927
Production of metallurgical silicon
With fotopomoschyu blogger victorprofessor we will visit the plant Silicium Kazakhstan, which produces silicon metal carbothermic process using special ore-thermal furnaces. This is one of the largest factories in the country and the only silicon plant in Kazakhstan. The plant was launched in autumn 2010.
As the prevalence of the earth's crust silicon is second only to oxygen, it is found mainly in the form of oxygen compounds (silica, silicate, etc.). High purity silicon used in semiconductor technology, and technical grade (96-99% Si) - black and nonferrous metallurgy for non-ferrous alloys on the basis of (silumin, etc.), Alloying (silicon steel and alloys used in electrical equipment) and deoxidation Steel and Alloys (removal of oxygen), the production of silicide, etc.
In the production process at the factory produces two types of products:
- Metal silicon (having a purity of not less than 98, 5%, used in aluminum and chemical industries)
- Silicon dust (ultrafine material obtained in the process of gas purification furnaces, it is used in the production of extra strong dry mixes)
17 ph
2. In the industry of technical purity silicon is obtained by restoring the melt SiO2 coke at a temperature of about 1800 degrees Celsius in the ore-smelting shaft furnaces. The purity of the thus obtained silicon can reach 99% 9 (main impurities - carbon and metals).
3. The basic unit for melting of silicon is a single-arc ore-thermal three-phase electric power from 8 to 25 MVA. The furnace is a round steel housing with a bottom, lined with refractory brickwork. Hearth (bottom) and the part of the wall height are lined with graphite blocks, the next layer of magnesite brick and an outer layer - fireclay (porous brick made of special refractory clay).
4. Power supply to the working space of the furnace is carried out using an electrode made of graphite. Self-baking electrodes in silicon technology are not applicable because of the possible contamination of the product components and the housing electrode electrode paste (iron, calcium, aluminum). The electrical parameters of the recovery process provided by a furnace transformer connected to the electrode short high current network, in which the current is 40-80 kA. As the mechanical electrode consumption are periodically lengthens Bypass via mechanisms. Adjusting the predetermined current strength of the electrode is performed by electrode perescheniya vertical axis.
5. Release of silicon is carried out almost continuously through Ledkov (a hole in the lining) in a steel-lined mold.
6. shunted arc furnace is a restoration of silicon from silica quartzite carbon reductant. Theoretical temperature of the beginning of 1670 degrees Celsius. The main types of reducing agents include charcoal (birch, pine), petcoke and coal.
7. From the ore-thermal furnace, the molten silica gets into the ladle from which it is poured into molds.
8. The plant currently operates one furnace, it will soon be put into operation the second, and then the plant's production capacity will be 30 thousand. Tons of silicon metal per year. In addition, the products will continue to be supplied to the polysilicon plant: its construction in Omsk starts this year. Now the finished products are exported to the EU.
9. By the way, the market price of silicon metal - EUR 2,500 per tonne.
10. Plant potrebyaet huge amounts of electricity to maintain the temperature in the furnace. Production around the clock. And at the first start of the furnace to its heating to the working temperature it took about two weeks.
11. The plant as a raw material for the production of silicon metal used vein quartz from Ulytautskogo area.
12. In the forms of silicon metal cools and solidifies.
13. Silicon metal is the basis for high-tech industry. Silicon - that solar cells and semiconductors for PCs, and much, much more.
14. By the way, the production of silicon metal completely without waste. Above the stove there are air ducts, and all the dust goes into the gas cleaning, where trapped microparticles. This silicon dust is a useful product in another part of the production. For example, earlier in melted quartz Europe only to it and then add to grind the concrete, in solutions which have a very high restorative properties. The quartz crystal lattice is very strong. And the 900-th grade of concrete can be obtained only by means of silicon. And there are waterproof putty, impact-resistant floors, these products are used to strengthen the underground tunnels.
15. After ostavanie silicon crushed into small pieces hydraulic hammer.
16. The finished product is packed in big bags - plastic bags for up 1,000 kilograms of metallurgical silicon and sent to customers.
17. What can be done with a commercial silicon? Technological chain in the production of silicon continues: metallurgical silicon - polysilicon - monocrystalline silicon - silicon wafers. For further purification of metallurgical silicon is distilled, turning to environmentally harmful chlorine compounds: dichlorosilane or trichlorosilane. After cleaning, the latter on a large distillation columns and polysilicon deposition processes is obtained, where the concentration of impurities is not more than ten-thousandth of a percent. Thereafter, it is melted into single crystal material, and single crystals are cut on the plate. The obtained 80% of monocrystalline silicon used in electronics.
Source:
As the prevalence of the earth's crust silicon is second only to oxygen, it is found mainly in the form of oxygen compounds (silica, silicate, etc.). High purity silicon used in semiconductor technology, and technical grade (96-99% Si) - black and nonferrous metallurgy for non-ferrous alloys on the basis of (silumin, etc.), Alloying (silicon steel and alloys used in electrical equipment) and deoxidation Steel and Alloys (removal of oxygen), the production of silicide, etc.
In the production process at the factory produces two types of products:
- Metal silicon (having a purity of not less than 98, 5%, used in aluminum and chemical industries)
- Silicon dust (ultrafine material obtained in the process of gas purification furnaces, it is used in the production of extra strong dry mixes)
17 ph
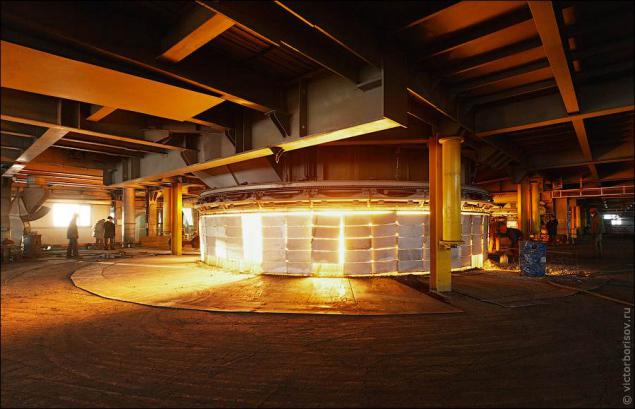
2. In the industry of technical purity silicon is obtained by restoring the melt SiO2 coke at a temperature of about 1800 degrees Celsius in the ore-smelting shaft furnaces. The purity of the thus obtained silicon can reach 99% 9 (main impurities - carbon and metals).
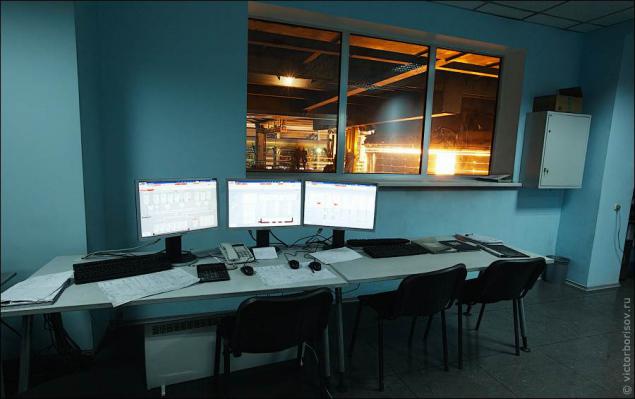
3. The basic unit for melting of silicon is a single-arc ore-thermal three-phase electric power from 8 to 25 MVA. The furnace is a round steel housing with a bottom, lined with refractory brickwork. Hearth (bottom) and the part of the wall height are lined with graphite blocks, the next layer of magnesite brick and an outer layer - fireclay (porous brick made of special refractory clay).
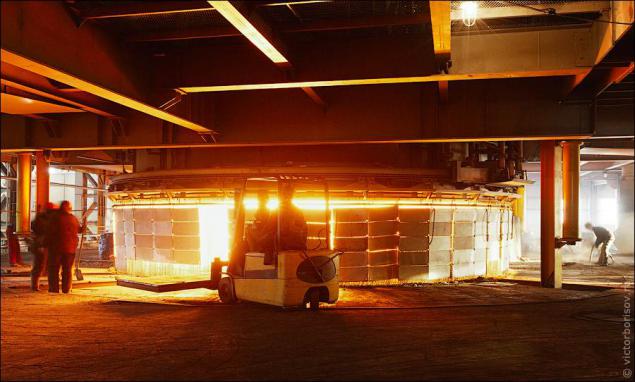
4. Power supply to the working space of the furnace is carried out using an electrode made of graphite. Self-baking electrodes in silicon technology are not applicable because of the possible contamination of the product components and the housing electrode electrode paste (iron, calcium, aluminum). The electrical parameters of the recovery process provided by a furnace transformer connected to the electrode short high current network, in which the current is 40-80 kA. As the mechanical electrode consumption are periodically lengthens Bypass via mechanisms. Adjusting the predetermined current strength of the electrode is performed by electrode perescheniya vertical axis.
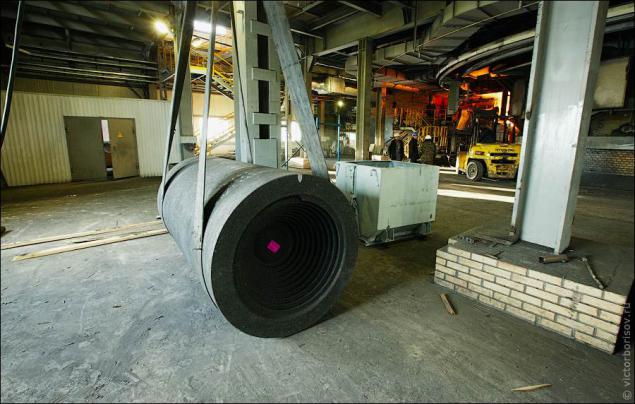
5. Release of silicon is carried out almost continuously through Ledkov (a hole in the lining) in a steel-lined mold.
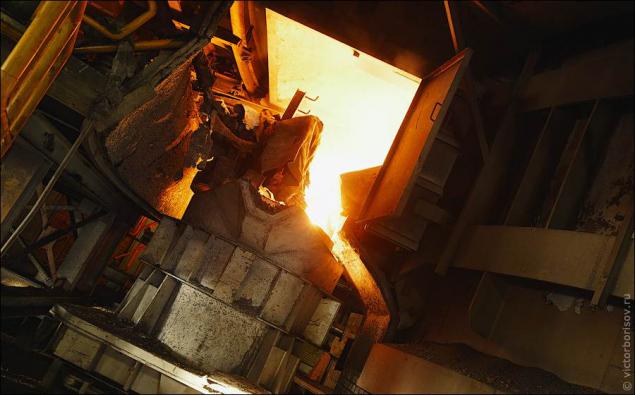
6. shunted arc furnace is a restoration of silicon from silica quartzite carbon reductant. Theoretical temperature of the beginning of 1670 degrees Celsius. The main types of reducing agents include charcoal (birch, pine), petcoke and coal.
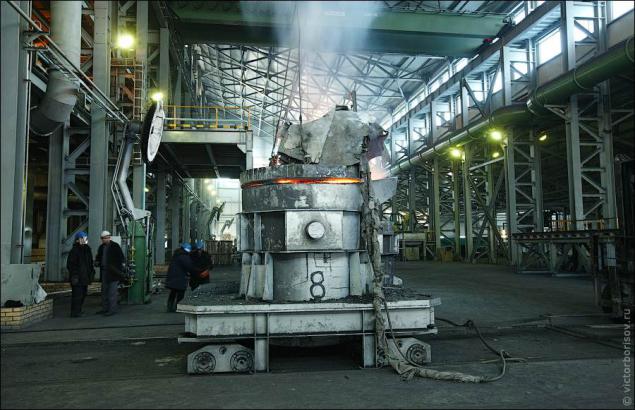
7. From the ore-thermal furnace, the molten silica gets into the ladle from which it is poured into molds.
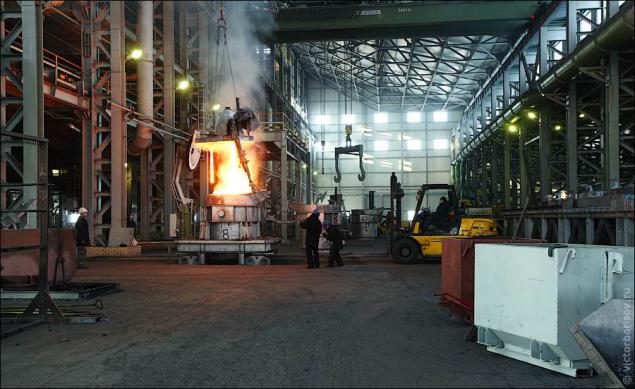
8. The plant currently operates one furnace, it will soon be put into operation the second, and then the plant's production capacity will be 30 thousand. Tons of silicon metal per year. In addition, the products will continue to be supplied to the polysilicon plant: its construction in Omsk starts this year. Now the finished products are exported to the EU.
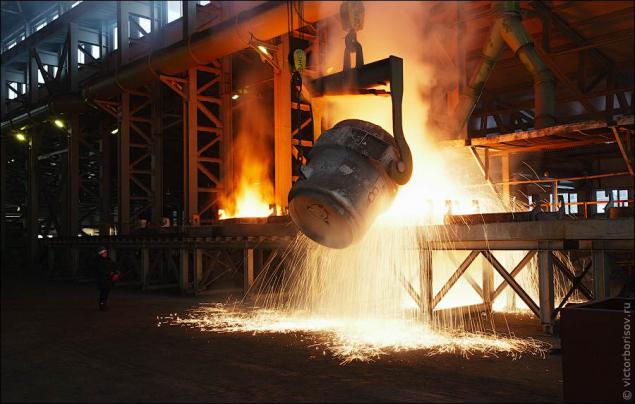
9. By the way, the market price of silicon metal - EUR 2,500 per tonne.
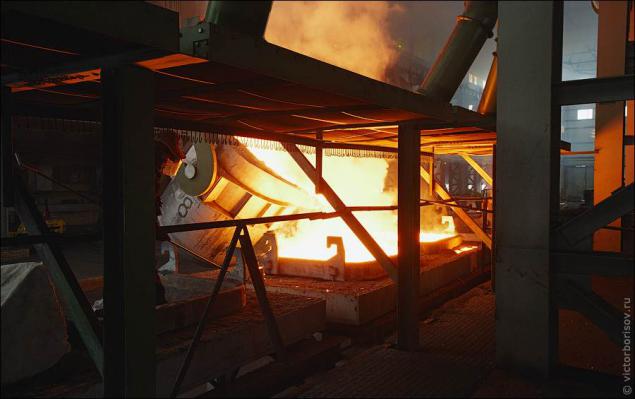
10. Plant potrebyaet huge amounts of electricity to maintain the temperature in the furnace. Production around the clock. And at the first start of the furnace to its heating to the working temperature it took about two weeks.
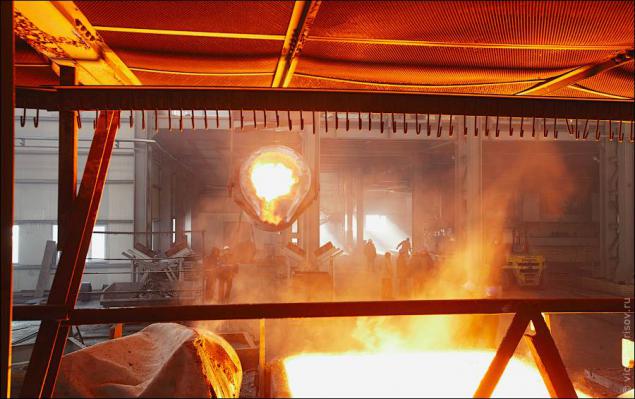
11. The plant as a raw material for the production of silicon metal used vein quartz from Ulytautskogo area.
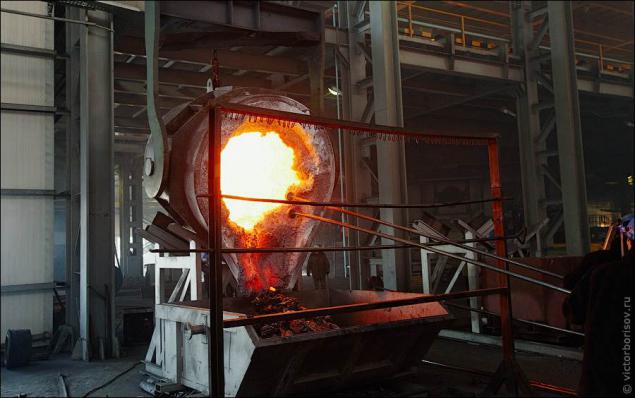
12. In the forms of silicon metal cools and solidifies.

13. Silicon metal is the basis for high-tech industry. Silicon - that solar cells and semiconductors for PCs, and much, much more.
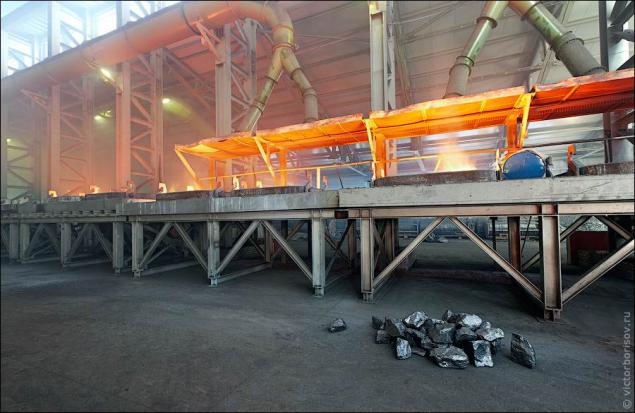
14. By the way, the production of silicon metal completely without waste. Above the stove there are air ducts, and all the dust goes into the gas cleaning, where trapped microparticles. This silicon dust is a useful product in another part of the production. For example, earlier in melted quartz Europe only to it and then add to grind the concrete, in solutions which have a very high restorative properties. The quartz crystal lattice is very strong. And the 900-th grade of concrete can be obtained only by means of silicon. And there are waterproof putty, impact-resistant floors, these products are used to strengthen the underground tunnels.
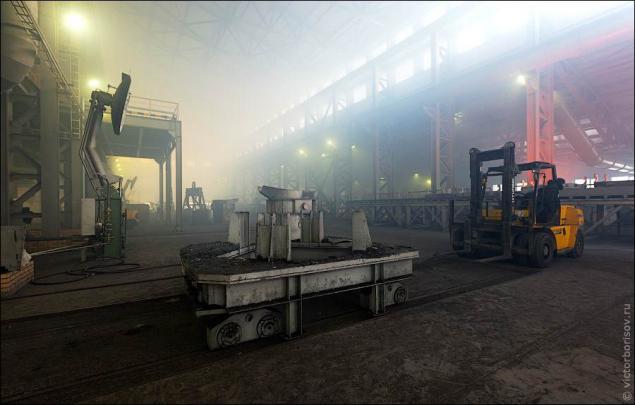
15. After ostavanie silicon crushed into small pieces hydraulic hammer.
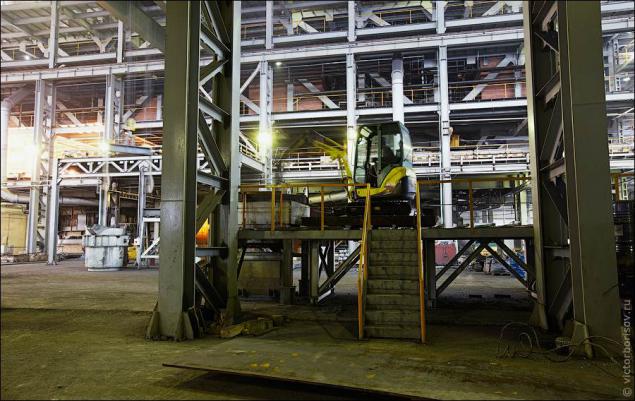
16. The finished product is packed in big bags - plastic bags for up 1,000 kilograms of metallurgical silicon and sent to customers.

17. What can be done with a commercial silicon? Technological chain in the production of silicon continues: metallurgical silicon - polysilicon - monocrystalline silicon - silicon wafers. For further purification of metallurgical silicon is distilled, turning to environmentally harmful chlorine compounds: dichlorosilane or trichlorosilane. After cleaning, the latter on a large distillation columns and polysilicon deposition processes is obtained, where the concentration of impurities is not more than ten-thousandth of a percent. Thereafter, it is melted into single crystal material, and single crystals are cut on the plate. The obtained 80% of monocrystalline silicon used in electronics.
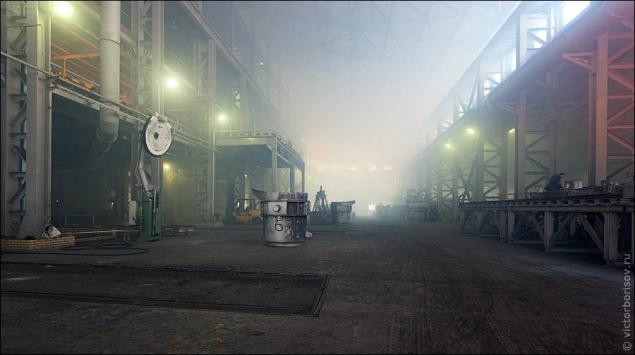
Source: