1647
Production of glass containers
Glass line.
It's about the Novosibirsk plant JSC "Plant" Screen ».
The history of the plant began after World War II - it was then the Soviet Union began to think about creating a base for the production of electronic devices for radar and television. In 1948 it was decided to build the plant, and in 1954, he had already begun his work as an enterprise electronic industry for the production of optoelectronic devices, cathode-ray tubes for oscilloscopes and television picture tubes for the assembly plants. For decades, the plant regularly supplied their products to the needs of the partner, but with the termination of mass production in the Russian television technology in 1994, it was converted to the production of glass.
Today JSC "Plant" Screen "- a company is a leading manufacturer of glass containers in the territory from the Urals to the Far East. Product range of the plant up bottles from colorless glass with capacity from 0, 25 liters to 1 liter for bottling of alcoholic beverages, beer and soft drinks; jars for juices, sauces and other canned products with capacities from 0, 25 to 3 liters; brown glass bottle.
Melting furnace.
Speaking of the largest production of glass in the Urals, I meant that production capacity - 620 million. Pcs. glass bottles a year. If we divide by 365, we get about 1, 7 million. Pcs. per day. One Novosibirsk many bottles would be a lot, glass demand among enterprises of Siberian and Far Eastern Federal District of Russia, as well as Kazakhstan and Kyrgyzstan.
But the biggest manufacture in this case - it's just two shops (production of colorless bottles and brown).
Technology of production of glass consists of the following sequential processes:
- Preparation of raw materials,
- Preparation charge,
- Cooking glass,
- Formation and annealing products,
- Quality control and packaging.
Preparation of the feedstock is a clean source of raw materials from unwanted impurities and their preparation for further processing and use. This should be separate storage of raw materials and the supply of raw materials into a hopper.
Charge - is a dry mixture of materials, which are served in a furnace for glass. Important in preparing the charge is determined by weighing the components in proportions and mixing to obtain a homogeneous mass. To prepare the blend, the following raw materials: quartz sand, dolomite flour, glass, chalk Technology, alumina, soda ash, sodium sulfate, obestsvechivateli, dyes, etc.
Ready, but not yet passed quality control bottles.
Melting furnace, which is fed batch and cullet. Performance of such a furnace of about 180 tons of glass per day.
Melting glass - the most difficult operation of all glass production, is produced in a continuous tank furnaces, which are pools built of fire-resistant materials.
Upon heating the charge to 1100 ... 1150 ° C, the formation of silicate initially in solid form and then melt. With further increase in temperature in the melt completely dissolve the most refractory components - formed glass melt. This molten glass is full of gas bubbles and non-uniform in composition. For clarification and homogenization of molten glass increases its temperature up to 1500 ... 1600 ° C. When the viscosity of the melt decreases and thus facilitating removal of gaseous inclusions and obtaining a homogeneous melt.
Glass at the furnace exit.
Color and transparency of the bottle is determined by adding (or absence) of dyes and silencers in charge. Mufflers (fluorine compounds, phosphorus et al.) Makes the glass opaque. By dyes are compounds of cobalt (blue), chromium (green), manganese (purple), iron (brown and blue-green colors) and others.
The process is quite malodorous.
Cooling the glass-finished glass to a temperature at which it acquires the viscosity required to produce blow glassware.
Submission of glass on glass line. At the bottom of the frame shows two bright drops falling glass - it's the future of the bottle.
The process of creating gob.
Finished glass melt is fed to the molding machines, where the molding products with use of appropriate equipment.
Desyatisektsionnaya line, producing a brown glass bottle.
After passing through the forming process, glassware is additionally heat treatment (annealing) in the direct heating furnace. Annealing is required to remove internal residual stress in glass, which gives the product integrity during subsequent processing and operation.
The temperature of the product at the inlet to the furnace annealing: approx. 400 ° C - 500 ° C.
The temperature of the product at the output: approx. 50 ° C - 80 ° C.
Glass after annealing
Spraying bottle with a special solution, which prevents scratches and scuffs on the bottles during transportation.
Products are ready, it remains only to pass quality control.
This complex is equipped with modern glass inspection machines that every second scan parameters for each glass bottles to meet customer requirements.
Packaged products.
I showed the process of manufacturing glass bottles on the new complex. There is another shop where they make clear bottles and jars, where quality control is done manually. The first 4 and 7 following photos taken right there.
Production of both departments are very noisy. Have to go to earplugs or noise reducing headphones.
The process of creating a two-liter cans.
Chekushki.
Vodka bottles after annealing.
Quality control.
Finished products.
Small video, filmed in the production.
--img27--
Source: dedmaxopka.livejournal.com
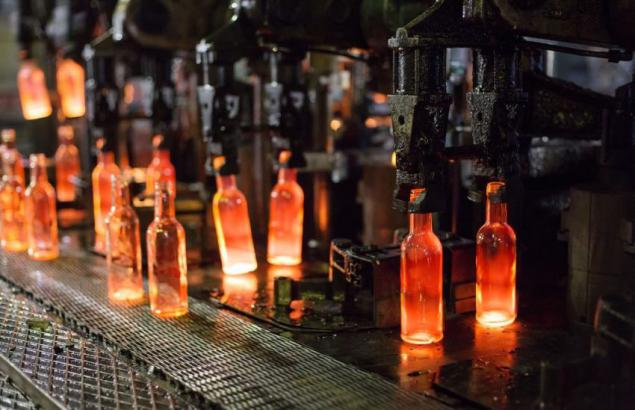
It's about the Novosibirsk plant JSC "Plant" Screen ».
The history of the plant began after World War II - it was then the Soviet Union began to think about creating a base for the production of electronic devices for radar and television. In 1948 it was decided to build the plant, and in 1954, he had already begun his work as an enterprise electronic industry for the production of optoelectronic devices, cathode-ray tubes for oscilloscopes and television picture tubes for the assembly plants. For decades, the plant regularly supplied their products to the needs of the partner, but with the termination of mass production in the Russian television technology in 1994, it was converted to the production of glass.
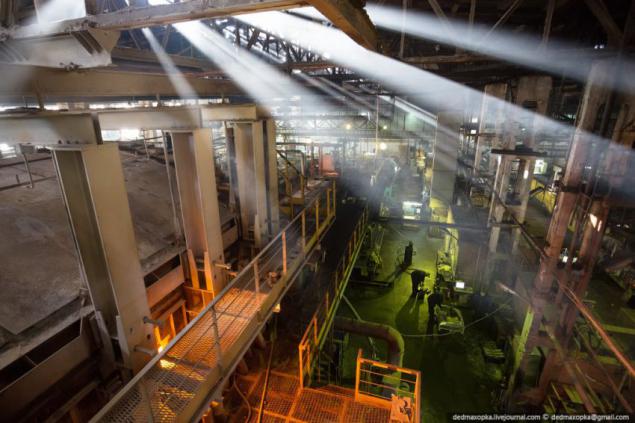
Today JSC "Plant" Screen "- a company is a leading manufacturer of glass containers in the territory from the Urals to the Far East. Product range of the plant up bottles from colorless glass with capacity from 0, 25 liters to 1 liter for bottling of alcoholic beverages, beer and soft drinks; jars for juices, sauces and other canned products with capacities from 0, 25 to 3 liters; brown glass bottle.
Melting furnace.
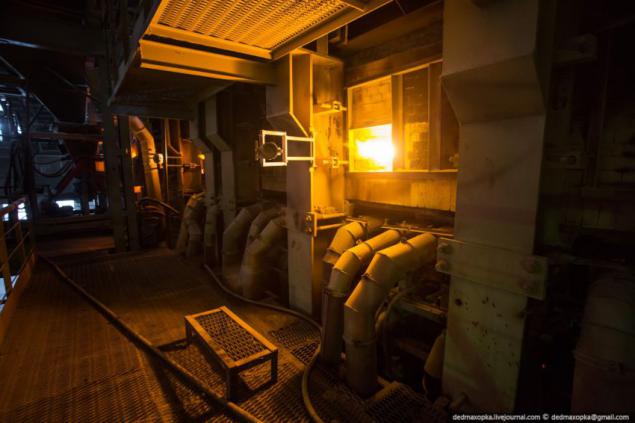
Speaking of the largest production of glass in the Urals, I meant that production capacity - 620 million. Pcs. glass bottles a year. If we divide by 365, we get about 1, 7 million. Pcs. per day. One Novosibirsk many bottles would be a lot, glass demand among enterprises of Siberian and Far Eastern Federal District of Russia, as well as Kazakhstan and Kyrgyzstan.
But the biggest manufacture in this case - it's just two shops (production of colorless bottles and brown).
Technology of production of glass consists of the following sequential processes:
- Preparation of raw materials,
- Preparation charge,
- Cooking glass,
- Formation and annealing products,
- Quality control and packaging.
Preparation of the feedstock is a clean source of raw materials from unwanted impurities and their preparation for further processing and use. This should be separate storage of raw materials and the supply of raw materials into a hopper.
Charge - is a dry mixture of materials, which are served in a furnace for glass. Important in preparing the charge is determined by weighing the components in proportions and mixing to obtain a homogeneous mass. To prepare the blend, the following raw materials: quartz sand, dolomite flour, glass, chalk Technology, alumina, soda ash, sodium sulfate, obestsvechivateli, dyes, etc.
Ready, but not yet passed quality control bottles.
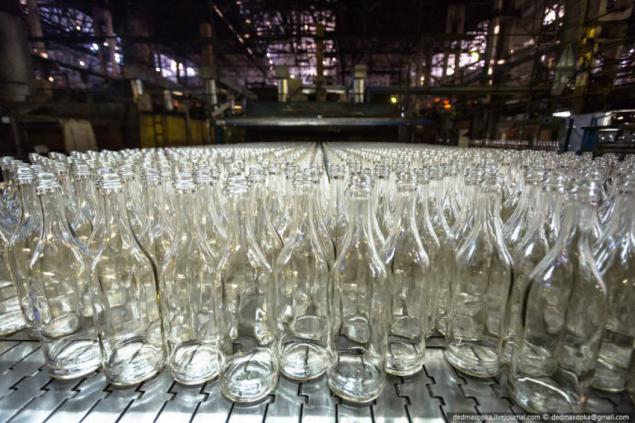
Melting furnace, which is fed batch and cullet. Performance of such a furnace of about 180 tons of glass per day.
Melting glass - the most difficult operation of all glass production, is produced in a continuous tank furnaces, which are pools built of fire-resistant materials.
Upon heating the charge to 1100 ... 1150 ° C, the formation of silicate initially in solid form and then melt. With further increase in temperature in the melt completely dissolve the most refractory components - formed glass melt. This molten glass is full of gas bubbles and non-uniform in composition. For clarification and homogenization of molten glass increases its temperature up to 1500 ... 1600 ° C. When the viscosity of the melt decreases and thus facilitating removal of gaseous inclusions and obtaining a homogeneous melt.
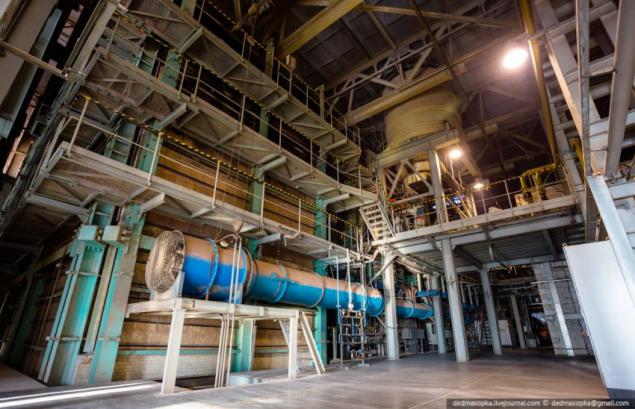
Glass at the furnace exit.
Color and transparency of the bottle is determined by adding (or absence) of dyes and silencers in charge. Mufflers (fluorine compounds, phosphorus et al.) Makes the glass opaque. By dyes are compounds of cobalt (blue), chromium (green), manganese (purple), iron (brown and blue-green colors) and others.
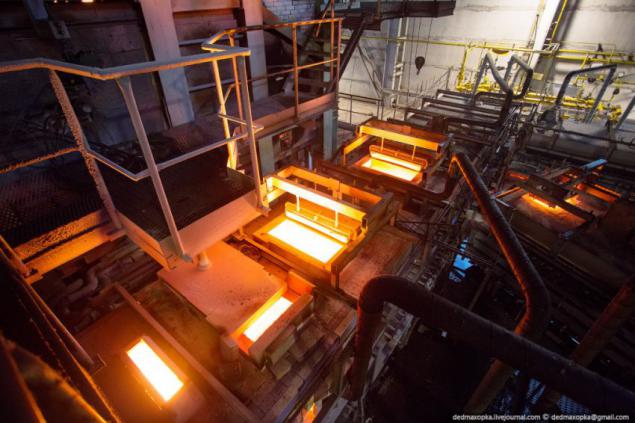
The process is quite malodorous.
Cooling the glass-finished glass to a temperature at which it acquires the viscosity required to produce blow glassware.
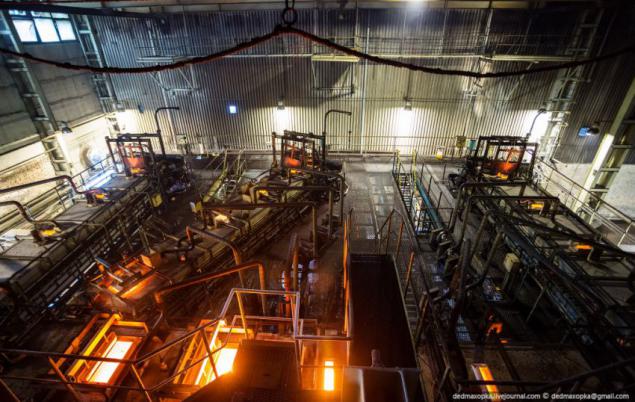
Submission of glass on glass line. At the bottom of the frame shows two bright drops falling glass - it's the future of the bottle.
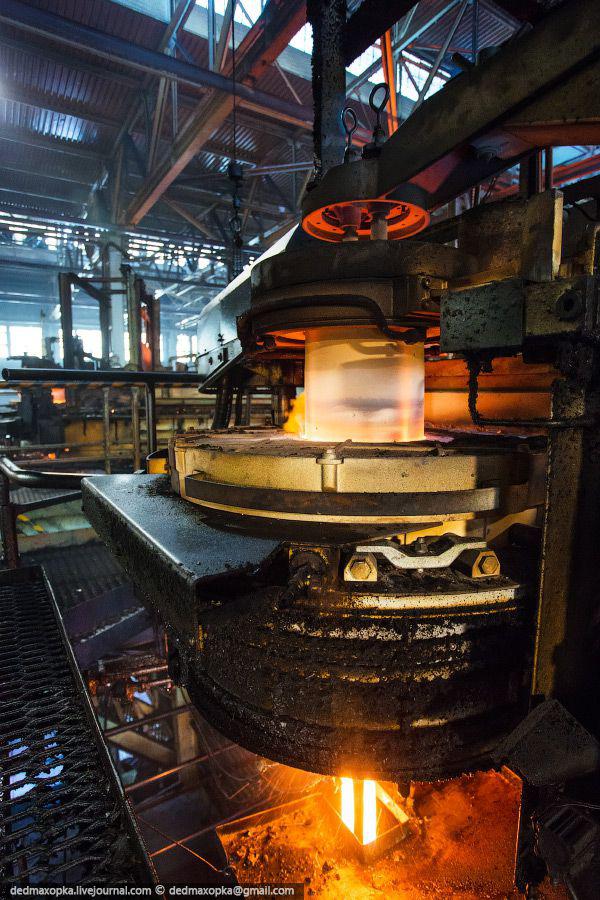
The process of creating gob.
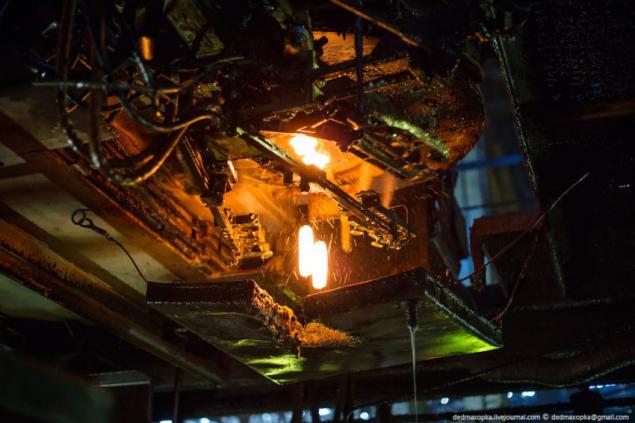
Finished glass melt is fed to the molding machines, where the molding products with use of appropriate equipment.
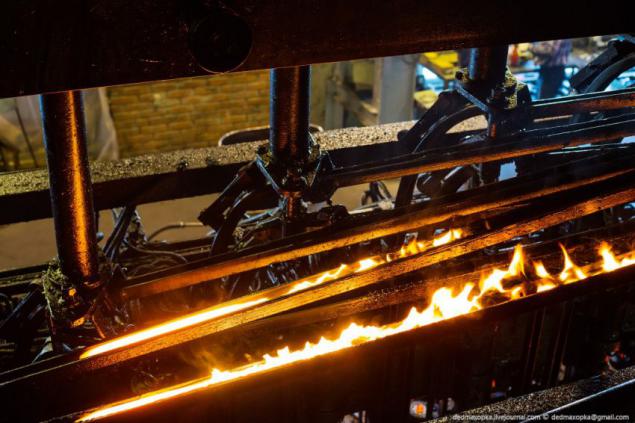
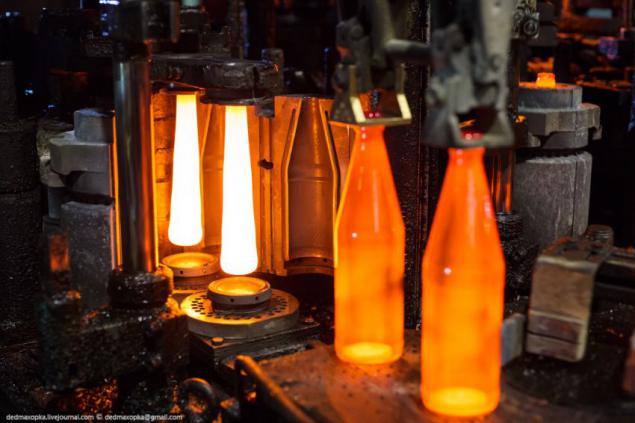
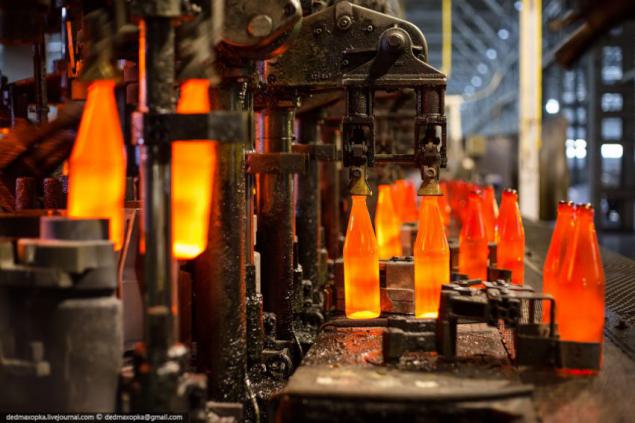
Desyatisektsionnaya line, producing a brown glass bottle.
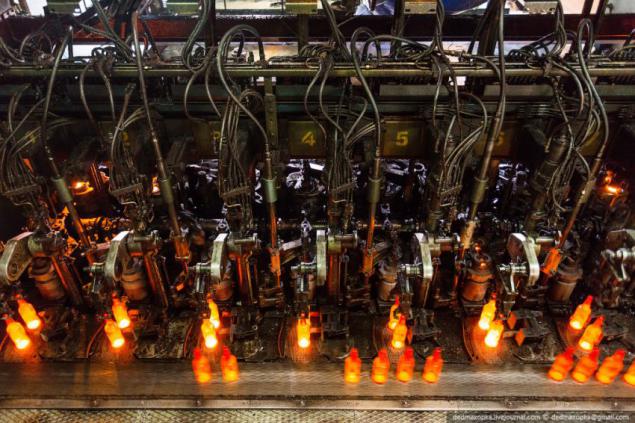
After passing through the forming process, glassware is additionally heat treatment (annealing) in the direct heating furnace. Annealing is required to remove internal residual stress in glass, which gives the product integrity during subsequent processing and operation.
The temperature of the product at the inlet to the furnace annealing: approx. 400 ° C - 500 ° C.
The temperature of the product at the output: approx. 50 ° C - 80 ° C.
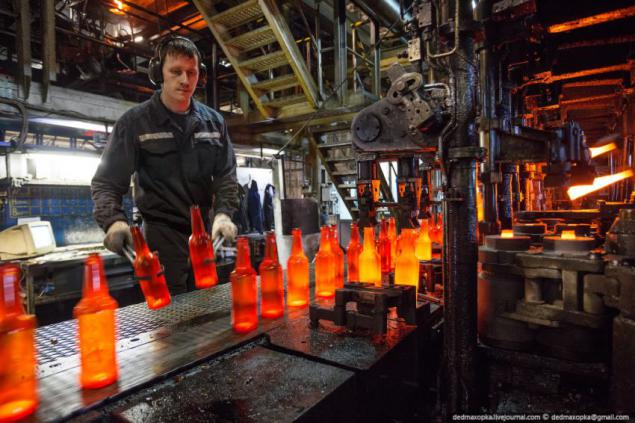
Glass after annealing
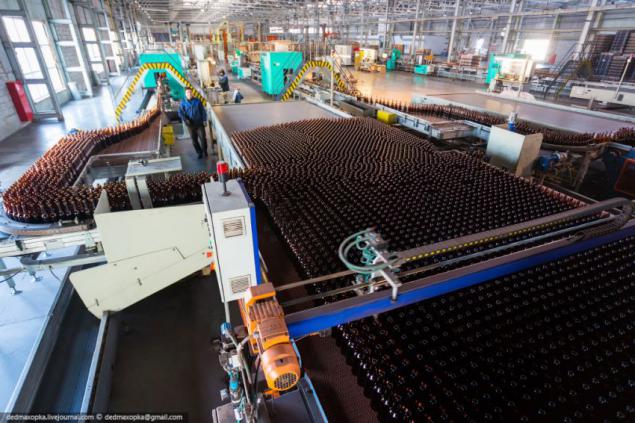
Spraying bottle with a special solution, which prevents scratches and scuffs on the bottles during transportation.
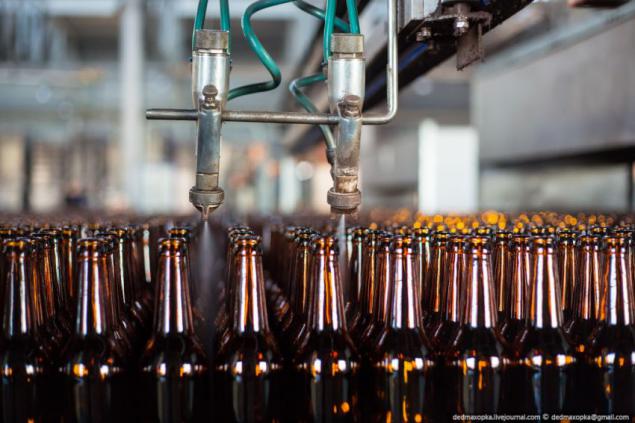
Products are ready, it remains only to pass quality control.

This complex is equipped with modern glass inspection machines that every second scan parameters for each glass bottles to meet customer requirements.
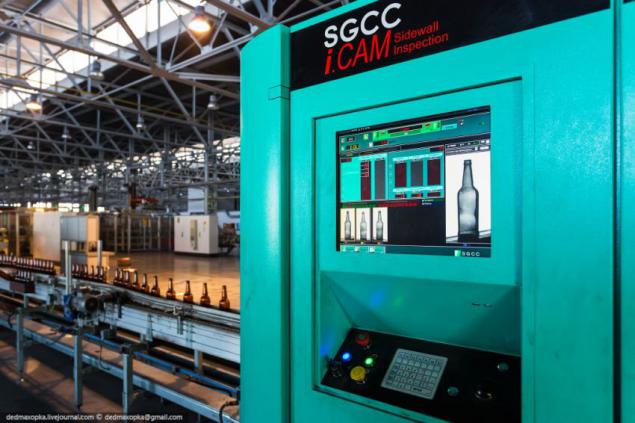
Packaged products.
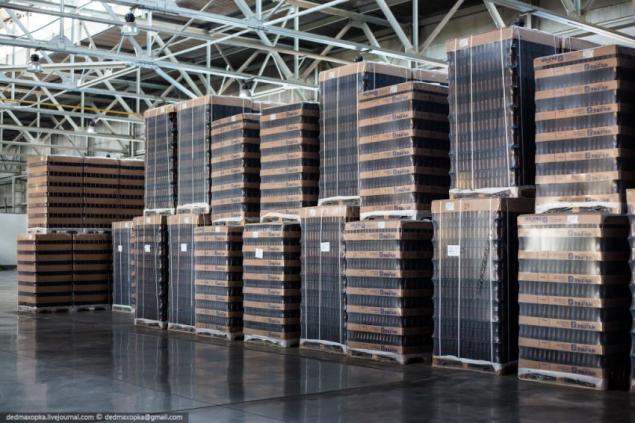
I showed the process of manufacturing glass bottles on the new complex. There is another shop where they make clear bottles and jars, where quality control is done manually. The first 4 and 7 following photos taken right there.
Production of both departments are very noisy. Have to go to earplugs or noise reducing headphones.
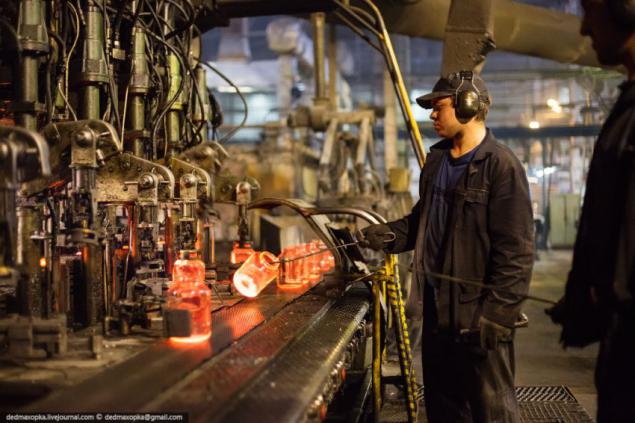
The process of creating a two-liter cans.
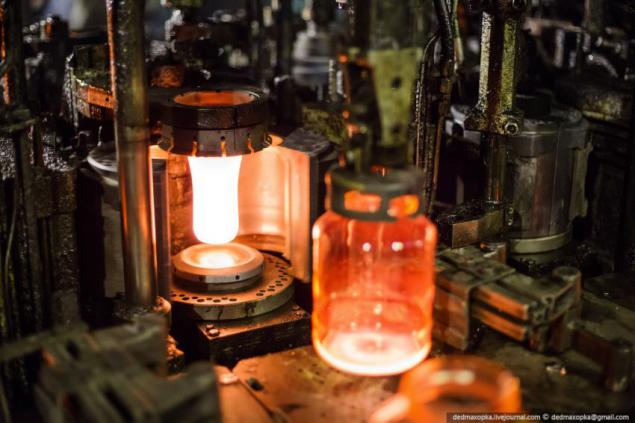
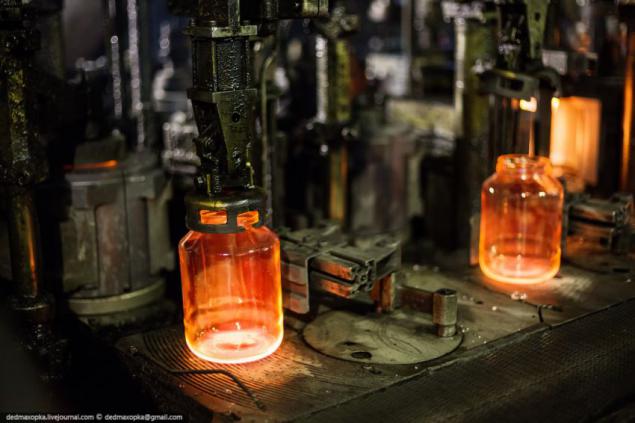
Chekushki.
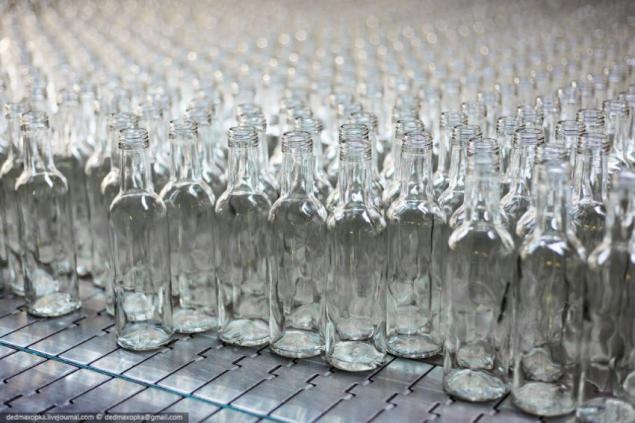
Vodka bottles after annealing.
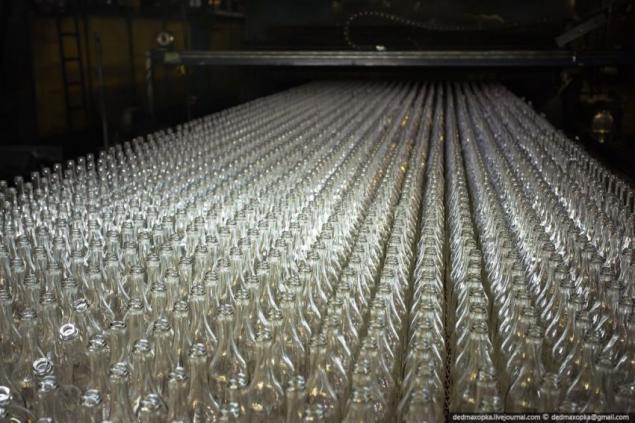
Quality control.
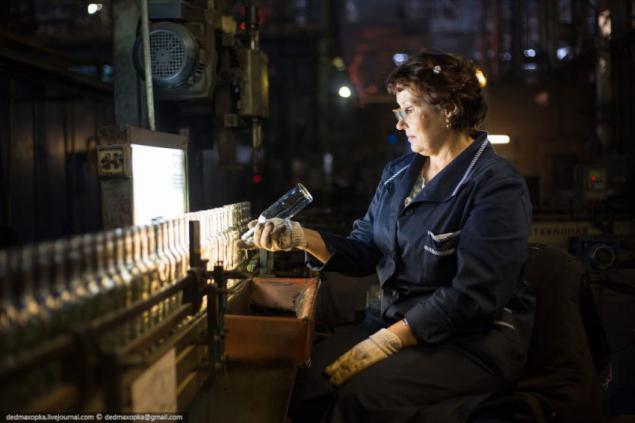
Finished products.
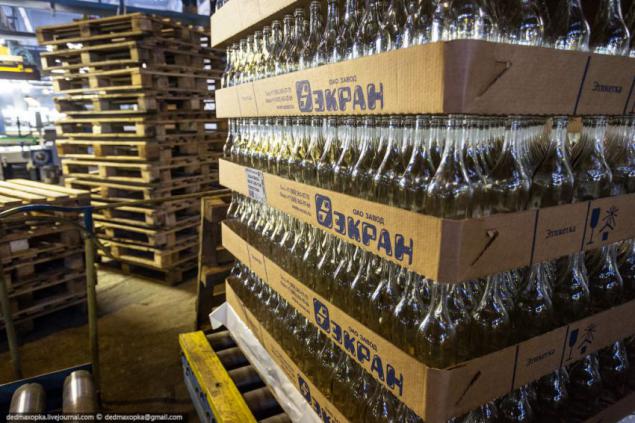
Small video, filmed in the production.
--img27--
Source: dedmaxopka.livejournal.com