977
0.2
2015-07-04
Рассказ о тепловозах-2
В первой части рассказа я кратко рассказал об устройстве и принципах работы тепловозов. В этой части я раскажу о том, как тепловозы ремонтируются, как происходит их разборка, ремонт, последующая сборка и настройка. К сожалению, во время съемок окончательно сдох мой цифровик, а в отдельных случаях (во избежание неприятностей) фотографировать приходилось почти подпольно, поэтому фоткал на «тапок». Но, в принципе, фото довольно разборчивы, все, что нужно, вполне смотрибельно.Ну а гурманам-эстетам фотодела заранее мои глубочайшие извинения.
Итак, поехали. Будет 36 фото.Просьба, подборку не ломать, потом отвечу на вопросы, если будут.
Ремонт тепловозов по степени сложности (величине) зависит от их пробегов. Чем больше пробег, тем крупнее ремонт. Самый крупный ремонт — с выемкой дизель-генератора из тепловоза с последующей разборкой дизеля и генератора, ремонтом всех узлов и агрегатов, последующей сборкой, настройкой и регулировкой дизель-генераторной установки (реостатными испытаниями).Существует и более мелкий ремонт, когда дизель не вынимается полностью из тепловоза, а происходит его частичная разборка, то есть состояние дизеля таково, что нет необходимости разбирать его весь, а можно разобрать и отремонтировать только те его части, которые нуждаются в ремонте. Об этом я тоже здесь расскажу
Перед разборкой из тепловоза сливаются все жидкости: вода, топливо, масло, из бункеров высыпается песок. Затем топливный бак промывается и пропаривается.На этом фото происходит пропарка топливного бака позле разэкипировки тепловоза.
Затем тепловоз ставится в цех. Происходит разборка дизеля, он рассоединяется со всеми трубопроводами и отсоединяется от тепловозной рамы.На этом фото крыша уже демонтирована для выемки дизеля.
Сняты передний редуктор и воздушный компрессор.Хорошо виден двухмашинный агрегат, который тоже будет демонтирован.
Это фото приведено для сравнения того что было с тем, что стало после разборки Сравните с верхним фото. Теперь дизель можно снимать с тепловоза. Вынимают его 30-тонным краном.
Снято все электрооборудование. Остались одни кабели, да и они скоро будут сняты.
Затем тепловоз ставится на домкраты. Отсоединяются кабели тяговых электродвигателей, отсоединяются опорно-возвращающие устройства тележек, затем тепловоз поднимают на домкратах и тележки (их на каждой секции две, на каждой по три тяговых двигателя) выкатываются из-под тепловоза. Теперь можно заниматься ремонтом трубопроводов, и опорных устройств тепловоза.
Еще фото, поближе.
Потом тяговые двигатели отсоединяются от тележек. Затем и тележка и тяговые двигатели тоже полностью разбираются и ремонтируются. На этм фото тяговые двигатели после ремонта и проверки подготовлены для установки обратно на тележку.
Иногда возникает необходимость ремонта только одного тягового двигателя. Чтобы не поднимать тепловоз на домкраты и не разбирать полностью тележку, придумано вот такое устройство, называется скатоопускной механизм. Тепловоз подгоняется на скатоопускник, отсоединяются кабели и крепеж только одного тягача, затем он опускается вместе с платформой скатоопускника и выезжает из-под тепловоза, который остается стоять. Таким же образом тяговый двигатель ставят на место.
А это станок для обточки бандажей колесных пар. Обычно колесная пара отсоединяется от тягового двигателя и в случае необходимости обтачивается на специальном станке. Но иногда бывает необходимо обточить бандаж не разбирая тягач(ну, наехал тепловоз на какое-то препятствие и получилась выбоина на колесе). Тогда тепловоз подгоняют на такой вот станок, зажимают колесную пару в специальном суппорте, чуть приподнимают и специальной фасонной фрезой обтачивают бандаж, постепенно вращая колесную пару.
Вернемся к дизелю. Его уже наполовину разобрали. Сняли тяговый генератор, турбины и нагнетатель наддувочного воздуха вместе с воздухоохладителями.
Турбины и нагнетатель отвезли для дальнейшей разборки и ремонта на участок ремонта агрегатов наддува. Здесь их разберут, очистят, отбалансируют и соберуют заново.
Теперь снимаем верхний коленчатый вал (на этом дизеле их два: верхний и нижний). Хорошо видны шестерни привода распредвалов топливных насосов высокого давления. Распредвалы тоже снимут для проверки степени износа кулачков, так как от этого зависит правильность подачи топлива в цилиндры дизеля…
Коленчатые валы сняты и уложены на специальные подставки. Их аккуратно оботрут, произведут замеры коренных и шатунных шеек. Если все в норме — вернут на место. Если нет — заменят другими.
Окончательная разборка дизеля. Выемка цилиндровых втулок, снятие всех трубопроводов, отсоединение блока дизеля от поддизельной рамы. Затем блок отправят в специальную моечную машину, где горячим моющим раствором отмоют до металла. Затем произведут линейные замеры блока, не покороблен ли он, соответствуют ли допускам все посадочные размеры втулок цилиндров и постелей подшипников. В последнее время блоки стали часто браковать. Что поделаешь — время берет свое. Если есть возможность, отправляют блоки в ремонт на крупные тепловозоремонтные заводы. Если нет — списывают.
Как вы уже поняли, сборка после ремонта происходит в порядке, обратном разборке.
Теперь небольшой рассказ о неполной разборке дизеля, без выемки его из тепловоза. Это более мелкий вид ремонта, при котором ремонтируются лишь отдельные части дизеля. На примере рассмотрим разборку дизеля 16ЧН26/26.На этом фото дизель в полностью собранном виде.
А здесь уже сняты топливные насосы высокого давления и штанги приводов впускных и выпускных клапанов.На этом фото хорошо видны пружины клапанов и ролики штанг приводов.
Здесь уже вынуты комлекты цилиндров (комлект — это поршень с шатуном, втулка цилидра и цилиндровая крышка с клапанами)
Если заглянуть внутрь, можно увидеть коленчатый вал, точнее, одну из его шатунных шеек.
Итак, тепловоз был разобран, затем собран. Теперь необходимо проверить качество его сборки, устранить недоделки, течи, выявить огрехи при сборке дизеля и электрической схемы, затем настроить параметры ДГУ. Для этого тепловоз подвергают реостатным испытаниям, для чего его электрическую силовую схему присоединяют к водяному нагрузочному реостату при помощи соединительных кабелей.На этом фото водяной реостат справа.
Кабели пропускают через специальное технологическое окно в корпусе тепловоза. Туда же подключают контрольный кабель для наблюдения за режимами и состянием работы электрической схемы тепловоза.
Пару слов о реостате. По сути дела, это гигантский кипятильник на 10 тонн воды, в который погружены металлические пластины, которые в свою очередь подключены к тяговому генератору тепловоза. А сам генератор отключается от тяговых двигателей и работает только на реостат. Таким образом, мы можем нагружать дизель-генератор тепловоза имитируя работу тяговых двигателей в различных режимах. То есть, стооя на месте мы как бы едем. Приэтом мы имеем возможность настраивать дизель-генератор тепловоза под полной нагрузкой, чего нам и нужно.
Вот вид реостата сверху. Видны положительные («плюсовые») и отрицательные («минусовые») пластины. ПРичем плюсовые пластины могут подниматься и опускаться отнсительно минусовых. Это сделано с целью изменения тока и напряжения тягового генератора тепловоза для имитации различных режимов езды тепловоза.
Итак, тепловоз присоединен к реостату, первичный запуск не выявил проблем с дизелем и со схемой (что бывает крайне редко, как правило, всегда проблемы находятся и иногда довольо серьезные). Проверяем работу всех систем под небольшой нагрузкой, попутно проводя обкатку и притирку подвижных соединений и подшипниковых узлов.Заглядываем в разные закоулки в поисках течей воды, масла и топлива. Часто течи обнаруживаются вот возле этого устройства — это водомасляный теплообменник, в котором охлаждается масло тепловоза.
Проверим также правильность сборки электрических аппаратов тепловоза. Поскольку их очень много, часто случаются ошибки при их сборке. Иногда поиск этих ошибок может затянуться надолго.
Теперь приступаем к реостатным испытаниям. Для начала регулируем обороты дизеля, для чего залезем вовнутрь регулятора частоты оборотов. Обороты регулируются настройкой вот этих электромагнитов(сигналы на них идут с контроллера машиниста), которые поочередно включаясь изменяют частоту вращения коленчатого вала дизеля. Как это происходит — описывать не буду, это достаточно долго.Могу только сказать, что каждой позиции контроллера машиниста должно соответствовать точно определенное количество оборотов и точно определенная мощность дизель-генераторной установки.Обороты контролируются при помощи штатного тахометра, кусочек которого виден на фото, но необходимая точность достигается путем контроля оборотов при помощи электронного тахометра, который подключается к тепловозу на время реостатных испытаний.
Обороты мы отрегулировали, теперь регулируем сопротивления, которые задают уровень необходимой мощности, выдаваемой тяговым генератором.
Проверяем точность настроек перед тем, как нагрузить генератор.
Нагружаем дизель-генератор и проверяем соответствие параметров при помощи контрольно — диагностической установки. На ней мы видим мощность, обороты, токи в обмотках электрических машин и аппаратов. Если видим несоответствия по параметрам, то лезем в схему тепловоза ищем причины и регулируем заново, после чего опять проверяем. И так до доведения параметров до правильных.
Итак, схема настроена. Но дизель еще нет. У него множество параметров: давление сгорания, угол опережения впрыска топлива, давление сжатия, температура выпускных газов и др. Все эти параметры также необходимо проверить и настроить в соответствии с заданными. Для этого мы проводим диагностику дизеля, для чего вешаем на него кучу разных датчиков. Сначала вибродатчики для определения момента впрыска топлива.
Теперь нужно определить давление сгорания в цилиндрах дизеля. Для этого мы открываем и продуваем индикаторный кран, который непосредственно связан с камерой сгорания цилиндра. Можете себе представить, с каким шумом, огнем, дымом и силой вырываются выхлопные газы из крана. Сейчас напротив него лучше не стоять, запросто можно получить ожог, а если работать без противошумных наушников, то повреждение слуха вам обеспечено.После продувки кран закрывается и на него наворачивается специальный датчик давления, сконструированный так, что может измерять давление внутри камеры сгорания до 140 кг/см при температуре 800-900 градусов Цельсия, а то и выше. Затем кран открывается для свободного доступа газов к датчику.
Вот так выглядит дизель, обвешанный датчиками диагностической установки. Еще для контроля за температурой выхлопных газов в специальные отверстия вставляются термопары. На ближнем плане видна локальная станция сбора, обработки и передачи данных на компьютер контрольно-диагностической установки.Хорошо видны датчики давления, навернутые на индикаторные краны. Дизель запущен, молотит на всю катушку, идет сбор данных о состоянии дизель-генераторной установки.
Так выглядит одно из меню программы диагностики. Прошу прощения, что это не скрин-шот, просто ноутбук побывал в стольких передрягах и столько пережил, что некоторые клавиши просто не работают и одной из неработающих и является клавиша Print Screen.Но поскольку информация с этой картинки не так важна, я думаю, что вы извините меня.
Вот еще одно меню программы диагностики с параметрами отдельно взятого цилиндра. Те цилиндры, которые не вписываются в параметры, подвергаются регулировкам: меняются неисправные насосы, форсунки, изменяется угол опережения подачи топлива, цикловая подача топливного насоса и пр. Затем вновь проводятся замеры и так далее до достижения требуемых параметров.
В недавние времена, когда диагностики еще не было, для замера давлений сгорания и давления сжатия по цилиндрам пользовались (да и сейчас часто пользуются) вот такой штукой — максиметром. Принцип тот же: на полной мощности открывают индикаторный кран, продувают, закрывают, затем накручивают на него максиметр снова открывают кран и меряют давление сгорания. Можете видеть, что шкала манометра имеет резерв до 160 очков. Замеры параметров с максиметром — это работа для мужиков с крепкими нервами и здоровьем. Представьте себе: дикий шум, грохот дизеля, вой турбин, пламя и дым выхлопных газов из индикаторного крана, жара под 80 градусов, а ты аккуратно наворачиваешь — сворачиваешь максиметр, фиксируешь показания манометра. Кстати, наконечник максиметра во время этой работы нагревается так, что от него можно запросто прикуривать.
Вот так выглядит бак реостата примерно в середине испытаний. Вода еще не закипела, но руку в нее лучше не совать, достаточно горячая.
Потом после реостатных испытаний тепловоз проходит еще и обкаточные, где проводится окончательная проверка всех систем.
Все, что здесь описано, не составляет и сотой части действительности. Более подробный отчет составил бы сотни фотографий с многостраничным их описанием. Поэтому не стОит даже и пытаться. На этому меня все.
Источник: www.yaplakal.com/
Итак, поехали. Будет 36 фото.Просьба, подборку не ломать, потом отвечу на вопросы, если будут.
Ремонт тепловозов по степени сложности (величине) зависит от их пробегов. Чем больше пробег, тем крупнее ремонт. Самый крупный ремонт — с выемкой дизель-генератора из тепловоза с последующей разборкой дизеля и генератора, ремонтом всех узлов и агрегатов, последующей сборкой, настройкой и регулировкой дизель-генераторной установки (реостатными испытаниями).Существует и более мелкий ремонт, когда дизель не вынимается полностью из тепловоза, а происходит его частичная разборка, то есть состояние дизеля таково, что нет необходимости разбирать его весь, а можно разобрать и отремонтировать только те его части, которые нуждаются в ремонте. Об этом я тоже здесь расскажу
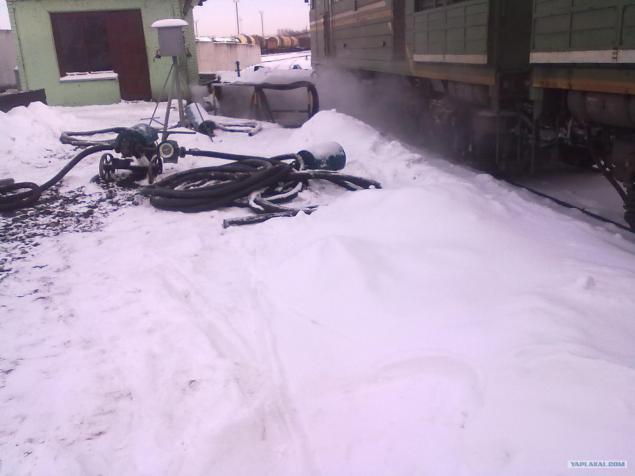
Перед разборкой из тепловоза сливаются все жидкости: вода, топливо, масло, из бункеров высыпается песок. Затем топливный бак промывается и пропаривается.На этом фото происходит пропарка топливного бака позле разэкипировки тепловоза.
Затем тепловоз ставится в цех. Происходит разборка дизеля, он рассоединяется со всеми трубопроводами и отсоединяется от тепловозной рамы.На этом фото крыша уже демонтирована для выемки дизеля.
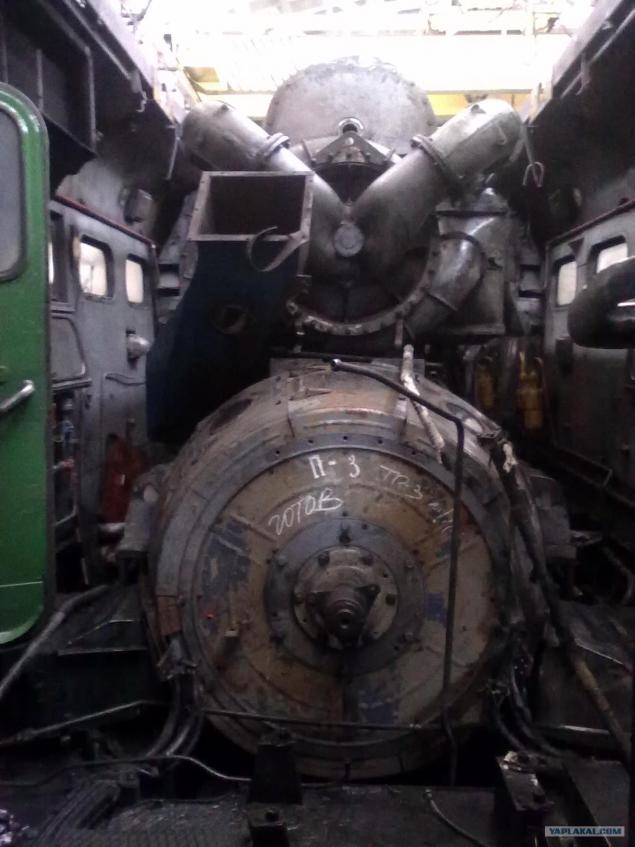
Сняты передний редуктор и воздушный компрессор.Хорошо виден двухмашинный агрегат, который тоже будет демонтирован.
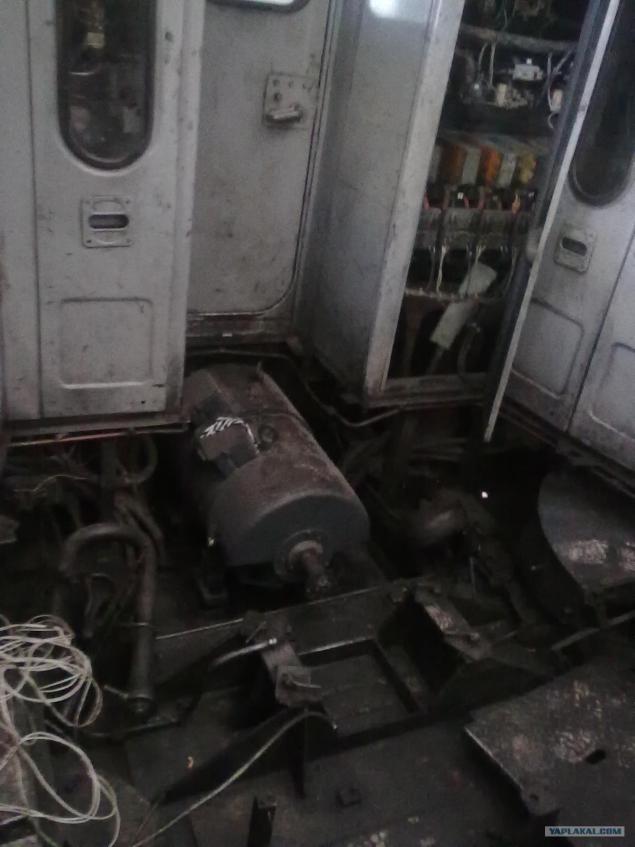
Это фото приведено для сравнения того что было с тем, что стало после разборки Сравните с верхним фото. Теперь дизель можно снимать с тепловоза. Вынимают его 30-тонным краном.
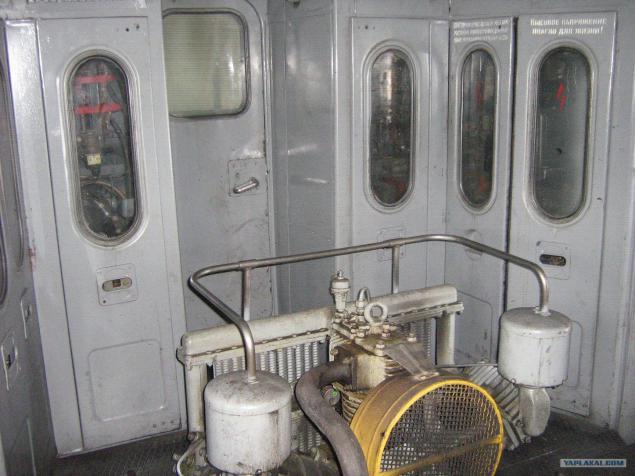
Снято все электрооборудование. Остались одни кабели, да и они скоро будут сняты.
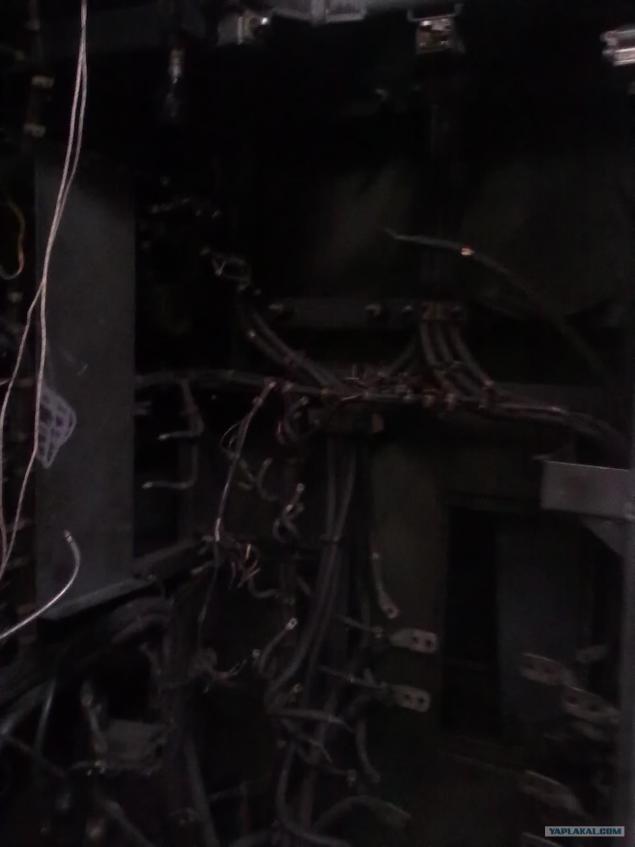
Затем тепловоз ставится на домкраты. Отсоединяются кабели тяговых электродвигателей, отсоединяются опорно-возвращающие устройства тележек, затем тепловоз поднимают на домкратах и тележки (их на каждой секции две, на каждой по три тяговых двигателя) выкатываются из-под тепловоза. Теперь можно заниматься ремонтом трубопроводов, и опорных устройств тепловоза.
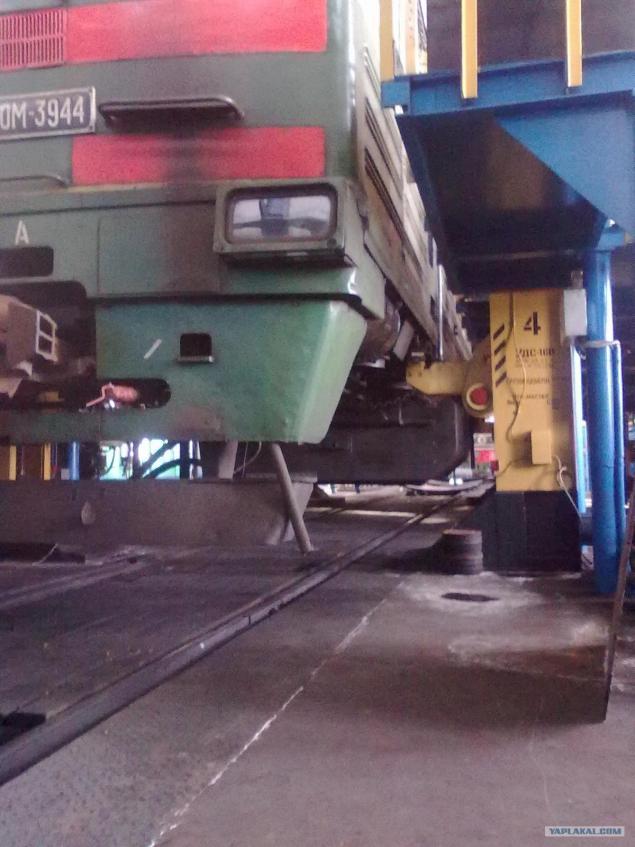
Еще фото, поближе.
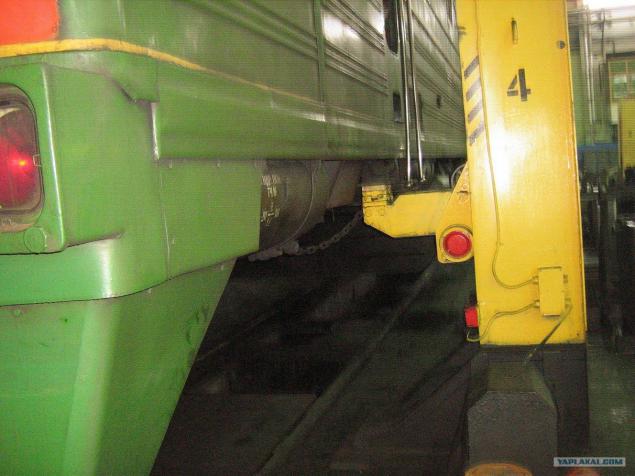
Потом тяговые двигатели отсоединяются от тележек. Затем и тележка и тяговые двигатели тоже полностью разбираются и ремонтируются. На этм фото тяговые двигатели после ремонта и проверки подготовлены для установки обратно на тележку.
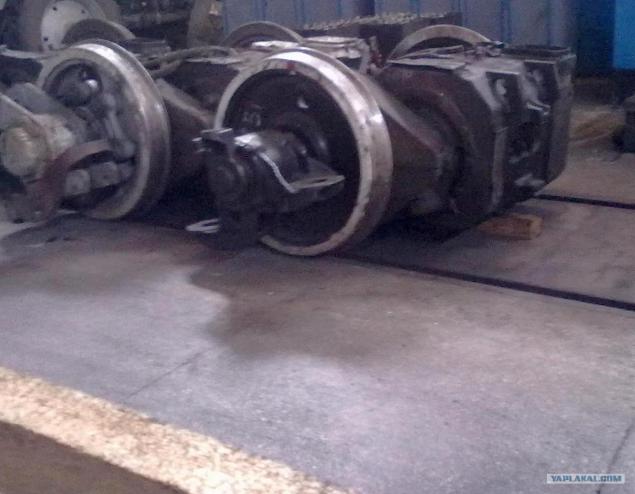
Иногда возникает необходимость ремонта только одного тягового двигателя. Чтобы не поднимать тепловоз на домкраты и не разбирать полностью тележку, придумано вот такое устройство, называется скатоопускной механизм. Тепловоз подгоняется на скатоопускник, отсоединяются кабели и крепеж только одного тягача, затем он опускается вместе с платформой скатоопускника и выезжает из-под тепловоза, который остается стоять. Таким же образом тяговый двигатель ставят на место.
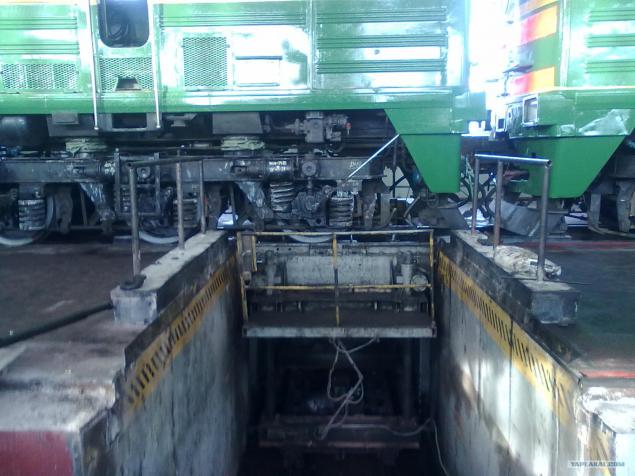
А это станок для обточки бандажей колесных пар. Обычно колесная пара отсоединяется от тягового двигателя и в случае необходимости обтачивается на специальном станке. Но иногда бывает необходимо обточить бандаж не разбирая тягач(ну, наехал тепловоз на какое-то препятствие и получилась выбоина на колесе). Тогда тепловоз подгоняют на такой вот станок, зажимают колесную пару в специальном суппорте, чуть приподнимают и специальной фасонной фрезой обтачивают бандаж, постепенно вращая колесную пару.
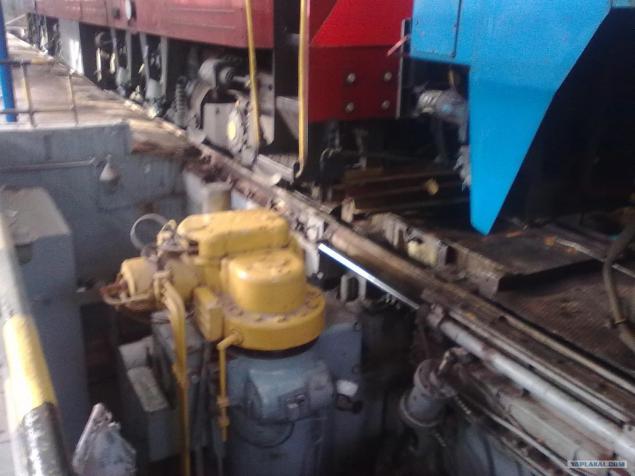
Вернемся к дизелю. Его уже наполовину разобрали. Сняли тяговый генератор, турбины и нагнетатель наддувочного воздуха вместе с воздухоохладителями.
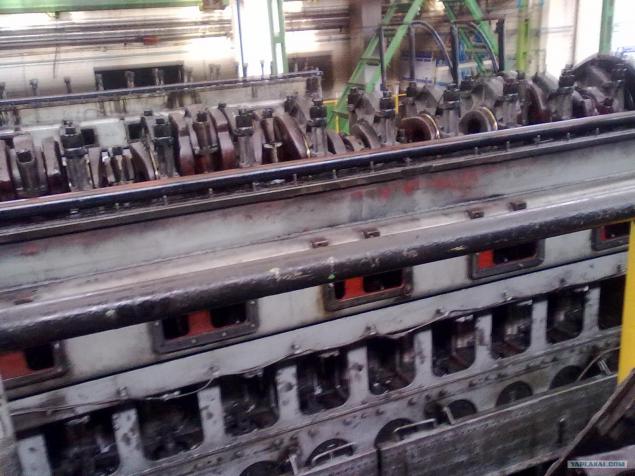
Турбины и нагнетатель отвезли для дальнейшей разборки и ремонта на участок ремонта агрегатов наддува. Здесь их разберут, очистят, отбалансируют и соберуют заново.
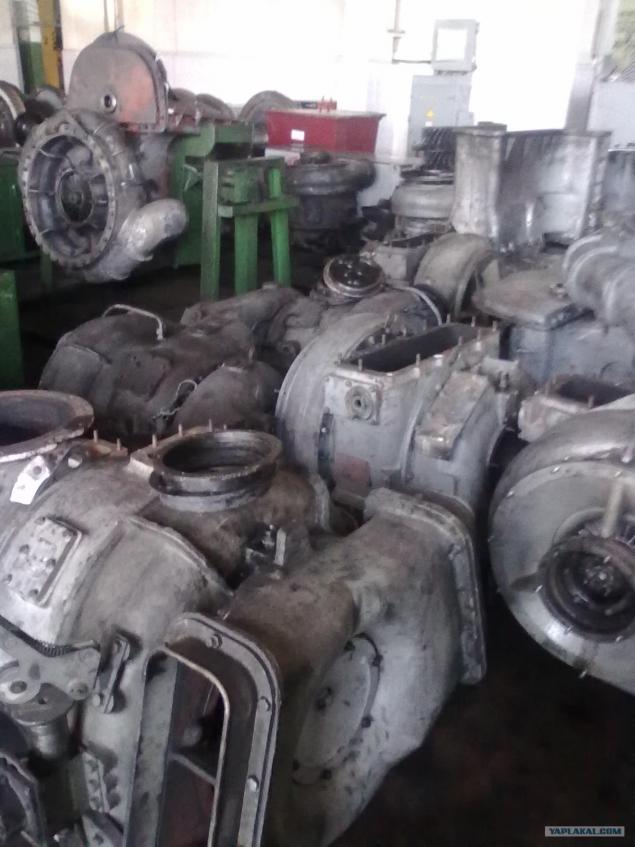
Теперь снимаем верхний коленчатый вал (на этом дизеле их два: верхний и нижний). Хорошо видны шестерни привода распредвалов топливных насосов высокого давления. Распредвалы тоже снимут для проверки степени износа кулачков, так как от этого зависит правильность подачи топлива в цилиндры дизеля…
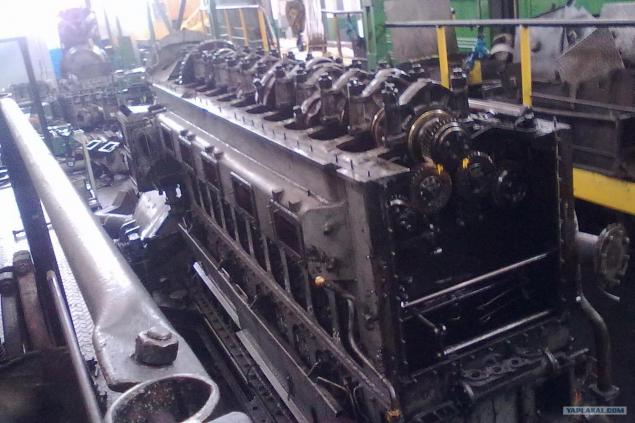
Коленчатые валы сняты и уложены на специальные подставки. Их аккуратно оботрут, произведут замеры коренных и шатунных шеек. Если все в норме — вернут на место. Если нет — заменят другими.
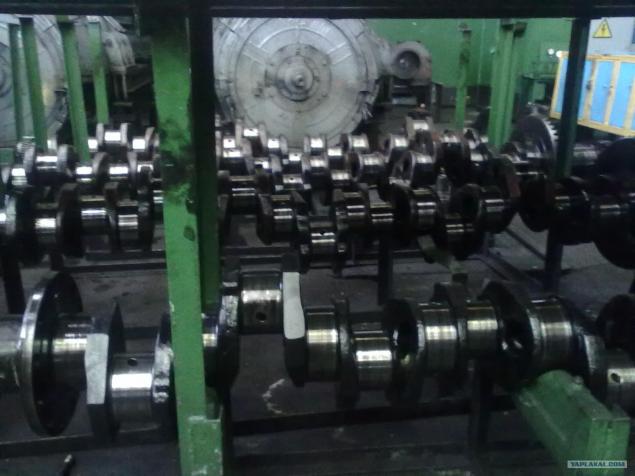
Окончательная разборка дизеля. Выемка цилиндровых втулок, снятие всех трубопроводов, отсоединение блока дизеля от поддизельной рамы. Затем блок отправят в специальную моечную машину, где горячим моющим раствором отмоют до металла. Затем произведут линейные замеры блока, не покороблен ли он, соответствуют ли допускам все посадочные размеры втулок цилиндров и постелей подшипников. В последнее время блоки стали часто браковать. Что поделаешь — время берет свое. Если есть возможность, отправляют блоки в ремонт на крупные тепловозоремонтные заводы. Если нет — списывают.

Как вы уже поняли, сборка после ремонта происходит в порядке, обратном разборке.
Теперь небольшой рассказ о неполной разборке дизеля, без выемки его из тепловоза. Это более мелкий вид ремонта, при котором ремонтируются лишь отдельные части дизеля. На примере рассмотрим разборку дизеля 16ЧН26/26.На этом фото дизель в полностью собранном виде.
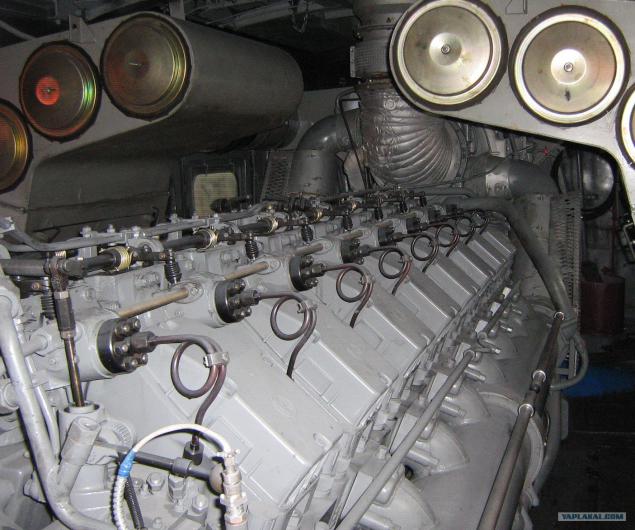
А здесь уже сняты топливные насосы высокого давления и штанги приводов впускных и выпускных клапанов.На этом фото хорошо видны пружины клапанов и ролики штанг приводов.
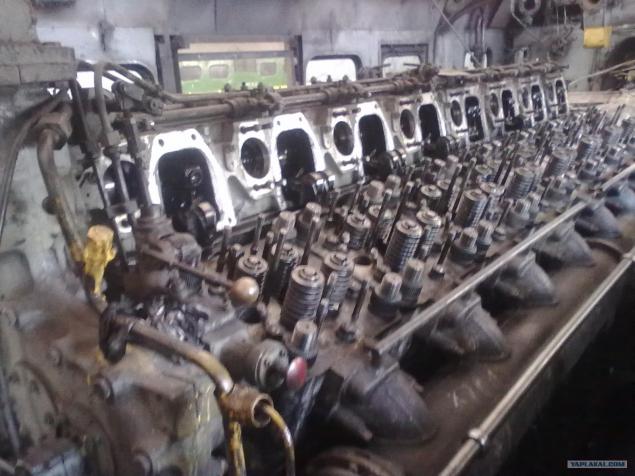
Здесь уже вынуты комлекты цилиндров (комлект — это поршень с шатуном, втулка цилидра и цилиндровая крышка с клапанами)
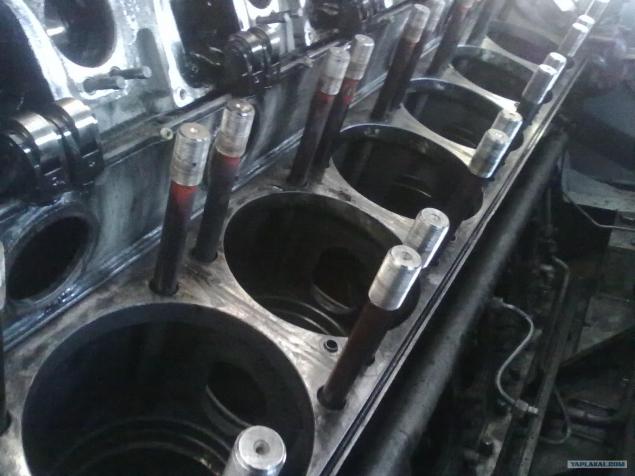
Если заглянуть внутрь, можно увидеть коленчатый вал, точнее, одну из его шатунных шеек.
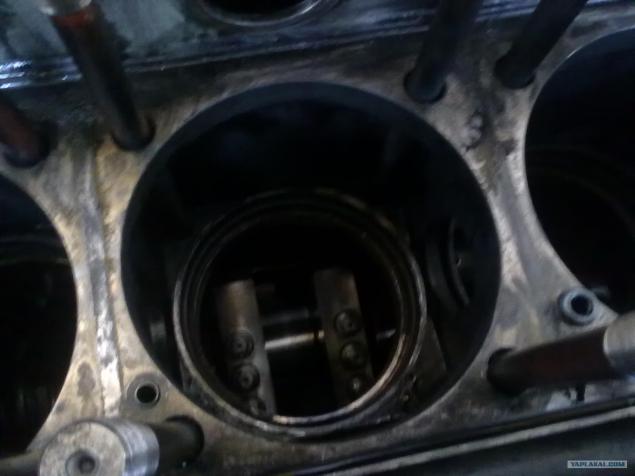
Итак, тепловоз был разобран, затем собран. Теперь необходимо проверить качество его сборки, устранить недоделки, течи, выявить огрехи при сборке дизеля и электрической схемы, затем настроить параметры ДГУ. Для этого тепловоз подвергают реостатным испытаниям, для чего его электрическую силовую схему присоединяют к водяному нагрузочному реостату при помощи соединительных кабелей.На этом фото водяной реостат справа.
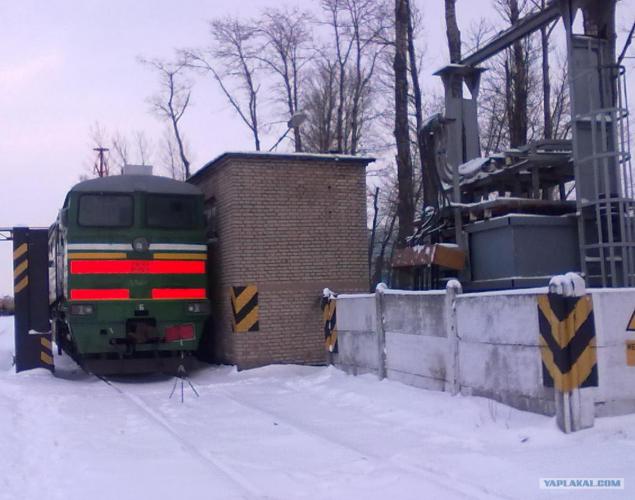
Кабели пропускают через специальное технологическое окно в корпусе тепловоза. Туда же подключают контрольный кабель для наблюдения за режимами и состянием работы электрической схемы тепловоза.
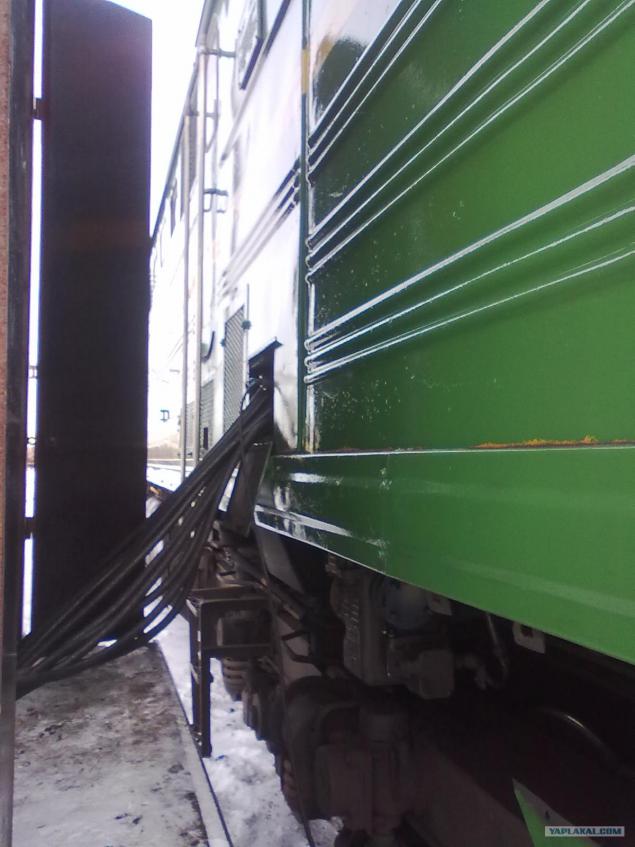
Пару слов о реостате. По сути дела, это гигантский кипятильник на 10 тонн воды, в который погружены металлические пластины, которые в свою очередь подключены к тяговому генератору тепловоза. А сам генератор отключается от тяговых двигателей и работает только на реостат. Таким образом, мы можем нагружать дизель-генератор тепловоза имитируя работу тяговых двигателей в различных режимах. То есть, стооя на месте мы как бы едем. Приэтом мы имеем возможность настраивать дизель-генератор тепловоза под полной нагрузкой, чего нам и нужно.
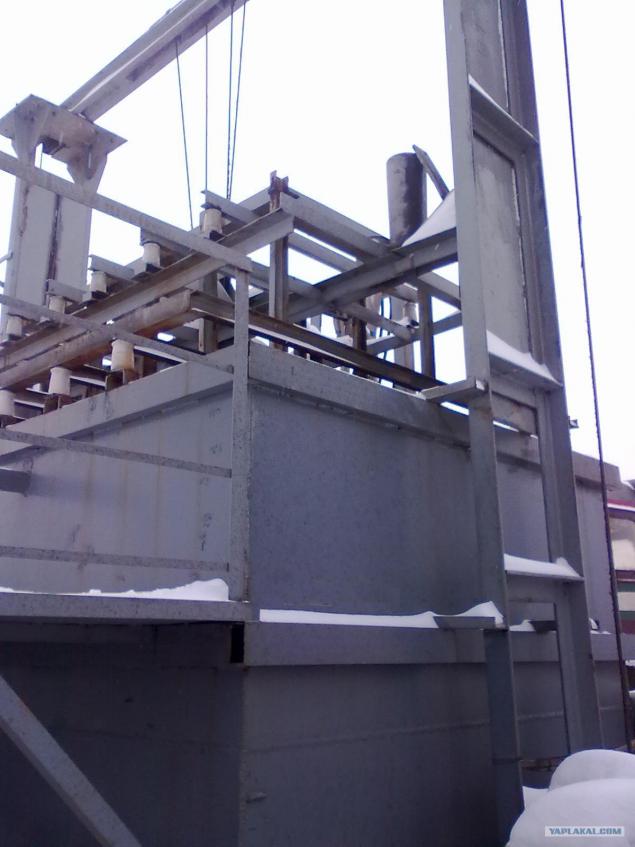
Вот вид реостата сверху. Видны положительные («плюсовые») и отрицательные («минусовые») пластины. ПРичем плюсовые пластины могут подниматься и опускаться отнсительно минусовых. Это сделано с целью изменения тока и напряжения тягового генератора тепловоза для имитации различных режимов езды тепловоза.

Итак, тепловоз присоединен к реостату, первичный запуск не выявил проблем с дизелем и со схемой (что бывает крайне редко, как правило, всегда проблемы находятся и иногда довольо серьезные). Проверяем работу всех систем под небольшой нагрузкой, попутно проводя обкатку и притирку подвижных соединений и подшипниковых узлов.Заглядываем в разные закоулки в поисках течей воды, масла и топлива. Часто течи обнаруживаются вот возле этого устройства — это водомасляный теплообменник, в котором охлаждается масло тепловоза.
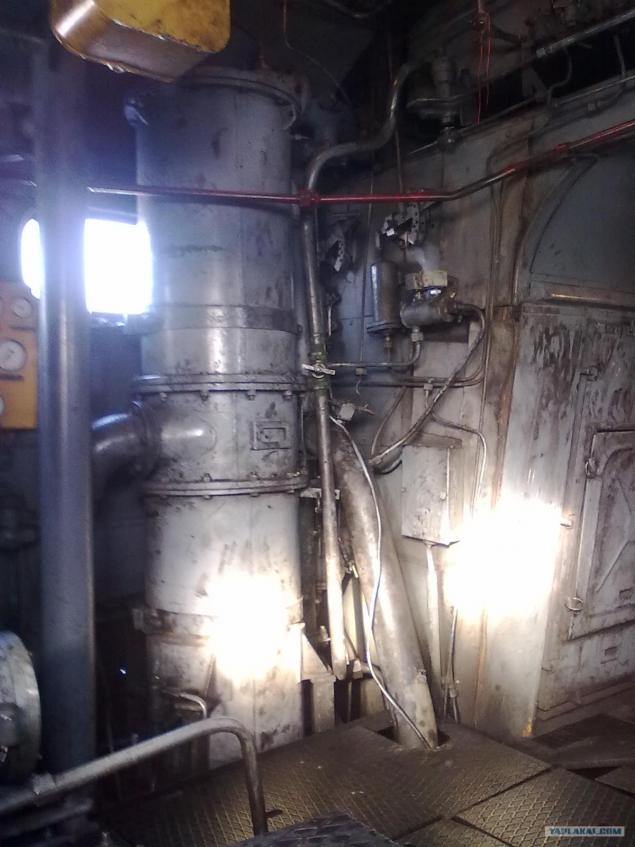
Проверим также правильность сборки электрических аппаратов тепловоза. Поскольку их очень много, часто случаются ошибки при их сборке. Иногда поиск этих ошибок может затянуться надолго.
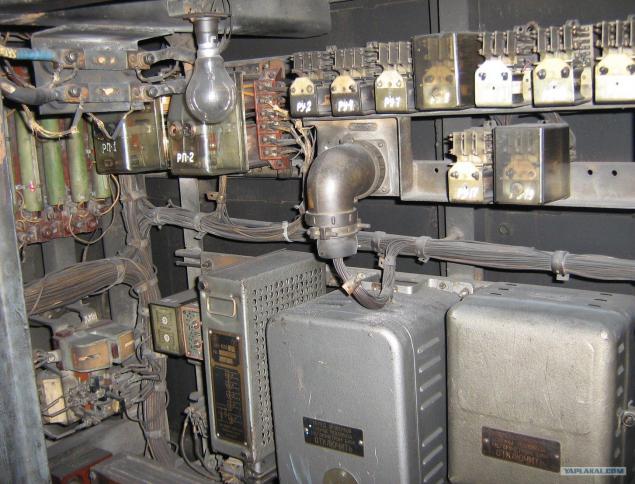
Теперь приступаем к реостатным испытаниям. Для начала регулируем обороты дизеля, для чего залезем вовнутрь регулятора частоты оборотов. Обороты регулируются настройкой вот этих электромагнитов(сигналы на них идут с контроллера машиниста), которые поочередно включаясь изменяют частоту вращения коленчатого вала дизеля. Как это происходит — описывать не буду, это достаточно долго.Могу только сказать, что каждой позиции контроллера машиниста должно соответствовать точно определенное количество оборотов и точно определенная мощность дизель-генераторной установки.Обороты контролируются при помощи штатного тахометра, кусочек которого виден на фото, но необходимая точность достигается путем контроля оборотов при помощи электронного тахометра, который подключается к тепловозу на время реостатных испытаний.
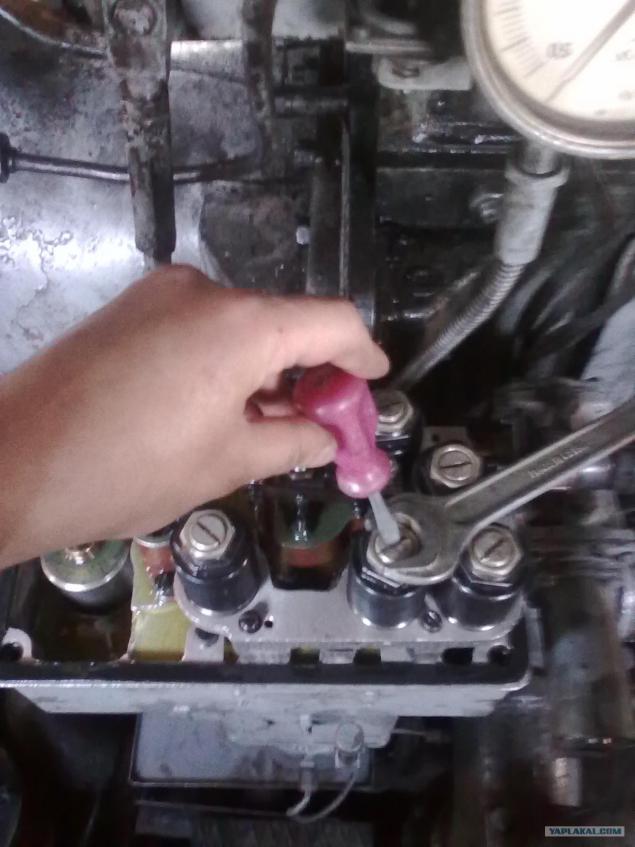
Обороты мы отрегулировали, теперь регулируем сопротивления, которые задают уровень необходимой мощности, выдаваемой тяговым генератором.
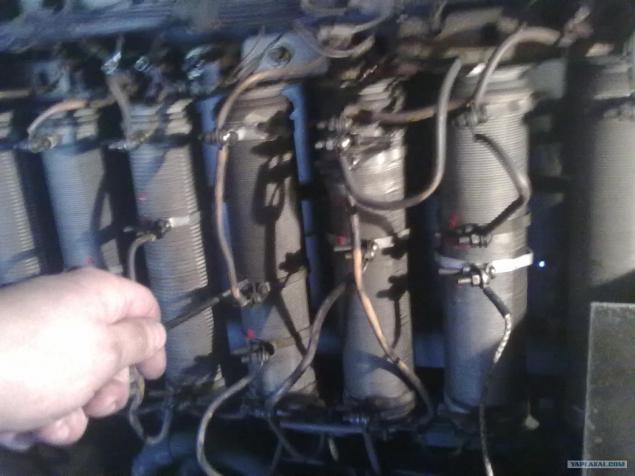
Проверяем точность настроек перед тем, как нагрузить генератор.
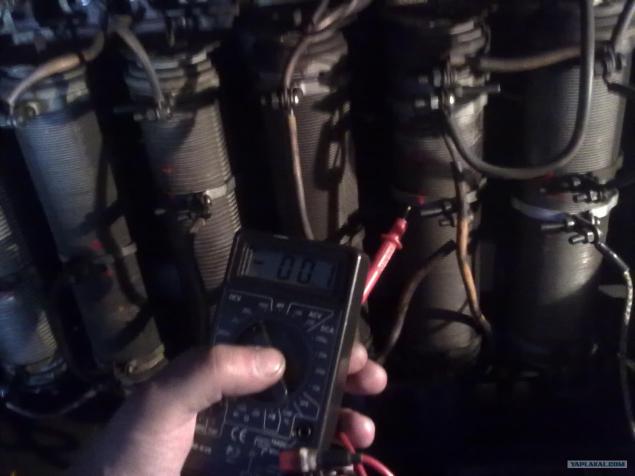
Нагружаем дизель-генератор и проверяем соответствие параметров при помощи контрольно — диагностической установки. На ней мы видим мощность, обороты, токи в обмотках электрических машин и аппаратов. Если видим несоответствия по параметрам, то лезем в схему тепловоза ищем причины и регулируем заново, после чего опять проверяем. И так до доведения параметров до правильных.
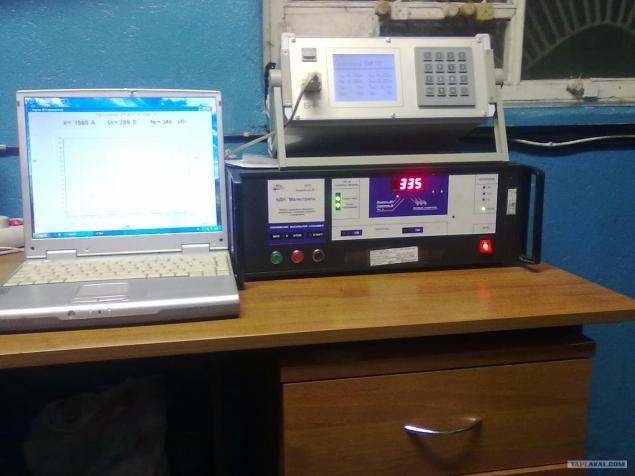
Итак, схема настроена. Но дизель еще нет. У него множество параметров: давление сгорания, угол опережения впрыска топлива, давление сжатия, температура выпускных газов и др. Все эти параметры также необходимо проверить и настроить в соответствии с заданными. Для этого мы проводим диагностику дизеля, для чего вешаем на него кучу разных датчиков. Сначала вибродатчики для определения момента впрыска топлива.
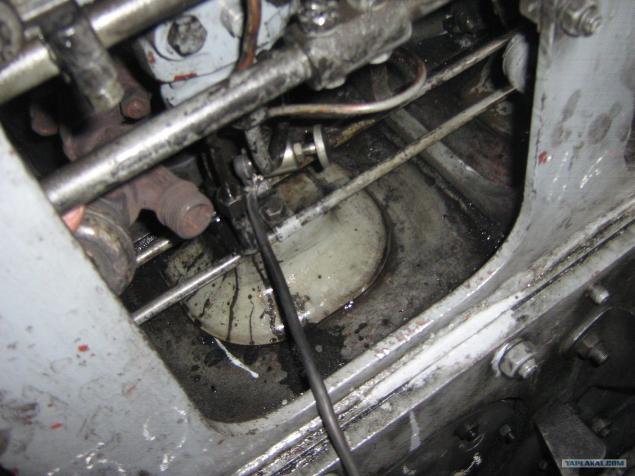
Теперь нужно определить давление сгорания в цилиндрах дизеля. Для этого мы открываем и продуваем индикаторный кран, который непосредственно связан с камерой сгорания цилиндра. Можете себе представить, с каким шумом, огнем, дымом и силой вырываются выхлопные газы из крана. Сейчас напротив него лучше не стоять, запросто можно получить ожог, а если работать без противошумных наушников, то повреждение слуха вам обеспечено.После продувки кран закрывается и на него наворачивается специальный датчик давления, сконструированный так, что может измерять давление внутри камеры сгорания до 140 кг/см при температуре 800-900 градусов Цельсия, а то и выше. Затем кран открывается для свободного доступа газов к датчику.
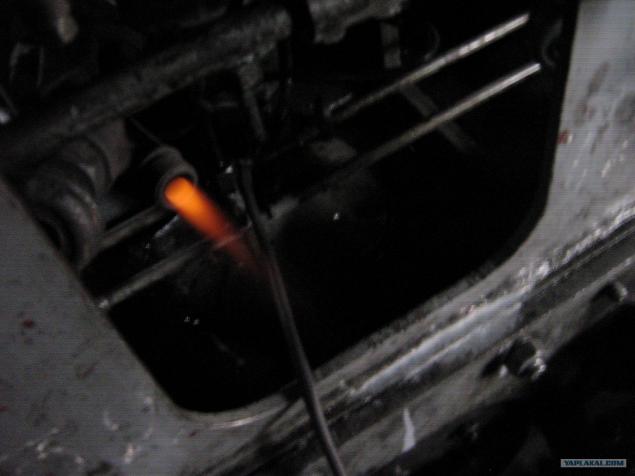
Вот так выглядит дизель, обвешанный датчиками диагностической установки. Еще для контроля за температурой выхлопных газов в специальные отверстия вставляются термопары. На ближнем плане видна локальная станция сбора, обработки и передачи данных на компьютер контрольно-диагностической установки.Хорошо видны датчики давления, навернутые на индикаторные краны. Дизель запущен, молотит на всю катушку, идет сбор данных о состоянии дизель-генераторной установки.
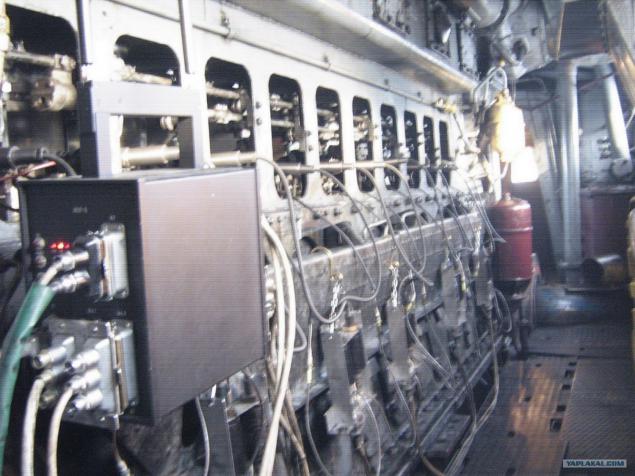
Так выглядит одно из меню программы диагностики. Прошу прощения, что это не скрин-шот, просто ноутбук побывал в стольких передрягах и столько пережил, что некоторые клавиши просто не работают и одной из неработающих и является клавиша Print Screen.Но поскольку информация с этой картинки не так важна, я думаю, что вы извините меня.
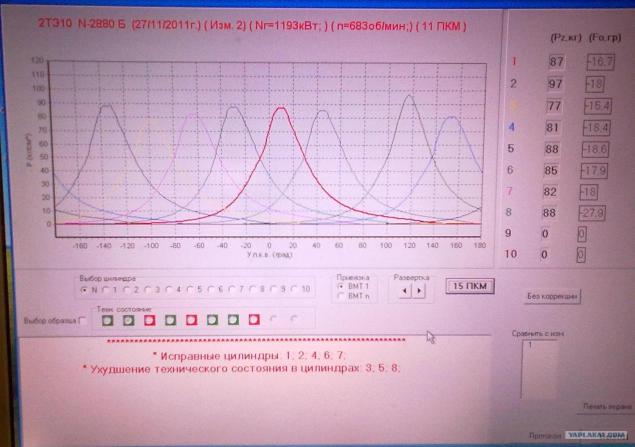
Вот еще одно меню программы диагностики с параметрами отдельно взятого цилиндра. Те цилиндры, которые не вписываются в параметры, подвергаются регулировкам: меняются неисправные насосы, форсунки, изменяется угол опережения подачи топлива, цикловая подача топливного насоса и пр. Затем вновь проводятся замеры и так далее до достижения требуемых параметров.
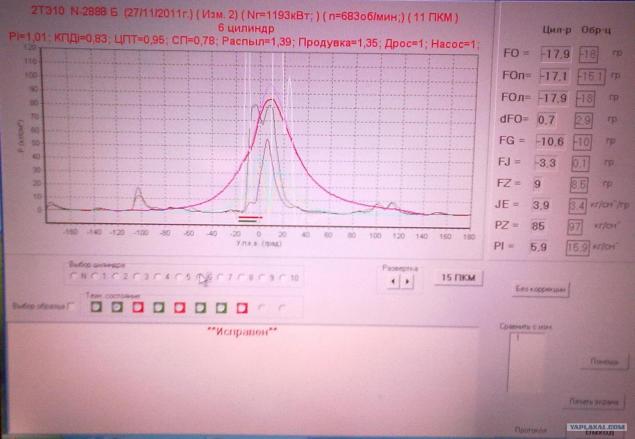
В недавние времена, когда диагностики еще не было, для замера давлений сгорания и давления сжатия по цилиндрам пользовались (да и сейчас часто пользуются) вот такой штукой — максиметром. Принцип тот же: на полной мощности открывают индикаторный кран, продувают, закрывают, затем накручивают на него максиметр снова открывают кран и меряют давление сгорания. Можете видеть, что шкала манометра имеет резерв до 160 очков. Замеры параметров с максиметром — это работа для мужиков с крепкими нервами и здоровьем. Представьте себе: дикий шум, грохот дизеля, вой турбин, пламя и дым выхлопных газов из индикаторного крана, жара под 80 градусов, а ты аккуратно наворачиваешь — сворачиваешь максиметр, фиксируешь показания манометра. Кстати, наконечник максиметра во время этой работы нагревается так, что от него можно запросто прикуривать.
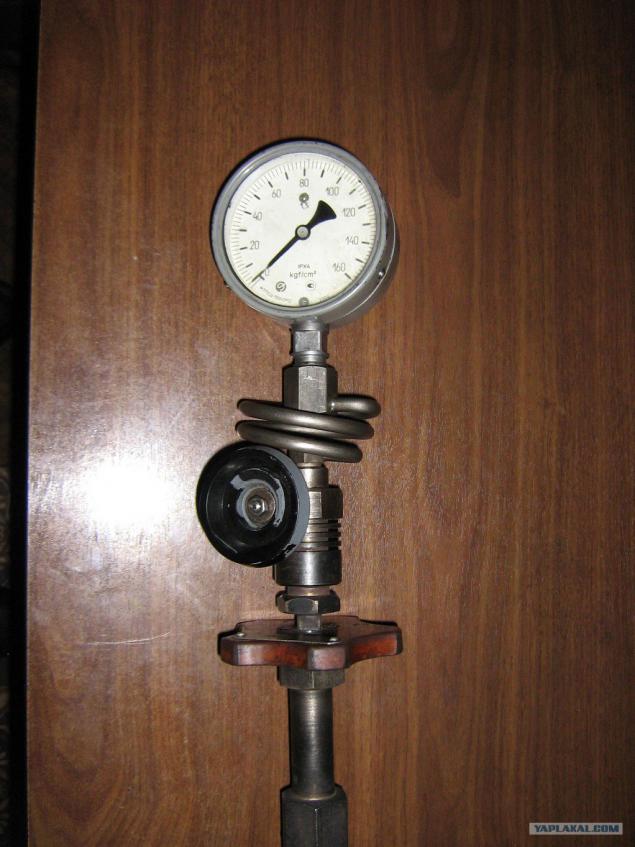
Вот так выглядит бак реостата примерно в середине испытаний. Вода еще не закипела, но руку в нее лучше не совать, достаточно горячая.
Потом после реостатных испытаний тепловоз проходит еще и обкаточные, где проводится окончательная проверка всех систем.
Все, что здесь описано, не составляет и сотой части действительности. Более подробный отчет составил бы сотни фотографий с многостраничным их описанием. Поэтому не стОит даже и пытаться. На этому меня все.
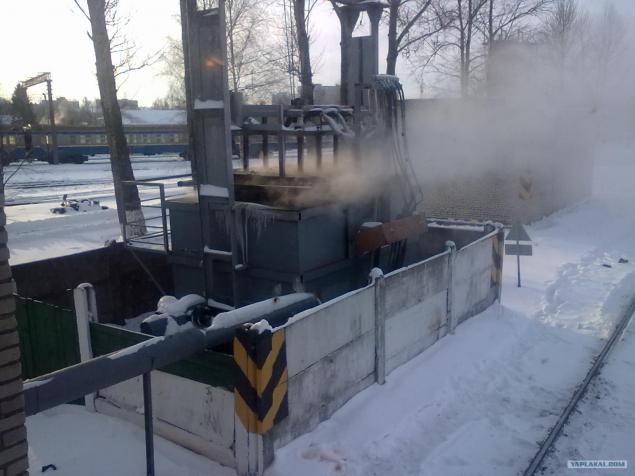
Источник: www.yaplakal.com/
Портал БАШНЯ. Копирование, Перепечатка возможна при указании активной ссылки на данную страницу.