681
0.2
2016-01-05
Калифорнийская компания разработала технологию 3д-печати высокопрочной керамики
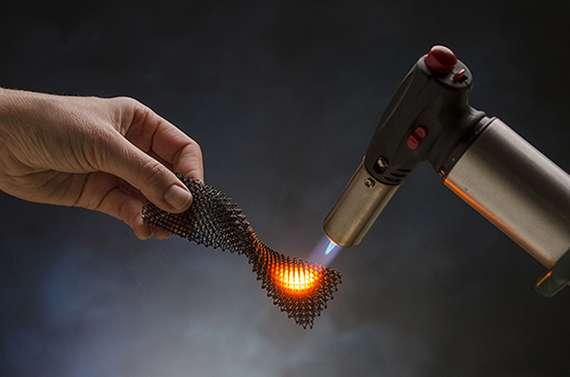
Исследователи из частной компании HRL Laboratories разработали и продемонстрировали новый метод аддитивного производства (3Д-печати), позволяющий создавать изделия из керамического материала высокой прочности. Получившийся материал выдерживает рекордные температуры и нагрузки.
Изделию из керамики, в отличие от металла или пластика, не так легко придать нужную форму. 3д-печать позволяет создавать изделия практически любой формы, но с её помощью пока ещё не удавалось изготавливать керамику.
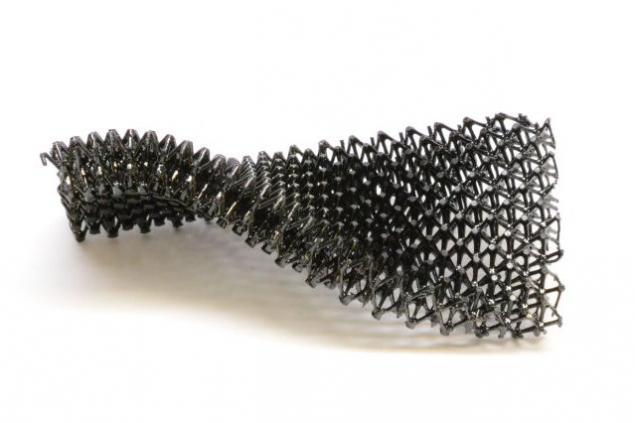
«3д-печать – очень важная новая технология, но пока что с её помощью нельзя было делать высокопрочные изделия, пригодные для инженерных разработок,- говорит соавтор работы, Тобиас Шэдлер [Tobias Schaedler]. – Мы хотели приспособить 3д-печать для создания высокопрочной и термостойкой керамики».
Тобиас не совсем прав – 3д-печать уже используется, например, для создания ракетных двигателей, способных выдерживать температуры до 3000 градусов Цельсия. Но керамику на принтере, действительно, пока ещё не печатали.
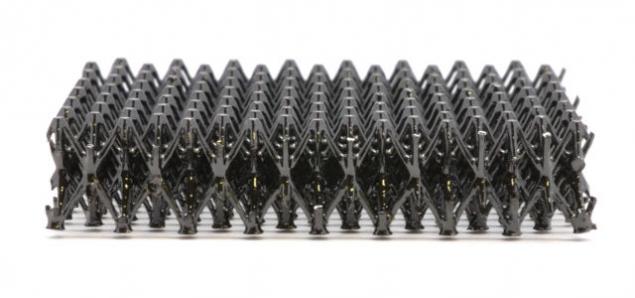
В качестве полуфабриката для материала выступает специальный полимер. После придания изделию нужной формы его подвергают высокотемпературной обработке, после которой он становится керамическим. В результате он приобретает способность выдерживать температуры как минимум до 2000 К (возможности проверить образцы при более высоких температурах у авторов работы просто не было).
Основы технологии не новы – ещё в 1960-х годах была придумана производная от полимеров керамика [polymer-derived ceramics]. В таких полимерах присутствуют основные составляющие керамики (кремний, азот). После нагревания из полимера улетучивается метан, углекислый газ и т.п., оставляя керамическую структуру, состоящую из кремния, углерода и азота. Получающееся изделие уменьшается в размерах, но сохраняет форму.
Новинкой в данном процессе стало использование веществ, полимеризующихся при воздействии на них ультрафиолетом. А это значит, что напечатать нужное изделие можно практически на любом серийном 3д-принтере (авторы работы так и сделали: они просто заказали готовый принтер).
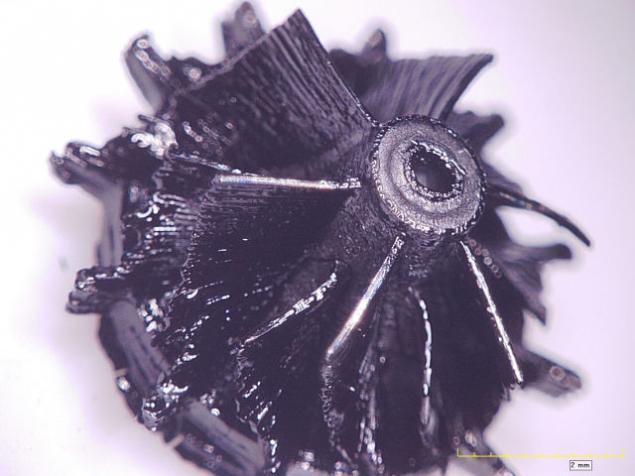
Кроме традиционной аддитивной технологии, при которой полимер слой за слоем выдавливается на подложку, авторы также попробовали метод под названием «саморазмножающаяся волновая структура» [self-propagating wave-guide technology]. Суть в том, что готовый полимер способен пропускать ультрафиолетовое излучение, в то время как полуфабрикат этого делать не может. В результате при использовании тщательно разработанных шаблонов можно полимеризовать достаточно большие области заготовки быстрее, чем «печатать» их на 3д-принтере.
Полимеризовавшиеся заготовки авторы затем грели в печи и получили на выходе керамические изделия, в составе которых содержатся 36% кислорода, 26% кремния, 33% углерода и 4% серы.
Кроме высокой термостойкости изделия получаются и очень прочными – их прочность авторы сравнивают с «сотовыми» конструкциями из алюминиевых сплавов. По мнению учёных, решётчатые структуры благодаря высокой прочности и низкому весу могут быть использованы при изготовлении «сверхзвуковых самолётов и реактивных двигателей».
Источник: geektimes.ru/post/268718/
Портал БАШНЯ. Копирование, Перепечатка возможна при указании активной ссылки на данную страницу.
9 Необычайно Интересных Мысленных Экспериментов С Человеческим Разумом
Обзор роботов-игрушек для детей