990
Assembling Lifan factory Derways
Pictures from the first private Russian automobile plant «Derways», successfully collecting Cherkessk cars of Chinese brands.
A few words about the company Derways. Name Derveis composed of the names of the founders, it is widely known in Karachayevo-Cherkessia brothers trees, and the English word "road» (ways). Initially, in 2002, it was a small car division of the holding "Mercury", which two years later released an SUV of its own design "Cowboy". In 2005, the Romanian company APO, which is a supplier of chassis, went bankrupt, and the owners have shifted production to the assembly of Chinese cars. Kits made in China, imported in Russia, then collected and sold. Now this brand Lifan, Jaime, Geely and Great Wall Hover. Production capacity of the plant - 130 thousand cars per year, the company employs at least 1,000 people, which is essential for Cherkessk. So, let's see how it looks. But before that, just in case, I warn that photo spread shot in the summer, a few months ago, there may be inaccuracies, please treat with understanding.
1. At the checkpoint. Right - the administrative building. Behind it is a large area of the plant, 23, 5 hectares.
2. Let's go directly to the customs area and the area where the containers are stored with a complete set, arriving here by sea from China, Chongqing, which is the headquarters of Lifan Industrial Group.
3. Mashinokomlekty unloaded, something delivered to the warehouse, which at once went to the welding shop.
4. Go to the welding shop.
5. The welding shop consists of three sections - sub-assemblies, the main welding line and the sample plot and straightening, where the body is sent to the painting (picture line at the end of the hall).
6. Welding partly automated and partly used manual labor.
9. Before you get to the next, paint shop, we give out special clothes, and we pass kraskosmesitelnoy room. Since Production dangerous it can be viewed only through the glass.
10-11. Line preparation for painting body 14 consists of baths in which each body immersion in a special cleaning solution passes first, and then it is applied to the primary primer by electrodeposition, after which the body is washed again.
12. Then superstructures fall on a line which is being processed seams and drying at high temperatures.
14. Clean the body before painting.
15. 8 painting robots in Japan are applied enamel. In the painting operation takes just 5 minutes, and to change the paint only 10 seconds.
16. The entire process is automated and controlled from outside the spray booth.
17-18. Paint shop consists of three floors, painting is carried out in the second to pull the car to the first, there is a special elevator.
20. After staining the body gets into a drying chamber in which it dwells for 45 minutes at a temperature of about 160 degrees.
21-22. Then superstructures move in the assembly shop.
23. Before you go to the assembly hall, we went to the neighboring areas, which set another assembly line.
24-26. It looks like a brand new assembly plant prior to installation of equipment in it:
26. These photos I made in the summer, now, I think, already doustanovit Equipment - January 2014 Derveis begins to produce new models, perhaps it will be precisely here.
27. And this is a general view of the current assembly plant.
28. There are two lines, they can produce up to 80 thousand cars per year.
29-31. Land assembly chassis.
33. Plot finish assembly.
35. Ready car leaves the production line. On the line, by the way, going at the same time cars of different brands.
36. The site diagnostics of German production.
37. Wash.
38. After that, the car stripped to the warehouse of finished products.
39. Shipment of car dealers is carried out by a private company "Yug-Trans", in which the presence of no less than 150 car carriers.
Even after I shot a photo spread with news feeds received information that the plant began assembling cars Taiwanese brand Luxgen.
Thanks to the administration for the tour!
timag82
A few words about the company Derways. Name Derveis composed of the names of the founders, it is widely known in Karachayevo-Cherkessia brothers trees, and the English word "road» (ways). Initially, in 2002, it was a small car division of the holding "Mercury", which two years later released an SUV of its own design "Cowboy". In 2005, the Romanian company APO, which is a supplier of chassis, went bankrupt, and the owners have shifted production to the assembly of Chinese cars. Kits made in China, imported in Russia, then collected and sold. Now this brand Lifan, Jaime, Geely and Great Wall Hover. Production capacity of the plant - 130 thousand cars per year, the company employs at least 1,000 people, which is essential for Cherkessk. So, let's see how it looks. But before that, just in case, I warn that photo spread shot in the summer, a few months ago, there may be inaccuracies, please treat with understanding.
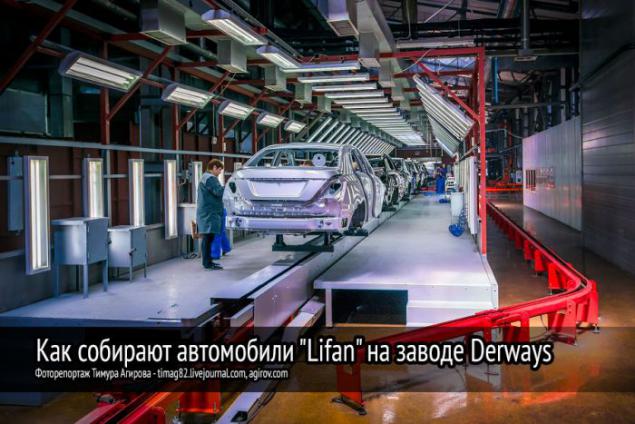
1. At the checkpoint. Right - the administrative building. Behind it is a large area of the plant, 23, 5 hectares.
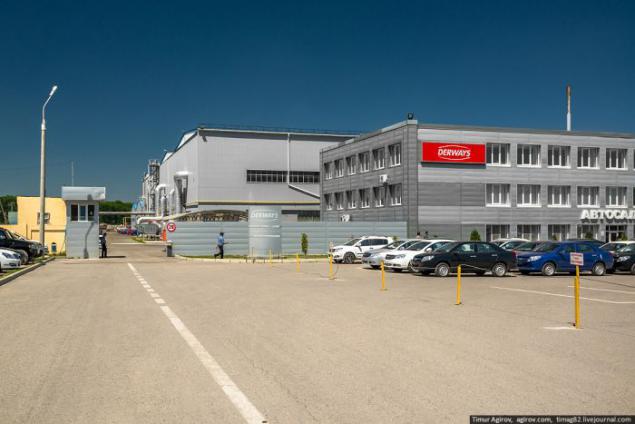
2. Let's go directly to the customs area and the area where the containers are stored with a complete set, arriving here by sea from China, Chongqing, which is the headquarters of Lifan Industrial Group.
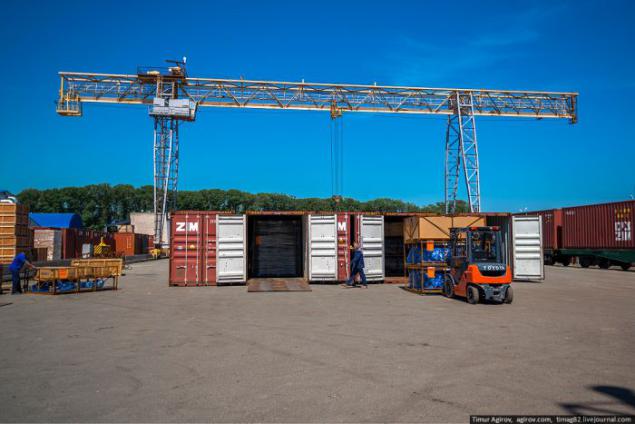
3. Mashinokomlekty unloaded, something delivered to the warehouse, which at once went to the welding shop.
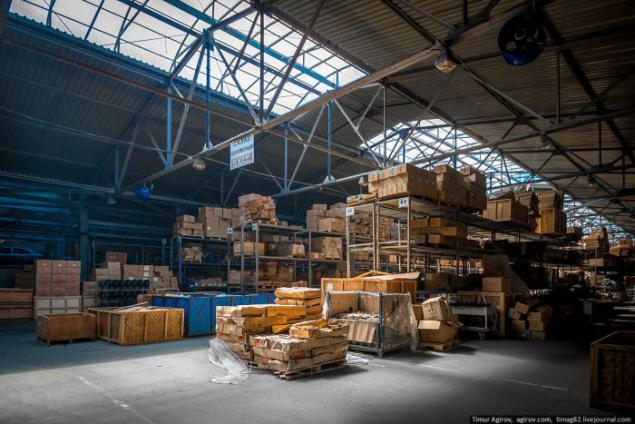
4. Go to the welding shop.
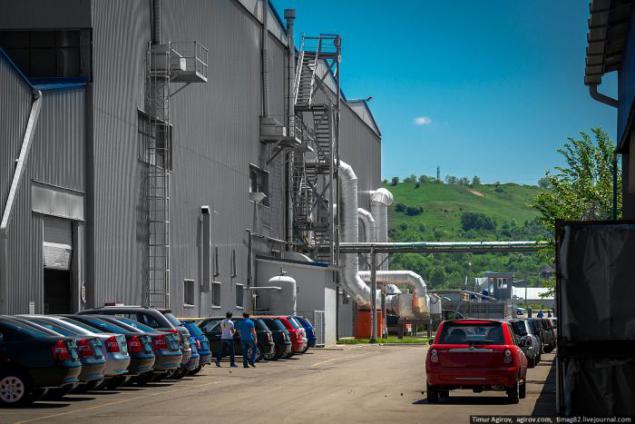
5. The welding shop consists of three sections - sub-assemblies, the main welding line and the sample plot and straightening, where the body is sent to the painting (picture line at the end of the hall).
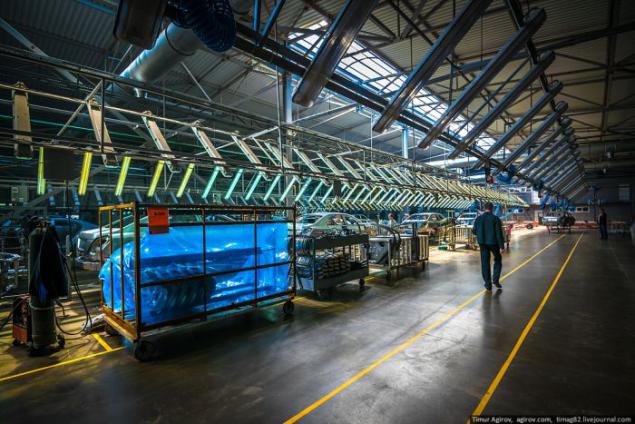
6. Welding partly automated and partly used manual labor.
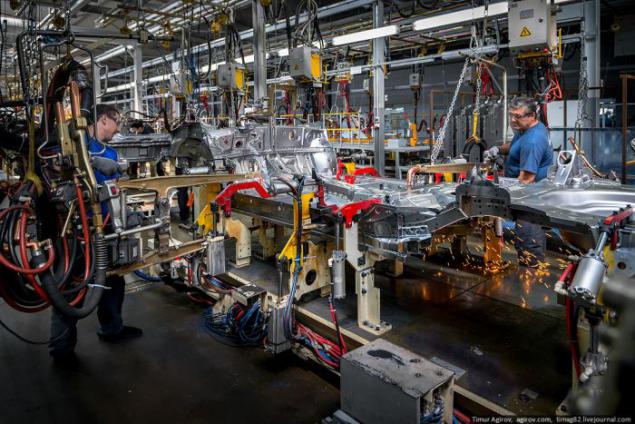
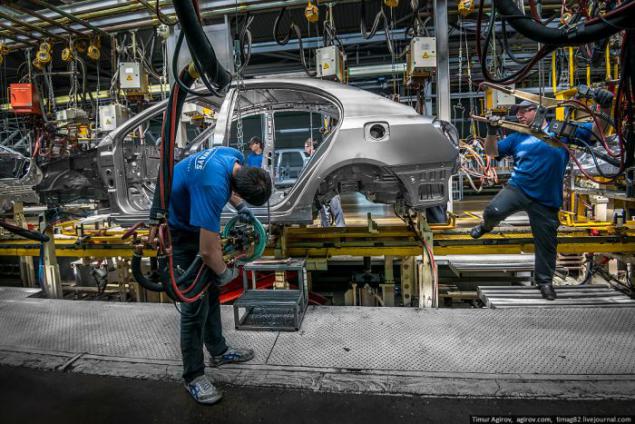
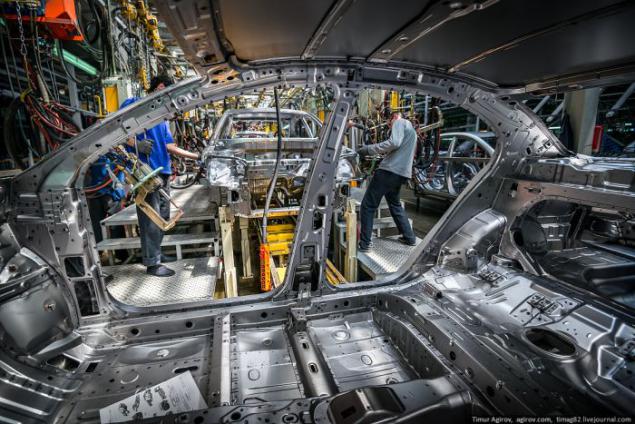
9. Before you get to the next, paint shop, we give out special clothes, and we pass kraskosmesitelnoy room. Since Production dangerous it can be viewed only through the glass.
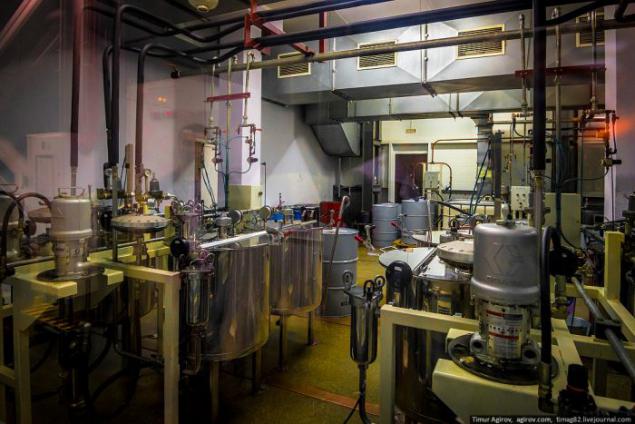
10-11. Line preparation for painting body 14 consists of baths in which each body immersion in a special cleaning solution passes first, and then it is applied to the primary primer by electrodeposition, after which the body is washed again.
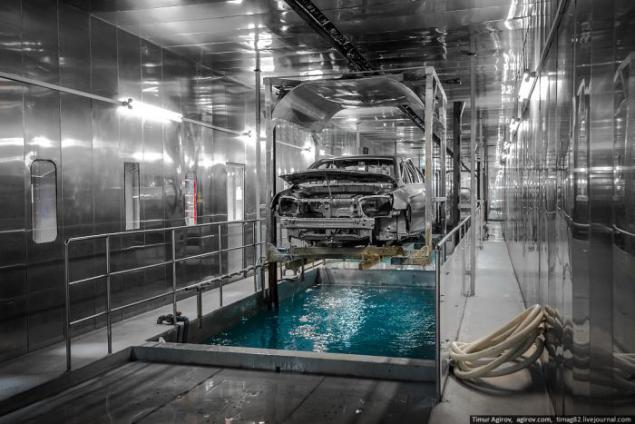
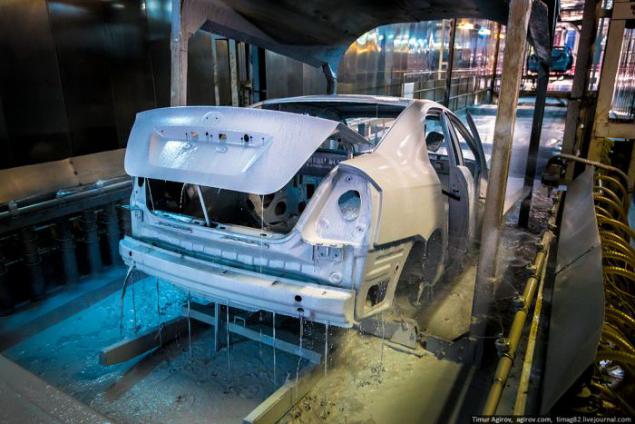
12. Then superstructures fall on a line which is being processed seams and drying at high temperatures.
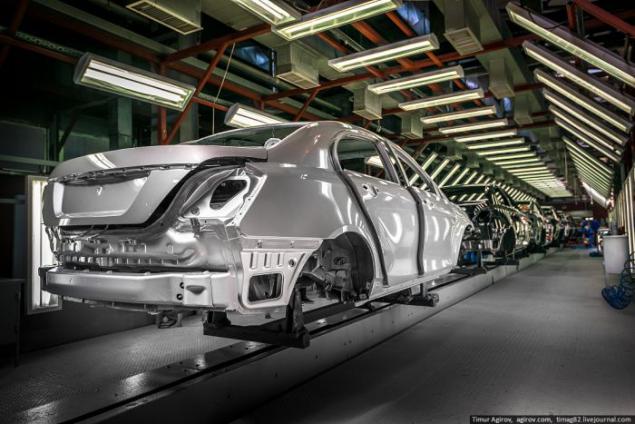
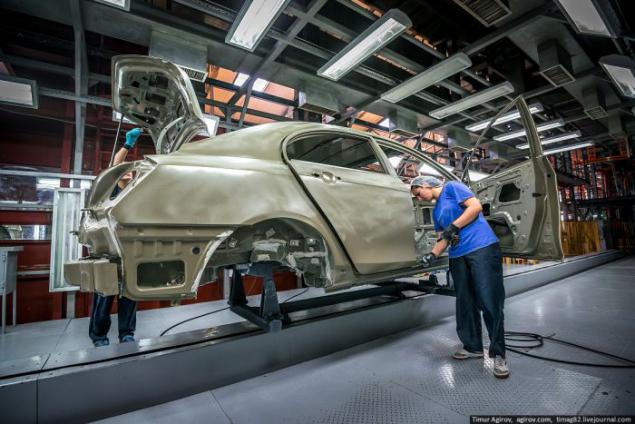
14. Clean the body before painting.
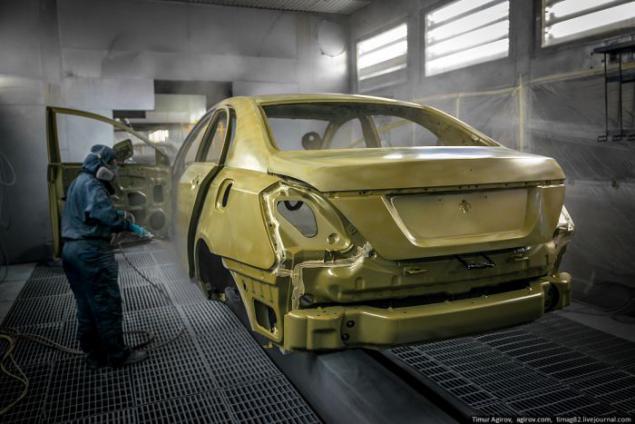
15. 8 painting robots in Japan are applied enamel. In the painting operation takes just 5 minutes, and to change the paint only 10 seconds.
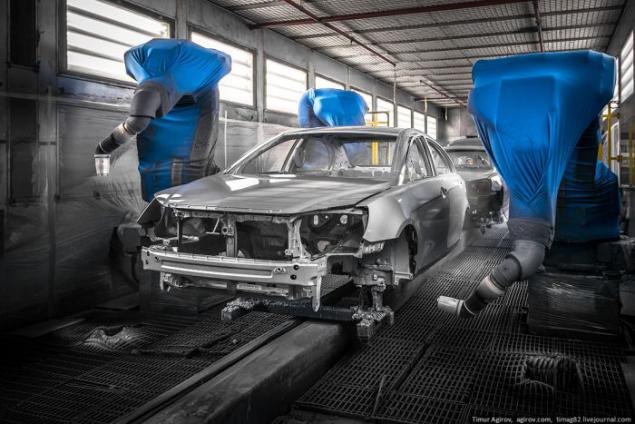
16. The entire process is automated and controlled from outside the spray booth.
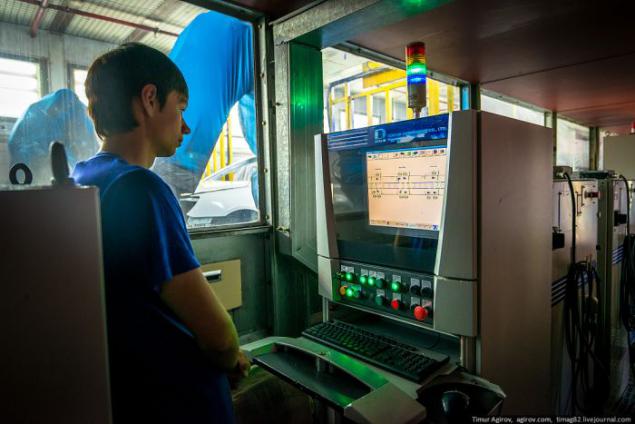
17-18. Paint shop consists of three floors, painting is carried out in the second to pull the car to the first, there is a special elevator.
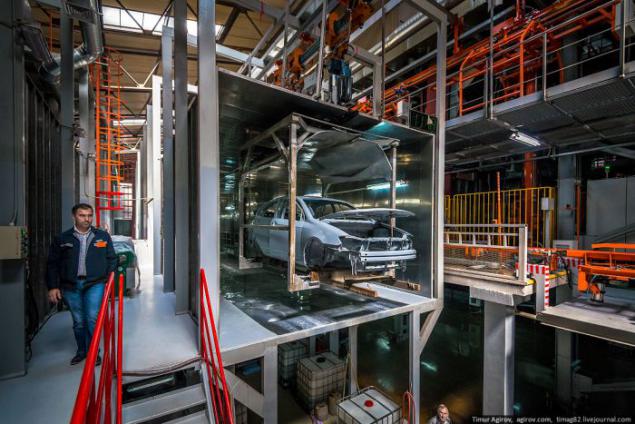
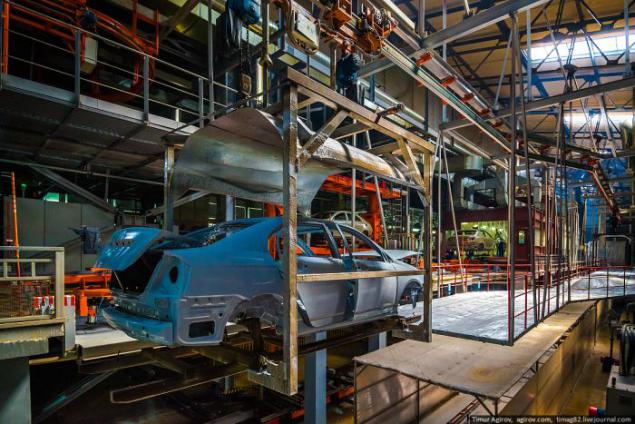
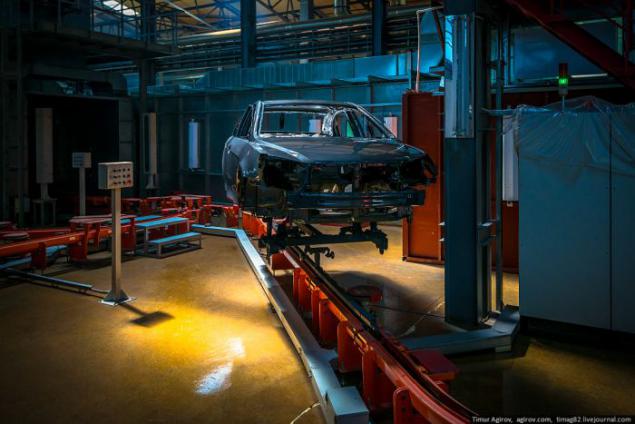
20. After staining the body gets into a drying chamber in which it dwells for 45 minutes at a temperature of about 160 degrees.
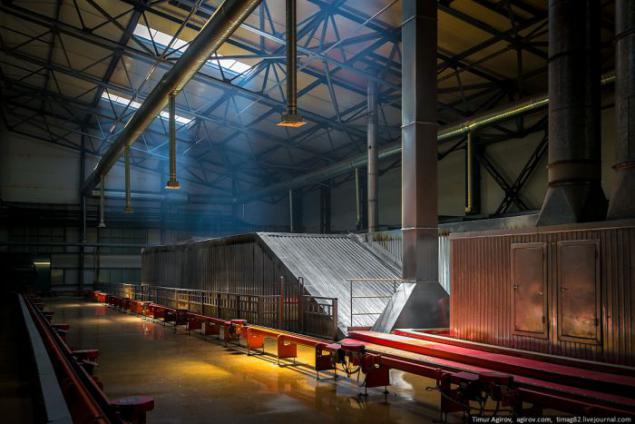
21-22. Then superstructures move in the assembly shop.
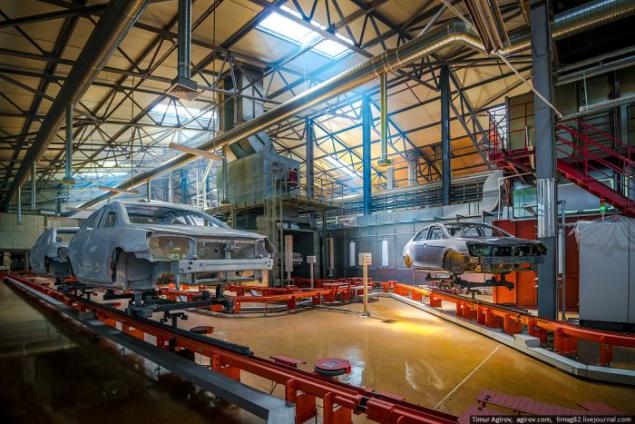
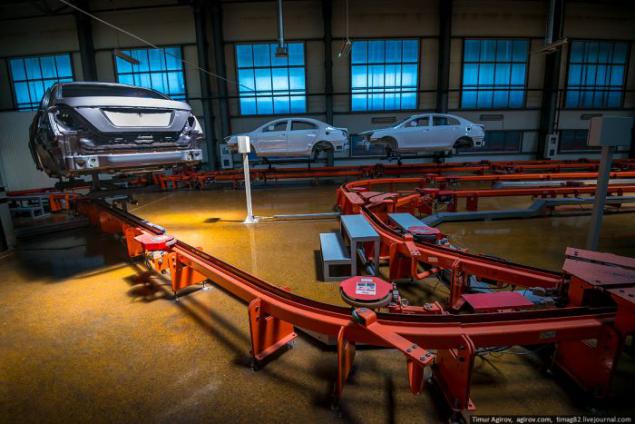
23. Before you go to the assembly hall, we went to the neighboring areas, which set another assembly line.
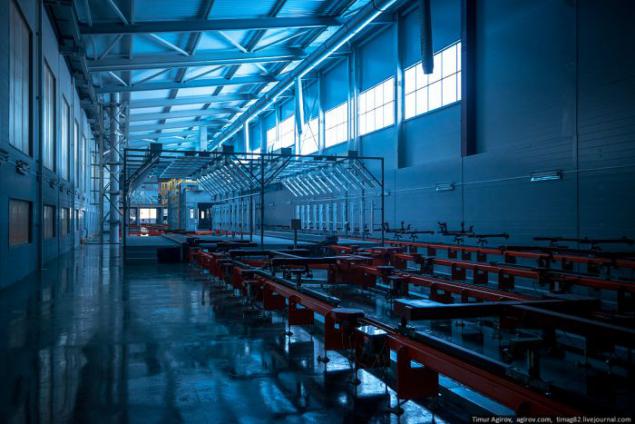
24-26. It looks like a brand new assembly plant prior to installation of equipment in it:
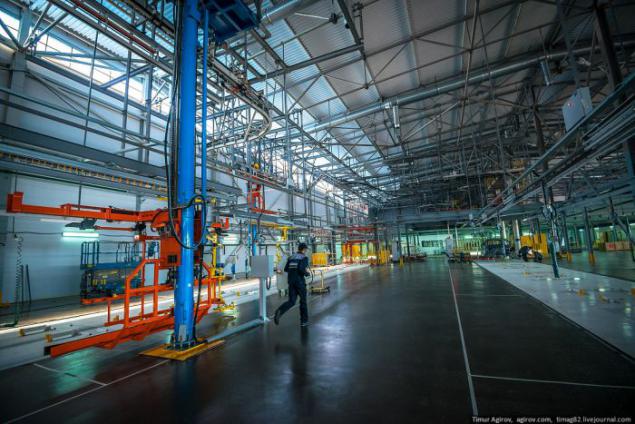
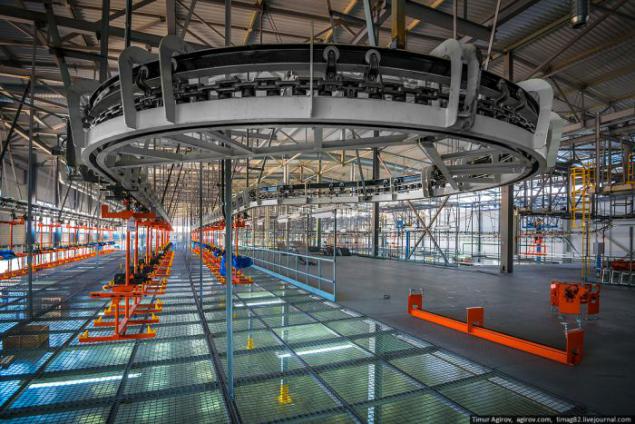
26. These photos I made in the summer, now, I think, already doustanovit Equipment - January 2014 Derveis begins to produce new models, perhaps it will be precisely here.
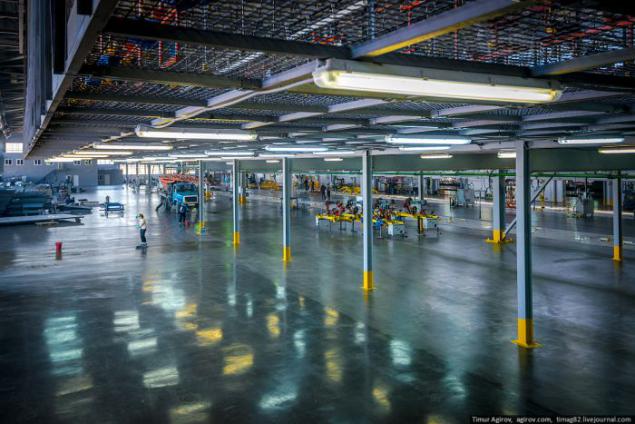
27. And this is a general view of the current assembly plant.
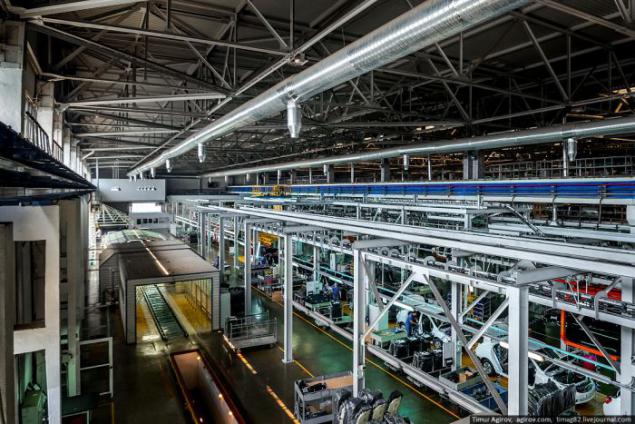
28. There are two lines, they can produce up to 80 thousand cars per year.
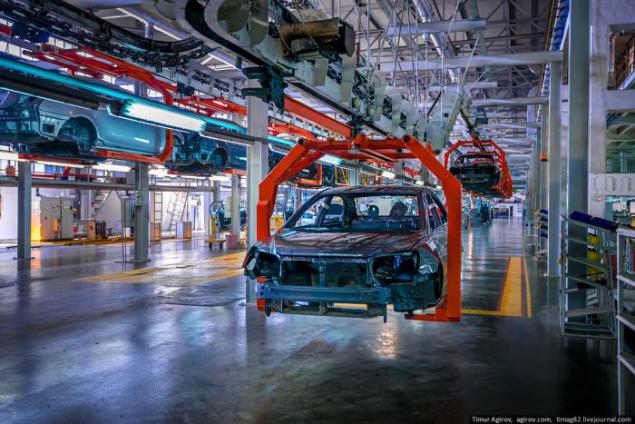
29-31. Land assembly chassis.
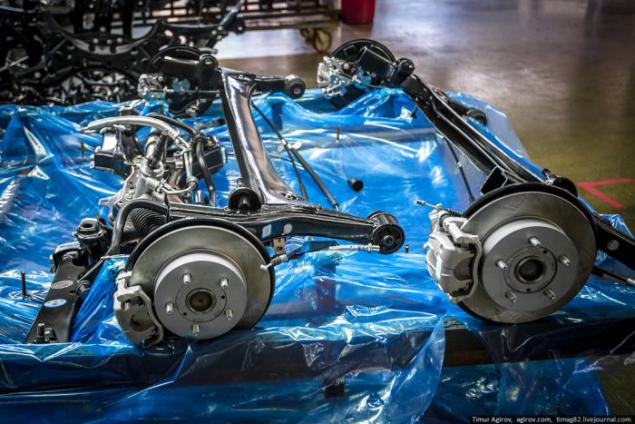
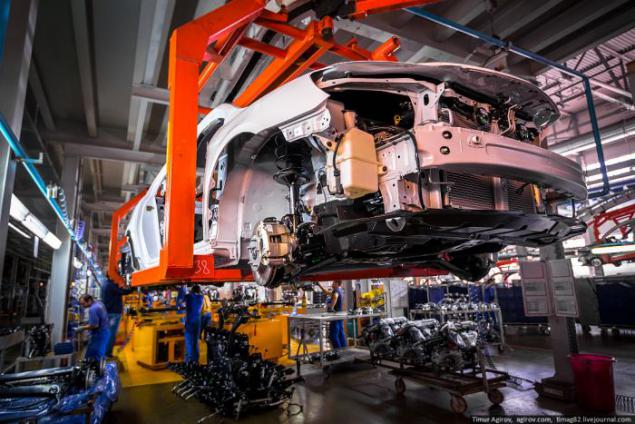
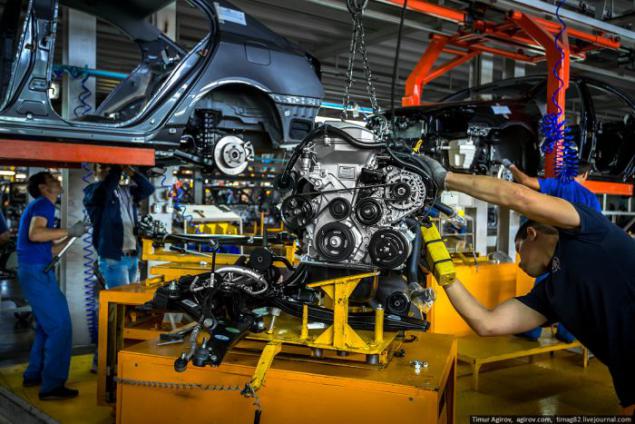
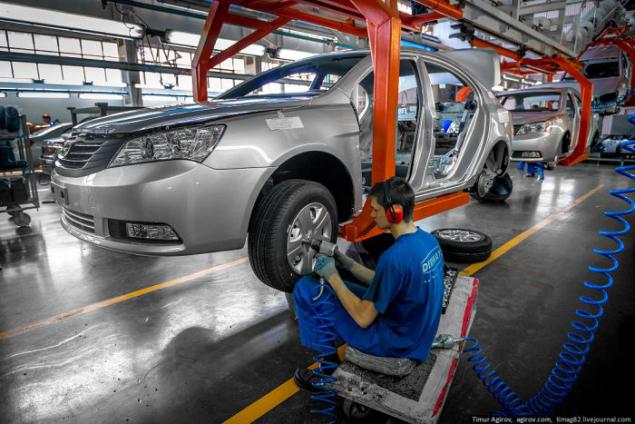
33. Plot finish assembly.
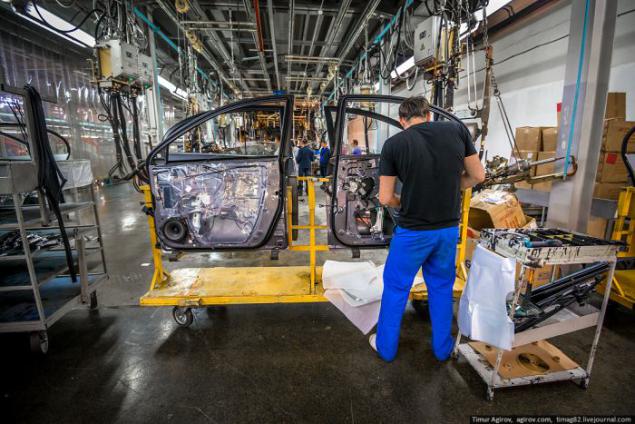
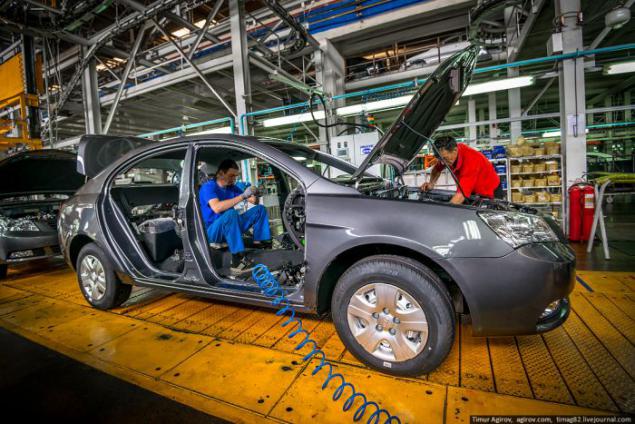
35. Ready car leaves the production line. On the line, by the way, going at the same time cars of different brands.
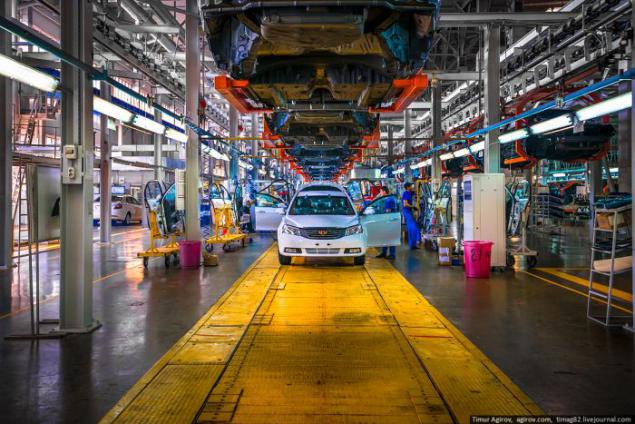
36. The site diagnostics of German production.
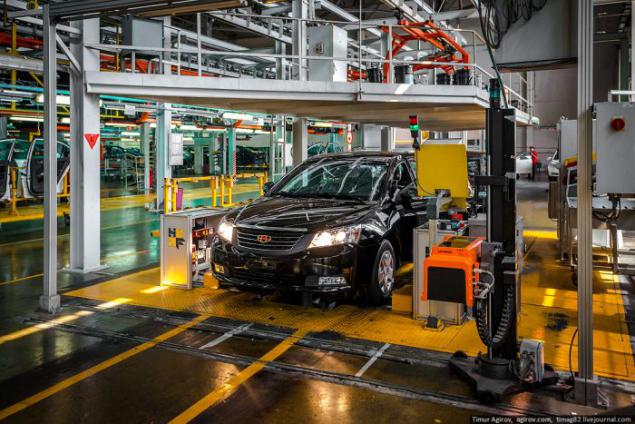
37. Wash.
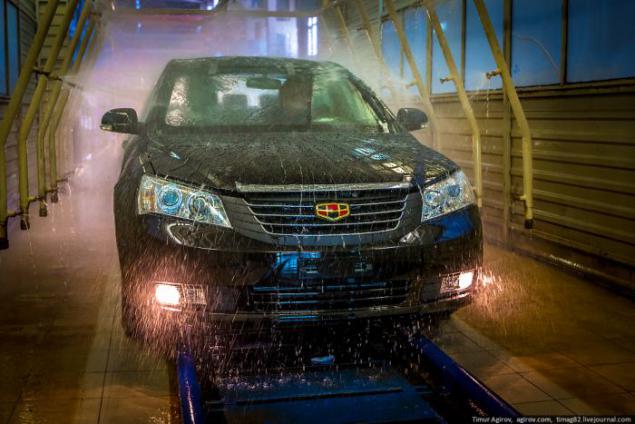
38. After that, the car stripped to the warehouse of finished products.
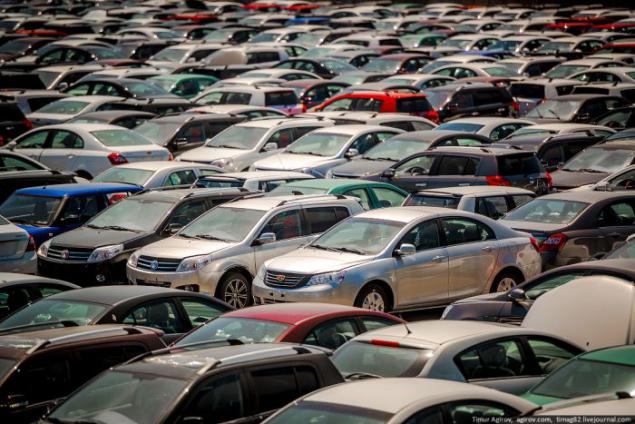
39. Shipment of car dealers is carried out by a private company "Yug-Trans", in which the presence of no less than 150 car carriers.
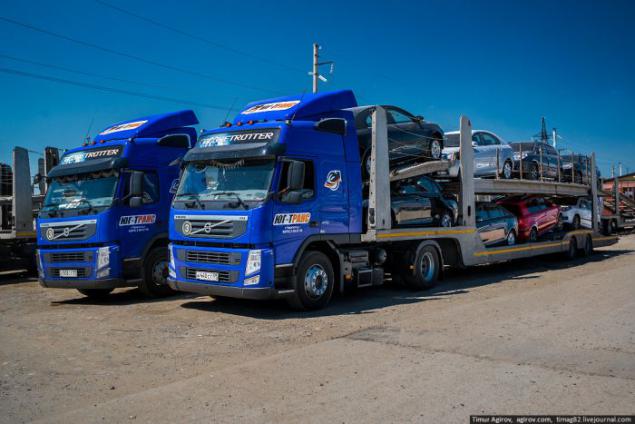
Even after I shot a photo spread with news feeds received information that the plant began assembling cars Taiwanese brand Luxgen.
Thanks to the administration for the tour!
timag82