2087
Injection molding in silicone - available small-scale production at home
Many of those who print the 3D-printer or faced with the need to get the party models in short order, or copied successfully received the item or get a product with strength characteristics superior to those of plastics for home 3d-printing.
3D-printer is not always able to carry out such tasks, but is perfect for the creation of a single sample, or a master model. And then we come to the aid of the materials produced by Smooth-On, probably the most popular manufacturer of cold-curing materials.
In this review we will compare the most basic and popular silicones, polyurethanes and supplements thereto, brief look at the main ways to create forms and products, think about where it can be used, and, finally, create a silicone mold and model.
Before writing this post, we passed three-day training from an authorized dealer Smooth-On in Russia to understand all the intricacies of casting in silicone.
Review process
The process of creating products using the casting is almost always the same: to create a model, it can help create a silicone mold, pour into it the material we get the product. But depending on the model, the required properties, the number of castings, each step can change dramatically. There are several ways to create a form, and the finished product.
A few words about the preparation of models, printed the 3D-printer. Smooth-On company turned its attention to this technology, and has released a special lacquer called XTC-3D. It perfectly smooths the characteristic patterns printed flaws visible layers that are sure to switch to silicone mold, and gives the surface a smooth and glossy look.
A detailed review of XTC 3D you can read here .
Methods of creation of forms
• Solid color
The easiest way: the model is placed in the formwork (special airtight container from the usual plexiglas, plastic or other material), it is fixed and filled with silicone. Well suited for a simple two-dimensional models, reliefs, souvenirs and branded products.
• Floating form
Similar to the previous one, only the model is placed, bearing in mind that the form is cut totally or partially to facilitate removal. The model can be suspended via a wire or placed on a thin support. The method is designed for more complex geometry, technical products, complex shapes.
• a dual form
This is one of the most complicated processes. It is to put the model on clay or plasticine framework that divides the silicone mold half.
Based placed special locks, which will provide precise alignment of the two forms and the absence of displacement. Going around the base formwork, sealed with hot glue or clay, and it filled the first half of the form. Then, after curing silicone form turns, clay or plasticine cleans, silicone coated with release agent, and filled the second half of the mold.
• Method "in spreads»
This method creates a so-called "stocking" form when silicon accurately follows the shape of the object and has a thickness of 3 mm to several centimeters. To create a form "in the spreads' needs sufficiently viscous silicone, which would not have flowed from the model.
You can use a specially designed for this silicones called thixotropic, and conventional, but modified with thickeners.
Silicon is applied with a brush or trowel in several layers, which alternates strength and speed solidification to form was the most detailed and robust. Once all the layers are prepared with the help of a special composition created a tough outer shell that will hold the shape.
by casting plastics
The easiest method is to fill the usual plastic in the shape it is suitable for home use and allows you to achieve acceptable quality. But, if necessary, for better results you can use high-pressure, which will almost completely remove air bubbles.
For this form, together with flooded plastic placed in a chamber in which is created an increased to 4 atmospheres pressure. The form must remain in the chamber all the time curing polyurethane. At this pressure, the bubbles are reduced to almost invisible to the eye size, which greatly improves the quality of the product.
Another method, the so-called priming "break-in", is used to create hollow bodies. The form is filled with a small amount of plastic, about 10% of the total volume filling hole is closed, and starts the rotation of all forms of the planes, manually or on a rotary machine. This hardens the plastic mold on the walls, creating a hollow model that can significantly reduce product weight and material savings.
Review silicones
• Mold Star Series 15, 16, 30
Silicones for creating forms based on platinum. Solidifies at room temperature to form a solid, flexible and very detailed form. Intended for molding silicone, polyurethane resins, polyester, wax and other materials. Chemically sensitive, and unable to work with the latex, and some other sulfur compounds.
The most basic and fundamental silicones that can solve most problems. The number in the title reflects the hardness of Shore A. It has a low viscosity, which in most cases work without degassing equipment. Material two component parts in a convenient mix ratio of 1: 1 by volume. Basically designed to create forms by solid fill.
• Rebound Series 25, 40
A series of silicone to create forms by "in the spreads," which is to be applied with a brush or spatula silicone on the surface of the model. It has a high viscosity, with the possibility of modifying the properties of using thickeners and accelerators for creating high-quality multi-layer form. A two-component mixed in the ratio 1: 1 by volume.
• Equinox Series 35, 38, 40
Silicone paste with a lifetime 1, 4 and 30 minutes. Designed for manual mixing, the consistency of thick dough. The figures correspond to the hardness Shore A. It has a very high tensile strength and durability. In the cured state it is safe for filling of chocolate, caramel and other ingredients.
• SortaClear Series 18, 37, 40
A series of translucent silicone. This feature is the optical transparency is used to create complex shapes split - the product is perfectly visible, allowing you to make a precise cut. As lot Equinox, it is safe for contact with foodstuffs.
Also silicones, there are many supplements that have a variety of effects. Accel-T and Plat-Cat are curing accelerators, Slo-jo - increases the lifetime of the silicone, Thi-Vex increases the viscosity of the silicone and allows the spread of his brush or trowel on the model, Silc-Pig - is concentrated pigments for coloring.
Review polyurethanes
• Series Smooth-Cast
The most basic and popular series of polyurethane to create the final product. The range includes more than 10 types of different plastics with different properties that allow the material to choose for your project. For example, Smooth-Cast 300 has a short lifetime in 3 minutes and cure time 10 minutes, allowing you to quickly play large batches of parts. Smooth-Cast 305 is similar to the previous one, but "lives" for 7 minutes, which allows for degassing the mixed components and get more quality product. ONYX has a deep black color, which is not achieved by the dyes, 65D ROTO designed to create a hollow model using the method of "running-in" 325 is indispensable for accurate color reproduction, 385 cures practically without shrinkage and as accurately copies the product.
• Series TASK
A series of polyurethane for special applications. Designed for industrial applications and has specific properties for specific tasks.
For your convenience, we have formed a special filters on the areas of application:
• Food:
Smooth-Sil 940 Series Sorta Clear, series Equinox, TASK 11.
• Architectural, pouring concrete and other abrasive materials:
Series VytaFlex, Series Brush-On, a series of Ez-Spray, a series of PMC.
• Medical: Simulation of tissues and organs
A series of Dragon Skin, additives Slacker, Ecoflex 0030, Ecoflex Gel, Body Double.
• Prototyping:
Virtually any polyurethanes and silicones, depending on the objectives and requirements. Series Mold Max, Mold Star, Smooth-Cast, TASK.
• Special effects and make-up:
Skin Tite, Body Double, Dragon Skin, Alja-Safe, Ecoflex, Soma Foama, Rubber Glass, Encapso K.
It should be noted that this division is still suspended and given to about a wide range of possibilities to introduce the company Smooth-On.
Review process
We will only use materials and equipment that can be applied at home. We try to create the most complex in the manufacture of a dual form.
We need:
• Platinum Silicone Mold Star 30
• Pouring polyurethane Smooth-Cast 300
• Nail of 3D-models XTC-3D
• Packing vinyl gloves
• Several of disposable plastic cups
• mixing bowl
• interlining gun
• Material for formwork (plastic panels)
• Sculptural clay
• Multiple paint brushes
In the role of the master model will make the model quite popular among the printers of the test bolt. We print it in black plastic on the PLA Picaso 3D Designer with a layer thickness of 100 microns. We did this on purpose in order to demonstrate the effect of XTC 3D, because not every 3D printer can print with a quality of 50 microns.
Next - treatment to cast the model is not taken over layering printed object. Handle bolt varnish XTC-3D (read more about this process can be found here ), and then the skins to a smooth matte surface.
Now the model is ready for filling with silicone. We put it on a clay foundation, through which we create a silicone mold of two parts.
The model should be immersed in clay exactly half, so begin the process of alignment of clay. The edges should be as smooth and fully conform to the model depends on the quality of the separation of silicone halves. Remove the excess clay and conclude a model in plastic formwork.
All joints of plastic handle interlining gun and close the formwork completely treat a clay foundation, do it recesses for locks.
Everything is ready for casting silicone. Since the two-component silicones and polyurethanes tend to be separated into fractions prior to each use, they must be thoroughly mixed in the tank.
After stirring mete out equal amounts of the two components in volume and begin to mix.
For this brand silicone outgassing in a vacuum chamber is optional, it is very convenient to: eliminate the occurrence of bubbles, which can spoil our form. Slowly pour the silicone into the mold, to the lowest point of it.
And leave to harden. Setting time for the brand silicone is 6 hours. After this time, free the model from the formwork.
Then remove the clay model is carefully cleaned from its residues, grease silicone release agent. In its absence, you can use an ordinary petroleum jelly, but the quality is a little worse.
And then we repeat the process, filling in the second half of the silicone mold.
After another 6 hours silicone mold is ready. With the blade neatly sever halves, take out the detail and assess what we've got.
Clearly visible locks, lay in the clay-based, good detail, despite the fact that the dividing line runs along a fairly difficult place, like dents letters.
In fact, for this model is not the best way to create the form. But we were curious to test this method, despite the difficulties.
So, everything is ready for pouring polyurethane. Connects the two halves of the mold using a formwork elements for rigidity, fastening using rubber bands, tape or other means, and proceed to the preparation of polyurethane.
Both components are mixed well by shaking them for 5-10 minutes. After that, we give a little stand to come out bubbles formed. Everything else the same way as with silicon: equal amount is metered by volume and mix them. And then we must act quickly: the lifetime of the polyurethane is only 3 minutes, and the time starts to go as soon as you mix the two components together. So what prevents quickly, but carefully, so as not to create unnecessary bubbles, and immediately poured into a mold.
After about 3 minutes, depending on the amount of material to occur fast setting plastic, and after 10 minutes the item is ready for harvesting.
The model is ready. Transferred everything detail of the original.
Conclusion
It should be noted that a truly enormous opportunities to use materials Smooth-On offers in conjunction with 3D-printing.
Now you can get the products of a large number of materials with very different properties, but not limited to classical PLA and ABS. Also available will be a limited production: printing just one copy, and properly handle it, you can in a fairly short period of time to create the necessary number of copies at home. In order to achieve an acceptable result is not necessarily the use of expensive equipment.
If you need the services of small-scale production to the Top 3D Shop offers .
57,123,826
Source: geektimes.ru/company/top3dshop/blog/251780/
3D-printer is not always able to carry out such tasks, but is perfect for the creation of a single sample, or a master model. And then we come to the aid of the materials produced by Smooth-On, probably the most popular manufacturer of cold-curing materials.
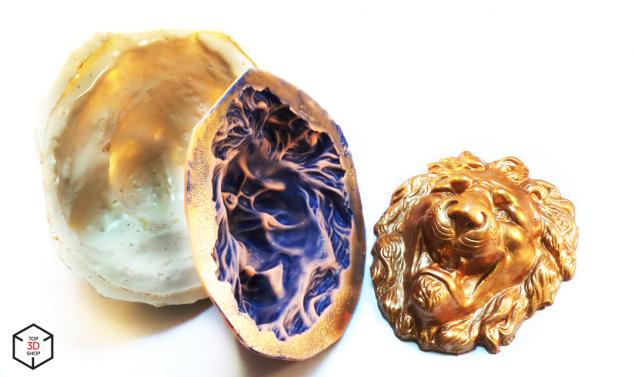
In this review we will compare the most basic and popular silicones, polyurethanes and supplements thereto, brief look at the main ways to create forms and products, think about where it can be used, and, finally, create a silicone mold and model.
Before writing this post, we passed three-day training from an authorized dealer Smooth-On in Russia to understand all the intricacies of casting in silicone.
Review process
The process of creating products using the casting is almost always the same: to create a model, it can help create a silicone mold, pour into it the material we get the product. But depending on the model, the required properties, the number of castings, each step can change dramatically. There are several ways to create a form, and the finished product.
A few words about the preparation of models, printed the 3D-printer. Smooth-On company turned its attention to this technology, and has released a special lacquer called XTC-3D. It perfectly smooths the characteristic patterns printed flaws visible layers that are sure to switch to silicone mold, and gives the surface a smooth and glossy look.
A detailed review of XTC 3D you can read here .
Methods of creation of forms
• Solid color
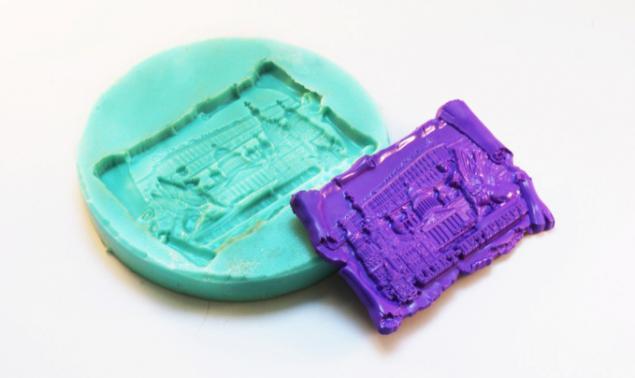
The easiest way: the model is placed in the formwork (special airtight container from the usual plexiglas, plastic or other material), it is fixed and filled with silicone. Well suited for a simple two-dimensional models, reliefs, souvenirs and branded products.
• Floating form
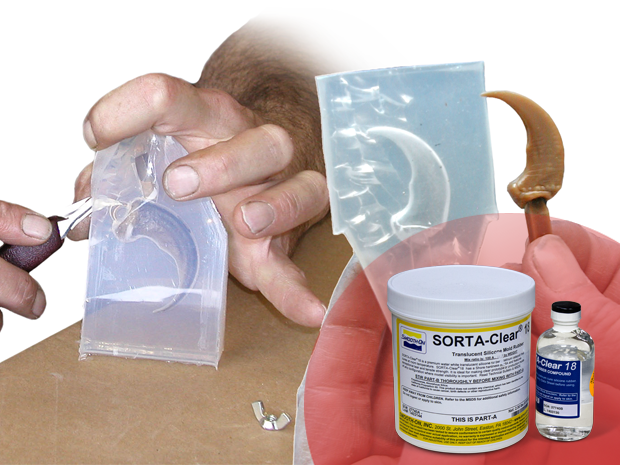
Similar to the previous one, only the model is placed, bearing in mind that the form is cut totally or partially to facilitate removal. The model can be suspended via a wire or placed on a thin support. The method is designed for more complex geometry, technical products, complex shapes.
• a dual form
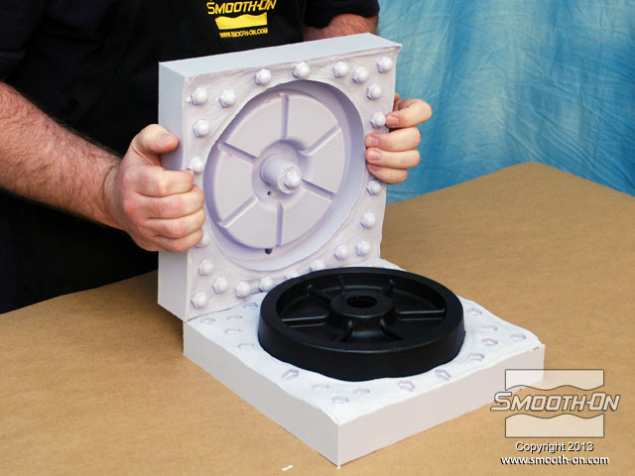
This is one of the most complicated processes. It is to put the model on clay or plasticine framework that divides the silicone mold half.
Based placed special locks, which will provide precise alignment of the two forms and the absence of displacement. Going around the base formwork, sealed with hot glue or clay, and it filled the first half of the form. Then, after curing silicone form turns, clay or plasticine cleans, silicone coated with release agent, and filled the second half of the mold.
• Method "in spreads»
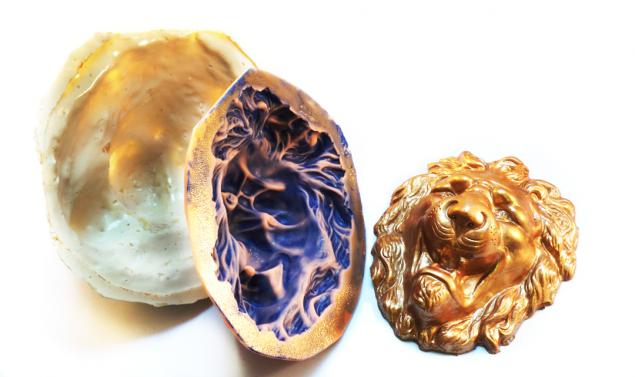
This method creates a so-called "stocking" form when silicon accurately follows the shape of the object and has a thickness of 3 mm to several centimeters. To create a form "in the spreads' needs sufficiently viscous silicone, which would not have flowed from the model.
You can use a specially designed for this silicones called thixotropic, and conventional, but modified with thickeners.
Silicon is applied with a brush or trowel in several layers, which alternates strength and speed solidification to form was the most detailed and robust. Once all the layers are prepared with the help of a special composition created a tough outer shell that will hold the shape.
by casting plastics
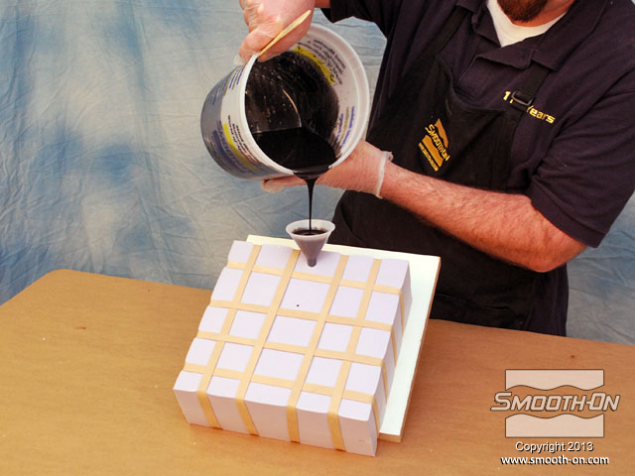
The easiest method is to fill the usual plastic in the shape it is suitable for home use and allows you to achieve acceptable quality. But, if necessary, for better results you can use high-pressure, which will almost completely remove air bubbles.
For this form, together with flooded plastic placed in a chamber in which is created an increased to 4 atmospheres pressure. The form must remain in the chamber all the time curing polyurethane. At this pressure, the bubbles are reduced to almost invisible to the eye size, which greatly improves the quality of the product.
Another method, the so-called priming "break-in", is used to create hollow bodies. The form is filled with a small amount of plastic, about 10% of the total volume filling hole is closed, and starts the rotation of all forms of the planes, manually or on a rotary machine. This hardens the plastic mold on the walls, creating a hollow model that can significantly reduce product weight and material savings.
Review silicones
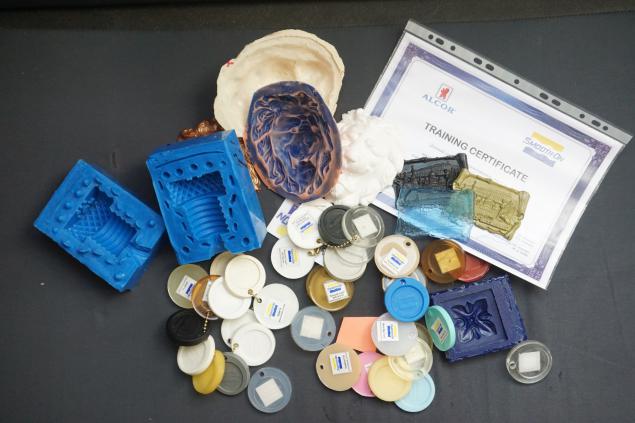
• Mold Star Series 15, 16, 30
Silicones for creating forms based on platinum. Solidifies at room temperature to form a solid, flexible and very detailed form. Intended for molding silicone, polyurethane resins, polyester, wax and other materials. Chemically sensitive, and unable to work with the latex, and some other sulfur compounds.
The most basic and fundamental silicones that can solve most problems. The number in the title reflects the hardness of Shore A. It has a low viscosity, which in most cases work without degassing equipment. Material two component parts in a convenient mix ratio of 1: 1 by volume. Basically designed to create forms by solid fill.
• Rebound Series 25, 40
A series of silicone to create forms by "in the spreads," which is to be applied with a brush or spatula silicone on the surface of the model. It has a high viscosity, with the possibility of modifying the properties of using thickeners and accelerators for creating high-quality multi-layer form. A two-component mixed in the ratio 1: 1 by volume.
• Equinox Series 35, 38, 40
Silicone paste with a lifetime 1, 4 and 30 minutes. Designed for manual mixing, the consistency of thick dough. The figures correspond to the hardness Shore A. It has a very high tensile strength and durability. In the cured state it is safe for filling of chocolate, caramel and other ingredients.
• SortaClear Series 18, 37, 40
A series of translucent silicone. This feature is the optical transparency is used to create complex shapes split - the product is perfectly visible, allowing you to make a precise cut. As lot Equinox, it is safe for contact with foodstuffs.
Also silicones, there are many supplements that have a variety of effects. Accel-T and Plat-Cat are curing accelerators, Slo-jo - increases the lifetime of the silicone, Thi-Vex increases the viscosity of the silicone and allows the spread of his brush or trowel on the model, Silc-Pig - is concentrated pigments for coloring.
Review polyurethanes
• Series Smooth-Cast
The most basic and popular series of polyurethane to create the final product. The range includes more than 10 types of different plastics with different properties that allow the material to choose for your project. For example, Smooth-Cast 300 has a short lifetime in 3 minutes and cure time 10 minutes, allowing you to quickly play large batches of parts. Smooth-Cast 305 is similar to the previous one, but "lives" for 7 minutes, which allows for degassing the mixed components and get more quality product. ONYX has a deep black color, which is not achieved by the dyes, 65D ROTO designed to create a hollow model using the method of "running-in" 325 is indispensable for accurate color reproduction, 385 cures practically without shrinkage and as accurately copies the product.
• Series TASK
A series of polyurethane for special applications. Designed for industrial applications and has specific properties for specific tasks.
For your convenience, we have formed a special filters on the areas of application:
• Food:
Smooth-Sil 940 Series Sorta Clear, series Equinox, TASK 11.
• Architectural, pouring concrete and other abrasive materials:
Series VytaFlex, Series Brush-On, a series of Ez-Spray, a series of PMC.
• Medical: Simulation of tissues and organs
A series of Dragon Skin, additives Slacker, Ecoflex 0030, Ecoflex Gel, Body Double.
• Prototyping:
Virtually any polyurethanes and silicones, depending on the objectives and requirements. Series Mold Max, Mold Star, Smooth-Cast, TASK.
• Special effects and make-up:
Skin Tite, Body Double, Dragon Skin, Alja-Safe, Ecoflex, Soma Foama, Rubber Glass, Encapso K.
It should be noted that this division is still suspended and given to about a wide range of possibilities to introduce the company Smooth-On.
Review process
We will only use materials and equipment that can be applied at home. We try to create the most complex in the manufacture of a dual form.
We need:
• Platinum Silicone Mold Star 30
• Pouring polyurethane Smooth-Cast 300
• Nail of 3D-models XTC-3D
• Packing vinyl gloves
• Several of disposable plastic cups
• mixing bowl
• interlining gun
• Material for formwork (plastic panels)
• Sculptural clay
• Multiple paint brushes
In the role of the master model will make the model quite popular among the printers of the test bolt. We print it in black plastic on the PLA Picaso 3D Designer with a layer thickness of 100 microns. We did this on purpose in order to demonstrate the effect of XTC 3D, because not every 3D printer can print with a quality of 50 microns.
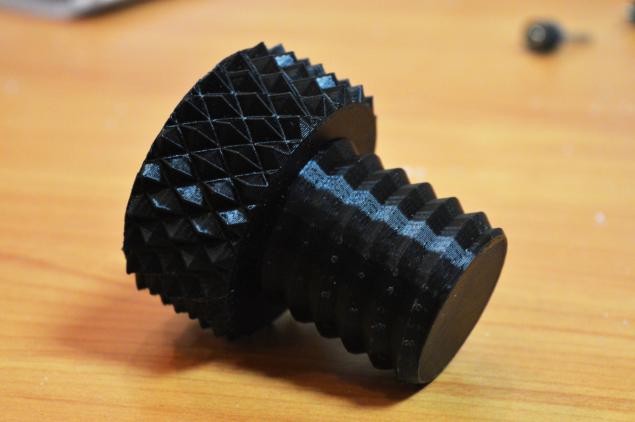
Next - treatment to cast the model is not taken over layering printed object. Handle bolt varnish XTC-3D (read more about this process can be found here ), and then the skins to a smooth matte surface.
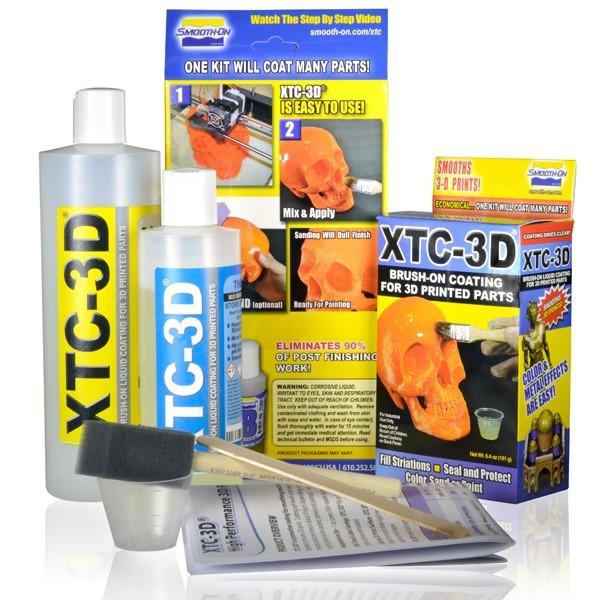
Now the model is ready for filling with silicone. We put it on a clay foundation, through which we create a silicone mold of two parts.
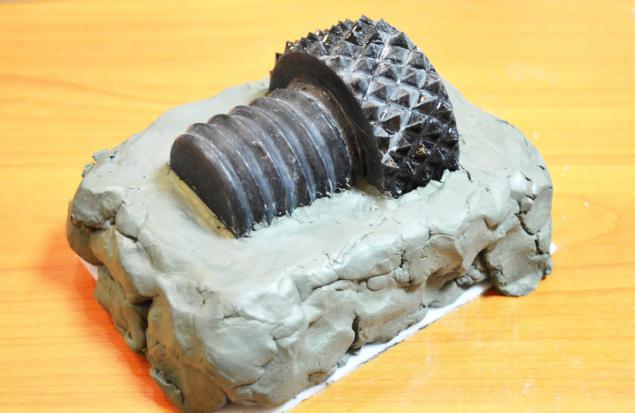
The model should be immersed in clay exactly half, so begin the process of alignment of clay. The edges should be as smooth and fully conform to the model depends on the quality of the separation of silicone halves. Remove the excess clay and conclude a model in plastic formwork.
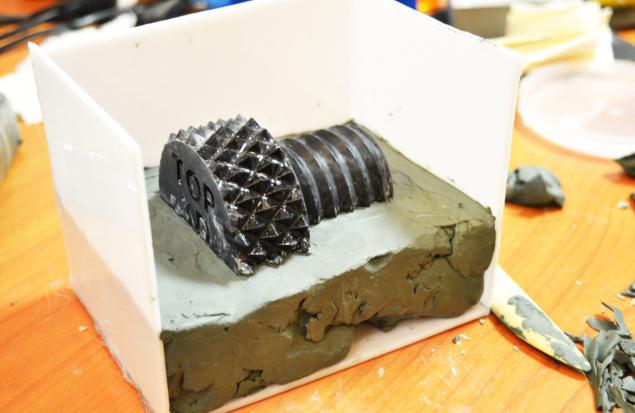
All joints of plastic handle interlining gun and close the formwork completely treat a clay foundation, do it recesses for locks.
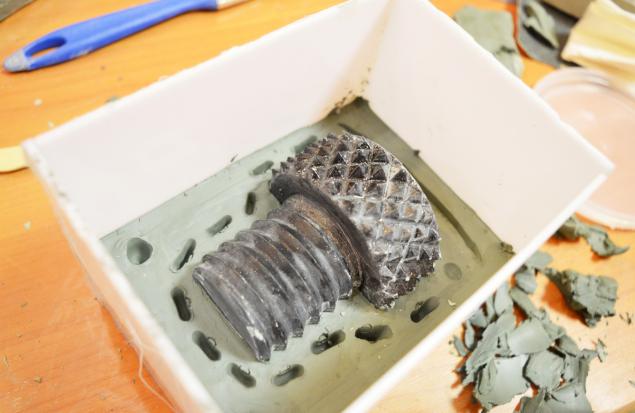
Everything is ready for casting silicone. Since the two-component silicones and polyurethanes tend to be separated into fractions prior to each use, they must be thoroughly mixed in the tank.
After stirring mete out equal amounts of the two components in volume and begin to mix.
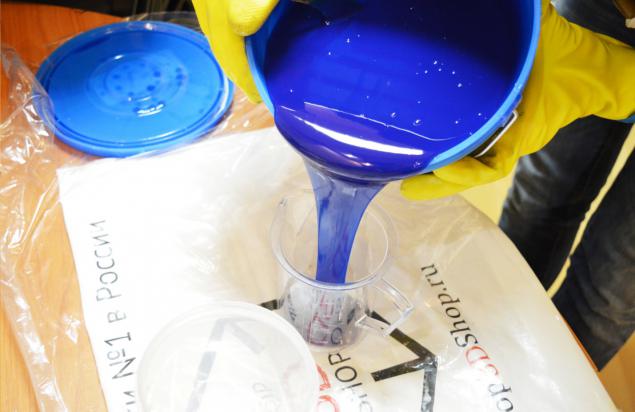
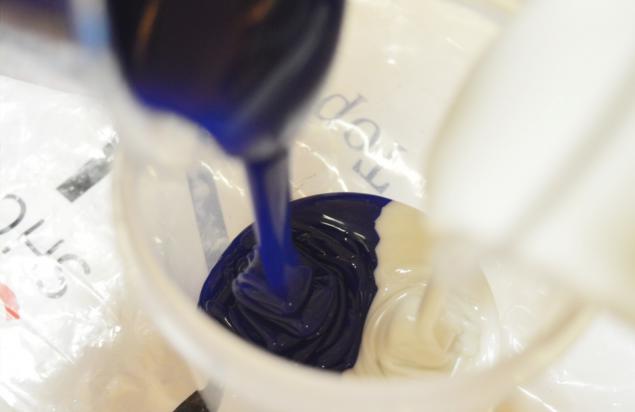
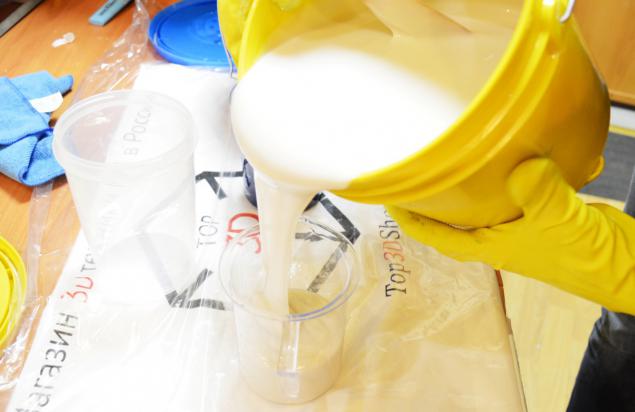
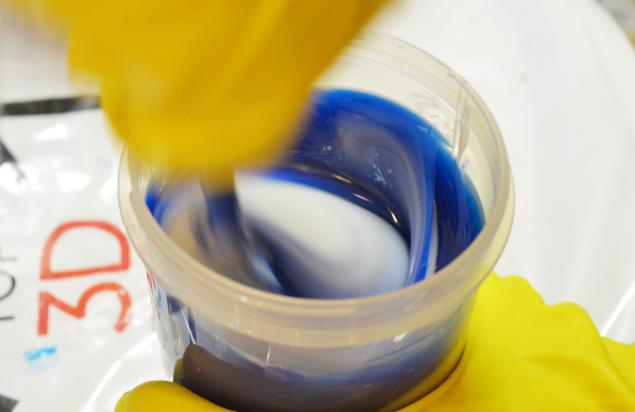
For this brand silicone outgassing in a vacuum chamber is optional, it is very convenient to: eliminate the occurrence of bubbles, which can spoil our form. Slowly pour the silicone into the mold, to the lowest point of it.
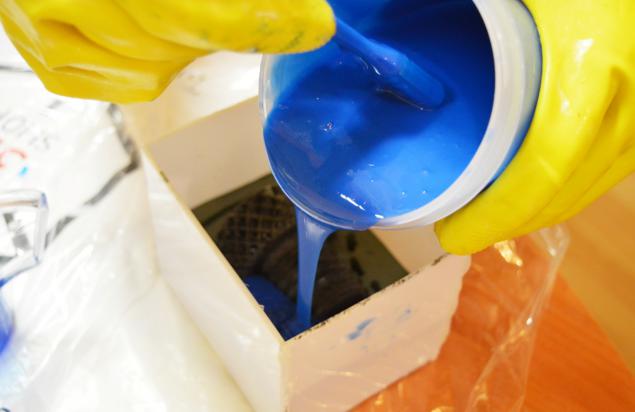
And leave to harden. Setting time for the brand silicone is 6 hours. After this time, free the model from the formwork.

Then remove the clay model is carefully cleaned from its residues, grease silicone release agent. In its absence, you can use an ordinary petroleum jelly, but the quality is a little worse.
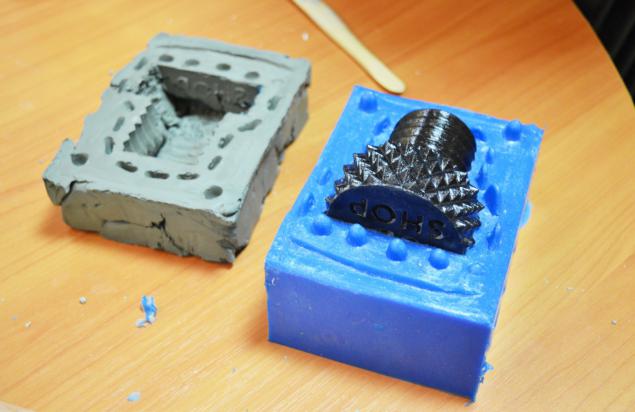
And then we repeat the process, filling in the second half of the silicone mold.
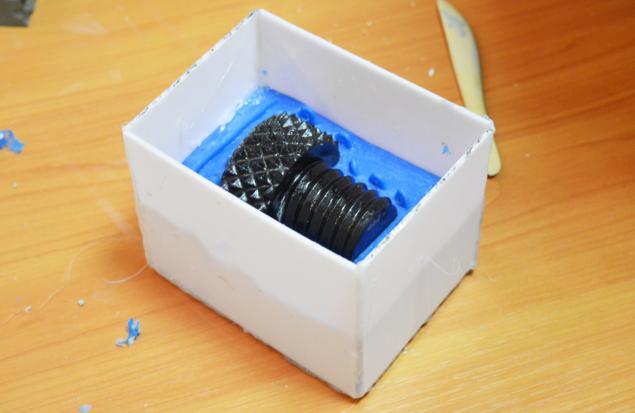
After another 6 hours silicone mold is ready. With the blade neatly sever halves, take out the detail and assess what we've got.
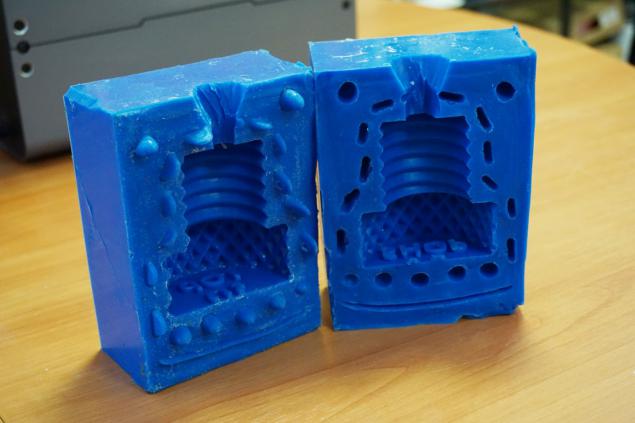
Clearly visible locks, lay in the clay-based, good detail, despite the fact that the dividing line runs along a fairly difficult place, like dents letters.
In fact, for this model is not the best way to create the form. But we were curious to test this method, despite the difficulties.
So, everything is ready for pouring polyurethane. Connects the two halves of the mold using a formwork elements for rigidity, fastening using rubber bands, tape or other means, and proceed to the preparation of polyurethane.
Both components are mixed well by shaking them for 5-10 minutes. After that, we give a little stand to come out bubbles formed. Everything else the same way as with silicon: equal amount is metered by volume and mix them. And then we must act quickly: the lifetime of the polyurethane is only 3 minutes, and the time starts to go as soon as you mix the two components together. So what prevents quickly, but carefully, so as not to create unnecessary bubbles, and immediately poured into a mold.
After about 3 minutes, depending on the amount of material to occur fast setting plastic, and after 10 minutes the item is ready for harvesting.
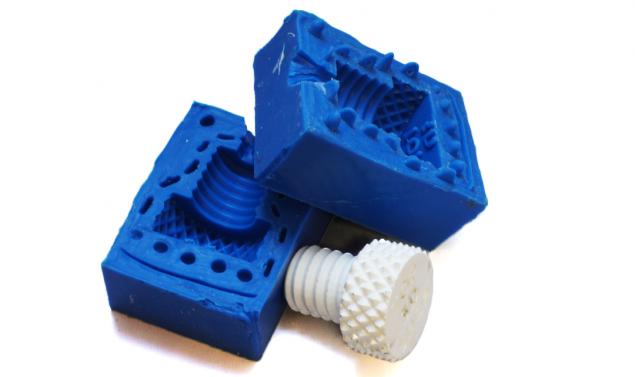
The model is ready. Transferred everything detail of the original.
Conclusion
It should be noted that a truly enormous opportunities to use materials Smooth-On offers in conjunction with 3D-printing.
Now you can get the products of a large number of materials with very different properties, but not limited to classical PLA and ABS. Also available will be a limited production: printing just one copy, and properly handle it, you can in a fairly short period of time to create the necessary number of copies at home. In order to achieve an acceptable result is not necessarily the use of expensive equipment.
If you need the services of small-scale production to the Top 3D Shop offers .
57,123,826
Source: geektimes.ru/company/top3dshop/blog/251780/