947
CNC machine from the fact that it was ...
We all have any dream. Who is to do the Jeep for fishing, and someone to make a radio-controlled airplane. I have the same - to have the CNC machine tool ...
26 pics + several videos.
Rummage Chinese websites have understood what to buy for $ 400 crap is clearly not desirable, but what is less suited for TX worth 800 + shipping, customs clearance, etc. - I decided to do it myself.
For about a landmark was taken Chinese. Having estimated one another - knew so much aluminum, but still smooth and I did not find, and the process will be difficult. The choice fell on plywood 18mm thick. Few popyhtev and collecting thoughts together, embodied all in avtokadny drawing
But of course everything from plywood not carve, especially rails and spindles ... Helped the Chinese again, they have been the order of ball screws (transmission: Ball), as well as directing 12mm diameter units with linear ball bearings, thrust bearings, spindle mount.
Chinese - interesting people. I ask - and the ends of both will be treated?
- And how to you?
- What usually take?
- Yes, everything is different ...
At such moments, I fell into a stupor, as did the NC for the first time. Of information on the Internet such as the sea, but when it comes to the nuances - then the full horror ...
The photo is also present motor - DSHI-200-2. They will carry the entire apparatus. Why would they? Yes, just had. And drivers for them were made a few years ago (yes, I have long mature)
Well, there are details left to do ... In the market bought the plywood and cut.
While this small pile of wood similar to what has to happen. Sometimes, in spite of that I even began to doubt: D
The cutting and Porting I'm not the pryamorukih, so bet the radius of curvature of the hands and their demands to the imaginary result - went to market and bought a helper.
Transferring drawing on plywood, has started drilling
The first attempts to unscrew the Z-axis
Bottom View
In the course of the work had to come up with methods and tools :) That's made a hole in the end (they are needed for furniture screeds, plywood still, nothing closet?)
For clamp fixing spindle - also furniture with snap-bolts, they had to drill a little tricky to not sticking.
This carriage Z back
This carriage X. The most disgusting part in the machine (since krivorukost still is, even with the drilling machine to put it exactly vertically was not so simple)
Dye decided to matte paint sprays. (Sorry for the quality just was not always at hand camera down)
From time to time it constructs drinking the remains of my blood and eat the last nerve, so that the assembly process fell from Chronicle ... The first test X and Z- axes. (video)
But his hands - it's not interesting ... I wanted to revive. Torment with wires, screws, and other nasty things - happen!
But this is only a small part of the work ... a lot more. Otlipnuv finally from the contemplation of the cyclic movement of the carriage, went raschertivat sidewall portal
Sides dopilivat hand, took away lot of effort, so a piece fell again. That kind of bokovinok screwed to the support X-axis.
Some items come from drilling Dunno, that's something like bored longitudinal parts, which had to be screwed Y guide. They are located on the sides of the desktop.
Remembering the assembly process is difficult to refrain from using profanity ... Well, in principle, the lower part of the box with rails, all the same as X, or by very similar ...
It seems to have everything, motors are directing too. As the photo shows the squares, 4-yoh bolts - it stops for the bearings that hold the spindle.
But chegoto not enough, nothing to fix the workpieces.
What to do? Sawing ... habit of plywood. Sorry I could not find a video where the machine himself sawing the desktop, there is a photo completion. Dada, conventional nuts! And of course installed a hammer: D
Well, more or less - all assembly is bolted to the machine table.
For wires were purchased chain (again, the Chinese helped :)
Yes, 4 large nuts in the table - flat clutches, just in case HB
Here are the most stubborn square and very important detail - the red button!
Use an emergency stop to the machine.
Well, the rear view
And of course - to the test! In fact, it takes up to manufacture the table, yes, okay.
Do not ask what kind of crap unknown sawing machine :) Just a test.
After a few tests on the plywood wanted to upgrade the machine. I decided to replace the carriage Z on duralumin. I bought a piece of the market and forced to cut the machine itself. The sound in this case was hard to describe ...
Well, that was able to saw
And the view from the front of
As well as the accuracy of the test (and should have) - a small printed kerchief, size of about 22 mm, pililos engraver V-shaped with a diameter of 0.2 mm. The width of the track - 0.3 mm.
Posted in [mergetime] 1371939859 [/ mergetime]
That's basically all I'm pretty happy with the results (yes, I'm very picky :))
But in principle, for the machine of plywood made from inexpensive parts and materials at hand came out pretty well.
In the next series - alteration of the machine, replacement of all plywood parts in aluminum or iron replacement spindles (my faulty, then they work, but sometimes poschёlkivayut - here respect the Chinese people, said that does not matter to replace. A bolt is on the way).
All tired wrote: D relaxed, lit a cigarette and admire comments :)
Source:
26 pics + several videos.
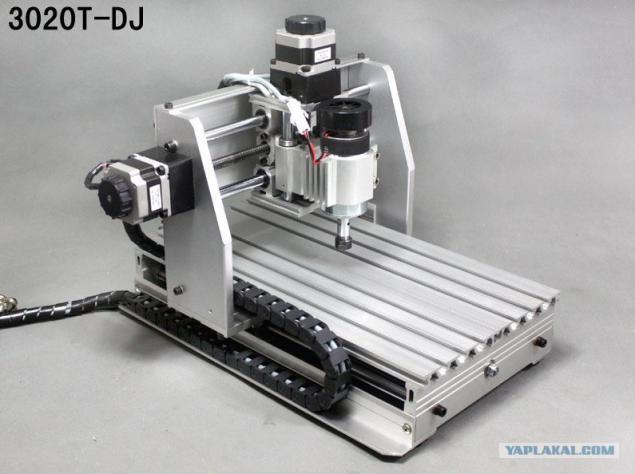
Rummage Chinese websites have understood what to buy for $ 400 crap is clearly not desirable, but what is less suited for TX worth 800 + shipping, customs clearance, etc. - I decided to do it myself.
For about a landmark was taken Chinese. Having estimated one another - knew so much aluminum, but still smooth and I did not find, and the process will be difficult. The choice fell on plywood 18mm thick. Few popyhtev and collecting thoughts together, embodied all in avtokadny drawing
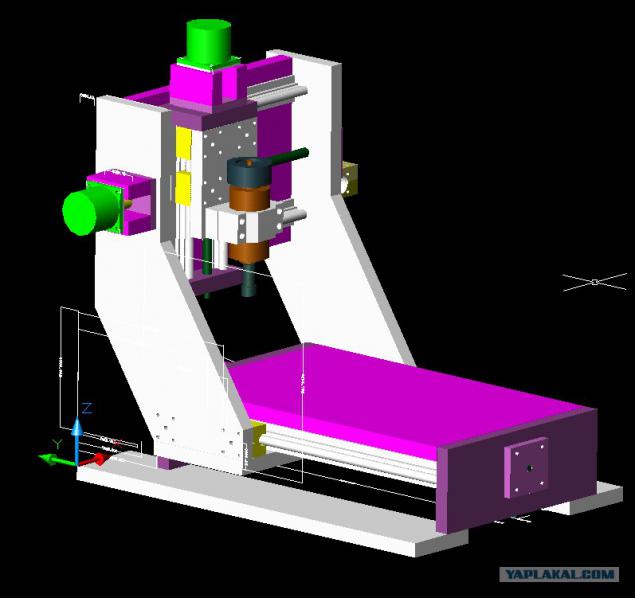
But of course everything from plywood not carve, especially rails and spindles ... Helped the Chinese again, they have been the order of ball screws (transmission: Ball), as well as directing 12mm diameter units with linear ball bearings, thrust bearings, spindle mount.
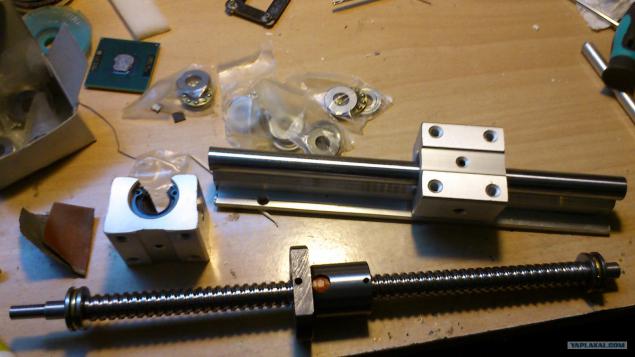
Chinese - interesting people. I ask - and the ends of both will be treated?
- And how to you?
- What usually take?
- Yes, everything is different ...
At such moments, I fell into a stupor, as did the NC for the first time. Of information on the Internet such as the sea, but when it comes to the nuances - then the full horror ...
The photo is also present motor - DSHI-200-2. They will carry the entire apparatus. Why would they? Yes, just had. And drivers for them were made a few years ago (yes, I have long mature)
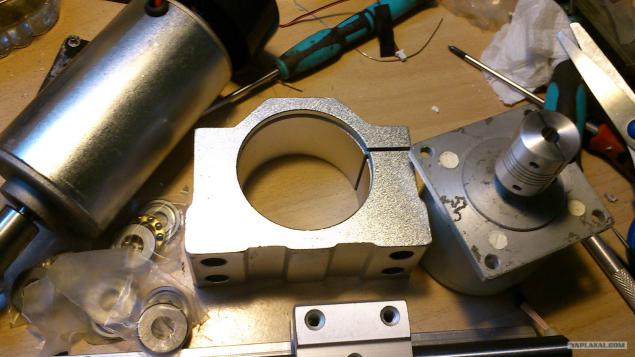
Well, there are details left to do ... In the market bought the plywood and cut.
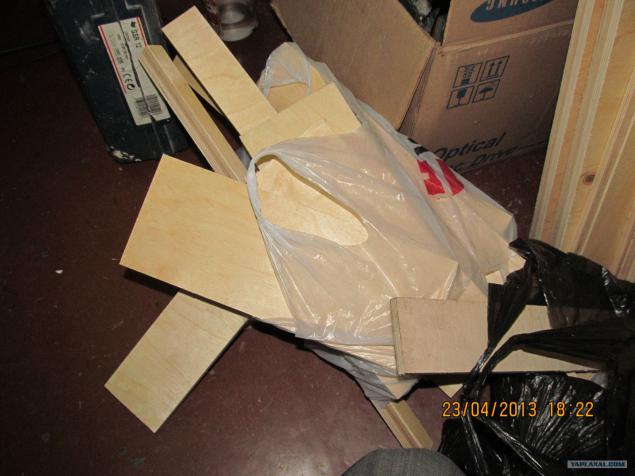
While this small pile of wood similar to what has to happen. Sometimes, in spite of that I even began to doubt: D
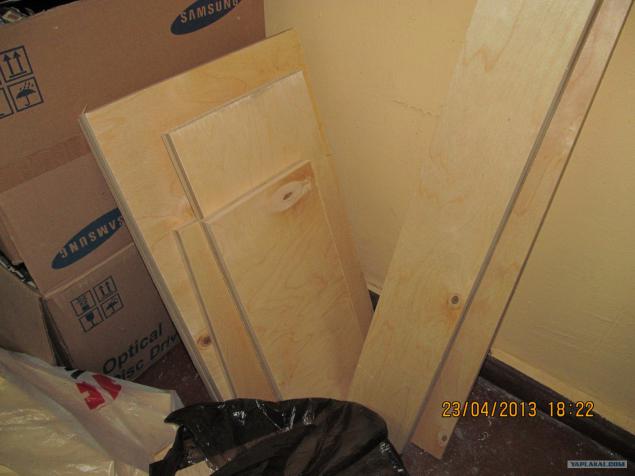
The cutting and Porting I'm not the pryamorukih, so bet the radius of curvature of the hands and their demands to the imaginary result - went to market and bought a helper.
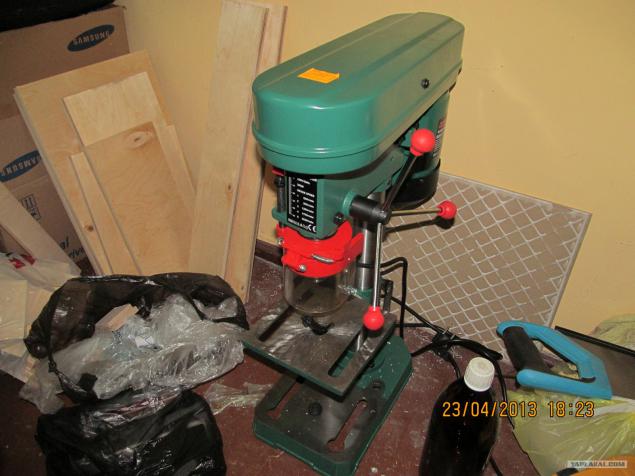
Transferring drawing on plywood, has started drilling
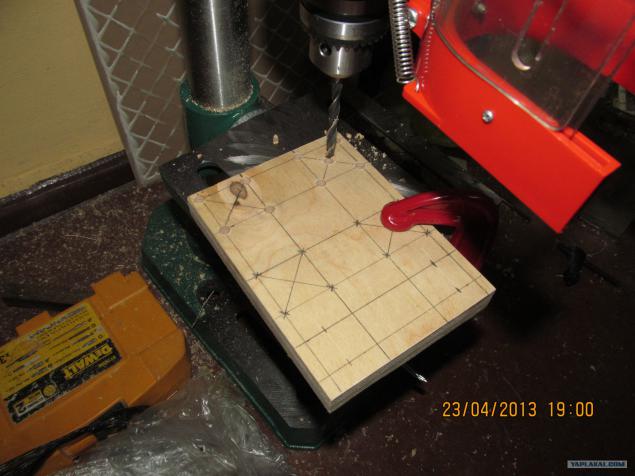
The first attempts to unscrew the Z-axis
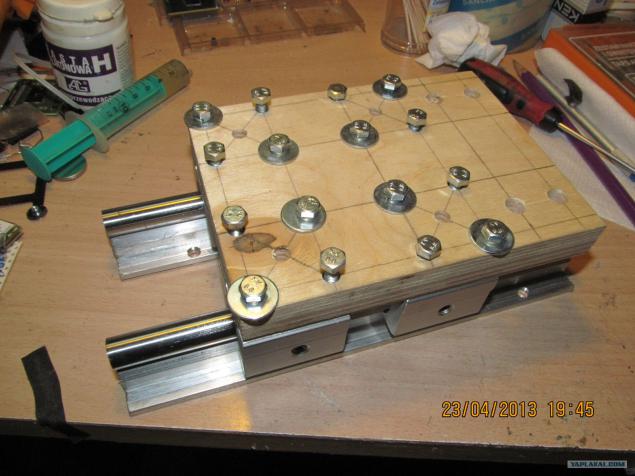
Bottom View
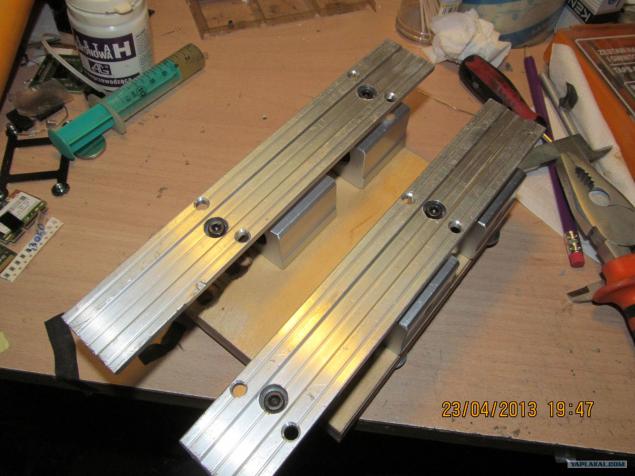
In the course of the work had to come up with methods and tools :) That's made a hole in the end (they are needed for furniture screeds, plywood still, nothing closet?)
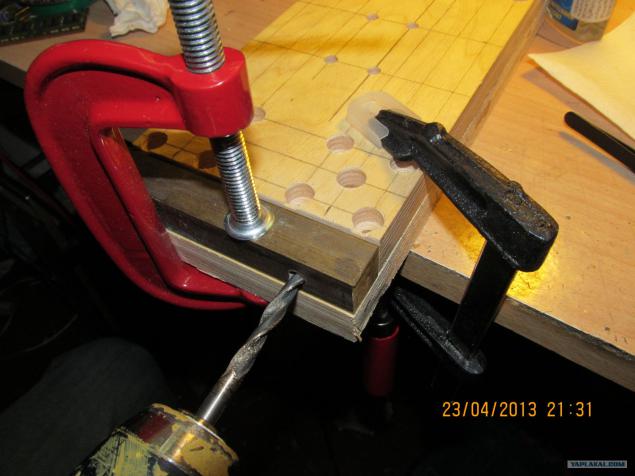
For clamp fixing spindle - also furniture with snap-bolts, they had to drill a little tricky to not sticking.
This carriage Z back

This carriage X. The most disgusting part in the machine (since krivorukost still is, even with the drilling machine to put it exactly vertically was not so simple)
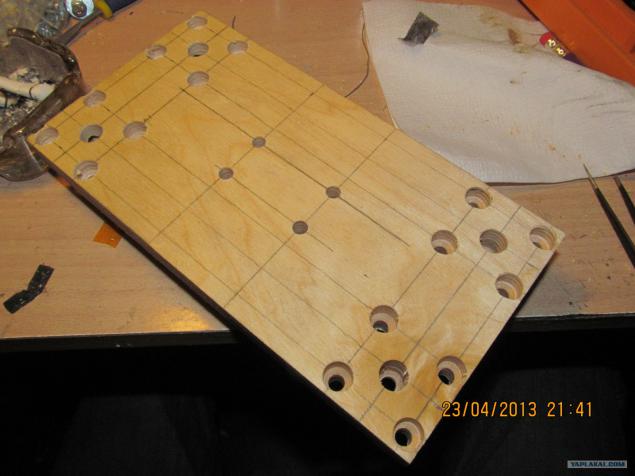
Dye decided to matte paint sprays. (Sorry for the quality just was not always at hand camera down)
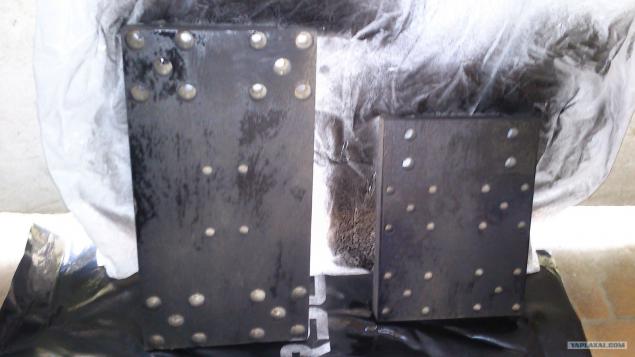
From time to time it constructs drinking the remains of my blood and eat the last nerve, so that the assembly process fell from Chronicle ... The first test X and Z- axes. (video)
But his hands - it's not interesting ... I wanted to revive. Torment with wires, screws, and other nasty things - happen!
But this is only a small part of the work ... a lot more. Otlipnuv finally from the contemplation of the cyclic movement of the carriage, went raschertivat sidewall portal
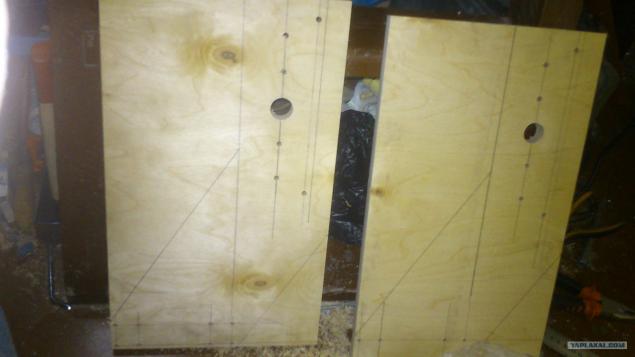
Sides dopilivat hand, took away lot of effort, so a piece fell again. That kind of bokovinok screwed to the support X-axis.
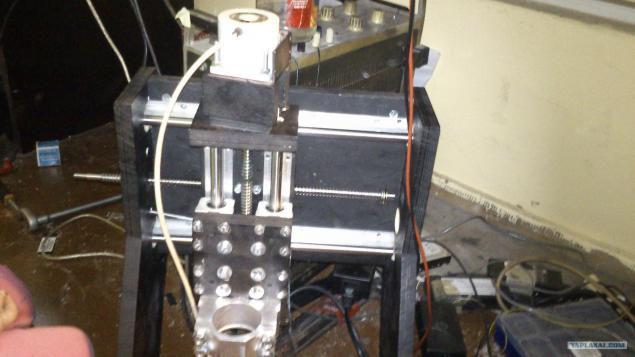
Some items come from drilling Dunno, that's something like bored longitudinal parts, which had to be screwed Y guide. They are located on the sides of the desktop.
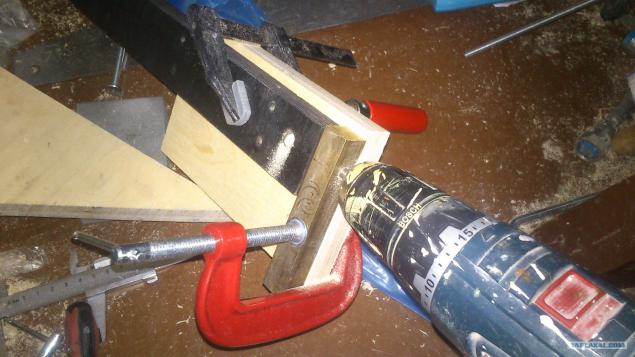
Remembering the assembly process is difficult to refrain from using profanity ... Well, in principle, the lower part of the box with rails, all the same as X, or by very similar ...
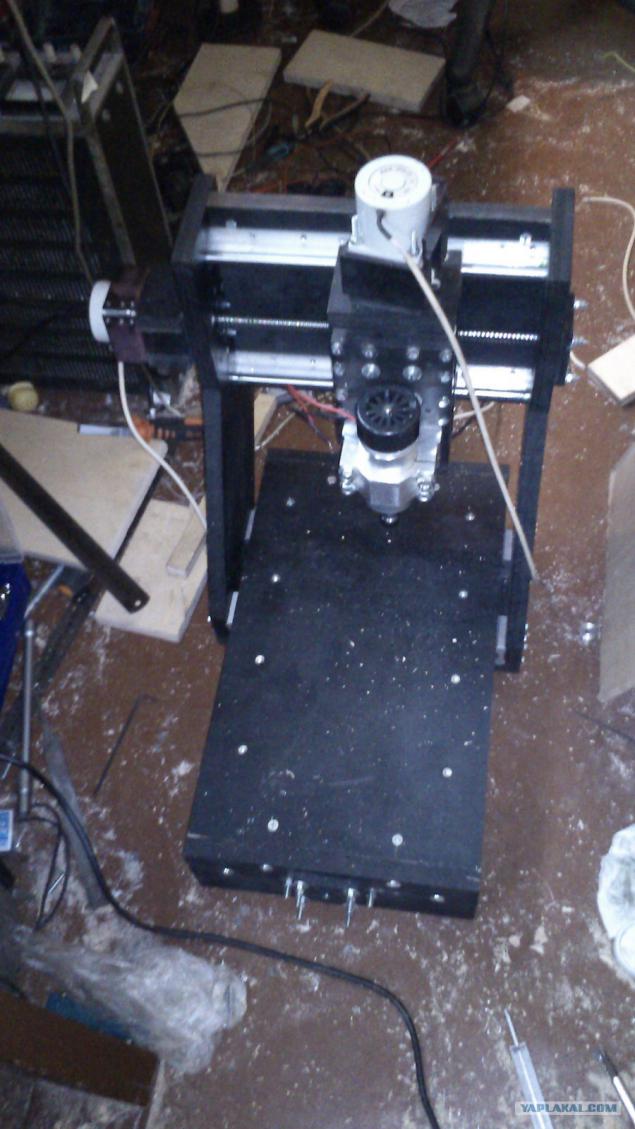
It seems to have everything, motors are directing too. As the photo shows the squares, 4-yoh bolts - it stops for the bearings that hold the spindle.
But chegoto not enough, nothing to fix the workpieces.
What to do? Sawing ... habit of plywood. Sorry I could not find a video where the machine himself sawing the desktop, there is a photo completion. Dada, conventional nuts! And of course installed a hammer: D
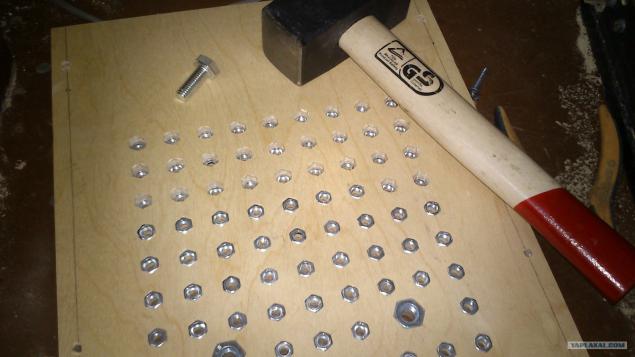
Well, more or less - all assembly is bolted to the machine table.
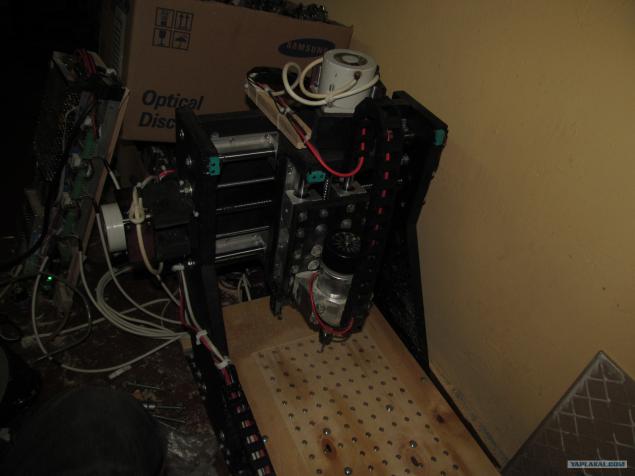
For wires were purchased chain (again, the Chinese helped :)
Yes, 4 large nuts in the table - flat clutches, just in case HB
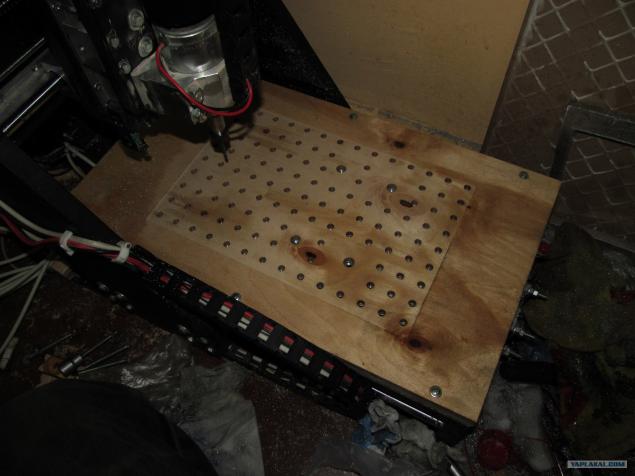
Here are the most stubborn square and very important detail - the red button!
Use an emergency stop to the machine.
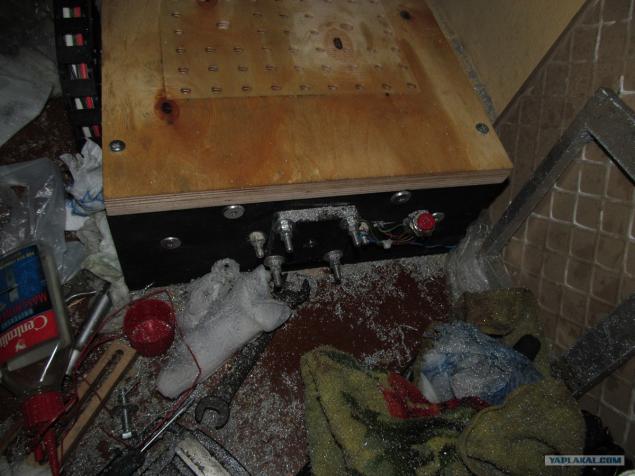
Well, the rear view
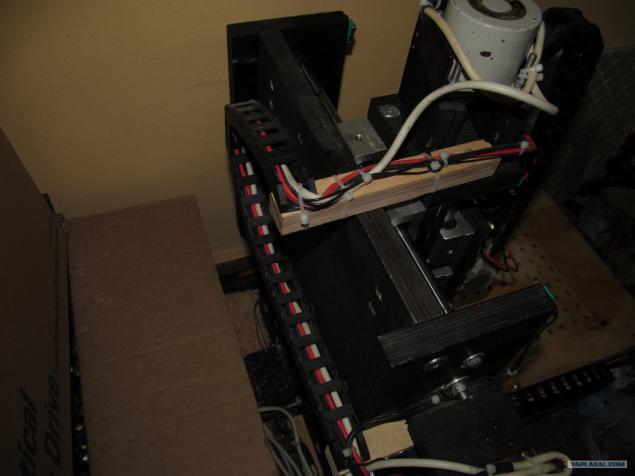
And of course - to the test! In fact, it takes up to manufacture the table, yes, okay.
Do not ask what kind of crap unknown sawing machine :) Just a test.
After a few tests on the plywood wanted to upgrade the machine. I decided to replace the carriage Z on duralumin. I bought a piece of the market and forced to cut the machine itself. The sound in this case was hard to describe ...
Well, that was able to saw
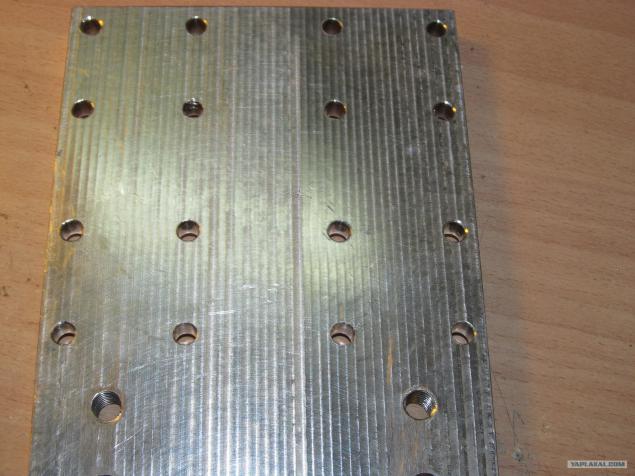
And the view from the front of

As well as the accuracy of the test (and should have) - a small printed kerchief, size of about 22 mm, pililos engraver V-shaped with a diameter of 0.2 mm. The width of the track - 0.3 mm.
Posted in [mergetime] 1371939859 [/ mergetime]
That's basically all I'm pretty happy with the results (yes, I'm very picky :))
But in principle, for the machine of plywood made from inexpensive parts and materials at hand came out pretty well.
In the next series - alteration of the machine, replacement of all plywood parts in aluminum or iron replacement spindles (my faulty, then they work, but sometimes poschёlkivayut - here respect the Chinese people, said that does not matter to replace. A bolt is on the way).
All tired wrote: D relaxed, lit a cigarette and admire comments :)
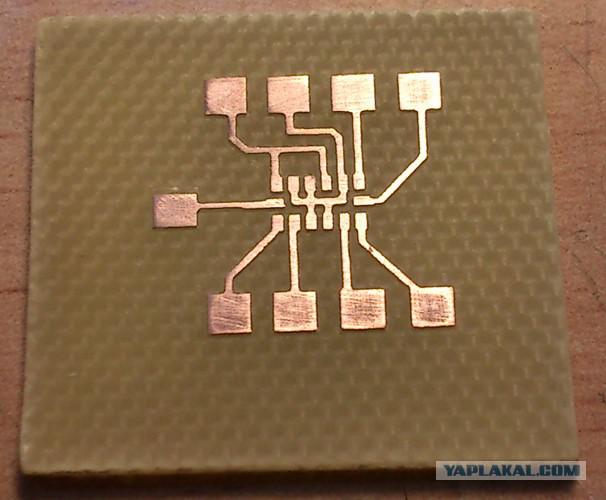
Source: