1002
Some details of the rocket Vulcan will be printed on 3D-printer
So will be able to save 50 to 90%
Photo ULA em>
In its new generation of rocket United Launch Alliance планирует use the 3D-printing to reduce production costs and simplify the development process by using rapid prototyping. Due to print parts made of plastic and metal is supposed to reduce the cost of a million dollars a year. In existing rocket Atlas V 3D-printing reduced the cost of the air conditioning system by 57%.
United Launch Alliance - a joint venture "Lockheed Martin" and "Boeing", which makes for about 12 launches per year. April 13 presentation at the Colorado chapter ULA Tory Bruno introduced a new missile with a fully Vulcan American engines. The first launch is scheduled for 2019, the price - from $ 165 million. It is assumed that the first-stage engine will be used again, for this they are going to shoot, Parachute and catch the helicopter. The new missile, its engines and bold plans for re-use are the answer to the current partial dependence ULA on Russian RD-180. It is noticeable that even the failed program's success landing the first stage rocket company SpaceX Falcon 9 precarious among the leadership of ULA.
Part of the Atlas and Delta rockets will also be printed, but ULA important to introduce 3D-press at the earliest stages of development, "Vulcan". Now choose the items to be printed. The lists of candidates more than 100 plastic and about 50 metal. It is expected that 3D-press will save about a million dollars a year.
Five-meter version of the "Volcano», ULA em>
Detail for the rocket is expensive, and if it is to book with a third-party company, you should take the time to provide specifications and find a common language. If the item is something wrong, then it will have to be sent back for revision. Time spent not only this, sometimes contractors do not have time to complete their work on time. Own 3D-press simplifies control over the production process. Printing will be used in the traditional role - for rapid prototyping. It allows you to immediately make the necessary detail to engineer could touch her, to evaluate the functionality before leaving the order for its manufacture.
To implement these plans were purchased two printers Fortus 900mc from Stratasys. First of all, these machines will be used to create a new air conditioning system rocket Atlas V. The system is designed for delivery of liquid nitrogen preflight electronic components rocket booster to cool them. Starting with a renewed SLE is planned for 2016. Before conditioning system contained 140 parts, which were produced by independent suppliers. With 3D-printing technology and моделирования stratified by fusing this number dropped to 16, which also reduced costs by 57%. Fell and the assembly of the device.
In the manufacture of thermoplastic used Stratasys ULTEM 9085, which has a wide range of operating temperatures - from cryogenic to extremely hot. Two new Fortus 900mc can not print using metal, 3D-printers for this purpose until just selected.
Source: geektimes.ru/post/249410/
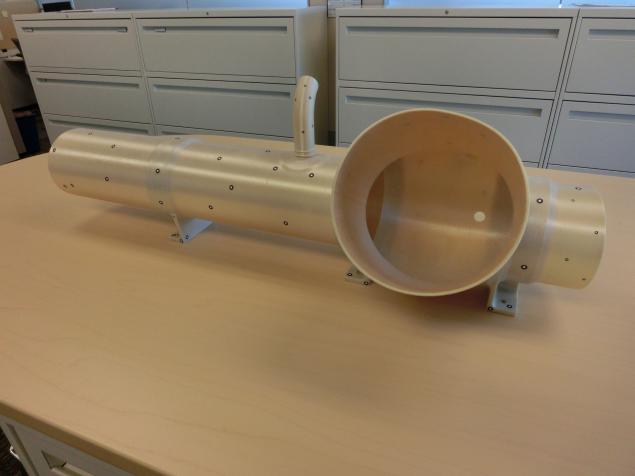
Photo ULA em>
In its new generation of rocket United Launch Alliance планирует use the 3D-printing to reduce production costs and simplify the development process by using rapid prototyping. Due to print parts made of plastic and metal is supposed to reduce the cost of a million dollars a year. In existing rocket Atlas V 3D-printing reduced the cost of the air conditioning system by 57%.
United Launch Alliance - a joint venture "Lockheed Martin" and "Boeing", which makes for about 12 launches per year. April 13 presentation at the Colorado chapter ULA Tory Bruno introduced a new missile with a fully Vulcan American engines. The first launch is scheduled for 2019, the price - from $ 165 million. It is assumed that the first-stage engine will be used again, for this they are going to shoot, Parachute and catch the helicopter. The new missile, its engines and bold plans for re-use are the answer to the current partial dependence ULA on Russian RD-180. It is noticeable that even the failed program's success landing the first stage rocket company SpaceX Falcon 9 precarious among the leadership of ULA.
Part of the Atlas and Delta rockets will also be printed, but ULA important to introduce 3D-press at the earliest stages of development, "Vulcan". Now choose the items to be printed. The lists of candidates more than 100 plastic and about 50 metal. It is expected that 3D-press will save about a million dollars a year.
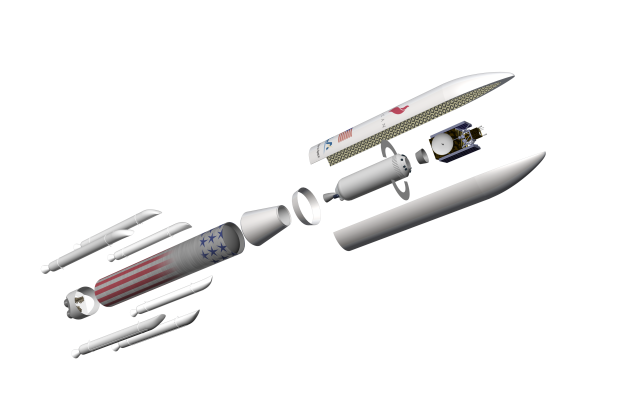
Five-meter version of the "Volcano», ULA em>
Detail for the rocket is expensive, and if it is to book with a third-party company, you should take the time to provide specifications and find a common language. If the item is something wrong, then it will have to be sent back for revision. Time spent not only this, sometimes contractors do not have time to complete their work on time. Own 3D-press simplifies control over the production process. Printing will be used in the traditional role - for rapid prototyping. It allows you to immediately make the necessary detail to engineer could touch her, to evaluate the functionality before leaving the order for its manufacture.
To implement these plans were purchased two printers Fortus 900mc from Stratasys. First of all, these machines will be used to create a new air conditioning system rocket Atlas V. The system is designed for delivery of liquid nitrogen preflight electronic components rocket booster to cool them. Starting with a renewed SLE is planned for 2016. Before conditioning system contained 140 parts, which were produced by independent suppliers. With 3D-printing technology and моделирования stratified by fusing this number dropped to 16, which also reduced costs by 57%. Fell and the assembly of the device.
In the manufacture of thermoplastic used Stratasys ULTEM 9085, which has a wide range of operating temperatures - from cryogenic to extremely hot. Two new Fortus 900mc can not print using metal, 3D-printers for this purpose until just selected.
Source: geektimes.ru/post/249410/
The first movie on "Youtube" 10 years old
Computer network Fukushima nuclear power plant is still running on Windows XP