985
Manufacturing carboxylic parts
And you know how to produce a carbon parts? The author of the post before this had never encountered such a production, but when it was offered by the company such visit, he gladly undertook this task.
Frankly, I have never before seen how these things are made, and did not even imagine all the technology.
But it turned out that getting to the plant not so simple. Two vendors under various pretexts refused to meet in the production and persistently called to his office. The third office and production were in the same building, and without thinking twice, I went to see him.
The plant looks pretty well, I carried out in the negotiation-showroom.
From the diversity of samples scatter eyes: carbon bicycle parts for cars and mototyuninga, all sorts of gizmos unknown purpose.
One piece hood for the BMW
Sometimes carboxylic fabric weave colored threads: red or blue, looks very unusual.
Details, painted completely, immediately and unlike conventional. Usually athletes are doing: they need low weight, and not show-off
Helmet.
But the main purpose of my visit was this:
Case for the iPad. I was interested in not the case, of course, but like his pieces: parts for the body of the phone, laptops, tablets. It is important to understand the technology proizodstva, to understand how they design it to be the most cheap and technologically. Therefore, after much negotiation and persuasion, I finally asked for a tour of the shop.
Carboxylic fabric coated with an adhesive layer comes in rolls. They come in different thicknesses, with a different weave pattern. Stored in special freezers.
The fabric is cut into pieces of the pattern, and are glued in several layers on the matrix. The matrices are easy, from something such as plastic and with an increased resource of aluminum.
Matrix, reaching the work laid out on the floor, each in its own sector.
The process of carbon sticker was located behind the glass doors, but I flatly refused to show it, they say, a terrible trade secret. But I do not think that there is something secret, simply cut with scissors and placed in the form of scraps.
After that, each part is packed in vacuum bags.
Air is pumped out of the packages and loaded into one of the two furnaces, more or less.
Finished parts are removed from the matrix. If the item is a complex form, and the matrix for it is a composite of several parts.
Quality control before delivery to the warehouse.
As you might imagine, this is not the whole process. Now, the details need to trim the edges and paint them with varnish. But this is a different site from the subcontractor. They offered to go and see, but I refused - that there is certainly nothing new.
Source: zorins.livejournal.com
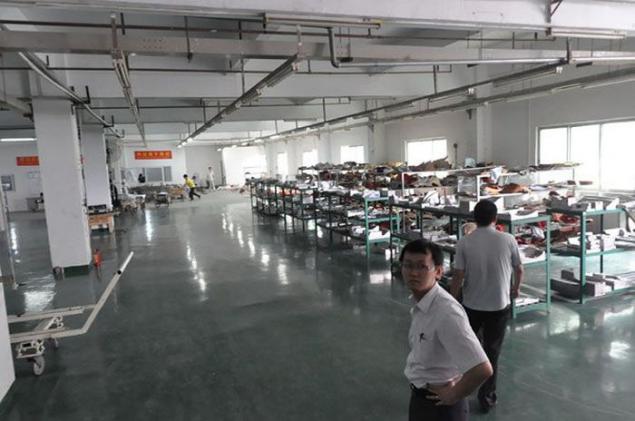
Frankly, I have never before seen how these things are made, and did not even imagine all the technology.
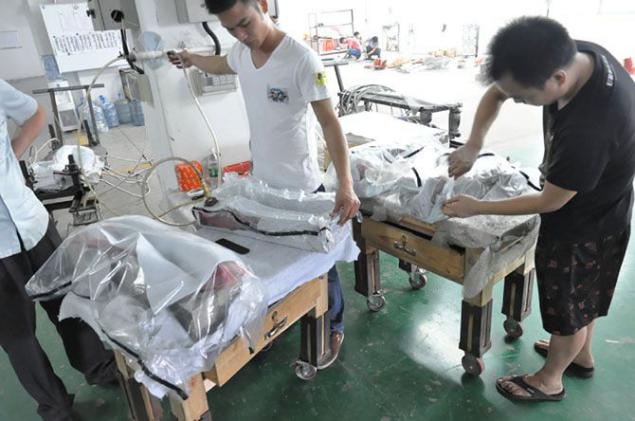
But it turned out that getting to the plant not so simple. Two vendors under various pretexts refused to meet in the production and persistently called to his office. The third office and production were in the same building, and without thinking twice, I went to see him.
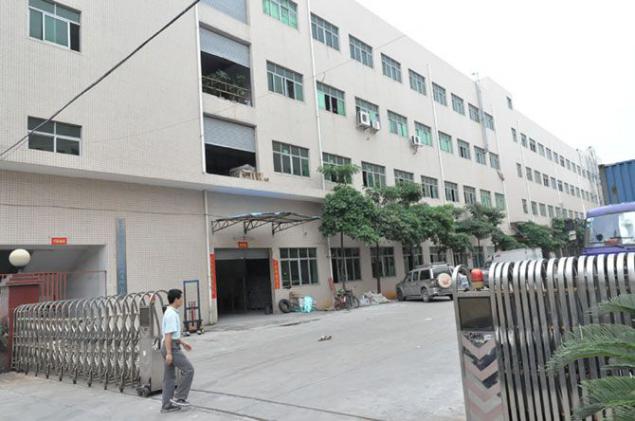
The plant looks pretty well, I carried out in the negotiation-showroom.
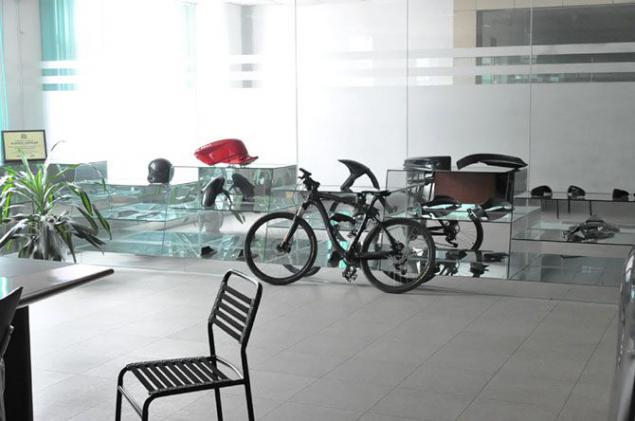
From the diversity of samples scatter eyes: carbon bicycle parts for cars and mototyuninga, all sorts of gizmos unknown purpose.
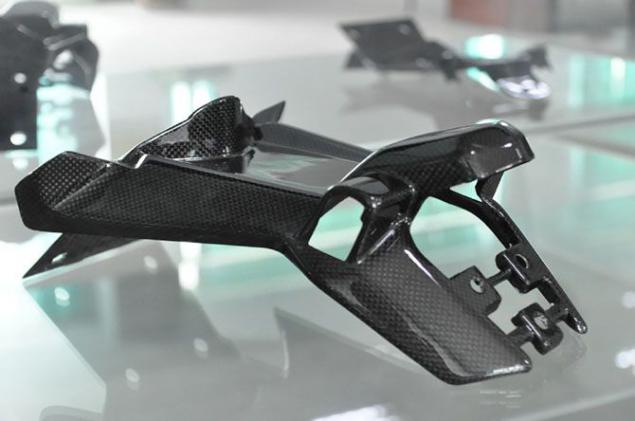
One piece hood for the BMW
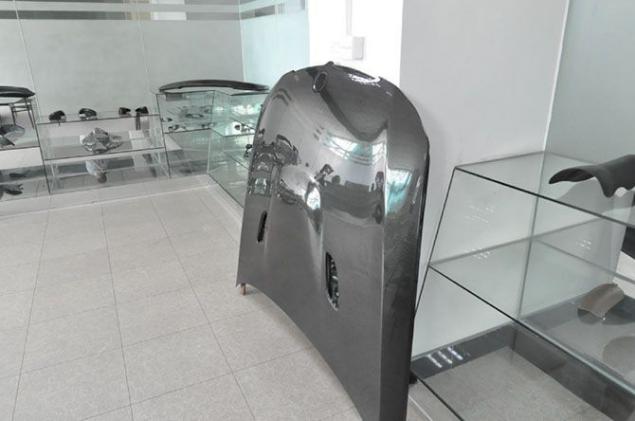
Sometimes carboxylic fabric weave colored threads: red or blue, looks very unusual.
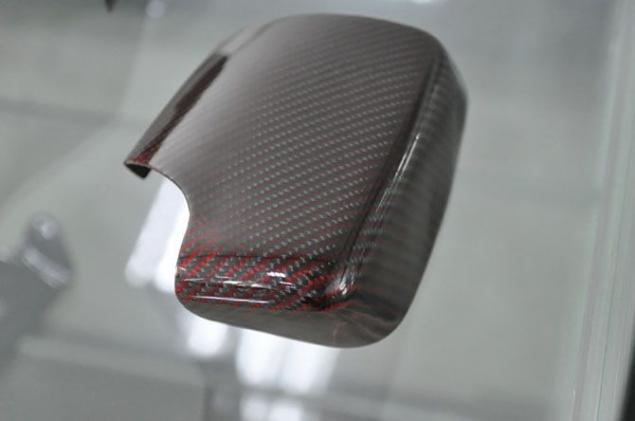
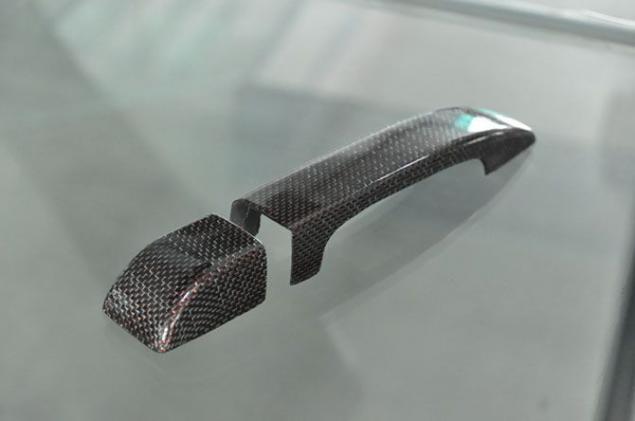
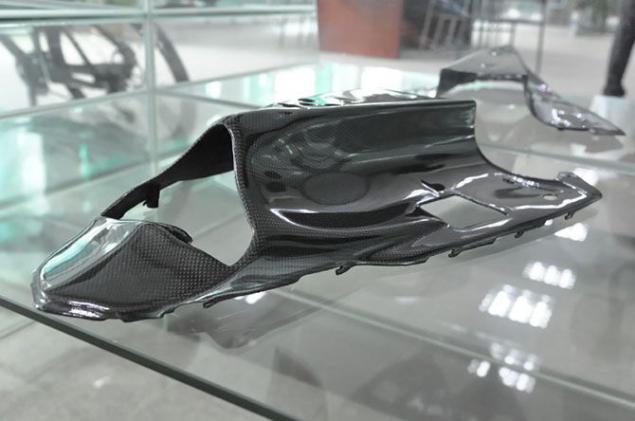
Details, painted completely, immediately and unlike conventional. Usually athletes are doing: they need low weight, and not show-off
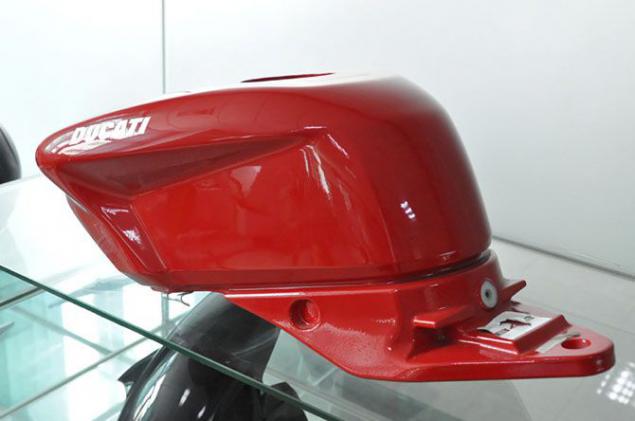
Helmet.
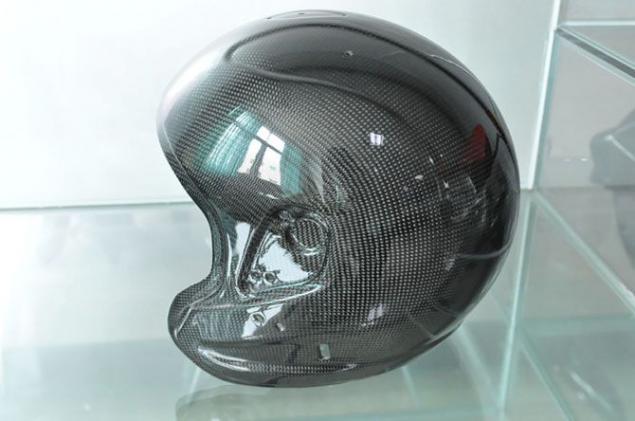
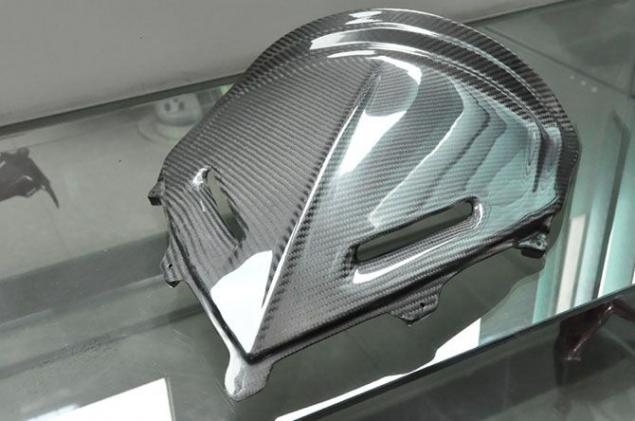
But the main purpose of my visit was this:
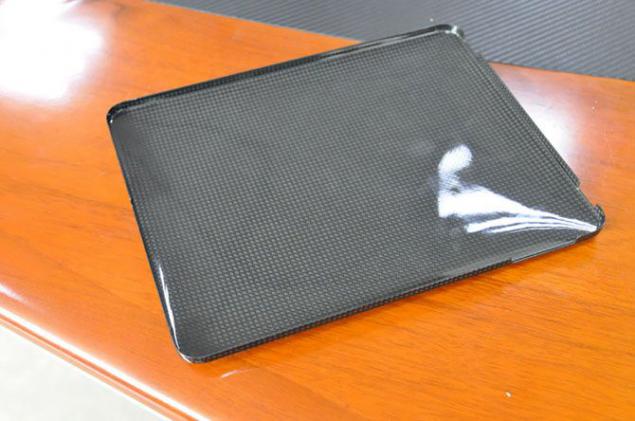
Case for the iPad. I was interested in not the case, of course, but like his pieces: parts for the body of the phone, laptops, tablets. It is important to understand the technology proizodstva, to understand how they design it to be the most cheap and technologically. Therefore, after much negotiation and persuasion, I finally asked for a tour of the shop.
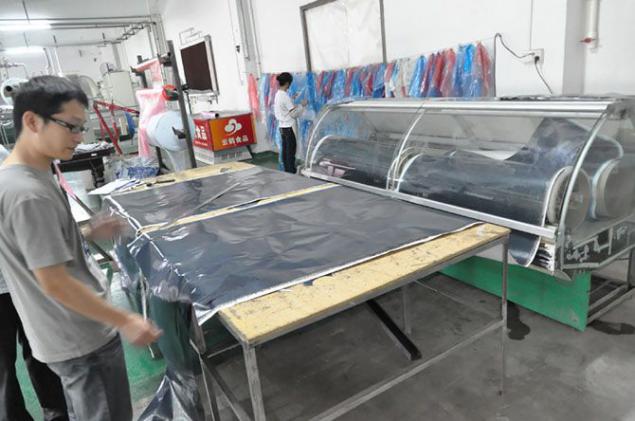
Carboxylic fabric coated with an adhesive layer comes in rolls. They come in different thicknesses, with a different weave pattern. Stored in special freezers.
The fabric is cut into pieces of the pattern, and are glued in several layers on the matrix. The matrices are easy, from something such as plastic and with an increased resource of aluminum.
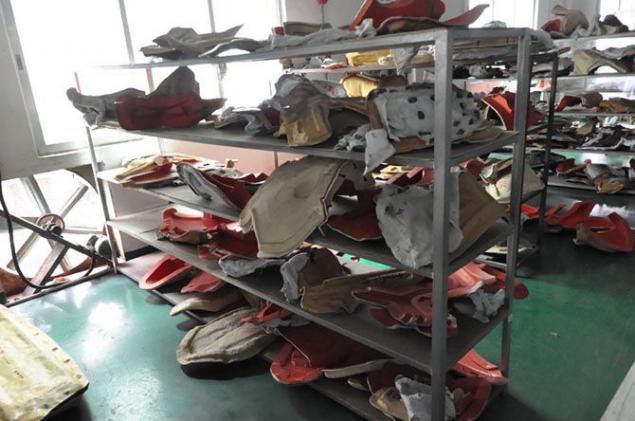
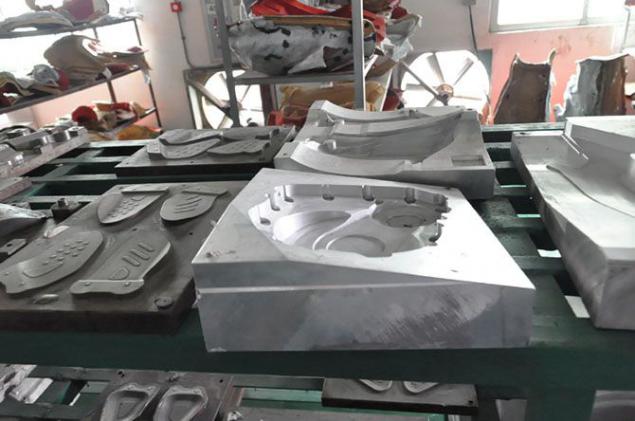
Matrix, reaching the work laid out on the floor, each in its own sector.
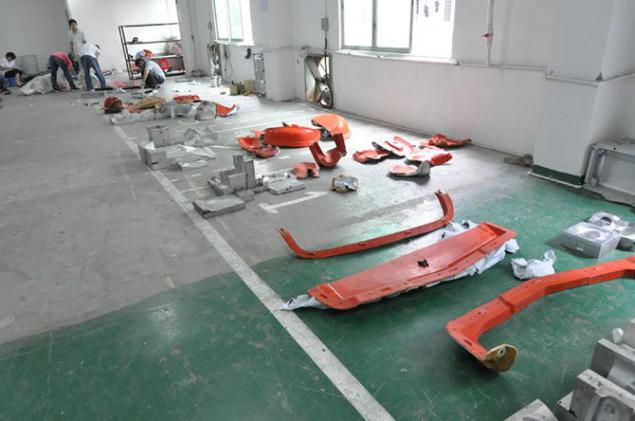
The process of carbon sticker was located behind the glass doors, but I flatly refused to show it, they say, a terrible trade secret. But I do not think that there is something secret, simply cut with scissors and placed in the form of scraps.
After that, each part is packed in vacuum bags.
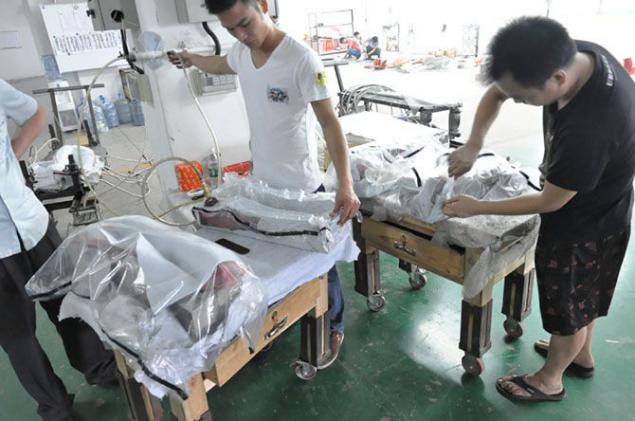
Air is pumped out of the packages and loaded into one of the two furnaces, more or less.
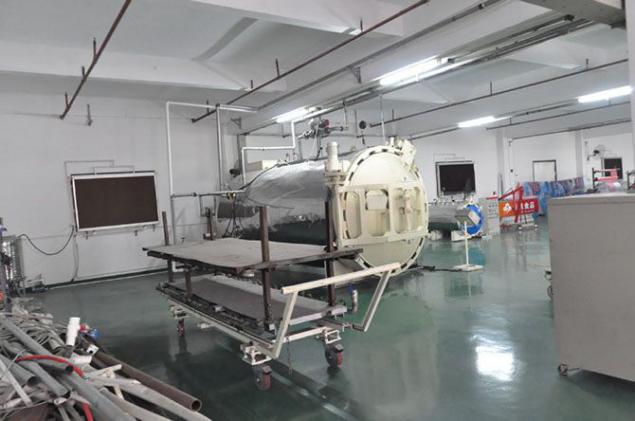
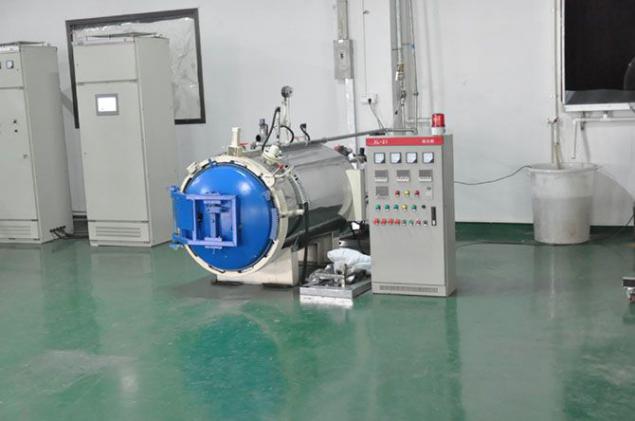
Finished parts are removed from the matrix. If the item is a complex form, and the matrix for it is a composite of several parts.
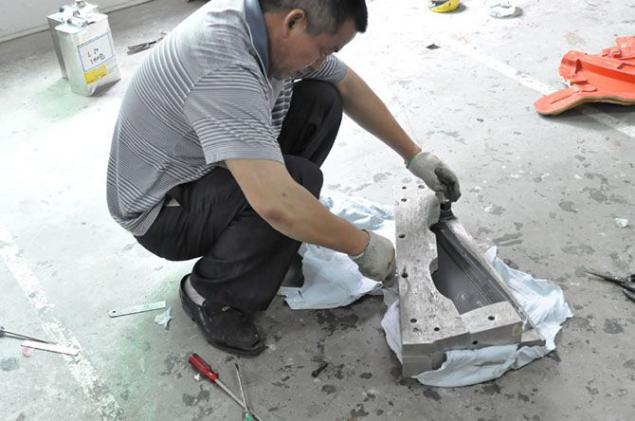
Quality control before delivery to the warehouse.
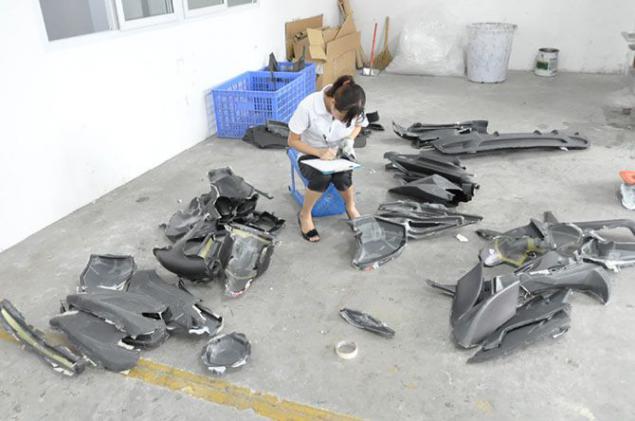
As you might imagine, this is not the whole process. Now, the details need to trim the edges and paint them with varnish. But this is a different site from the subcontractor. They offered to go and see, but I refused - that there is certainly nothing new.
Source: zorins.livejournal.com