2774
How the Steel Was Tempered
Few imagine the steel production process. We only see the end result, not thinking about how to get out of a piece of ore car, cutlery or other metal products. Today we have a chance to learn how the Steel Was Tempered, meet people - masters of fiery profession. Kazakhstan's largest steel company - "ArcelorMittal Temirtau" agreed to show their production.
The company consists of Iron and Steel Works, 8 coal mines and mine 4. Iron and Steel Works, known as Kazakhstan Magnitogorsk - a city within a city. Around it for a day - is unrealistic. The total area occupied by a giant iron and steel, is 5000 ha. (Photo by Igor Uzarevicha)
Currently the company employs more than 40,000 people at the metallurgical plant about 18 thousand (Photo by Igor Uzarevicha)
The process of obtaining the metal is a complex process chain with a plurality of operations. And it begins with the extraction of ore and deliver it to the Iron and Steel Works. Raw materials are supplied with a 5-fields - Lisakovsk, Karazhal (mine Atasu) Karkaralinsk (Kentobe) Stepnogorsk (mine Atansor) and Sokolov-Sarbai field.
Raw materials (ore warehouse). This continually deliver raw materials and prepare for the process of agglomeration (obogoschenie). Kazakhstan ore has low iron content and a high content of phosphorus, which gives the metal brittleness. Therefore, technology metkombinata designed specifically through the use of local ore. Agglomeration - the process of preparing ore concentrate for further processing, namely ironmaking.
The total length of the pipes at the plant no one can even imagine. The account goes on hundreds of kilometers.
Car dumper - rotating around its axis platform on which is fixed and flipped the car weighing about 100 tons.
Load pours into the hopper of which is fed to a conveyor for delivery to the site of processing.
Michael, car dumper operator:
- We have been working 12-hour shifts a day, in any weather. Continuous process. Not to say that is not tired, but are used to. Work is work.
Feed wagons with raw materials does not stop for a minute.
The total length of the pipeline for the transportation of raw materials to the plant - 42 kilometers.
In this chamber are mixed and crushed ore beneficiation and additional components required for the manufacture of cast iron - the original cast product.
And so they look like from above.
Master technician diagnoses equipment.
These warning signs can be found everywhere. After all, most often the cause of accidents is the human factor.
Agloproizvodstva vapor pipe. The height of 250 meters.
Prepared for the enrichment of ore, lay in the sintering machine.
Under the influence of a high temperature additive and iron content in technologically agglomerate rises to the desired level.
In the process of agglomeration the mixture of ore to fuel sintered agglomerates - ready raw material for the blast furnace.
But in order to get the iron, need a high temperature in the furnace, and this temperature can give coke specially prepared coal which is supplied to the plant from coal mines of Karaganda region (photo by Igor Uzarevicha)
Coke is produced in the coking plant, which is part of the metallurgical plant. Coke oven battery - Wall of separate sections, where coal is sintered without access of oxygen at a temperature of about 1700 degrees. With this vozeystviyu give the product (coke) is highly caloric (heat transfer) and a low ash content.
Delayed Coking Process captures. A huge fiery mass is squeezed out of the camera ....
... And falls with a crash into the prepared special wagon.
This is very similar to a volcanic eruption.
Worker cleans valve chamber.
Process controls girl-operator.
Electric locomotive driver - also a girl.
Women everywhere are themselves. And even here manage to break up the flower beds.
This pyramid is the process of "wet" (water) cooling of coke. Column of steam at the same time "shoots" at 50 meters.
Here's what a blast furnace outside.
And this is - inside. Height - 25 floors. There blend (mixture of sintered iron, coke, limestone and dolomite) is converted into molten iron. The temperature inside the oven reaches 1700-2000 degrees, and in the taphole, through which flows the molten iron at its release - 1400 degrees.
All hearth wear protective clothing and shoes, designed for high temperatures. Just so you can safely go to the metalllu at close distance.
For refractory channels (Lethke) molten metal flows into the buckets to be sent to the converter shop.
Sampled to determine the quality of pig iron.
Hearth cast-iron molds sample.
Gornova be - hard work. And really dangerous. By the way, the president of Kazakhstan started his career here, on the Kazakhstan Magnitogorsk, in the blast furnace - hearth.
Remote control blast furnace.
For the smooth operation of the blast furnace should be kept under the control of all parameters.
Here are stored samples of slag and iron.
Workers come with change.
The next step - steelmaking. Here iron steel cook, adding scrap and other necessary technology components. Combine in Temirtau produces more than 180 grades of steel.
The temperature in this shop as in the desert at noon.
Intermediate data during cooking temperature steel. Maximum 1620 degrees.
For protection against overheating is regularly supplied with water.
The very process of cooking steel scale can safely prirovnyat for the launch.
This machine is almost enters the boiler for work.
This happens sampling to determine compliance steels necessary parameters.
To make the steel of the relevant properties of the additives are added (ligatures). In this case - aluminum.
Watch the process without special glasses filters impossible.
Fiery extravaganza inside the furnace-boiler. Boiling steel.
Finished steel is supplied to the Department of continuous casting. While lifting the bucket workers removed to the maximum distance.
In one steel ladle 290 tons of liquid steel.
Cover the bucket.
The molten steel is supplied to the continuous casting machine.
And on the output of the first finished products - slabs - steel billets.
Throughout the plant hung posters, clearly reminiscent of the consequences of negligence in their work. After metallurgical production involves dangerous risks - high temperatures, moving machinery and heavy loads.
Next slabs are used in rolling production, which is composed of shop hot-rolled, cold rolled, shop, shop tinplate (of which then make cans of canned food!) And hot alyumotsinkovaniya shop. Slabs are rolled into a thin sheet iron, the thickness of which varies to polumillimetra.Takim way of 9 meters workpiece turns about a kilometer of finished steel for further processing of metal and produce the final product.
Roll stretched on shafts, after which it is subjected to galvanizing by dipping into a bath of molten zinc. At the exit - the canvas with a mirror reflective surface. Metal-coated aluminum and zinc, does not corrode, and therefore is the most popular among consumers.
Finished products are packed and ready for shipment.
Painting line. Ready metal products "ArcelorMittal" diverges around the world - 75 countries! (Photo by Igor Uzarevicha).
And after a hard day of work metallurgical hurry home to their families
via Source
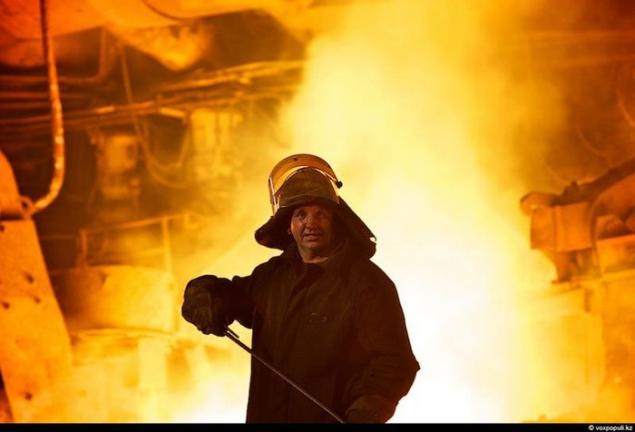
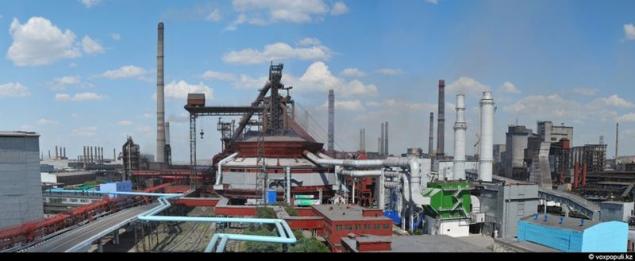
The company consists of Iron and Steel Works, 8 coal mines and mine 4. Iron and Steel Works, known as Kazakhstan Magnitogorsk - a city within a city. Around it for a day - is unrealistic. The total area occupied by a giant iron and steel, is 5000 ha. (Photo by Igor Uzarevicha)
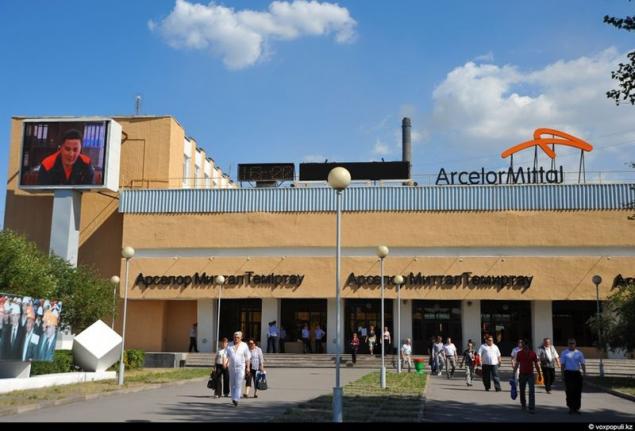
Currently the company employs more than 40,000 people at the metallurgical plant about 18 thousand (Photo by Igor Uzarevicha)
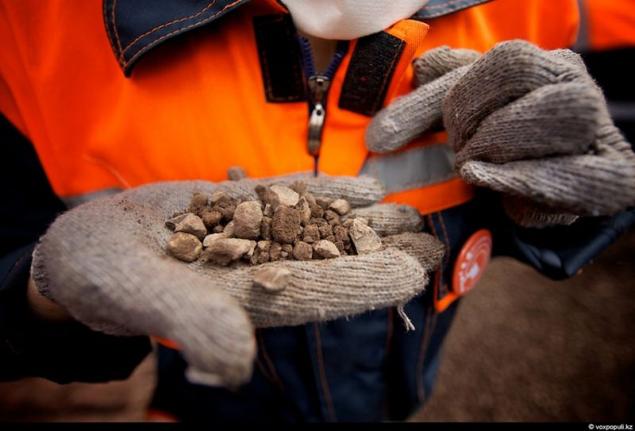
The process of obtaining the metal is a complex process chain with a plurality of operations. And it begins with the extraction of ore and deliver it to the Iron and Steel Works. Raw materials are supplied with a 5-fields - Lisakovsk, Karazhal (mine Atasu) Karkaralinsk (Kentobe) Stepnogorsk (mine Atansor) and Sokolov-Sarbai field.
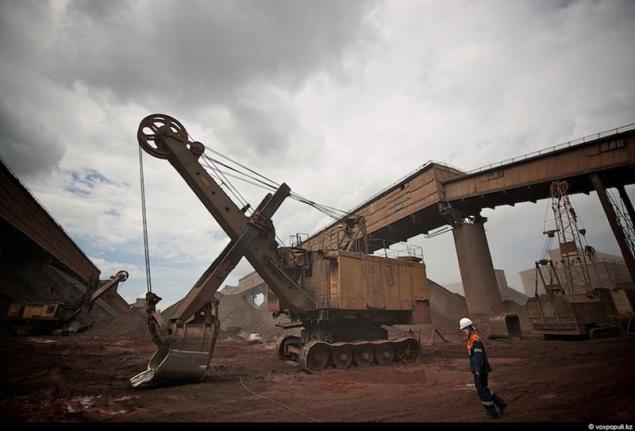
Raw materials (ore warehouse). This continually deliver raw materials and prepare for the process of agglomeration (obogoschenie). Kazakhstan ore has low iron content and a high content of phosphorus, which gives the metal brittleness. Therefore, technology metkombinata designed specifically through the use of local ore. Agglomeration - the process of preparing ore concentrate for further processing, namely ironmaking.
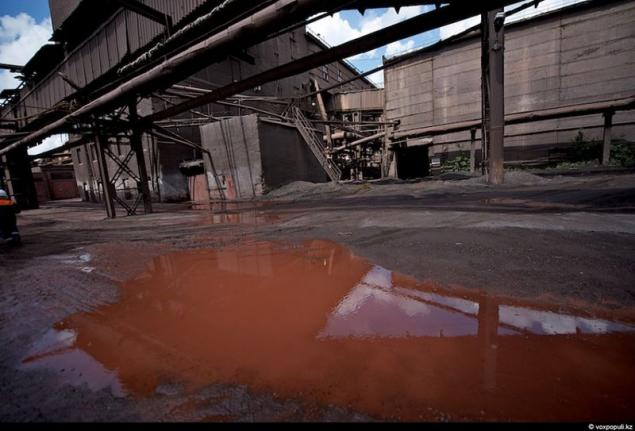
The total length of the pipes at the plant no one can even imagine. The account goes on hundreds of kilometers.
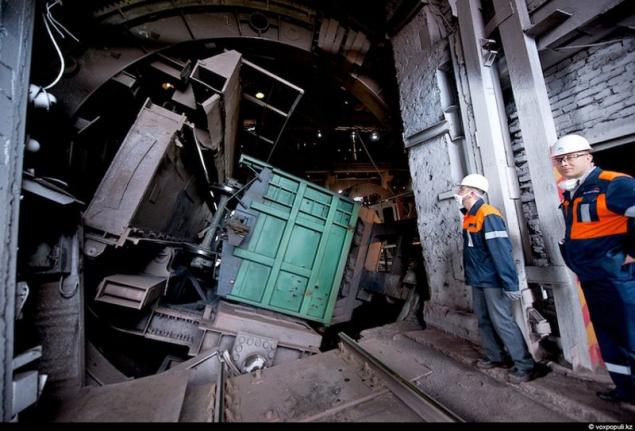
Car dumper - rotating around its axis platform on which is fixed and flipped the car weighing about 100 tons.
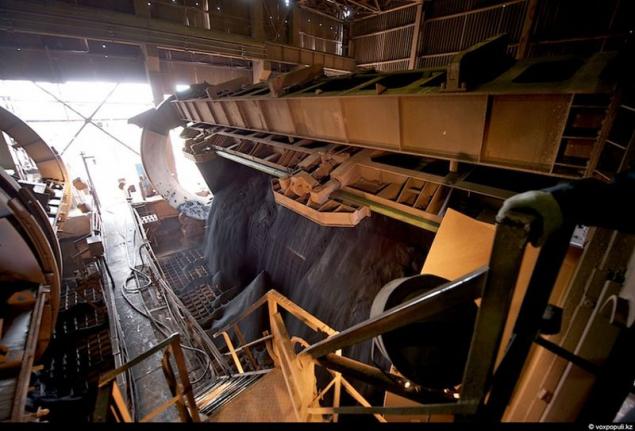
Load pours into the hopper of which is fed to a conveyor for delivery to the site of processing.
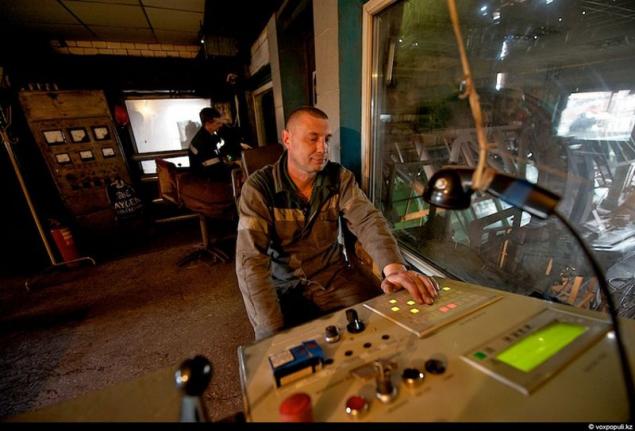
Michael, car dumper operator:
- We have been working 12-hour shifts a day, in any weather. Continuous process. Not to say that is not tired, but are used to. Work is work.
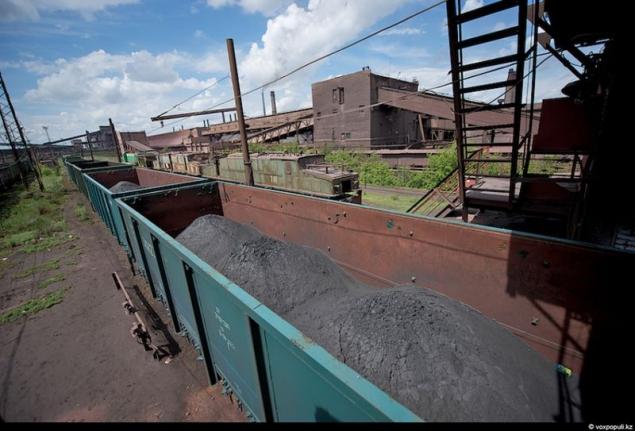
Feed wagons with raw materials does not stop for a minute.
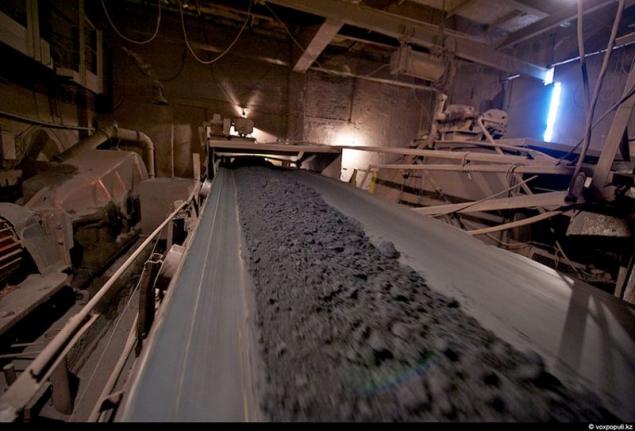
The total length of the pipeline for the transportation of raw materials to the plant - 42 kilometers.
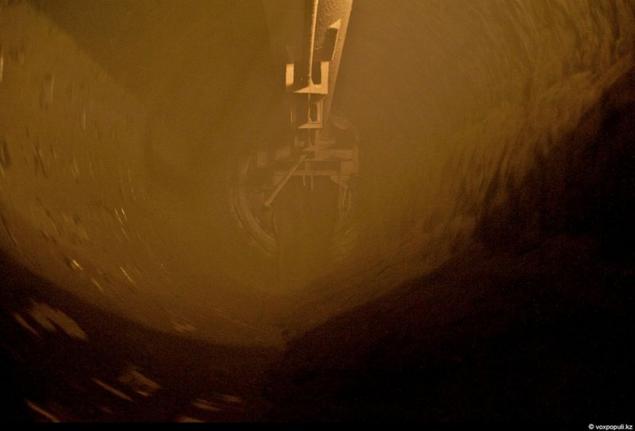
In this chamber are mixed and crushed ore beneficiation and additional components required for the manufacture of cast iron - the original cast product.
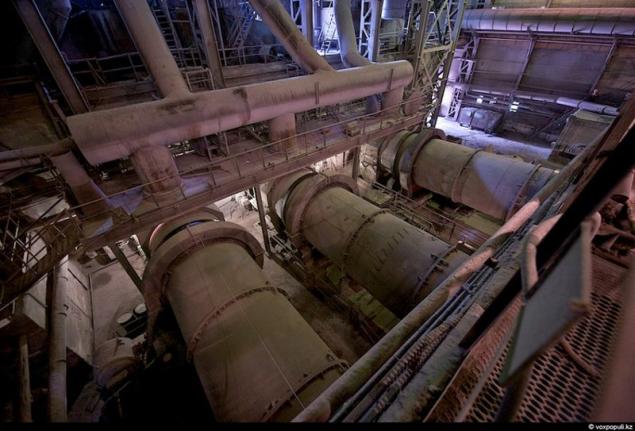
And so they look like from above.
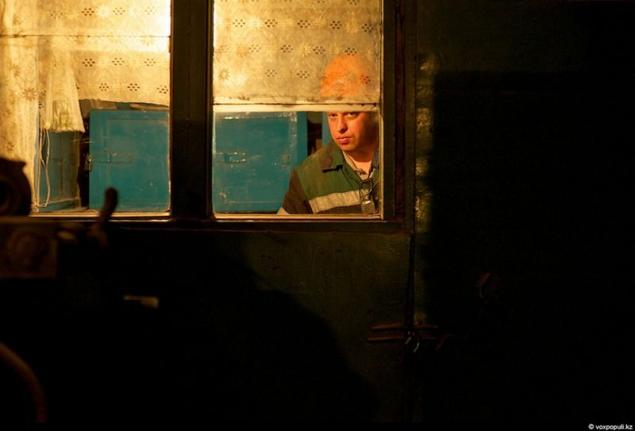
Master technician diagnoses equipment.
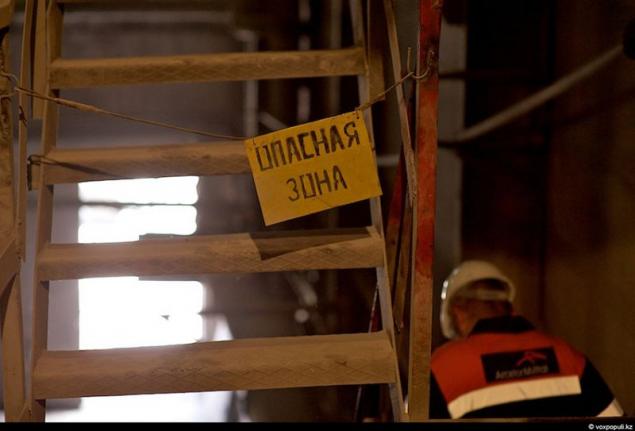
These warning signs can be found everywhere. After all, most often the cause of accidents is the human factor.
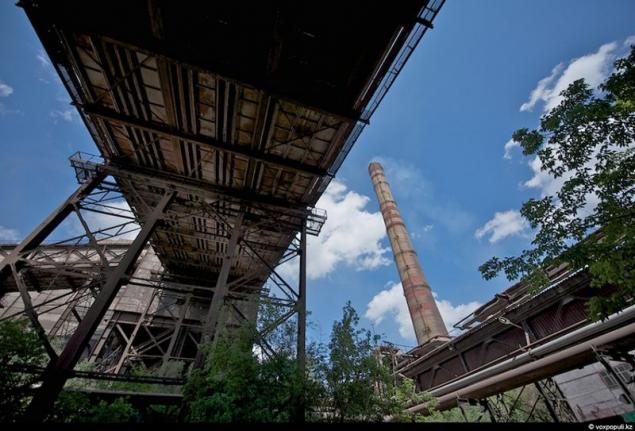
Agloproizvodstva vapor pipe. The height of 250 meters.
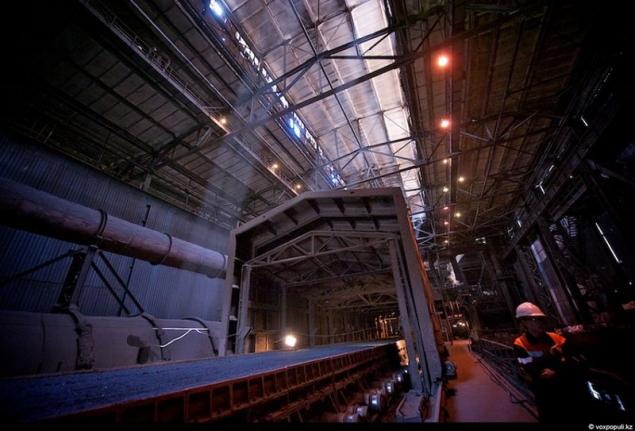
Prepared for the enrichment of ore, lay in the sintering machine.
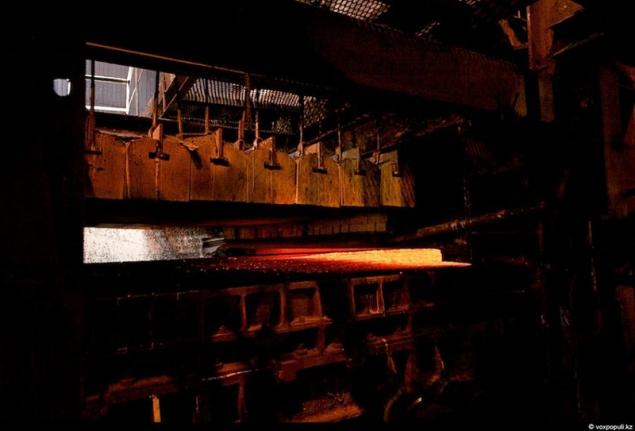
Under the influence of a high temperature additive and iron content in technologically agglomerate rises to the desired level.
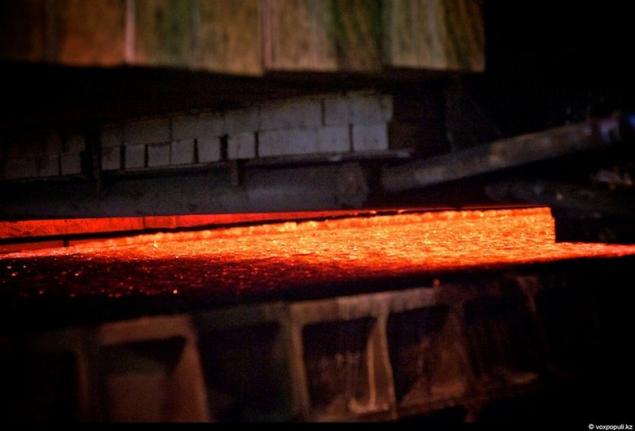
In the process of agglomeration the mixture of ore to fuel sintered agglomerates - ready raw material for the blast furnace.
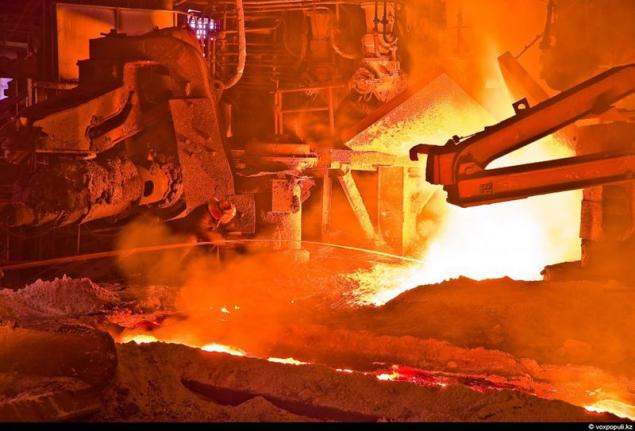
But in order to get the iron, need a high temperature in the furnace, and this temperature can give coke specially prepared coal which is supplied to the plant from coal mines of Karaganda region (photo by Igor Uzarevicha)
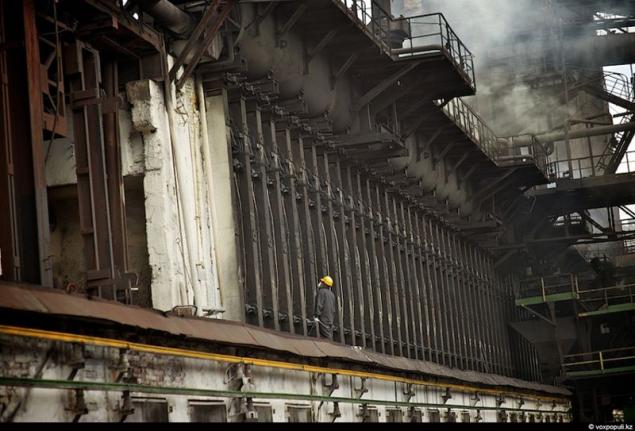
Coke is produced in the coking plant, which is part of the metallurgical plant. Coke oven battery - Wall of separate sections, where coal is sintered without access of oxygen at a temperature of about 1700 degrees. With this vozeystviyu give the product (coke) is highly caloric (heat transfer) and a low ash content.
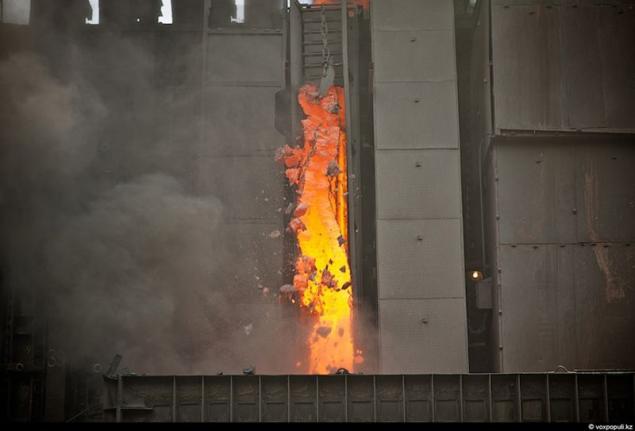
Delayed Coking Process captures. A huge fiery mass is squeezed out of the camera ....
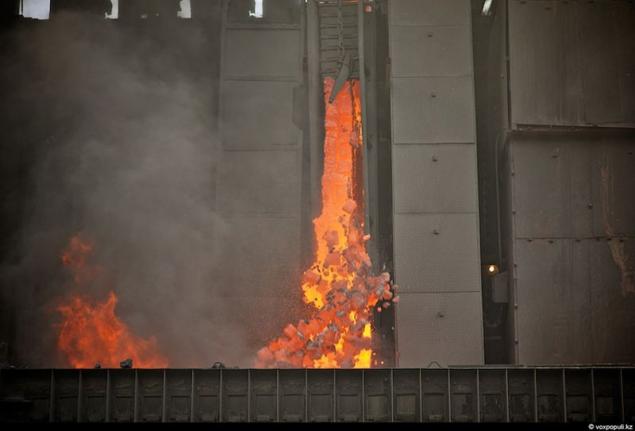
... And falls with a crash into the prepared special wagon.
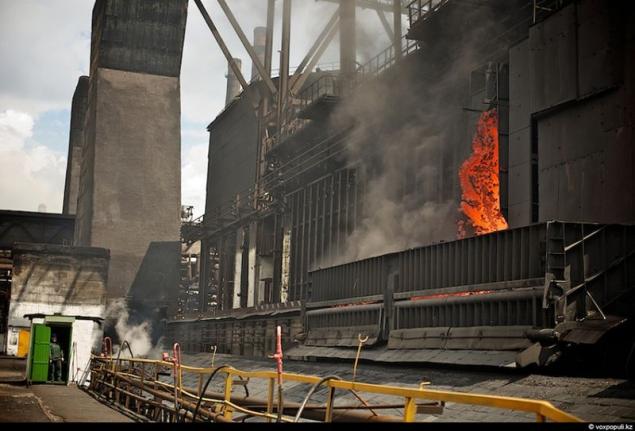
This is very similar to a volcanic eruption.
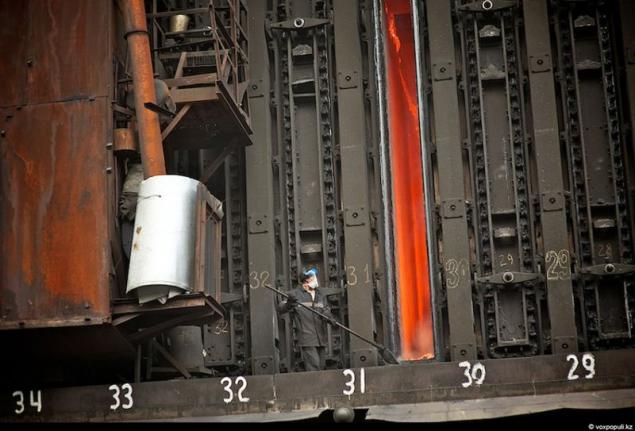
Worker cleans valve chamber.
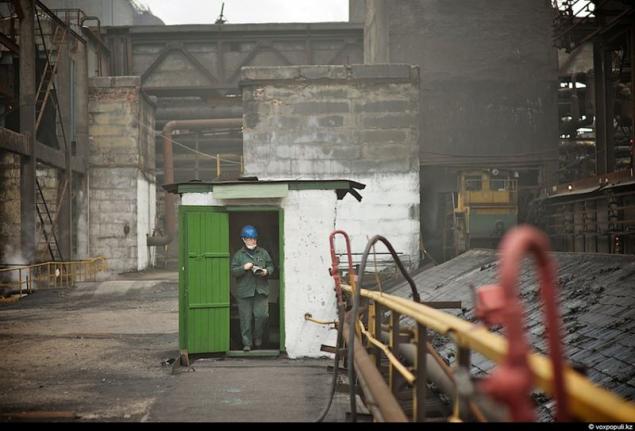
Process controls girl-operator.
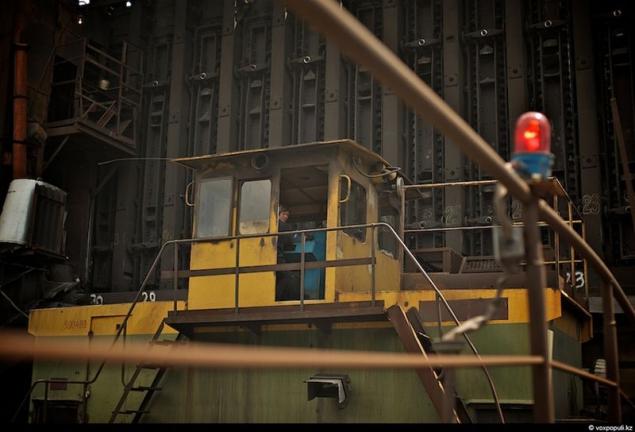
Electric locomotive driver - also a girl.
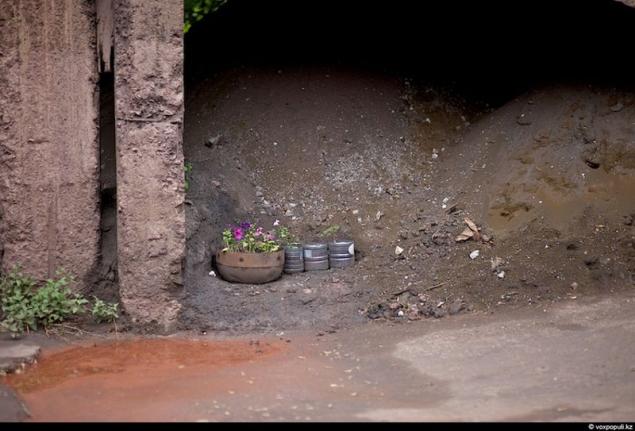
Women everywhere are themselves. And even here manage to break up the flower beds.
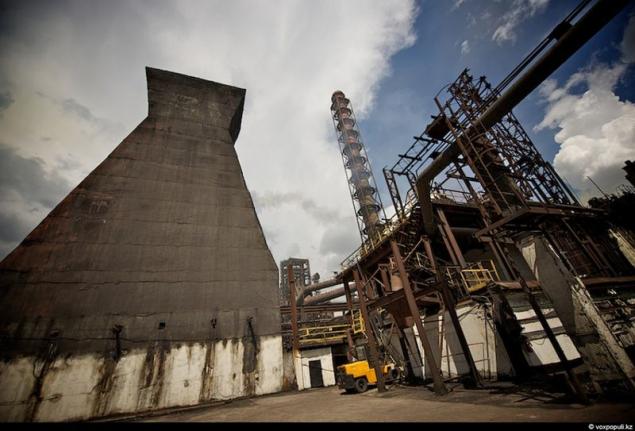
This pyramid is the process of "wet" (water) cooling of coke. Column of steam at the same time "shoots" at 50 meters.
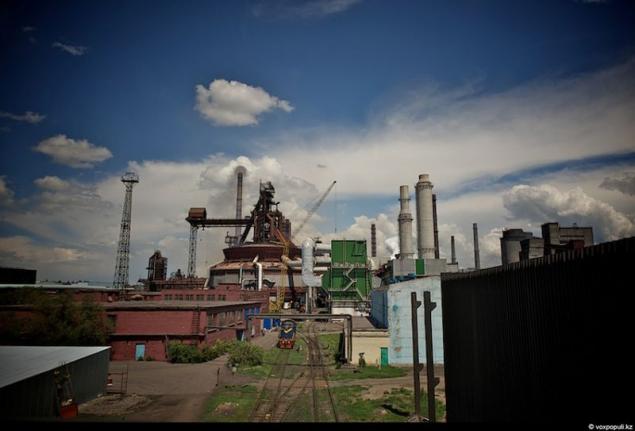
Here's what a blast furnace outside.
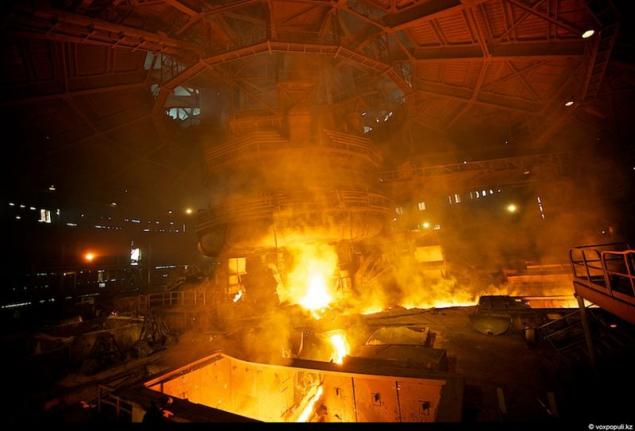
And this is - inside. Height - 25 floors. There blend (mixture of sintered iron, coke, limestone and dolomite) is converted into molten iron. The temperature inside the oven reaches 1700-2000 degrees, and in the taphole, through which flows the molten iron at its release - 1400 degrees.
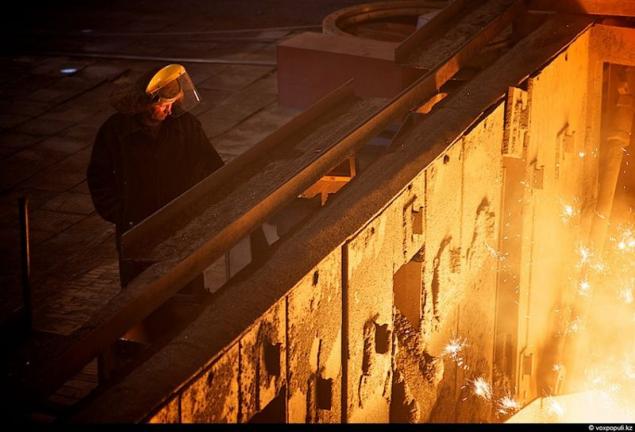
All hearth wear protective clothing and shoes, designed for high temperatures. Just so you can safely go to the metalllu at close distance.
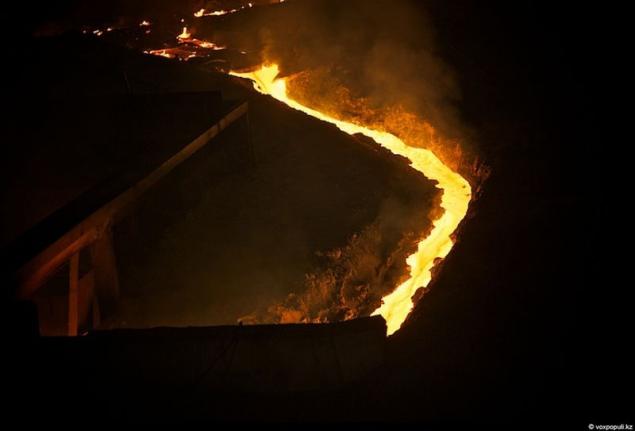
For refractory channels (Lethke) molten metal flows into the buckets to be sent to the converter shop.
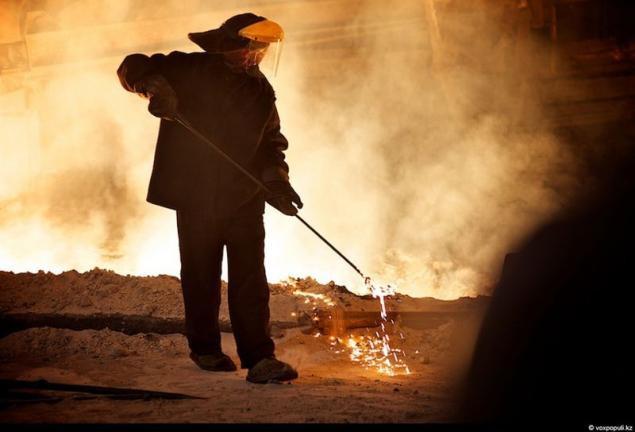
Sampled to determine the quality of pig iron.
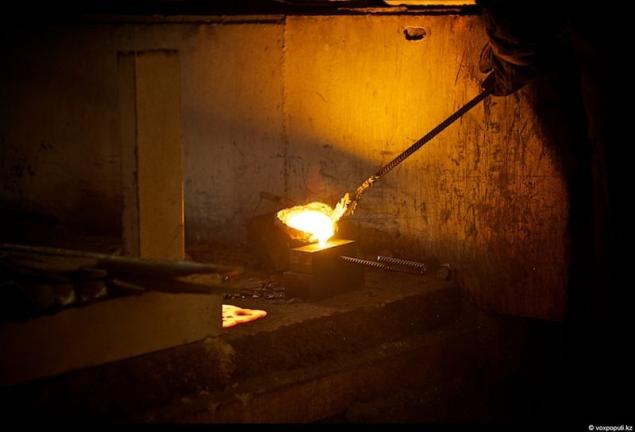
Hearth cast-iron molds sample.
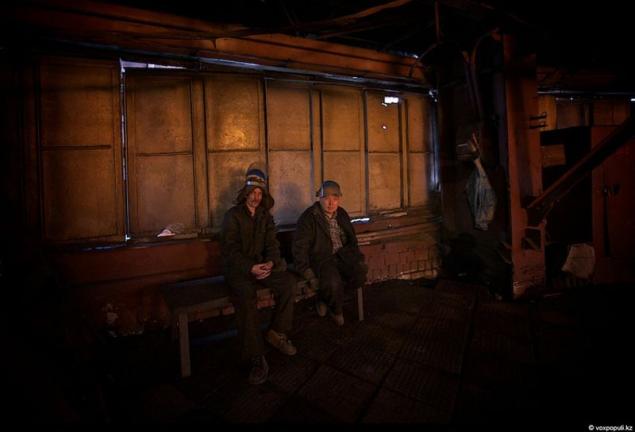
Gornova be - hard work. And really dangerous. By the way, the president of Kazakhstan started his career here, on the Kazakhstan Magnitogorsk, in the blast furnace - hearth.
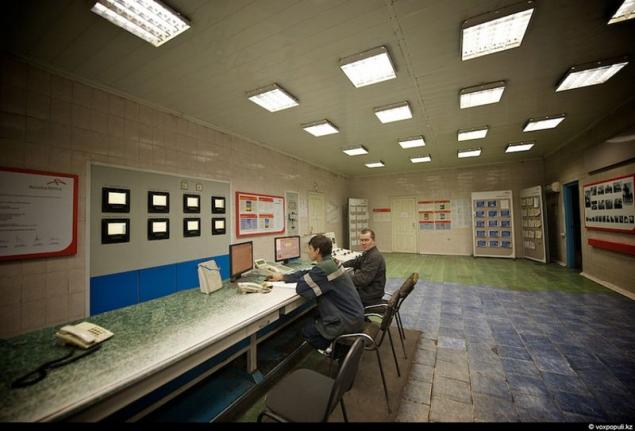
Remote control blast furnace.
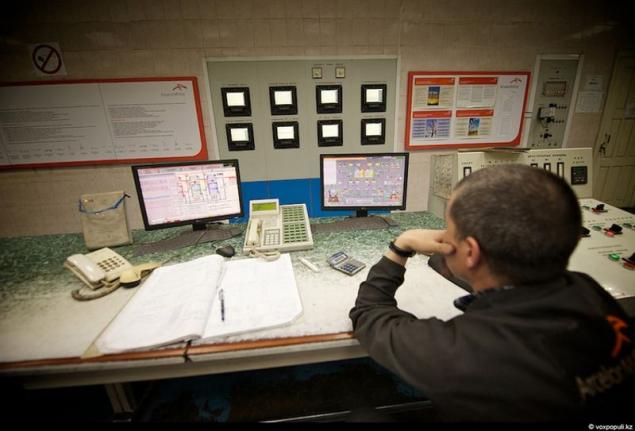
For the smooth operation of the blast furnace should be kept under the control of all parameters.
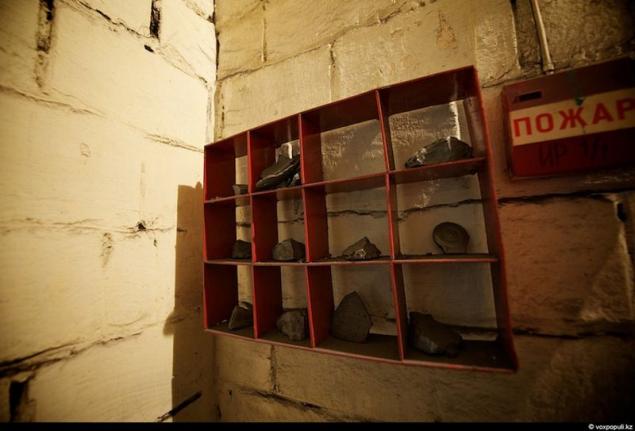
Here are stored samples of slag and iron.
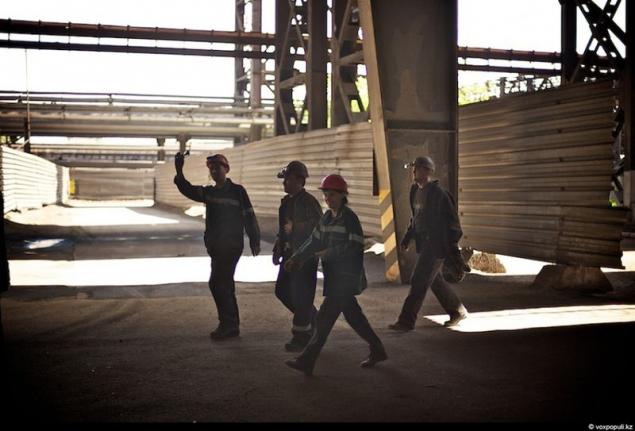
Workers come with change.
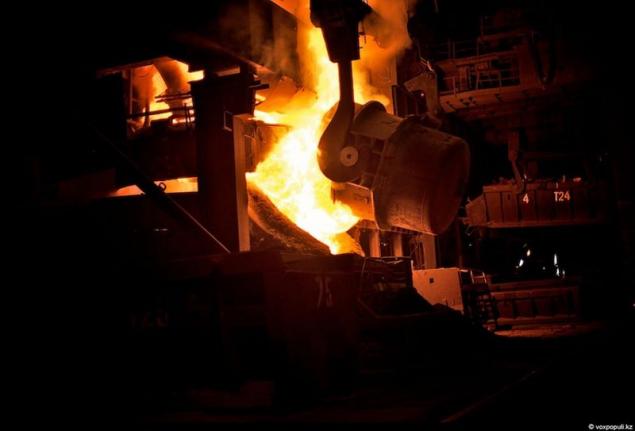
The next step - steelmaking. Here iron steel cook, adding scrap and other necessary technology components. Combine in Temirtau produces more than 180 grades of steel.
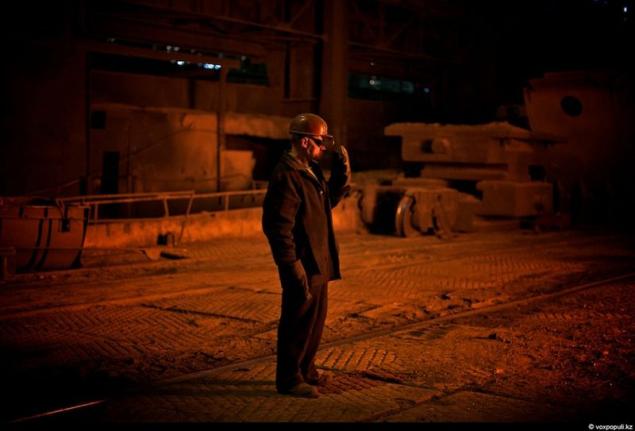
The temperature in this shop as in the desert at noon.
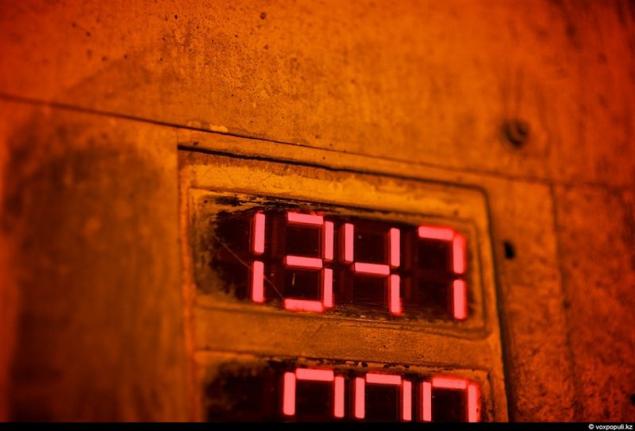
Intermediate data during cooking temperature steel. Maximum 1620 degrees.
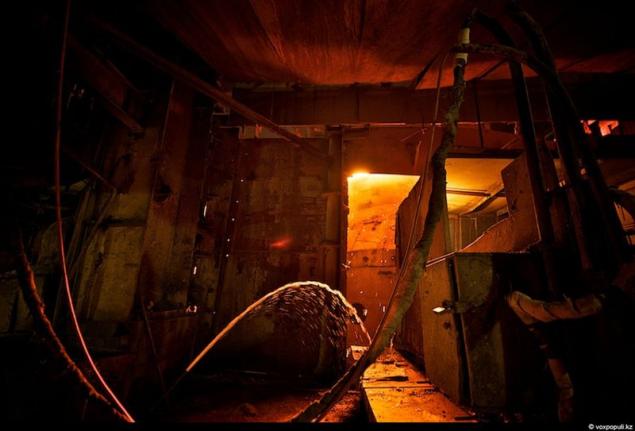
For protection against overheating is regularly supplied with water.
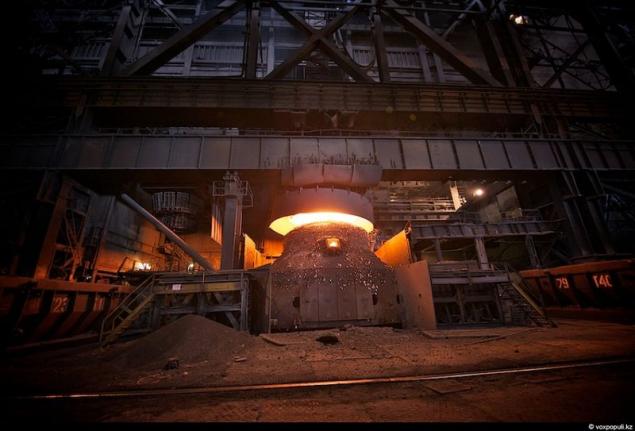
The very process of cooking steel scale can safely prirovnyat for the launch.
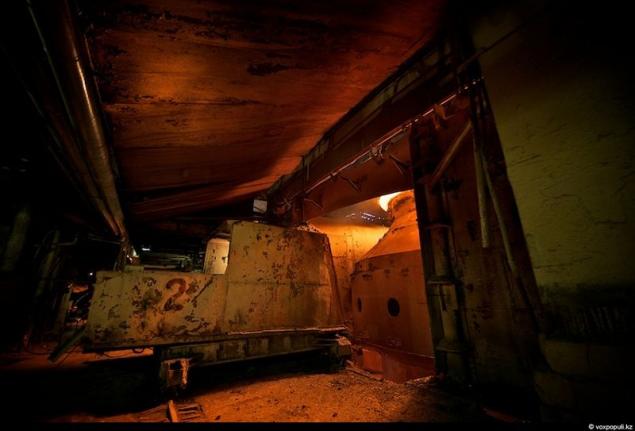
This machine is almost enters the boiler for work.
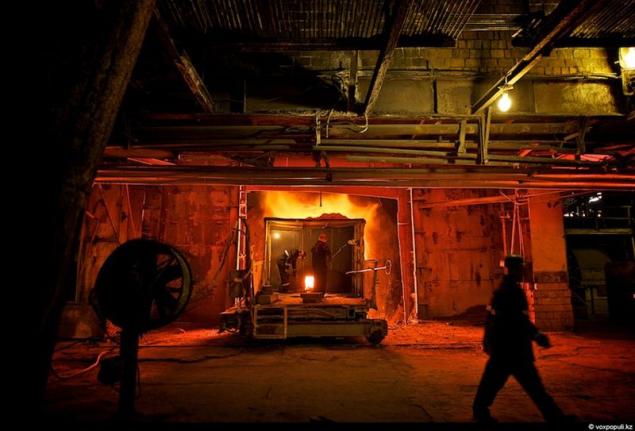
This happens sampling to determine compliance steels necessary parameters.
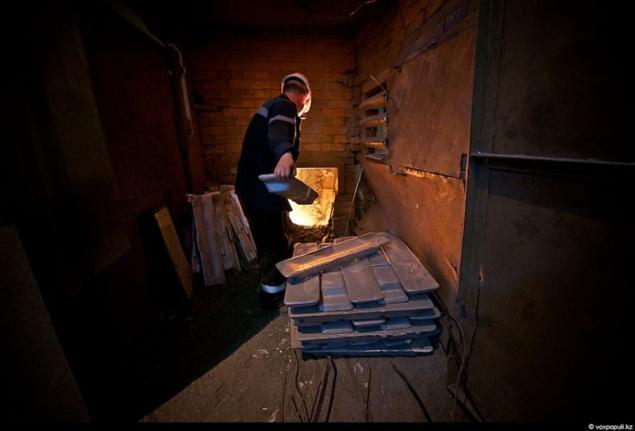
To make the steel of the relevant properties of the additives are added (ligatures). In this case - aluminum.
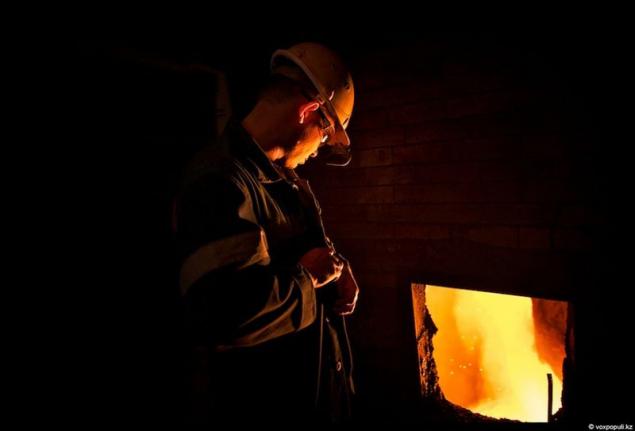
Watch the process without special glasses filters impossible.
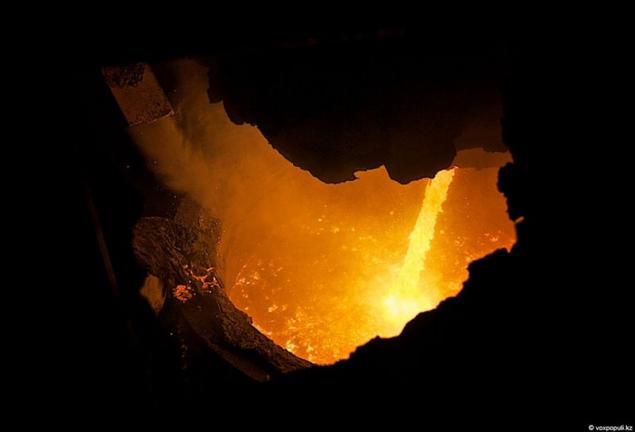
Fiery extravaganza inside the furnace-boiler. Boiling steel.
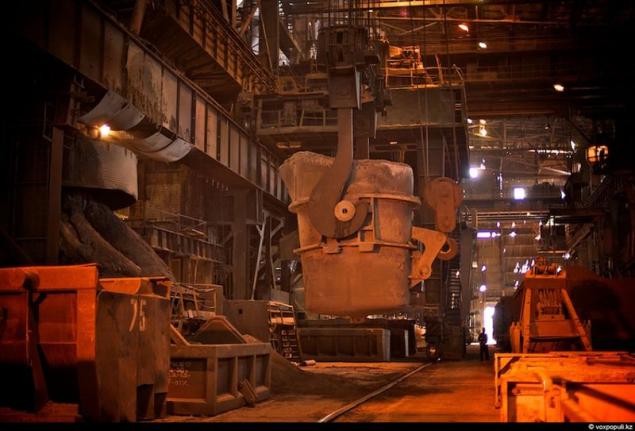
Finished steel is supplied to the Department of continuous casting. While lifting the bucket workers removed to the maximum distance.
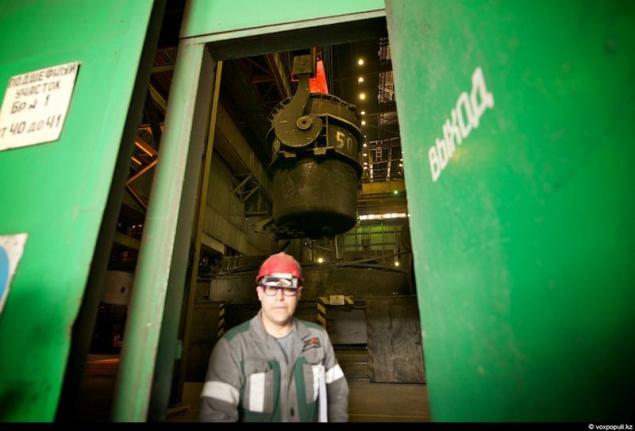
In one steel ladle 290 tons of liquid steel.
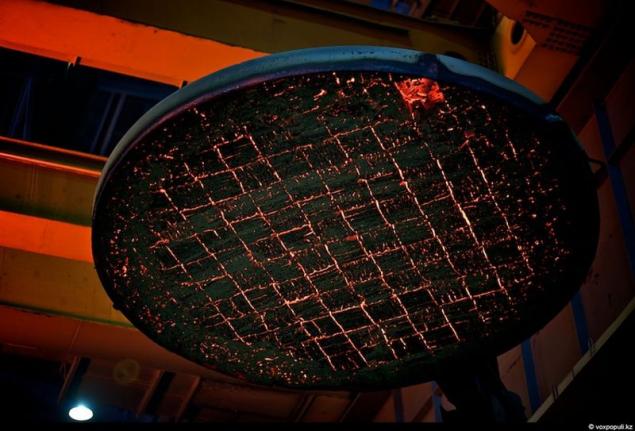
Cover the bucket.

The molten steel is supplied to the continuous casting machine.
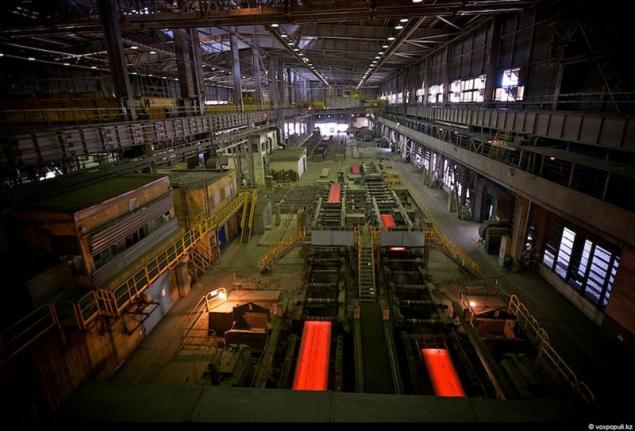
And on the output of the first finished products - slabs - steel billets.
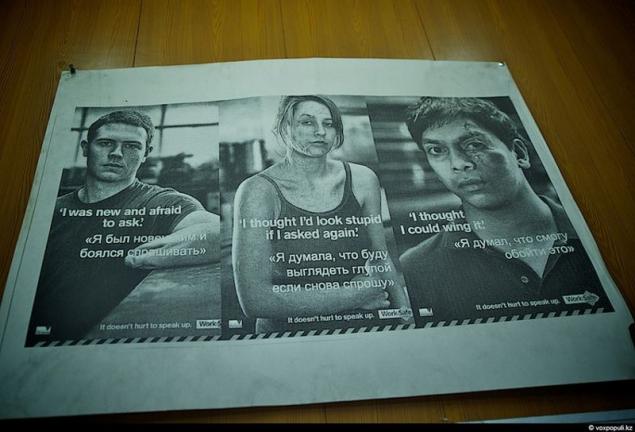
Throughout the plant hung posters, clearly reminiscent of the consequences of negligence in their work. After metallurgical production involves dangerous risks - high temperatures, moving machinery and heavy loads.

Next slabs are used in rolling production, which is composed of shop hot-rolled, cold rolled, shop, shop tinplate (of which then make cans of canned food!) And hot alyumotsinkovaniya shop. Slabs are rolled into a thin sheet iron, the thickness of which varies to polumillimetra.Takim way of 9 meters workpiece turns about a kilometer of finished steel for further processing of metal and produce the final product.
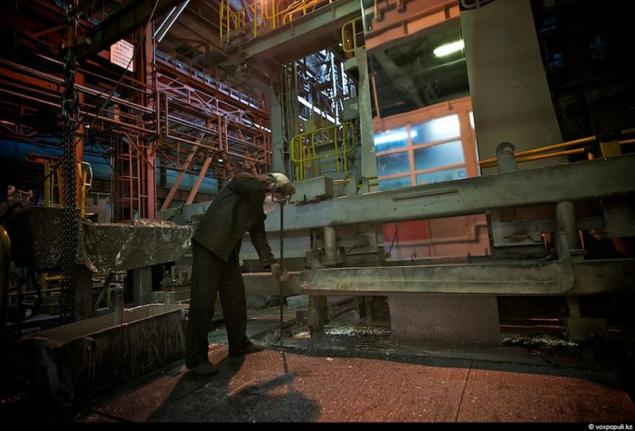
Roll stretched on shafts, after which it is subjected to galvanizing by dipping into a bath of molten zinc. At the exit - the canvas with a mirror reflective surface. Metal-coated aluminum and zinc, does not corrode, and therefore is the most popular among consumers.
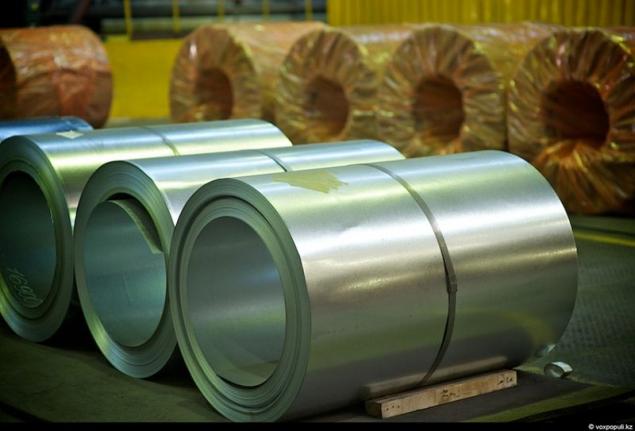
Finished products are packed and ready for shipment.
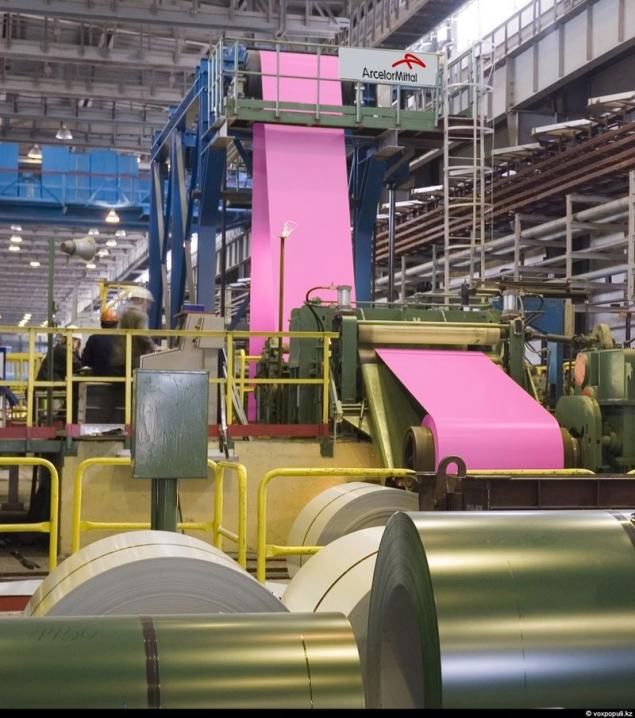
Painting line. Ready metal products "ArcelorMittal" diverges around the world - 75 countries! (Photo by Igor Uzarevicha).
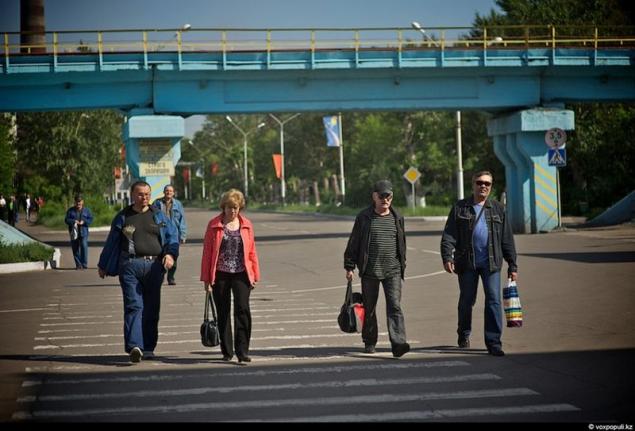
And after a hard day of work metallurgical hurry home to their families
via Source