681
California-based company has developed a technology 3D printing of high-strength ceramics
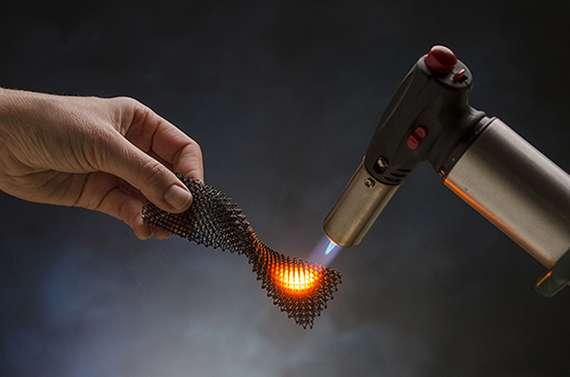
Researchers from the private company HRL Laboratories developed and demonstrated a new method additive manufacturing (3D printing), allowing you to create products of high strength ceramic material. The resulting material can withstand the temperature and record the load.
Ceramics, unlike metal or plastic, not easy to make the desired shape. 3D printing allows you to create products of almost any shape, but it can help have not yet been able to make ceramics.
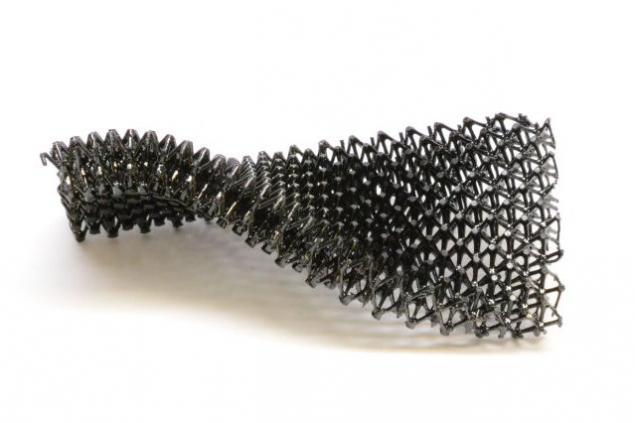
"3D printing - a very important new technology, but so far that it could not be done using high-strength products, suitable for engineering design, - says co-author , Tobias Shedler [Tobias Schaedler]. - We would like to accommodate 3-D printing to create high-strength and heat-resistant ceramics ».
Tobias is not quite right - 3D printing is already used, for example, to create rocket engines , capable of withstanding temperatures up to 3000 degrees Celsius. But ceramics on the printer, really, not yet published.
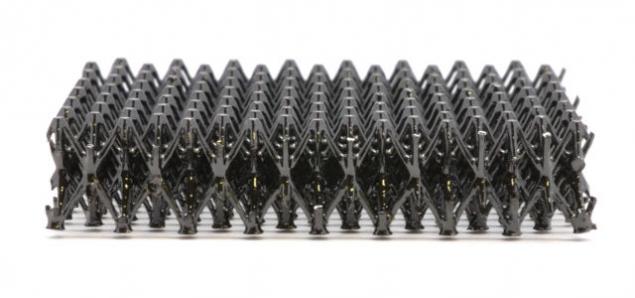
As an intermediate product for the material acts as a special polymer. After giving the product a desired shape, it is subjected to high temperature treatment, after which it becomes a ceramic. As a result, he gains the ability to withstand temperatures of at least up to 2000 K (check the possibility of the samples at higher temperatures, the authors of the work just did not have).
The basic technology is not new - back in the 1960s, was invented by a derivative of the polymer ceramic [polymer-derived ceramics]. In such polymers, contains the basic components of ceramics (silicon, nitrogen). After heating the resin volatilizes, methane, carbon dioxide and the like, leaving the ceramic structure composed of silicon, carbon and nitrogen. The resulting product is reduced in size, but retains its shape.
The novelty in this process is the use of substances that polymerize when exposed to ultraviolet light. This means that the desired product can be printed on almost any serial-3D printer ( authors of so did they simply order printer ready).
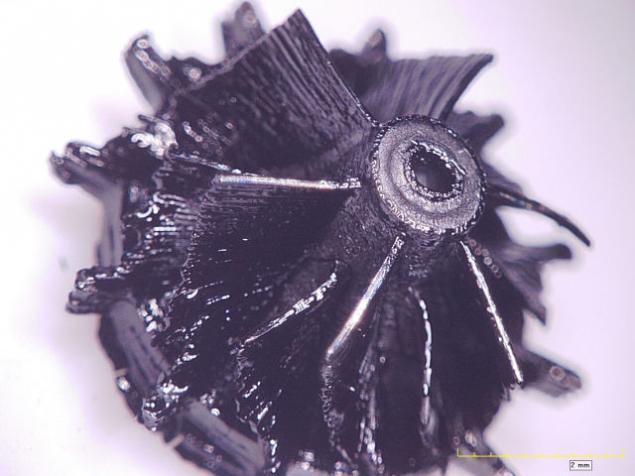
Besides conventional additive technology, in which the polymer layer by layer extruded onto the substrate, we have also tried a technique called "self-replicating wave structure» [self-propagating wave-guide technology]. The bottom line is that the finished polymer is capable of transmitting ultraviolet radiation, while the semi-finished product that can not do. As a result, using carefully designed templates can be polymerized sufficiently large areas of the workpiece faster than "print" them into 3-D printer.
Polymerized preform authors then heated in an oven to yield ceramic products, in which the composition contains 36% oxygen, 26% silicon, 33% carbon, and 4% of sulfur.
In addition to the high thermal stability of the product obtained and very strong - their strength compared with the authors 'cell' structures made of aluminum alloys. According to scientists, a lattice structure due to the high strength and low weight may be used in the manufacture of "supersonic aircraft and jet engines."
Source: geektimes.ru/post/268718/