809
What's wrong with McPherson, and why he is not giving up without a fight
The more dynamic acceleration, the stronger of the "steering wheel" keeps the driver. They say it's fear. And it is not challenged, because the way it is: the faster the car accelerates, the less safe it becomes for the one who disperses.
And why? Because any machine can not be equally well controlled throughout its range of available speeds and trajectories. And when it comes to speed, what they are higher the more significant are the forces that strive to bring down the guide wheels from the planned course followed by the driver of the car being taken away from the selected path and all the ensuing consequences of unsafe circumstances.
Paradoxically, because of the above reasons are more likely to be afraid of and firmer hold on the steering wheel must be the drivers of cars equipped with the most common, and we have more and especially revered by amateurs repair for minimum money single arm suspension, McPherson also called by the name of the creator.
8 photos, and text.
How to become an honorary innovator
Earl Steele McPherson motivated by a desire to simplify and reduce the cost of this front suspension. And he got his. Unlike conventional suspension at the time with two triangular wishbones, one above the other, in the suspension McPherson has only one lower arm.
And in the design, developed directly McPherson, this lever was not even a triangle, and the single. However lever fixed to the body at only one point, can not withstand the longitudinal forces acting upon the wheel and hold it in the desired direction. To close the triangle, as the second arm MacPherson used stabilizer, but it was only half the battle. The main thing was what the developer of the function entrusted to the second arm, because the wheel, too, can not be fixed only at one point.
Shock little resemblance to the lever, but that the upper shock absorber fastening to the body and the bottom bracket to the wheel hub replace the upper arm. Moreover, the damper housing, rotates with the wheel around its own stock, replaced the pin. As rewarded Ford, you where he worked Earl Steele McPherson, a designer is not known, but in the USSR such rationalization would be pulled exactly the title of a well-deserved and honorable. The first production car, which has been used this solution was Ford Vedette 1948 sample.
Simple, cheap but not cheerful
For single-lever the idea even if not immediately, but seized all. Halving suspension components provide the same depreciation of their production. The entire structure is a single assembly unit and, therefore, to simplify and reduce the cost again conveyor assembly. Due to fewer wearing hinges become easier and cheaper to repair. But most importantly, thanks to the compact suspension McPherson could not be better suited for front wheel drive cars with transverse engine layout. All these advantages and ensure that ten years after the invention of fifteen McPherson was the "number one" among the hangers.
But the coin is known to be two sides. Acting as a guide member, and received a shock load, which experienced double wishbones upper arm. Hence, high friction on the guide rod, wear and faster time shock absorber failure. In addition, the suspension McPherson shock and vibration transmitted to the upper suspension strut, which means that the body itself, so for the ride comfort of the machine with the lever pendants lost vehicles, which served only to shock damping function. However, today these drawbacks McPherson little relevant. Designers and technologists in the cap had not slept - improved durability of shock absorbers, body insulated with pillows and stretchers. However, against the disadvantages inherent McPherson kinematic engineers were powerless.
Shoulder running
In McPherson struts wheel is rotated relative to the upper strut and ball joint. For foreign exchange stability and stability of the car it is desirable that the continuation of the line passing through the centers of support, crossed the contact patch the tire from the outside to the center of this spot. For McPherson such geometric daunting task because there is a limit to which the layout of the engine compartment allows you to tilt the rack. The distance remaining between the point of intersection of the axis of rotation of the wheel and the center of the tire contact patch, called a shoulder running. What is more, the significant impact on the control of the forces acting on the wheel in the middle of his contact with the road.
While the car is going straight on a flat road, that's okay, because the moments of these forces on the right and left wheel symmetrically balanced. Problems begin when the car is moving or when you turn one of the wheels rolls over uneven. In the first case, there occurs a difference between the torque transmitted to right and left wheels. In the second, the position of the center of the contact patch with the road one of the wheels. In any case, the symmetry is broken, there is an imbalance moments of the forces applied to the wheels, which has a negative feedback force on the steering system. With a sharp acceleration, motion in a changing traction, this phenomenon is also possible. Driver it feels like a spontaneous attempt to get off the path of the car and makes it necessary to steer. The higher the speed, the steeper the turn, the greater impact on the lack of stability of the machine McPherson.
And the power and speed increase, which could not affect the popularity of McPherson developers cars. On the model of the small size classes, where single lever suspension because of their compactness eliminates the problems associated with the placement of the engine and engine compartment attachments in distress, its position remains steadfast. In other cases, began to give preference to double, if not multi-link suspension, such as in the Audi A4 / A6, VW Passat B5, Mazda6 or Peugeot 407.
Not one step back
It turned out, however, that McPherson and there is life in the old dog.
Confirmation of this - single-lever design, which appeared under the high-sounding titles like HiPerStrut or RevoKnuckle in the last few years, General Motors, Ford, Renault and other companies.
If you do not pay attention to the features of their general sense it is that the common first knuckle and shock absorber divided swivels.
As a result, the knuckle had the opportunity to rotate around the bar. It did not save lever suspension of its congenital defect, but allowed to reduce shoulder running more than doubled compared to the traditional McPherson and thereby significantly reduce the parasitic moment, causing spontaneous torque steer that violates precision driving.
Of course, immediately visible and cons "gipershtrutov" and "revoknakley." The suspension became harder and more expensive. Impair its maintainability, increased cost of repairs. It has become a big weight and unsprung masses is that impair a smooth ride. However, it is doubtful that all of these parameters of the New-McPherson concede multi-link suspension similar to those used in the VW Passat B5 or a Peugeot 407.
Moreover, given that the wheel in all New-McPherson turns not relative to the shock absorber rod and the axis passing through the added joints, the rod must be unloaded and less wear and, therefore, a shock absorber, ceteris paribus, more likely to fail later than usual McPherson. For this reason, you can simplify the design of the rack supports, partly able to compensate for the increase in the cost of manufacturing and repair improved "odnorychazhki».
McPherson is still faulty. However, apart from the shortcomings of the suspension has undeniable advantages, thanks to which we can predict that in the foreseeable future, it is unlikely to put himself to competing designs on the blades.
Source
And why? Because any machine can not be equally well controlled throughout its range of available speeds and trajectories. And when it comes to speed, what they are higher the more significant are the forces that strive to bring down the guide wheels from the planned course followed by the driver of the car being taken away from the selected path and all the ensuing consequences of unsafe circumstances.
Paradoxically, because of the above reasons are more likely to be afraid of and firmer hold on the steering wheel must be the drivers of cars equipped with the most common, and we have more and especially revered by amateurs repair for minimum money single arm suspension, McPherson also called by the name of the creator.
8 photos, and text.
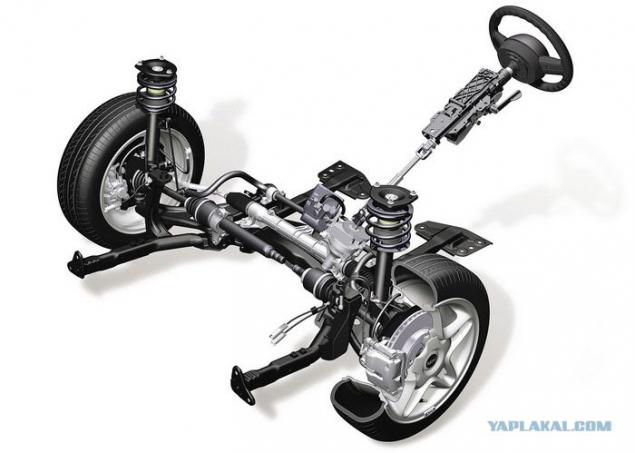
How to become an honorary innovator
Earl Steele McPherson motivated by a desire to simplify and reduce the cost of this front suspension. And he got his. Unlike conventional suspension at the time with two triangular wishbones, one above the other, in the suspension McPherson has only one lower arm.
And in the design, developed directly McPherson, this lever was not even a triangle, and the single. However lever fixed to the body at only one point, can not withstand the longitudinal forces acting upon the wheel and hold it in the desired direction. To close the triangle, as the second arm MacPherson used stabilizer, but it was only half the battle. The main thing was what the developer of the function entrusted to the second arm, because the wheel, too, can not be fixed only at one point.
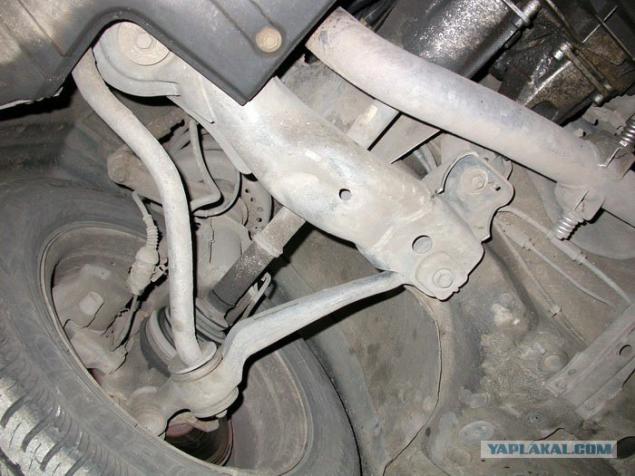
Shock little resemblance to the lever, but that the upper shock absorber fastening to the body and the bottom bracket to the wheel hub replace the upper arm. Moreover, the damper housing, rotates with the wheel around its own stock, replaced the pin. As rewarded Ford, you where he worked Earl Steele McPherson, a designer is not known, but in the USSR such rationalization would be pulled exactly the title of a well-deserved and honorable. The first production car, which has been used this solution was Ford Vedette 1948 sample.
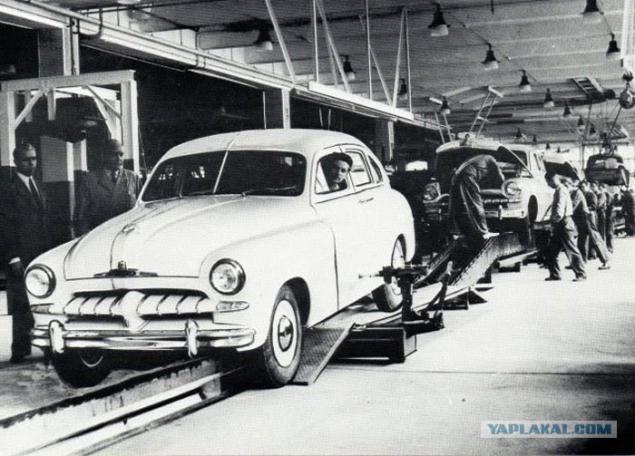
Simple, cheap but not cheerful
For single-lever the idea even if not immediately, but seized all. Halving suspension components provide the same depreciation of their production. The entire structure is a single assembly unit and, therefore, to simplify and reduce the cost again conveyor assembly. Due to fewer wearing hinges become easier and cheaper to repair. But most importantly, thanks to the compact suspension McPherson could not be better suited for front wheel drive cars with transverse engine layout. All these advantages and ensure that ten years after the invention of fifteen McPherson was the "number one" among the hangers.
But the coin is known to be two sides. Acting as a guide member, and received a shock load, which experienced double wishbones upper arm. Hence, high friction on the guide rod, wear and faster time shock absorber failure. In addition, the suspension McPherson shock and vibration transmitted to the upper suspension strut, which means that the body itself, so for the ride comfort of the machine with the lever pendants lost vehicles, which served only to shock damping function. However, today these drawbacks McPherson little relevant. Designers and technologists in the cap had not slept - improved durability of shock absorbers, body insulated with pillows and stretchers. However, against the disadvantages inherent McPherson kinematic engineers were powerless.
Shoulder running
In McPherson struts wheel is rotated relative to the upper strut and ball joint. For foreign exchange stability and stability of the car it is desirable that the continuation of the line passing through the centers of support, crossed the contact patch the tire from the outside to the center of this spot. For McPherson such geometric daunting task because there is a limit to which the layout of the engine compartment allows you to tilt the rack. The distance remaining between the point of intersection of the axis of rotation of the wheel and the center of the tire contact patch, called a shoulder running. What is more, the significant impact on the control of the forces acting on the wheel in the middle of his contact with the road.
While the car is going straight on a flat road, that's okay, because the moments of these forces on the right and left wheel symmetrically balanced. Problems begin when the car is moving or when you turn one of the wheels rolls over uneven. In the first case, there occurs a difference between the torque transmitted to right and left wheels. In the second, the position of the center of the contact patch with the road one of the wheels. In any case, the symmetry is broken, there is an imbalance moments of the forces applied to the wheels, which has a negative feedback force on the steering system. With a sharp acceleration, motion in a changing traction, this phenomenon is also possible. Driver it feels like a spontaneous attempt to get off the path of the car and makes it necessary to steer. The higher the speed, the steeper the turn, the greater impact on the lack of stability of the machine McPherson.
And the power and speed increase, which could not affect the popularity of McPherson developers cars. On the model of the small size classes, where single lever suspension because of their compactness eliminates the problems associated with the placement of the engine and engine compartment attachments in distress, its position remains steadfast. In other cases, began to give preference to double, if not multi-link suspension, such as in the Audi A4 / A6, VW Passat B5, Mazda6 or Peugeot 407.
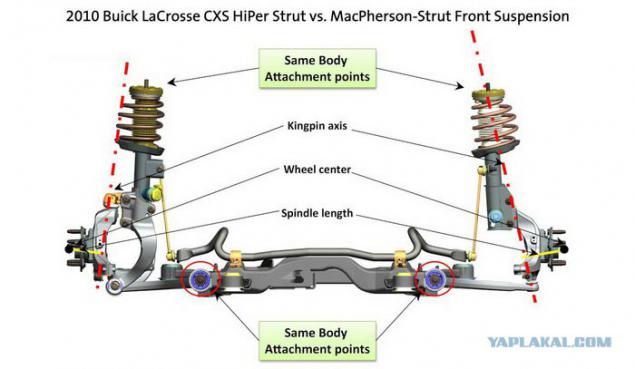
Not one step back
It turned out, however, that McPherson and there is life in the old dog.
Confirmation of this - single-lever design, which appeared under the high-sounding titles like HiPerStrut or RevoKnuckle in the last few years, General Motors, Ford, Renault and other companies.
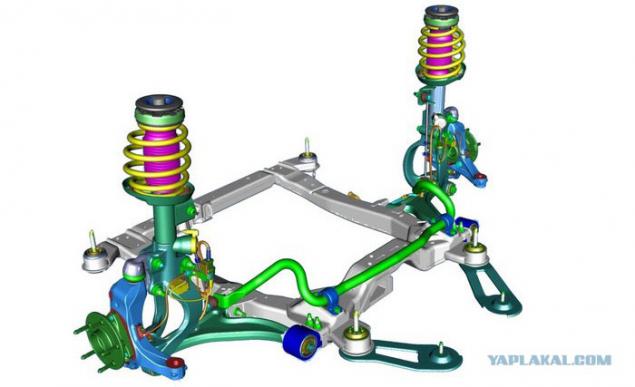
If you do not pay attention to the features of their general sense it is that the common first knuckle and shock absorber divided swivels.
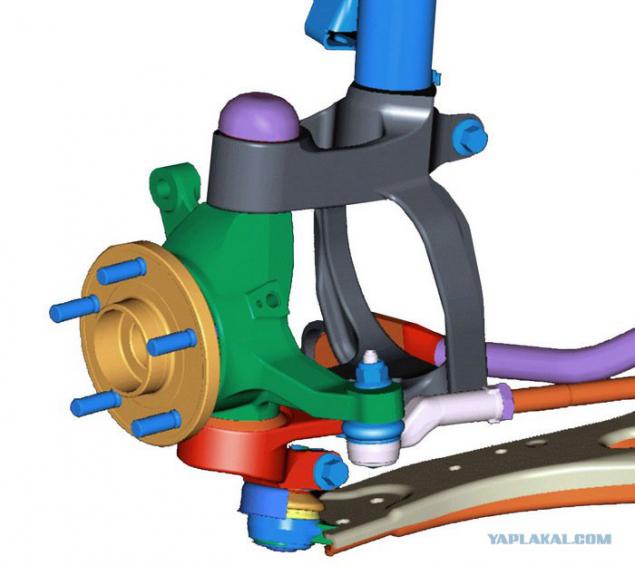
As a result, the knuckle had the opportunity to rotate around the bar. It did not save lever suspension of its congenital defect, but allowed to reduce shoulder running more than doubled compared to the traditional McPherson and thereby significantly reduce the parasitic moment, causing spontaneous torque steer that violates precision driving.
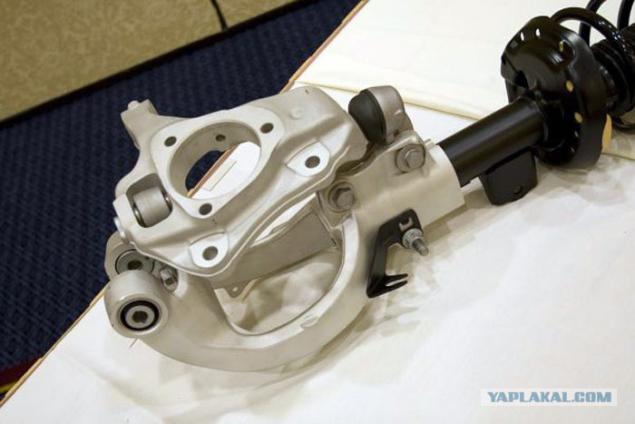
Of course, immediately visible and cons "gipershtrutov" and "revoknakley." The suspension became harder and more expensive. Impair its maintainability, increased cost of repairs. It has become a big weight and unsprung masses is that impair a smooth ride. However, it is doubtful that all of these parameters of the New-McPherson concede multi-link suspension similar to those used in the VW Passat B5 or a Peugeot 407.
Moreover, given that the wheel in all New-McPherson turns not relative to the shock absorber rod and the axis passing through the added joints, the rod must be unloaded and less wear and, therefore, a shock absorber, ceteris paribus, more likely to fail later than usual McPherson. For this reason, you can simplify the design of the rack supports, partly able to compensate for the increase in the cost of manufacturing and repair improved "odnorychazhki».
McPherson is still faulty. However, apart from the shortcomings of the suspension has undeniable advantages, thanks to which we can predict that in the foreseeable future, it is unlikely to put himself to competing designs on the blades.
Source
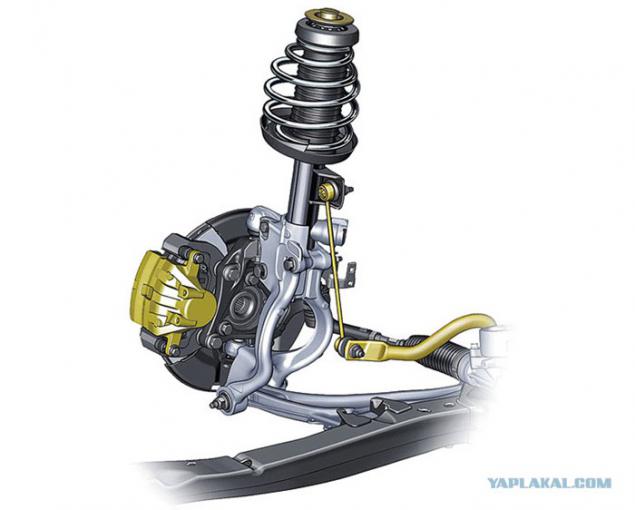