2295
Iron ore
Today, along with the author of this photo essay, we are going in the Lebedinsky Mining and Processing Plant. Under the cut you will learn how to extract iron ore and what happens to her after she came to the plant in the middle of a career is a mountain with waste rock, around which all the extracted ore containing iron. In the near future it is planned to blow it up piece by piece and take out of the pit.
First talk about the pit itself. Lebedinsky GOK - is Russia's largest mining and enrichment of iron ore and has the world's largest open pit iron ore. The plant and quarry located in the Belgorod region, between the towns of Stary Oskol and Gubkin. View of the top careers. It really is huge and growing every day. The depth of the pit of Lebedinsky GOK - 250 m above sea level or 450 m - from the surface of the earth (and the diameter - 4 to 5 kilometers), it is constantly seeping groundwater, and if not for the pumps, it is filled to the top for the month. He twice recorded in the Guinness Book of Records as the largest quarry of non-combustible mineral resources.
Little official information: Lebedinsky GOK is a concern, "Metalloinvest" and is a leading producer of iron ore products in Russia. In 2011, the share of concentrate combine to total annual production of iron ore concentrate and sinter ore in Russia was 21%. In a career running a lot of all kinds of techniques, but the most noticeable of course multi-ton dump trucks "BelAZ" and «Caterpillar».
In the year, both the plant belonging to the company (Lebedinsky GOK and Mikhailovsky) produce about 40 million. Tons of iron ore in the form of concentrate and sinter ore (it's not the volume of production, and have enriched ore, that is separated from the waste rock). Thus it appears that in two GOKah day produced an average of about 110 thousand tons of iron ore concentrate. This kid at a time carries up to 220 tons (!) Of iron ore.
Excavator gives a signal and gives it gently back up. Just a few buckets and filled with giant body. Excavator again gives a signal and the truck pulls.
Recently bought "BelAZ" capacity of 160 and 220 tons (still load trucks in quarries was no more than 136 tonnes), and expected to reach excavators "Hitachi" with a bucket capacity of 23 cubic meters (currently the maximum capacity of mining excavators bucket of 12 cubic meters).
"BelAZ" and «Caterpillar» alternate. Import truck carries all the way to 180 tons. A heavy-duty dump trucks - it is a new technology, now coming to the mining companies in the framework of the investment program of "Metalloinvest" to improve the efficiency of mining and transport complex.
Interesting texture of the stone, pay attention. If I am not mistaken from left quartzite from such ore mined iron. The quarry is full of not only iron ore, but also a variety of minerals. They generally are not of interest for further processing in an industrial scale. Today, of the gangue get chalk and make rubble for construction purposes.
Every day in the career of Lebedinsky GOK operates 133 units of the main mining equipment (30 large trucks, 38 shovels, 20 burstankov 45 traction units).
Of course, I was hoping to see spectacular explosions, but even if they were held on this day, I still have not been able to enter the territory of a career. Such an explosion is done once in three weeks. All machinery safety standards (and a lot of it) before it is output from the quarry.
Lebedinsky GOK and Mikhailovsky GOK - the two largest plant for the extraction and processing of iron ore in Russia in terms of production. Company "Metalloinvest" has the second-largest proven reserves of iron ore - about 14, 6 billion tons in the international classification JORS that ensures nearly 150 years of operating period at the current level of production. So the residents of Stary Oskol and Gubkin will be employed for a long time.
Probably noticed in previous photos, the weather was not very good, was rain and fog in the career of standing. Closer to leave it a little scattered, but still not much. I pulled a photo as possible. Dimensions career certainly impressive.
Iron ore is charged immediately to the railway compositions, in special reinforced wagons that take out the ore from the mine, they are called dump cars, their carrying capacity - 105 tons.
The geological formations on which you can learn the history of the Earth.
Giant machines from the height of the observation platform seem to be no more than an ant.
Then carry the ore to the plant, where the process of separating the gangue by magnetic separation: fine ore is crushed and then sent to a magnetic drum (separator) to which, in accordance with the laws of physics all the iron sticks, not iron - washed off with water. Then from the resulting iron ore pellets and make hot briquette iron (HBI), which is then used for steelmaking. Hot briquetted iron (HBI) - a type of DRI (DRI). Material with high (& gt; 90%) iron, obtained by the technology is different from the domain processing. It is used as a raw material for steel production. High quality (with a small amount of harmful impurities) replacement of cast iron, scrap metal. Unlike iron, HBI in production is not used coal coke. Briquetted iron production process is based on the processing of iron ore (pellets), high temperatures, mostly by natural gas.
HBI within the plant simply do not you come, because the process of hot baking pies held at a temperature of about 900 degrees, and sunbathe in Stary Oskol I was not in the plans).
Lebedinsky GOK - the only producer of HBI in Russia and the CIS. The plant began production of this product in 2001, running the shop for production of HBI (HBI plant-1) with the use of technology HYL-III capacity of 1, 0 million tonnes per year. In 2007, the GOK has completed construction of the second plant for production of HBI (HBI plant-2) using the technology MIDREX with a production capacity of 1, 4 million tons per year. At present, the production capacity LGOK is 2, 4 million tons of HBI per year.
When we visited the quarry Oskol Electric Steel Works (OEMK) included in the Steel segment companies. In one of the shops of the plant produced here are steel billets. Their length can reach between 4 and 12 meters, depending on the wishes of customers.
You see sparks? In place of the bar steel is cut.
Interesting machine with a bucket called badevoz in a fused slag in the production process.
In neighboring shop OEMK grind and polished steel rods of different diameters, rolled past in another shop. By the way, this plant - the seventh largest company in Russia for the production of steel and steel produktsii.V 2011, the share of steel production in the OEMK amounted to 5% of the total steel produced in Rocsii share of rolled products was also 5%.
OEMK applies advanced technologies, including direct iron reduction and electric arc, which ensures production of high quality metal, with a reduced content of impurities.
The main consumers of steel OEMK on the Russian market are the automotive, engineering, pipe, hardware and bearing industries.
Metal OEMK exported to Germany, France, USA, Italy, Norway, Turkey, Egypt and many other countries.
The company has mastered the production of long products for the manufacture of products used by the world's leading automakers.
By the way, I am not the first time I've noticed on such industries women - crane operator.
This plant almost sterile cleanliness, not typical for such productions.
I like neatly stacked steel rods.
At the request of the customer for each product is glued sticker.
On the sticker stamped heat number and steel grade code.
The opposite end can be marked with paint, but to each packet to the manufactures tag attached to the contract number, country of destination, steel grade, heat number, size in mm, supplier name and package weight.
These products - the standard by which the equipment is configured for precise rolling.
And this machine can scan a product and detect microcracks and defects before the metal falls to the customer.
The company serious about safety.
All water used in the production of purified recently established super-modern equipment.
This installation of sewage treatment plant. After treatment, it is cleaner than the river, where it was released.
Engineering water almost distilled. As with any process water can not drink it, but once you can try, it is not dangerous to health.
The next day we went to Zheleznogorsk, located in the Kursk region. That there is Mikhailovsky GOK. In the picture - under construction complex roasting machine №3. It will produce pellets.
Its construction will be invested 450 million. Dollars. The company will be built and put into operation in 2014
This layout of the plant.
Then we went to the careers of Mikhailovsky GOK. Depth MGOKa career - more than 350 meters above ground, and its size - 3 to 7 kilometers. Its territory is actually three career can be seen in the picture from a satellite. One large and two smaller ones. After about 3-5 years the quarry will grow so much that would be a great one, and maybe catch up in size Lebedinsky pit.
In a career involved 49 trucks, 54 of traction unit 21 diesel locomotive, 72 excavators, 17 drilling rigs, 28 bulldozers and graders 7. The rest of the extraction of ore in the GOK is not different from LGOK.
At this time, we still managed to get to the plant, where iron ore concentrate is converted to the final product - Pellets ... Pellets - lumps of crushed ore concentrate. Semi-finished steel production of iron. It is a product of the enrichment of iron ore concentrating special ways. It is used in blast furnaces to produce pig iron.
For the production of iron ore pellets used. For initial removal of mineral impurities (crude) and finely ground ore is enriched by various methods. The process of manufacturing pellets is often called "balling". The charge that is a mixture of finely chopped concentrates of iron mineral flux (additives regulating the composition of the product), and reinforcing additives (usually bentonite), moistened and subjected to pelletizing in rotating bowls (pellet) or drums-pelletizers. They are the most in the picture.
Come closer.
As a result, pelletizing get close to spherical particles with a diameter of 5 ÷ 30 mm.
It is quite interesting to observe the process.
Then, pellets of the tape sent to the body burning.
They are dried and calcined at 1200 ÷ 1300 ° C in special installations - roasting machines. Roasting machine (usually a conveyor type) represent the conveyor of the kiln trucks (pallet) that move on rails. But the picture - concentrate, which will soon hit the drums.
In the upper part of the burning car on a trolley kilns heating furnace, in which the combustion of gaseous, solid or liquid fuel and coolant for the formation of drying, heating and firing pellets. There are roasting machine cooled pellets directly on the machine and with external cooling. This process, unfortunately, we have not seen.
Burnt pellets acquire a high mechanical strength. When roasting removes a significant portion of the sulfur impurities. It looks like a ready-to-eat product).
Despite the fact that the equipment is used in Soviet times, the process is automated, and to monitor them do not need a large number of staff.
Source: kak-eto-sdelano.livejournal.com

First talk about the pit itself. Lebedinsky GOK - is Russia's largest mining and enrichment of iron ore and has the world's largest open pit iron ore. The plant and quarry located in the Belgorod region, between the towns of Stary Oskol and Gubkin. View of the top careers. It really is huge and growing every day. The depth of the pit of Lebedinsky GOK - 250 m above sea level or 450 m - from the surface of the earth (and the diameter - 4 to 5 kilometers), it is constantly seeping groundwater, and if not for the pumps, it is filled to the top for the month. He twice recorded in the Guinness Book of Records as the largest quarry of non-combustible mineral resources.
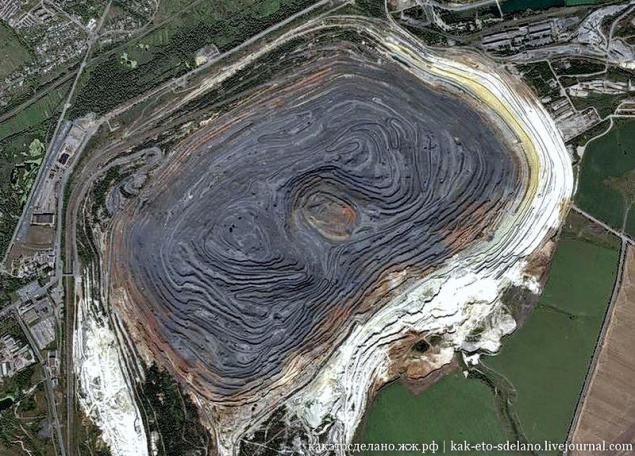
Little official information: Lebedinsky GOK is a concern, "Metalloinvest" and is a leading producer of iron ore products in Russia. In 2011, the share of concentrate combine to total annual production of iron ore concentrate and sinter ore in Russia was 21%. In a career running a lot of all kinds of techniques, but the most noticeable of course multi-ton dump trucks "BelAZ" and «Caterpillar».
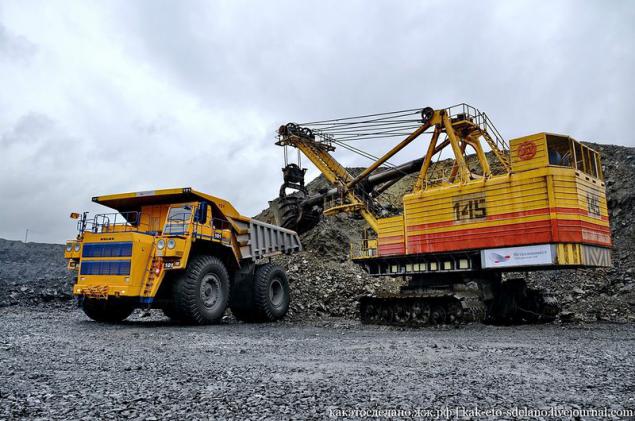
In the year, both the plant belonging to the company (Lebedinsky GOK and Mikhailovsky) produce about 40 million. Tons of iron ore in the form of concentrate and sinter ore (it's not the volume of production, and have enriched ore, that is separated from the waste rock). Thus it appears that in two GOKah day produced an average of about 110 thousand tons of iron ore concentrate. This kid at a time carries up to 220 tons (!) Of iron ore.
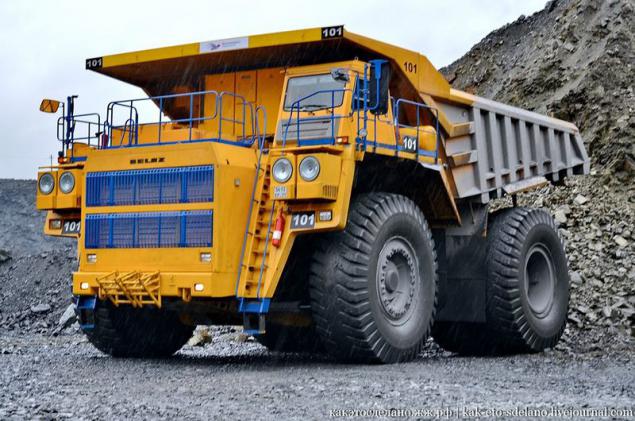
Excavator gives a signal and gives it gently back up. Just a few buckets and filled with giant body. Excavator again gives a signal and the truck pulls.
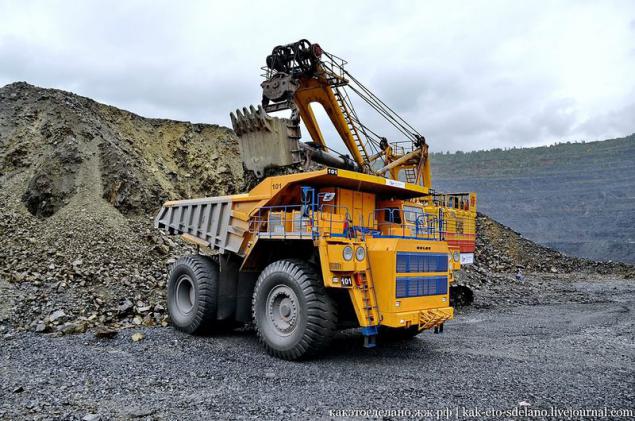
Recently bought "BelAZ" capacity of 160 and 220 tons (still load trucks in quarries was no more than 136 tonnes), and expected to reach excavators "Hitachi" with a bucket capacity of 23 cubic meters (currently the maximum capacity of mining excavators bucket of 12 cubic meters).
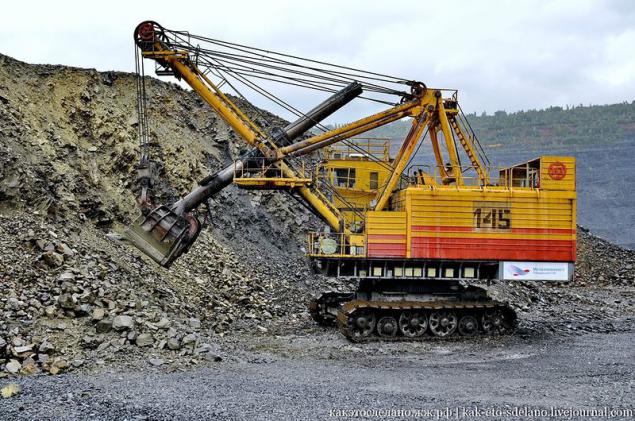
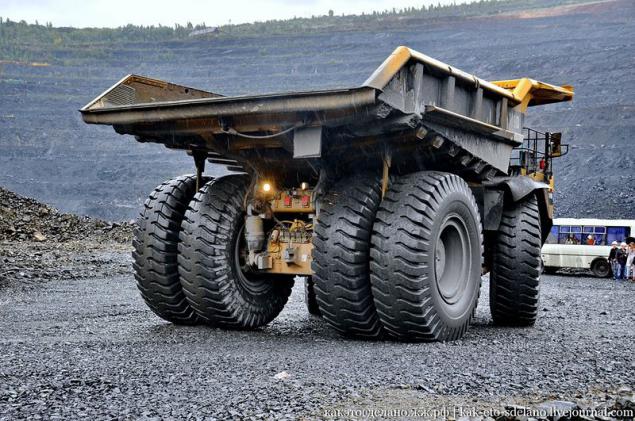
"BelAZ" and «Caterpillar» alternate. Import truck carries all the way to 180 tons. A heavy-duty dump trucks - it is a new technology, now coming to the mining companies in the framework of the investment program of "Metalloinvest" to improve the efficiency of mining and transport complex.
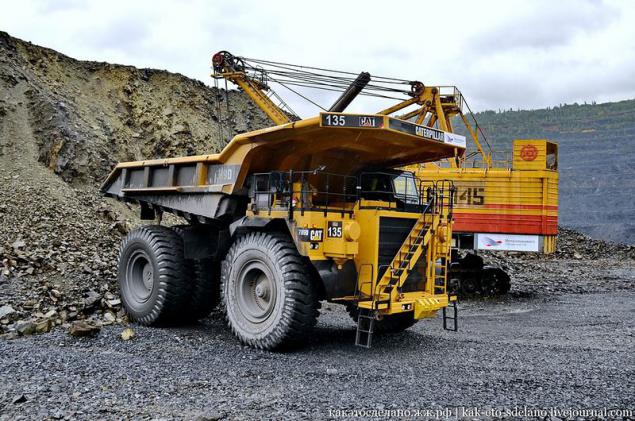
Interesting texture of the stone, pay attention. If I am not mistaken from left quartzite from such ore mined iron. The quarry is full of not only iron ore, but also a variety of minerals. They generally are not of interest for further processing in an industrial scale. Today, of the gangue get chalk and make rubble for construction purposes.
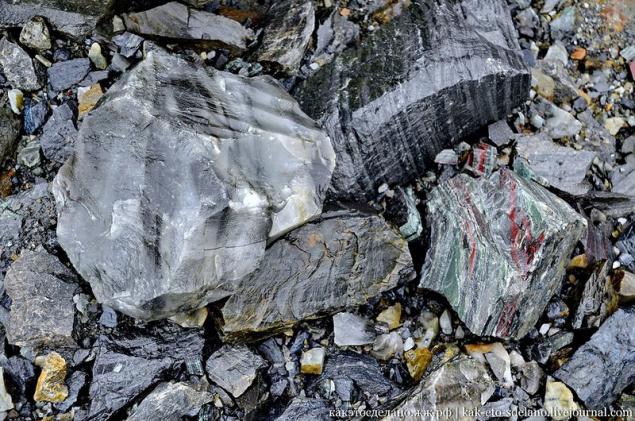
Every day in the career of Lebedinsky GOK operates 133 units of the main mining equipment (30 large trucks, 38 shovels, 20 burstankov 45 traction units).
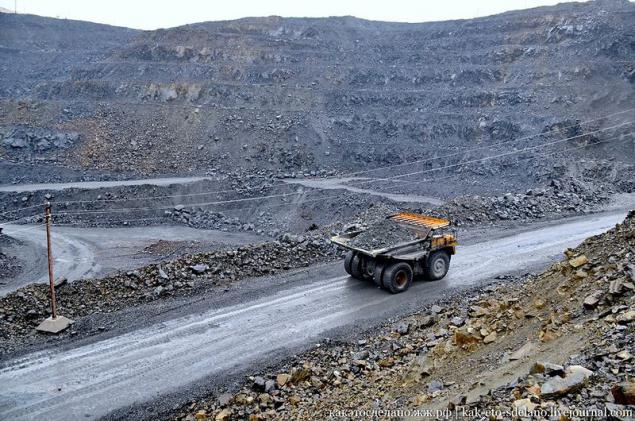
Of course, I was hoping to see spectacular explosions, but even if they were held on this day, I still have not been able to enter the territory of a career. Such an explosion is done once in three weeks. All machinery safety standards (and a lot of it) before it is output from the quarry.
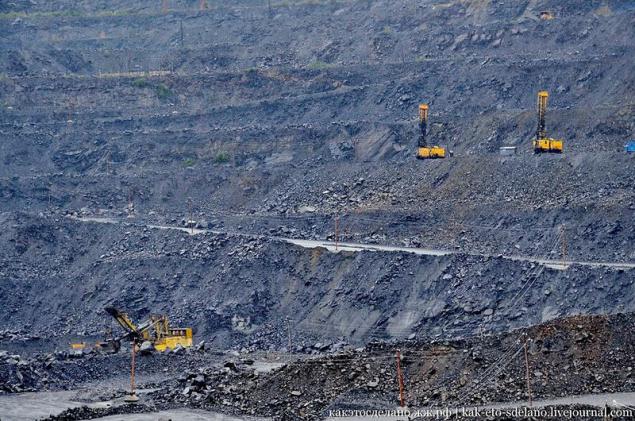
Lebedinsky GOK and Mikhailovsky GOK - the two largest plant for the extraction and processing of iron ore in Russia in terms of production. Company "Metalloinvest" has the second-largest proven reserves of iron ore - about 14, 6 billion tons in the international classification JORS that ensures nearly 150 years of operating period at the current level of production. So the residents of Stary Oskol and Gubkin will be employed for a long time.
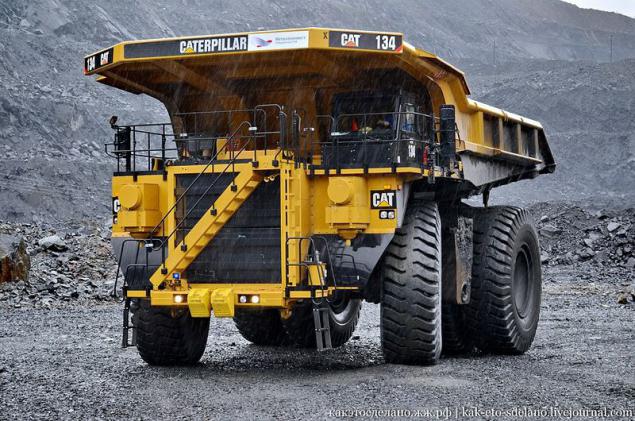
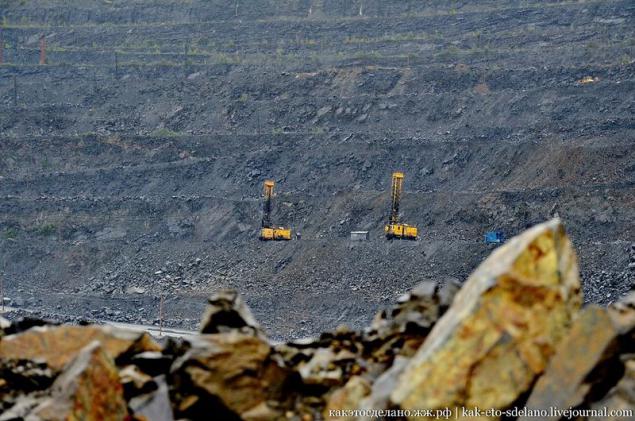
Probably noticed in previous photos, the weather was not very good, was rain and fog in the career of standing. Closer to leave it a little scattered, but still not much. I pulled a photo as possible. Dimensions career certainly impressive.
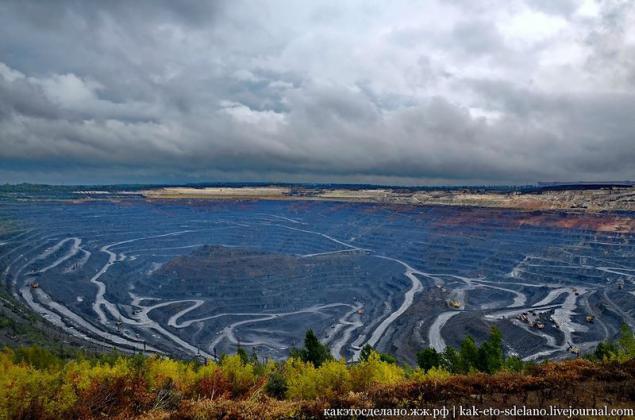
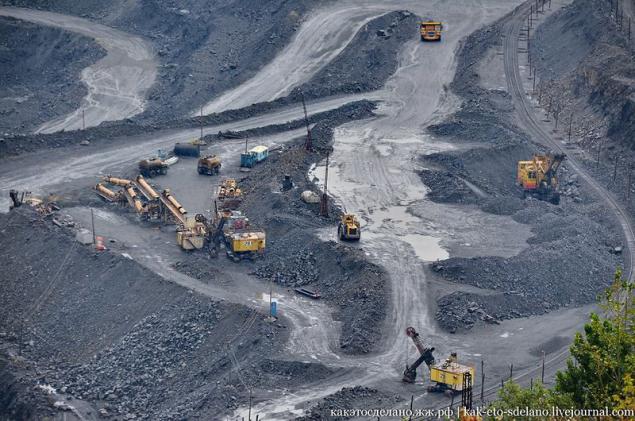
Iron ore is charged immediately to the railway compositions, in special reinforced wagons that take out the ore from the mine, they are called dump cars, their carrying capacity - 105 tons.
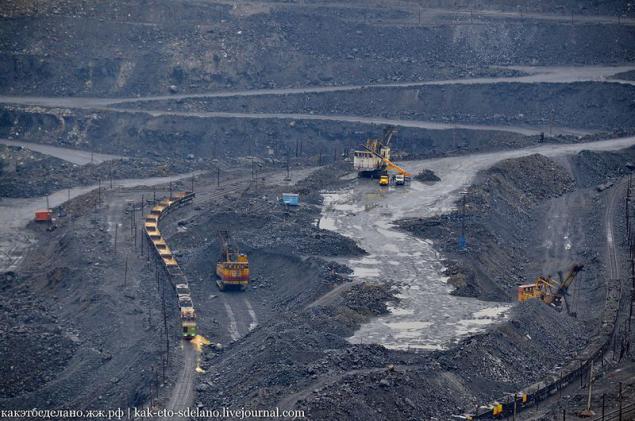
The geological formations on which you can learn the history of the Earth.
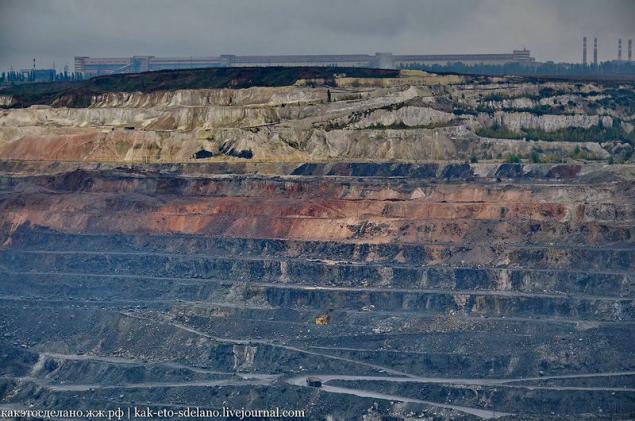
Giant machines from the height of the observation platform seem to be no more than an ant.
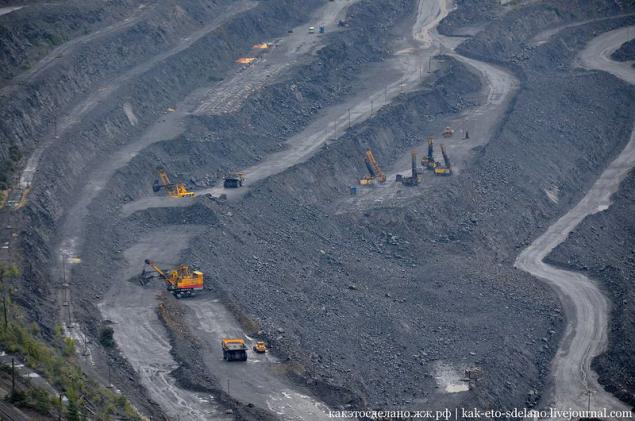
Then carry the ore to the plant, where the process of separating the gangue by magnetic separation: fine ore is crushed and then sent to a magnetic drum (separator) to which, in accordance with the laws of physics all the iron sticks, not iron - washed off with water. Then from the resulting iron ore pellets and make hot briquette iron (HBI), which is then used for steelmaking. Hot briquetted iron (HBI) - a type of DRI (DRI). Material with high (& gt; 90%) iron, obtained by the technology is different from the domain processing. It is used as a raw material for steel production. High quality (with a small amount of harmful impurities) replacement of cast iron, scrap metal. Unlike iron, HBI in production is not used coal coke. Briquetted iron production process is based on the processing of iron ore (pellets), high temperatures, mostly by natural gas.
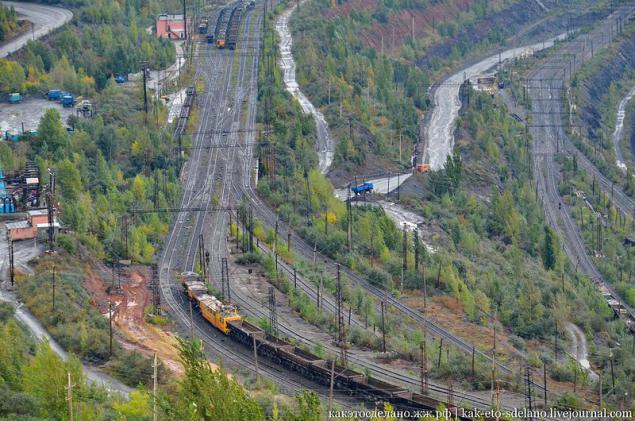
HBI within the plant simply do not you come, because the process of hot baking pies held at a temperature of about 900 degrees, and sunbathe in Stary Oskol I was not in the plans).
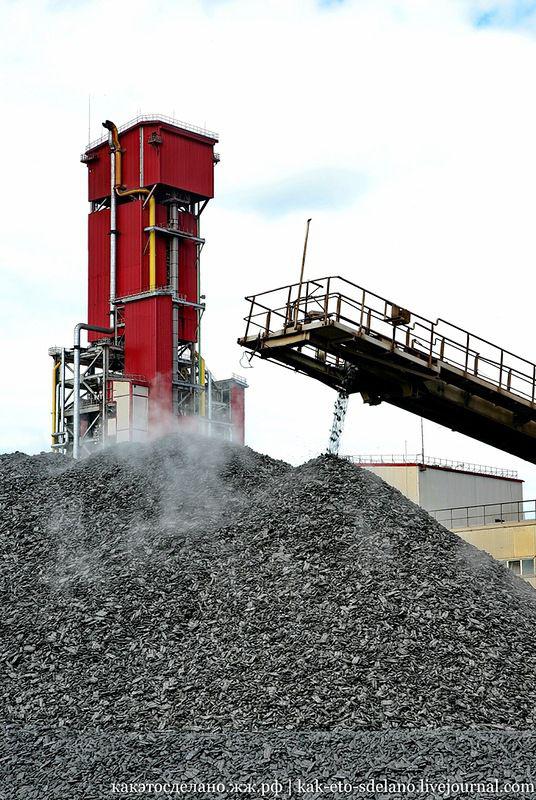
Lebedinsky GOK - the only producer of HBI in Russia and the CIS. The plant began production of this product in 2001, running the shop for production of HBI (HBI plant-1) with the use of technology HYL-III capacity of 1, 0 million tonnes per year. In 2007, the GOK has completed construction of the second plant for production of HBI (HBI plant-2) using the technology MIDREX with a production capacity of 1, 4 million tons per year. At present, the production capacity LGOK is 2, 4 million tons of HBI per year.
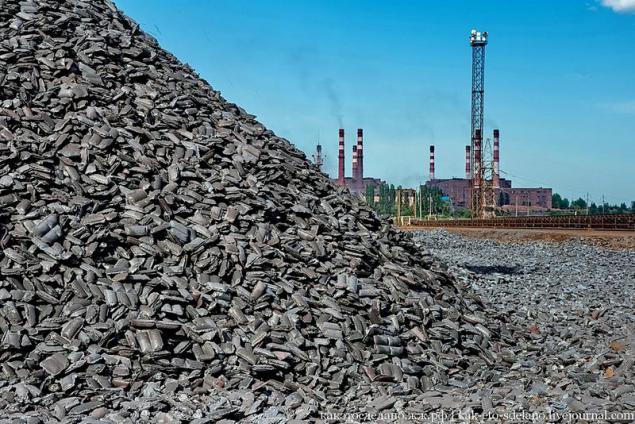
When we visited the quarry Oskol Electric Steel Works (OEMK) included in the Steel segment companies. In one of the shops of the plant produced here are steel billets. Their length can reach between 4 and 12 meters, depending on the wishes of customers.
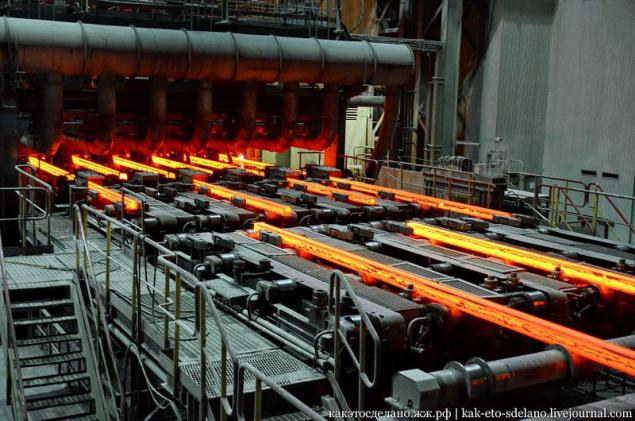
You see sparks? In place of the bar steel is cut.
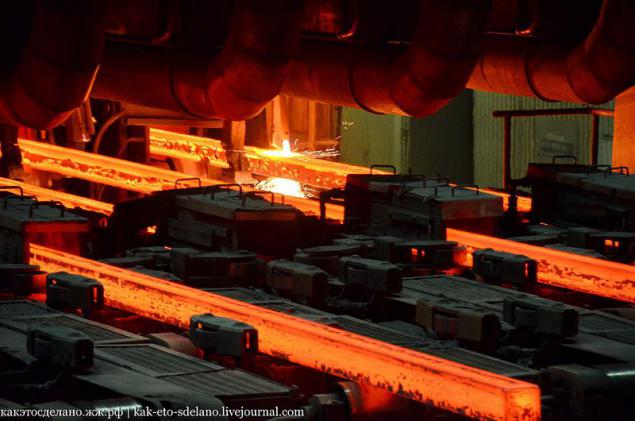
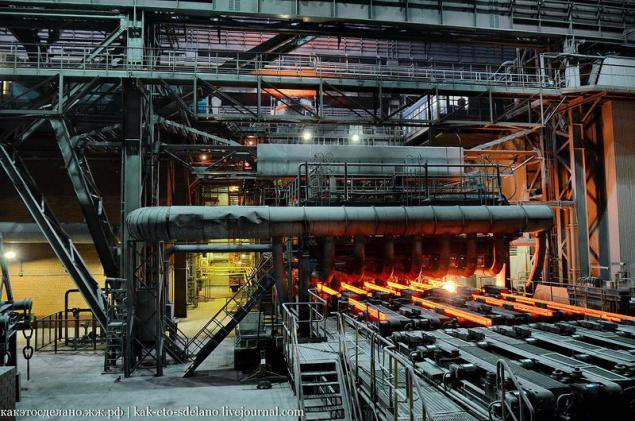
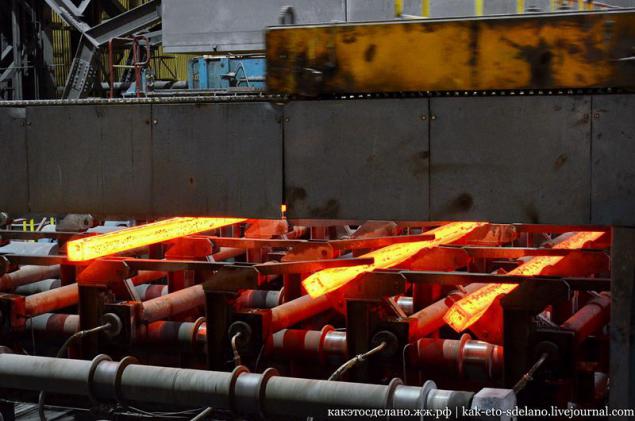
Interesting machine with a bucket called badevoz in a fused slag in the production process.
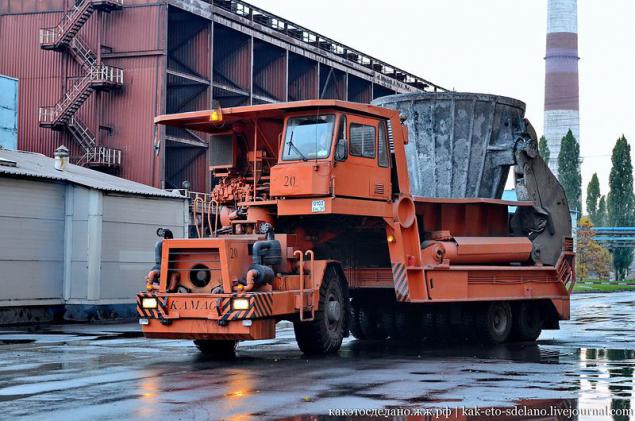
In neighboring shop OEMK grind and polished steel rods of different diameters, rolled past in another shop. By the way, this plant - the seventh largest company in Russia for the production of steel and steel produktsii.V 2011, the share of steel production in the OEMK amounted to 5% of the total steel produced in Rocsii share of rolled products was also 5%.
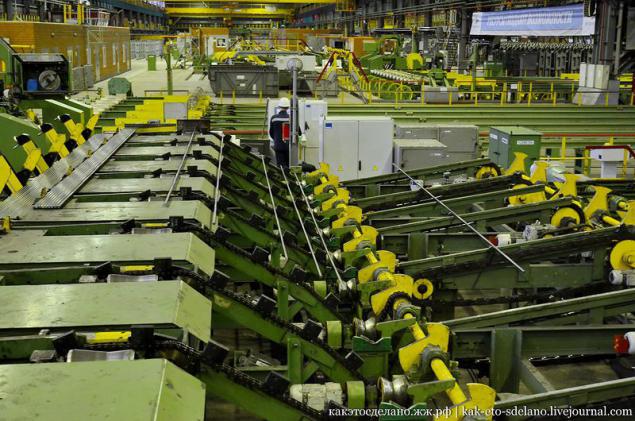
OEMK applies advanced technologies, including direct iron reduction and electric arc, which ensures production of high quality metal, with a reduced content of impurities.
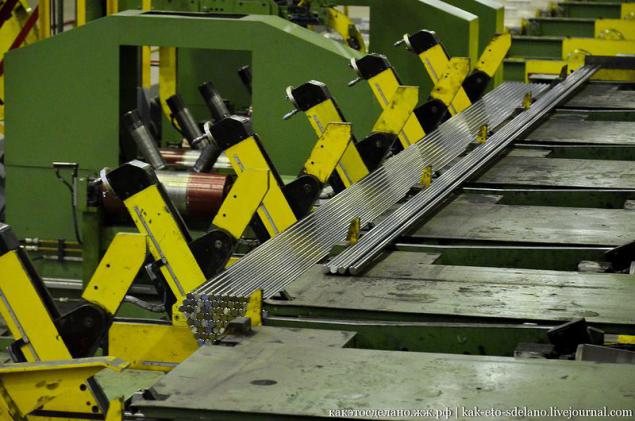
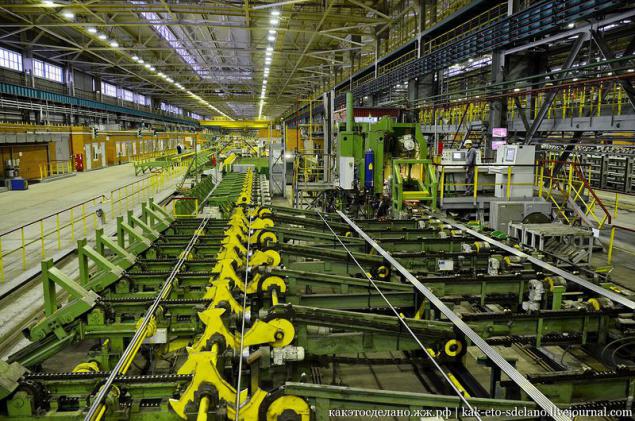
The main consumers of steel OEMK on the Russian market are the automotive, engineering, pipe, hardware and bearing industries.
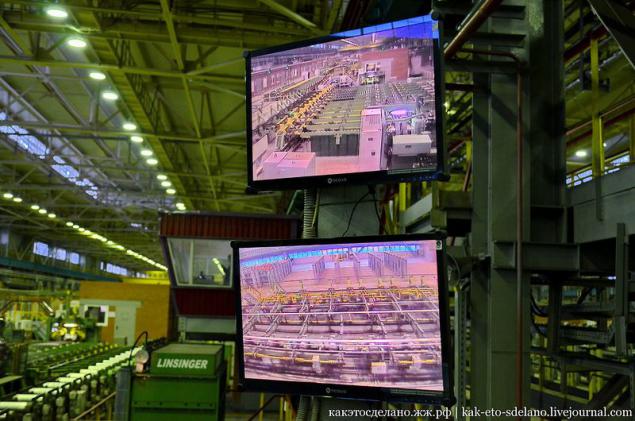
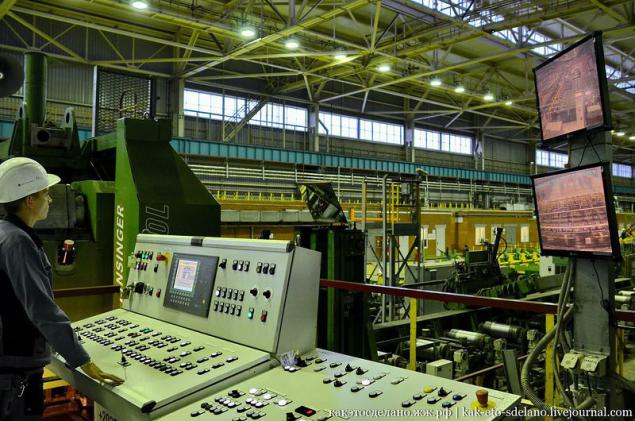
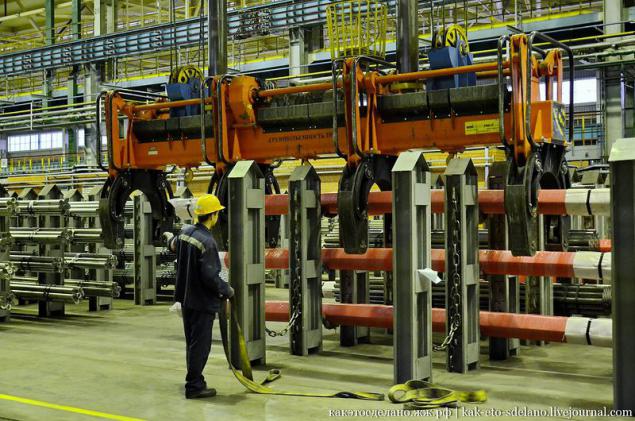
Metal OEMK exported to Germany, France, USA, Italy, Norway, Turkey, Egypt and many other countries.
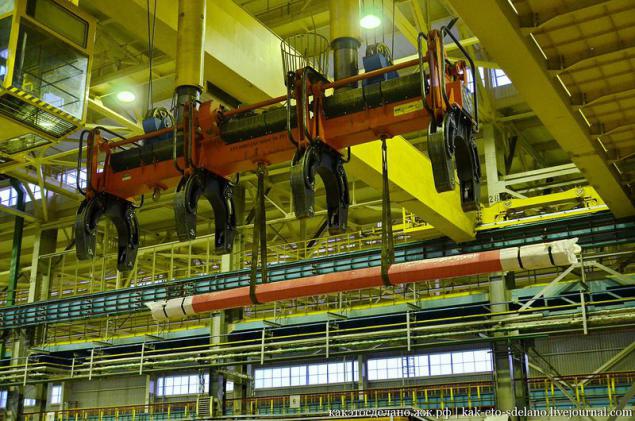
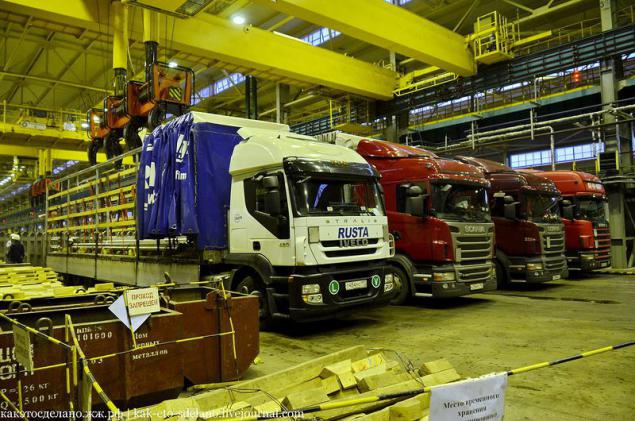
The company has mastered the production of long products for the manufacture of products used by the world's leading automakers.

By the way, I am not the first time I've noticed on such industries women - crane operator.
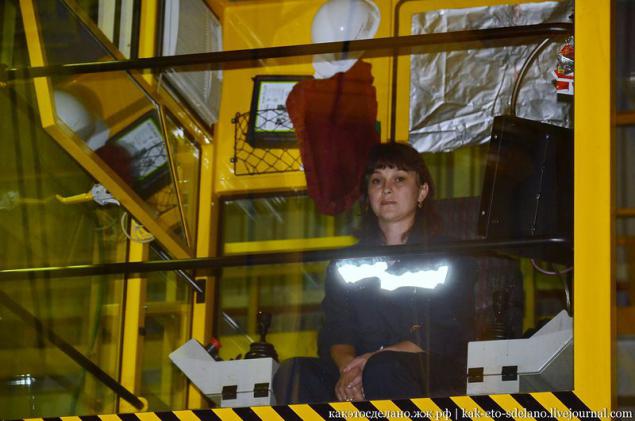
This plant almost sterile cleanliness, not typical for such productions.
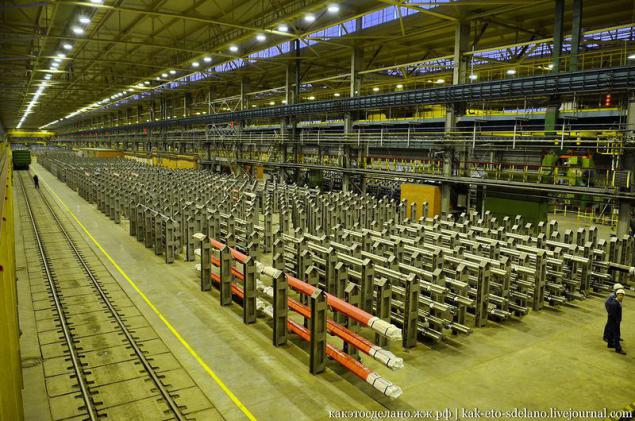
I like neatly stacked steel rods.
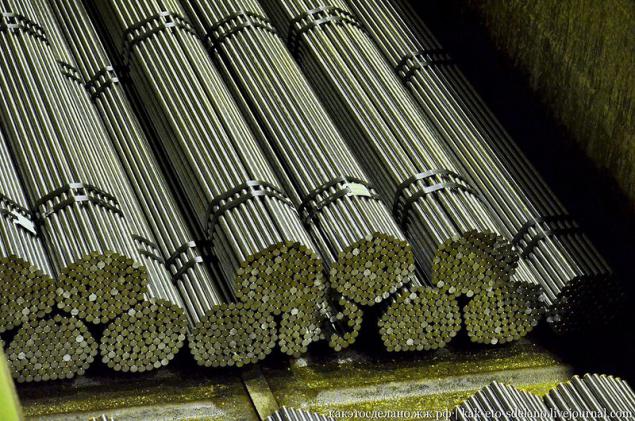
At the request of the customer for each product is glued sticker.
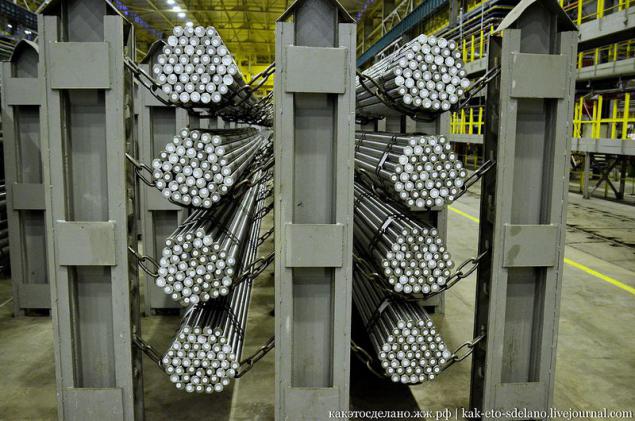
On the sticker stamped heat number and steel grade code.
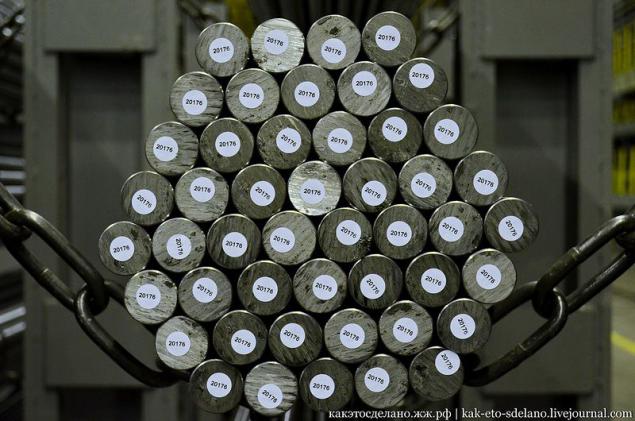
The opposite end can be marked with paint, but to each packet to the manufactures tag attached to the contract number, country of destination, steel grade, heat number, size in mm, supplier name and package weight.
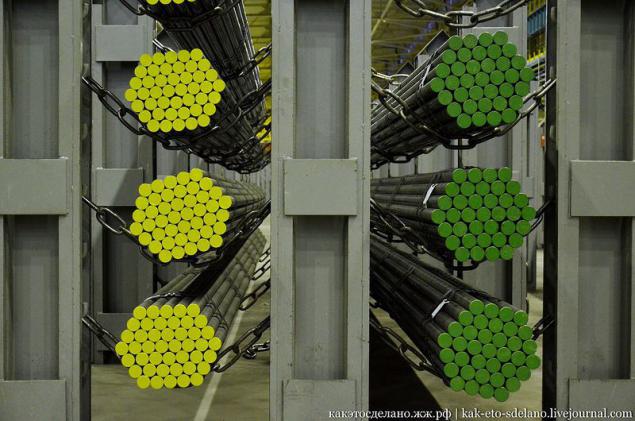
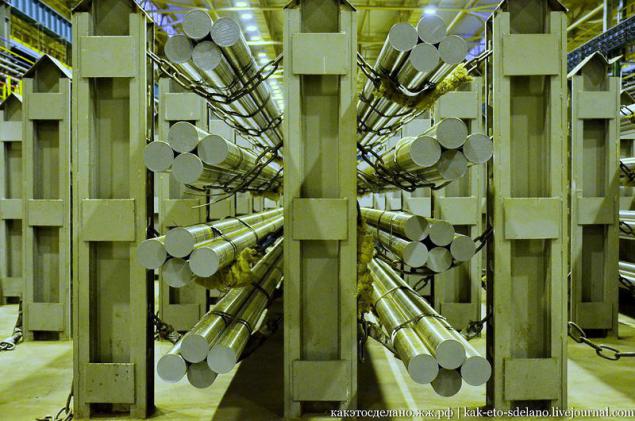
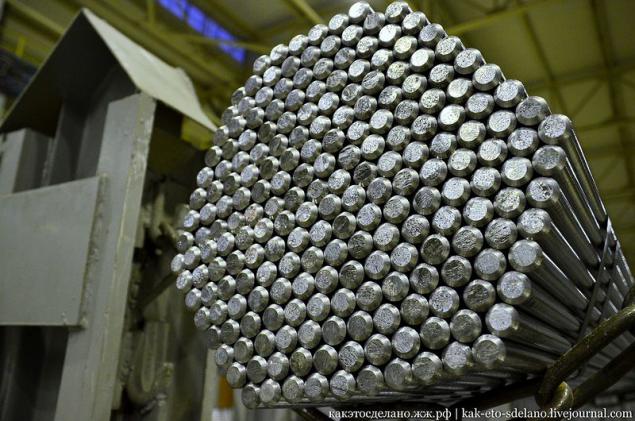
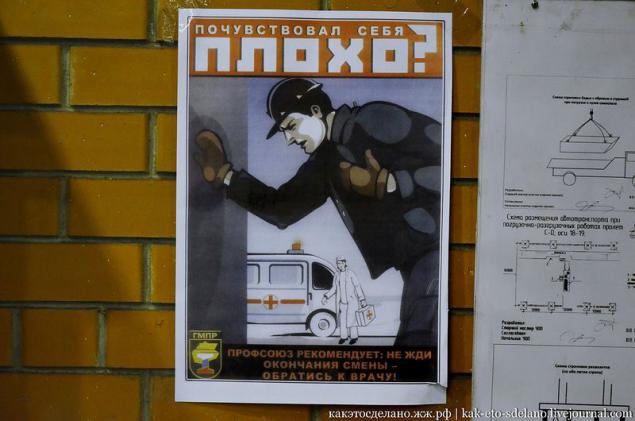
These products - the standard by which the equipment is configured for precise rolling.
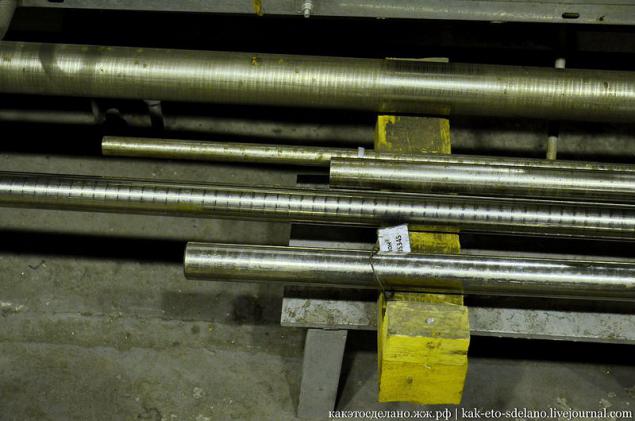
And this machine can scan a product and detect microcracks and defects before the metal falls to the customer.
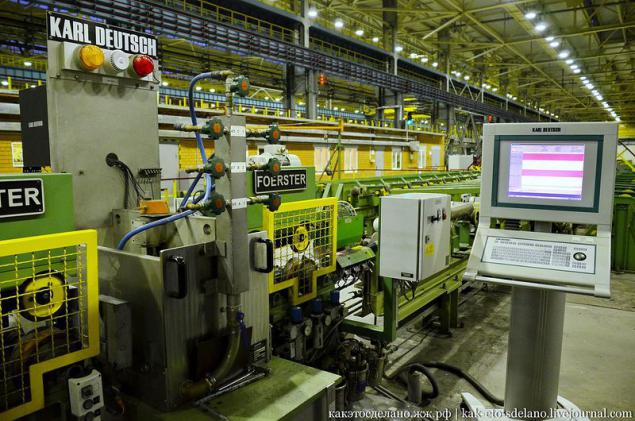
The company serious about safety.
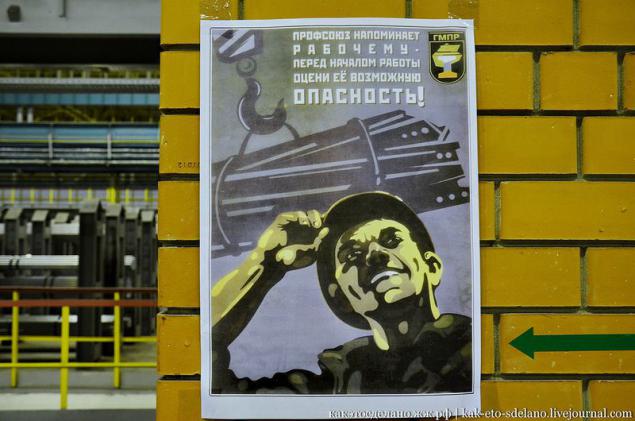
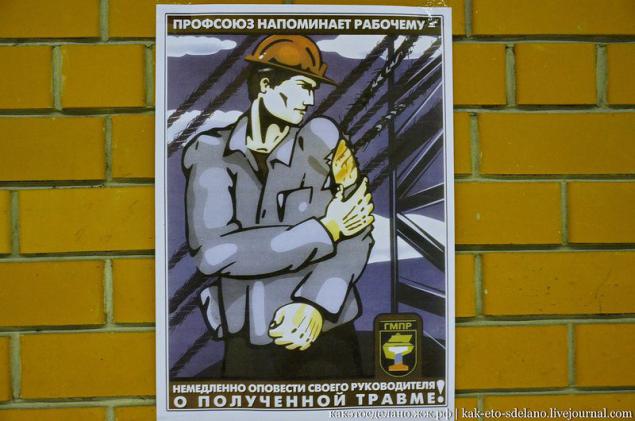
All water used in the production of purified recently established super-modern equipment.
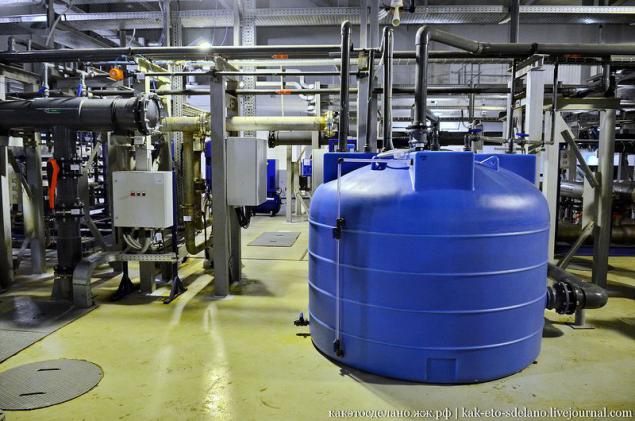
This installation of sewage treatment plant. After treatment, it is cleaner than the river, where it was released.
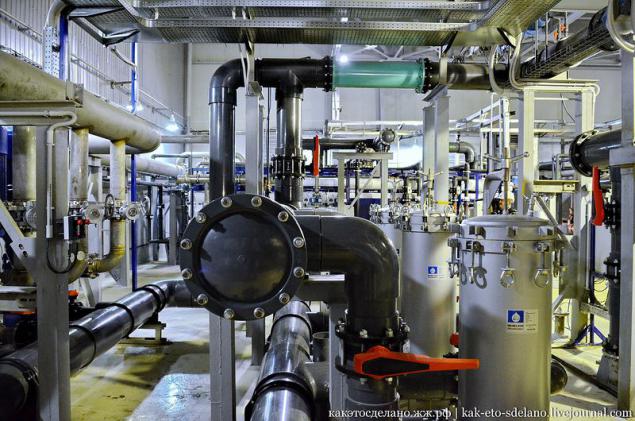
Engineering water almost distilled. As with any process water can not drink it, but once you can try, it is not dangerous to health.
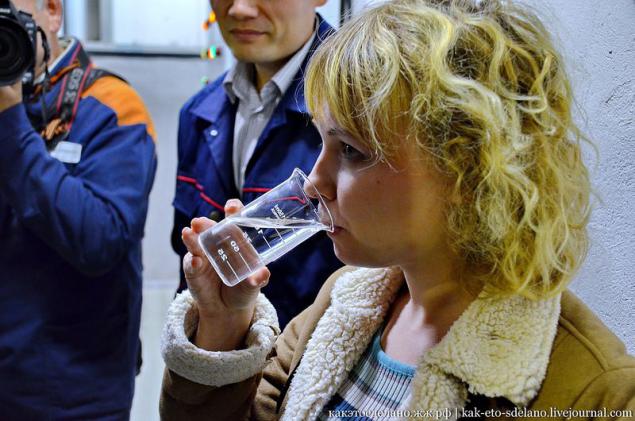
The next day we went to Zheleznogorsk, located in the Kursk region. That there is Mikhailovsky GOK. In the picture - under construction complex roasting machine №3. It will produce pellets.
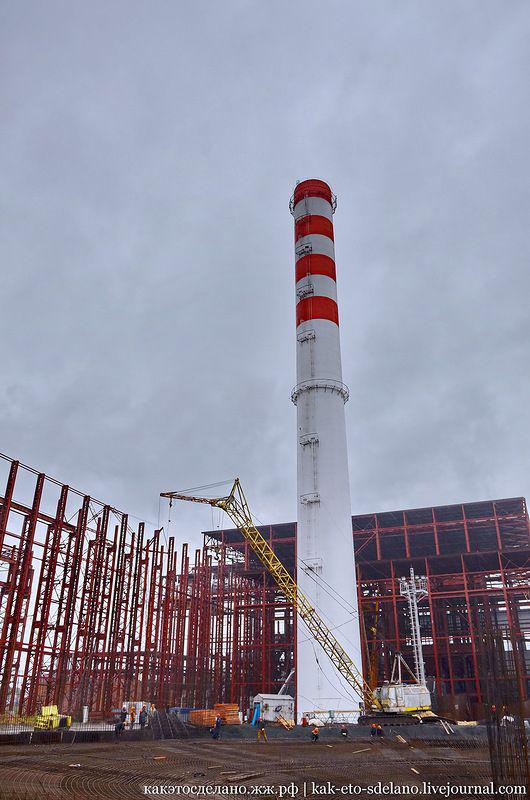
Its construction will be invested 450 million. Dollars. The company will be built and put into operation in 2014
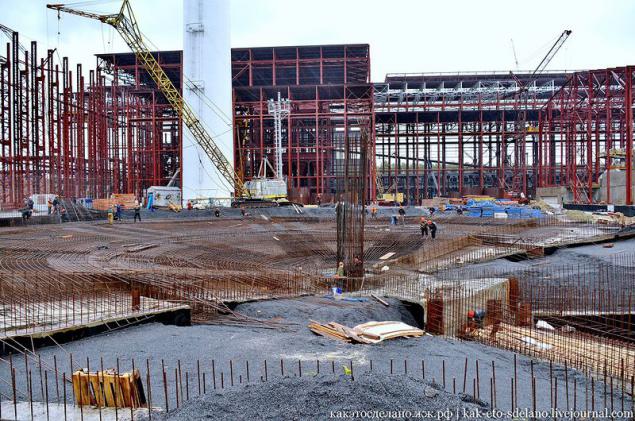
This layout of the plant.
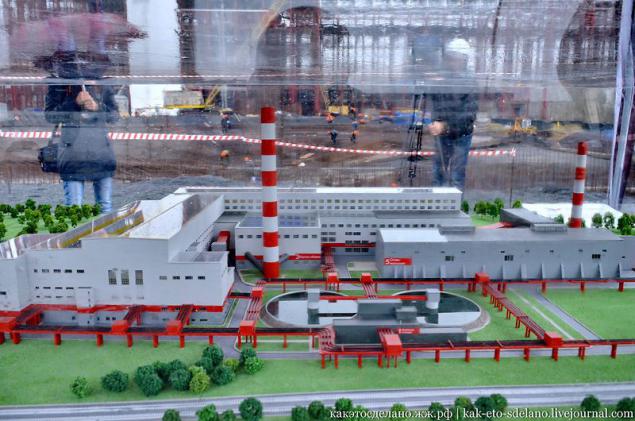
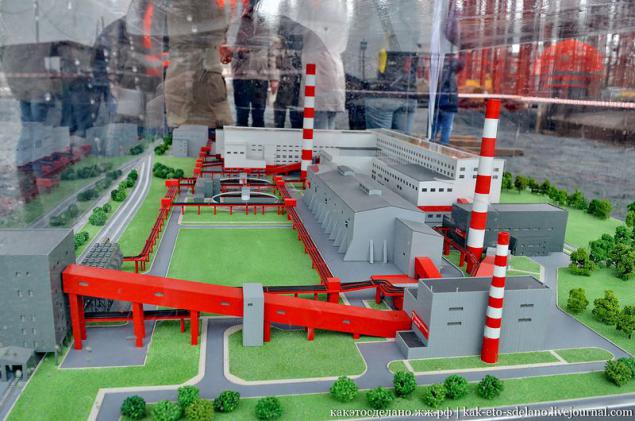
Then we went to the careers of Mikhailovsky GOK. Depth MGOKa career - more than 350 meters above ground, and its size - 3 to 7 kilometers. Its territory is actually three career can be seen in the picture from a satellite. One large and two smaller ones. After about 3-5 years the quarry will grow so much that would be a great one, and maybe catch up in size Lebedinsky pit.
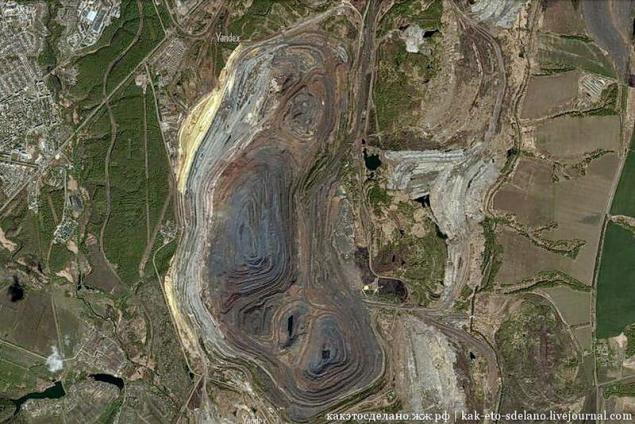
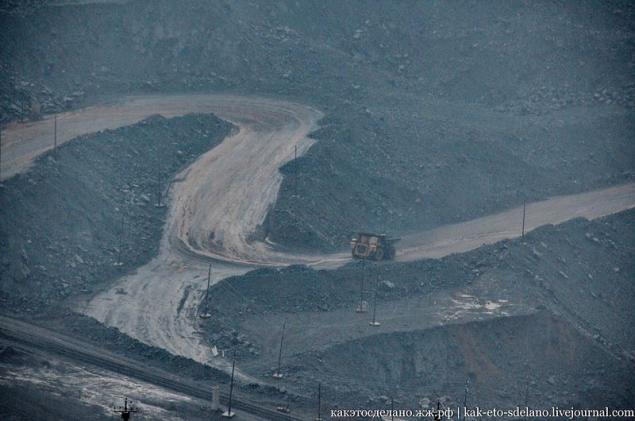
In a career involved 49 trucks, 54 of traction unit 21 diesel locomotive, 72 excavators, 17 drilling rigs, 28 bulldozers and graders 7. The rest of the extraction of ore in the GOK is not different from LGOK.
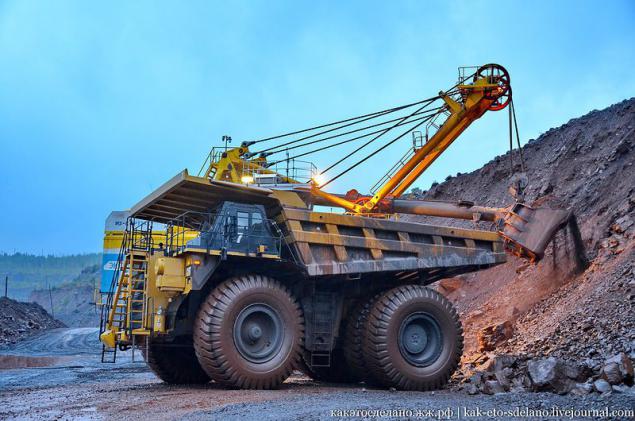
At this time, we still managed to get to the plant, where iron ore concentrate is converted to the final product - Pellets ... Pellets - lumps of crushed ore concentrate. Semi-finished steel production of iron. It is a product of the enrichment of iron ore concentrating special ways. It is used in blast furnaces to produce pig iron.
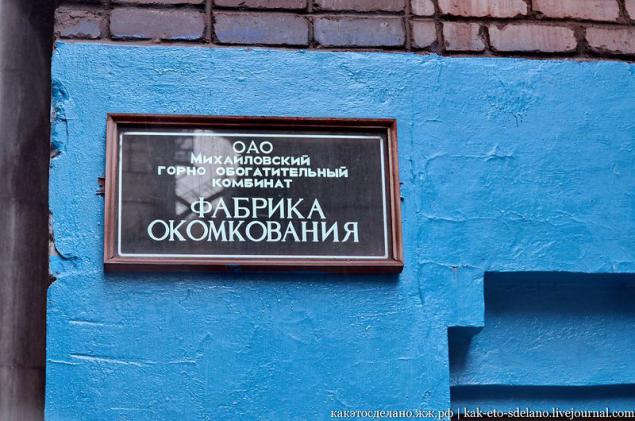
For the production of iron ore pellets used. For initial removal of mineral impurities (crude) and finely ground ore is enriched by various methods. The process of manufacturing pellets is often called "balling". The charge that is a mixture of finely chopped concentrates of iron mineral flux (additives regulating the composition of the product), and reinforcing additives (usually bentonite), moistened and subjected to pelletizing in rotating bowls (pellet) or drums-pelletizers. They are the most in the picture.
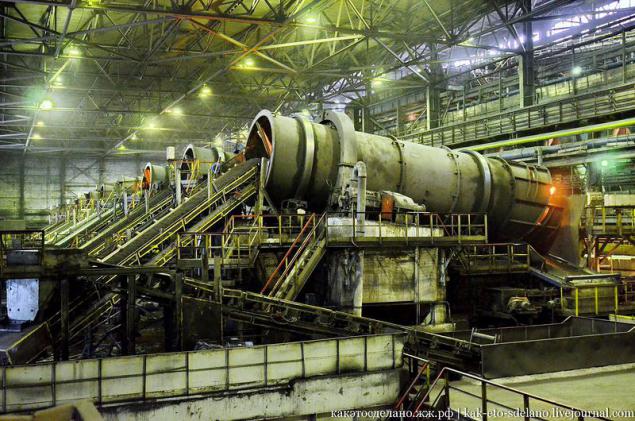
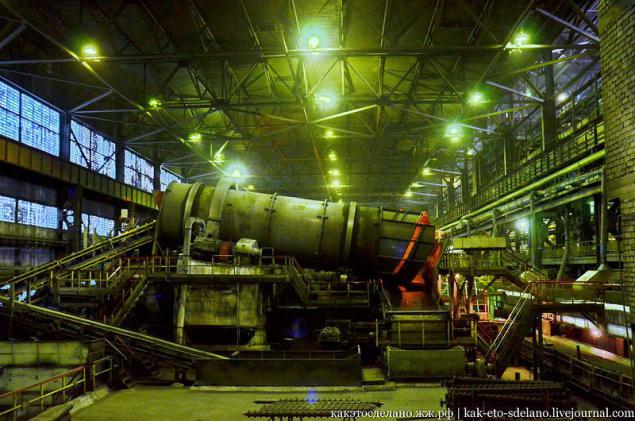
Come closer.
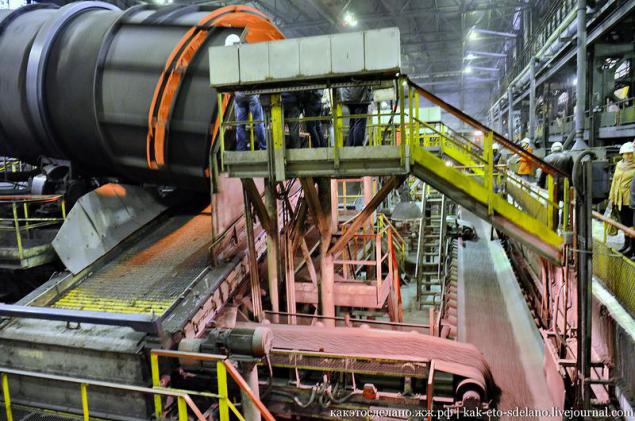
As a result, pelletizing get close to spherical particles with a diameter of 5 ÷ 30 mm.
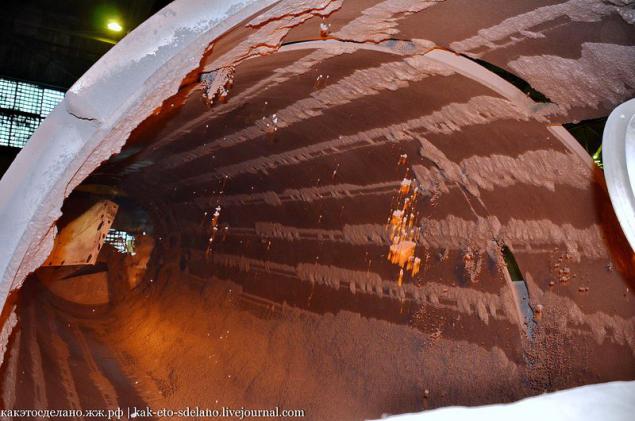
It is quite interesting to observe the process.
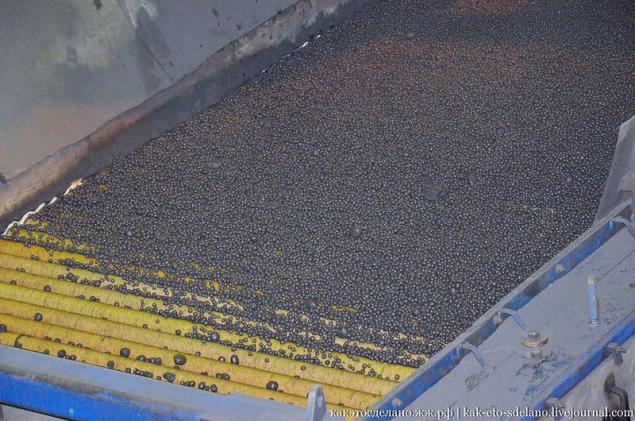
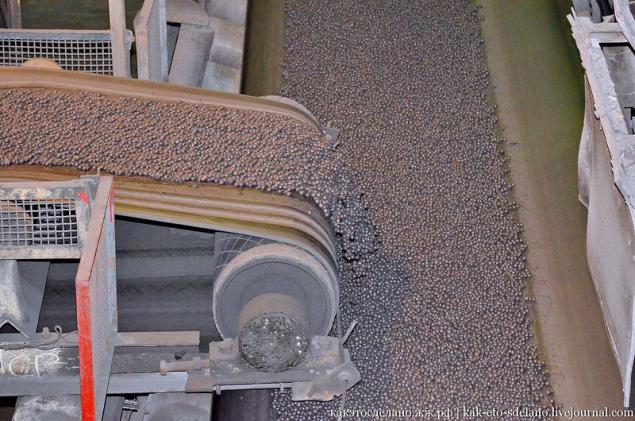
Then, pellets of the tape sent to the body burning.
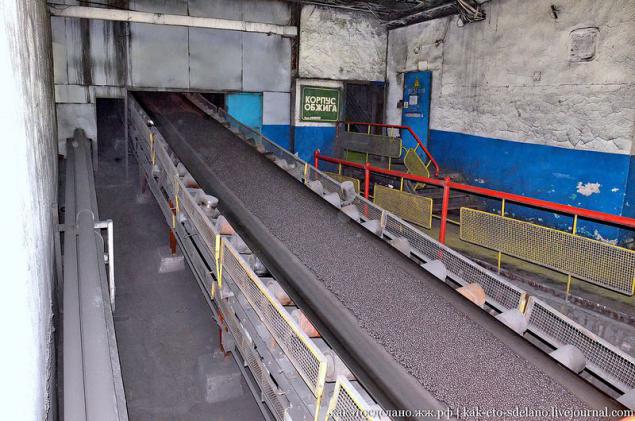
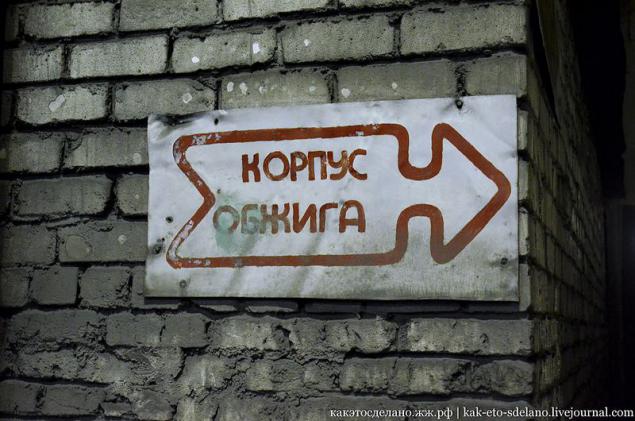
They are dried and calcined at 1200 ÷ 1300 ° C in special installations - roasting machines. Roasting machine (usually a conveyor type) represent the conveyor of the kiln trucks (pallet) that move on rails. But the picture - concentrate, which will soon hit the drums.
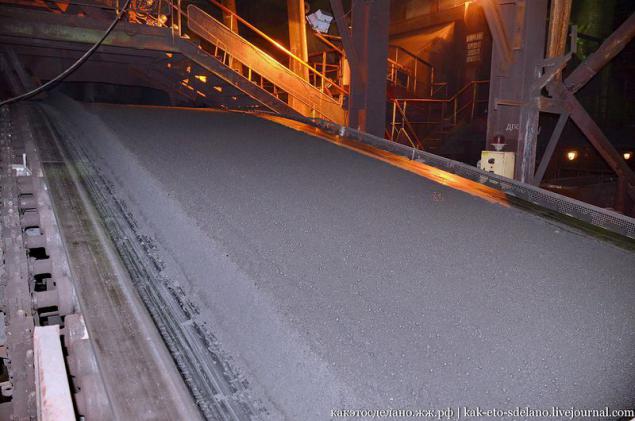
In the upper part of the burning car on a trolley kilns heating furnace, in which the combustion of gaseous, solid or liquid fuel and coolant for the formation of drying, heating and firing pellets. There are roasting machine cooled pellets directly on the machine and with external cooling. This process, unfortunately, we have not seen.
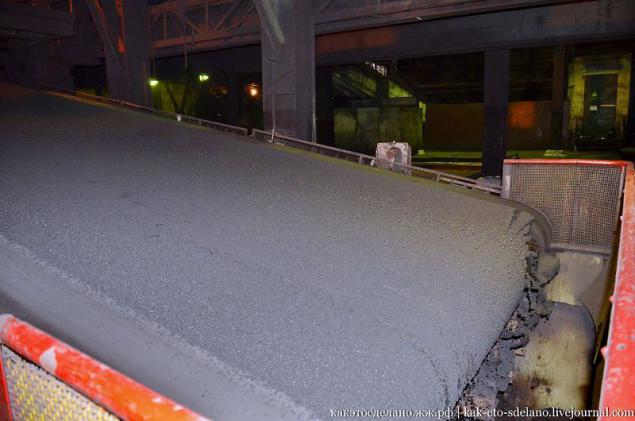
Burnt pellets acquire a high mechanical strength. When roasting removes a significant portion of the sulfur impurities. It looks like a ready-to-eat product).
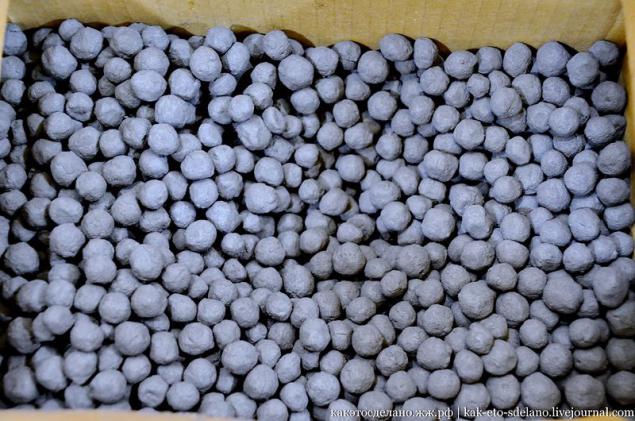
Despite the fact that the equipment is used in Soviet times, the process is automated, and to monitor them do not need a large number of staff.
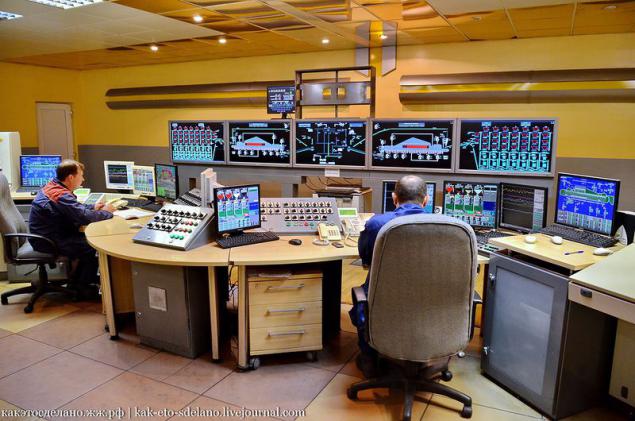
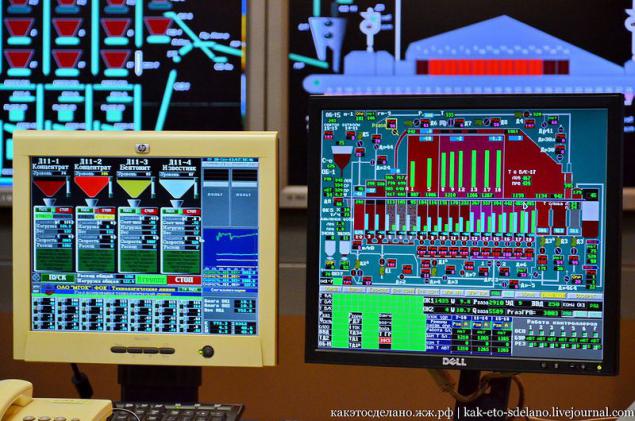
Source: kak-eto-sdelano.livejournal.com