2480
Direct injection
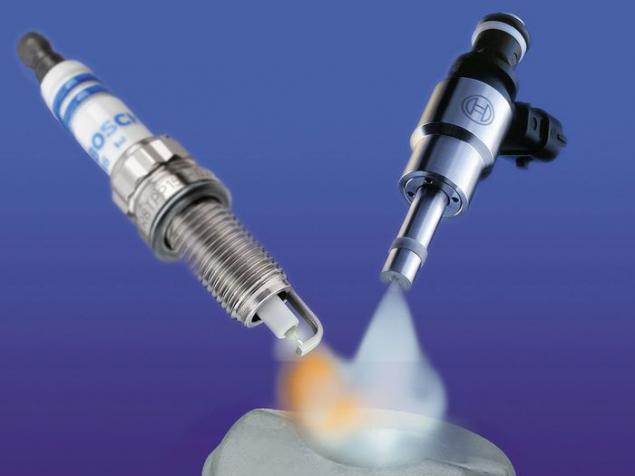
In the cloud and on the slopes
Revived less than 20 years ago, straight, or direct, injection has more than a century. After all engines running on heavy fuel, constructed according to the same principle - the injectors they are located inside the combustion chambers. Their development, as we know, different designers involved in the second half of the XIX century. A patent was obtained by Rudolf Diesel in 1892. In 1925 the world saw another construction, start up on gasoline, which is ignited by the spark plug. But then the engine was able to work on many of flammable liquids - diesel, kerosene, oil. These substances are already lit compression.
Truly gasoline engine with direct injection appeared only in 1937. It was a well-known aviation Daimler-Benz DB 601, for which Bosch has developed a mechanical fuel system. It turned out for the aircraft direct injection - the best option. For compensation in the form of slightly increased weight and demands fuel quality 12-cylinder V- «obraznik" acquired more power and stability in all modes, including the flight conditions, including "aerobatics". DB 601 was produced under license in Italy and Japan, in Germany, establishing many of the planes, the most famous of which - Messerschmitt BF 109.
In 1940, by way of Daimler went to BMW. Direct injection the Bavarians had a 14-cylinder two-row "star", sets including the popular among the Luftwaffe Focke-Wulf Fw 190. Not far behind the Germans, Soviet designers. Similar in design BMW engine AL-82FN direct injection appeared in 1942 and helped win the fighter La-5FN air superiority. And then came the era of jet engines ...
DB 601 (left), BMW 801 (center), and AL-82FN (right) appeared around the same time, but different design. Motor Daimler-Benz was customary in the automotive sense V12. BMW and Soviet engine had a radial arrangement of cylinders in two rows and staggered. Were different volume and power. Almost 34-liter DB developed the 1100-1200 hp, BMW - 42 liters and more than a thousand "horses". And the same engine capacity Russian 'star' forced to 1700-1900 hp
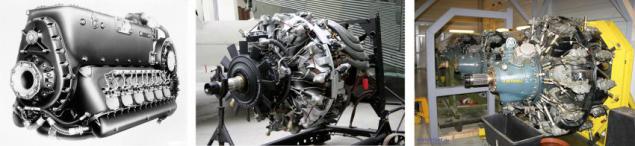
By car direct injection "returned" in 1951. The German company Goliath, owned concern Borgward, relying on fuel economy against the backdrop of post-war devastation, decided to release a small two-stroke two-cylinder coupe with a motor with fuel equipment Bosch. Model 700 Sport, however, did not differ fuel appetite and at the same time, demanded unusual for carburettor cars service.
Goliath 700 Sport was the first car, an example of direct fuel injection. We can not say that the machine failed. Just a poor German people were not ready for operation even economical, but difficult to maintain motor
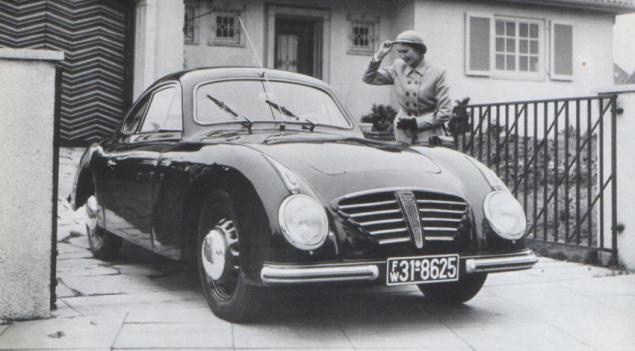
Engineers and marketers Mercedes-Benz such problems do not seem worried. 300 SL sample of 1954 known as the "gull wing", having the same "boshevsky" three-liter injection on row "Six", was the vehicle of a different order, not the budget. What to talk about his sporting versions of speakers from 1951. And the more of those "Silver Arrow", which appeared later to participate in the Formula 1 and had already V8.
"Road» Mercedes-Benz 300 SL and its three-liter row "Six", the power of which with the help of direct injection has been raised from 115 to 240 hp Good model appeared on the "long" races, until a 300 SLR - already with V8, also equipped with a direct injection
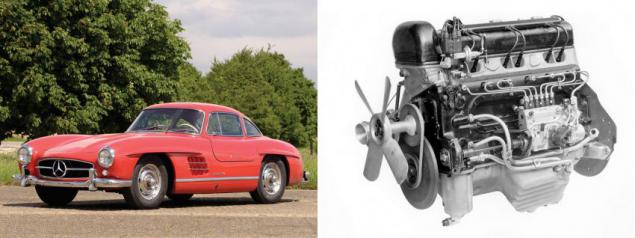
Prechamber
Racing - there is fuel and the other, and many thousands of the resource is not needed. However, to run direct injection into series production of the company is not in a hurry. Although work on obtaining optimal carburetion certainly were. For example, in the 70's with an eye on diesels some Japanese firms have experimented with pre- combustion chamber jet ignition. Its essence was to ensure that in addition to the main above the piston existed pre-chamber. Was fed a rich mixture in a conventional camera - poor. Ignition occurs in the settling chamber via the spark plug. And already from it sees torch burned the bulk of the fuel. Incidentally, the first experience with a similar scheme were put in the USSR. In the mid-50 small parties was released "Six" GAZ-51F. She was stronger than normal unit 10 hp and slightly more economical. That, apparently, did not offset the complexity of the production of her head. The situation with the Japanese motor was different. They get cost-effective, but with a margin lying down in the then rules on emissions of CO, given the lethal concentration of nitric oxide. Recall that then still lacking quality emissions system.
For a while, since 1982 cylinder head with the prechamber and extra valves still produced in series. They are equipped with the modified engine ZMZ-402, which is mounted on the GAZ-3102
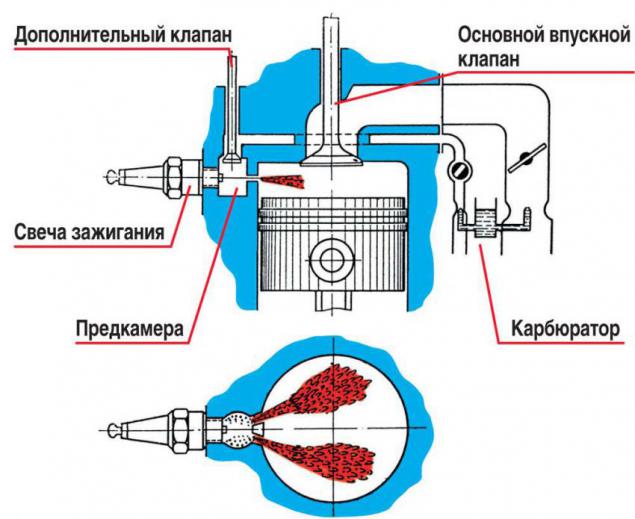
Prechamber jet ignition postponed - probably until better times. About direct injection, similar, and do not forget. Developing technologies of metal processing and electronics control the engine. As a result, Mitsubishi, first in 1996, followed by Toyota in 1997, presented their GDI and D4.
By layers
Why, they ask, do we need a direct fuel injection? From aircraft engines, or, say, Mercedes engines 50's all clear. There injection through better compared to spray the carburetor and obtain a homogeneous fuel mixture itself gave power increase. But if we now compare identical units with distributed and direct injection, no difference in horsepower is not revealed. Somewhere on the characteristics of the installation with direct injection look even worse. So what's the point? In an effort to follow the general trends of producers - to increase efficiency while reducing fuel consumption and emissions. All this has previously been achieved by optimizing the feed mixture and combustion processes. Now the fuel injection has reached a new stage in the evolution.
What is needed for this "optimization"? At first glance, a little bit. High pressure fuel pump, injectors arranged in the combustion chamber and able to provide finer spray. And a special form of the bottom of the piston, which "tightens up" the mixture, to determine its best mixing and directing to the spark plug. But this is only "physical" tip direct injection. Beneath it - "intelligent" electronic control, allows for various options of injection.
For example, most of the credit and the essence of direct injection - work in unloaded mode on ultra-lean mixture with a ratio of air and gasoline about 40: 1. This just does not break out the candle. It has its own trick - a small amount of fuel supplied to the combustion chamber at the end of the compression stroke. Twisting using moldings piston gasoline concentrated in candles, where it turns relatively rich mixture, and throughout the rest of the combustion chamber - the poor. The first flash of sparks, the second is from her. This so-called stratified charge.
Speaking of nodes located in a region of the combustion chamber, the direct injection does not seem complicated. Well, inside the nozzle, well, at the bottom of the piston intricate shapes. Nevertheless, a new approach to carburetion made globally to revise and mechanical parts, and the engine management system
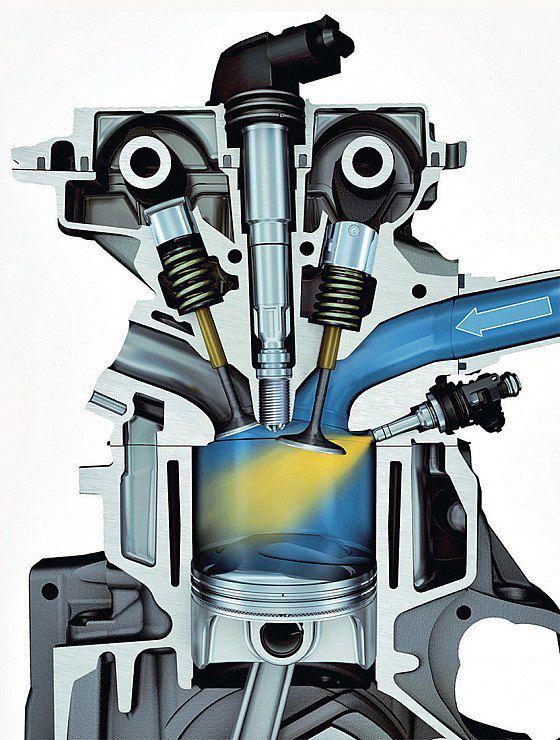
With smooth acceleration and uniform motion with direct injection engines run on conventional mixture with a ratio of 14, 7: 1. But the transition from superpoor mixture on the rich, that is, a sharp acceleration, also demanded a creative engineering approach. In order to eliminate detonation or uncontrolled inflammation in the early intake stroke injected a small amount of gasoline, cooling the combustion chamber. The second feed is performed at the end of the compression stroke. Thus engine "knocking his fingers," moved to a rich fuel mixture.
Experiments
It would seem that he is the perfect engine for all modes of traffic. Economical in traffic and measured driving, and able to "shoot" when necessary. But at what price! In the early 2000s, all the charm of the new technologies first to appreciate the people of the Far East and Siberia. Mitsubishi Motors with GDI (gasoline direct injection), which immediately nicknamed "Jedi", "accustomed" to the Japanese gasoline literally rebelling against our "gasoline." We will not touch the exhaust gas cleaning system. Although the same EGR, especially useful in the case of direct injection - to reduce emissions of nitrogen oxides - is itself a source of problems. The catalyst is designed for cleaning again from NOx, could "sentence" only refill the fuel surrogate. However, not once, not with a dirt tank of petrol disabling and submersible pump, the fuel being supplied to the main pump. He "overtax" trying to overcome traffic jams in the lines too small cross section. It happens that the pressure sensor duril, again forcing the submersible pump to operate at full.
Toyotovskih system D4, in particular, that which was equipped with the "eternal» 3S, tossed another surprise. Its high pressure pump plunger type has two specific features. With considerable deterioration of gasoline surpluses not fully flowed through the channel of "the return", falling straight into the crankcase and diluting the motor oil. Owner continues to operate the car at a loss of power, in fact, not only had to change the fuel pump, but also to restore the power of the engine group. But to prevent the "kapitalku" in another case could only check the oil level. One of the sealing gum in the pump had a small lifetime, and after a while ... yes, again gasoline in oil and two or three level on the dipstick.
Toyota quickly fix any problems with the pump, which met at 3S-FSE. Series motors AZ frightened by the fuel pump is much smaller and cars with it, such as the minivan Gaia, popular. True, and usually had some kind of "distributively vpryskovym" alternative
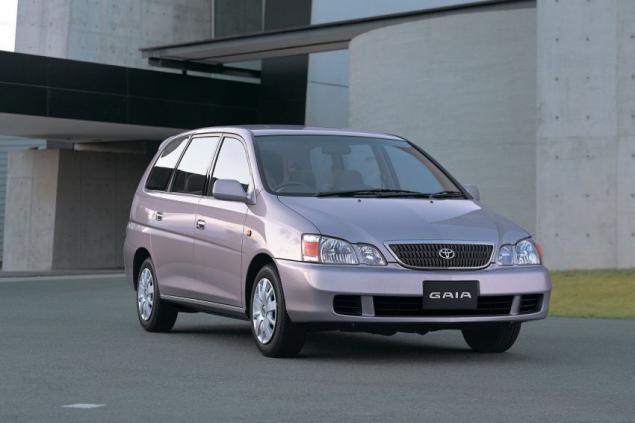
"Experimented" on consumers and BMW. 1, 6 and 2, 0-liter "four» N43 and three-liter "six» N53, N54 and N55, which appeared in 2007, in one degree or another cause trouble. Especially distinguished N54. There were problems with the supply pump, a pressure sensor nozzles. Pump thrashed several times, and in 2010 the North American market concern on models with this engine decided a revocable campaign.
Nissanovskie "Six» VQ with Neo Di and folksvagenovskie FSI and TFSI engines and direct injection without moping in electronics and even the piston group. However, their direct injection characteristic ailments that are specific to them, did not suffer. Probably negative experience Mitsubishi and Toyota studied thoroughly and efficiently. The same can be said about the system HPi in Peugeot and Citroen, on IDE at Renault, CGI at Mercedes, or about SCi EcoBoost engine in Ford. Some horror stories about their performance injection inaudible. However, "the French" direct use metered. Nissan of Neo Di almost refused, applying it in a few cases (for example, 190-hp Juke Patrol or the last generation). Toyota continues its development, but the direction of the combined - directly-distributed - injection, which exists in several models for the domestic market and not at all Lexus. In Mitsubishi from GDI, it seems abandoned. Anyway, in cars, in past generations it had now stand traditional fuel systems. Mass direct injection faithful VAG, passed him with Mercedes BMW, partially Ford, Hyundai and GM.
Toyota and Lexus went on to direct injection combined. Each cylinder serve two nozzles - a combustion chamber for a second valve in the intake passage. In the unloaded mode works the first (left), during acceleration and at high speeds - both
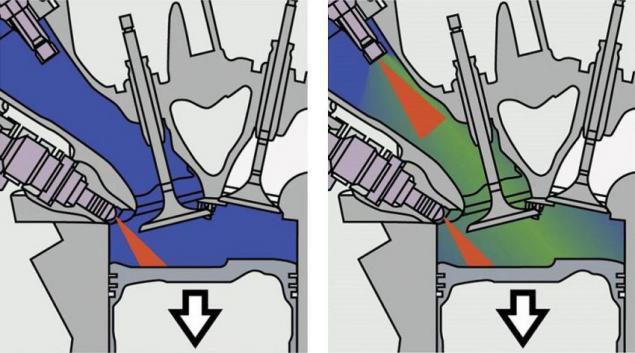
At cold start working as both injectors. "Distribution" delivers fuel to the intake stroke, "directly" - on the compression stroke. Why is all this necessary? The development potential of the internal combustion engine is largely exhausted. In this case the motors must meet the strict standards for the environment, be cost-effective and remain powerful. You can only achieve this through such "high-tech nuance»
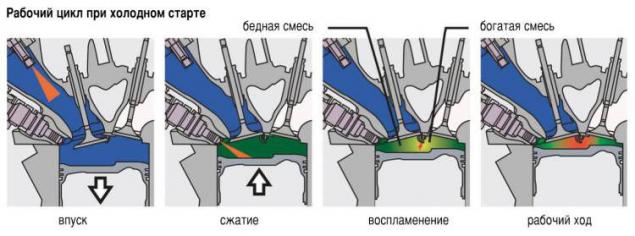
Operating rules
In general, not every manufacturer and every model is ready to use direct injection. With the "premium brand" all clear, advanced technology, we can say, put on status. "Folk" is the brand stratified charge in the majority adopting models poprestizhnee and not in all markets. The situation here as with diesel engines equipped with common rail, which some companies still do not dare to offer in our market.
More precisely, the worse. Indeed, a key node of the entire system - pump - works on the same principles that a similar device in diesel engines. The spray, which is needed for the preparation of ultra-lean and homogeneous mixture is obtained thanks to the very high pressures. If conventional pumps develop about 3-4 atm, these already provide 50-130 atm. And basically no matter what at the pump design - one he has a plunger, three, or seven, or maybe the pressure is developed with the help of spaced parallel plates. Such atmosphere reaches a high, high precision machining. For them, even the sulfur - abrasive, not to mention the "solid foreign inclusions." And the water, it must be confessed, still gets in our fuel similar to sulfuric or some other "vigorous" acid. "Verdict" pump or at least significantly reduce its life, cause outages due to "rough" spray gasoline refueling capable only rich such "additives" fuel. Buying a car with direct injection, which will be operated away from civilization, from the gas station where not exactly poured cocktail of raw water and it's not even a lottery - guaranteed way to service. Why, run into a lethal mixture for the pump and can be more or less in large cities. And such cases are not massively, but there.
High pressure fuel pump driven by the camshaft, but not always easy to access it. Incidentally, it is quite logical to add fuel, lubricating and cleaning additives, what is commercially available. But manufacturers do not permit. Only the fuel that Russia recognized quality (it is, of course, petrol Euro 4 or Euro 5). Therefore, no adjustment of the fuel equipment to our conditions no
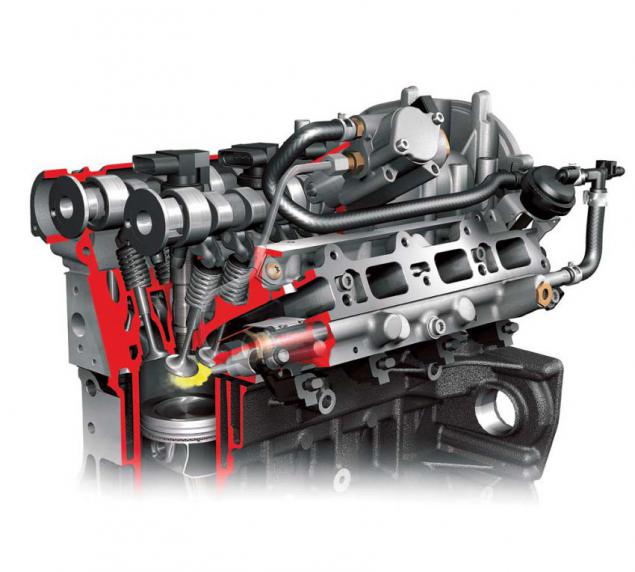
And count on the warranty of the purchased vehicle from a dealer in this case is not necessary. Take samples of petrol and easily prove that the failure is caused by poor-quality fuel. Meanwhile, the cost of the injection pump is quite high - from 10 to 50 thousand. Rub. So in fact also have to change the injectors. They also operate with high pressure and as susceptible to wear. It has 3, 5-6 thousand. Rub. apiece. Plus repair time for which the victim of our fuel, of course, will not receive a replacement vehicle.
And in a diesel engine high pressure pump even works in "fat" environment in Local. And gasoline - which lubricating ability ?! In general, fuel pump wear even under greenhouse conditions on an ideal fuel. Talk about the resource, even approaches that of a conventional pump is not necessary. And what is this resource? The manufacturer declares that the pump is designed for the whole lifetime of the car. However, as we know, this "time" for the firms is often a guarantee. 100 thousand. Km fuel system components, and the truth is stretched. Even 150. Still, choosing a used car with such runs, not immediately lay in operating expenses the cost of the pump and injectors. And, in addition, take into account that the EGR system and the throttle body requires relatively frequent cleaning. In the context of work on the ultra-lean mixture so in city traffic, these sites are able to grow over 20 per thousand. Km or less. For comparison, the two-liter "direct" engine Focus III, where there is no recycling, cleaning the intake need 40-50 thousand. Km. In the most severe cases even have to clean the channels in the cylinder head. To minimize this effect, once in awhile 500-1000 km worth giving the engine at high rpm.
Node EGR neat and after a certain mileage for jams. Probably need to clean the channels in the cylinder head and, of course, the throttle valve. Last after cleaning is necessary also to adapt the scanner
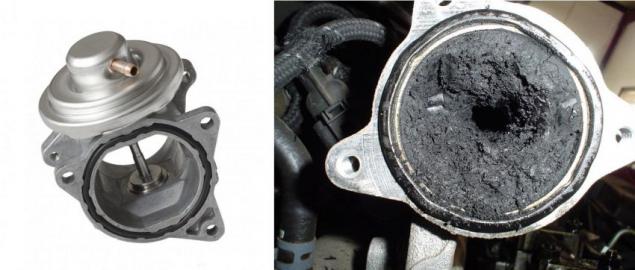
So whether you need to be afraid of direct injection? Yes, motors with him when contaminated channels are losing power. Owners are attached to the gas station with high-quality fuel. Some real savings of gasoline at the claimed 10-15% or even 20% will manifest only under ideal conditions, that is at idle or low speed. Finally, at any time, fuel injection equipment may require the unexpected financial investments. But, for example, modern transmissions without any gasoline where "softer" and more expensive to repair. And then, observing certain rules, we can hope for a trouble-free operation.