842
Torrefied pellets
Torrefied, or bio-coal (black), pellets have a number of advantages compared to conventional, otherwise known as white. These advantages are manifested particularly clearly when co-firing torrefied pellets and coal at the thermal power plants (TPP).
For different market names hidden same well-known production process: firing of solid biomass (eng. — torrefaction) and subsequent granulation into pellets; similar technology is used in the roasting of coffee beans. The firing process was first used in the 1930-ies in France (the French verb torrefier, which is translated as "to roast", mostly used to denote the process of roasting coffee beans). Unlike coffee beans, solid biomass is burnt without oxygen at a temperature of 200-330 ° C.
Chemical analysis of the biomass after this firing showed that it acquires a large calorific value, energy consumption and improved compared to neeregirovannom biomass combustion results. The firing process is applicable to all types of biomass.
The Netherlands: ahead of the restof the Duiven is a small village in the province of Gelderland, near the border with Germany. Since its founding in the Roman period and to enter here into operation of a small brewery in our times, she has not played any meaningful role in the industry of the Netherlands.
That all changed the last few years. The Duiven became a major center of the global pellet industry. RWE Innogy — a 100% subsidiary of one of the world's largest energy concern RWE (which has a share "Gazprom"), together with the Dutch company Topell Energy (39% of which is owned by RWE) has invested 15 million euros in the construction of the largest in the world today for the production of torrefaction pellets.
Torrefied pellets (TP) by the process of torrefaction acquire the characteristics that distinguish them from ordinary pellets the better. Suffice it to say that the caloric value of one ton of pellets tarifitsirovannyim higher than one ton of pellets neeregirovannom.
Why the German concern RWE is implementing a project abroad? The answer is simple: in accordance with the laws of the Netherlands, all coal-fired power plants are bound together with the coal to burn any biomass, for that state, since 2002 and to this day, guaranteed to pay this TPP grant in the amount of 5-6 Euro cents for every kilowatt-hour of electricity generated in co-firing of biomass. In Germany such conditions for TES yet (according to the German law on renewable energy as only electricity generation from stations up to 20 MW at 100% biomass). Therefore, sales of industrial wood pellets in Belgium and the Netherlands, which has also a similar Dutch state program grants under co-firing, are much higher than in Germany. Based on the above described advantages of TP, a European pellet producers and energy companies are doing now a bet on torrefied wood torrefied pellets and other solid biomass with the aim of obtaining competitive advantages over manufacturers classic pellets.
Plant in Duiven was commissioned in the spring of 2011. The line capacity torrefazione and granulation — 8 tons per hour, raw material is wood waste. "Now the main task, — speaks the employee of the Department of venture capital investment of RWE Innogy Crispin lake is the output of the plant at the highest possible level of annual volume of output not less than 60 kt". Mr. lake was in charge of this project from the stage of pre-design work, so the process of torrefaction knows everything. In his opinion, the main problem of plant in Duiven is ensuring continuous supply of raw materials in the industrial scale, which today is not easy to achieve not only in the Netherlands, but also in some other Western European countries. Even have to sort and recycle the so-called old wood — any wood products, overage, down to the furniture, excluding parts coated with paints. Torrefied pellets are supplied to the coal plant working adjacent to the village town of Geertruidenberg.
How does the so-called "torbed reactor" (Torbed Reactor) — patented main module of the plant of torrefaction pellets in Duiven?
Raw materials in the form of ground wood biomass fed to the reactor and heated without access of oxygen to a temperature of 220-330 °C. the Heating lasts from several seconds to one hour, depending on the established mode of torrefaction. During this process, the gas formed, which provides the high temperature necessary for the process of torrefaction. In order to start the reactor, using an external energy source. Once the reactor reaches the desired operating temperature, the process is closed without energy supply. After completion of the mode of torrefaction, the duration of which is determined depending on the quality of the input materials, the output is a homogeneous product with high energy density, excellent quality of grinding, humidity 5 %, containing less than neeregirovannom biomass, the amount of impurities. In addition, torrefied pellets become hydrophobic, i.e. the ability to repel moisture and to resist the processes of decay and fermentation, which gives the opportunity to store them even in the open air.
"Compared to traditional pellets TP have many advantages, and most importantly — is, of course, increased energy density," — said the expert of the Department of bioenergy and environment Austrian Institute of technology and chemistry in Vienna Martin English. During torrefaction the biomass properties are changed radically: it destroys the structure of cellulose, evaporates much of the moisture, the formation of free molecules of carbon, hydrogen and oxygen. On the structure of the torrefied pellets is similar to coal, because in the course of chemical processes in wood and other plant biomass by torrefaction all the carbon is converted into biochar (unsaturated hydrocarbons) are oxidized and react with the oxygen molecules. Biochar has the same properties as fossil coal, and can easily be burned along with him. Due to the fact that as a result of firing is greatly reduced moisture content of torrefied pellets, they become brittle and are crushed more easily than standard pellets. Therefore, when co-firing with coal TP no need to upgrade the technological fuel supply line — no need to install a pellet crusher, and a separate feed system of pellets.
In most coal fired power plants used the torch method of burning fuel, and coal before feeding to boiler is crushed to pulverized condition and industrial pellets co-firing on the crusher are crushed to the size of about 2 mm. Torrefied pellets are milled together with coal, and due to the above-described properties, their grinding requires less energozatrat than the classical grinding pellets. Torrefied pellets can be pre-mixed with coal at a fuel depot power station. Since the energy density of the TA superior to ordinary pellets, reduced transport costs and warehousing, for storage of torrefied pellets does not require any special dry room, they can be stored even in the open air, together with coal. Simple wood pellets with this storage, due to the biological activity of the wood absorb moisture from the air, lose calorie, rot and water resistant and are destroyed. Torrevieja also allows to reduce the sulfate content of the pellets. But perhaps the main motivation for the application of torrefaction in Europe environmental focus is the use of torrefied biomass (reduction of greenhouse gas emissions when co-firing with coal) and the limited resource base for the production of ordinary wood pellets. The demand for energy wood is increasing every year and even increasing exponentially the use of energy plantation of plants does not solve the problem of shortage of raw materials for biofuel production.
The quality of the raw materials for the manufacture of pellets torrefazioni not to meet such stringent requirements as to quality of raw material for wood pellets is simple, — for the production of TP you can use chips of the lowest quality or the crust. The resource base for the manufacture of torrefied pellets is expanding due to the fact that in the process you can use straw, hay, residues from the production of vegetable oils, sugar beet processing, other agriculture waste, municipal solid waste (MSW), and even various plastics. To torrefazioni can be a mixture of different solid biomass. For example, the company FoxCoal in the Netherlands have torrefazione plastic along with scrap paper and got the high quality granules, which in many ways superior to coal. By the way, torrefied biomass is often called biochar.
In the Netherlands, created the Association of torrefaction (The Dutch Torrefaction Association — DTA), which includes: company 4Energy Invest from Belgium, the Netherlands research center for energy (The Energy research Centre of the Netherlands, ECN) and the Dutch company FoxCoal, Topell Energy Torr-Coal Technology.
Technology of torrefaction of biomass are doing in Holland and other well-known companies, such as BTG (Biomass Technology Group). The Netherlands is firmly in first place in the world by number of companies and public institutions working in this field.
Table 1. The influence of process parameters of torrefaction on structure
torrefied wood
In 2006, the Dutch specialist in thermodynamics and pyrolysis of biomass mark Jan Prins in the journal, devoted to Analytics and the practical application of pyrolysis (Journal of Analytical and Applied Pyrolysis), as well as in the work published by the University of Eindhoven (Eindhoven University of Technology, Environmental Technology Group, Department of Chemical Engineering and Chemistry), cited the results of thermodynamic studies of the processes of torrefaction and gasification of wood, which he conducted jointly with a group of researchers. From these results it follows that the characteristics of torrefied wood directly depend on the type of wood used, the duration and temperature of the process. In table. 1 shows the results of comparison of characteristics of torrefaction of willow before and after under the two regimes of the process.
Prospects of torrefaction in GermanyIn Germany, unlike other Western European countries, the use of torrefied biomass is seen only in the long term. Wood pellets are used in the German market is almost 100 % only in power in utility boilers for heating residential sector, farms, small industrial enterprises (in contrast to the Netherlands, Belgium, UK, where pellets are used mainly for electricity generation). In Germany, pellets are burned in boilers up to 300 kW (in private households) and small boiler plants with capacity up to 3 MW.
At the forum, held at the international exhibition pelletan (Interpellets), which is held annually in Stuttgart, Deputy Chairman of the German Association of producers of pellets (DEPV) Hans Martin Behr said that today Torrevieja is irrelevant for the power system of Germany. He believes "fundamentally incorrect attempts to increase the efficiency of operating today, the European TES, most of whom work on "prehistoric equipment", due to the combustion of new generation biofuels. Why not solve this problem by means of modernization of power plants for optimum burning of common biomass?"
Such statements, likely due to the fact that now in Germany, as has been pointed out many European experts, there is an overproduction of wood pellets. In 2001, Germany produced 1.86 million tons of pellets and consumed only 1.4 million tonnes when the actual performance of all pellet plants of 2.7 million tons per year. In 2012, according to forecasts, the country will produce more than 2 million tonnes of wood pellets. Most of this production corresponds to the standards Din+ or the new European standard EN-A1, A2. Industrial pellets are produced in small volumes, as thermal power plants operating on solid biofuels in Germany use mainly wood waste (wood chips, waste sanitary felling, thinning, landscaping, old wood, etc.).
And the export of such granules from Germany at a power plant in the Netherlands is not competitive producers in the U.S. and Canada, where production costs are lower, and transport costs when shipping across the Atlantic to Rotterdam large ocean-going vessels per ton is much less than the cost of transport by road or rail from Germany.
In Germany there really are no economic prerequisites for the production of torrefied pellets. Local of wood raw material for thermal power plants is enough. But for other types of biomass annually to generate significant amounts of raw materials. For example, straw, according to German research centre for biomass (DBFZ), can be used from 8 to 13 million tons per year. And the first and only thermal power plant in Emsland, using baled straw, put into operation only this year.
However, some German research centers and energy concern, trying to keep up with the times and conduct a study of torrefaction of biomass, getting to these development grants from the EU. Since January 2012 such work under the 7th Research programme on bioenergy the EU has DBFZ; date of completion of research and presentation of results in 2015. The project involved more than 20 European companies and research centers. They include subsidiaries of the major European energy concern, such as RWE Innogy, E. on UK, Vattenfall AB, the Austrian research Institute for chemistry and technology (OFI), the energy research Centre of the Netherlands (ECN). Director of Department bioenergy systems, DBFZ, Janet Witt says that this center is the focal point of the entire project in the course of experiments and research will be torrefication different types of solid biomass co-firing torrefied biofuels obtained from lignite and coal in different proportions. Based on the results of the research will make recommendations for producers of solid biofuels: what is biomass and how best to torrefazioni. Tests will be carried out on reactors of different types: fixed, movable, rotary-drum reactor, fluidized bed, etc. Then torrefied biomass will pelletize and briquetting in order to determine which equipment is most suitable for these purposes. Torrefied pellets and briquettes will be tested for the preservation of properties during storage under open air (tested for reaction with the soil layer and water repellency).
RWE Innogy in 2009 set demonstration equipment for the torrefaction of biomass in Talgatom Institute (Gas-Waerme Institut) in Essen in the framework of another research project, in which participate: the Ruhr-University of Bochum (Ruhr-Universitaet Bochum), Higher technical school in Aachen (Technische Hochschule Aachen), the company "Thyssen-Krupp metal" (Thyssen Krupp Steel), manufacturer of equipment for granulation of biomass "Poli münch GmbH" (Muench Edelstahl GmbH) and the company "Hitachi Power" (Hitachi Power Europa). Since 2012, this project includes not only scientific research work on the torrefaction of biomass, but also work to find other opportunities to improve the quality of solid biomass for more efficient combustion, particularly in conjunction with coal.
The management of energy Vattenfall is one of Europe's leading electricity producers (mainly in Germany and Sweden) on coal-fired power plants — production of torrefied pellets in a volume of 5 million tons per year by 2020 on the plants that will be built in the United States and South America. Director of group planning and the use of biomass Ulrich Rusch, however, tells about these plans quite carefully, given that today only implemented small pilot projects of torrefaction and on this basis to launch large-scale production is not easy. Still required to conduct all sorts of tests, and explore a real working technology of torrefaction. For these purposes it is planned to purchase torrefied pellets from 40 manufacturers around the world, and at the Berlin thermal power plant "Reuter West" group to conduct the technical testing for the joint combustion of torrefied pellets with coal in varying proportions. Preliminary tests of co-incineration of industrial pellets, or as they became known recently, white pellets (Whitе Pellets), coal-fired power plants of the concern showed that the mixture of pellets and coal should be not more than 20% of the white pellet of total fuel burned at the station. In the case of using torrefied (black) granules and this number could be increased to 50-70 %.
Many of the above-described research in Germany are also due to the fact that in 2018 the state will cease subsidizing the coal mining industry. 15 July 2011 entered into force the new Law on coal (Steinkohlefinanzierungsgesetz) governing state subsidies for coal mining in Germany and state aid closed mines and laid off miners. The amount of aid will gradually decrease and by the end of 2018 it will completely stop. The possibility of extending subsidies excluded, since the agreement of the European Commission on new grants were received in 2011, only under the condition that in 2018, this work will be completed. Probably this year and that will end the era of coal production in Germany, if only by the time energy prices will not grow much.
In other European countries? In 2008 in Sweden, the company BioEndev (Bio Energy Development North AB) launched a pilot project for the torrefaction of biomass. In 2009, she produced the first batch of torrefied biofuel and received funding from the Swedish energy administration for the creation of industrial torrefication installation in Tokyo and continued research of torrefaction at the University of umeå. In late 2009, began designing torrefication the installation of 22 MW. "This is the first in the world torrefication line such a big power," said a Professor at the University of umeå Anders Nordin. Such studies and conducts experiments and another Swedish company Torkapparater AB, which since 1937 is developing technology to drying wood.
Table 2. The characteristics of torrefied pellets,
achieved in the pilot plant of the company Thermya SA, in comparison
with classic characteristics of pellets and wood chips
In France the technologies of torrefaction has been the company Thermya SA, patented a new principle of the reactor (Torspyd) with two vertically spaced columns, which are in opposite directions to continuously move the biomass and gas. In table. 2 shows the characteristics of torrefied pellets obtained in the pilot plant of this company, in comparison with the classical characteristics of pellets and wood chips.
Not to mention here another French company Biogreen, with its technology of thermal processing of biomass and waste by torrefaction, pyrolysis and gasification with the use of a patented electrical heating screw (auger) conveyor and equipment for heat treatment of bulk product.
When the torrefaction of the solid biomass according to this technology, the output is a lump biochar, whose characteristics are similar to characteristics srednekaloriynye fossil fuels and liquid biofuels (so-called pyrolysis oil) and biogas that can be used as:
Although the technology of the firm Biogreen is primarily intended for the disposal and processing of wastes: biomass, MSW, plastics and other things, it can be used for the torrefaction of wood pellets or briquettes.
The British company Rotawave Biocoal Ltd. has developed a technology based on the principle of microwaves and therefore called microwave technology for biochar (Microwave technology for biocoal), which allows to extract from biomass torrefied solid biofuels and organic oils. The technology is based on the use of high-frequency electromagnetic effects on materials that are in unique ceramic drum that allows to keep system high temperature mode, to minimize operating costs and ensures a small size of production.
Table 3. Examples of investment costs in projects plants
torrefaction of wood pellets in Europe
According to statistics from the International energy Agency, in EU countries, biomass is used in more than 150 coal-fired power plants as fuel for co-firing. Most of these TES are located in the Netherlands, Belgium, Denmark, great Britain and Poland. In Poland, the planned construction of thermal power plant designed for co-firing torrefied biomass and coal. Today, as biomass is mainly used wood pellets and some pellets from agricultural waste (straw, sunflower husks, etc.).
Commercial Director of Topell Energy Robin Post van der Burg at the conference on the generation of alternative energy in March 2012 in Rotterdam discussed with Russian partners the possibility of deliveries to Russia of equipment for torrefaction. Robin Post van der Burg stated that, according to him, the world is now engaged in Torrevieja more than 60 commercial companies and research institutes.
Torrefied pellets are used in thermal power plant irregular, one might say, in the order of testing. No company has so far failed to establish serial production of technological equipment for the torrefaction. And almost all the constructed plants and lines for the torrefaction of biomass mainly work in demo mode or, at best, produce products in the amount lower than the real power.
Nevertheless, European interest in torrefied pellets growing. Talking about it and data about investment costs in projects of plants for the torrefaction of pellets (tab. 3).
published
P. S. And remember, only by changing their consumption — together we change the world! ©
Join us in Facebook , Vkontakte, Odnoklassniki
Source: lesprominform.ru/jarchive/articles/itemshow/2683
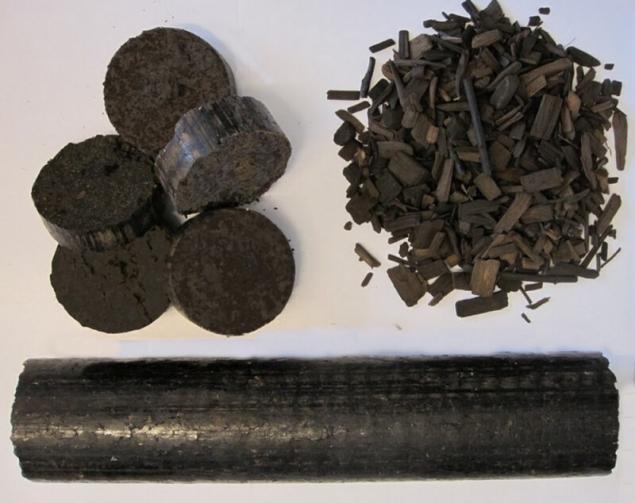
For different market names hidden same well-known production process: firing of solid biomass (eng. — torrefaction) and subsequent granulation into pellets; similar technology is used in the roasting of coffee beans. The firing process was first used in the 1930-ies in France (the French verb torrefier, which is translated as "to roast", mostly used to denote the process of roasting coffee beans). Unlike coffee beans, solid biomass is burnt without oxygen at a temperature of 200-330 ° C.
Chemical analysis of the biomass after this firing showed that it acquires a large calorific value, energy consumption and improved compared to neeregirovannom biomass combustion results. The firing process is applicable to all types of biomass.
The Netherlands: ahead of the restof the Duiven is a small village in the province of Gelderland, near the border with Germany. Since its founding in the Roman period and to enter here into operation of a small brewery in our times, she has not played any meaningful role in the industry of the Netherlands.
That all changed the last few years. The Duiven became a major center of the global pellet industry. RWE Innogy — a 100% subsidiary of one of the world's largest energy concern RWE (which has a share "Gazprom"), together with the Dutch company Topell Energy (39% of which is owned by RWE) has invested 15 million euros in the construction of the largest in the world today for the production of torrefaction pellets.
Torrefied pellets (TP) by the process of torrefaction acquire the characteristics that distinguish them from ordinary pellets the better. Suffice it to say that the caloric value of one ton of pellets tarifitsirovannyim higher than one ton of pellets neeregirovannom.
Why the German concern RWE is implementing a project abroad? The answer is simple: in accordance with the laws of the Netherlands, all coal-fired power plants are bound together with the coal to burn any biomass, for that state, since 2002 and to this day, guaranteed to pay this TPP grant in the amount of 5-6 Euro cents for every kilowatt-hour of electricity generated in co-firing of biomass. In Germany such conditions for TES yet (according to the German law on renewable energy as only electricity generation from stations up to 20 MW at 100% biomass). Therefore, sales of industrial wood pellets in Belgium and the Netherlands, which has also a similar Dutch state program grants under co-firing, are much higher than in Germany. Based on the above described advantages of TP, a European pellet producers and energy companies are doing now a bet on torrefied wood torrefied pellets and other solid biomass with the aim of obtaining competitive advantages over manufacturers classic pellets.
Plant in Duiven was commissioned in the spring of 2011. The line capacity torrefazione and granulation — 8 tons per hour, raw material is wood waste. "Now the main task, — speaks the employee of the Department of venture capital investment of RWE Innogy Crispin lake is the output of the plant at the highest possible level of annual volume of output not less than 60 kt". Mr. lake was in charge of this project from the stage of pre-design work, so the process of torrefaction knows everything. In his opinion, the main problem of plant in Duiven is ensuring continuous supply of raw materials in the industrial scale, which today is not easy to achieve not only in the Netherlands, but also in some other Western European countries. Even have to sort and recycle the so-called old wood — any wood products, overage, down to the furniture, excluding parts coated with paints. Torrefied pellets are supplied to the coal plant working adjacent to the village town of Geertruidenberg.
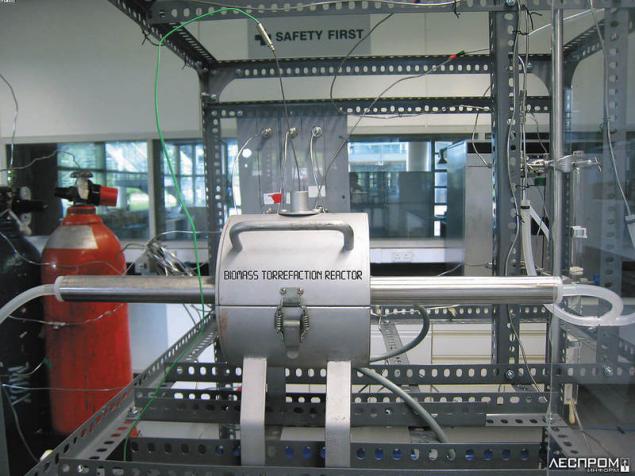
How does the so-called "torbed reactor" (Torbed Reactor) — patented main module of the plant of torrefaction pellets in Duiven?
Raw materials in the form of ground wood biomass fed to the reactor and heated without access of oxygen to a temperature of 220-330 °C. the Heating lasts from several seconds to one hour, depending on the established mode of torrefaction. During this process, the gas formed, which provides the high temperature necessary for the process of torrefaction. In order to start the reactor, using an external energy source. Once the reactor reaches the desired operating temperature, the process is closed without energy supply. After completion of the mode of torrefaction, the duration of which is determined depending on the quality of the input materials, the output is a homogeneous product with high energy density, excellent quality of grinding, humidity 5 %, containing less than neeregirovannom biomass, the amount of impurities. In addition, torrefied pellets become hydrophobic, i.e. the ability to repel moisture and to resist the processes of decay and fermentation, which gives the opportunity to store them even in the open air.
"Compared to traditional pellets TP have many advantages, and most importantly — is, of course, increased energy density," — said the expert of the Department of bioenergy and environment Austrian Institute of technology and chemistry in Vienna Martin English. During torrefaction the biomass properties are changed radically: it destroys the structure of cellulose, evaporates much of the moisture, the formation of free molecules of carbon, hydrogen and oxygen. On the structure of the torrefied pellets is similar to coal, because in the course of chemical processes in wood and other plant biomass by torrefaction all the carbon is converted into biochar (unsaturated hydrocarbons) are oxidized and react with the oxygen molecules. Biochar has the same properties as fossil coal, and can easily be burned along with him. Due to the fact that as a result of firing is greatly reduced moisture content of torrefied pellets, they become brittle and are crushed more easily than standard pellets. Therefore, when co-firing with coal TP no need to upgrade the technological fuel supply line — no need to install a pellet crusher, and a separate feed system of pellets.
In most coal fired power plants used the torch method of burning fuel, and coal before feeding to boiler is crushed to pulverized condition and industrial pellets co-firing on the crusher are crushed to the size of about 2 mm. Torrefied pellets are milled together with coal, and due to the above-described properties, their grinding requires less energozatrat than the classical grinding pellets. Torrefied pellets can be pre-mixed with coal at a fuel depot power station. Since the energy density of the TA superior to ordinary pellets, reduced transport costs and warehousing, for storage of torrefied pellets does not require any special dry room, they can be stored even in the open air, together with coal. Simple wood pellets with this storage, due to the biological activity of the wood absorb moisture from the air, lose calorie, rot and water resistant and are destroyed. Torrevieja also allows to reduce the sulfate content of the pellets. But perhaps the main motivation for the application of torrefaction in Europe environmental focus is the use of torrefied biomass (reduction of greenhouse gas emissions when co-firing with coal) and the limited resource base for the production of ordinary wood pellets. The demand for energy wood is increasing every year and even increasing exponentially the use of energy plantation of plants does not solve the problem of shortage of raw materials for biofuel production.
The quality of the raw materials for the manufacture of pellets torrefazioni not to meet such stringent requirements as to quality of raw material for wood pellets is simple, — for the production of TP you can use chips of the lowest quality or the crust. The resource base for the manufacture of torrefied pellets is expanding due to the fact that in the process you can use straw, hay, residues from the production of vegetable oils, sugar beet processing, other agriculture waste, municipal solid waste (MSW), and even various plastics. To torrefazioni can be a mixture of different solid biomass. For example, the company FoxCoal in the Netherlands have torrefazione plastic along with scrap paper and got the high quality granules, which in many ways superior to coal. By the way, torrefied biomass is often called biochar.
In the Netherlands, created the Association of torrefaction (The Dutch Torrefaction Association — DTA), which includes: company 4Energy Invest from Belgium, the Netherlands research center for energy (The Energy research Centre of the Netherlands, ECN) and the Dutch company FoxCoal, Topell Energy Torr-Coal Technology.
Technology of torrefaction of biomass are doing in Holland and other well-known companies, such as BTG (Biomass Technology Group). The Netherlands is firmly in first place in the world by number of companies and public institutions working in this field.
Table 1. The influence of process parameters of torrefaction on structure
torrefied wood
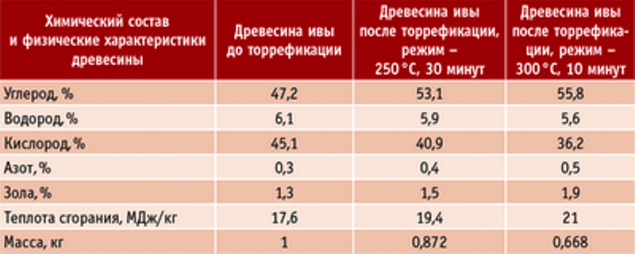
In 2006, the Dutch specialist in thermodynamics and pyrolysis of biomass mark Jan Prins in the journal, devoted to Analytics and the practical application of pyrolysis (Journal of Analytical and Applied Pyrolysis), as well as in the work published by the University of Eindhoven (Eindhoven University of Technology, Environmental Technology Group, Department of Chemical Engineering and Chemistry), cited the results of thermodynamic studies of the processes of torrefaction and gasification of wood, which he conducted jointly with a group of researchers. From these results it follows that the characteristics of torrefied wood directly depend on the type of wood used, the duration and temperature of the process. In table. 1 shows the results of comparison of characteristics of torrefaction of willow before and after under the two regimes of the process.
Prospects of torrefaction in GermanyIn Germany, unlike other Western European countries, the use of torrefied biomass is seen only in the long term. Wood pellets are used in the German market is almost 100 % only in power in utility boilers for heating residential sector, farms, small industrial enterprises (in contrast to the Netherlands, Belgium, UK, where pellets are used mainly for electricity generation). In Germany, pellets are burned in boilers up to 300 kW (in private households) and small boiler plants with capacity up to 3 MW.
At the forum, held at the international exhibition pelletan (Interpellets), which is held annually in Stuttgart, Deputy Chairman of the German Association of producers of pellets (DEPV) Hans Martin Behr said that today Torrevieja is irrelevant for the power system of Germany. He believes "fundamentally incorrect attempts to increase the efficiency of operating today, the European TES, most of whom work on "prehistoric equipment", due to the combustion of new generation biofuels. Why not solve this problem by means of modernization of power plants for optimum burning of common biomass?"
Such statements, likely due to the fact that now in Germany, as has been pointed out many European experts, there is an overproduction of wood pellets. In 2001, Germany produced 1.86 million tons of pellets and consumed only 1.4 million tonnes when the actual performance of all pellet plants of 2.7 million tons per year. In 2012, according to forecasts, the country will produce more than 2 million tonnes of wood pellets. Most of this production corresponds to the standards Din+ or the new European standard EN-A1, A2. Industrial pellets are produced in small volumes, as thermal power plants operating on solid biofuels in Germany use mainly wood waste (wood chips, waste sanitary felling, thinning, landscaping, old wood, etc.).
And the export of such granules from Germany at a power plant in the Netherlands is not competitive producers in the U.S. and Canada, where production costs are lower, and transport costs when shipping across the Atlantic to Rotterdam large ocean-going vessels per ton is much less than the cost of transport by road or rail from Germany.
In Germany there really are no economic prerequisites for the production of torrefied pellets. Local of wood raw material for thermal power plants is enough. But for other types of biomass annually to generate significant amounts of raw materials. For example, straw, according to German research centre for biomass (DBFZ), can be used from 8 to 13 million tons per year. And the first and only thermal power plant in Emsland, using baled straw, put into operation only this year.
However, some German research centers and energy concern, trying to keep up with the times and conduct a study of torrefaction of biomass, getting to these development grants from the EU. Since January 2012 such work under the 7th Research programme on bioenergy the EU has DBFZ; date of completion of research and presentation of results in 2015. The project involved more than 20 European companies and research centers. They include subsidiaries of the major European energy concern, such as RWE Innogy, E. on UK, Vattenfall AB, the Austrian research Institute for chemistry and technology (OFI), the energy research Centre of the Netherlands (ECN). Director of Department bioenergy systems, DBFZ, Janet Witt says that this center is the focal point of the entire project in the course of experiments and research will be torrefication different types of solid biomass co-firing torrefied biofuels obtained from lignite and coal in different proportions. Based on the results of the research will make recommendations for producers of solid biofuels: what is biomass and how best to torrefazioni. Tests will be carried out on reactors of different types: fixed, movable, rotary-drum reactor, fluidized bed, etc. Then torrefied biomass will pelletize and briquetting in order to determine which equipment is most suitable for these purposes. Torrefied pellets and briquettes will be tested for the preservation of properties during storage under open air (tested for reaction with the soil layer and water repellency).
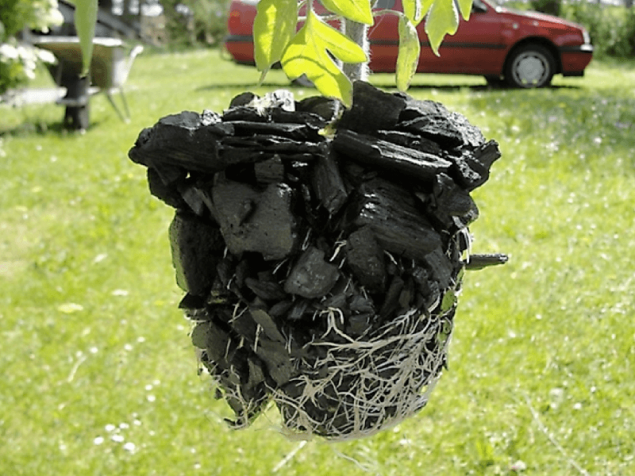
RWE Innogy in 2009 set demonstration equipment for the torrefaction of biomass in Talgatom Institute (Gas-Waerme Institut) in Essen in the framework of another research project, in which participate: the Ruhr-University of Bochum (Ruhr-Universitaet Bochum), Higher technical school in Aachen (Technische Hochschule Aachen), the company "Thyssen-Krupp metal" (Thyssen Krupp Steel), manufacturer of equipment for granulation of biomass "Poli münch GmbH" (Muench Edelstahl GmbH) and the company "Hitachi Power" (Hitachi Power Europa). Since 2012, this project includes not only scientific research work on the torrefaction of biomass, but also work to find other opportunities to improve the quality of solid biomass for more efficient combustion, particularly in conjunction with coal.
The management of energy Vattenfall is one of Europe's leading electricity producers (mainly in Germany and Sweden) on coal-fired power plants — production of torrefied pellets in a volume of 5 million tons per year by 2020 on the plants that will be built in the United States and South America. Director of group planning and the use of biomass Ulrich Rusch, however, tells about these plans quite carefully, given that today only implemented small pilot projects of torrefaction and on this basis to launch large-scale production is not easy. Still required to conduct all sorts of tests, and explore a real working technology of torrefaction. For these purposes it is planned to purchase torrefied pellets from 40 manufacturers around the world, and at the Berlin thermal power plant "Reuter West" group to conduct the technical testing for the joint combustion of torrefied pellets with coal in varying proportions. Preliminary tests of co-incineration of industrial pellets, or as they became known recently, white pellets (Whitе Pellets), coal-fired power plants of the concern showed that the mixture of pellets and coal should be not more than 20% of the white pellet of total fuel burned at the station. In the case of using torrefied (black) granules and this number could be increased to 50-70 %.
Many of the above-described research in Germany are also due to the fact that in 2018 the state will cease subsidizing the coal mining industry. 15 July 2011 entered into force the new Law on coal (Steinkohlefinanzierungsgesetz) governing state subsidies for coal mining in Germany and state aid closed mines and laid off miners. The amount of aid will gradually decrease and by the end of 2018 it will completely stop. The possibility of extending subsidies excluded, since the agreement of the European Commission on new grants were received in 2011, only under the condition that in 2018, this work will be completed. Probably this year and that will end the era of coal production in Germany, if only by the time energy prices will not grow much.
In other European countries? In 2008 in Sweden, the company BioEndev (Bio Energy Development North AB) launched a pilot project for the torrefaction of biomass. In 2009, she produced the first batch of torrefied biofuel and received funding from the Swedish energy administration for the creation of industrial torrefication installation in Tokyo and continued research of torrefaction at the University of umeå. In late 2009, began designing torrefication the installation of 22 MW. "This is the first in the world torrefication line such a big power," said a Professor at the University of umeå Anders Nordin. Such studies and conducts experiments and another Swedish company Torkapparater AB, which since 1937 is developing technology to drying wood.
Table 2. The characteristics of torrefied pellets,
achieved in the pilot plant of the company Thermya SA, in comparison
with classic characteristics of pellets and wood chips
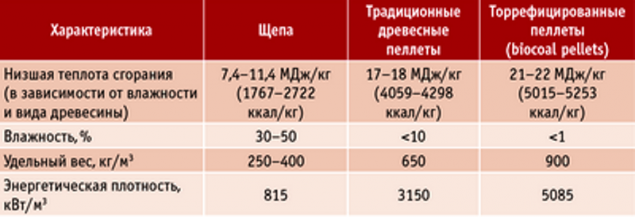
In France the technologies of torrefaction has been the company Thermya SA, patented a new principle of the reactor (Torspyd) with two vertically spaced columns, which are in opposite directions to continuously move the biomass and gas. In table. 2 shows the characteristics of torrefied pellets obtained in the pilot plant of this company, in comparison with the classical characteristics of pellets and wood chips.
Not to mention here another French company Biogreen, with its technology of thermal processing of biomass and waste by torrefaction, pyrolysis and gasification with the use of a patented electrical heating screw (auger) conveyor and equipment for heat treatment of bulk product.
When the torrefaction of the solid biomass according to this technology, the output is a lump biochar, whose characteristics are similar to characteristics srednekaloriynye fossil fuels and liquid biofuels (so-called pyrolysis oil) and biogas that can be used as:
- fuel for the boiler;
- fuel to generate electricity;
- raw materials for the production of chemicals and resins;
- liquid smoke in the food industry;
- preservatives, such as antiseptic;
- fuel for diesel engine.
Although the technology of the firm Biogreen is primarily intended for the disposal and processing of wastes: biomass, MSW, plastics and other things, it can be used for the torrefaction of wood pellets or briquettes.
The British company Rotawave Biocoal Ltd. has developed a technology based on the principle of microwaves and therefore called microwave technology for biochar (Microwave technology for biocoal), which allows to extract from biomass torrefied solid biofuels and organic oils. The technology is based on the use of high-frequency electromagnetic effects on materials that are in unique ceramic drum that allows to keep system high temperature mode, to minimize operating costs and ensures a small size of production.
Table 3. Examples of investment costs in projects plants
torrefaction of wood pellets in Europe
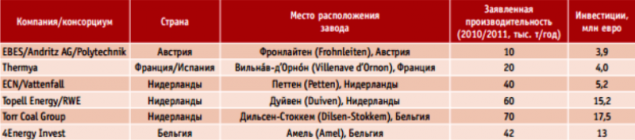
According to statistics from the International energy Agency, in EU countries, biomass is used in more than 150 coal-fired power plants as fuel for co-firing. Most of these TES are located in the Netherlands, Belgium, Denmark, great Britain and Poland. In Poland, the planned construction of thermal power plant designed for co-firing torrefied biomass and coal. Today, as biomass is mainly used wood pellets and some pellets from agricultural waste (straw, sunflower husks, etc.).
Commercial Director of Topell Energy Robin Post van der Burg at the conference on the generation of alternative energy in March 2012 in Rotterdam discussed with Russian partners the possibility of deliveries to Russia of equipment for torrefaction. Robin Post van der Burg stated that, according to him, the world is now engaged in Torrevieja more than 60 commercial companies and research institutes.
Torrefied pellets are used in thermal power plant irregular, one might say, in the order of testing. No company has so far failed to establish serial production of technological equipment for the torrefaction. And almost all the constructed plants and lines for the torrefaction of biomass mainly work in demo mode or, at best, produce products in the amount lower than the real power.
Nevertheless, European interest in torrefied pellets growing. Talking about it and data about investment costs in projects of plants for the torrefaction of pellets (tab. 3).
published
P. S. And remember, only by changing their consumption — together we change the world! ©
Join us in Facebook , Vkontakte, Odnoklassniki
Source: lesprominform.ru/jarchive/articles/itemshow/2683