1525
Disposable motors
Active Steering, a control system for the blind zones and layout, on-board media with multiple functions. Until recently, it was the prerogative solely of representative models, but is now rapidly going "to the people", to the masses. General trends, progress, fierce competition ... But there are also constantly stricter environmental requirements. Plus struggle "overweight" and the need to meet the standards of passive safety. Advanced technology and money, money ... The development, introduction. Automakers have something to grab the head.
As a result, a modern car for the price should be different from its predecessor from the 90s, like a fighter of the fifth generation fighter of the fourth, that is 3-5 times. It is, of course, more expensive, but not at a pace. Somewhere changing generation, its cost is increased by 10%, and even only 5%.
Of course, the company has powerful leverage to maintain a "creeping inflation". For example, combining with each other at the division of responsibilities. Or transfer of the development of individual nodes / devices / systems, small firms without financial ambitions. Bedzhinzhiniring! In the end, the unification of small things. The worst thing is that this situation can expect the consumer is the engine or the gearbox on the "German" - "Americans" as those familiar to "Japanese." Or press buttons on your "premium" if the neighbor in "consumer goods". Agree, is not fatal. However, in order to save manufacturers employ its entire design and technological potential encroaching on the sacred - life and reliability of the engine.
Weight is everything
It is difficult to say who was the first to think about the global reduction of engine weight through the use of a cylinder block of aluminum rather than cast iron. Perhaps the designers dreamed about this ever since the invention of ICE. Still strong and almost three times cheaper iron harder winged metal corrosion is unstable, it has a much lower thermal conductivity, making such units required more extensive cooling system.
Engine with aluminum cylinder blocks have been used not only in sport. For example, our legendary diesel V-2, is installed on the tanks T-34 and KV, are made of aluminum alloy - silumin - and had a wet sleeve. However, by the middle of the war due to lack of "winged metal block steel cast iron
We only know that in the 30s of the last century engines made of aluminum with inserted in them wet cast iron liners, where between them and the body of the unit is the coolant, it has been used in some racing cars. By the middle of the last century, this design was the move to the conveyors (one of the best examples - the motor Moskvich-412). However, widespread iron (as the core material) is not replaced because it was technologically difficult and had a number of shortcomings - low stiffness block, increased load on the sleeve, a tendency to "blowing" pads with a little overheated.
Engine UZAM had enough innovative for its time structure - light unit and the wet liners. Someone still tuning the engine. But the producers of these for the most part abandoned - due to the low stiffness of the block and high loads on the sleeve
In the late 60's - early 70's back to the familiar pattern with dry liners placed in the body of the unit without coolant channels. Only naturally, instead of iron to aluminum block selected. They say that was a pioneer Honda. If this is not the case, willing to believe. Why is this not done earlier? Pressing on a hot cast-iron parts with an interference fit in a much less durable aluminum - technically very complex process. Besides these metals different coefficient of thermal expansion - in heating between the sleeve and the motor unit may occur gap. But the "blanks" engine gets hard. However, as with iron. But, of course, with an impressive saving in weight. Close to the technology of this century went on. Pressing liners replaced by injection block around them. They look as though fused in aluminum. And if the first method is extruded and allowed to change the liner, and some manufacturers offer repair their size, the latter in some cases this will not officially admit. One of the supporters of this design - the company Toyota, the first production test was performed in 1997. However, even before other blocks experimented with firm, generally devoid of sleeves.
Hard to say, when the blocks in which the thin-walled cast iron liners if fused in aluminum. But just that, at least until recently, such a structure used Nissan and Toyota. Officially, these units are not repairable. But after appropriate running as beautiful look in the interior
Sleeves? Why would they?
A tempting prospect - avoid the use of iron and sleeves, thus eliminating the pressing-or molds, also beating the difference between the temperature characteristics of the two materials and making the removal of heat from the cylinder much more intense. To put it in production, certainly cheaper. Maybe even the resource? We only need to somehow harden the cylinder bore and the steel rings so bare aluminum ...
Again, it is difficult to say when and who put the first experiments and generally thought of it as we say now, "nano-coatings." Supposedly back in the 60's leading manufacturers of motor sports, like Cosworth, experimented with different surface treatment of cylinders. But serial debut caseless engine known. It took place in 1971 on the Chevrolet Vega. Unit 2 of its 3-liter "four" was made from an aluminum alloy with 17% silicon. Intensive cooling of the cylinder bore allow this material to crystallize in this area, and in the same etching acid washed away molecules of aluminum, making the most solid wall. According to her, both in cast iron, you have to work the piston rings. It was an achievement! Which, alas, dashed banal problems. Because of failures in the cooling system of the engine is easy to overheat. Guaranteed to "kill" it and oil to replace that in the United States have always been treated very freely. Yes, for sure, and themselves liquid at the time could not provide high-quality lubricant.
In many ways, its not a very good reputation Vega obliged motor. Only in the first two years it was withdrawn almost half a million copies. However, it was not directly related to the engine block - enough other problems. And then he began to "die" and CPG engine. In 1976, the upgraded machine - the system cooling and the piston ring - but the attitude of the car is not changed
In general, the first serial "disposable" drive does not become hostage to technology excludes its recovery - normal maintenance sins characteristic of any machine. So focused on the mirror cylinder crystallizing silicon are not deducted from the accounts. By the end of the 80 it took to adopt the European manufacturers. Later, a method perfected. There were aluminum liner, which was saturated with silicon alone, the share of the latter increased to 27%.
Development of technologies for the manufacture of aluminum blocks with rich silicon mirrors of cylinders engaged in the two German companies - Mahle and Kolbenschmidt. In the case where it is about 17% silicon technology is called, respectively, Silumal and Alusil. But Kolbenschmidt also provides a method Locasil, wherein the sleeve are performed separately, and the proportion of silica is increased by 10%. By the way, in both cases on the cylinder walls are afraid of hard mechanical contacts, from which there are deep teaser. After all, under a thin layer of silicon rich - soft aluminum
In the early 90's of the sport on conveyors came another technology of hardening the bore - the composition of the electroplated nickel and silicon carbide (better known under the name Nikasil). This, in particular, "addicted» BMW, Audi, Jaguar. And the Bavarians were not limited only to the friction surfaces - about ten years ago they had a "bimetallic" motor. His sleeves are made of aluminum, the rest - a magnesium alloy, which is even easier. In short, the experiments with metals and coatings continue. Among them, for example, plasma spraying compositions based on iron or laser alloying the same silicon. In the long term - drawing on the wall of the cylinder of titanium nitride.
The coatings on the mirrors are different cylinders. For example, Honda has long and unsuccessfully using plasma deposition of iron-containing compounds. The block is made with an open cooling jacket - not to be confused with wet liners. The latter are generally not
Repair is always possible
All of these "nano" have allowed not only to win the title, eliminating thermal combination of different metals. Presenting their manufacturers have stated that they will make the motors of the resource. In theory, that's right. Silicon and nickel are harder and thus wear resistant cast iron. In practice, the operation of all-aluminum engine was not so rosy. The first disappointment came in the mid 90s. Bavarian "six" and "eight" in volume 2, 0 to 4, 0 l (Series M52 and M60) with nickel-coated silicon sold in the United States, Britain, Eastern Europe and especially in Russia falls well before 100 thousand. km surprised owners wear unit. As it turned out, the sulfur, which were rich in oil in these countries react with the coating and destroys it. This officially engines were considered non-repairable. After such a scandal in the BMW from the "Nikas" refused. But limited and it seems reformulated it is still used in sports such as motorcycle Suzuki.
Covering Nikasil (at Mahle) and Galnical (at Kolbenschmidt) of nickel and silicon carbide is probably the most solid in the existing. However, the affected chemical - sulfur contained in the fuel. Now only used in sports, such as motorcycle "two-stroke»
What other expertise? You can talk about the run in 300-350 thousand. Km, regardless of whether one is talking about hardening silicon cylinder bores or plasma spraying of some compositions. And, alas, resource dependency on the working volume is not so revealing as before. For example, gasoline more than 4-liter V8 from the VAG and Porsche, is, to wear 300 thousand. Recall that the other is completely cast iron or metal liners from this polutoralitrovye motors went longer. And how to forget the exploits of some Japanese resource units, living without changing the piston rings 700 and even 800 thousand. Km? And three hundred for modern engines have not "limit". Some installations, such as, FSI and TFSI from Audi, are willing to give up to 200 thousand. Km, and sometimes even immediately after a hundred. And it is often subject to the oil change intervals (that we need to reduce by half against the factory) and the tolerances of the manufacturer it is (which is especially necessary in respect of "the Germans"). The more "disposable" block can impose rigid mechanical action, for example, breaking piston rings or something more serious. Price of the issue varies greatly. Blocks some sort of "fours" can cost in the range of 75-150 thousand. Rub. But something V-shaped ability to assess and 500 thousand. Expensive, and sometimes disproportionate cost of a used car.
Until recently, one could hardly assume that carmakers to encroach on the most sacred - a resource of cylinder-piston group (CPG). And what about the second or third owner with a good run? The latter can range only 120-150 thousand. Km
There is an alternative! Do not say exactly when, but definitely more than a decade ago, some Russian services have mastered the technology gilzovaniya aluminum blocks. Of course, it's more complex operation than if it was a cast-iron details. However, it is the only option when buying motor beushnyh risky or financially disadvantageous. On the reconstruction of the engines have aluminum liners and pistons. You can make them yourself - billet offered. In the end, reality always choose cast iron liners from some of the "left" of the unit and squander it under the new pistons of the engine repaired. The easiest and most popular way! And put one metal to another, our mechanics are not afraid. The cost of the operation, of course, will vary depending on the region and the engine. For example, in large cities gilzovka another "eight" will cost 40 thousand. Rub., And "four" in the province can "revive" and for 5000. Of course, without sleeves and other parts CPG. And still does not compare with the prices of new units. Why, spraying special formulations have reduced even bed crankshafts, crank liner damaged. According to the master, rarely get a block that can not be returned to operation.
Zagilzovat can be any unit, even such complex as folksvagenovsky W12. Anyway, as long as it allows the thickness of the cylinder walls
Canned really worn blocks and aluminum parts, but it is desirable to cool in liquid nitrogen, and the defect rate can be very high. Mechanics usually cost cast iron liners, picking them out of the offer, which is available on the open market
Timing at risk
Behind the scenes, along with modern engines came into our lives, and good oil appetite. Understandable! For maximum ease pistons made compact T-shaped. Because of this thin rings on them, no longer able to remove excess grease quality. As a result, if more recent one, 5-2 liters of oil ugorevshego 10 thousand. Km or talked about driving at high speed, or a problem with the caps / rings, but now it is in order. Particularly different number of engines VAG and BMW, whose consumption is capable of reaching up to half a liter of a liter per thousand. However, some engines are already deprived Bavarian dipstick. The level sensor monitors on whose testimony can not always rely on ... We look forward to the continuation of other companies?
Pistons are getting smaller and smaller. Shrinking them and rings, which are no longer able to cope with their quality objectives
All this is logical, as amended on marketing, the results of the evolution of ICE. But how to explain what happens to the chain-driven camshaft (RM)? The circuit certainly returned to the engines to the mechanism of timing was less of a problem, and the owners have less to spend. Manufacturers and say - it is designed for a lifetime. Too bold score! But in fairness, we note - some companies (BMW, Nissan, Toyota) circuit is really "walk" under 200 or even 250 thousand. Km. More frequently, 100-120 thousand are one feature, which operation of the car becomes unpleasant or impossible - because of the stretching circuit "float away" phase. Engine troit or simply not start.
Leaf Chain Timing Resource single or double-row. At least we can talk about them as "eternal" item, if for eternity to take a run at 250 thousand. Km
There are also quite egregious. So, known folksvagenovsky VR6 (Touareg with them the most popular) chain may take up to 80 thousand. Km. And after or skip over the teeth, or even tear. Since it is typical for modern engines result - "brotherly" meeting with piston valves. Moreover, the replacement of the chain is complicated by the fact that the timing is located on the rear side of the engine, for which the unit had to be removed. The same situation is in all respects with the Bavarian turbodiesel "quartet" volume of two liters. Source chain may be about 80 thousand. Km tensile it jumps or breaks, the mechanism is "behind" the motor. A similar result in, again, a popular gasoline mersedesovskoy installation of 1, 8 liters ready to come before - after 60 thousand. Km. A hair's breadth as in the Korean diesel engines, which were installed on the Sorento and Santa Fe (2, 2 and 2, 5 l.). Against this background, FSI / TFSI from VAG look almost perfectly - a stretching and hopping circuit must be prepared after 100 thousand. Toyota and completely flawless. On its units circuit if early sometimes stretched, at least it remains on the teeth. But even without the restoration of the "head" is produced much. On some engines, and its replacement will cost 30, and 40, and even 100 thousand. Rub. Do not strap - need to change with the gear, and they are now "ennobled" phase shifters.
As for the timing of the general trends, they are generally dismal. It is no longer exclusive gear holding a crankshaft only by the bolt tightening torque - without the usual key. Saving its groove? Occurs, albeit rarely, the opposite construction, where the timing sprocket formed with the crankshaft integrally. Replacement of a chain similar to "kapitalki"? Enter not into use cast iron - hollow camshafts with press-fit on the cam slots. When will a little loose and jump?
As a result, a modern car for the price should be different from its predecessor from the 90s, like a fighter of the fifth generation fighter of the fourth, that is 3-5 times. It is, of course, more expensive, but not at a pace. Somewhere changing generation, its cost is increased by 10%, and even only 5%.
Of course, the company has powerful leverage to maintain a "creeping inflation". For example, combining with each other at the division of responsibilities. Or transfer of the development of individual nodes / devices / systems, small firms without financial ambitions. Bedzhinzhiniring! In the end, the unification of small things. The worst thing is that this situation can expect the consumer is the engine or the gearbox on the "German" - "Americans" as those familiar to "Japanese." Or press buttons on your "premium" if the neighbor in "consumer goods". Agree, is not fatal. However, in order to save manufacturers employ its entire design and technological potential encroaching on the sacred - life and reliability of the engine.
Weight is everything
It is difficult to say who was the first to think about the global reduction of engine weight through the use of a cylinder block of aluminum rather than cast iron. Perhaps the designers dreamed about this ever since the invention of ICE. Still strong and almost three times cheaper iron harder winged metal corrosion is unstable, it has a much lower thermal conductivity, making such units required more extensive cooling system.
Engine with aluminum cylinder blocks have been used not only in sport. For example, our legendary diesel V-2, is installed on the tanks T-34 and KV, are made of aluminum alloy - silumin - and had a wet sleeve. However, by the middle of the war due to lack of "winged metal block steel cast iron
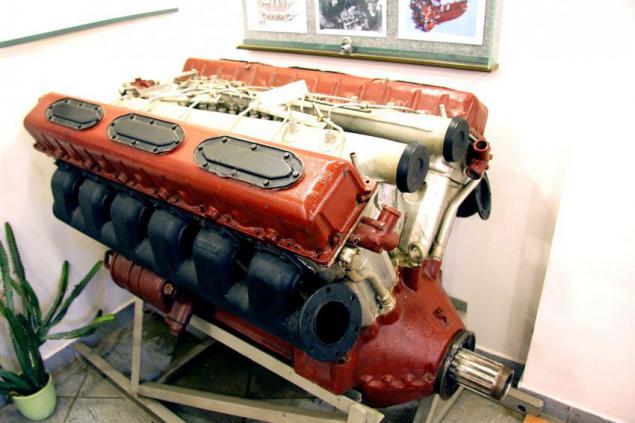
We only know that in the 30s of the last century engines made of aluminum with inserted in them wet cast iron liners, where between them and the body of the unit is the coolant, it has been used in some racing cars. By the middle of the last century, this design was the move to the conveyors (one of the best examples - the motor Moskvich-412). However, widespread iron (as the core material) is not replaced because it was technologically difficult and had a number of shortcomings - low stiffness block, increased load on the sleeve, a tendency to "blowing" pads with a little overheated.
Engine UZAM had enough innovative for its time structure - light unit and the wet liners. Someone still tuning the engine. But the producers of these for the most part abandoned - due to the low stiffness of the block and high loads on the sleeve
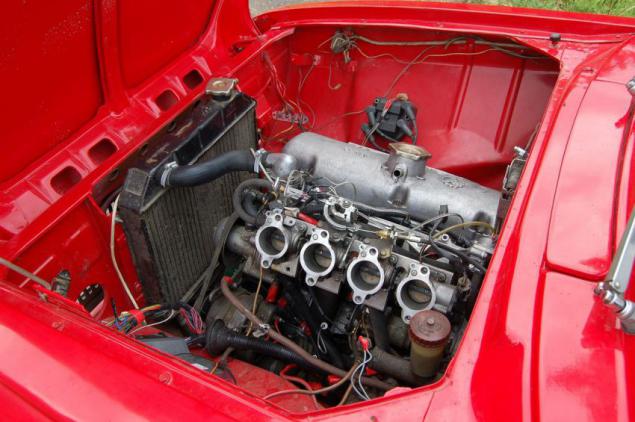
In the late 60's - early 70's back to the familiar pattern with dry liners placed in the body of the unit without coolant channels. Only naturally, instead of iron to aluminum block selected. They say that was a pioneer Honda. If this is not the case, willing to believe. Why is this not done earlier? Pressing on a hot cast-iron parts with an interference fit in a much less durable aluminum - technically very complex process. Besides these metals different coefficient of thermal expansion - in heating between the sleeve and the motor unit may occur gap. But the "blanks" engine gets hard. However, as with iron. But, of course, with an impressive saving in weight. Close to the technology of this century went on. Pressing liners replaced by injection block around them. They look as though fused in aluminum. And if the first method is extruded and allowed to change the liner, and some manufacturers offer repair their size, the latter in some cases this will not officially admit. One of the supporters of this design - the company Toyota, the first production test was performed in 1997. However, even before other blocks experimented with firm, generally devoid of sleeves.
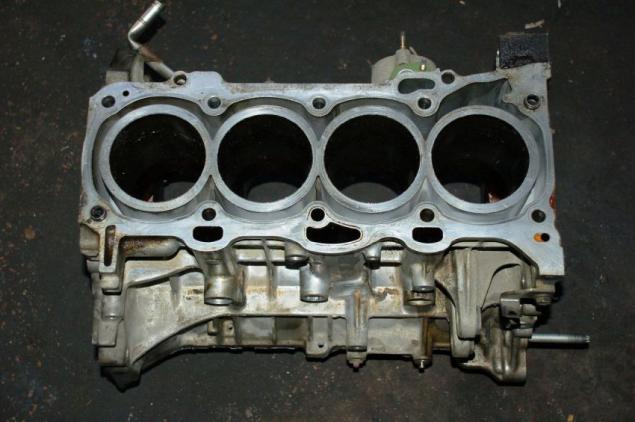
Hard to say, when the blocks in which the thin-walled cast iron liners if fused in aluminum. But just that, at least until recently, such a structure used Nissan and Toyota. Officially, these units are not repairable. But after appropriate running as beautiful look in the interior
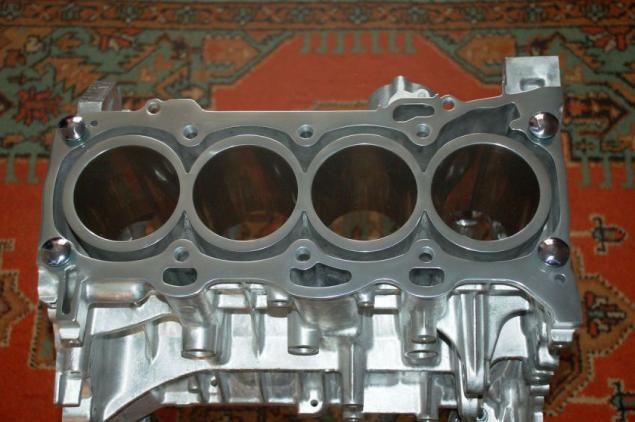
Sleeves? Why would they?
A tempting prospect - avoid the use of iron and sleeves, thus eliminating the pressing-or molds, also beating the difference between the temperature characteristics of the two materials and making the removal of heat from the cylinder much more intense. To put it in production, certainly cheaper. Maybe even the resource? We only need to somehow harden the cylinder bore and the steel rings so bare aluminum ...
Again, it is difficult to say when and who put the first experiments and generally thought of it as we say now, "nano-coatings." Supposedly back in the 60's leading manufacturers of motor sports, like Cosworth, experimented with different surface treatment of cylinders. But serial debut caseless engine known. It took place in 1971 on the Chevrolet Vega. Unit 2 of its 3-liter "four" was made from an aluminum alloy with 17% silicon. Intensive cooling of the cylinder bore allow this material to crystallize in this area, and in the same etching acid washed away molecules of aluminum, making the most solid wall. According to her, both in cast iron, you have to work the piston rings. It was an achievement! Which, alas, dashed banal problems. Because of failures in the cooling system of the engine is easy to overheat. Guaranteed to "kill" it and oil to replace that in the United States have always been treated very freely. Yes, for sure, and themselves liquid at the time could not provide high-quality lubricant.
In many ways, its not a very good reputation Vega obliged motor. Only in the first two years it was withdrawn almost half a million copies. However, it was not directly related to the engine block - enough other problems. And then he began to "die" and CPG engine. In 1976, the upgraded machine - the system cooling and the piston ring - but the attitude of the car is not changed
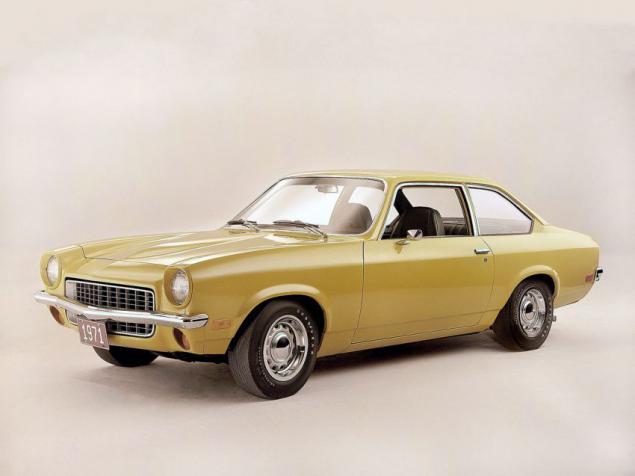
In general, the first serial "disposable" drive does not become hostage to technology excludes its recovery - normal maintenance sins characteristic of any machine. So focused on the mirror cylinder crystallizing silicon are not deducted from the accounts. By the end of the 80 it took to adopt the European manufacturers. Later, a method perfected. There were aluminum liner, which was saturated with silicon alone, the share of the latter increased to 27%.
Development of technologies for the manufacture of aluminum blocks with rich silicon mirrors of cylinders engaged in the two German companies - Mahle and Kolbenschmidt. In the case where it is about 17% silicon technology is called, respectively, Silumal and Alusil. But Kolbenschmidt also provides a method Locasil, wherein the sleeve are performed separately, and the proportion of silica is increased by 10%. By the way, in both cases on the cylinder walls are afraid of hard mechanical contacts, from which there are deep teaser. After all, under a thin layer of silicon rich - soft aluminum
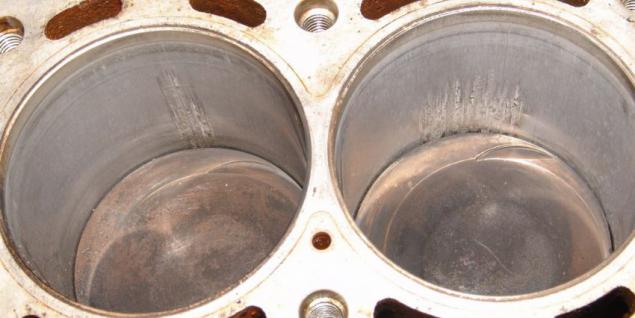
In the early 90's of the sport on conveyors came another technology of hardening the bore - the composition of the electroplated nickel and silicon carbide (better known under the name Nikasil). This, in particular, "addicted» BMW, Audi, Jaguar. And the Bavarians were not limited only to the friction surfaces - about ten years ago they had a "bimetallic" motor. His sleeves are made of aluminum, the rest - a magnesium alloy, which is even easier. In short, the experiments with metals and coatings continue. Among them, for example, plasma spraying compositions based on iron or laser alloying the same silicon. In the long term - drawing on the wall of the cylinder of titanium nitride.
The coatings on the mirrors are different cylinders. For example, Honda has long and unsuccessfully using plasma deposition of iron-containing compounds. The block is made with an open cooling jacket - not to be confused with wet liners. The latter are generally not
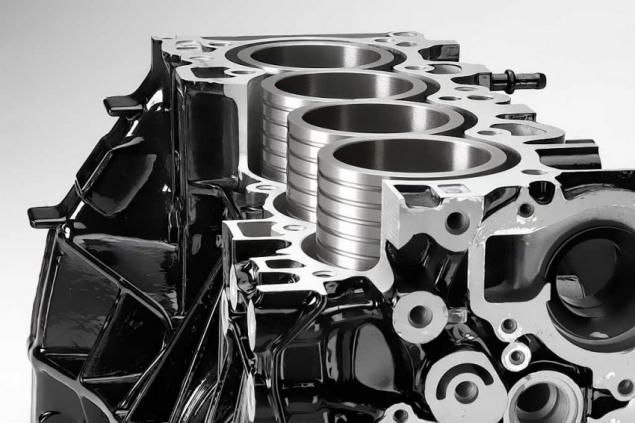
Repair is always possible
All of these "nano" have allowed not only to win the title, eliminating thermal combination of different metals. Presenting their manufacturers have stated that they will make the motors of the resource. In theory, that's right. Silicon and nickel are harder and thus wear resistant cast iron. In practice, the operation of all-aluminum engine was not so rosy. The first disappointment came in the mid 90s. Bavarian "six" and "eight" in volume 2, 0 to 4, 0 l (Series M52 and M60) with nickel-coated silicon sold in the United States, Britain, Eastern Europe and especially in Russia falls well before 100 thousand. km surprised owners wear unit. As it turned out, the sulfur, which were rich in oil in these countries react with the coating and destroys it. This officially engines were considered non-repairable. After such a scandal in the BMW from the "Nikas" refused. But limited and it seems reformulated it is still used in sports such as motorcycle Suzuki.
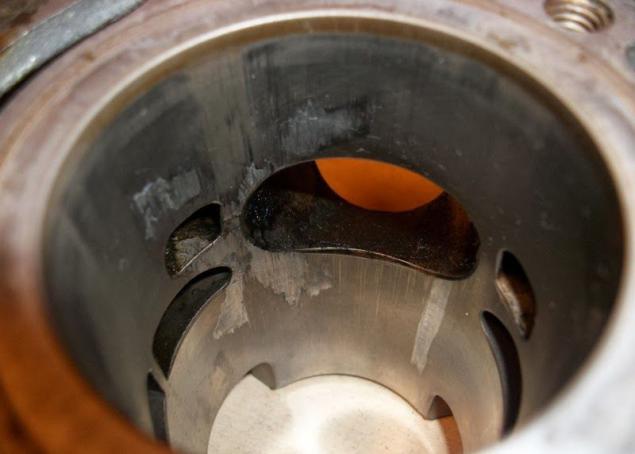
Covering Nikasil (at Mahle) and Galnical (at Kolbenschmidt) of nickel and silicon carbide is probably the most solid in the existing. However, the affected chemical - sulfur contained in the fuel. Now only used in sports, such as motorcycle "two-stroke»
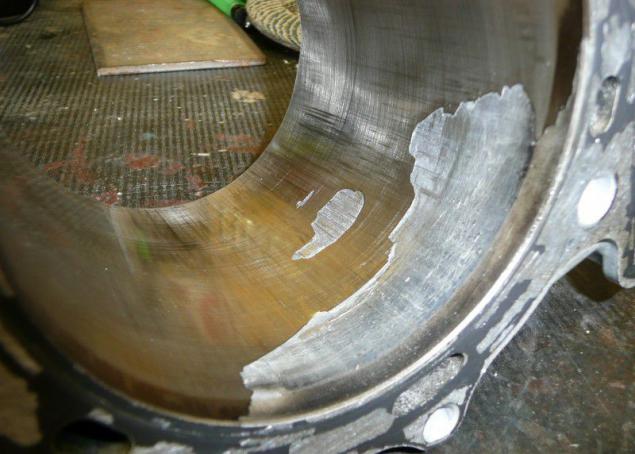
What other expertise? You can talk about the run in 300-350 thousand. Km, regardless of whether one is talking about hardening silicon cylinder bores or plasma spraying of some compositions. And, alas, resource dependency on the working volume is not so revealing as before. For example, gasoline more than 4-liter V8 from the VAG and Porsche, is, to wear 300 thousand. Recall that the other is completely cast iron or metal liners from this polutoralitrovye motors went longer. And how to forget the exploits of some Japanese resource units, living without changing the piston rings 700 and even 800 thousand. Km? And three hundred for modern engines have not "limit". Some installations, such as, FSI and TFSI from Audi, are willing to give up to 200 thousand. Km, and sometimes even immediately after a hundred. And it is often subject to the oil change intervals (that we need to reduce by half against the factory) and the tolerances of the manufacturer it is (which is especially necessary in respect of "the Germans"). The more "disposable" block can impose rigid mechanical action, for example, breaking piston rings or something more serious. Price of the issue varies greatly. Blocks some sort of "fours" can cost in the range of 75-150 thousand. Rub. But something V-shaped ability to assess and 500 thousand. Expensive, and sometimes disproportionate cost of a used car.
Until recently, one could hardly assume that carmakers to encroach on the most sacred - a resource of cylinder-piston group (CPG). And what about the second or third owner with a good run? The latter can range only 120-150 thousand. Km
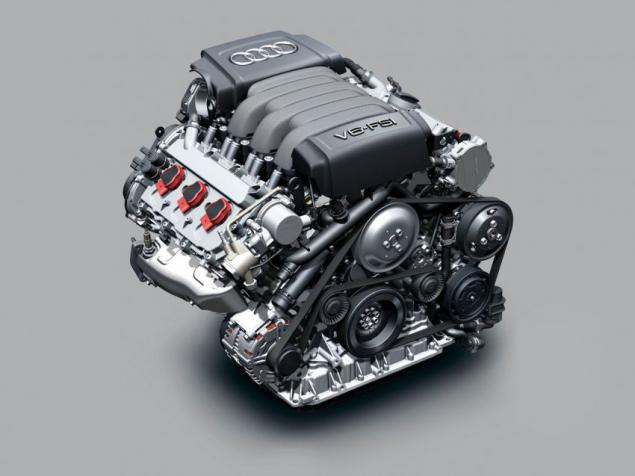
There is an alternative! Do not say exactly when, but definitely more than a decade ago, some Russian services have mastered the technology gilzovaniya aluminum blocks. Of course, it's more complex operation than if it was a cast-iron details. However, it is the only option when buying motor beushnyh risky or financially disadvantageous. On the reconstruction of the engines have aluminum liners and pistons. You can make them yourself - billet offered. In the end, reality always choose cast iron liners from some of the "left" of the unit and squander it under the new pistons of the engine repaired. The easiest and most popular way! And put one metal to another, our mechanics are not afraid. The cost of the operation, of course, will vary depending on the region and the engine. For example, in large cities gilzovka another "eight" will cost 40 thousand. Rub., And "four" in the province can "revive" and for 5000. Of course, without sleeves and other parts CPG. And still does not compare with the prices of new units. Why, spraying special formulations have reduced even bed crankshafts, crank liner damaged. According to the master, rarely get a block that can not be returned to operation.
Zagilzovat can be any unit, even such complex as folksvagenovsky W12. Anyway, as long as it allows the thickness of the cylinder walls
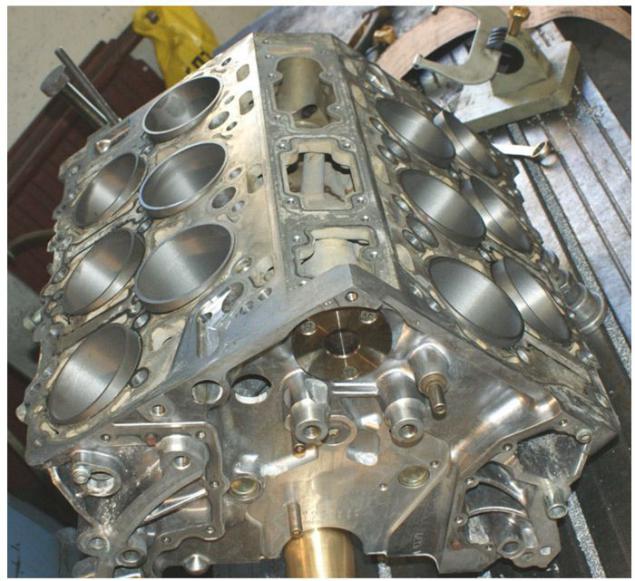
Canned really worn blocks and aluminum parts, but it is desirable to cool in liquid nitrogen, and the defect rate can be very high. Mechanics usually cost cast iron liners, picking them out of the offer, which is available on the open market
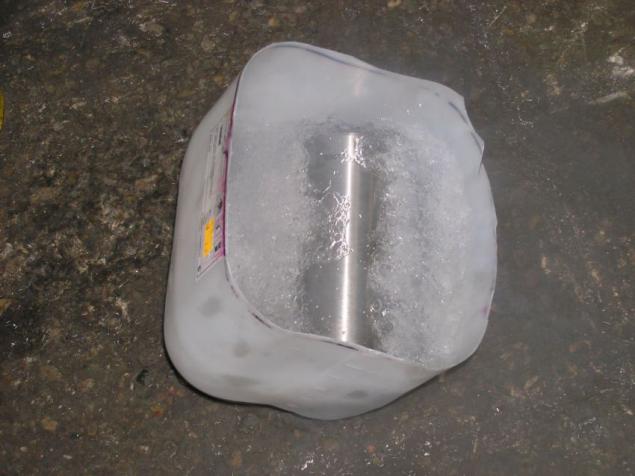
Timing at risk
Behind the scenes, along with modern engines came into our lives, and good oil appetite. Understandable! For maximum ease pistons made compact T-shaped. Because of this thin rings on them, no longer able to remove excess grease quality. As a result, if more recent one, 5-2 liters of oil ugorevshego 10 thousand. Km or talked about driving at high speed, or a problem with the caps / rings, but now it is in order. Particularly different number of engines VAG and BMW, whose consumption is capable of reaching up to half a liter of a liter per thousand. However, some engines are already deprived Bavarian dipstick. The level sensor monitors on whose testimony can not always rely on ... We look forward to the continuation of other companies?
Pistons are getting smaller and smaller. Shrinking them and rings, which are no longer able to cope with their quality objectives
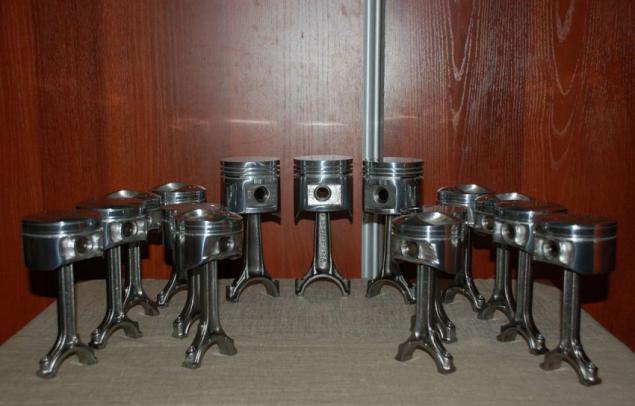
All this is logical, as amended on marketing, the results of the evolution of ICE. But how to explain what happens to the chain-driven camshaft (RM)? The circuit certainly returned to the engines to the mechanism of timing was less of a problem, and the owners have less to spend. Manufacturers and say - it is designed for a lifetime. Too bold score! But in fairness, we note - some companies (BMW, Nissan, Toyota) circuit is really "walk" under 200 or even 250 thousand. Km. More frequently, 100-120 thousand are one feature, which operation of the car becomes unpleasant or impossible - because of the stretching circuit "float away" phase. Engine troit or simply not start.
Leaf Chain Timing Resource single or double-row. At least we can talk about them as "eternal" item, if for eternity to take a run at 250 thousand. Km
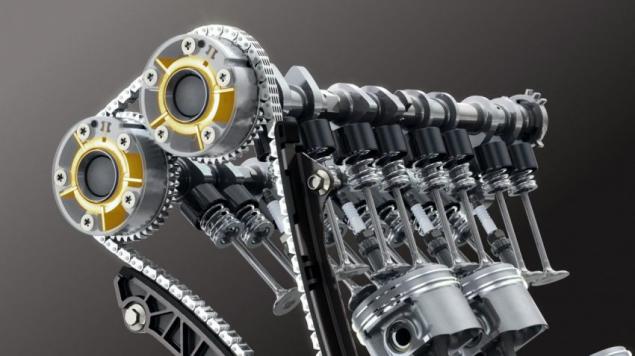
There are also quite egregious. So, known folksvagenovsky VR6 (Touareg with them the most popular) chain may take up to 80 thousand. Km. And after or skip over the teeth, or even tear. Since it is typical for modern engines result - "brotherly" meeting with piston valves. Moreover, the replacement of the chain is complicated by the fact that the timing is located on the rear side of the engine, for which the unit had to be removed. The same situation is in all respects with the Bavarian turbodiesel "quartet" volume of two liters. Source chain may be about 80 thousand. Km tensile it jumps or breaks, the mechanism is "behind" the motor. A similar result in, again, a popular gasoline mersedesovskoy installation of 1, 8 liters ready to come before - after 60 thousand. Km. A hair's breadth as in the Korean diesel engines, which were installed on the Sorento and Santa Fe (2, 2 and 2, 5 l.). Against this background, FSI / TFSI from VAG look almost perfectly - a stretching and hopping circuit must be prepared after 100 thousand. Toyota and completely flawless. On its units circuit if early sometimes stretched, at least it remains on the teeth. But even without the restoration of the "head" is produced much. On some engines, and its replacement will cost 30, and 40, and even 100 thousand. Rub. Do not strap - need to change with the gear, and they are now "ennobled" phase shifters.
As for the timing of the general trends, they are generally dismal. It is no longer exclusive gear holding a crankshaft only by the bolt tightening torque - without the usual key. Saving its groove? Occurs, albeit rarely, the opposite construction, where the timing sprocket formed with the crankshaft integrally. Replacement of a chain similar to "kapitalki"? Enter not into use cast iron - hollow camshafts with press-fit on the cam slots. When will a little loose and jump?