1602
Behind the scenes of the future: a robotic factory Audi
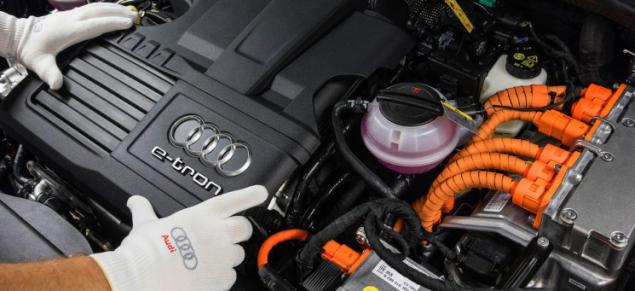
Cars evolve. We went from the burning of fossil tanks in our cars to charging from the outlet for one night, and now invent more and more sophisticated ways of transportation. Along with this progress inseparably and production methods. Let's take a look inside the production plant megasekretnogo Audi in Germany, where people are working near robots to collect thousands of cars a day.
Welcome to Ingolstadt. The city's population is 127 000 people, is located here head office and production lines of the company.
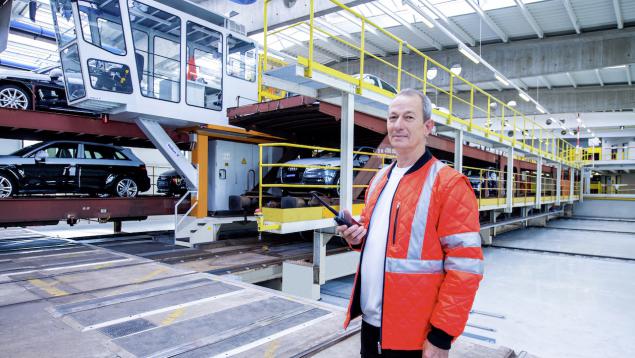
When we say "head office", really mean it. The plant in Ingolstadt area is not inferior to the city of Monaco, whose population is less than the number of employees working here 40 000 people operate everything - from the assembly of Audi A3, A3 e-tron, A3 g-tron, A4 sedan and Q5 crossover to control sales and support. It is a city of glass and steel, introduced ideas of precision engineering and luxury.
Ingolstadt churns out 2,500 finished cars a day - all done in a special workshop at the plant. The toolroom Audi creates his own instruments and elements of the body; in paint - spray paint robots for 4-5 hours; It has a research and development center with its own room for crash tests to test and improve existing models; as well as the assembly hall, where all completed together.
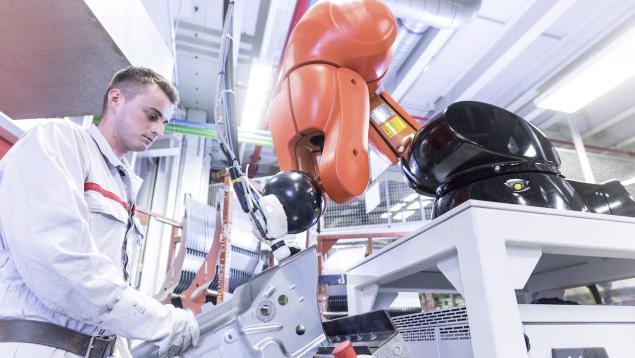
As soon as we go in the assembly hall, a large open space lit with light. The only objects that occupy space on the square - a giant orange with lots of robots for welding extremely precise components with the speed of light and unbearable heat. Often working process takes place in the dark, because robots do not need light.
One man stands near the robot, giving new details. His robot wheel arches creates a model Q5, forming them of 12 aluminum parts.
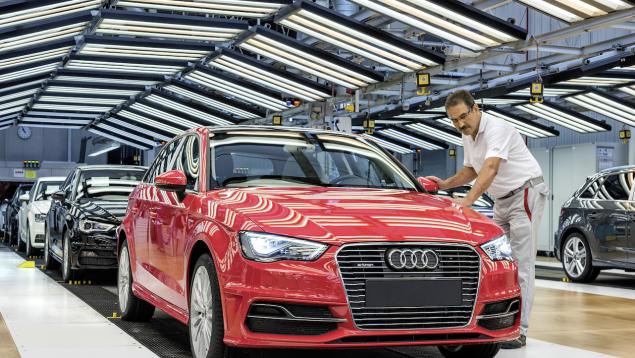
Before you fill the hall these robots a few years earlier, the plant had to be a lot of welders, doing thousands of spot welds. Automation has allowed Audi to fulfill thousands of orders a day.
800 robots working around the clock, and people complement the process of 12-hour shifts. The ventilation system operates non-stop feeding fresh air into closed rooms, giving it a sweet smell to enhance the comfort of the remaining employees.
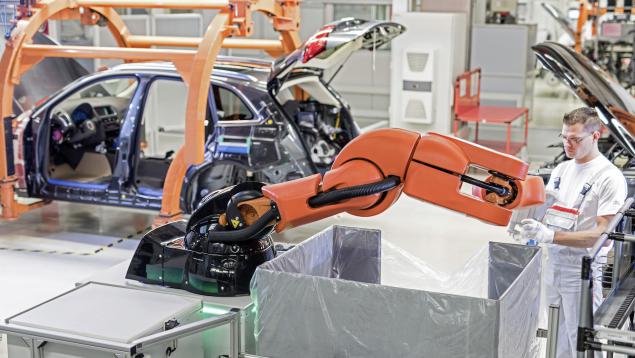
The whole complex is very energy efficient - solar panels on the roof of a lot of saves. The building itself was created in 1950, but the equipment is advanced.
As for the plant out of the gate which travels 2,500 cars a day, it is surprisingly uncluttered. First of all this is made possible thanks to the practical German thinking: cars are automatically transported between stations over the heads of workers in the system of lifts and conveyors. After fastening component robot raises its own, gradually passing to the next item.
Robots perform much of the work, including welding spot, forming and assembly. Giant electrodes on both sides of the clamping claws fed automatically by connecting the two parts.
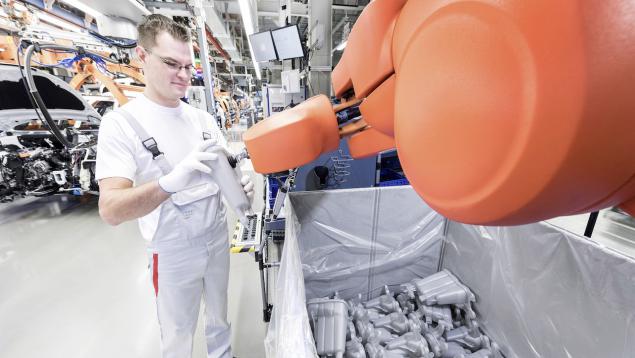
Robots do not themselves silly, since they have behave differently on each machine, depending on customer preferences. The plant in Ingolstadt collects only cars on order - instead of having to fill showrooms all over the world the same machines. One customer wants a sunroof that is, at some point, the robot has to take a new part. Another need a steering wheel on the right and someone else - a different interior design and color.
To control the robots and let them know what comes next, each machine has a small gray unit of data that provides information on what you need to attach and in which order. Robots read the data and select the appropriate essential component.
In order to guarantee compliance with the quality at Audi have robots with laser measuring every detail when it is transported between stations - so check the safety, accuracy and compliance with the customer's request. If the car has to be a hatch in the roof, and it is missing, the item is marked, before you go further. And to make sure that the welding robots are functioning correctly, every 4 hours into the process on the assembly line a dummy command. This test machine is later removed from the line and completely disassembled to ensure proper operation of the robot.
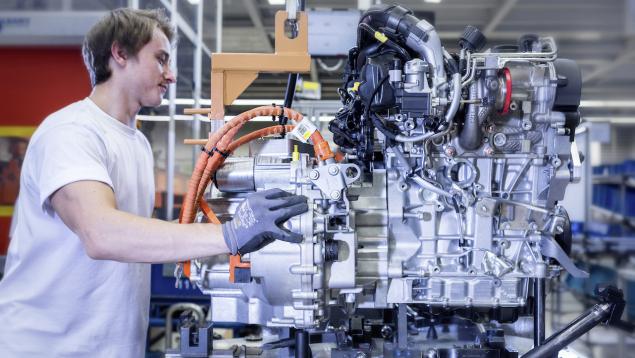
The largest concentration of employees, people in the factory - on the lines of final assembly and finishing shops, where employees set for assembly seats, steering wheels, airbags, stereo systems and other components. This is where the most advanced cooperation between humans and robots, to improve efficiency.
Instead of employees is constantly stooped and strains are used, power seats, on which you can "float" around the assembly line, to take the necessary component and move back into the car to install. It looks like a flying seat attached to the production line.
The plant in Ingolstadt reasonably split rail roads connecting it with loading ports for further transportation to Europe and around the world. Covered car automatically moved to the storage area for the automatic loading of the train - all controlled by a small team responsible for logistics.
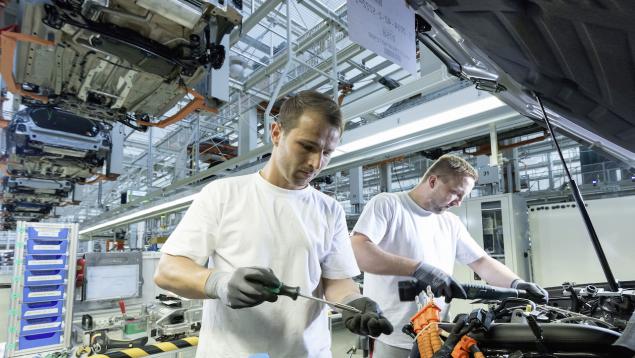
This plant - not unique: the Audi has more than 10 assembly centers in the world (from Europe to India and even China) to create beautiful brand new TT, SUVs Q7, sports A1 and S1 and wild supercar R8.
The question is whether the company's plants in the future, people are working, if the robots were so effective. If you believe a member of the board of directors in Audi AG Dr. Hubert Valtlyu, there is no doubt.
He believes that robots will never completely replace humans in factories automakers.
In the future, the plants will not be without people. We will continue to take decisions relating to the production process. And workers will remain a key element of the production-oriented success and future progress, - he said.
Blockquote>![]()
This is a new era in the industry that brings an incredible process of cooperation between man and machine, to improve the assembly skills of people, and it's just wonderful!
Source: geektimes.ru/company/robohunter/blog/252578/
Swedish scientists have created an artificial neuron that can communicate with the living neurons
Summer entertainment. The boom itself to take on holiday?