727
Breeam Good for the suburban
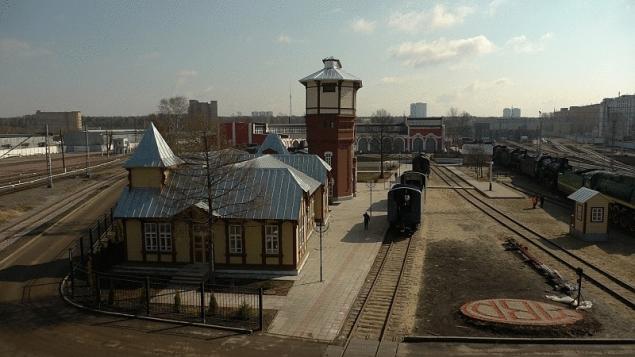
NOT EVERY GREEN OBJECT is necessarily commercial. It is not always the goal of certification is to increase the value or the capitalization of the project. Environmental quality in the project, confirmed by international certificate, and can be an expression of the global environmental policy of the company. Teamwork of the customer and the designers has led to a natural result is a higher valuation of the object according to BREEAM. We are talking about one of the newest industrial complexes of the Russian Railways – motor-carload depot of the station of Suburban.
One of the main objectives of the Environmental strategy of JSC RZHD for the period until 2017 and the prospect of up to 2030, published on 21 may 2014 is the introduction of principles of "green standards" on the facilities of JSC RZD. These are taken in quotation marks words could be a Manifesto, if in April 2015 at the Suburban station of the Moscow railway did not appear the most modern in the Russian motor-car depot, constructed in accordance with these standards and received a rating of BREEAM Good. We will discuss the details of the certification and the characteristics of the object, which enabled the depot to get certified.
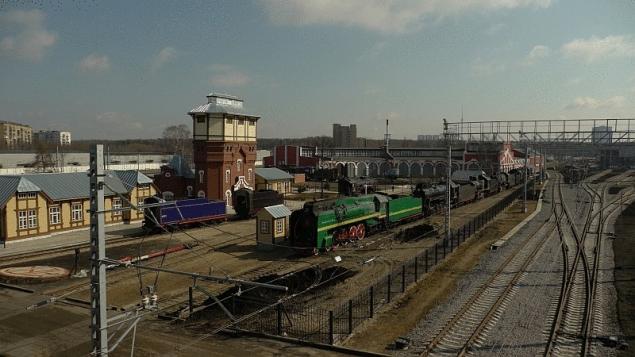
Suburban station on the Riga direction of the Moscow railway appeared in 1901, when it was built locomotive depot. The station is located within the boundaries of Moscow, near the Sokol. Mostly historic buildings have been preserved still – building wooden station on the street Cosmonaut Volkov, and the building of the locomotive depot fan type with a turning circle, and the water tower. During the war the station remained intact, and today its buildings form a unique architectural ensemble. And locomotive depot, and other buildings of the station are still in force and even serve the very retro-locomotives.
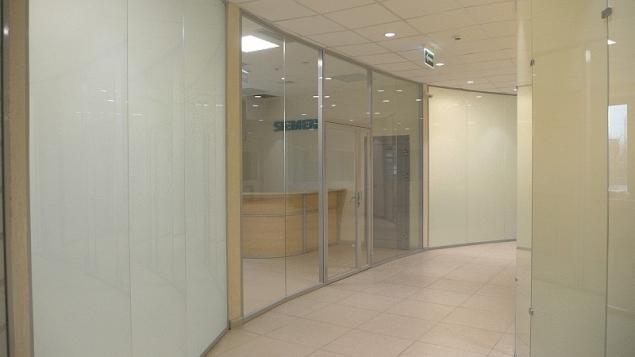
The purpose of the stages of certification
In 2009, Russian Railways signed a contract with German company Siemens for the supply to Russia of high-speed trains Desiro. A localized version of the German train, which is under contract with the manufacturer now collected at the plant in Verkhnyaya Pyshma, known under the commercial name of "Swallow".
It is a modern train, which in the future will be equipped with high-speed roads in some regions of Russia. Accordingly, for the services of these technically sophisticated trains require new conditions which demanded the creation of a new complex. The design of the new depot began in the same year 2009 companies of JSC "NIIAS", OJSC "Giprotyazhmash" and "Project office 1520".
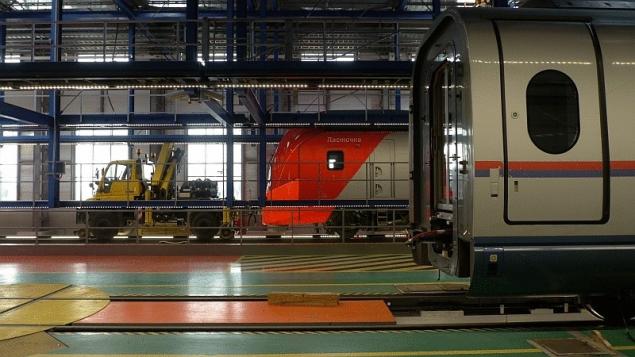
However, the reason that prompted the customer and designers to engage in certification at this facility, was not only a technical difficulty accepted where foreign trains. On this project the experts of the Railways and the contractors design organizations, green certification has been tried to develop a new management model. In the future, this design approach will allow you to confidently design and build railway facilities in accordance with the highest international quality standards and fulfill the requirements of green standards.
Construction of the depot, the multi-stages, and by 2015, the certification according to BREEAM passed the first stage – plant maintenance area 16639 sqm Certification was carried out according to the scheme for commercial buildings – BREEAM Europe Commercial Industrial (2009). This scheme allows to estimate the storage building and premises for light manufacturing and repair shops. Depo has been certified for the stage "Project" and received a rating of Good c percentage of points 47,87%. In June 2015, the building will be certified at the stage of completed construction, the planned level of the final certificate as Good.
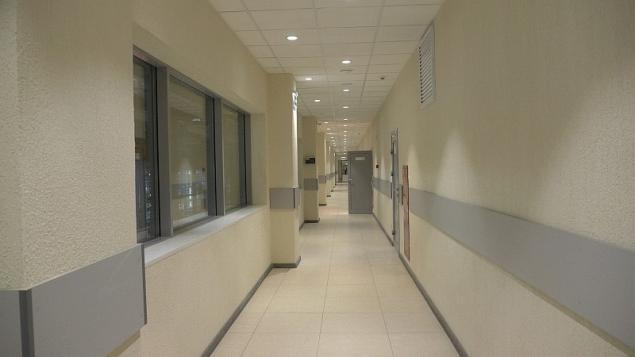
Features certification
Certification specialist – consultant at environmental innovations leading consulting company John Lang LaSalle Ksenia Agapova noted that the building of the depot was initially put enough energy-efficient solutions, therefore the project does not have to make many changes. A preliminary assessment of the project began on the stage of the stage P, so the architectural decision and design is also not changed.
All the changes affected mainly the engineering systems and their doukomplektatsiya (for example, solenoid valves and motion sensors), as well as the General plan (the allocation of places for Bicycle Parking, landscaping and places for the separate accumulation of waste). In addition, required additional research – e.g. research on potential flood risk from anthropogenic and natural sources. Lots of efforts have gone and the optimization of the lighting project is and efficient distribution of lighting, and the use of combined lighting and led technology and control automation.
But because BREEAM assesses and certifies only the building itself, and the depot is still production-technological complex, it was necessary to distinguish between technological processes and the viability of the building.
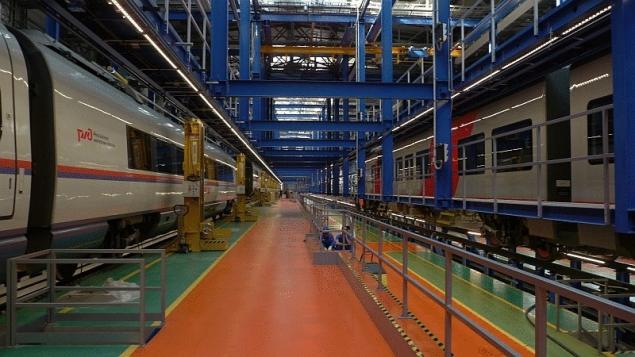
The main difficulty
Designers to work on a building under BREEAM certification had for the first time in the John Lang LaSalle noted that a key difficulty was to educate designers on new design standards and new style of thinking. However, the achieved targets were quite high.
So, in the field of construction management, energy efficiency, internal environment quality implemented more than 50% of the criteria, more than 80% of all criteria were implemented in terms of "waste management" and "accessibility". For example, waste from demolition was recycled and used by the contractor directly to the construction site was organized separate collection of waste.
Good accessibility to alternative transport modes was achieved not only due to the availability of public transport, and install Bicycle Parking facilities and reduce the number of Parking spaces for cars on the project. Measures were taken to reduce water consumption – planting of native plant species to reduce the need for watering, the installation of solenoid valves to reduce leakage and install water-saving fittings.

During the certification conducted energy modeling, which allowed us to predict the expected energy consumption for a given object. The power consumption of the case THAT amounted to 142 kWh per square meter, which is 25% less than power consumption of similar buildings, designed in accordance with ASHRAE standard 90.1-2007.
Reduction of water consumption according to the methodology of BREEAM – about 30%, more than 40% of the materials for the bedding is a secondary raw material. Certification depot BREEAM was launched in September 2012, the certificate on the stage of the project was obtained in August 2013.
Structural elements
Tell me more about the measures that have been taken in this project to achieve BREEAM Good indicators. By blocking the main objects of the depot was reduced the total area of exterior walls on 4300 sq. m. that provided the economy of building constructions and energy consumption.
Building envelope have improved resistance to heat transfer compared to standard. The roof insulation is made of mineral wool slabs "Technorap", wall – extrusion foamed polystyrene and mineral wool plates. Windows are double-glass filling chambers with argon, is made of a thermally insulated aluminum profile DOORS with termostabile. Reduced resistance to heat transfer R=1,0 m2°C/W, which is 3.3 times more effective than the standard.
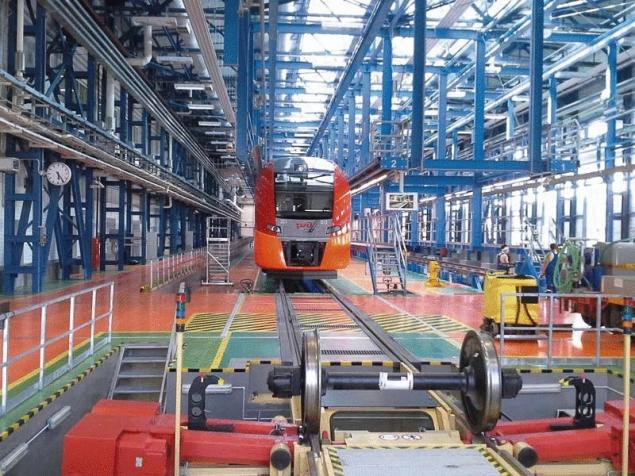
The emphasis is on natural light
Particularly worth mentioning is the organization of building lighting, as this issue in the design was paid a lot of attention. First, the building is designed to maximize natural day lighting. The very orientation of the complex allows to avoid the blinding sun and glare, and layout of the premises and locations jobs office part chosen in such a way as to facilitate comfortable use of daylight and to every employee working in the building, had a window view.
It has long been established that the ability to look out of the window and thus refocus the gaze creates a favorable environment that allows you to feel oneness with the rest of the world, and also helps to avoid eye diseases.
Inside the space is organized with transparent dividers. The Windows are arranged automatically adjustable louvers controlled by actuators connected to the KNX Protocol. In automatic mode depending on the position of the sun, the activator controls the actuator, setting the desired position of the louvers to the desired degree of shading.
LEDs and automation
What sways the actual lighting fixtures, then, firstly, in the shop maintenance, used fluorescent lamps with high light output ratios; second, all fluorescent lamps equipped with electronic start-control devices (electronic ballasts increase the energy efficiency of lamps).
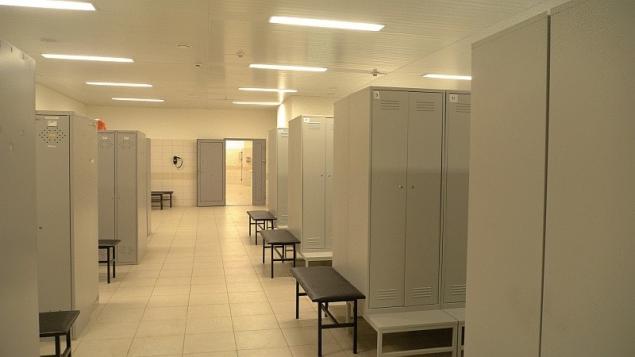
In the office part of the illumination of the corridors implemented with led lamps and indoor fluorescent luminaires with ballast for flexible control of lighting, switching and dimming. Signals to control the ballast received from special DALI gateways connected via the KNX Protocol.
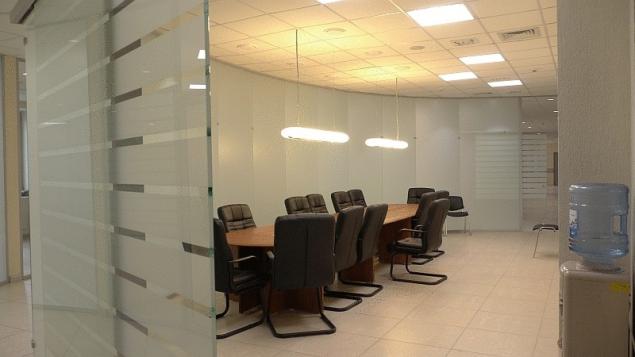
Interesting organized and automated lighting control. In each room of the office block above each group of jobs installed presence sensor and light sensor. If the employee leaves the workplace without turning the lights off manually, turning off the lights happen according to the signal from the presence sensor. So the lighting is damirovna, if the illumination outside of the workplace exceeds certain limits.
In areas corridor lighting is switched on by the signal of the motion sensor. The sensor captures the movement of people and gives the signal to turn on the gateway. Order in the absence of motion the man left in a dark corridor, is a slow fading light. In places where the most likely finding people in static position, presence detectors are installed. In bathrooms equipped with solenoid valves which block the water when you turn off the light. Overlap of water occurs after light-off, after a time sufficient for the water filling the toilet tank.
The total energy savings, compared to analogue, in the domestic lighting amounted to 76 thousand kW/h.
Heating and air conditioning
Heating in the workshop organized with the help of highly efficient water infrared emitters and also air heating with recirculation. Air conditioning is only used in the administrative areas. Provided control system automation of Central heat points, custom control heating and air.
To ensure local control over the temperature regime in the premises of the building provides thermostatic valves on all radiators. In addition, the reduction of energy consumption is achieved through the measurement and management of energy consumption for different types of uses, such as heating, hot water, ventilation, air-conditioning.
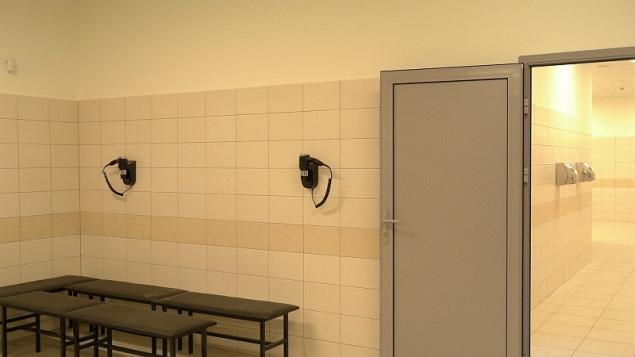
Water conservation
Interesting solutions were applied on water conservation. In addition to the system of accounting for costs of water, wash basin faucets aerators with a capacity of 2-3 l/min, applied shower hoses with a restrictor of water flow with a capacity of 7-8 l/min; toilet buttons with dual flush 3-6 l/min.
Rain water from roofs, roads and industrial sites is given to local treatment facilities, cleared and used subsequently for washing the washing complex compositions, as well as for watering lawns and roads. Maximum savings of drinking water in the depot will be 40 m3/day or 14.6 m3/year.
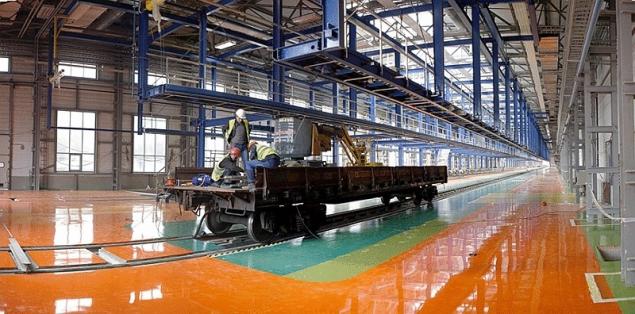
Thus, combining the latest engineering and construction achievements, a new depot at the station near Moscow will become, according to the expectations of railway workers, the best in Russia. By the way, the similar equipment and the appointment of the railcar depot in Russia only two – Metallostroy in the Leningrad region and Sochi, but they do not have international ecological certificate. Created in Moscow, one of a kind complex aspires to become a leader in their industry and example of sustainable building for all of Russia. published
P. S. And remember, only by changing their consumption — together we change the world! ©
Source: green-city.su/breeam-good-dlya-podmoskovnoj/