1066
0.2
2015-02-23
ЛиАЗ - Ликинский Автобусный Завод
69 фото © dalnoboi-russia
Представляем вашему вниманию фоторепортаж с Ликинского автобусного завода. Устраивайтесь удобней, фотографий будет много.
1. Наша экскурсия по заводу начинается с прессово-заготовительного цеха.
2. Здесь происходит продольный и поперечный раскрой рулонной стали, а так же все необходимые заготовки для холодной штамповки деталей будущих автобусов.
3. Линия «Хальброн».
4. В холодноштамповочном производстве изготавливают облицовочные панели кузова, а также детали и узлы элементов каркаса кузова.
5. Участок лазерной резки с применением комплекса «Trumpf TL — 3030».
6. С помощью хитрого крана оператор подаёт металлический лист в рабочую зону станка.
7. Нам удалось заглянуть за защитный экран и подсмотреть, как луч лазера на огромной скорости прожигает правильный профиль будущей заготовки.
8. Спустя некоторое время, станок выгружает готовые детали.
9. Но это лишь начало долгого процесса.
10. Чуть позже, с помощью пресса, им придадут нужную форму
11. Готовые детали ждут отправки на следующие этапы производства.
12. Рабочий процесс.
13. Изготовление, змеевика — испарителя, воздушной системы. Позже увидим, как деталь выглядит на готовом автобусе.
14. Теперь проследуем в цех сварочно-кузовного производства. На фотографии — линия сборки-сварки крыши SCHLATTER. Предварительно рабочие набирают на стапеле элементы будущей крыши.
15. SCHLATTER за работой.
16. Следуем по нитке конвейера и мы. Шаг за шагом, элементы автобуса приобретают всё новые и новые детали.
17. Собирается передняя панель автобуса. Сварщик за работой.
18. Наконец, настаёт время, когда на конвейере собирают в единое целое все элементы каркаса автобуса. Передняя часть – на фото.
19. Так называемая рама – нижняя, несущая часть кузова автобуса.
20. На стапеле, соблюдая строгую геометрию кузова, все детали собирают в единое целое
21. Оператор.
22. Сварка кузова на стапеле. Теперь, при желании, можно рассмотреть силуэт будущего автобуса.
23. Дальше, на конвейере, готовую раму обшивают листами металла.
24. Для того чтобы борта автобуса были абсолютно ровные, на ЛиАЗе применяют уникальную технологию. Перед сваркой, лист металла нагревают до температуры 90 градусов по Цельсию. Он увеличивается в размерах и лишь потом, его натягивают на раму.
25. Заключительные штрихи кузовного производства.
26. Обратите внимание, две части, сочленённого автобуса поступают на катафорезную обработку кузова.
27. Аналогов такого процесса для кузовов таких габаритов в России, других странах СНГ и странах ближнего зарубежья нет
28. Командует процессом хрупкая девушка.
29. Кузова поочерёдно окунают в несколько огромных ванн.
30. В своё время завод стал первым предприятием в России, применившим полную антикоррозионную обработку кузовов методом катафореза. Суть этого метода электролитического окрашивания состоит в том, что изделие, помещённое в катафорезную ванну, подвергается воздействию электрического поля. В результате этого специальная краска на водной основе осаждается на всё изделие целиком, не пропуская даже труднодоступных уголков. Сцепление эпоксидного слоя с металлом чрезвычайно прочно, а получившееся покрытие устойчиво к самым агрессивным погодным условиям.
30. В своё время завод стал первым предприятием в России, применившим полную антикоррозионную обработку кузовов методом катафореза. Суть этого метода электролитического окрашивания состоит в том, что изделие, помещённое в катафорезную ванну, подвергается воздействию электрического поля. В результате этого специальная краска на водной основе осаждается на всё изделие целиком, не пропуская даже труднодоступных уголков. Сцепление эпоксидного слоя с металлом чрезвычайно прочно, а получившееся покрытие устойчиво к самым агрессивным погодным условиям.
32. Для меня было откровением то, что крыша автобуса, на сто процентов покрыта пластиковым листом.
33. На ЛиАЗе утверждают, что эта технология на порядок практичней и долговечней.
34. На предприятии постоянно трудятся около полторы тысячи рабочих, при средней зарплате в 35 тысяч рублей.
35. На данный момент, февраль 2012 г., каждую смену за ворота завода выходит 10 новеньких автобусов.
36. Но самый вал по заказам на ЛиАЗе приходится на конец года, т.к. основные заказчики предприятия бюджетные организации. В такие моменты выход автобусов с конвейера резко увеличивается. Предприятие набирает временных рабочих и поднимает зарплаты.
37. Кузова являются предметом законной гордости завода.
38. ЛиАЗ гарантирует, что кузова его автобусов прослужат не менее 12 лет до сквозной коррозии.
39. Поделись улыбкой своей!
40. Заключительный этап перед отправкой кузова окраску.
41. Дружба.
42. Выплывают расписные.
43. Настало время взяться за дело мастерам оконных дел.
44. Прижимы.
45. Сказать, что работа буквально горит в руках мастеров, будет недостаточно — это надо увидеть собственными глазами.
46. Размеры предприятия впечатляют. Ветка конвейера плывет по двум этажам одновременно
47. Настало время спуститься к заключительной линии сборки автобусов. Каждые 45 мин на конвейере устанавливают мосты, каждые 90 двигатель.
48. По желанию заказчика машины комплектуются мостами фирм ZF, Raba или отечественными КААЗ.
49. В данном случае, как видно на фото, на автобус установлен ведущий мост немецкого производителя — фирмы ZF.
50. Выбор двигателя и коробки так же зависит от желания заказчика. Гамма агрегатов широка, от отечественных ЯМЗ и КАМАЗ, до лучших импортных образцов фирм MAN, Caterpillar, Cummins. Коробки скоростей Voith, ZF.
52. Далее наступает не менее интересный момент стыковки двух половинок сочленённого автобуса.
53. Как известно, ЛиАЗ один из первых заводов, кто наладил выпуск в России автобусов подобной конструкции.
54. Именно с началом серийного производства автобуса ЛиАЗ-6212, с наших улиц стали пропадать венгерские «гармошки» от Икаруса.
55. Гидроцилиндры в узле сочленения снабжены электронными мозгами, и теперь, чтобы исключить занос прицепа и жёсткие удары в крайних положениях, цилиндры меняют степень демпфирования в зависимости от угловой скорости поворота.
56. На ЛиАЗе применена принципиально новая схема — ведущие колёса на сочленённых автобусах находятся на прицепе. Именно он толкает автобус. Поэтому, при опасности складывания на скользком покрытии, цилиндры механизма блокируются.
57. Механизм сочленения стоит порядка 1 млн. рублей. Из них, сам механизм 700 тыс. и ещё 300 тыс. так называемая «гармошка».
58. Двери обыкновенные.
59.И не дай Бог, «на всякий пожарный».
60. Основные заказчики ЛиАЗа крупные автохозяйства в городах-миллионниках.
61. Серия автобусов с жёлто — оранжевой окраской предназначена для новой программы Правительства Москвы. Яркие автобусы будут ходить по выделенным полосам для движения пассажирского транспорта.
62.
63. Отладка и тестирование электроники.
64. Заправка автобусов техническими жидкостями. В данном случае, в систему кондиционирования автобуса заправляют хладагент
65. Рабочее место водителя автобуса. На мой взгляд, все сделано на уровне.
66. Мне удалость стать первым пассажиром новенького автобуса. Не удивляйтесь отсутствию сидений в салоне. Таков заказ Мосгортранса, видимо срок службы сидений дольше, чем срок службы самого автобуса.
67. Но прежде чем покинуть территорию завода автобус попадает на линию независимого контроля. Это специальная методика аудита автомобиля «CSA», выполнена на базе зарубежных стандартов, её цель дать независимую оценку качества автомобиля «с позиции
68. И лишь потом, автобус отправится к потребителю, и к своим пассажирам.
69… За организацию и проведение экскурсии, огромное спасибо директору завода ЛиАЗ Казакову Александру Михайловичу, а так же директору департамента массовых коммуникаций ООО «Русские Автобусы – Группа ГАЗ» Ворониной Элле Александровне, и лично PR менеджеру Фефеловой Ольге Андреевне.
Добавлено в [mergetime]1328513105[/mergetime]
Отсюда sdelanounas.ru/blogs/13510/#cut
Источник: www.yaplakal.com/
Представляем вашему вниманию фоторепортаж с Ликинского автобусного завода. Устраивайтесь удобней, фотографий будет много.
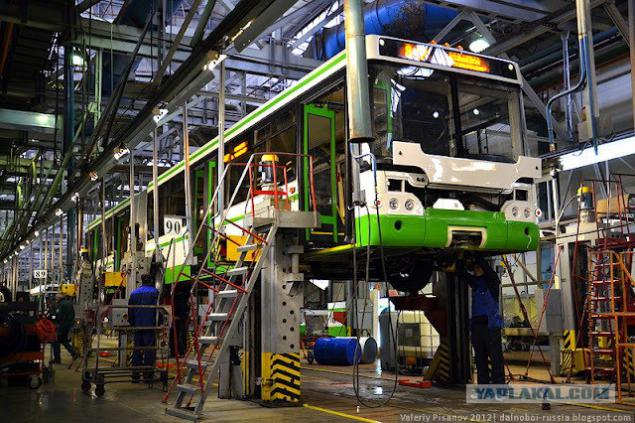
1. Наша экскурсия по заводу начинается с прессово-заготовительного цеха.
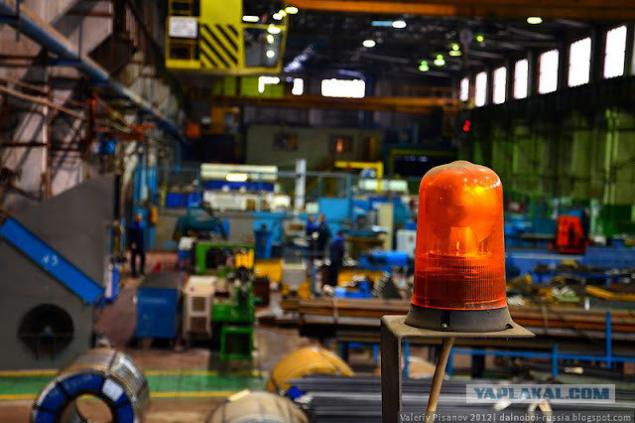
2. Здесь происходит продольный и поперечный раскрой рулонной стали, а так же все необходимые заготовки для холодной штамповки деталей будущих автобусов.
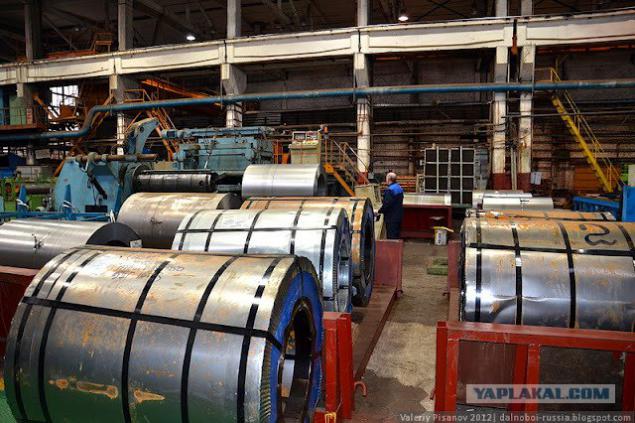
3. Линия «Хальброн».
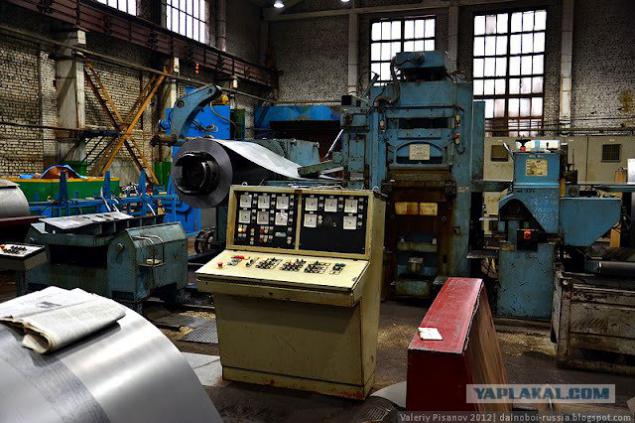
4. В холодноштамповочном производстве изготавливают облицовочные панели кузова, а также детали и узлы элементов каркаса кузова.
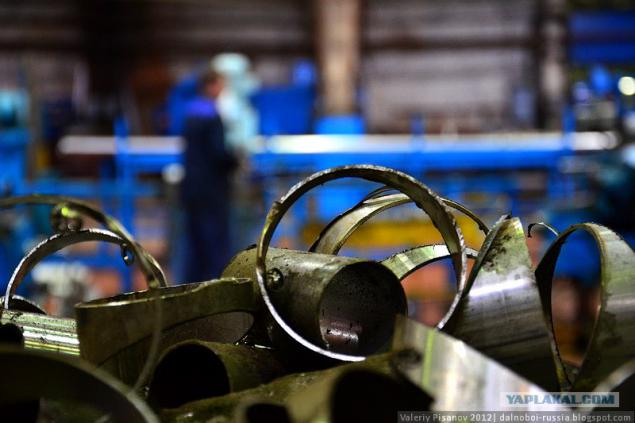
5. Участок лазерной резки с применением комплекса «Trumpf TL — 3030».
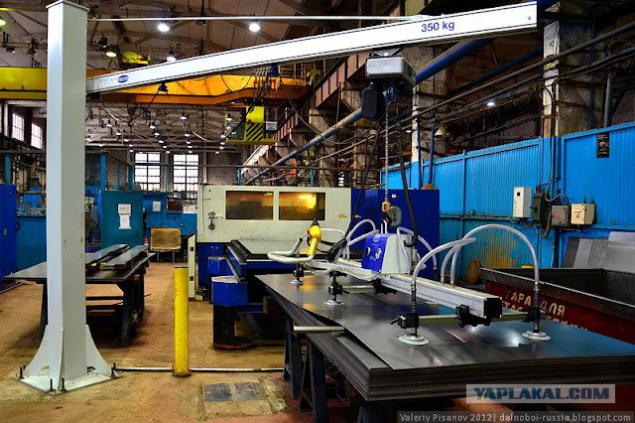
6. С помощью хитрого крана оператор подаёт металлический лист в рабочую зону станка.
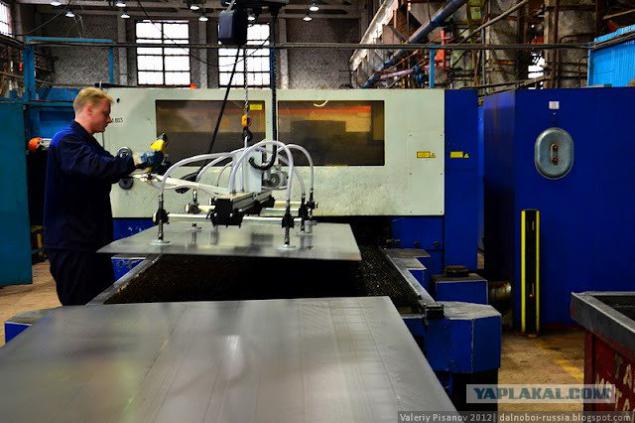
7. Нам удалось заглянуть за защитный экран и подсмотреть, как луч лазера на огромной скорости прожигает правильный профиль будущей заготовки.
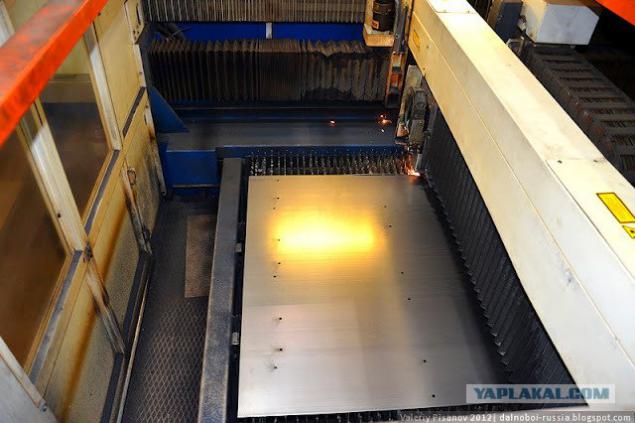
8. Спустя некоторое время, станок выгружает готовые детали.
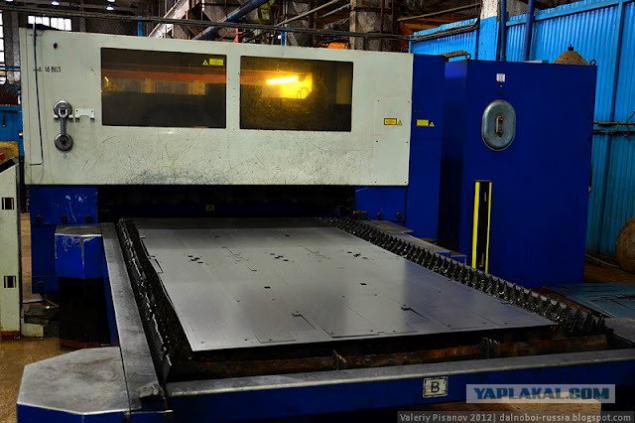
9. Но это лишь начало долгого процесса.
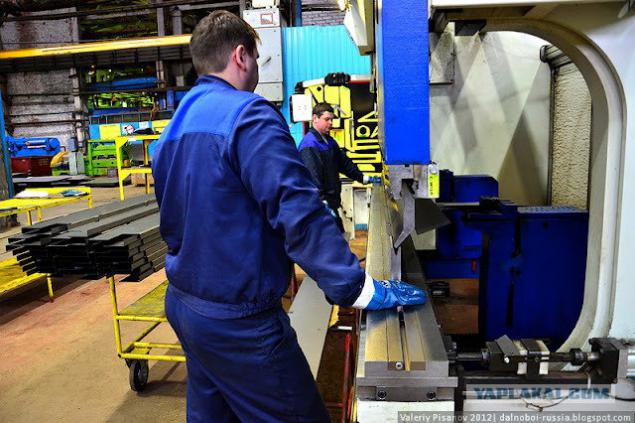
10. Чуть позже, с помощью пресса, им придадут нужную форму
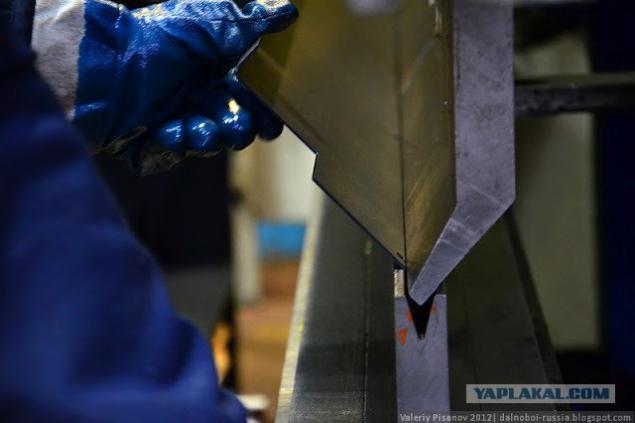
11. Готовые детали ждут отправки на следующие этапы производства.
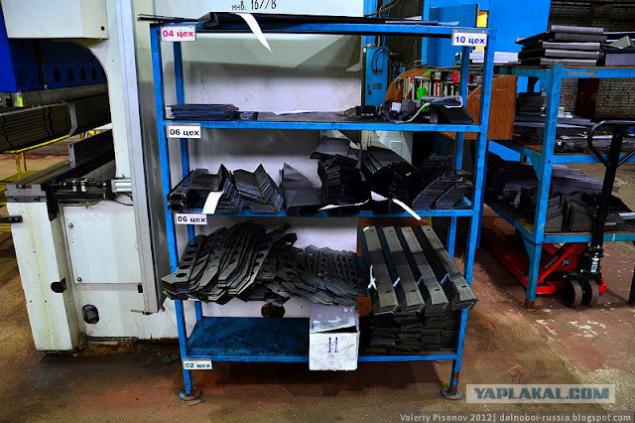
12. Рабочий процесс.
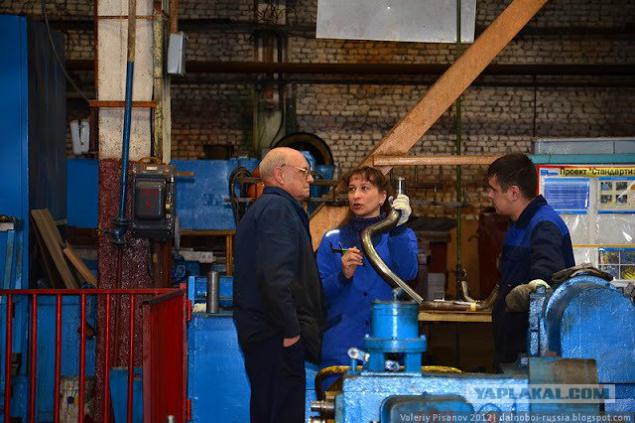
13. Изготовление, змеевика — испарителя, воздушной системы. Позже увидим, как деталь выглядит на готовом автобусе.
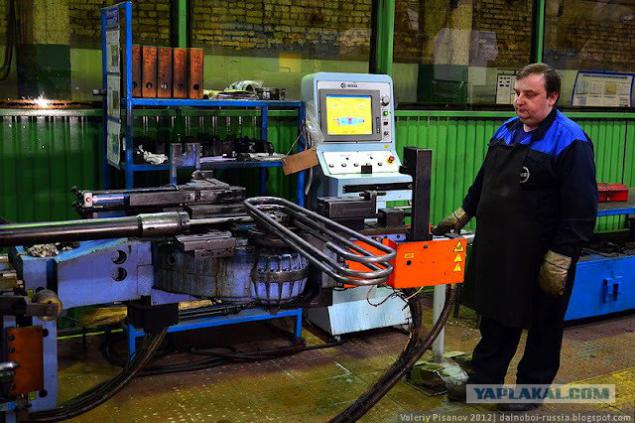
14. Теперь проследуем в цех сварочно-кузовного производства. На фотографии — линия сборки-сварки крыши SCHLATTER. Предварительно рабочие набирают на стапеле элементы будущей крыши.
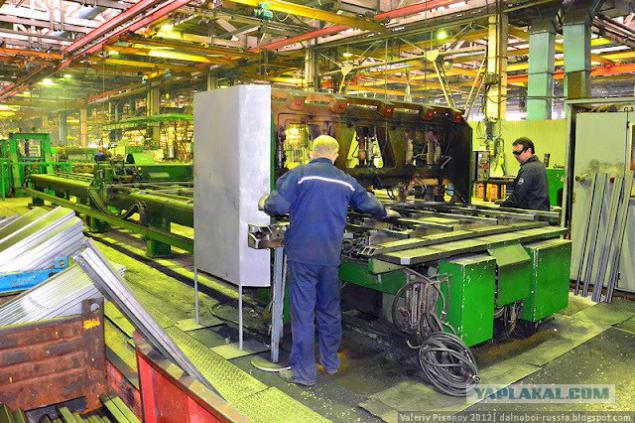
15. SCHLATTER за работой.
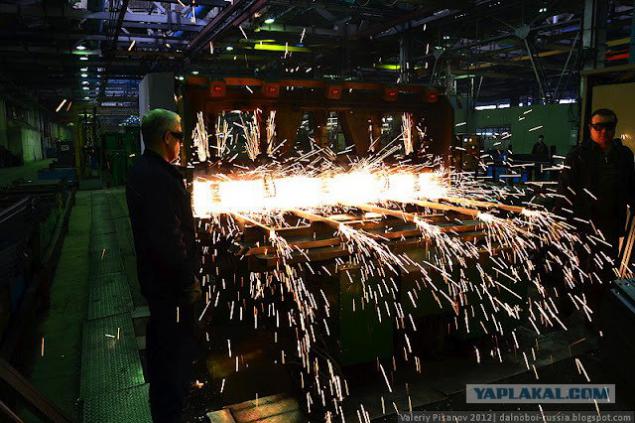
16. Следуем по нитке конвейера и мы. Шаг за шагом, элементы автобуса приобретают всё новые и новые детали.
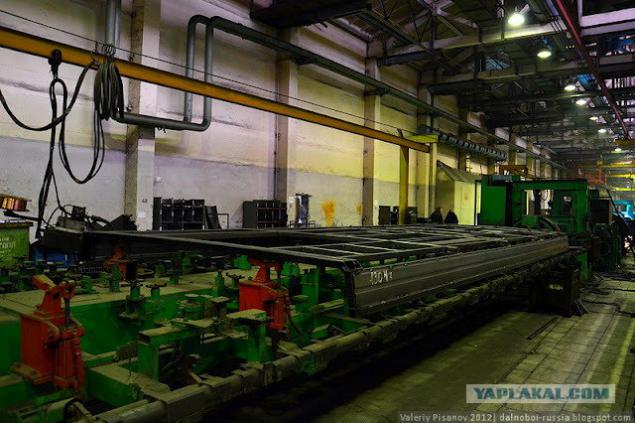
17. Собирается передняя панель автобуса. Сварщик за работой.
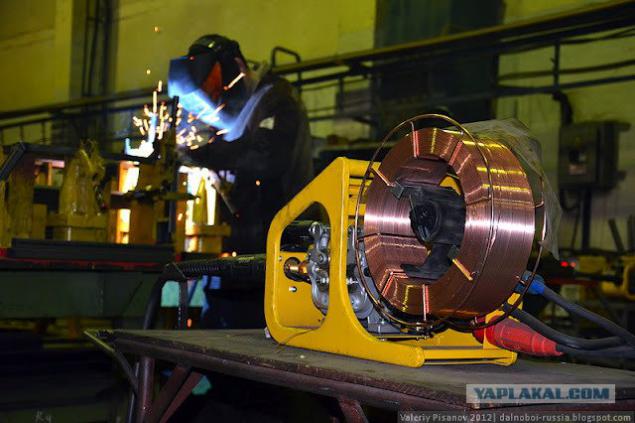
18. Наконец, настаёт время, когда на конвейере собирают в единое целое все элементы каркаса автобуса. Передняя часть – на фото.
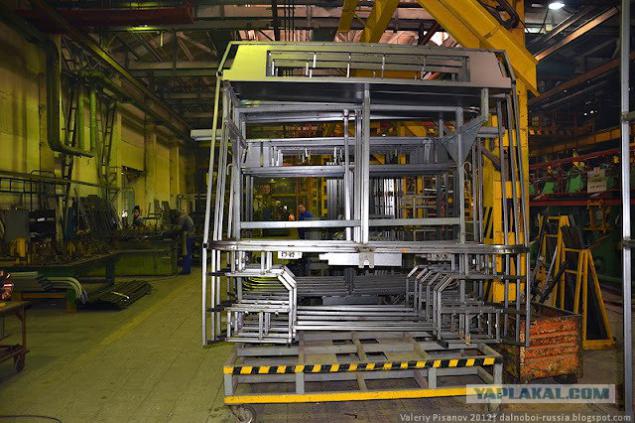
19. Так называемая рама – нижняя, несущая часть кузова автобуса.
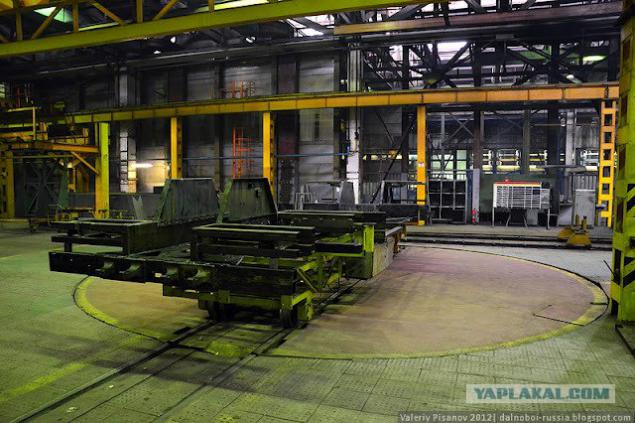
20. На стапеле, соблюдая строгую геометрию кузова, все детали собирают в единое целое
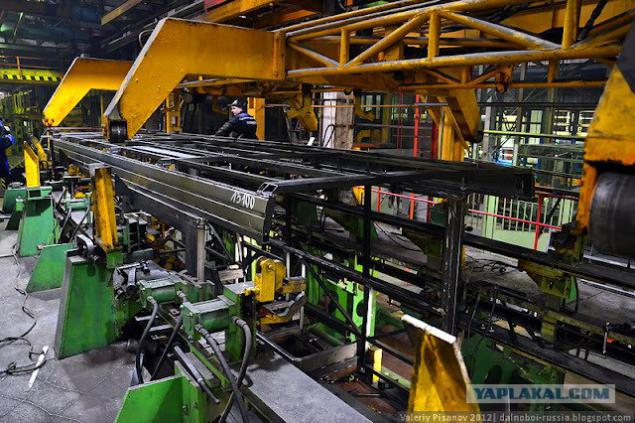
21. Оператор.
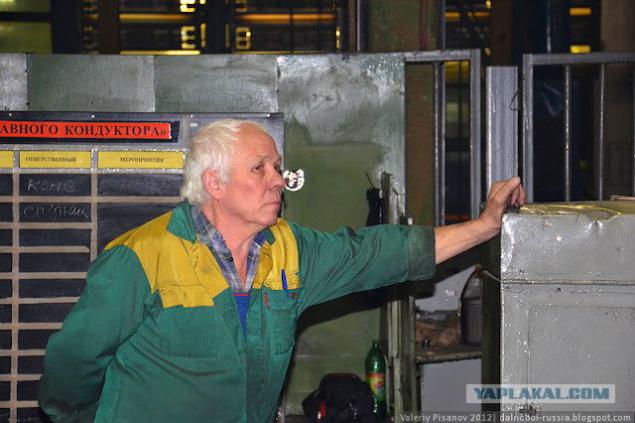
22. Сварка кузова на стапеле. Теперь, при желании, можно рассмотреть силуэт будущего автобуса.
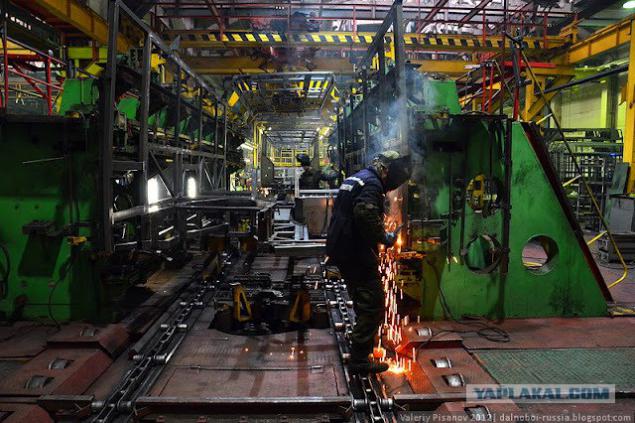
23. Дальше, на конвейере, готовую раму обшивают листами металла.
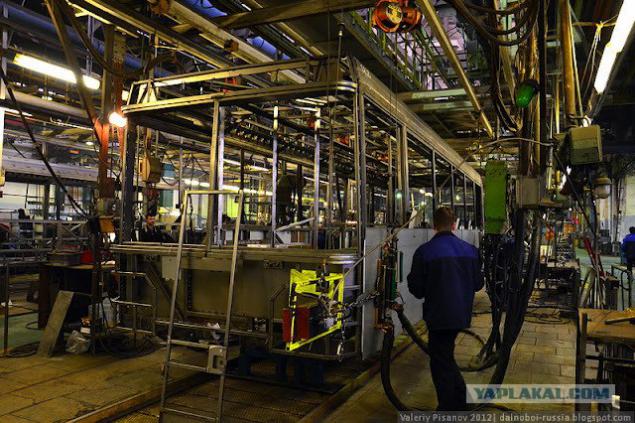
24. Для того чтобы борта автобуса были абсолютно ровные, на ЛиАЗе применяют уникальную технологию. Перед сваркой, лист металла нагревают до температуры 90 градусов по Цельсию. Он увеличивается в размерах и лишь потом, его натягивают на раму.
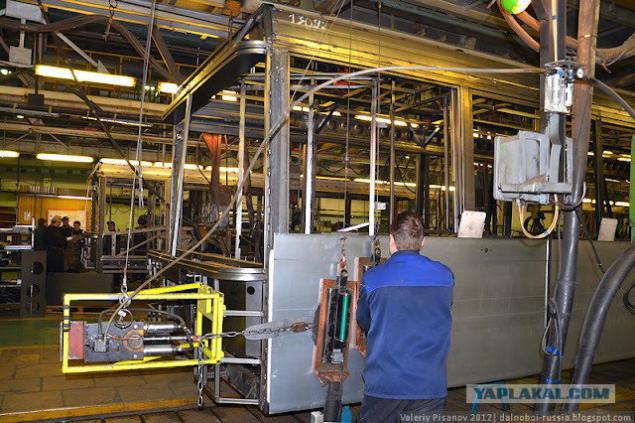
25. Заключительные штрихи кузовного производства.
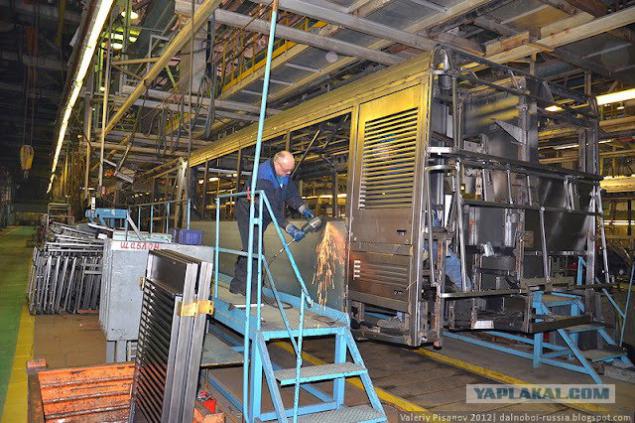
26. Обратите внимание, две части, сочленённого автобуса поступают на катафорезную обработку кузова.
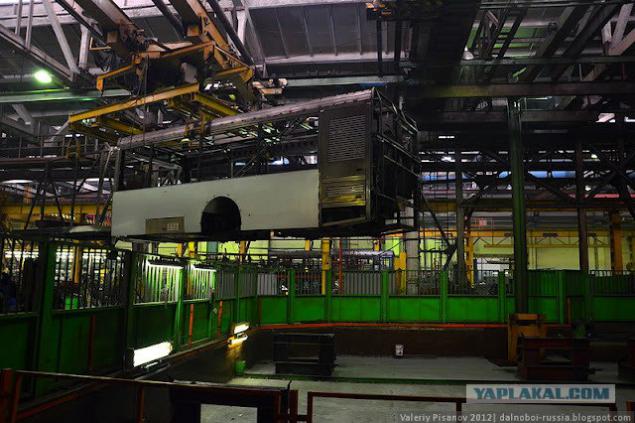
27. Аналогов такого процесса для кузовов таких габаритов в России, других странах СНГ и странах ближнего зарубежья нет
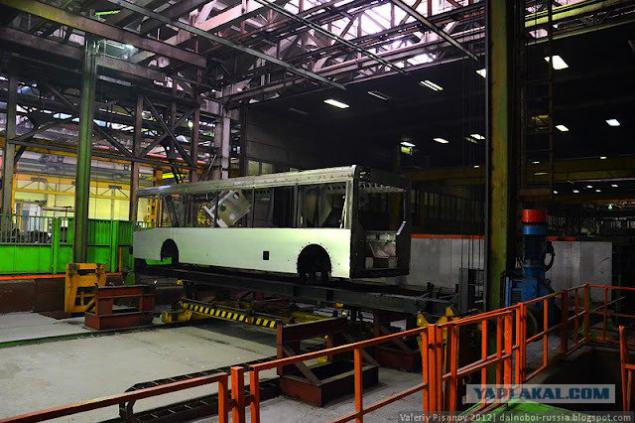
28. Командует процессом хрупкая девушка.
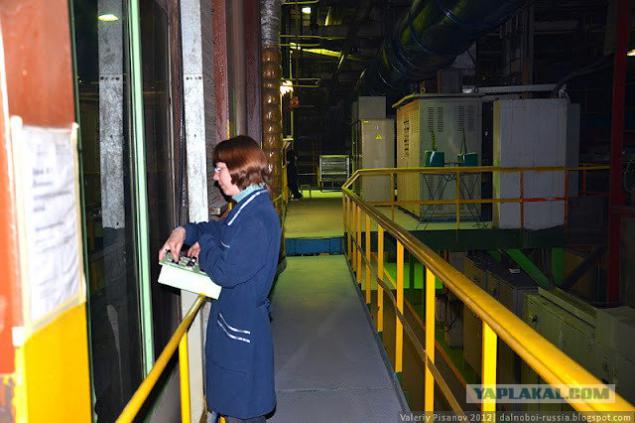
29. Кузова поочерёдно окунают в несколько огромных ванн.
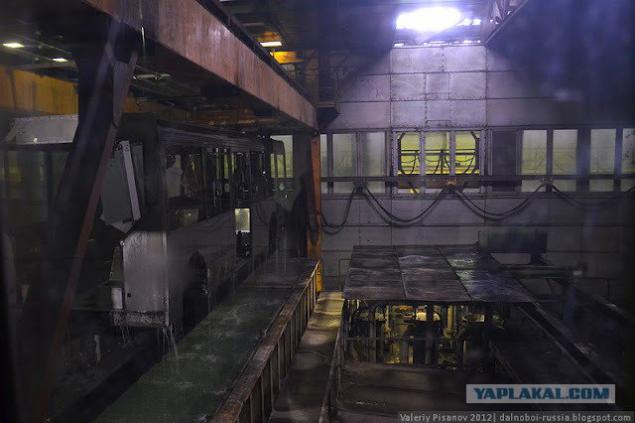
30. В своё время завод стал первым предприятием в России, применившим полную антикоррозионную обработку кузовов методом катафореза. Суть этого метода электролитического окрашивания состоит в том, что изделие, помещённое в катафорезную ванну, подвергается воздействию электрического поля. В результате этого специальная краска на водной основе осаждается на всё изделие целиком, не пропуская даже труднодоступных уголков. Сцепление эпоксидного слоя с металлом чрезвычайно прочно, а получившееся покрытие устойчиво к самым агрессивным погодным условиям.

30. В своё время завод стал первым предприятием в России, применившим полную антикоррозионную обработку кузовов методом катафореза. Суть этого метода электролитического окрашивания состоит в том, что изделие, помещённое в катафорезную ванну, подвергается воздействию электрического поля. В результате этого специальная краска на водной основе осаждается на всё изделие целиком, не пропуская даже труднодоступных уголков. Сцепление эпоксидного слоя с металлом чрезвычайно прочно, а получившееся покрытие устойчиво к самым агрессивным погодным условиям.
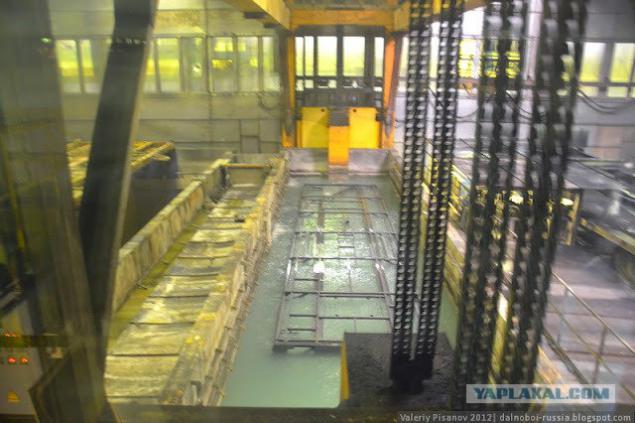
32. Для меня было откровением то, что крыша автобуса, на сто процентов покрыта пластиковым листом.
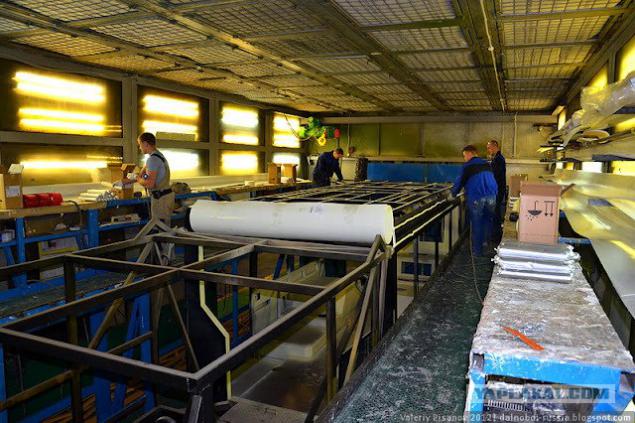
33. На ЛиАЗе утверждают, что эта технология на порядок практичней и долговечней.
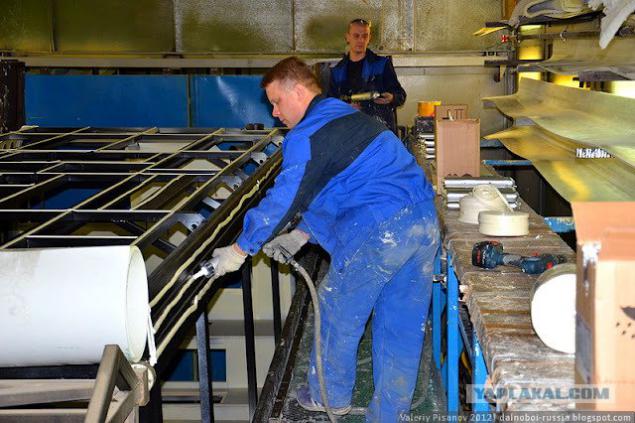
34. На предприятии постоянно трудятся около полторы тысячи рабочих, при средней зарплате в 35 тысяч рублей.
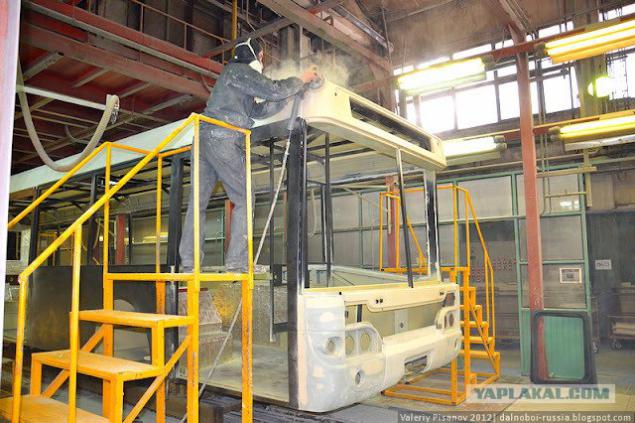
35. На данный момент, февраль 2012 г., каждую смену за ворота завода выходит 10 новеньких автобусов.
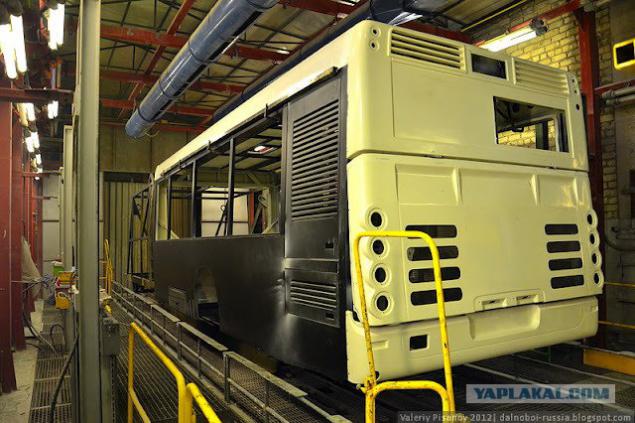
36. Но самый вал по заказам на ЛиАЗе приходится на конец года, т.к. основные заказчики предприятия бюджетные организации. В такие моменты выход автобусов с конвейера резко увеличивается. Предприятие набирает временных рабочих и поднимает зарплаты.
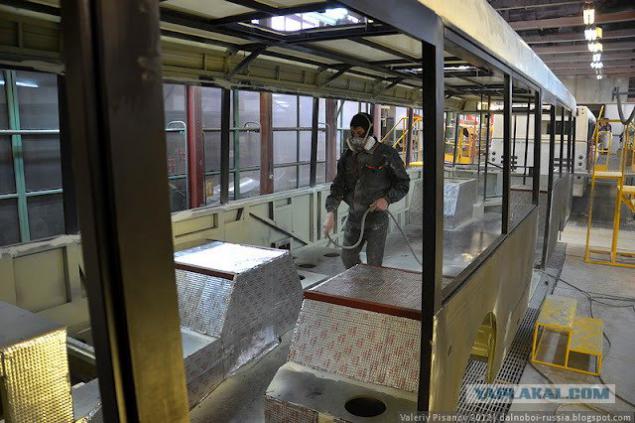
37. Кузова являются предметом законной гордости завода.
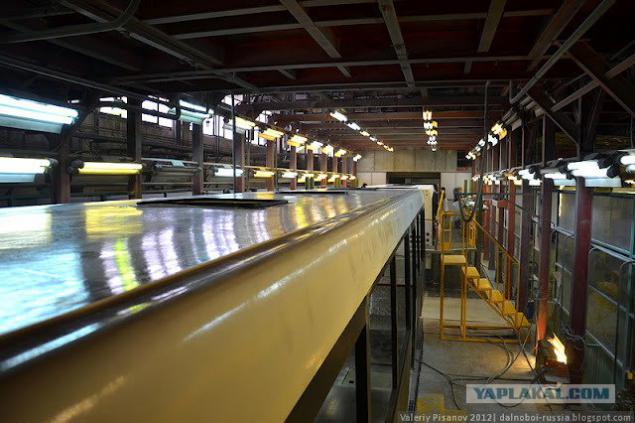
38. ЛиАЗ гарантирует, что кузова его автобусов прослужат не менее 12 лет до сквозной коррозии.
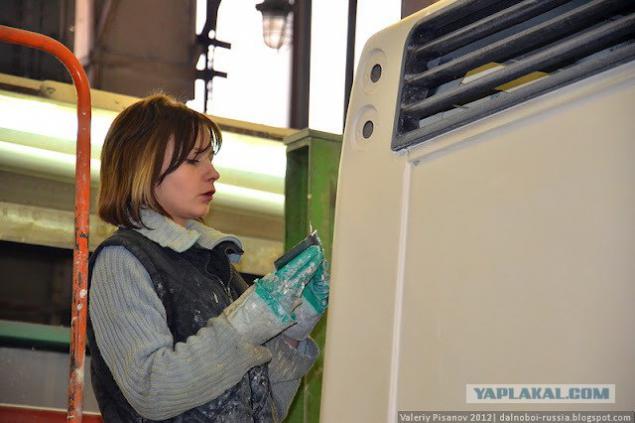
39. Поделись улыбкой своей!
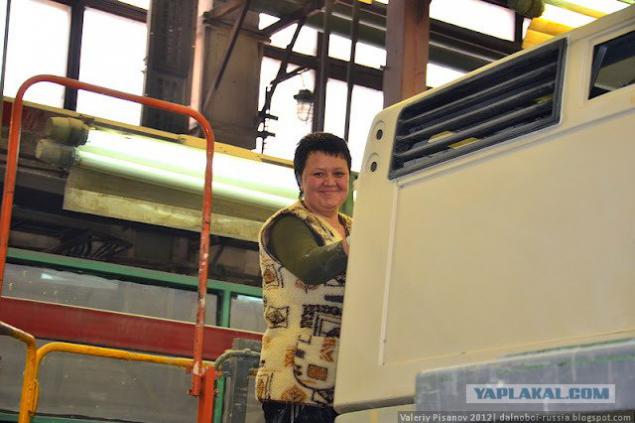
40. Заключительный этап перед отправкой кузова окраску.
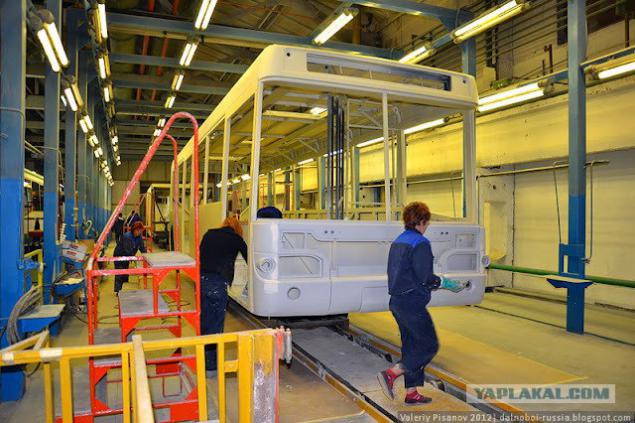
41. Дружба.
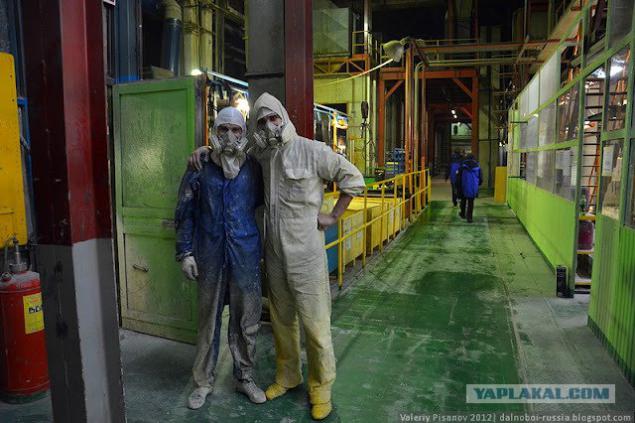
42. Выплывают расписные.
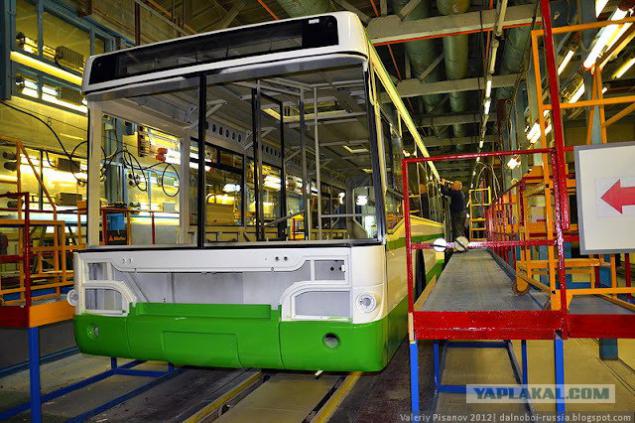
43. Настало время взяться за дело мастерам оконных дел.
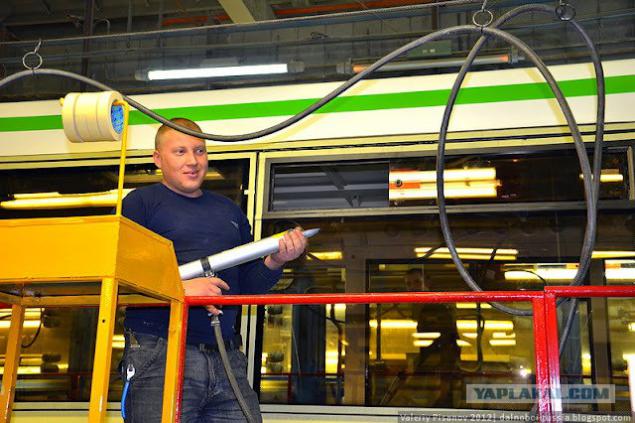
44. Прижимы.
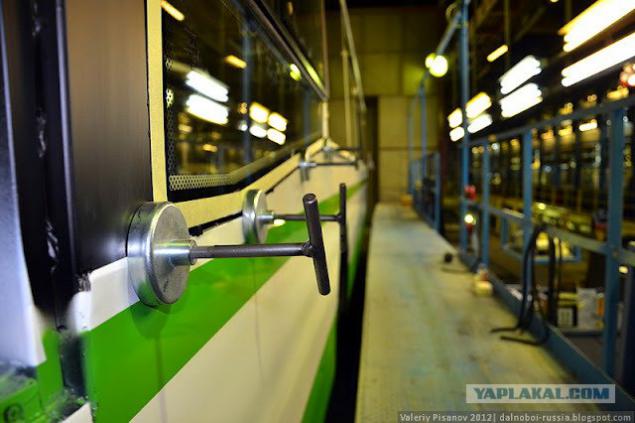
45. Сказать, что работа буквально горит в руках мастеров, будет недостаточно — это надо увидеть собственными глазами.
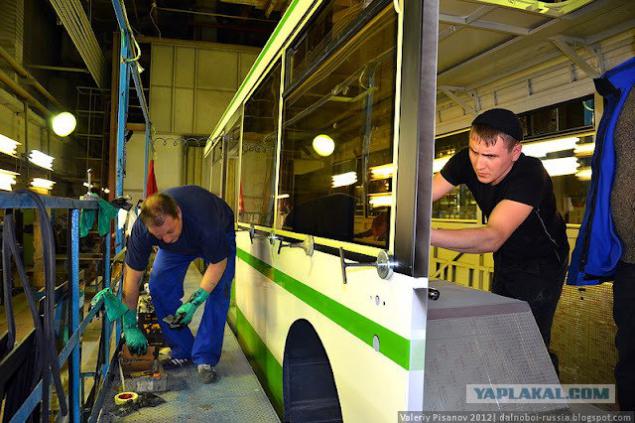
46. Размеры предприятия впечатляют. Ветка конвейера плывет по двум этажам одновременно
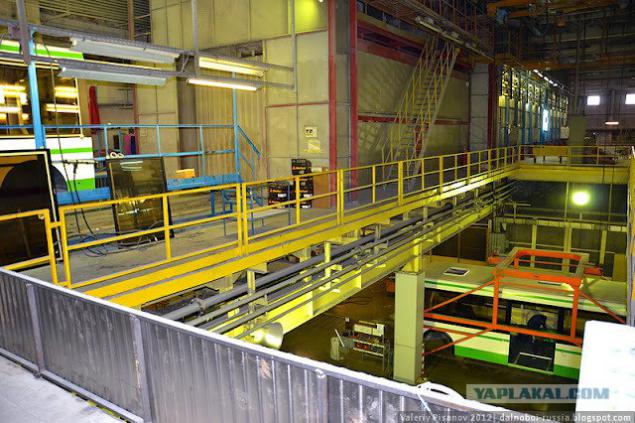
47. Настало время спуститься к заключительной линии сборки автобусов. Каждые 45 мин на конвейере устанавливают мосты, каждые 90 двигатель.
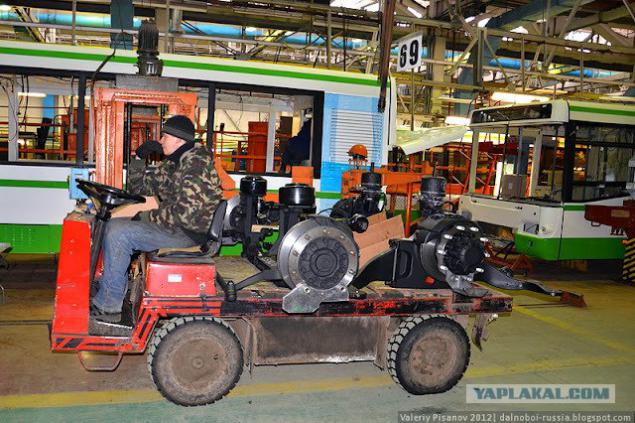
48. По желанию заказчика машины комплектуются мостами фирм ZF, Raba или отечественными КААЗ.
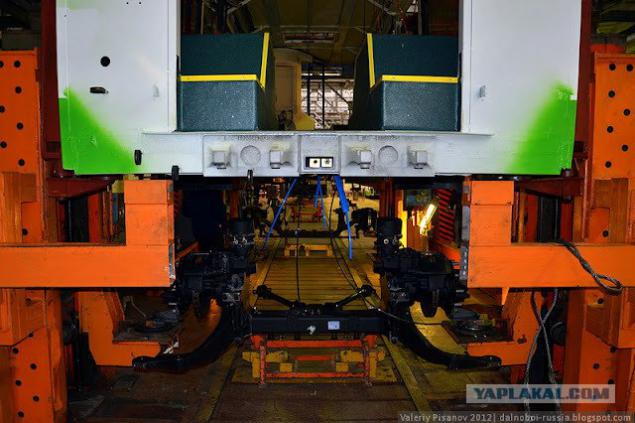
49. В данном случае, как видно на фото, на автобус установлен ведущий мост немецкого производителя — фирмы ZF.
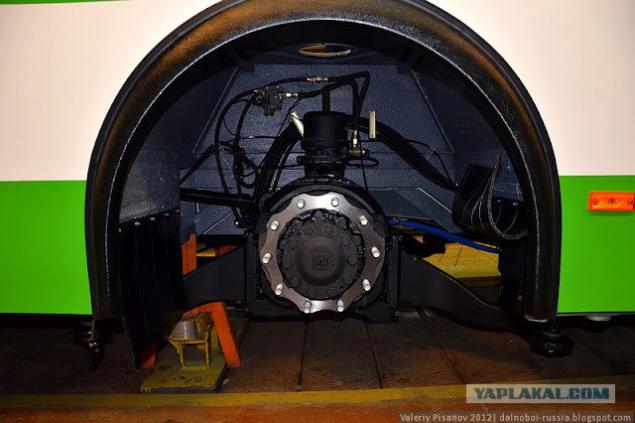
50. Выбор двигателя и коробки так же зависит от желания заказчика. Гамма агрегатов широка, от отечественных ЯМЗ и КАМАЗ, до лучших импортных образцов фирм MAN, Caterpillar, Cummins. Коробки скоростей Voith, ZF.
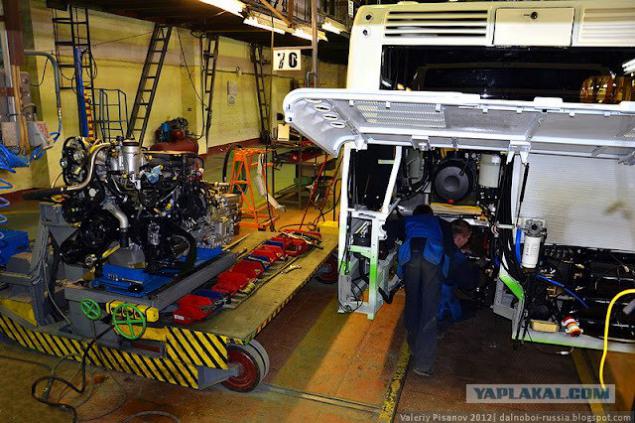
52. Далее наступает не менее интересный момент стыковки двух половинок сочленённого автобуса.
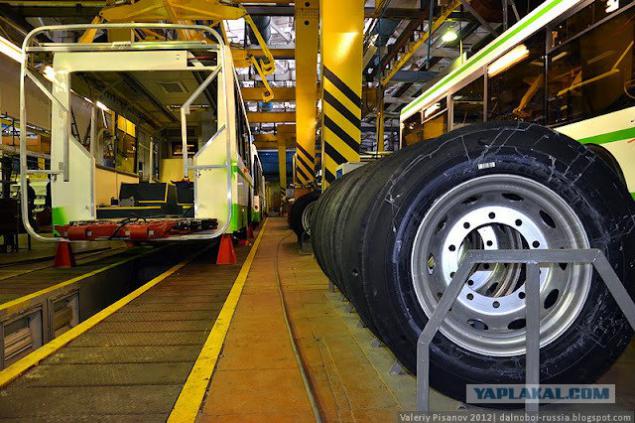
53. Как известно, ЛиАЗ один из первых заводов, кто наладил выпуск в России автобусов подобной конструкции.
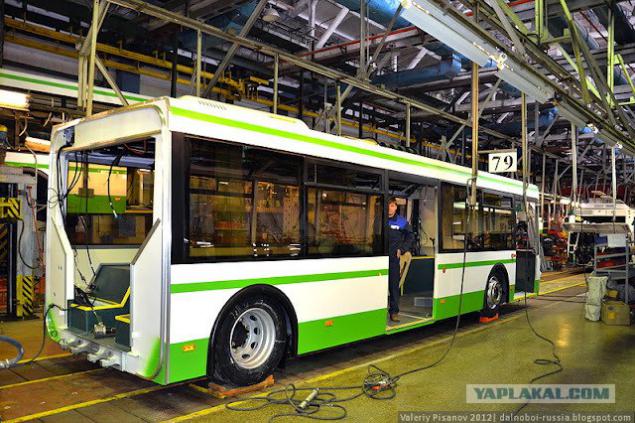
54. Именно с началом серийного производства автобуса ЛиАЗ-6212, с наших улиц стали пропадать венгерские «гармошки» от Икаруса.
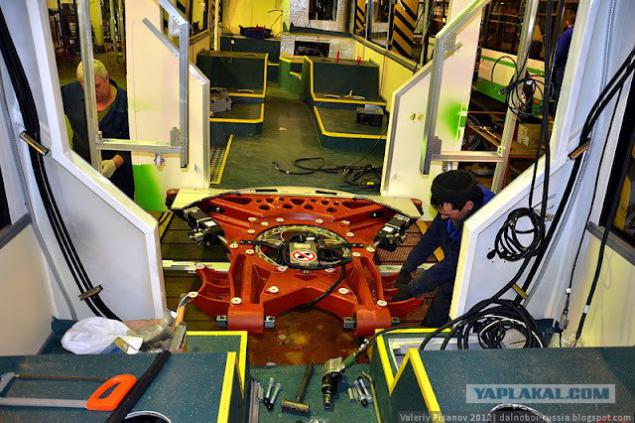
55. Гидроцилиндры в узле сочленения снабжены электронными мозгами, и теперь, чтобы исключить занос прицепа и жёсткие удары в крайних положениях, цилиндры меняют степень демпфирования в зависимости от угловой скорости поворота.
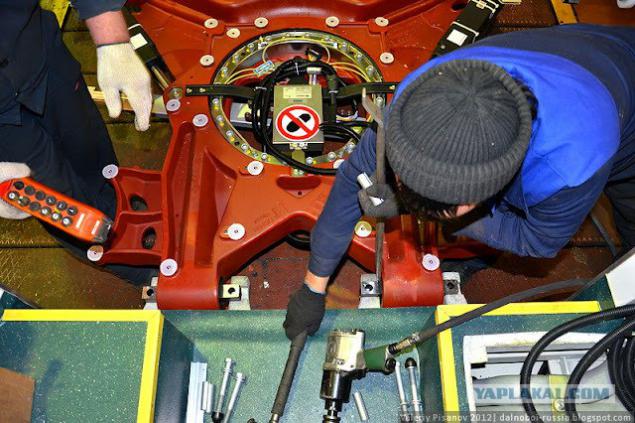
56. На ЛиАЗе применена принципиально новая схема — ведущие колёса на сочленённых автобусах находятся на прицепе. Именно он толкает автобус. Поэтому, при опасности складывания на скользком покрытии, цилиндры механизма блокируются.
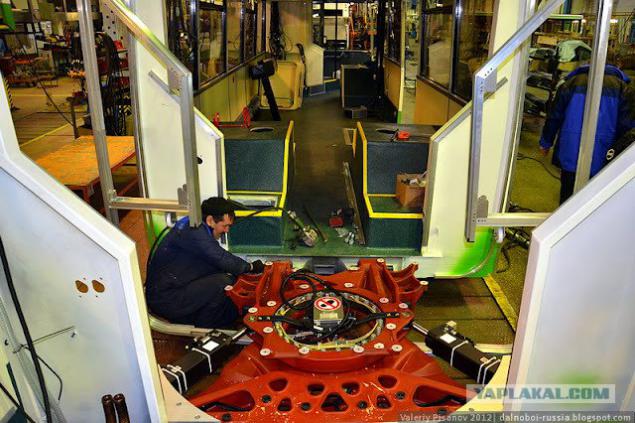
57. Механизм сочленения стоит порядка 1 млн. рублей. Из них, сам механизм 700 тыс. и ещё 300 тыс. так называемая «гармошка».
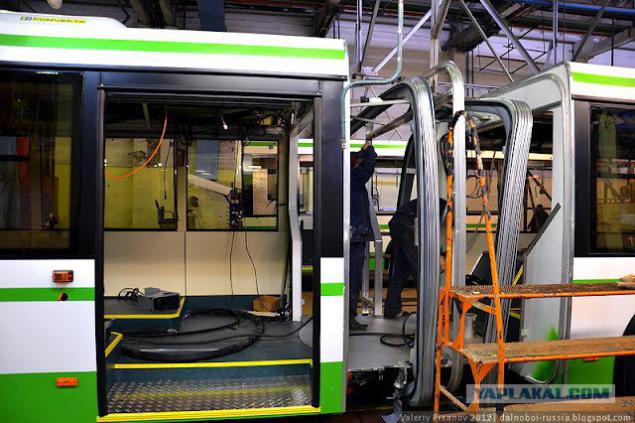
58. Двери обыкновенные.
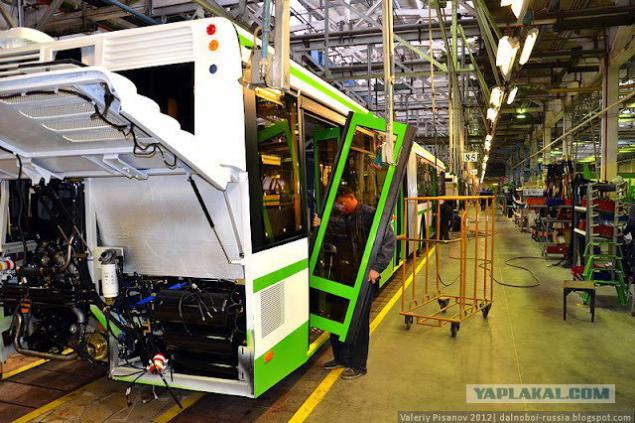
59.И не дай Бог, «на всякий пожарный».
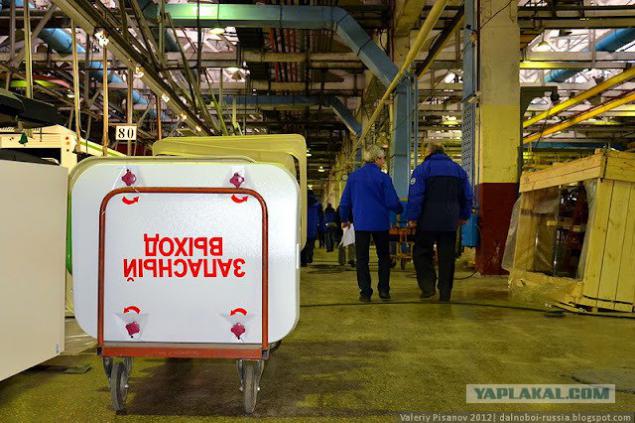
60. Основные заказчики ЛиАЗа крупные автохозяйства в городах-миллионниках.
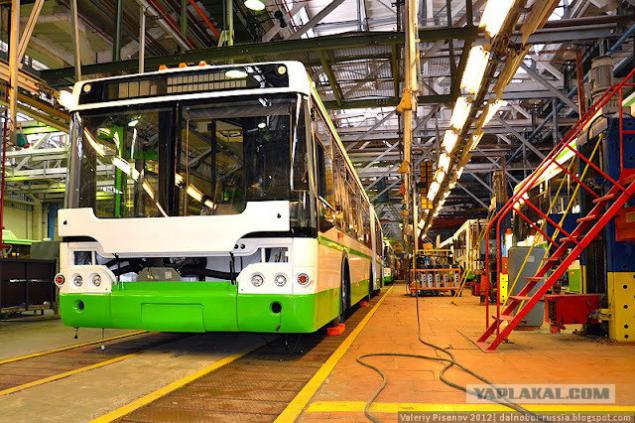
61. Серия автобусов с жёлто — оранжевой окраской предназначена для новой программы Правительства Москвы. Яркие автобусы будут ходить по выделенным полосам для движения пассажирского транспорта.
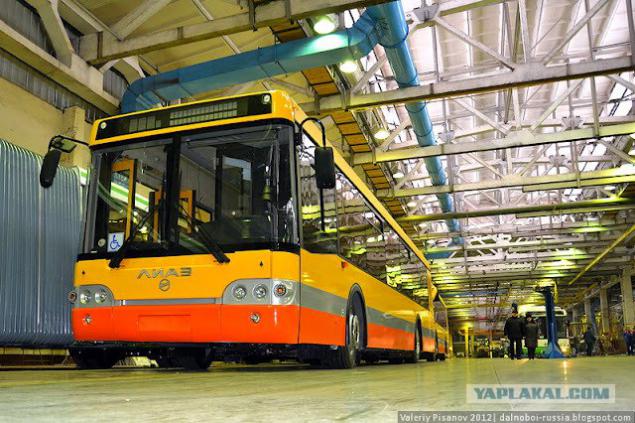
62.
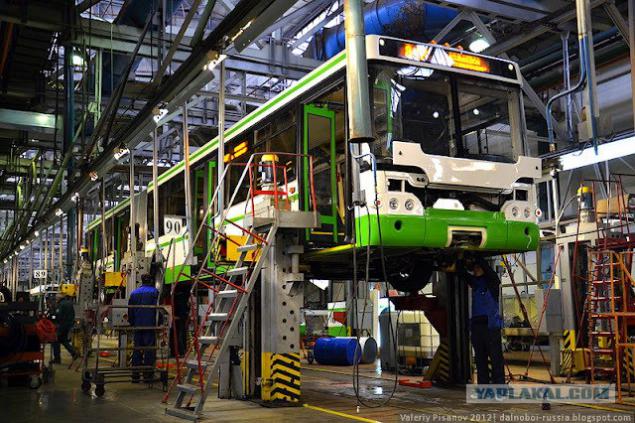
63. Отладка и тестирование электроники.
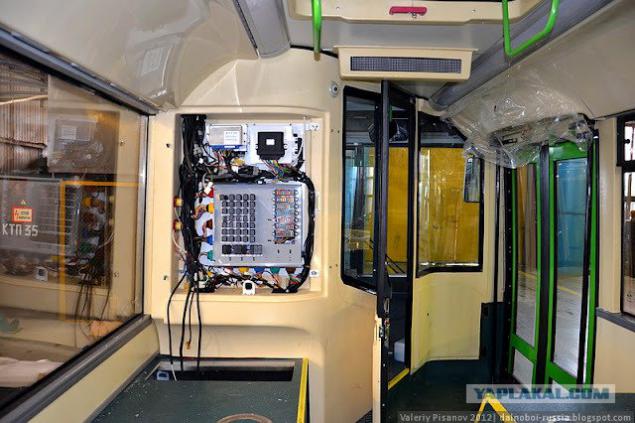
64. Заправка автобусов техническими жидкостями. В данном случае, в систему кондиционирования автобуса заправляют хладагент
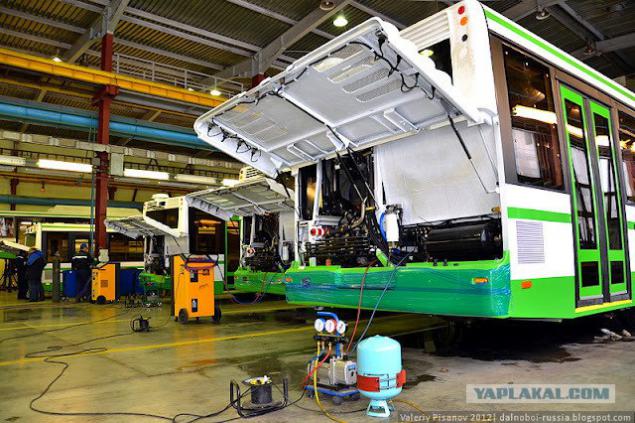
65. Рабочее место водителя автобуса. На мой взгляд, все сделано на уровне.
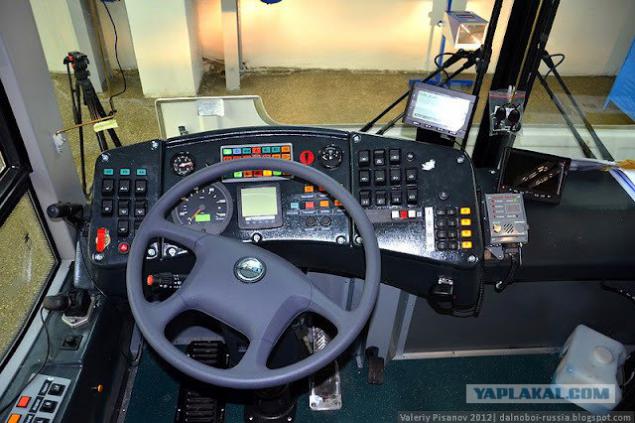
66. Мне удалость стать первым пассажиром новенького автобуса. Не удивляйтесь отсутствию сидений в салоне. Таков заказ Мосгортранса, видимо срок службы сидений дольше, чем срок службы самого автобуса.
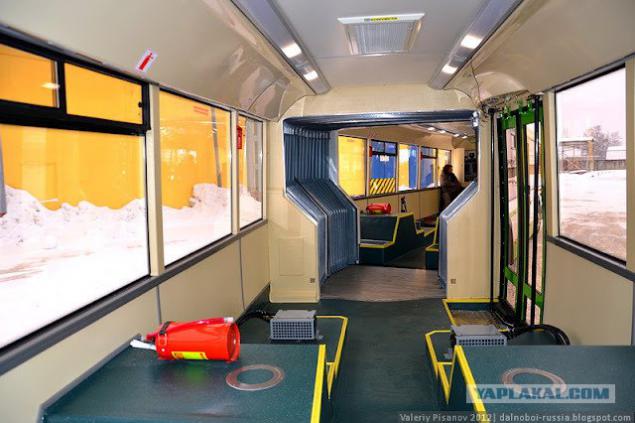
67. Но прежде чем покинуть территорию завода автобус попадает на линию независимого контроля. Это специальная методика аудита автомобиля «CSA», выполнена на базе зарубежных стандартов, её цель дать независимую оценку качества автомобиля «с позиции
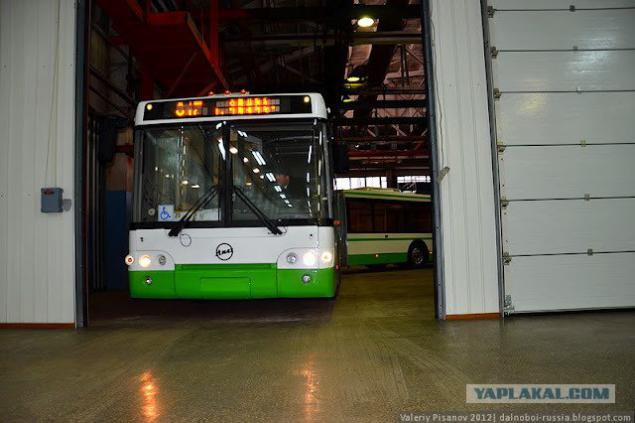
68. И лишь потом, автобус отправится к потребителю, и к своим пассажирам.
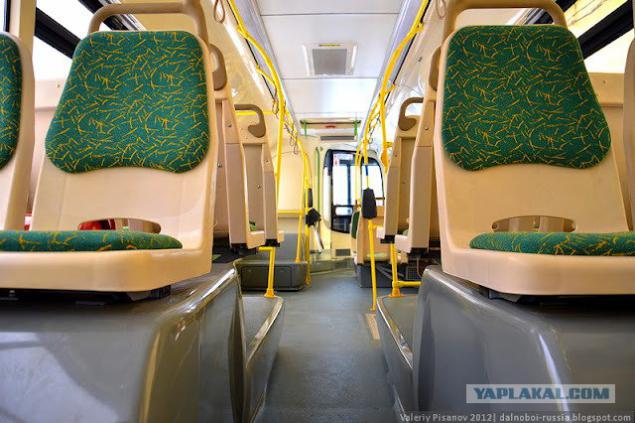
69… За организацию и проведение экскурсии, огромное спасибо директору завода ЛиАЗ Казакову Александру Михайловичу, а так же директору департамента массовых коммуникаций ООО «Русские Автобусы – Группа ГАЗ» Ворониной Элле Александровне, и лично PR менеджеру Фефеловой Ольге Андреевне.
Добавлено в [mergetime]1328513105[/mergetime]
Отсюда sdelanounas.ru/blogs/13510/#cut
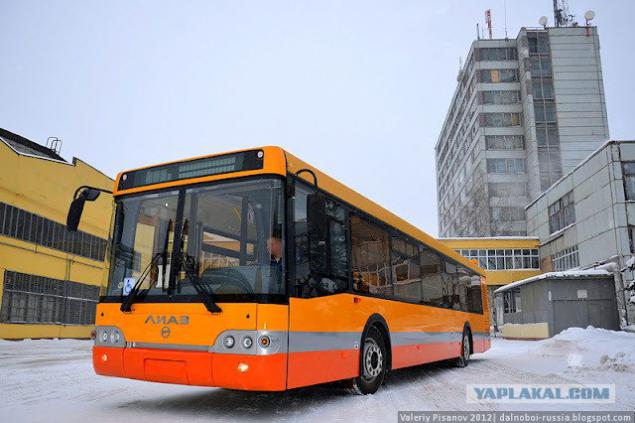
Источник: www.yaplakal.com/
Портал БАШНЯ. Копирование, Перепечатка возможна при указании активной ссылки на данную страницу.