945
Excursion to Vyksa Steel Works
Back in the Soviet era, it has become the largest manufacturer VMZ electric-welded pipes and railway wheels. In one post can not embrace all the production facilities of the company. I'll show you the ISS-500 (no, this is not the international space station) and complex electric-welded pipe of large diameter pipes, which are issued single-seam welded pipes for main oil and gas pipelines with a diameter up to 1420 mm and wall thickness up to 48 mm.
Slyabohranilische. Here begins the MCS-500. ISS - metallurgical complex mill-5000. The construction of the complex took four years - from May 2007 to October 2011. (commissioned November 25, 2011). Products MKS-5000 - a thick sheet of high-strength steel for the manufacture of large diameter pipes. The design capacity of the complex is 1, 5 million. Tonnes of sheet (rental) per year.
The slabs are sent to the gas stove.
There slab during 4-5 hours heated at a temperature of from 900 to 1300 degrees. Control of temperature of metal in the furnace is Dualsens temperature units.
Harvesting warmed up and ready for execution at the mill.
Such is the red brick enters the rolls.
In the photo is visible on the time of descaling hot rolling mill - scale removal from the metal surface with water under high pressure.
Our slab already half unrolled.
As a pancake in a frying pan.
The drive system of the rollers of the motor. The incredible beauty of the movement.
Each roller mill to move the sheet has an individual drive.
The water supply system for the installation of cooling sheets.
Megaprivod clips! Everything works from a single motor and a tricky junction box!
Water on plant circulates in a closed circuit.
Cooling of rolled sheet.
Deep - slow cooling section sheets, which lasts at least 48 hours!
And right there is a refrigerator. It is written on the label.
It rolled sheets are cooled and fall into a cold straightening machine.
Visual inspection is almost finished sheet.
Tilter for turning sheet. It is necessary because it is necessary to examine both the surface.
Scissors for trimming. Can cut metal thickness up to 48 mm. Basically, fat
a sheet of high strength steel is ready. Then he moved to the workshop, which produces pipe.
From a warehouse in the right sheet output tray served.
Very nice magnetic grip.
In the corners of the sheet strips welded technology - they are used to ensure the quality of the weld seam of the pipe. The fact is that at the beginning and end of the seam welding process does not meet the required parameters. And not to cut the piece of pipe came up with a solution.
Sheets with welded bars on the conveyor technology comes at a press hem edges.
Press hem edges. Here, the sheet is prepared for processing in stepwise molding press.
The next step - stepwise molding press.
Presses 6000 tonnes oppression sheet into a tube.
A few minutes - and prefabricated pipe ready.
Already familiar technology for welding strips. Note: the pipe is far from a perfect circle.
Visual inspection of the inner surface.
In the first phase welding is done inseam that just pierces the edge of the pipe.
Trims boil manually.
Generally pipe shop is huge. Around there are different lines for the production of all kinds of pipes, differing from each other in diameter and purpose. Alas, one does not show the entire reportage.
The main welding seam. First, the electrodes are exposed.
The tube is then pushed back a little back to the start of the process was at the bar.
Welding seam!
Flux is suctioned to clean and reuse.
Ready seam.
All pipe is ready. At the same time there is a number of welding pipes.
At each stage, in addition to the visual and automated control is present. In the photo, for example, the installation of inspection for each seam of each tube!
This pulls the tube from the conveyor for a detailed study. It will cut into pieces, check seam section, will take samples of metal and probed every part!
Russian size! Just that same 1,420-mm pipes with a wall thickness of 48 mm.
Behind the scenes remained the installation of expansion, which decompresses the pipe from the inside, giving it the shape of a perfect circle. Next, the pipe cover internal and external anti-corrosion coating and sent to the warehouse where and shipped to customers.
April 15 at the factory produced the first pipe to the underwater section of the "South Stream"! Total company will supply for this project 600 kilometers of pipes. The depth of the stream more than two kilometers, so the pipeline increased requirements. Specifically, the roundness can be up to four millimeters. This value is less than twice the standard. VSW is able to release an hour about 135 tons of such pipes (the weight of one - 9 tons.
And some photos from the company, which looks like a city.
A beautiful bucket of steel mill division of railway wheels.
One of the stages of the process for the production of railway wheels. Cool the mold, which is filled with steel ingots, from which subsequently make wheels. Of this production must, of course, prepare a separate report.
Just a beautiful view of the railway track. By the way, their total length at VSW - 157 kilometers.
. Really like this shot ...
Source: russos.livejournal.com
Slyabohranilische. Here begins the MCS-500. ISS - metallurgical complex mill-5000. The construction of the complex took four years - from May 2007 to October 2011. (commissioned November 25, 2011). Products MKS-5000 - a thick sheet of high-strength steel for the manufacture of large diameter pipes. The design capacity of the complex is 1, 5 million. Tonnes of sheet (rental) per year.
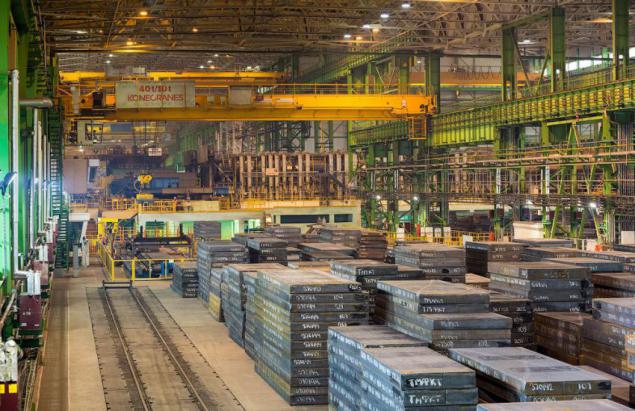
The slabs are sent to the gas stove.
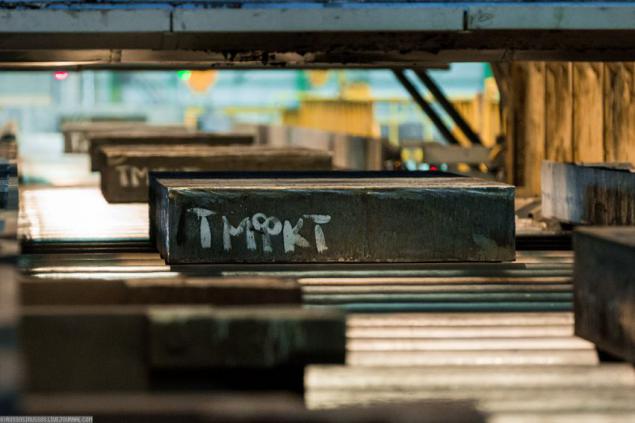
There slab during 4-5 hours heated at a temperature of from 900 to 1300 degrees. Control of temperature of metal in the furnace is Dualsens temperature units.
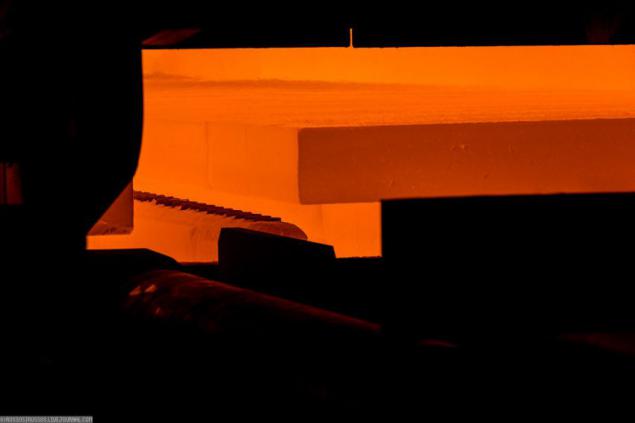
Harvesting warmed up and ready for execution at the mill.
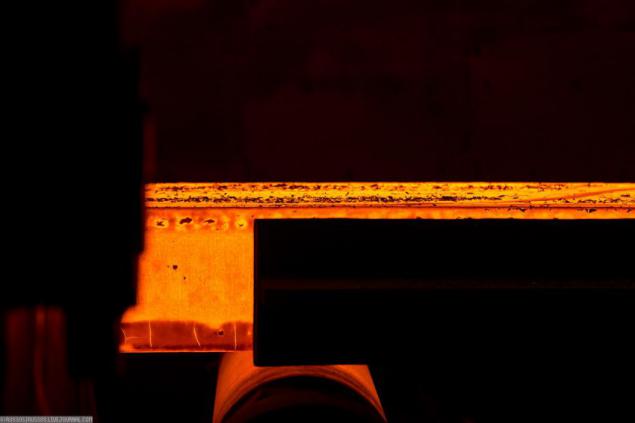
Such is the red brick enters the rolls.
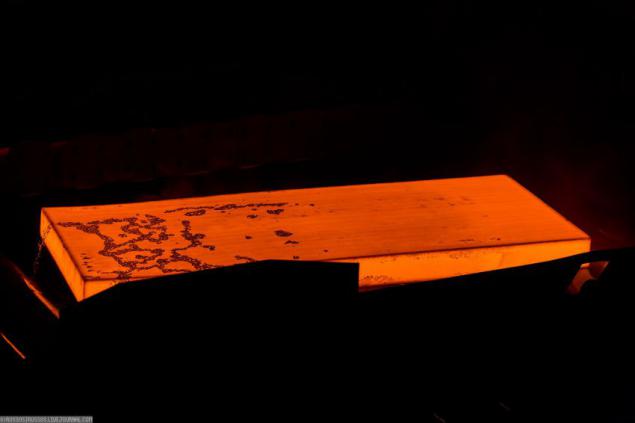
In the photo is visible on the time of descaling hot rolling mill - scale removal from the metal surface with water under high pressure.
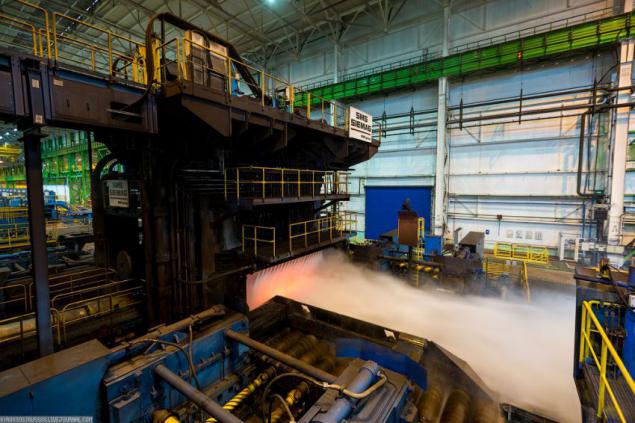
Our slab already half unrolled.
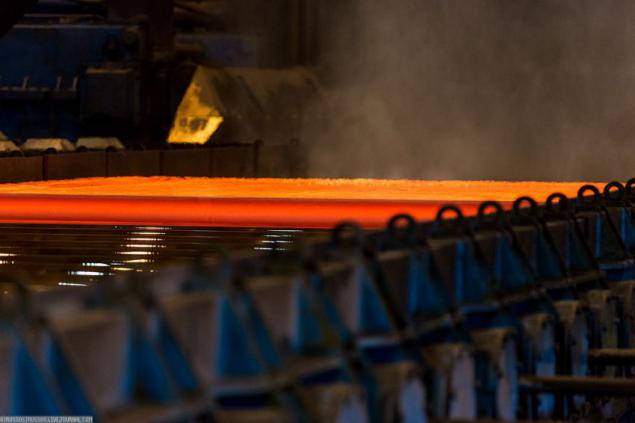
As a pancake in a frying pan.
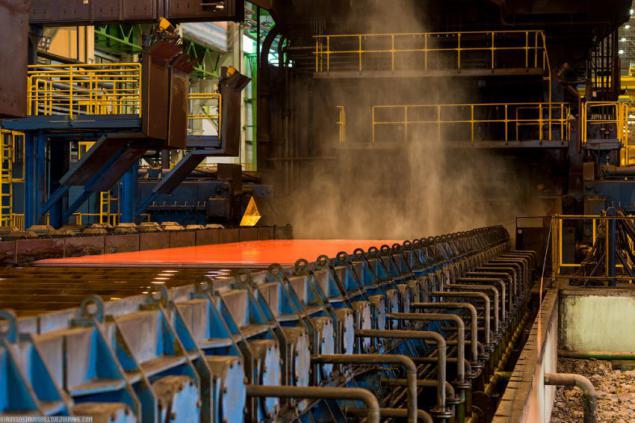
The drive system of the rollers of the motor. The incredible beauty of the movement.
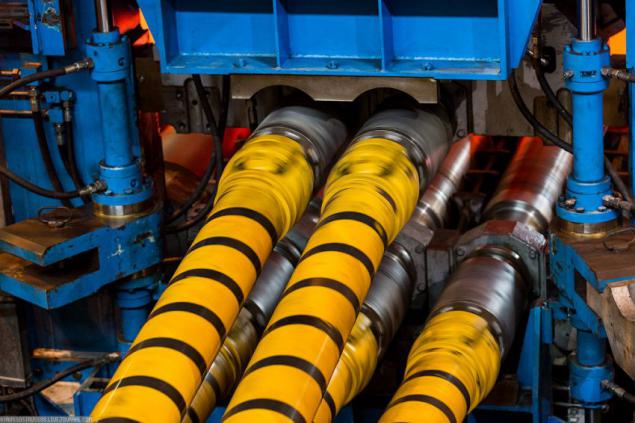
Each roller mill to move the sheet has an individual drive.
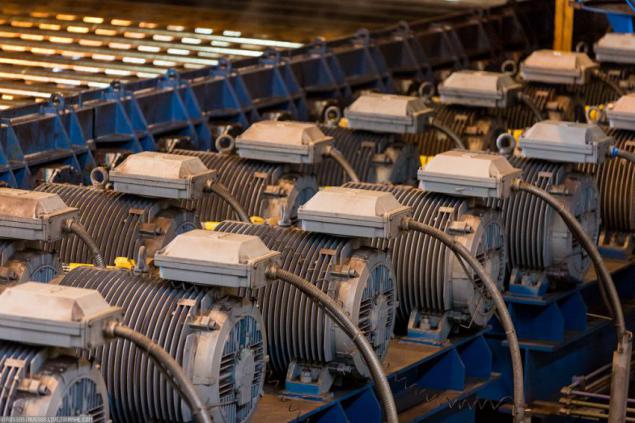
The water supply system for the installation of cooling sheets.
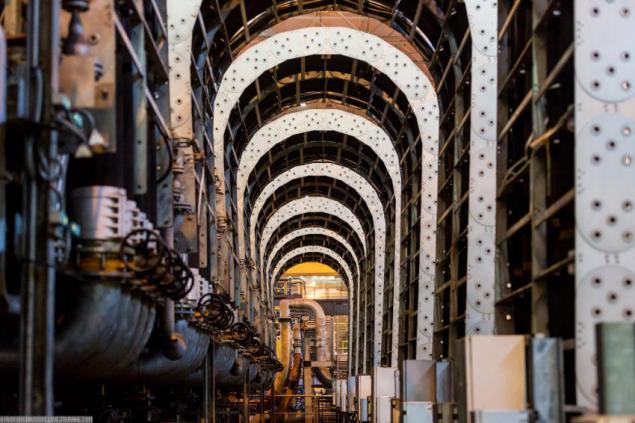
Megaprivod clips! Everything works from a single motor and a tricky junction box!
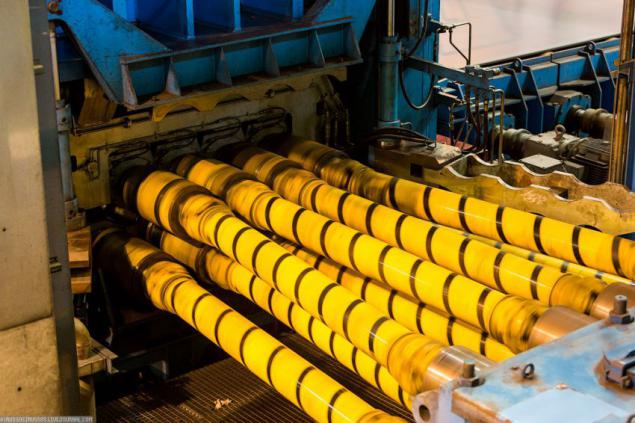
Water on plant circulates in a closed circuit.
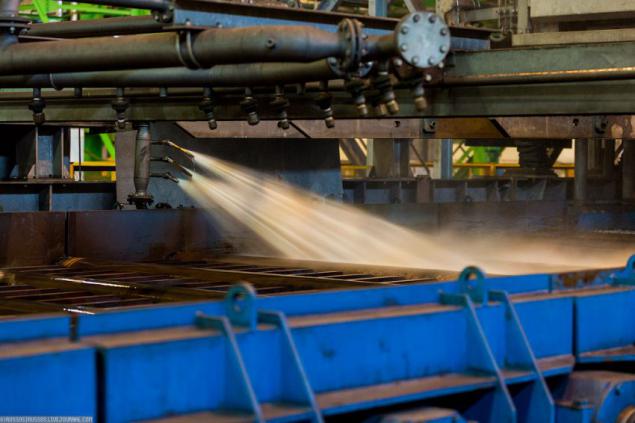
Cooling of rolled sheet.
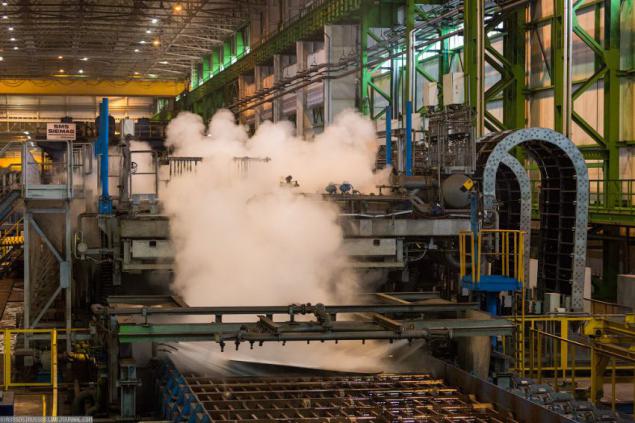
Deep - slow cooling section sheets, which lasts at least 48 hours!
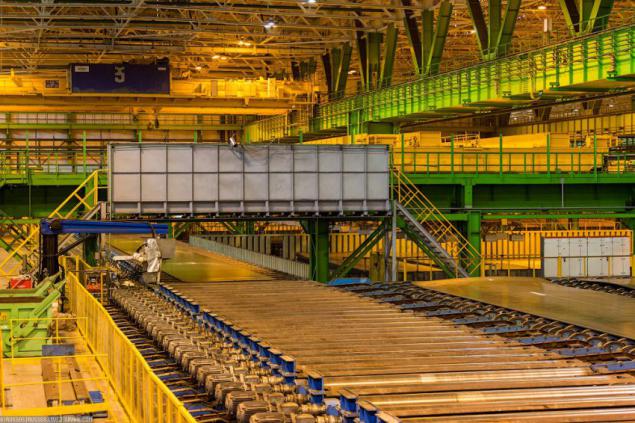
And right there is a refrigerator. It is written on the label.
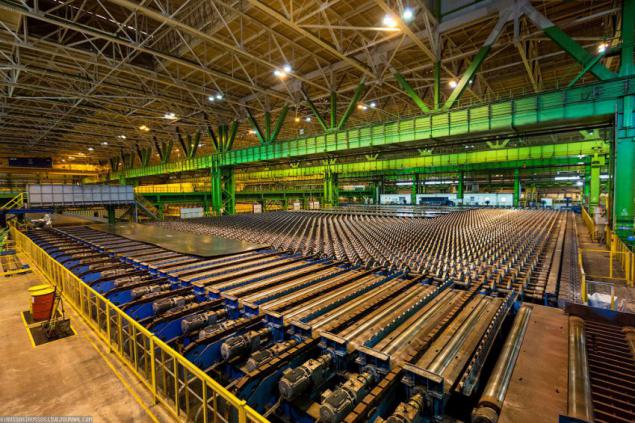
It rolled sheets are cooled and fall into a cold straightening machine.
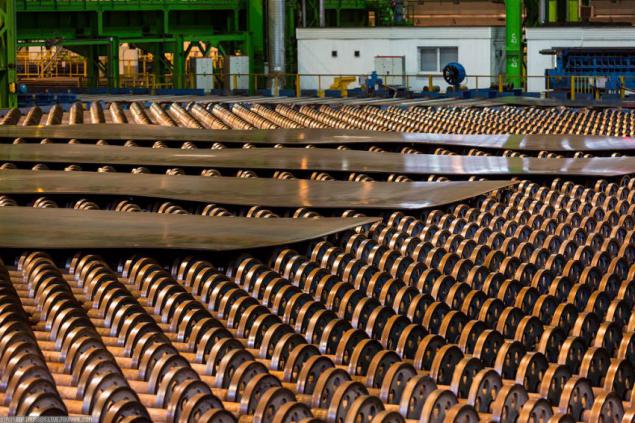
Visual inspection is almost finished sheet.
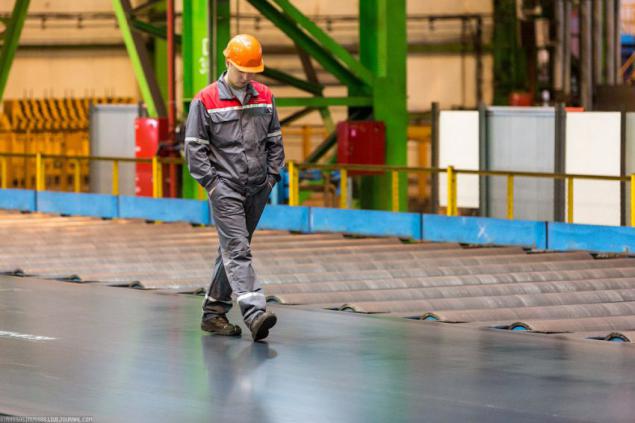
Tilter for turning sheet. It is necessary because it is necessary to examine both the surface.
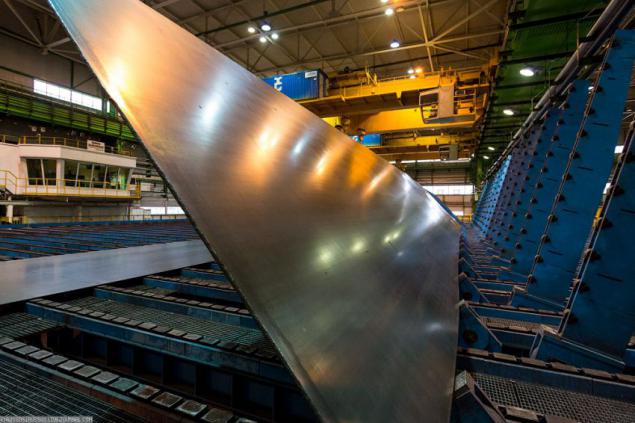
Scissors for trimming. Can cut metal thickness up to 48 mm. Basically, fat
a sheet of high strength steel is ready. Then he moved to the workshop, which produces pipe.
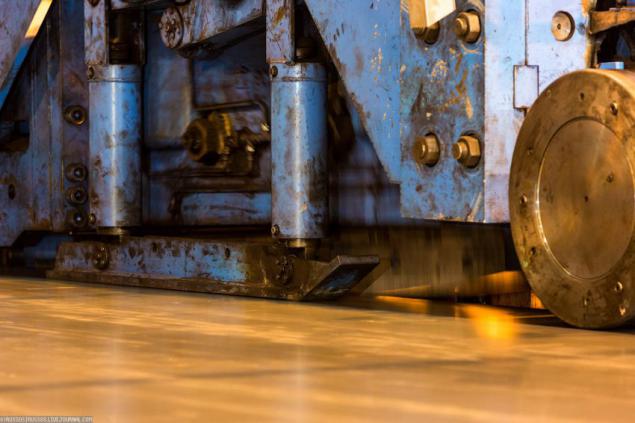
From a warehouse in the right sheet output tray served.
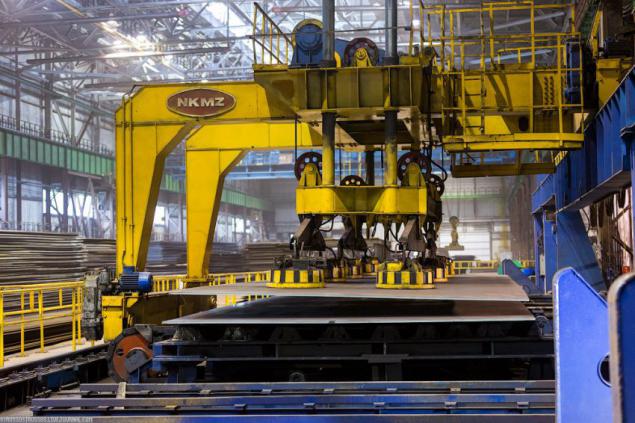
Very nice magnetic grip.
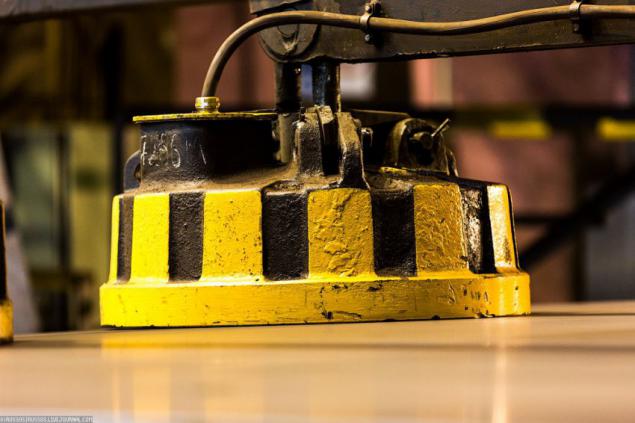
In the corners of the sheet strips welded technology - they are used to ensure the quality of the weld seam of the pipe. The fact is that at the beginning and end of the seam welding process does not meet the required parameters. And not to cut the piece of pipe came up with a solution.
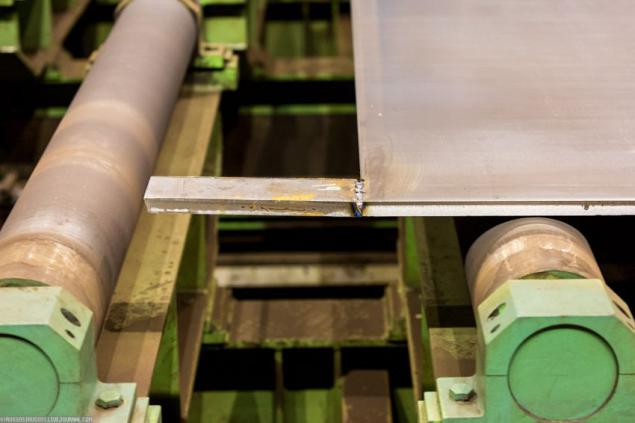
Sheets with welded bars on the conveyor technology comes at a press hem edges.
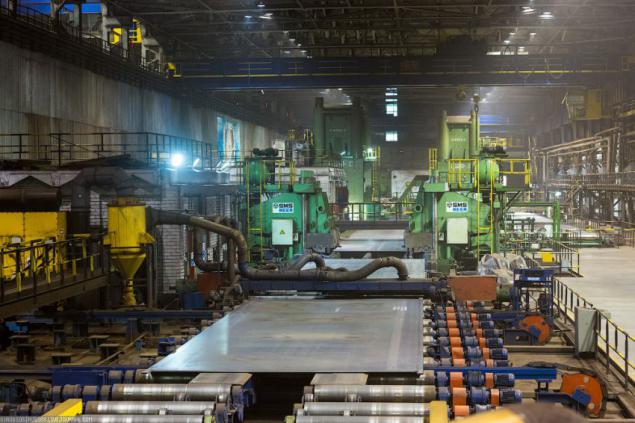
Press hem edges. Here, the sheet is prepared for processing in stepwise molding press.
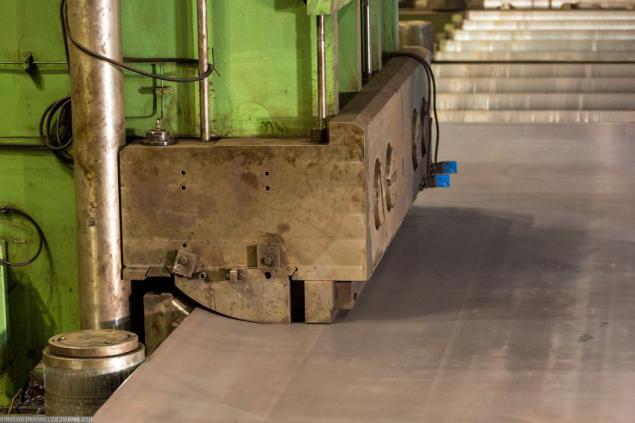
The next step - stepwise molding press.
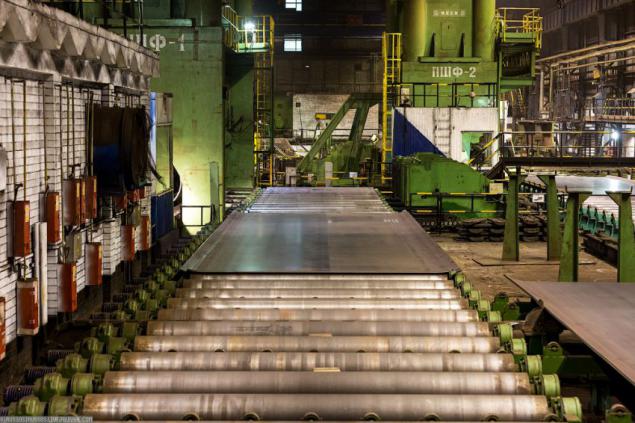
Presses 6000 tonnes oppression sheet into a tube.
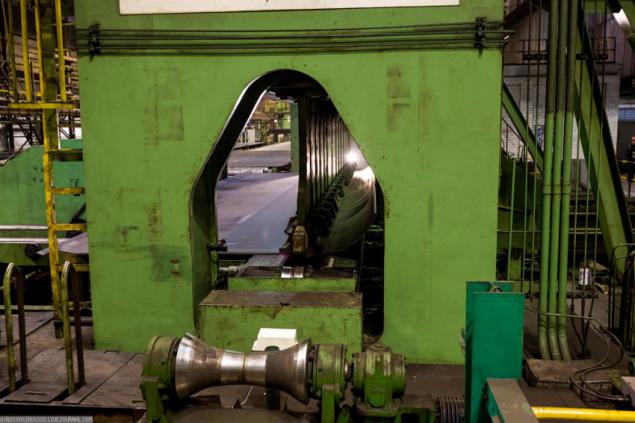
A few minutes - and prefabricated pipe ready.
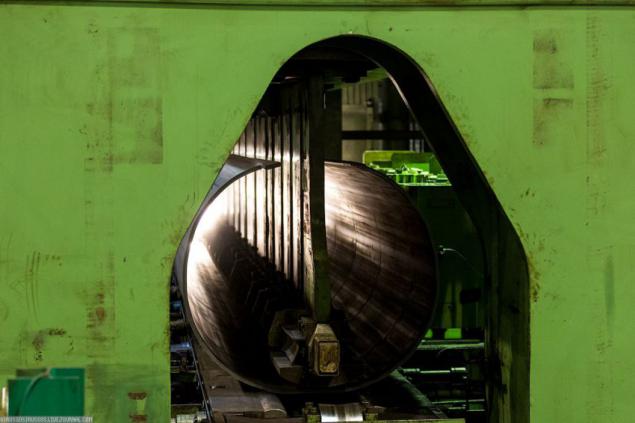
Already familiar technology for welding strips. Note: the pipe is far from a perfect circle.
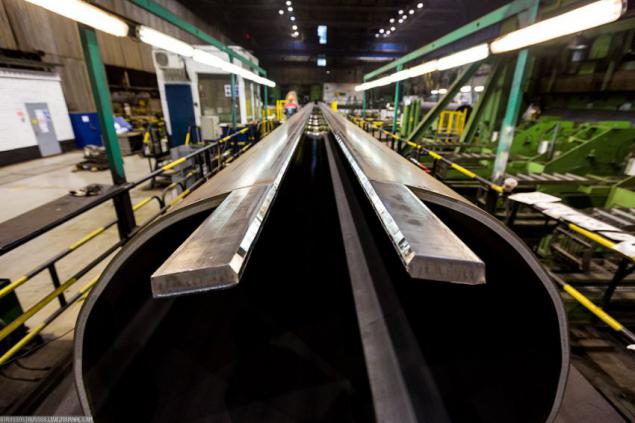
Visual inspection of the inner surface.
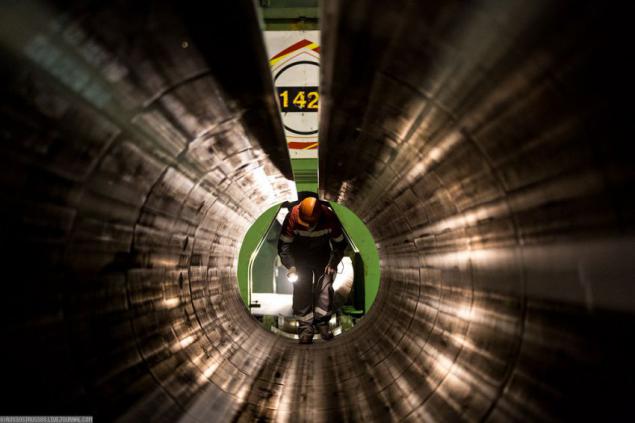
In the first phase welding is done inseam that just pierces the edge of the pipe.
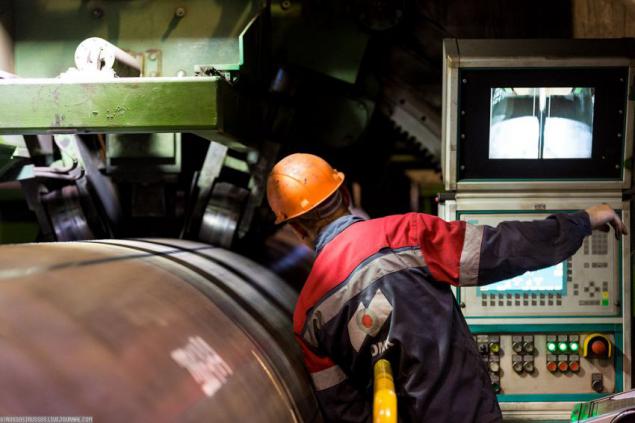
Trims boil manually.
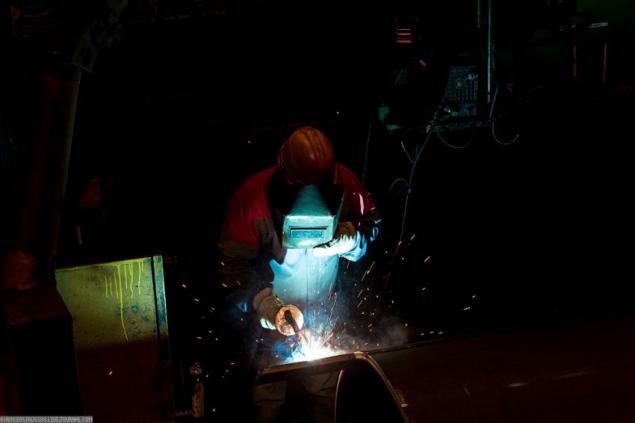
Generally pipe shop is huge. Around there are different lines for the production of all kinds of pipes, differing from each other in diameter and purpose. Alas, one does not show the entire reportage.
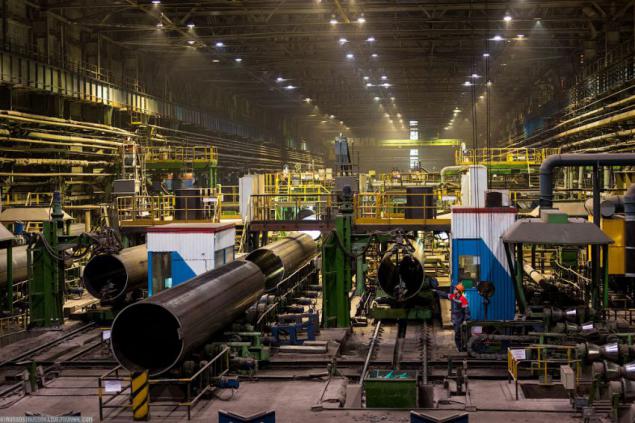
The main welding seam. First, the electrodes are exposed.
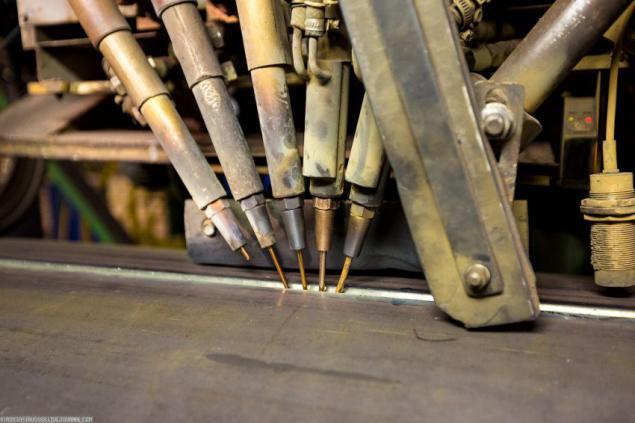
The tube is then pushed back a little back to the start of the process was at the bar.
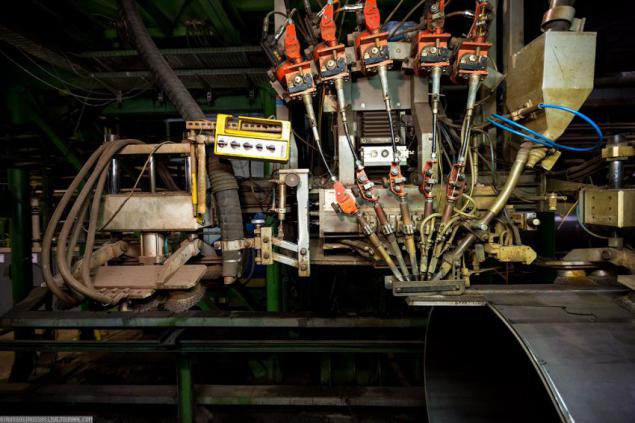
Welding seam!
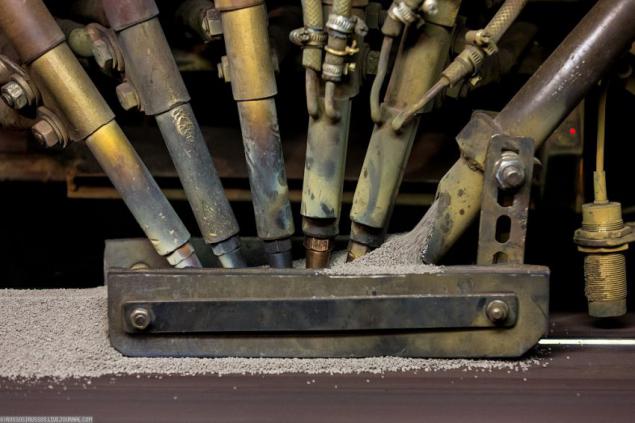
Flux is suctioned to clean and reuse.
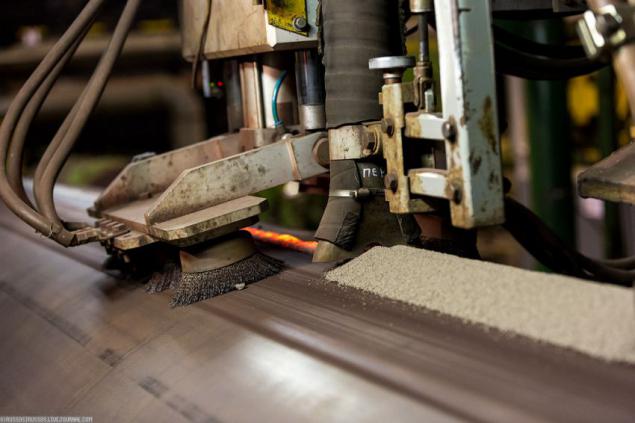
Ready seam.
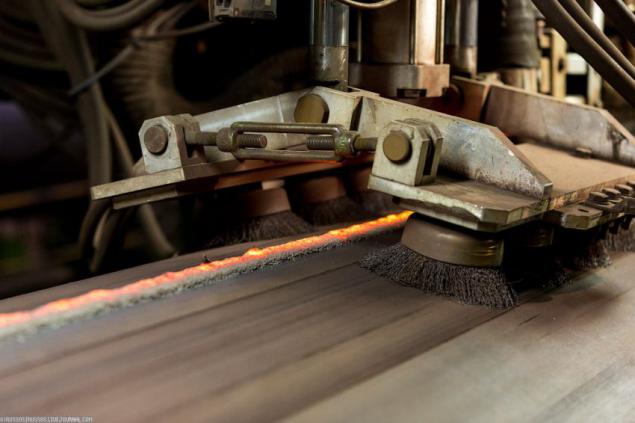
All pipe is ready. At the same time there is a number of welding pipes.
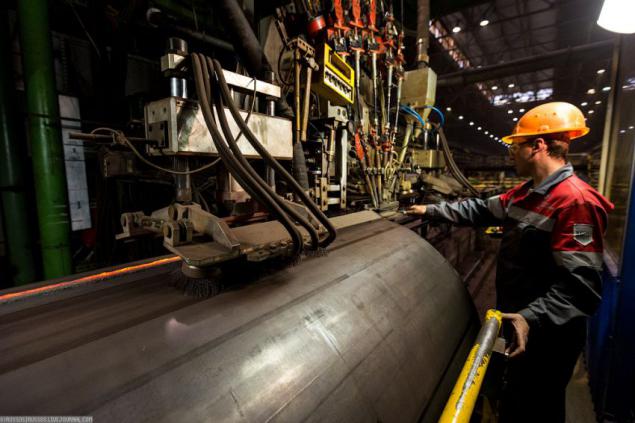
At each stage, in addition to the visual and automated control is present. In the photo, for example, the installation of inspection for each seam of each tube!
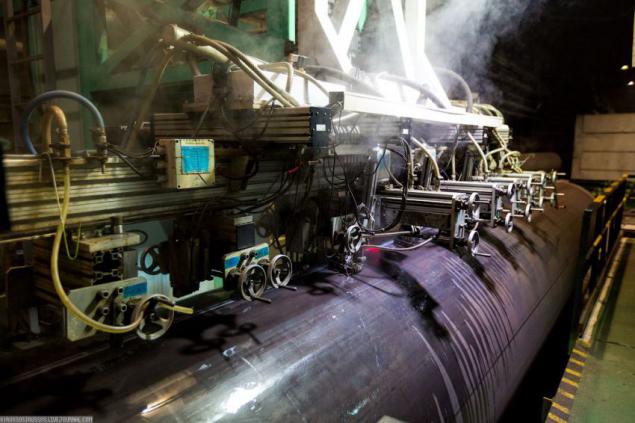
This pulls the tube from the conveyor for a detailed study. It will cut into pieces, check seam section, will take samples of metal and probed every part!
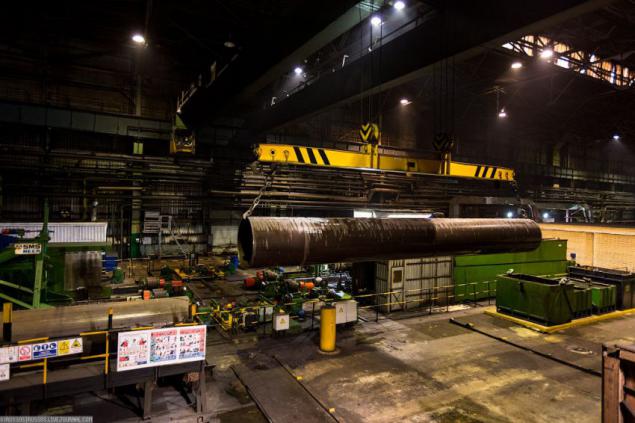
Russian size! Just that same 1,420-mm pipes with a wall thickness of 48 mm.
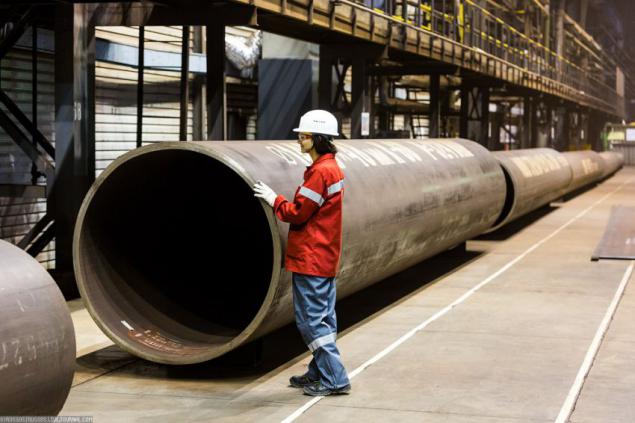
Behind the scenes remained the installation of expansion, which decompresses the pipe from the inside, giving it the shape of a perfect circle. Next, the pipe cover internal and external anti-corrosion coating and sent to the warehouse where and shipped to customers.
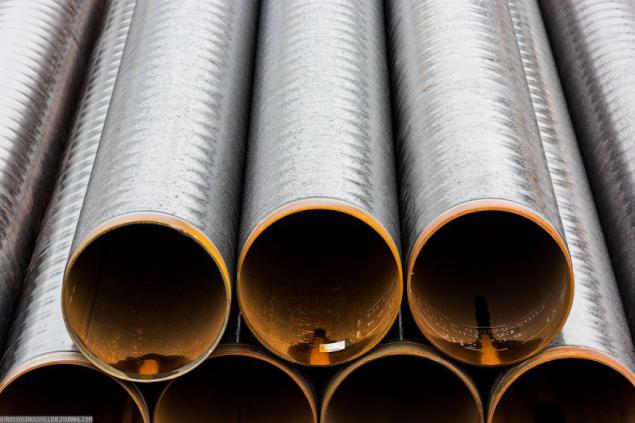
April 15 at the factory produced the first pipe to the underwater section of the "South Stream"! Total company will supply for this project 600 kilometers of pipes. The depth of the stream more than two kilometers, so the pipeline increased requirements. Specifically, the roundness can be up to four millimeters. This value is less than twice the standard. VSW is able to release an hour about 135 tons of such pipes (the weight of one - 9 tons.
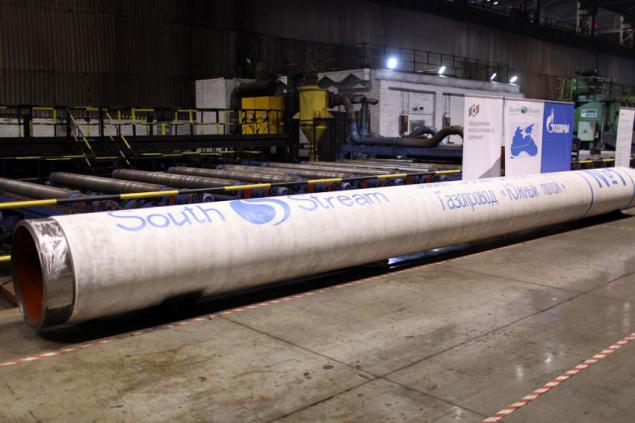
And some photos from the company, which looks like a city.
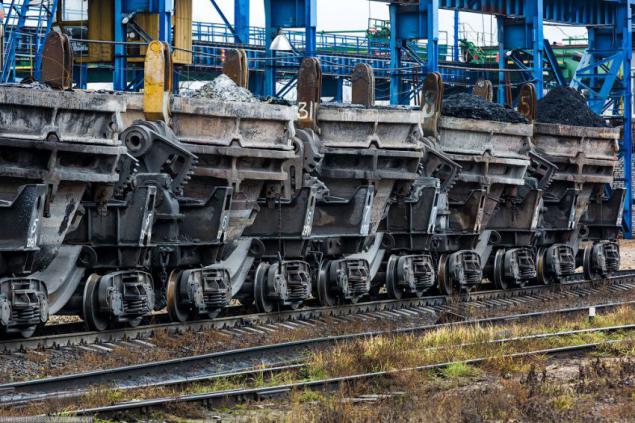
A beautiful bucket of steel mill division of railway wheels.
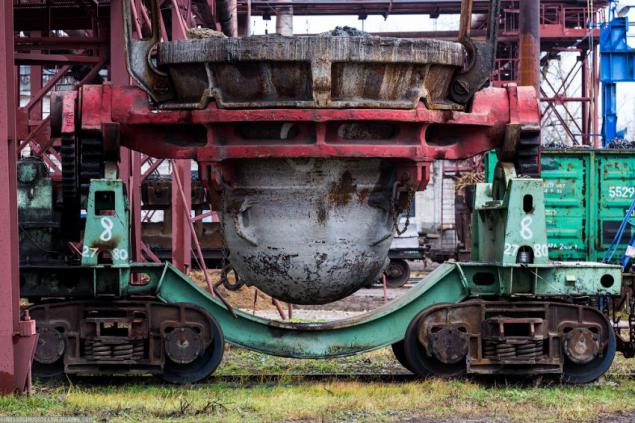
One of the stages of the process for the production of railway wheels. Cool the mold, which is filled with steel ingots, from which subsequently make wheels. Of this production must, of course, prepare a separate report.
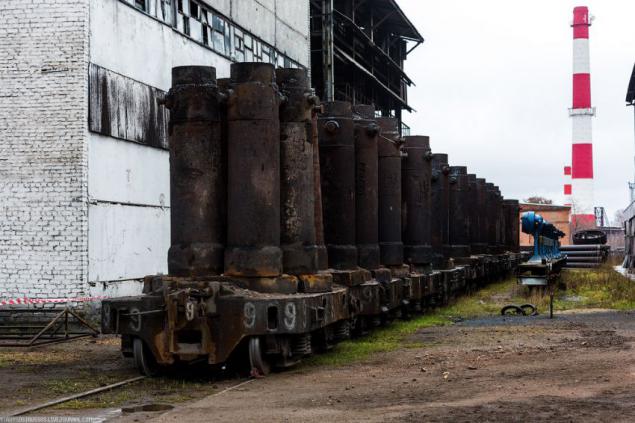
Just a beautiful view of the railway track. By the way, their total length at VSW - 157 kilometers.
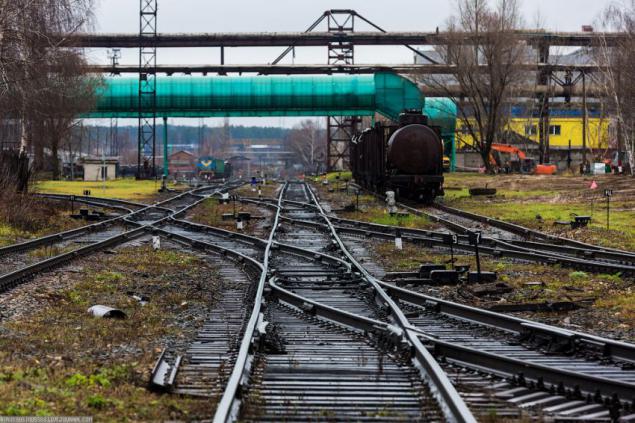
. Really like this shot ...
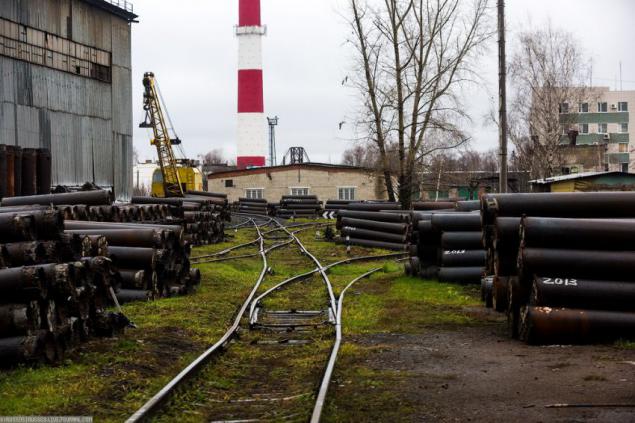
Source: russos.livejournal.com