681
Empresa con sede en California, ha desarrollado una tecnología de impresión 3D de la cerámica de alta resistencia
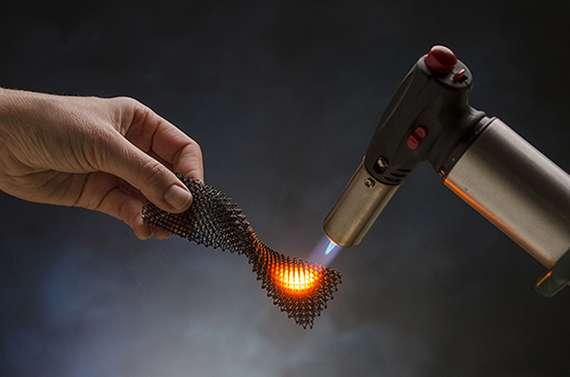
Investigadores de la empresa privada Laboratorios HRL desarrollaron y demostraron un nuevo método fabricación aditiva (la impresión 3D), que le permite crear productos de material cerámico de alta resistencia. El material resultante puede resistir la temperatura y registrar la carga.
Cerámica, a diferencia de metal o plástico, no es fácil para hacer la forma deseada. La impresión 3D permite crear productos de casi cualquier forma, pero puede ayudar aún no han sido capaces de hacer cerámica.
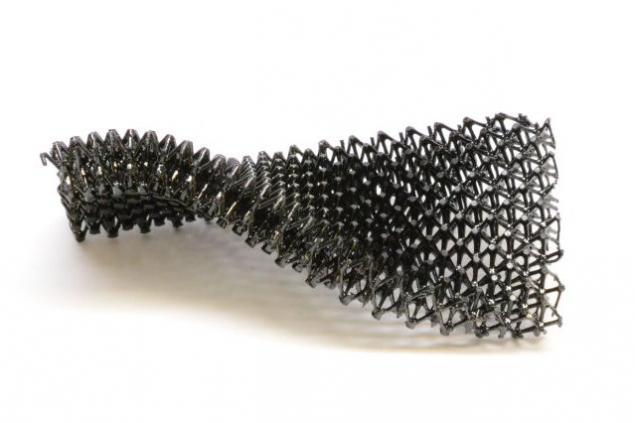
"La impresión 3D - una nueva tecnología muy importante, pero hasta el momento que no se podía hacer uso de productos de alta resistencia, apto para el diseño de ingeniería, - dice el coautor , Tobias Shedler [Tobias Schaedler]. - Nos gustaría dar cabida a la impresión 3-D para crear de alta resistencia y resistente al calor cerámica »
.
Tobias no está bien - la impresión en 3D ya se utiliza, por ejemplo, para crear motores de cohetes , capaz de soportar temperaturas de hasta 3.000 grados centígrados. Pero la cerámica en la impresora, en realidad, aún no publicadas.
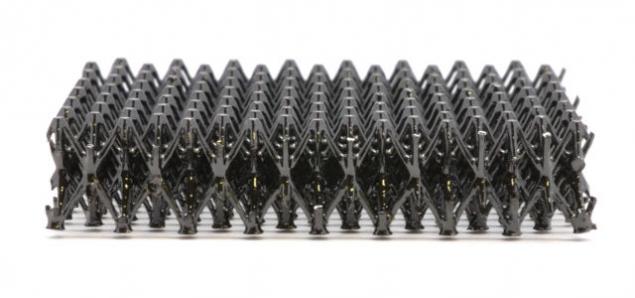
Como un producto intermedio para el material actúa como un polímero especial. Después de dar al producto una forma deseada, se somete a tratamiento a alta temperatura, después de lo cual se convierte en una cerámica. Como resultado, se obtiene la capacidad de soportar temperaturas de al menos hasta 2000 K (comprueba la posibilidad de que las muestras a temperaturas más altas, los autores de la obra simplemente no tienen).
La tecnología básica no es nueva - de vuelta en la década de 1960, fue inventado por un derivado de las cerámicas [cerámicas de polímeros derivados] de polímero. En tales polímeros, contiene los componentes básicos de cerámica (silicio, nitrógeno). Después de calentar la resina se volatiliza, metano, dióxido de carbono y similares, dejando la estructura cerámica compuesta de silicio, carbono y nitrógeno. El producto resultante se reduce en tamaño, pero conserva su forma.
La novedad en este proceso es el uso de sustancias que polimerizan cuando se exponen a la luz ultravioleta. Esto significa que el producto deseado se puede imprimir en casi cualquier impresora serial-3D (autores de lo hicieron ellos simplemente pedir impresora lista).
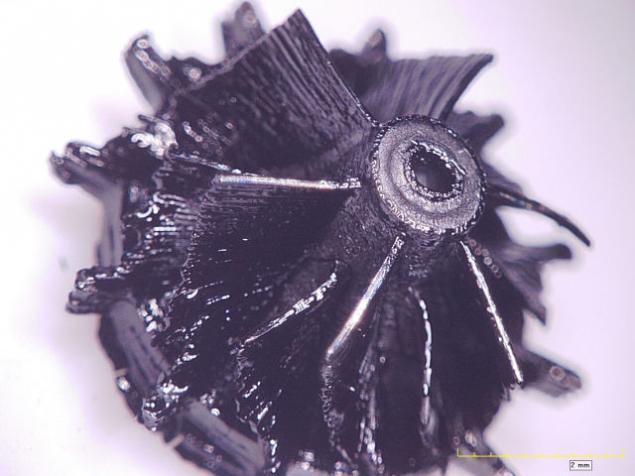
Además de la tecnología aditivo convencional, en el que la capa de polímero por capa extruida sobre el sustrato, también hemos intentado una técnica llamada "estructura de onda auto-replicantes» [tecnología de guía de ondas autopropagante]. La conclusión es que el polímero final es capaz de transmitir la radiación ultravioleta, mientras que el producto semi-terminado que no puede hacer. Como resultado, el uso de plantillas cuidadosamente diseñados puede ser polimerizado suficientemente grandes superficies de la pieza de trabajo más rápido que "imprimir" ellos en la impresora 3-D.
Autores de preforma polimerizados calentaron en un horno para producir productos cerámicos, en el que la composición contiene 36% de oxígeno, 26% de silicio, 33% de carbono, y 4% de azufre.
Además de la alta estabilidad térmica del producto obtenido y muy fuerte - su fuerza en comparación con los autores de células 'estructuras hechas de aleaciones de aluminio. Según los científicos, una estructura reticular debido a la alta resistencia y bajo peso puede ser utilizado en la fabricación de "motores de aviones y avión supersónico."
Fuente: geektimes.ru/post/268718/
9 muy interesantes experimentos mentales con la mente humana
Visión general de los juguetes robóticos para niños