1632
Production of laminated veneer lumber
The question of their own living space arises sooner or later everyone. Concerned about this problem and including me. Recently, after visiting the exhibition devoted to the construction of a house I was interested in the question of what and how to make building materials for a simple wooden house, which at a price more affordable than the cheapest odnushka in the capital.
Continued under the cut
It all starts with the fact that the plant received here such bags with wooden planks. Production specialist before starting the production cycle checks each such packet for compliance. Selectively checked the boards and after confirming the quality they are sent to the first stage. If the percentage of defects and suchkovin on workpieces exceed the permissible limits, then the packet is sent back to the supplier.
Raw material from which will be made lumber - pine and spruce.
The territory of the plant is not small, the distance can be seen under construction building, which will produce more blanks than in other shops.
After the boards are chosen they are collected in a drying package - a set of blanks to be placed in the drying chamber. Boards pre overtighten this tape to the drying process, they are not distorted.
In the production of 6 drying chambers up to 75 cubic meters
Look inside.
Packages boards are in the chamber for 6-8 days at a temperature of 65-68 degrees. The drying chamber is equipped with sensors, humidity, temperature, to keep track of the right technology drying boards.
This photo svezheskleennogo not treated timber, you can see how the boards of various sizes make a single durable timber. On it I'll continue.
But back to production. After drying, the package with the boards gets to the shop.
Here it passes through the machine, which is planed board on all four sides. At this stage, the workers carried out a visual check of each board re-checked for defects and suchkovin. Immediately determined what the board will go on the inside and outside of the future timber. More interesting board suchkovin fewer are on the outer side.
As I said, the board of which is timber from pine and spruce. Since they are similar in structure to the fibers, they can be glued together without any problems with each other. And some more information for observation - spruce and pine boards can be distinguished by suchkovinam - pine they are larger than spruce.
Next, glue the boards. Here, the device has been disconnected because the image can be from a nearby shop to see gluing machine to work.
That's the rain adhesive covers the board with one hand.
Excess is removed roll. Depending on each individual order cant make / glue the boards of several different lengths and widths. I almost forgot to say - in the production of timber for future use do not do. Its production starts only after the customer has ordered the house (already prepared the foundation) or individual parts.
Adhesive used in the production has been certified for safety and does not contain formaldehyde and hazardous substances to humans.
In this barrel curing agent, which is mixed with glue immediately before gluing.
After the glue boards are lubricated and properly routed, they are placed under the press, which are 40 minutes. Then they were removed and their "rest" two hours before they reach the next stage.
Further, the workpiece move to the next stage, but not before harvesting timber again passes through the machine, which processes it on all four sides.
It looks like after the timber profiling, but that's not all. As you can see the ends of the uneven bars and do not cut into the desired parts.
By the way, the accuracy of the cutting profile is determined by such laser sensors.
Tried to burn the notes, but for some reason it did not work.
Another nice detail - a cooler with cool water. A very necessary thing in the production.
But we digress. Further beam falls on a machine that cuts the face and ...
bowl cuts - groove in the rod required for transverse assembly. Bowl, by the way, the only place that will be charged to the insulation. When assembling the walls of the house insulation is not only used at the junction.
Well, that and prepare the items for the home. The ends are processed mechanical sealant.
And this is a complete package for the home. Such single-house will be a few.
Each item is marked with a piece of paper with a barcode, which contains all the information about the tool bar, to the point where it needs to be laid in the house.
And one more detail: after the preparation of each such party for a specific project, made reference sections, which are then explored in plant laboratory for compliance. The slice is heated and cooled to a predetermined temperature for 50 cycles to simulate winter and summer, i.e. building of this theoretically timber 50 can stand.
The process monitors and camera, which, as I said shows the production process online visitors factory.
The monitor displays the details of the production process. In photos - projects that are carried out at the moment.
An example of this sample, which stands in the workshop can be seen as the angle of the walls of the house looks. These pins are held together only by iron angles, and the rest length of the wall beams is placed on the wooden pins.
Go to the next step. Here finished lumber treated with an antiseptic for fire-biosecurity. It protects it from bugs, bark beetles, mold, rot, and prevents the house from fire. Must specify that the action of antiseptics is certainly not forever, but it retains the properties of the beam for some time, and in the case of fire, the house does not ignite as a match because in the processing of wood preservative derived oxygen.
If necessary timber can take antiseptic baths.
After this stage, it can be said that the production process and the preparation timber for the customer is completed. But that's not all.
After processing the antiseptic timber harvested again in such packets ready to be sent to the client.
On each packet of information about the customer and the content. Note the words "min. crown 20 "and" max. crown 43 "- this means that in this package there are details that are suitable for assembly on 20" layer "of the walls to 43. This is in order not to open all packages in search of the necessary components - all of which can be in one package up to a certain stage of assembly.
We saw almost the entire chain of production, however, is not finished our tour, we go to the next shop to find out some more details. By the way, pay attention to this house, here is one of the offices of the company, which employs sales staff, call center professionals, architects and designers. As you know, it is completely made on this production and assembled employees of the company.
The next workshop production of more size, there are newer, German machines doing here beam up to 12 meters and superbrus with an area of more than the ones we've seen before.
In this workshop timber also made of individual boards which are spliced by means of adhesive in long board.
Lots of boards with defects and suchkovinami that can damage future product cut. In this photo - waste production.
And it is ready to board, of which will be glued beams. Here there is all the same process chain that we've seen before, because I will not repeat.
Trinadtsatimetrovy press.
After processing, the boards, their ends are cut "herringbone" and further when pasting machine with pressure presses the boards to each other. That's enough to glue the board.
Well, after the board glued to the timber, processed, and on this machine cut profile. And add that board, glued together from separate boards of various sizes are stronger than from solid planks, because the wood shrinks over time, and it increases the voltage between the other glued boards, and the short-cut blanks completely minimize this effect. Cross beams when building a house, too, made from such timber, on a mandatory basis.
Here superbrus. By the way, a customer who orders a timber for your home, select the size of the cross section to your taste. Here, the company can help him decide on a project, or create your own project with the architect and engineers Good Wood.
This superstanok Hundeggera that at this point cuts the cup in the rod.
Noticed that in the shops works well ventilation and dust, which is inevitable in such activities does not hang in the air for a long time.
With dust and tiny filings are also struggling and humidifiers. The good thing is, you have to make yourself at home.
Although there are production waste in the form of scraps, we can say that it is virtually non-waste production (in economic terms), because wood is not suitable for timber production is sold as fuel for the fire, and used for their own needs, as well as fuel.
Sawdust briquettes made here are for kindling fireplaces.
At the end of the tour again I found ready-made bags for drying oven.
In this capacity gather dust production.
Finally, let us enter into a small two-story house at the company who can view anyone. Looks nice.
I almost forgot to mention the house for their clients collect only the company's specialists, from laying the foundation to roofing and installation of the boiler, and the like, which is very convenient.
It has its own boiler room, which is important.
House is made of the simple beam. Sure enough, after assembly of the house have to paint it to keep its properties. Incidentally, an advantage over the conventional timber in a log that eventually timber shrinks only 1-2% and the beam - 15%! Besides whole timber can not be dried without deformation.
Very spacious and bright kitchen.
Smoothly flows into the living room. The toilet and the bathroom did not look, because at this point they were interested potential buyers, wandering around the house).
On the ground floor there is living rooms, because the area of the house is quite small. And on the second floor are three. The first two - children's rooms.
The third room - bedroom for the parents.
Posted in [mergetime] 1400819912 [/ mergetime]
Now you know how to make a timber for house construction. Thanks to everyone who read to the end.
Materials escogido7
I have all
Continued under the cut
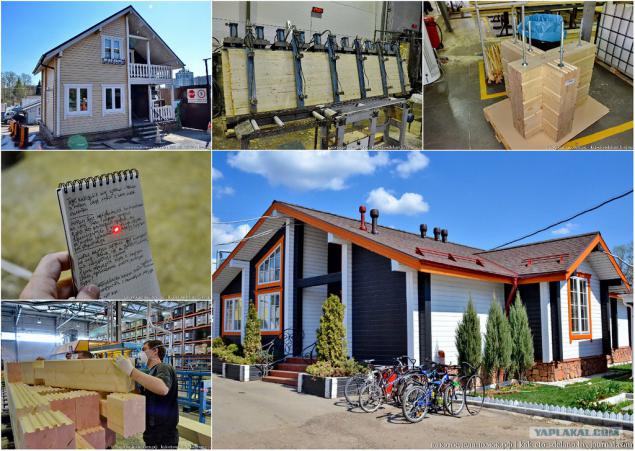
It all starts with the fact that the plant received here such bags with wooden planks. Production specialist before starting the production cycle checks each such packet for compliance. Selectively checked the boards and after confirming the quality they are sent to the first stage. If the percentage of defects and suchkovin on workpieces exceed the permissible limits, then the packet is sent back to the supplier.
Raw material from which will be made lumber - pine and spruce.
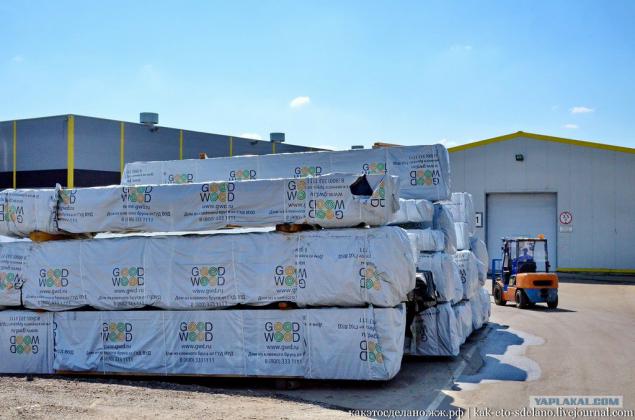
The territory of the plant is not small, the distance can be seen under construction building, which will produce more blanks than in other shops.
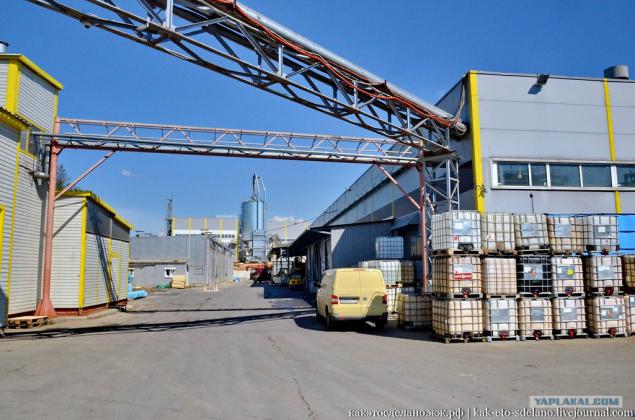
After the boards are chosen they are collected in a drying package - a set of blanks to be placed in the drying chamber. Boards pre overtighten this tape to the drying process, they are not distorted.
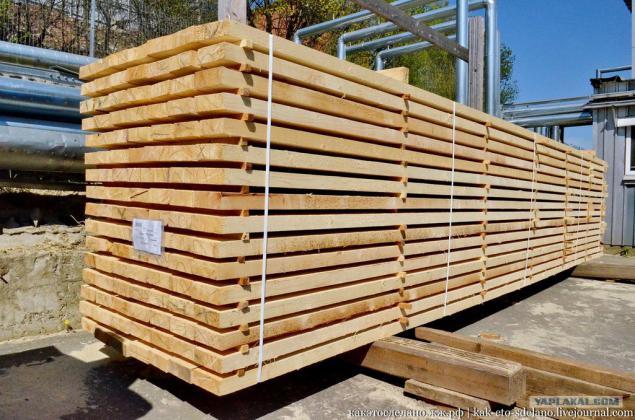
In the production of 6 drying chambers up to 75 cubic meters
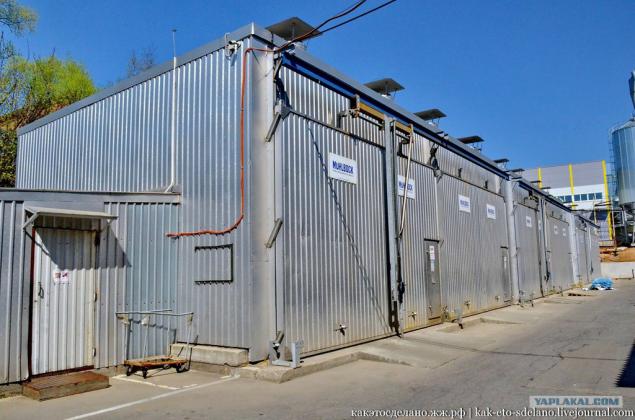
Look inside.
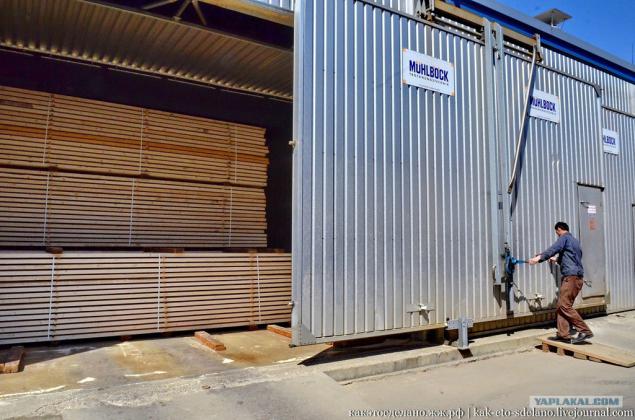
Packages boards are in the chamber for 6-8 days at a temperature of 65-68 degrees. The drying chamber is equipped with sensors, humidity, temperature, to keep track of the right technology drying boards.
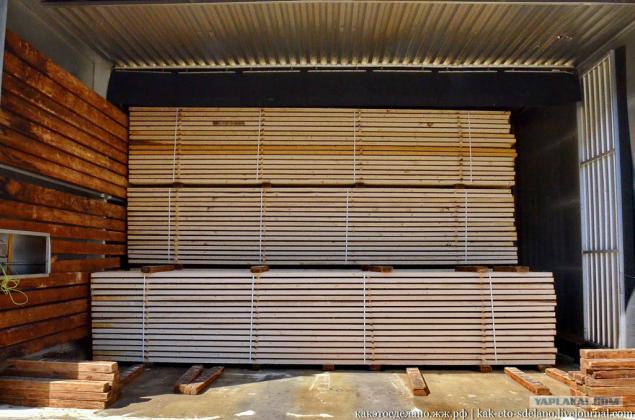
This photo svezheskleennogo not treated timber, you can see how the boards of various sizes make a single durable timber. On it I'll continue.
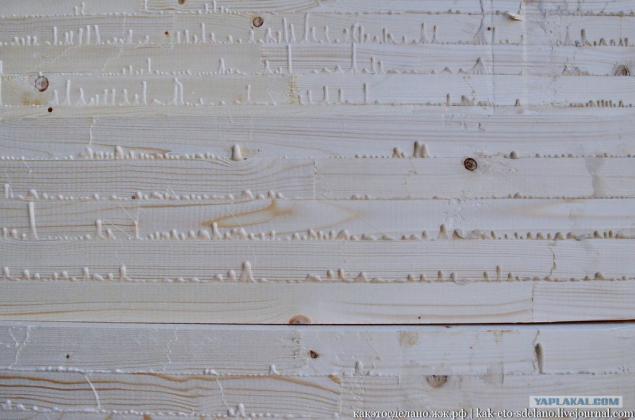
But back to production. After drying, the package with the boards gets to the shop.
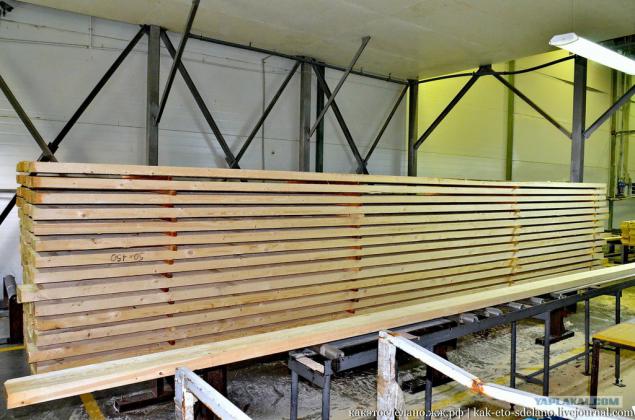
Here it passes through the machine, which is planed board on all four sides. At this stage, the workers carried out a visual check of each board re-checked for defects and suchkovin. Immediately determined what the board will go on the inside and outside of the future timber. More interesting board suchkovin fewer are on the outer side.
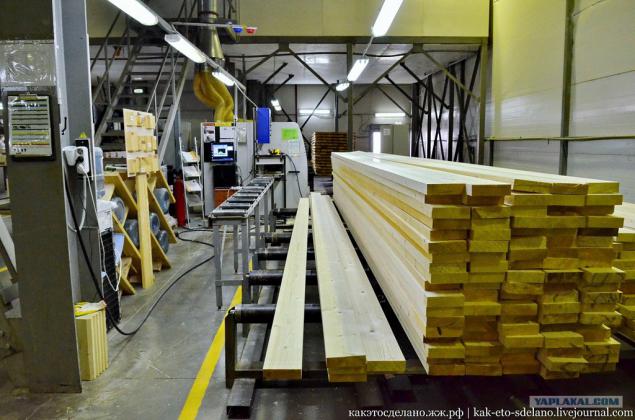
As I said, the board of which is timber from pine and spruce. Since they are similar in structure to the fibers, they can be glued together without any problems with each other. And some more information for observation - spruce and pine boards can be distinguished by suchkovinam - pine they are larger than spruce.
Next, glue the boards. Here, the device has been disconnected because the image can be from a nearby shop to see gluing machine to work.
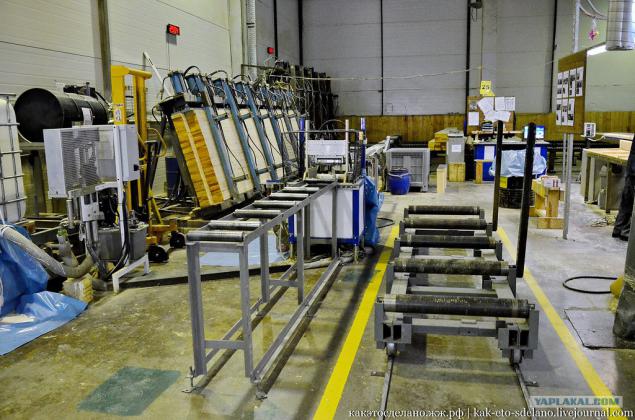
That's the rain adhesive covers the board with one hand.
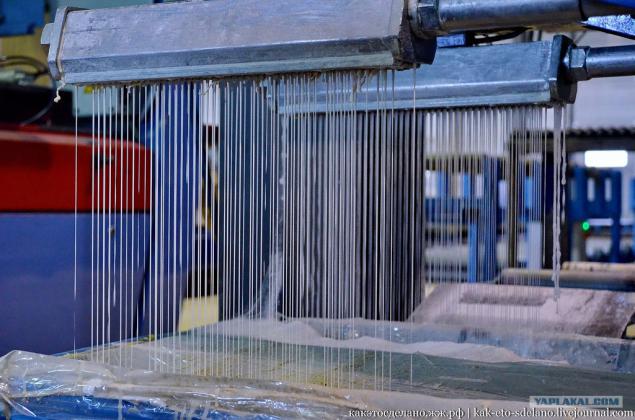
Excess is removed roll. Depending on each individual order cant make / glue the boards of several different lengths and widths. I almost forgot to say - in the production of timber for future use do not do. Its production starts only after the customer has ordered the house (already prepared the foundation) or individual parts.
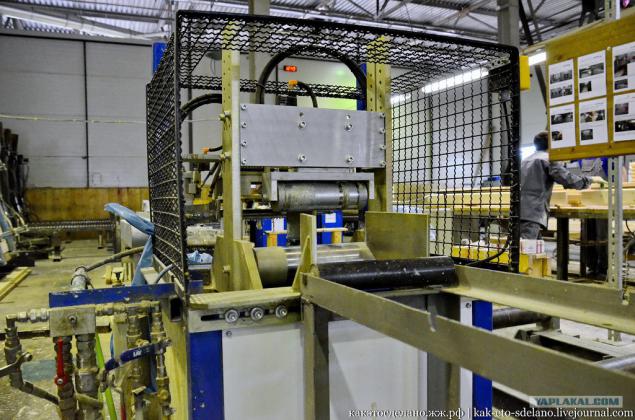
Adhesive used in the production has been certified for safety and does not contain formaldehyde and hazardous substances to humans.
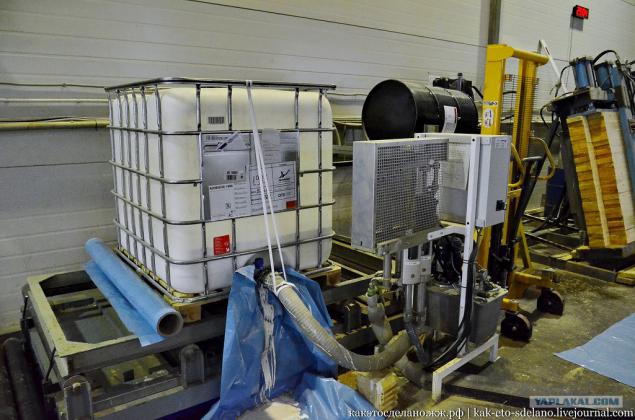
In this barrel curing agent, which is mixed with glue immediately before gluing.
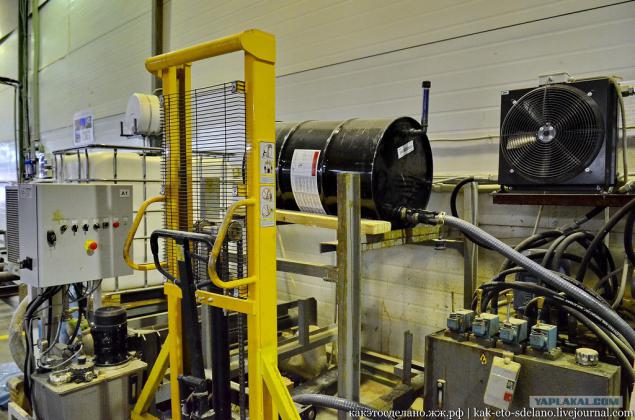
After the glue boards are lubricated and properly routed, they are placed under the press, which are 40 minutes. Then they were removed and their "rest" two hours before they reach the next stage.
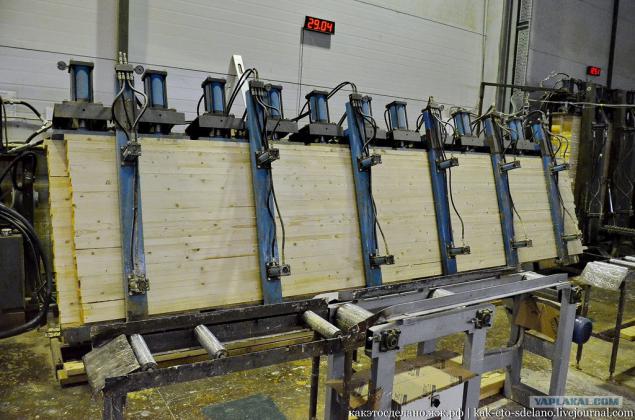
Further, the workpiece move to the next stage, but not before harvesting timber again passes through the machine, which processes it on all four sides.
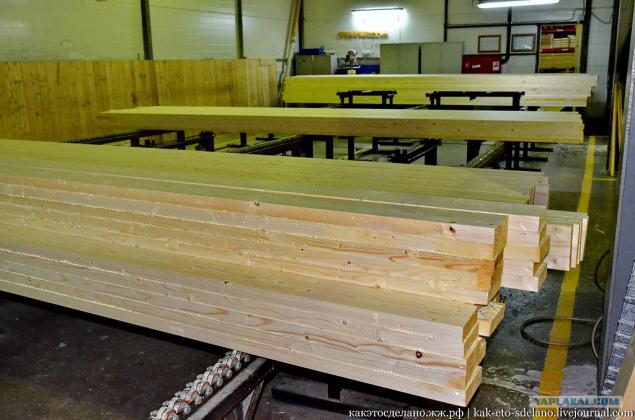
It looks like after the timber profiling, but that's not all. As you can see the ends of the uneven bars and do not cut into the desired parts.
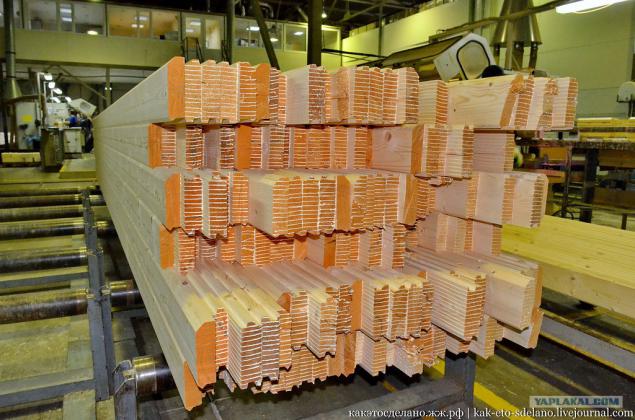
By the way, the accuracy of the cutting profile is determined by such laser sensors.
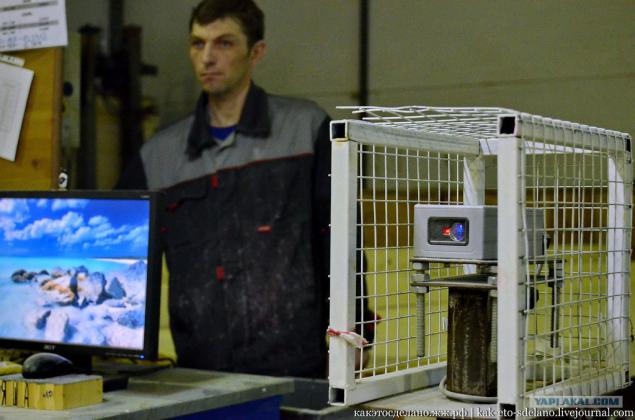
Tried to burn the notes, but for some reason it did not work.
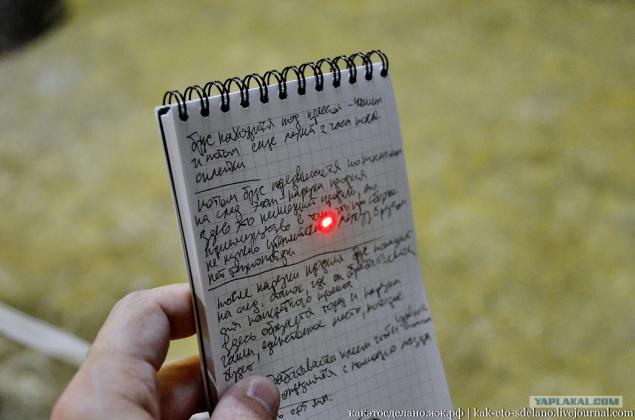
Another nice detail - a cooler with cool water. A very necessary thing in the production.
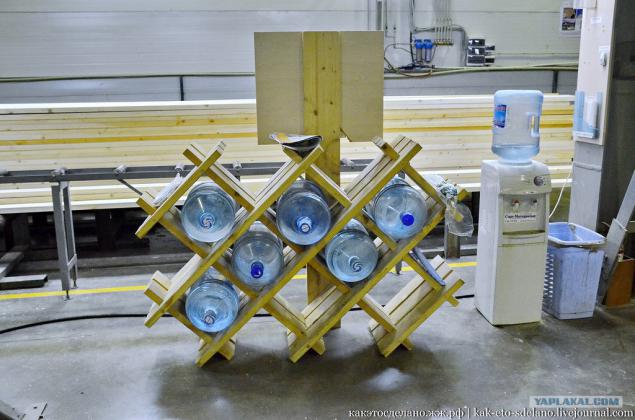
But we digress. Further beam falls on a machine that cuts the face and ...
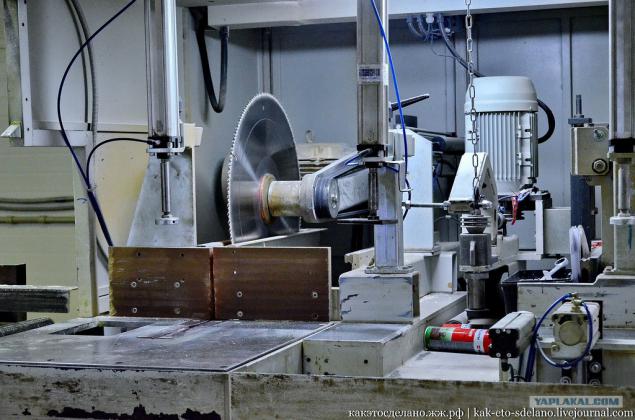
bowl cuts - groove in the rod required for transverse assembly. Bowl, by the way, the only place that will be charged to the insulation. When assembling the walls of the house insulation is not only used at the junction.
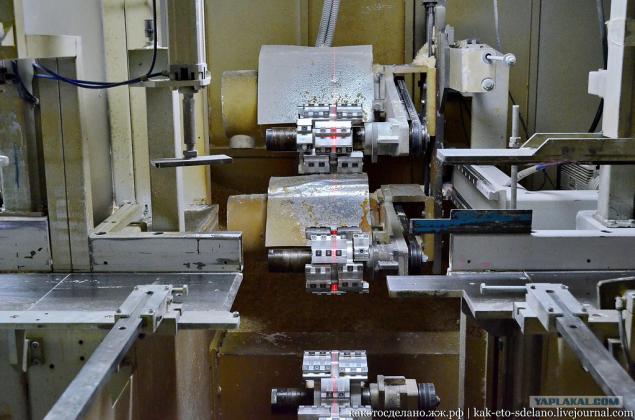
Well, that and prepare the items for the home. The ends are processed mechanical sealant.
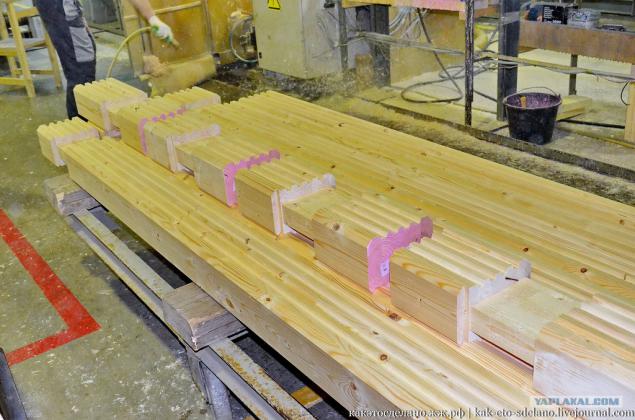
And this is a complete package for the home. Such single-house will be a few.
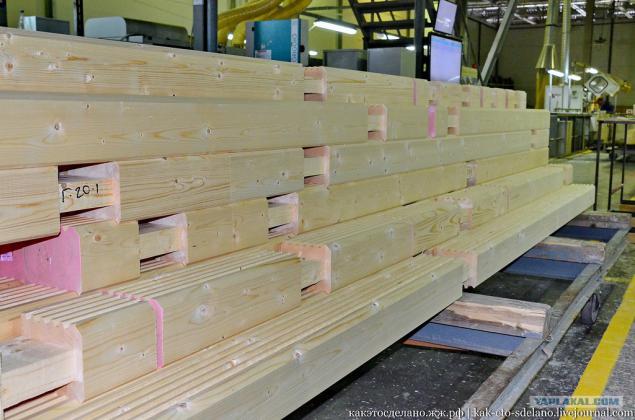
Each item is marked with a piece of paper with a barcode, which contains all the information about the tool bar, to the point where it needs to be laid in the house.
And one more detail: after the preparation of each such party for a specific project, made reference sections, which are then explored in plant laboratory for compliance. The slice is heated and cooled to a predetermined temperature for 50 cycles to simulate winter and summer, i.e. building of this theoretically timber 50 can stand.
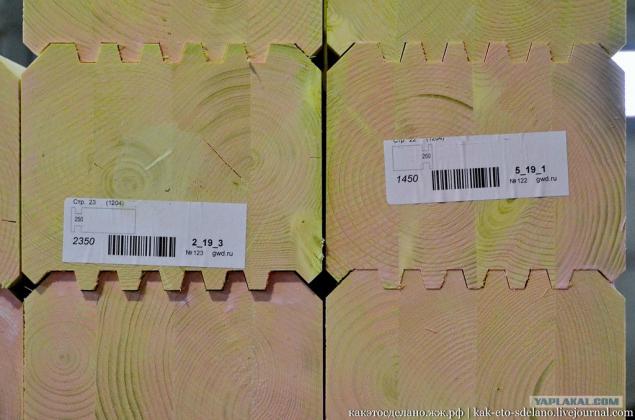
The process monitors and camera, which, as I said shows the production process online visitors factory.
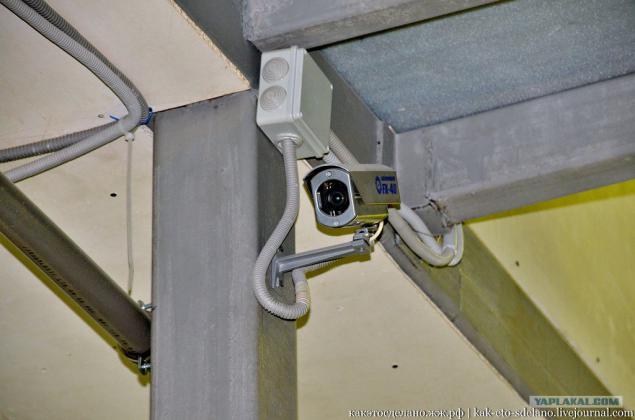
The monitor displays the details of the production process. In photos - projects that are carried out at the moment.
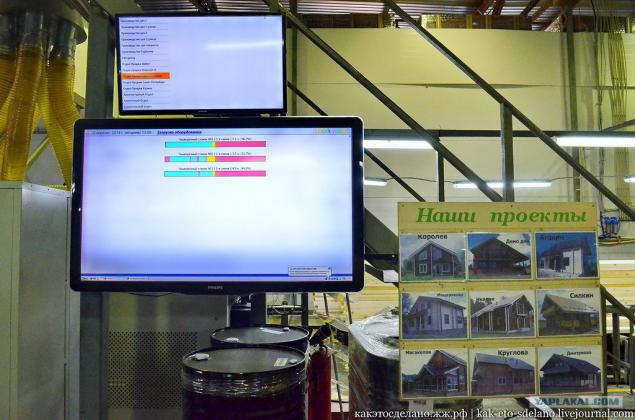
An example of this sample, which stands in the workshop can be seen as the angle of the walls of the house looks. These pins are held together only by iron angles, and the rest length of the wall beams is placed on the wooden pins.
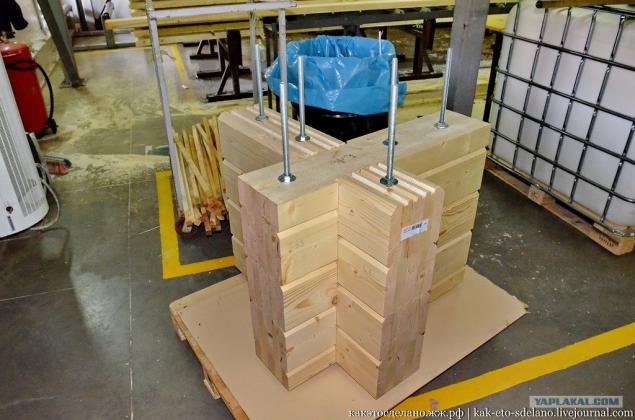
Go to the next step. Here finished lumber treated with an antiseptic for fire-biosecurity. It protects it from bugs, bark beetles, mold, rot, and prevents the house from fire. Must specify that the action of antiseptics is certainly not forever, but it retains the properties of the beam for some time, and in the case of fire, the house does not ignite as a match because in the processing of wood preservative derived oxygen.
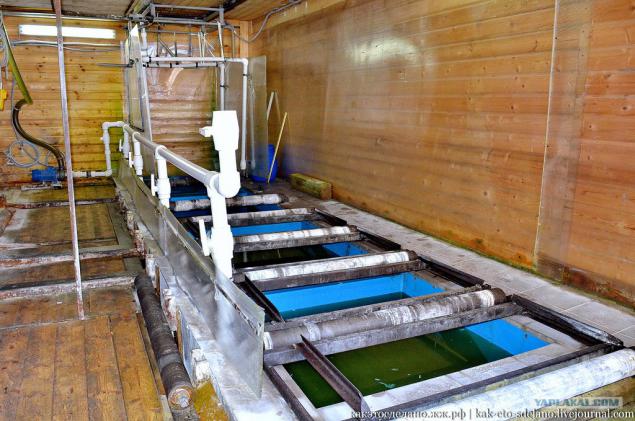
If necessary timber can take antiseptic baths.
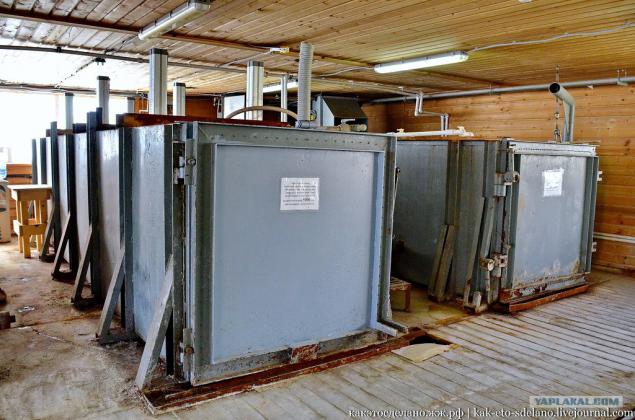
After this stage, it can be said that the production process and the preparation timber for the customer is completed. But that's not all.
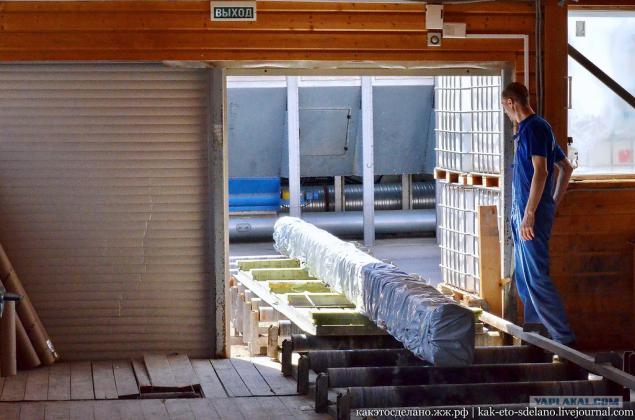
After processing the antiseptic timber harvested again in such packets ready to be sent to the client.
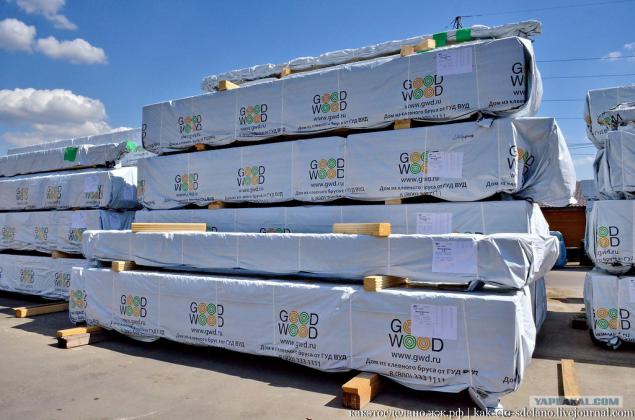
On each packet of information about the customer and the content. Note the words "min. crown 20 "and" max. crown 43 "- this means that in this package there are details that are suitable for assembly on 20" layer "of the walls to 43. This is in order not to open all packages in search of the necessary components - all of which can be in one package up to a certain stage of assembly.
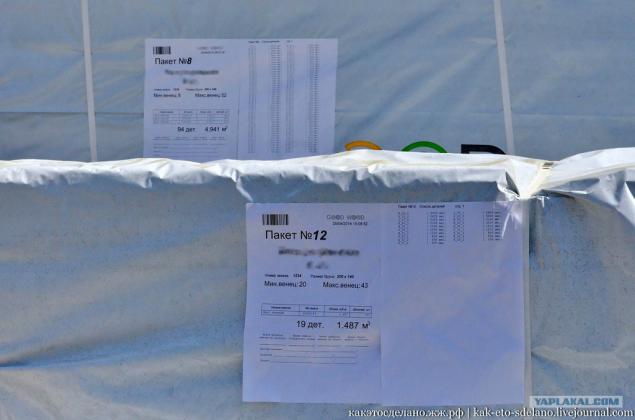
We saw almost the entire chain of production, however, is not finished our tour, we go to the next shop to find out some more details. By the way, pay attention to this house, here is one of the offices of the company, which employs sales staff, call center professionals, architects and designers. As you know, it is completely made on this production and assembled employees of the company.
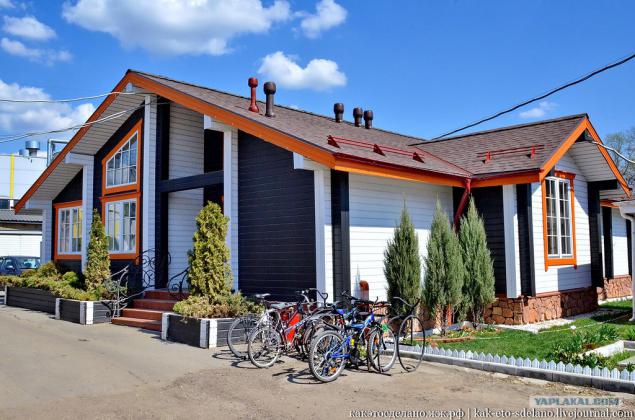
The next workshop production of more size, there are newer, German machines doing here beam up to 12 meters and superbrus with an area of more than the ones we've seen before.
In this workshop timber also made of individual boards which are spliced by means of adhesive in long board.
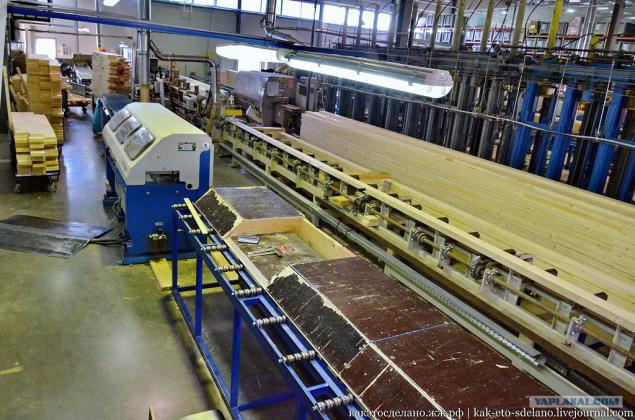
Lots of boards with defects and suchkovinami that can damage future product cut. In this photo - waste production.
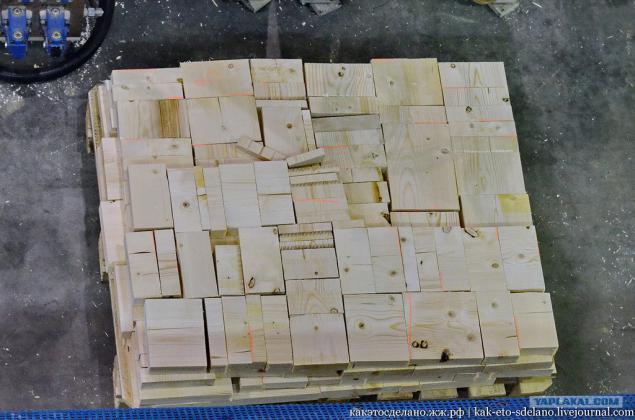
And it is ready to board, of which will be glued beams. Here there is all the same process chain that we've seen before, because I will not repeat.
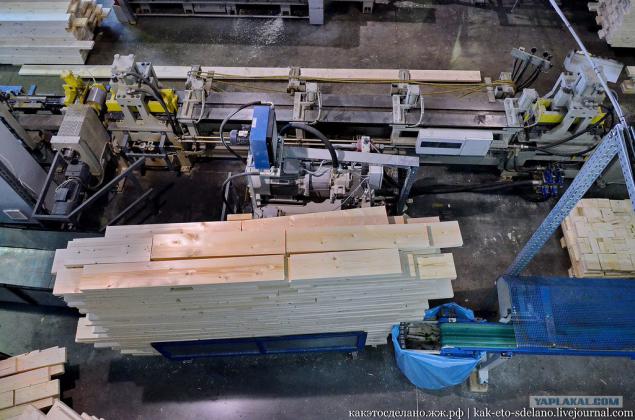
Trinadtsatimetrovy press.
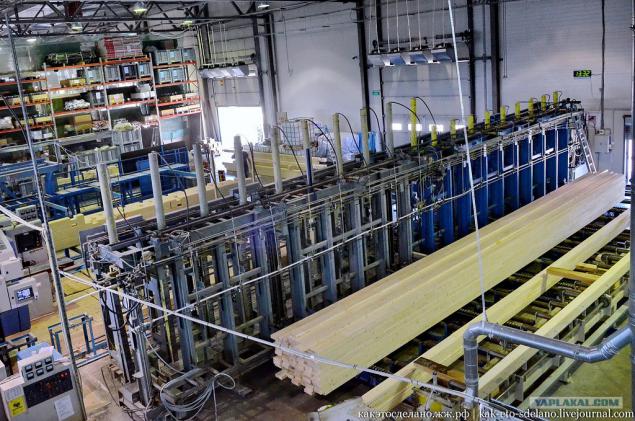
After processing, the boards, their ends are cut "herringbone" and further when pasting machine with pressure presses the boards to each other. That's enough to glue the board.
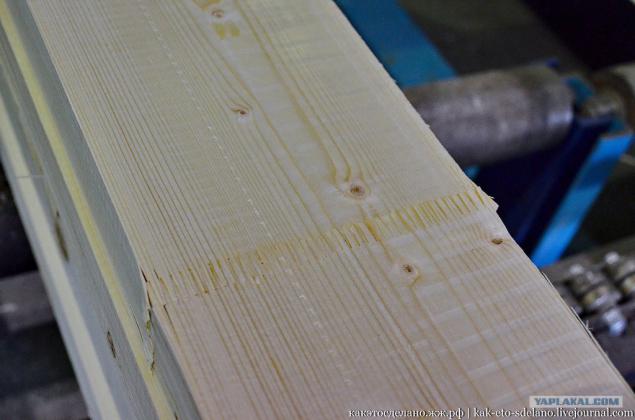
Well, after the board glued to the timber, processed, and on this machine cut profile. And add that board, glued together from separate boards of various sizes are stronger than from solid planks, because the wood shrinks over time, and it increases the voltage between the other glued boards, and the short-cut blanks completely minimize this effect. Cross beams when building a house, too, made from such timber, on a mandatory basis.
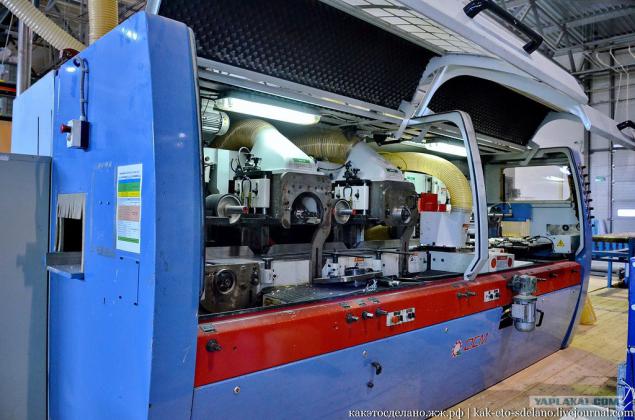
Here superbrus. By the way, a customer who orders a timber for your home, select the size of the cross section to your taste. Here, the company can help him decide on a project, or create your own project with the architect and engineers Good Wood.
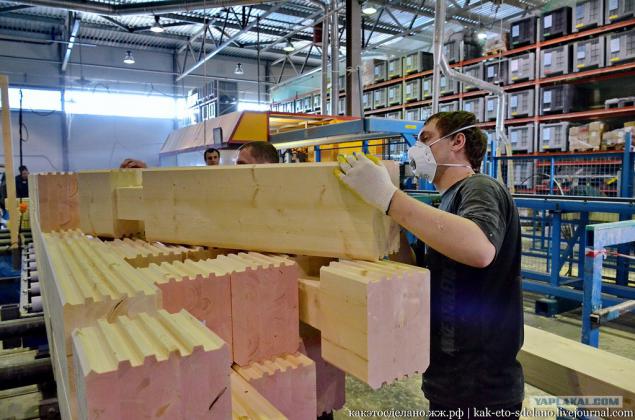
This superstanok Hundeggera that at this point cuts the cup in the rod.
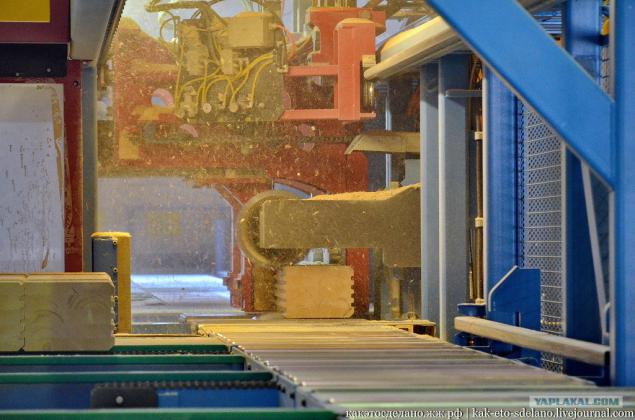
Noticed that in the shops works well ventilation and dust, which is inevitable in such activities does not hang in the air for a long time.

With dust and tiny filings are also struggling and humidifiers. The good thing is, you have to make yourself at home.
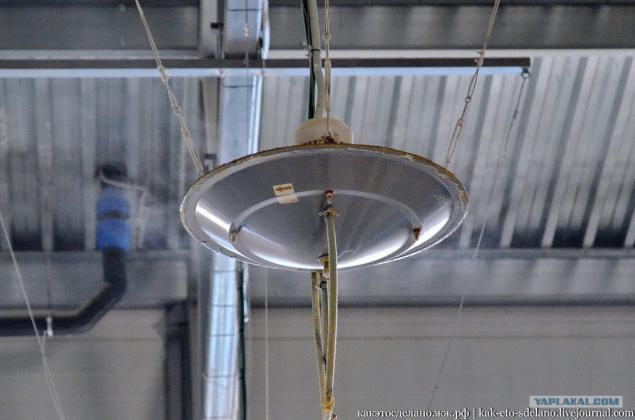
Although there are production waste in the form of scraps, we can say that it is virtually non-waste production (in economic terms), because wood is not suitable for timber production is sold as fuel for the fire, and used for their own needs, as well as fuel.
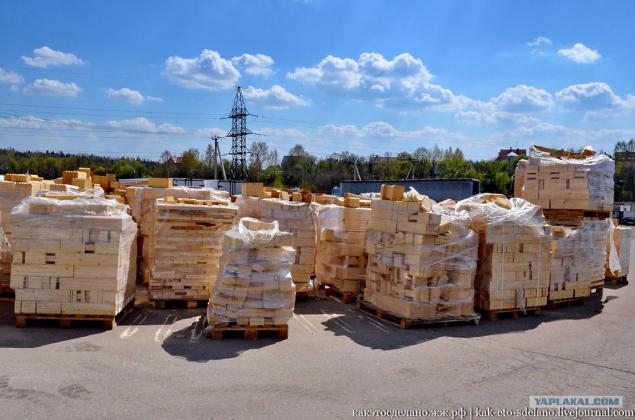
Sawdust briquettes made here are for kindling fireplaces.
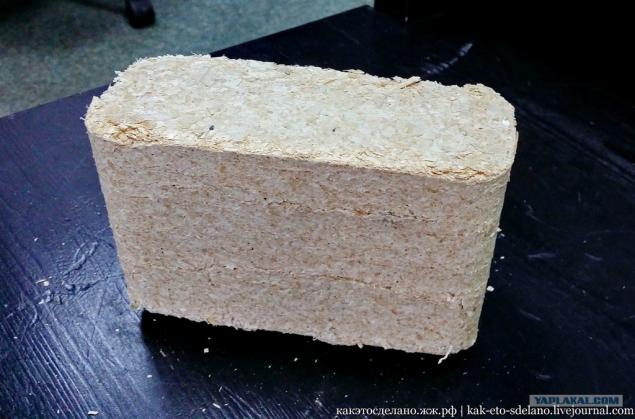
At the end of the tour again I found ready-made bags for drying oven.
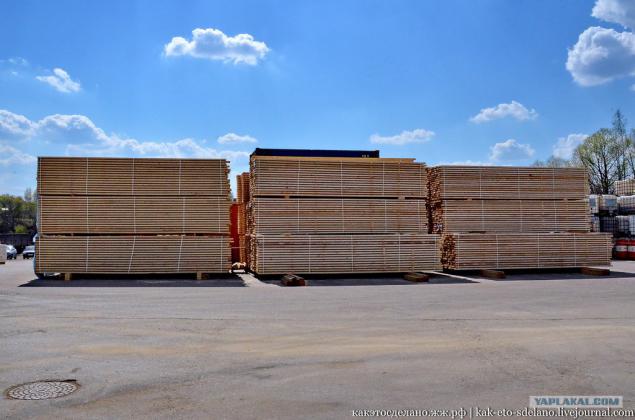
In this capacity gather dust production.
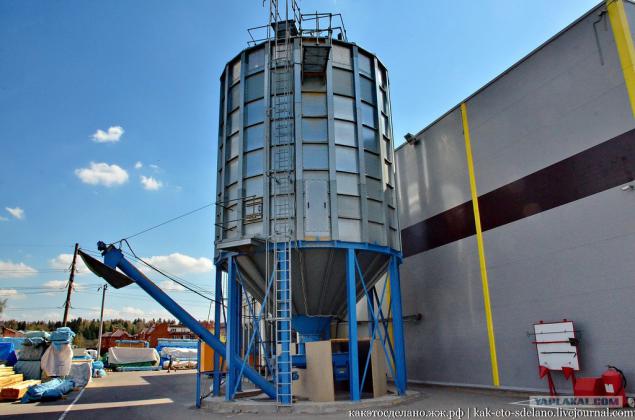
Finally, let us enter into a small two-story house at the company who can view anyone. Looks nice.
I almost forgot to mention the house for their clients collect only the company's specialists, from laying the foundation to roofing and installation of the boiler, and the like, which is very convenient.
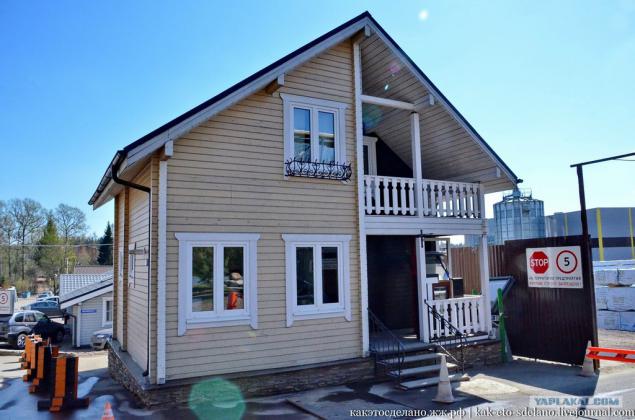
It has its own boiler room, which is important.
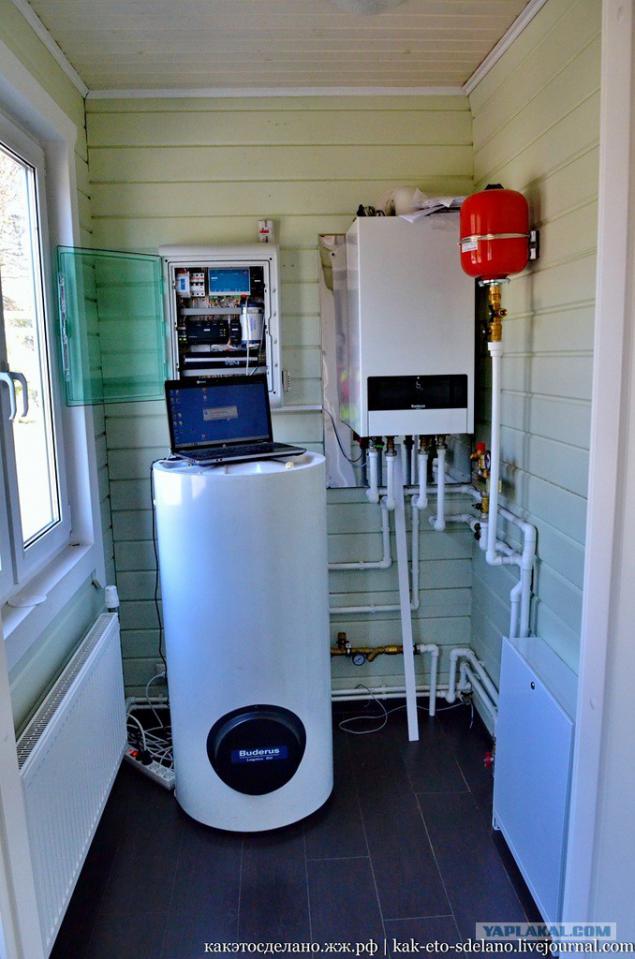
House is made of the simple beam. Sure enough, after assembly of the house have to paint it to keep its properties. Incidentally, an advantage over the conventional timber in a log that eventually timber shrinks only 1-2% and the beam - 15%! Besides whole timber can not be dried without deformation.
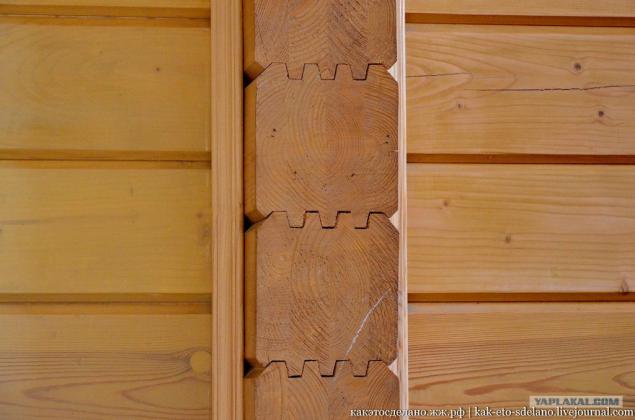
Very spacious and bright kitchen.
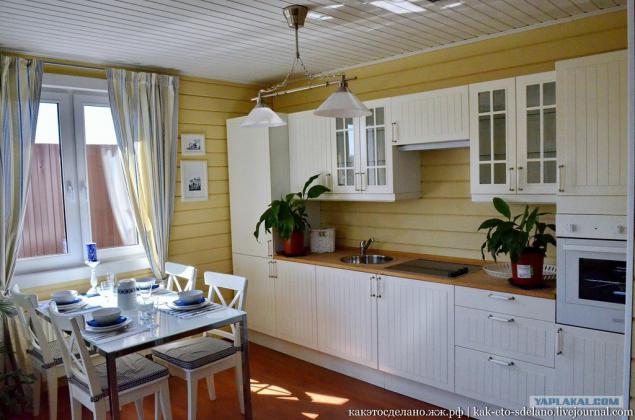
Smoothly flows into the living room. The toilet and the bathroom did not look, because at this point they were interested potential buyers, wandering around the house).
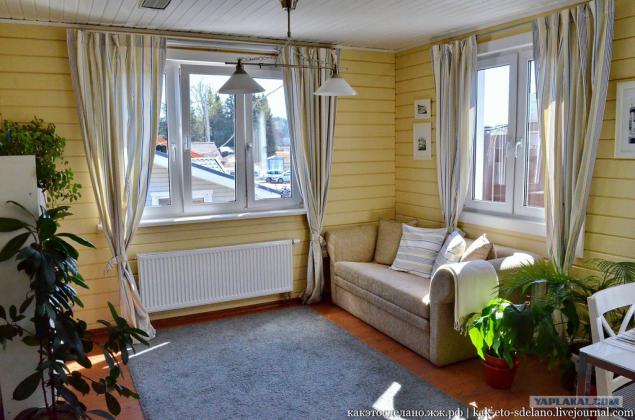
On the ground floor there is living rooms, because the area of the house is quite small. And on the second floor are three. The first two - children's rooms.
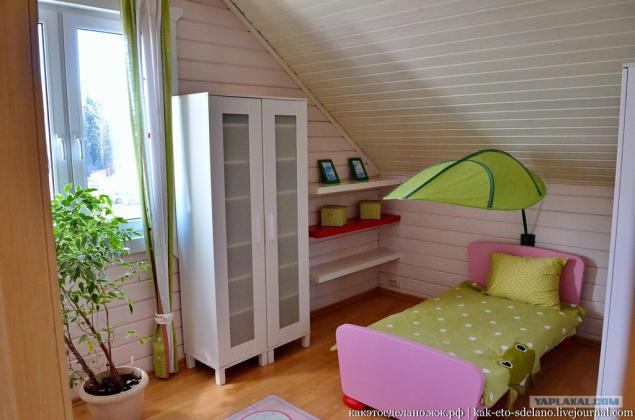
The third room - bedroom for the parents.
Posted in [mergetime] 1400819912 [/ mergetime]
Now you know how to make a timber for house construction. Thanks to everyone who read to the end.
Materials escogido7
I have all
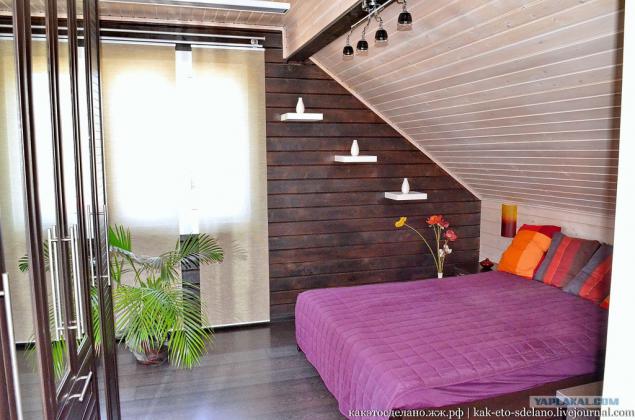