1176
In "Maroussi" in the kitchen
The emergence of Russian national sports car still seems to be something incredible. We have long been accustomed to the idea that to date the peak of the evolution of the Russian automotive industry are outdated by at least a decade Lada Priora and Kalina, so imagine the serial domestic car, able to compete on the racetrack, for example, products of the company Lotus, difficult for us.
But in September, almost two years after the launch of the project on creation of the Russian sports car Marussia, in the center of Moscow has opened a showroom where anyone can order a one of the two production models "Maroussi" - B1 or B2. Both of the car - the most real mid-engined rear-drive sports coupe that can change the first hundred kilometers per hour in less than five seconds. And when you consider that the price of Marussia B1 start at 100 thousand euros, and on the Marussia B2 - from 117 thousand euro, it turns out that the creators of the project showman and racing driver Nikolay Fomenko and Yefim Ostrovsky political consultant prepared for sports car enthusiasts a real bomb. < br />
"Marussia Motors" has managed to hold sled presentation to customers ... abroad. The first official test held at the Paul Ricard circuit this summer. From the perspective of the creators of the project, this approach to the promotion of the Russian project is nothing strange - management decided that persuade motorists to buy Russian domestic sports cars will be possible only after they begin to demand from foreigners.
How are sales at "Maroussi" in Russia after the opening of the Moscow showroom, not yet reported, but the customers abroad, according to Fomenko, has enough: after the test in France "Marussia Motors" has received 700 orders from Western buyers.
A month after the opening of the auto show us "Avto.Lente" managed to get to the location of the company's plant in Moscow Marussia Motors, which established small-scale production of domestic "bomb».
Refrigerator
This is only the theater begins with a hanger, and any automobile plant - a large company logo at the entrance. But Marussia Motors is no own territory, so a visit to the Russian manufacturers of sports cars you get through the gate located near the metro station "Botanical Garden" plant for the production of refrigeration equipment "Snowflake", where the company leases a manufacturing facility.
However, being near a large office building "Marussia Motors" about "bytovuhu" forget - we would like, put on the production of sports cars. This clearly demonstrates parked in front of the porch Marussia B1, on which to work each day comes Marussia chief designer and vice president of the RAF Igor Ermilin. In Soviet times Ermilin worked in the laboratory of fast cars MADI. Then, four years ago, I created a racing prototype Fenix, who is ranked in the series due to a lack of investors.
With "Marusia" Ermilin lucky - this project has money. In the assembly shop, where we took the first thing the project manager Dmitry Rodionov, the work is in full swing - the six stocks set frames are in varying degrees of readiness of sports cars. At one stall is collected only in others it has already bolted front and rear subframes on which the suspension, engine, transmission and exhaust system.
This - not posed shot. Employees of the assembly shop and worked before we came there, and continued to work after we left.
Slipway installed in a spacious bright room of about 300 square meters. There is no doroguschego repair and clean floors, and workers do not go in white coats, but in ordinary blue overalls, but on the benches perfect order reigns, and the details laid out neatly on the shelves. No oil stains on the floors, large windows, a lot of air ... On the walls hang laminated drawings, BOMs and routings with all provisions of GOST frames, stamps and signatures, made the drawing calligraphic font. In general - a good working environment with a taste of the studio at some Soviet aircraft CB.
True, the first good impression just spoil the warning signs - like the one in which they say that the torque wrench is a "precision instrument" and use it as a hammer is needed. But, as explained to us Rodionov until such visual aids are necessary, as professionals ready to work in the assembly shop hard to find, and many workers have to train from scratch.
Semis
Models B1 and B2 differ among themselves only body design - is under the carbon-fiber monocoque panels on a spatial steel frame in both versions is the same. It is made here at the factory, only in the other shop: welded frame and twisted bolt of steel pipes (steel Russia, HGSA steel brand, which was created for the needs of the aviation industry), and the walls of the cabin is a "sandwich" of two aluminum sheets, the space between which is filled with a special foam. On some flat surface caused noise and anti-vibration material - is also home to use when building a music show cars.
Two "Marusya" had time to visit, and the British Silverstone, during the presentation of the joint project company Corsorth, Marussia Motors and formulaic Team Virgin F1.
The front and rear multi-link suspension for "Maroussi" - actually racing in its design. They are designed and tuned by own design office. Shock absorbers and springs - famous in the sports circles of the German brand KW, and their characteristics were selected specifically for Russian cars. By the body screw posts with several options settings stiffness (and compression and rebound) attached with eccentrics that allow you to change the clearance of the car literally on the sidelines. However, hardly a sports car owners for 100 thousand euros will be doing it yourself.
However, even full-time ride height at Marussia really small, so for all sports cars set the hydraulic system, through which the clearance can be increased from 55 to 110 millimeters by pressing the button in the cabin - for example, when it is necessary to move the lying policeman. It also supplies the KW. He says Rodionov, first had the idea of designers to use Russian shock absorbers "Plaza", but their characteristics appeared unstable, so I had to urgently seek a new partner - agreed with the Germans.
Call the manufacturer of brake system Rodionov refused, citing trade secrets (adding, however, that it is made not in Russia and in China), but that's about the engines that are installed on the Russian sports cars in "Marusya" says eagerly. Now, by ordering one of the models, you can choose from two power units designed for "Marusya Motors" company Cosworth. This is a 3, 5-liter "aspirated" power of 300 horsepower and 360-horsepower turbocharged engine capacity of 2, 8 liters. Transmission from "Marus" is one - six-step "automatic", but very soon it will be added and manual transmission. In addition, it is known that the turbo "six" of 2, 8 liters should see 420-strong version.
When you create a production plant management was faced with the fact that the labor market is desperately short of qualified specialists. Moreover, we are talking about professionals KB, and the workers who work in the shop.
Now at "Maroussia Motoros" employs about 300 people, of whom 150 are involved directly in production, and 52 specialists worked in the design office.
Learn from the workers that we met on the size of their salaries did not work - a specific amount, we did not call anybody. But it is the staff "Marussia Motors," with whom we were able to talk, argue that by the standards of Moscow factory pay "good money».
Impressions? Most positive. It can be seen, at least in the assembly shop of the project "Maroussia" really creates hands of Russian engineers and workers. And it is important for those who want to have their own Russian sports car appeared.
The design of the car, of course, missing parts that look, to put it mildly, unpresentable. For example, look into the cockpit of one of nedosobrannuyu "Marus", we first saw a large tin box of one of the controllers that control the vehicle electrics. And let this part none of the customers are likely to ever see in person, Rodionov agrees that not everything in the car the impression of technological masterpiece. But the arguments in favor of the sports car he has, "I assure you that I see in the car a lot more flaws than you. The design of the car is being finalized. But these "flaws", if I may call them, have no effect on his driving and other consumer qualities ».
Stove-shop
Production of "Marus" - a self-contained, almost like "AvtoVAZ". At the plant there own metalworking shop and the assembly line, and a great body for the production of carboxylic body panels that are "baked" here - on the territory of the plant "Snowflake". It is also the body, which employs engineers and designers, and are also being developed, digitized and then machined on CNC master template for the subsequent manufacture of carbon fiber parts.
As it happens, we have seen with their own eyes - installed in a separate room five-axis milling machine often have to include, to carve out new forms of boobs to replace those that are deteriorating - a matrix enough to produce 100 parts. Thereafter, it cracks and scratches, because of which the part quality deteriorates.
The process of making matrix is impressive - the machine is a steel frame height by three meters, on which the manipulator moves to the cutter. With this machine we are cut from a large piece of laminated polymer to form the side panels of one of the "Marus". On the part of these manipulations are similar to the lesson of calligraphy for the hand of a giant robot.
1 Harvesting matrix for one of the body panels Marussia.
2 The accuracy with which operates the cutter is impressive - almost perfect surfaces are smooth and require minimal further revision.
3 cube, from which then machined blank is glued together several layers of solid polymer.
2 Impregnation of carbon fiber fabric with a thermosetting resin.
When the matrix is prepared, it is treated and then repeatedly laid carbon fiber fabric that is impregnated with thermosetting resin. The resulting "sandwich" harden for several hours in an autoclave where the temperature is gradually increased to 180 degrees, and the pressure - up to eight bar.
The shop, which are glued and processed future body panels, looks are not so technologically, as the room with a robotic milling machines, and not as neat as the assembly site. There is clearly not enough shelving for storing blanks, and two spray booths where the resin impregnated cloth is not enough space for working with spray paint guns, matrices, and many cans and boxes of chemicals. And around the repair shop would not be prevented, but, apparently, as long as the plant does not have enough resources to it to put in order the dirtiest stage in the processing chain.
Ready-made body parts painted by hand, in a normal good spray booth. Paint use modern, water-based, which is applied to the body parts in three layers - to reduce the impact of carbon texture on the exterior paintwork. However, perfectly smooth parts still do not look - if you look closely, the surface of any body made of carbon fiber (even big-name producers) barely noticeable Bouguereau like "shagreen" in the paint.
The appearance of both modifications Marussia sports coupe was developed in Russia by domestic designers. Services of foreign companies in matters of design initiators and investors of the project decided not to use.
Lapping driving performance "Marus" Russian experts were engaged, too. This itself Nikolai Fomenko, who has experience of playing in international racing series, and invited experts, whose names somehow kept secret.
But sometimes painted parts do not have to - some customers are asked to make a body of unpainted carbon fiber. According to Rodionov, the factory "Marussia Motors" and are ready to execute such an order, but without painting the car will cost the customer more expensive than painted - the so-called "species" carbon difficult to manufacture, as in this case it is necessary to achieve a perfect seal, and pieces of carbon fiber fabric monitor closely the pattern of weaving on all surfaces.
Unpainted body - this is only one of many options for personalization, available to customers, "Marus". For example, for each machine by default sewn unique interior. Design plastic interior elements, such as buttons, door handles and steering wheel, too easy to change - because they are made in the shop adjacent to the painting area using the technology that makes it easy to modify the shape of manufactured parts.
How? The developers are coming up with the design bureau Design details - for example, buttons to the front panel, then "grown" on its 3D-plotter and transmitted to the injection site. There, with the help of a master sample in two hours made a silicone mold (much time is needed to silicone "rose"), and the resulting matrix is filled with polyurethane, which hardens in a vacuum molding machine for 40 minutes. In mass production changeover thermoforming equipment for such a short time and with such microscopic costs, of course, impossible. This finished parts require almost no post-processing - it is only necessary to clean off the burr and the color of the polymer can be almost anyone.
Casting technology in silicone molds with which the plant "Marussia Motors" made of polyurethane buttons, door handles and other plastic interior parts 1, can not be called difficult. In the presence of a master sample manufacturing silicone matrix only takes two hours. It's enough to fill a liquid solution master-detail and allow to harden the silicone. Then the matrix 3 is cut into two parts, cut holes in it, through which it is fed, and liquid polyurethane displaced by leaving them air stapler fasten the two halves and placed in a vacuum shape molding machine 4.
Here, in vacuo, plasticizer and filler are mixed 2. The mixture was then poured into a mold and cured at a temperature of 40-60 degrees Celsius to harden the polymer. The finished item is removed from the mold, cleaned from burr, grind and sent to the assembly plant. One form is sufficient for 30 - 35 castings, and all year requires 300 - 500 of products of the same type.
In fact, the buyer "Maroussi" can order not only individual interior paint scheme, or a body, but also the design of the machine. After all, our own production of body panels enables designers to make changes to their form at any time. The main thing is to have enough money for a client a whim.
OUTLOOK
Impressions from a visit to the factory "Marusya Motors" have been mixed. On the one hand, we have not seen any high-tech assembly line that we drew imagination, or "sink" ready, bright cars, awaiting its customers. On the other hand, the Moscow company Marussia - is not a "Potemkin village", and work in the shops in full swing, although it very few people know.
According to Rodionov, the attitude to the Russian media "Marusya" can be described more as a negative, whereas abroad the Russian sports car was greeted with great optimism. "At the exhibition in Monaco to our stand came a wealthy man from somewhere in the Emirates and said that he was ready to buy a car exhibition right now, paying on the spot, - says Dmitry. - Had to be abandoned, as this car, we could not sell, and the buyer was very upset ».
One of the clearest examples of the Napoleonic pretensions Marissia Motors Company is the project for the production of its own crossover. At the opening of the Moscow showroom Nikolai Fomenko said that three years later near Volokolamsk near Moscow will open the company's plant, which will be deployed edition coupe Marussia F2, and its capacity is 10 thousand cars a year.
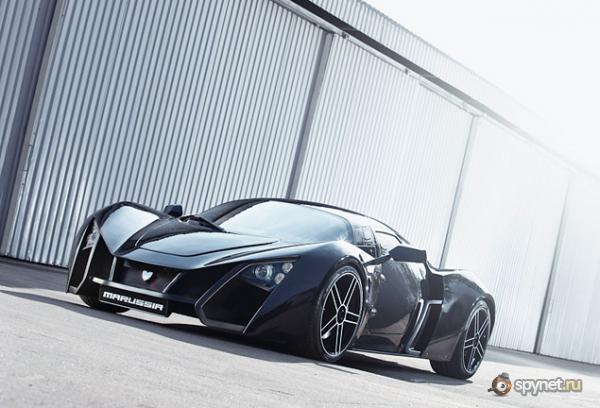
But in September, almost two years after the launch of the project on creation of the Russian sports car Marussia, in the center of Moscow has opened a showroom where anyone can order a one of the two production models "Maroussi" - B1 or B2. Both of the car - the most real mid-engined rear-drive sports coupe that can change the first hundred kilometers per hour in less than five seconds. And when you consider that the price of Marussia B1 start at 100 thousand euros, and on the Marussia B2 - from 117 thousand euro, it turns out that the creators of the project showman and racing driver Nikolay Fomenko and Yefim Ostrovsky political consultant prepared for sports car enthusiasts a real bomb. < br />
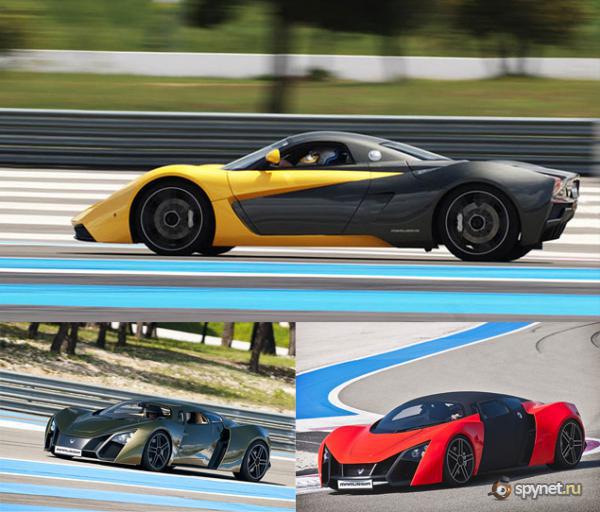
"Marussia Motors" has managed to hold sled presentation to customers ... abroad. The first official test held at the Paul Ricard circuit this summer. From the perspective of the creators of the project, this approach to the promotion of the Russian project is nothing strange - management decided that persuade motorists to buy Russian domestic sports cars will be possible only after they begin to demand from foreigners.
How are sales at "Maroussi" in Russia after the opening of the Moscow showroom, not yet reported, but the customers abroad, according to Fomenko, has enough: after the test in France "Marussia Motors" has received 700 orders from Western buyers.
A month after the opening of the auto show us "Avto.Lente" managed to get to the location of the company's plant in Moscow Marussia Motors, which established small-scale production of domestic "bomb».
Refrigerator
This is only the theater begins with a hanger, and any automobile plant - a large company logo at the entrance. But Marussia Motors is no own territory, so a visit to the Russian manufacturers of sports cars you get through the gate located near the metro station "Botanical Garden" plant for the production of refrigeration equipment "Snowflake", where the company leases a manufacturing facility.
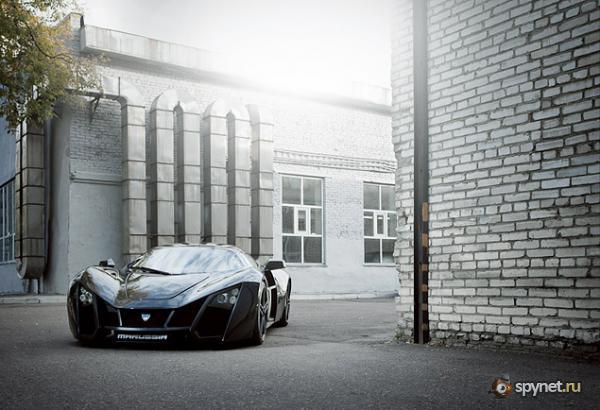
However, being near a large office building "Marussia Motors" about "bytovuhu" forget - we would like, put on the production of sports cars. This clearly demonstrates parked in front of the porch Marussia B1, on which to work each day comes Marussia chief designer and vice president of the RAF Igor Ermilin. In Soviet times Ermilin worked in the laboratory of fast cars MADI. Then, four years ago, I created a racing prototype Fenix, who is ranked in the series due to a lack of investors.
With "Marusia" Ermilin lucky - this project has money. In the assembly shop, where we took the first thing the project manager Dmitry Rodionov, the work is in full swing - the six stocks set frames are in varying degrees of readiness of sports cars. At one stall is collected only in others it has already bolted front and rear subframes on which the suspension, engine, transmission and exhaust system.
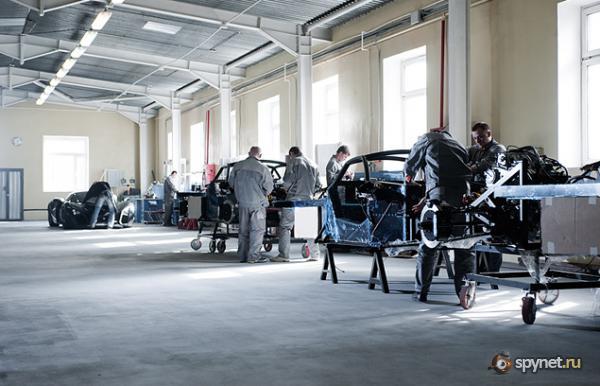
This - not posed shot. Employees of the assembly shop and worked before we came there, and continued to work after we left.
Slipway installed in a spacious bright room of about 300 square meters. There is no doroguschego repair and clean floors, and workers do not go in white coats, but in ordinary blue overalls, but on the benches perfect order reigns, and the details laid out neatly on the shelves. No oil stains on the floors, large windows, a lot of air ... On the walls hang laminated drawings, BOMs and routings with all provisions of GOST frames, stamps and signatures, made the drawing calligraphic font. In general - a good working environment with a taste of the studio at some Soviet aircraft CB.
True, the first good impression just spoil the warning signs - like the one in which they say that the torque wrench is a "precision instrument" and use it as a hammer is needed. But, as explained to us Rodionov until such visual aids are necessary, as professionals ready to work in the assembly shop hard to find, and many workers have to train from scratch.
Semis
Models B1 and B2 differ among themselves only body design - is under the carbon-fiber monocoque panels on a spatial steel frame in both versions is the same. It is made here at the factory, only in the other shop: welded frame and twisted bolt of steel pipes (steel Russia, HGSA steel brand, which was created for the needs of the aviation industry), and the walls of the cabin is a "sandwich" of two aluminum sheets, the space between which is filled with a special foam. On some flat surface caused noise and anti-vibration material - is also home to use when building a music show cars.
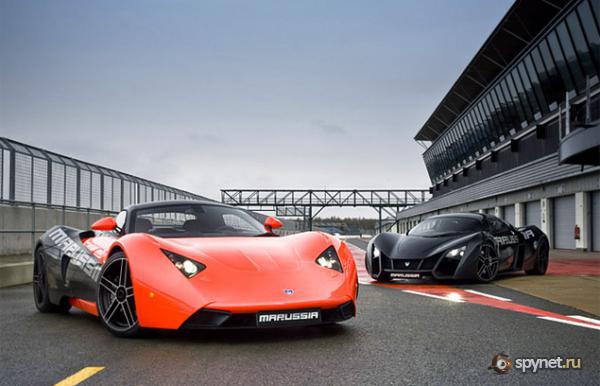
Two "Marusya" had time to visit, and the British Silverstone, during the presentation of the joint project company Corsorth, Marussia Motors and formulaic Team Virgin F1.
The front and rear multi-link suspension for "Maroussi" - actually racing in its design. They are designed and tuned by own design office. Shock absorbers and springs - famous in the sports circles of the German brand KW, and their characteristics were selected specifically for Russian cars. By the body screw posts with several options settings stiffness (and compression and rebound) attached with eccentrics that allow you to change the clearance of the car literally on the sidelines. However, hardly a sports car owners for 100 thousand euros will be doing it yourself.
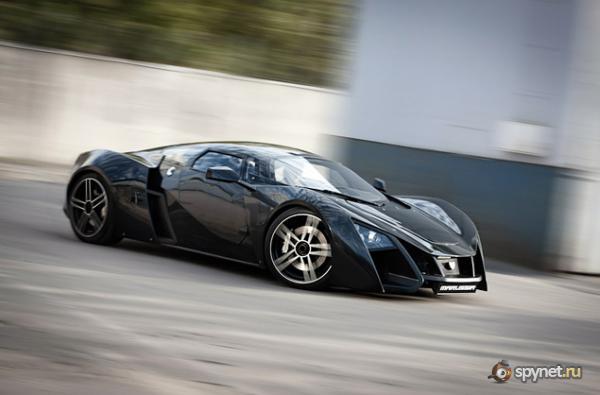
However, even full-time ride height at Marussia really small, so for all sports cars set the hydraulic system, through which the clearance can be increased from 55 to 110 millimeters by pressing the button in the cabin - for example, when it is necessary to move the lying policeman. It also supplies the KW. He says Rodionov, first had the idea of designers to use Russian shock absorbers "Plaza", but their characteristics appeared unstable, so I had to urgently seek a new partner - agreed with the Germans.
Call the manufacturer of brake system Rodionov refused, citing trade secrets (adding, however, that it is made not in Russia and in China), but that's about the engines that are installed on the Russian sports cars in "Marusya" says eagerly. Now, by ordering one of the models, you can choose from two power units designed for "Marusya Motors" company Cosworth. This is a 3, 5-liter "aspirated" power of 300 horsepower and 360-horsepower turbocharged engine capacity of 2, 8 liters. Transmission from "Marus" is one - six-step "automatic", but very soon it will be added and manual transmission. In addition, it is known that the turbo "six" of 2, 8 liters should see 420-strong version.
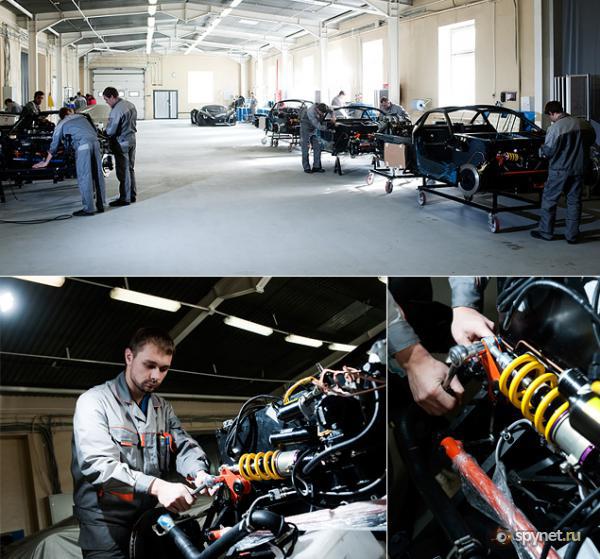
When you create a production plant management was faced with the fact that the labor market is desperately short of qualified specialists. Moreover, we are talking about professionals KB, and the workers who work in the shop.
Now at "Maroussia Motoros" employs about 300 people, of whom 150 are involved directly in production, and 52 specialists worked in the design office.
Learn from the workers that we met on the size of their salaries did not work - a specific amount, we did not call anybody. But it is the staff "Marussia Motors," with whom we were able to talk, argue that by the standards of Moscow factory pay "good money».
Impressions? Most positive. It can be seen, at least in the assembly shop of the project "Maroussia" really creates hands of Russian engineers and workers. And it is important for those who want to have their own Russian sports car appeared.
The design of the car, of course, missing parts that look, to put it mildly, unpresentable. For example, look into the cockpit of one of nedosobrannuyu "Marus", we first saw a large tin box of one of the controllers that control the vehicle electrics. And let this part none of the customers are likely to ever see in person, Rodionov agrees that not everything in the car the impression of technological masterpiece. But the arguments in favor of the sports car he has, "I assure you that I see in the car a lot more flaws than you. The design of the car is being finalized. But these "flaws", if I may call them, have no effect on his driving and other consumer qualities ».
Stove-shop
Production of "Marus" - a self-contained, almost like "AvtoVAZ". At the plant there own metalworking shop and the assembly line, and a great body for the production of carboxylic body panels that are "baked" here - on the territory of the plant "Snowflake". It is also the body, which employs engineers and designers, and are also being developed, digitized and then machined on CNC master template for the subsequent manufacture of carbon fiber parts.
As it happens, we have seen with their own eyes - installed in a separate room five-axis milling machine often have to include, to carve out new forms of boobs to replace those that are deteriorating - a matrix enough to produce 100 parts. Thereafter, it cracks and scratches, because of which the part quality deteriorates.
The process of making matrix is impressive - the machine is a steel frame height by three meters, on which the manipulator moves to the cutter. With this machine we are cut from a large piece of laminated polymer to form the side panels of one of the "Marus". On the part of these manipulations are similar to the lesson of calligraphy for the hand of a giant robot.
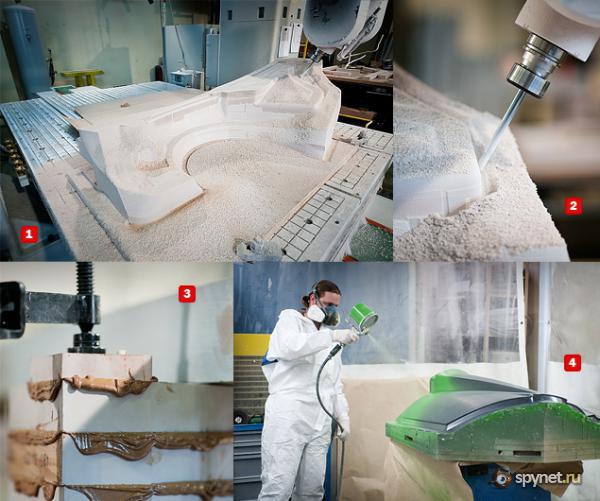
1 Harvesting matrix for one of the body panels Marussia.
2 The accuracy with which operates the cutter is impressive - almost perfect surfaces are smooth and require minimal further revision.
3 cube, from which then machined blank is glued together several layers of solid polymer.
2 Impregnation of carbon fiber fabric with a thermosetting resin.
When the matrix is prepared, it is treated and then repeatedly laid carbon fiber fabric that is impregnated with thermosetting resin. The resulting "sandwich" harden for several hours in an autoclave where the temperature is gradually increased to 180 degrees, and the pressure - up to eight bar.
The shop, which are glued and processed future body panels, looks are not so technologically, as the room with a robotic milling machines, and not as neat as the assembly site. There is clearly not enough shelving for storing blanks, and two spray booths where the resin impregnated cloth is not enough space for working with spray paint guns, matrices, and many cans and boxes of chemicals. And around the repair shop would not be prevented, but, apparently, as long as the plant does not have enough resources to it to put in order the dirtiest stage in the processing chain.
Ready-made body parts painted by hand, in a normal good spray booth. Paint use modern, water-based, which is applied to the body parts in three layers - to reduce the impact of carbon texture on the exterior paintwork. However, perfectly smooth parts still do not look - if you look closely, the surface of any body made of carbon fiber (even big-name producers) barely noticeable Bouguereau like "shagreen" in the paint.
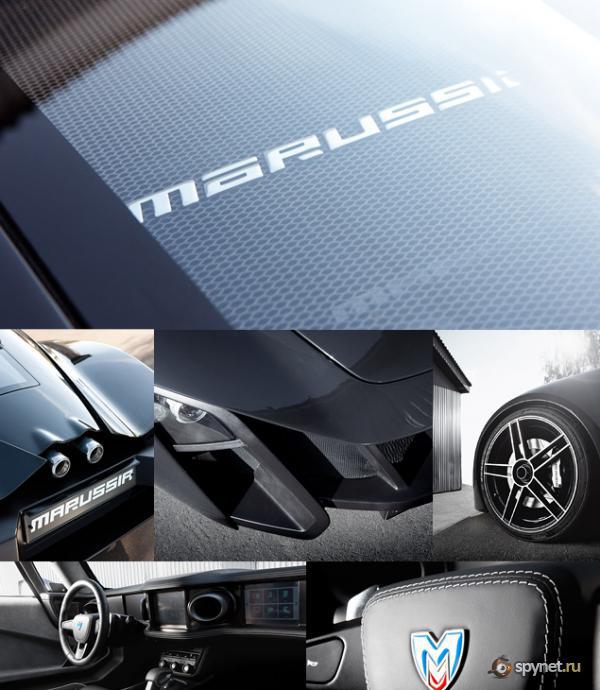
The appearance of both modifications Marussia sports coupe was developed in Russia by domestic designers. Services of foreign companies in matters of design initiators and investors of the project decided not to use.
Lapping driving performance "Marus" Russian experts were engaged, too. This itself Nikolai Fomenko, who has experience of playing in international racing series, and invited experts, whose names somehow kept secret.
But sometimes painted parts do not have to - some customers are asked to make a body of unpainted carbon fiber. According to Rodionov, the factory "Marussia Motors" and are ready to execute such an order, but without painting the car will cost the customer more expensive than painted - the so-called "species" carbon difficult to manufacture, as in this case it is necessary to achieve a perfect seal, and pieces of carbon fiber fabric monitor closely the pattern of weaving on all surfaces.
Unpainted body - this is only one of many options for personalization, available to customers, "Marus". For example, for each machine by default sewn unique interior. Design plastic interior elements, such as buttons, door handles and steering wheel, too easy to change - because they are made in the shop adjacent to the painting area using the technology that makes it easy to modify the shape of manufactured parts.
How? The developers are coming up with the design bureau Design details - for example, buttons to the front panel, then "grown" on its 3D-plotter and transmitted to the injection site. There, with the help of a master sample in two hours made a silicone mold (much time is needed to silicone "rose"), and the resulting matrix is filled with polyurethane, which hardens in a vacuum molding machine for 40 minutes. In mass production changeover thermoforming equipment for such a short time and with such microscopic costs, of course, impossible. This finished parts require almost no post-processing - it is only necessary to clean off the burr and the color of the polymer can be almost anyone.
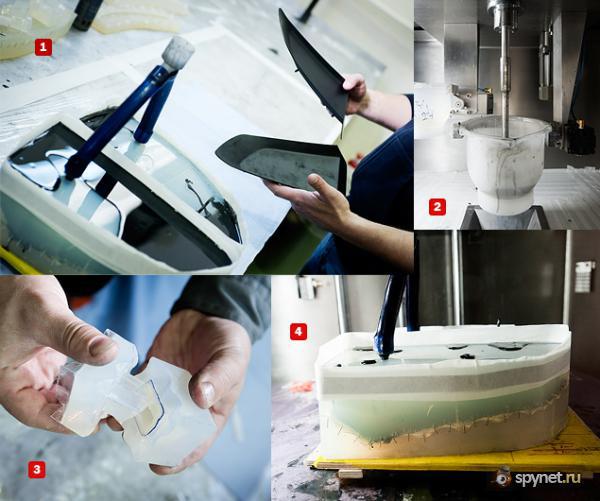
Casting technology in silicone molds with which the plant "Marussia Motors" made of polyurethane buttons, door handles and other plastic interior parts 1, can not be called difficult. In the presence of a master sample manufacturing silicone matrix only takes two hours. It's enough to fill a liquid solution master-detail and allow to harden the silicone. Then the matrix 3 is cut into two parts, cut holes in it, through which it is fed, and liquid polyurethane displaced by leaving them air stapler fasten the two halves and placed in a vacuum shape molding machine 4.
Here, in vacuo, plasticizer and filler are mixed 2. The mixture was then poured into a mold and cured at a temperature of 40-60 degrees Celsius to harden the polymer. The finished item is removed from the mold, cleaned from burr, grind and sent to the assembly plant. One form is sufficient for 30 - 35 castings, and all year requires 300 - 500 of products of the same type.
In fact, the buyer "Maroussi" can order not only individual interior paint scheme, or a body, but also the design of the machine. After all, our own production of body panels enables designers to make changes to their form at any time. The main thing is to have enough money for a client a whim.
OUTLOOK
Impressions from a visit to the factory "Marusya Motors" have been mixed. On the one hand, we have not seen any high-tech assembly line that we drew imagination, or "sink" ready, bright cars, awaiting its customers. On the other hand, the Moscow company Marussia - is not a "Potemkin village", and work in the shops in full swing, although it very few people know.
According to Rodionov, the attitude to the Russian media "Marusya" can be described more as a negative, whereas abroad the Russian sports car was greeted with great optimism. "At the exhibition in Monaco to our stand came a wealthy man from somewhere in the Emirates and said that he was ready to buy a car exhibition right now, paying on the spot, - says Dmitry. - Had to be abandoned, as this car, we could not sell, and the buyer was very upset ».
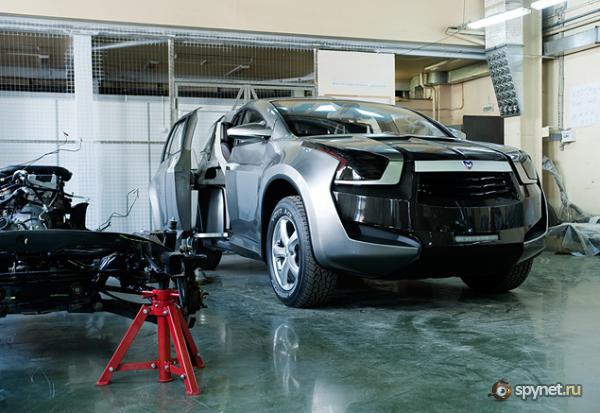
One of the clearest examples of the Napoleonic pretensions Marissia Motors Company is the project for the production of its own crossover. At the opening of the Moscow showroom Nikolai Fomenko said that three years later near Volokolamsk near Moscow will open the company's plant, which will be deployed edition coupe Marussia F2, and its capacity is 10 thousand cars a year.