606
APWorks showed 35-pound elektromototsikl out of 3D-printers
APWorks, a subsidiary of Airbus Group, presented a fully functional motorcycle, printed the 3D-printer. Vehicle Light Rider frame is made of a composite material developed by Scalmalloy and weighs only 6 kilograms. The weight of all the motorcycle - 35 kilograms. The company claims that the 6-kilowatt electric motorcycle can accelerate it to 80 kilometers per hour in seconds.
The company's specialists have optimized APWorks motorcycle frame structure and using a special aluminum alloy to make it strong enough for daily loads and normal driving scenarios, but at the same time to reduce the weight to a minimum.
APWorks in Scalmalloy used material. According to him the company itself, it is light as aluminum, and plastic, such as titanium. This is one of the new material at the moment, which has developed Airbus Group. The alloy consists of aluminum, magnesium, scandium - AlMgSc. Scandium in combination with other metals gives strength at constant weight, so it is often used in the aerospace industry. It was used in the construction of station "Mir" and the International Space Station.
One example of the use APWorks material - is now made with Autodesk partition separating the passenger compartment from the onboard aircraft cuisine. The new version weighs 30 kilograms instead of the old 65 kilograms, which is more than twice better. The form of the frame walls designed to withstand the required load.
What is important is not only the material. Shape optimization elektromototsikl frame made him look like a skeleton. The material itself is light enough to frame weighed only 6 kg. Motorcycle equipped with a 6-kilowatt motor that will drive it to 80 kilometers per hour in a few seconds. On a single charge Light Rider will travel up to 60 kilometers.
To create a frame APWorks used the technology of selective laser 3D-printing, to distribute Scalmalloy powder in layers of 60 microns thickness. Frame parts - hollow, which makes it possible not only to reduce weight but also to hide the cables and screw-in point
. APWorks prints and gather 50 motorcycles Light Rider. The company asked for 50 thousand euro each. To become a proud owner of this miracle of technology, you will first need to make 2,000 euros at the expense of the manufacturer. The remaining 48 thousand have to pay later.
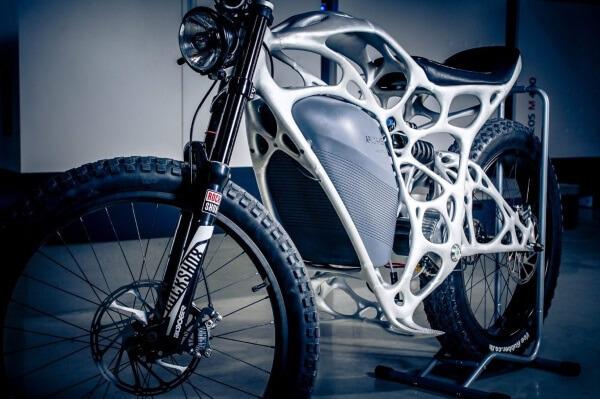
The company's specialists have optimized APWorks motorcycle frame structure and using a special aluminum alloy to make it strong enough for daily loads and normal driving scenarios, but at the same time to reduce the weight to a minimum.
APWorks in Scalmalloy used material. According to him the company itself, it is light as aluminum, and plastic, such as titanium. This is one of the new material at the moment, which has developed Airbus Group. The alloy consists of aluminum, magnesium, scandium - AlMgSc. Scandium in combination with other metals gives strength at constant weight, so it is often used in the aerospace industry. It was used in the construction of station "Mir" and the International Space Station.
One example of the use APWorks material - is now made with Autodesk partition separating the passenger compartment from the onboard aircraft cuisine. The new version weighs 30 kilograms instead of the old 65 kilograms, which is more than twice better. The form of the frame walls designed to withstand the required load.
What is important is not only the material. Shape optimization elektromototsikl frame made him look like a skeleton. The material itself is light enough to frame weighed only 6 kg. Motorcycle equipped with a 6-kilowatt motor that will drive it to 80 kilometers per hour in a few seconds. On a single charge Light Rider will travel up to 60 kilometers.
To create a frame APWorks used the technology of selective laser 3D-printing, to distribute Scalmalloy powder in layers of 60 microns thickness. Frame parts - hollow, which makes it possible not only to reduce weight but also to hide the cables and screw-in point
. APWorks prints and gather 50 motorcycles Light Rider. The company asked for 50 thousand euro each. To become a proud owner of this miracle of technology, you will first need to make 2,000 euros at the expense of the manufacturer. The remaining 48 thousand have to pay later.