526
Condensing boilers in the autonomous heat supply
Significant amounts of new construction contributed to the widespread adoption of autonomous heat generators of various types and creation on their basis of decentralized heating systems.
Basic directions of increase of efficiency of gas-fired boilers is the introduction of condensing technology. In condensing boilers is not only sensible heat but also a part of the latent heat of condensation of water vapor from the flue gas, ensuring the operational efficiency of the boiler up to 95-96% on higher heating value (105-107% on lower heating value).
The importance of this trend underlines the EU Directive 2009/125 / EC, by which to 15.10.2015 in the EU countries are not allowed to use the facilities of the new building of autonomous heating systems on the basis of non-condensing boilers with gas fuel.
These factors explain the increased interest in condensing technology and in our country that requires careful analysis of the features of its design and application. The article is devoted mostly fired condensing fuser, although many of the provisions applicable to outdoor boilers.
For condensing boilers are characterized by the use of heat exchangers increased heat transfer area and making them corrosion-resistant materials (stainless steel, copper, aluminum alloys and others.). Often, the heat exchanger is partitioned and fitted with devices "gravity" collection and neutralization of condensate. To improve the operating efficiency of the boiler condensing heat exchanger it is necessary to apply the coolant (water) is a low temperature below the temperature of the flue gas dew point, since only in this case can onny-condensation mode. Therefore, in the thermal circuit of the boiler piping components should not be used recycling and mix with the coolant in the return line, hydraulic controls, squirrel collectors and other mixing devices, raising the return temperature.
In the scheme of the condensate collection and drainage should be installed converter as condensate is acidic pH = 3, 5-4, 0.
In addition to these highlights serious problems with the use of condensing boilers are connected with the organization of the aerodynamic modes of flues and chimneys. Almost all gas condensing boilers are equipped with premix burners (complete pre-mixing), the organization of work which is carried out by means of blowing fan or exhauster. The second scheme is widely used as a gas burner is carried out at a lower pressure and a vacuum in the furnace instead of using the blow fan in a pressurized furnace. However, in both cases, the conditions of use in the boiler must be a point "0" (Vol. E. The total pressure of the combustion products is equal to atmospheric pressure). Thus, the whole smoke path from the boiler to be under vacuum. Given this, great attention should be paid to the aerodynamic regime and samotyage created chimney. This vastly important as condensation products of combustion of the boiler may have a temperature of 50-60 ° C and a moisture content close to the saturation state. Small design temperature difference of products of combustion and ambient - in unfavorable conditions 20-30 ° C (summer), provides samotyagu chimney height of 10 m about 8 Pa, that for typical conditions (polypropylene or metal pipe, λtr ≈ 0, 02) will provide a the speed of movement of the flue gas is not more than 1 m / sec.
Such low velocity will lead to an increased cooling of the flue gases in the chimney and "blowing" flow of combustion products at the outlet already at low wind speeds. The inevitable cooling of the saturated flue gas flues and chimney causes condensation to collect on which you want to arrange a chimney condensate "pot" or siphon elbows with neutralizer "sour" condensate. The main problems with this occur in the winter under the terms neobmerzaniya kondensatootvodnogo node at negative ambient temperatures.
These cold climates modes chimneys at outside temperatures below -30 ° C will inevitably result in frosting of the chimney and the formation of ice uninsulated areas, so insulation output areas and open gaskets chimneys is mandatory.
This condition requires the installation of flues and chimney in a heated room with heat and waterproofing or for a group of chimney (one to two boilers) mandatory install it completely in a heated room (inside the building).
The ducts drain the condensate from the flue pipe to the boiler bias through kondensatootvodny boiler unit. For flues and chimneys condensing boilers, for the reasons stated, is almost completely eliminated coaxial scheme smoke and air supply to the combustion even if the internal insulation of flues and chimneys. Under the terms of corrosion resistance, prevent steam, and moisture permeability and heat resistance to condensing boilers the most widespread flues and chimneys are made of polypropylene and stainless steel.
Calculations have shown that the operational efficiency of condensing wall of thermal blocks in different climatic conditions higher than "traditional" stand-alone heat generators up to 6-8%, which corresponds to the annual cycle of the same fuel economy.
Given that condensing boilers cost exceeds the value of "traditional" at 35-100%, and to develop an autonomous heating system must be in the low-temperature coolant (with a corresponding increase of capital investments in the heating system), to pay off an autonomous heating system using a condensing boiler at reduced costs, will about 3-5 years old.
Basic directions of increase of efficiency of gas-fired boilers is the introduction of condensing technology. In condensing boilers is not only sensible heat but also a part of the latent heat of condensation of water vapor from the flue gas, ensuring the operational efficiency of the boiler up to 95-96% on higher heating value (105-107% on lower heating value).
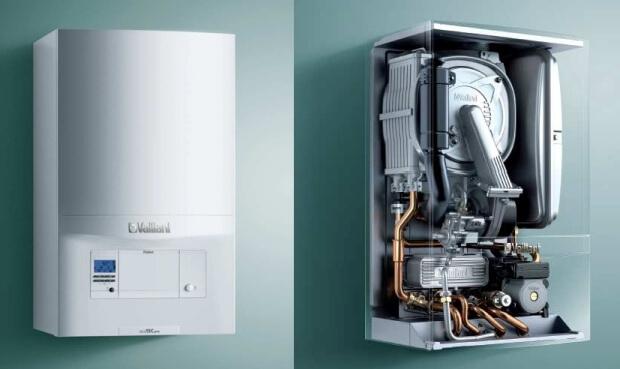
The importance of this trend underlines the EU Directive 2009/125 / EC, by which to 15.10.2015 in the EU countries are not allowed to use the facilities of the new building of autonomous heating systems on the basis of non-condensing boilers with gas fuel.
These factors explain the increased interest in condensing technology and in our country that requires careful analysis of the features of its design and application. The article is devoted mostly fired condensing fuser, although many of the provisions applicable to outdoor boilers.
For condensing boilers are characterized by the use of heat exchangers increased heat transfer area and making them corrosion-resistant materials (stainless steel, copper, aluminum alloys and others.). Often, the heat exchanger is partitioned and fitted with devices "gravity" collection and neutralization of condensate. To improve the operating efficiency of the boiler condensing heat exchanger it is necessary to apply the coolant (water) is a low temperature below the temperature of the flue gas dew point, since only in this case can onny-condensation mode. Therefore, in the thermal circuit of the boiler piping components should not be used recycling and mix with the coolant in the return line, hydraulic controls, squirrel collectors and other mixing devices, raising the return temperature.
In the scheme of the condensate collection and drainage should be installed converter as condensate is acidic pH = 3, 5-4, 0.
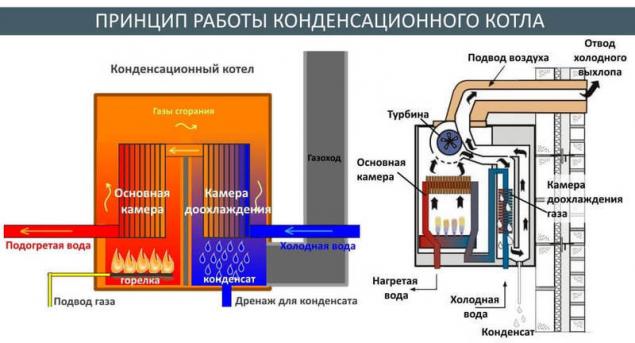
In addition to these highlights serious problems with the use of condensing boilers are connected with the organization of the aerodynamic modes of flues and chimneys. Almost all gas condensing boilers are equipped with premix burners (complete pre-mixing), the organization of work which is carried out by means of blowing fan or exhauster. The second scheme is widely used as a gas burner is carried out at a lower pressure and a vacuum in the furnace instead of using the blow fan in a pressurized furnace. However, in both cases, the conditions of use in the boiler must be a point "0" (Vol. E. The total pressure of the combustion products is equal to atmospheric pressure). Thus, the whole smoke path from the boiler to be under vacuum. Given this, great attention should be paid to the aerodynamic regime and samotyage created chimney. This vastly important as condensation products of combustion of the boiler may have a temperature of 50-60 ° C and a moisture content close to the saturation state. Small design temperature difference of products of combustion and ambient - in unfavorable conditions 20-30 ° C (summer), provides samotyagu chimney height of 10 m about 8 Pa, that for typical conditions (polypropylene or metal pipe, λtr ≈ 0, 02) will provide a the speed of movement of the flue gas is not more than 1 m / sec.
Such low velocity will lead to an increased cooling of the flue gases in the chimney and "blowing" flow of combustion products at the outlet already at low wind speeds. The inevitable cooling of the saturated flue gas flues and chimney causes condensation to collect on which you want to arrange a chimney condensate "pot" or siphon elbows with neutralizer "sour" condensate. The main problems with this occur in the winter under the terms neobmerzaniya kondensatootvodnogo node at negative ambient temperatures.
These cold climates modes chimneys at outside temperatures below -30 ° C will inevitably result in frosting of the chimney and the formation of ice uninsulated areas, so insulation output areas and open gaskets chimneys is mandatory.
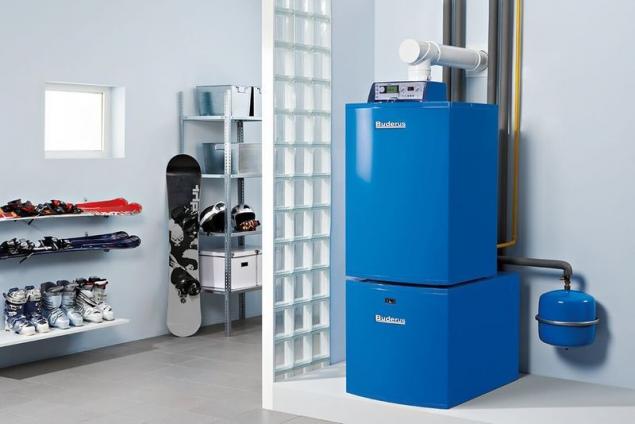
This condition requires the installation of flues and chimney in a heated room with heat and waterproofing or for a group of chimney (one to two boilers) mandatory install it completely in a heated room (inside the building).
The ducts drain the condensate from the flue pipe to the boiler bias through kondensatootvodny boiler unit. For flues and chimneys condensing boilers, for the reasons stated, is almost completely eliminated coaxial scheme smoke and air supply to the combustion even if the internal insulation of flues and chimneys. Under the terms of corrosion resistance, prevent steam, and moisture permeability and heat resistance to condensing boilers the most widespread flues and chimneys are made of polypropylene and stainless steel.
Calculations have shown that the operational efficiency of condensing wall of thermal blocks in different climatic conditions higher than "traditional" stand-alone heat generators up to 6-8%, which corresponds to the annual cycle of the same fuel economy.
Given that condensing boilers cost exceeds the value of "traditional" at 35-100%, and to develop an autonomous heating system must be in the low-temperature coolant (with a corresponding increase of capital investments in the heating system), to pay off an autonomous heating system using a condensing boiler at reduced costs, will about 3-5 years old.
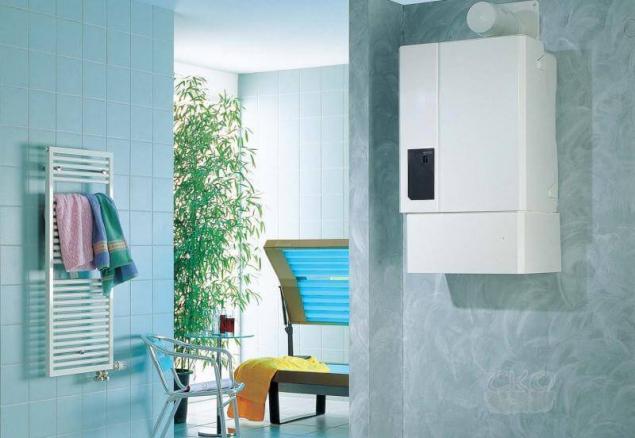