and the way he held eight jobs that brought victory to the team from the KAIST (if you want to view all full, this can be done by link, accelerated version here):
1. Setting on driving.
Teams are allowed to make modifications to the vehicle Polaris , their robots have been easier to cars in and out of it. Team KAIST installed metal device with two levers at the bottom of the car; When DRC-HUBO by clicking on one of the levers, cable system worked so that the second lever is pressed on the accelerator. With his left hand holding on to a robot car, and the right to manage the wheel. He performed this task very fast (the process took a little more than a minute), and, unlike the other teams did not stop passing obstacles.
2. Setting to get out of the vehicle.
It was one of the most difficult tasks. In preparation for it, Professor Oh, he told us, he came out of the car several times to understand what part of the body movement and uses it. He concluded that it would take a "dynamic approach". His team has programmed DRC-HUBO so that he raised his hands and held on to the machine frame. The robot uses 100 newtons of thrust for each hand. When the body of the robot arm is raised, it largely falls out of the car, although the movement is controlled (thanks to the "dynamic approach"). Pay attention to his excellent maneuver to get out of the car at around 1:00!
About Professor said that while developing this movement burned a few engines, but the problem was solved by using the most powerful, specially manufactured engines. At the moment, the robot can leave the car in less than 4 minutes, and when he was on earth, he kneels down and leaves.
3. Setting the door.
Unlike other robots, which were to be (and to balance on two legs), to perform this task, DRC-HUBO could stand on his knees, turning the door handle. He deftly uses his other hand to hold the door open until the knob rotates. In less than 2 minutes, he passed through the doorway.
4. Setting a valve.
Note that at the beginning of the video lidar moves up and down to allow operators to scan the area in front of the robot. Then, when DRC-HUBO to close the valve, he turns his upper body 180 degrees. Pay attention to his movements on the 0:20, because you may not notice (the shooting angle does not show the lower part of the body of the robot, unfortunately). In this position, still on his knees, the robot can raise the body so that it is easier to cope with the bolt (why stand if it is not needed?). The robot scans the area using lidar, determines the position and after 3 minutes the task performs. Note that needed only one turn, but DRC-HUBO made two full turns! At 2:01 you can see how the robot "returns" of SARS in the normal position.
5. Specify the wall.
It was a difficult task for most teams, because the robot had to keep a drill and press the button incl. / Off. To use the device. < DRC-HUBO to apply force-torque sensors on each hand, to better capture the instrument. You can see how the robot moves and he even moves the drill on the shelf (knocking another drill on the way), in order to better seize it. When the robot manages to capture tool operators show place for the perforation, and the rest of the robot performs himself. It employs 20 Newtons of thrust force, and you can see how he uses his body to move the drill perfect circle. The job takes 11 minutes of the robot.
6. Setting surprise.
This task consisted in to pull the plug and insert it into a different outlet. Notice how the DRC-HUBO scans the floor and notice that drill, he rejected the buyout earlier, it is on its way. The robot turns and moves the tool knees. Then he tries to turn around and it seems as if he hit the wall. Operators clearly notice the problem, it leaves a little bit ahead and then can turn around. Finally, the robot approaches to the wall socket, which is set higher than the door handle and the latch. It's time to get up, and you can watch it, since the 3:05 mark. < DRC-HUBO takes a few steps forward and after a while starts the job. He grabs the plug on the cable; we believe that it was intended that operators can better consider the fork and the robot arm is not overshadowed her that would make the job impossible. By the time you can see it at around 7:47, the robot tries to insert the plug and socket near misses. After some corrective movements, the job is done! It took 13 minutes and 30 seconds - more than all the other jobs.
7. Setting for promotion through the rubble.
< DRC-HUBO can move your knees forward or turn 180 degrees to the torso and legs go forward, acting like a bulldozer blade. And that's what he does to do the job. You can see how he turns the body at around 0:28. It looks cool. The robot raises his hands - probably so they do not mess up the garbage. Then he begins to move through the rubble. He stops for just a second when it seems as if a piece of wood stuck in a cinder block, so it turns slightly to the left to remove it from the road. Pushes the plastic pipe to the right. At around 4:14 he turns torso again and becomes opposite steps. The job takes less than 5 minutes.
8. Setting in steps.
About Professor said that for many tasks, especially raising the stairs, it is important that the robot could see his legs. The large robot type ATLAS can hardly do it, they need to bend the body, making it difficult balancing act. < DRC-HUBO solves this problem very clever way. He climbs the stairs backwards! Thus his knees do not block the camera and you can see his feet and the ground. But how he can see his feet when lifted backwards? Turning Torso, of course! You can see the whole process, starting with a mark of 0:26. Robot kneels before the stairs, and then suddenly turned back to her. Then he gets up at 0:55, and you'll see how it turns torso 180 degrees. He can now scan and start to climb the stairs. But note that before he takes two steps to the side, to the left (1:45)! After a couple of minutes - which seemed like an eternity for the audience - the robot is finally beginning to rise, overcoming the last three steps one after the other. Clearly! In less than 7 minutes DRC-HUBO is on the platform. In the video, there is no sound, but at this point, the team and the audience burst into applause.
< KAIST made four copies DRC-HUBO and practiced without tethers more than a month before the competition. They are trained on the street, in a parking lot with a rough surface and in different weather conditions, including strong sunlight and wind. "If we do not remove the safety cable operators will be afraid," - said the professor about the master class after the event.
He added that during the training they perform all tasks in both modes - standing and kneeling (the average time was 30 minutes). The team good at clearing the rubble hands DRC-HUBO , that they failed to demonstrate on DRC Finals , and they are also able to perform more complex tasks on the surface than the one that was in the competition.
It is a pity that we could not show all the ability of the robot in the competition ... it was all too easy! - сказал About Professor , down from the stage to the applause.
Blockquote>
Source: geektimes.ru/company/robohunter/blog/251898/