1277
Photos from the first test drive Yo-mobile (18 photos)
Just a few months ago it was announced that the first cars that were supposed to get off the assembly line in late 2012 - early 2013, there will be only through 2-2, 5 years. Hitch turned to layoffs in the companies, but the development of the car continues and ambitious plans - in effect.
Ensure that we have succeeded in secrecy (no cameras, camcorders, and even voice recorders) at the site in Minsk, where the prototypes are being tested. Of course, we do not even have shown pre-production sample, and the so-called mullahs - a model with a body from another machine, but equipped with all the units of the future crossover.
Preceded by acquaintance with the novelty press conference held by the new General Director of "e-AUTO" Andrew Ginsburg, "One of the goals of the event - it is a little break appeared in recent skepticism about the fact that we are doing something incomprehensible without result . We want to show that, in principle, all of what we have said, is borne out not only in words, but in reality "- said Ginsburg. According to the CEO of the company, the project will be completed before the end of this year. After that, it will give the partners who will bring it into compliance with Russian standards.
Ginsburg said that the main innovation which e-mobility threatens competitors - a buffer storage of energy on the basis of small supercapacitor. "This is the fundamental difference between our hybrid of all declared and produced at the moment of this class of cars, - said Ginsburg. - He not only gives us the opportunity to overcome the short distances, but, most importantly, very well dispersed and effective use of the braking energy, taking it most. All currently existing hybrid battery simply does not allow to collect a part of it. " A little later, at the site, Ginsburg called the approximate figures: Yo-crossover collects up to 60% of the braking energy, while, as, for example, Toyota Prius - not more than 30%
.
Basic questions of journalists called the body - because it is not found in nature. "To date, we have come to a situation where the power function takes on the frame, made by stamping and forming technology. This frame is nevertheless significantly stronger monocoque, has a much smaller number of parts and the very power structure is about 30% lighter than a traditional monocoque. The outer surface of the body is scheduled to make a special material. These are materials based on ABS, pre-painted, which eliminates the need for painting line at our plant, and allows us to significantly save money and be more environmentally friendly. This material allows a perfectly normal to carry out any repair work in a normal car service. Breakdowns are restored roughly the same way as failure motorcycle plating ". - Ginsburg explained
.
So, the main features of the crossover: the work on the gas and gasoline, low fuel consumption (according to test results, 6 liters per 100 km in the city), light weight (about 1 300 kg), and, of course, mechatronic module. Ginsburg assured that it is no analogues: "I can not say that this is some kind of revolution, but at the moment these units are not available on the world market for sure. This module we are developing in collaboration with a fairly well known company KTM. Develop a long time, since the beginning of the year, these modules are tested at the landfill. For quite a high mileage. Today we can say that it is a finished product, which is already preparing for mass production, and that we will be in this year's show at an exhibition in Crocus-Expo. The module contains a motor, two stage gearbox with differential, control electronics, cooling system. This module weighs less than 50 kilograms. "
So, on the road ...
Skepticism vanished, had only to pull on a test specimen with the place. It feels like, the car accelerates from zero to 60 km / h in less than 3 seconds, after which, however, should be a certain failure, and after 80 km / h the car accelerates very reluctantly. Anyway, the performance for driving on city commendable. And this despite the fact that the mass of the test body around 300 kg higher than that will be placed on production machines. Bring the car on the line get up to speed 129 km / h (on the straight part of the track is about 3 km long, in the "gas to the floor" position). Rate control innovations for obvious reasons - because of the lack of "native" of the body - is impossible
.
Hold down the speed of around 50 km / h, I was able to pass only on electricity for about 2 km, then turn the engine. Interestingly, it is not connected immediately when sudden acceleration, as in most hybrids: while it is possible, the car accelerates only on electricity. Connecting ICE, by the way, is very sharp. The machine for a split second loses momentum booster, it seems, even the brakes. However, in the second instance, which was made a month later, this process has been going much more smoothly.
Differ mullahs and interior decoration. If older is only one display, acting as a dashboard (here and speedometer, and a supercapacitor charge information, and other communications), the second and more entertainment, built on the Android system. While the software is still not fully developed, but it is available the radio, and some functionality to "listalkoy" screen in the manner of tablets, and the background is the animation demonstrates the impressive graphics capabilities of the device. Perhaps, after 2 years, when the first serial crossover e-mobility, similar devices will be equipped with most of the cars, but now it looks quite unusual.
In general, despite the lack of e-mobile body, we were able to confirm one thing: it exists. And this is probably good news. Still to this technological twists to make an attractive body and the normal noise insulation, keep the dynamic performance and fuel consumption at the current level, as well as leave the price on the stated level (400 000) - then a novelty even possible to count on a certain success. And if all that will live up to the assembly line, and does not mutate into a budget cars from the last century, the words of Dmitry Jarota, said in an informal conversation on the way to the track, you will need to carve in granite: "The people who did this damn - them for it
not ashamed. " Source: autonews.ru -
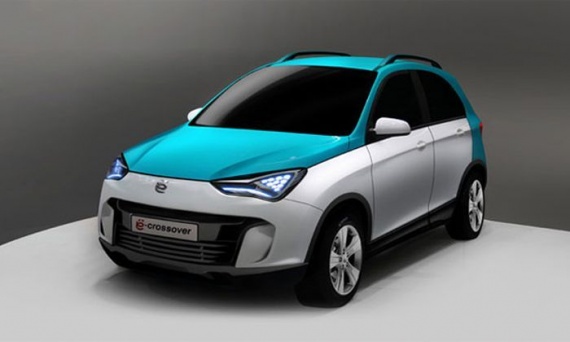
Ensure that we have succeeded in secrecy (no cameras, camcorders, and even voice recorders) at the site in Minsk, where the prototypes are being tested. Of course, we do not even have shown pre-production sample, and the so-called mullahs - a model with a body from another machine, but equipped with all the units of the future crossover.
Preceded by acquaintance with the novelty press conference held by the new General Director of "e-AUTO" Andrew Ginsburg, "One of the goals of the event - it is a little break appeared in recent skepticism about the fact that we are doing something incomprehensible without result . We want to show that, in principle, all of what we have said, is borne out not only in words, but in reality "- said Ginsburg. According to the CEO of the company, the project will be completed before the end of this year. After that, it will give the partners who will bring it into compliance with Russian standards.
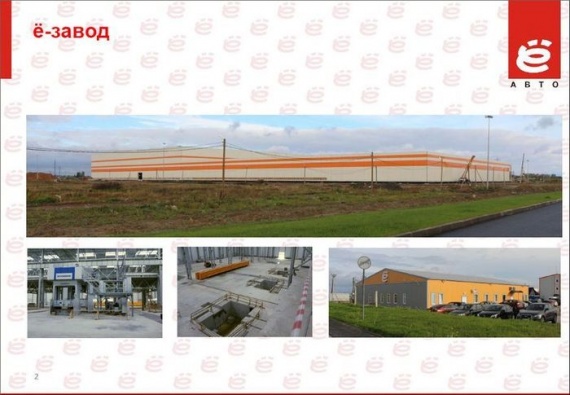
Ginsburg said that the main innovation which e-mobility threatens competitors - a buffer storage of energy on the basis of small supercapacitor. "This is the fundamental difference between our hybrid of all declared and produced at the moment of this class of cars, - said Ginsburg. - He not only gives us the opportunity to overcome the short distances, but, most importantly, very well dispersed and effective use of the braking energy, taking it most. All currently existing hybrid battery simply does not allow to collect a part of it. " A little later, at the site, Ginsburg called the approximate figures: Yo-crossover collects up to 60% of the braking energy, while, as, for example, Toyota Prius - not more than 30%
.
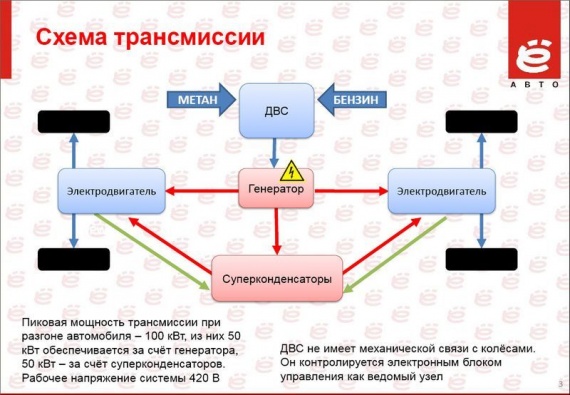
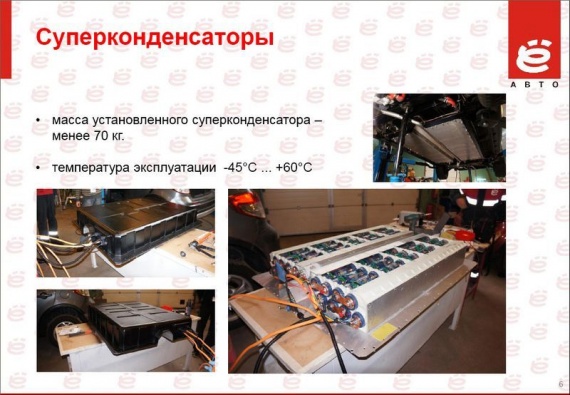
Basic questions of journalists called the body - because it is not found in nature. "To date, we have come to a situation where the power function takes on the frame, made by stamping and forming technology. This frame is nevertheless significantly stronger monocoque, has a much smaller number of parts and the very power structure is about 30% lighter than a traditional monocoque. The outer surface of the body is scheduled to make a special material. These are materials based on ABS, pre-painted, which eliminates the need for painting line at our plant, and allows us to significantly save money and be more environmentally friendly. This material allows a perfectly normal to carry out any repair work in a normal car service. Breakdowns are restored roughly the same way as failure motorcycle plating ". - Ginsburg explained
.
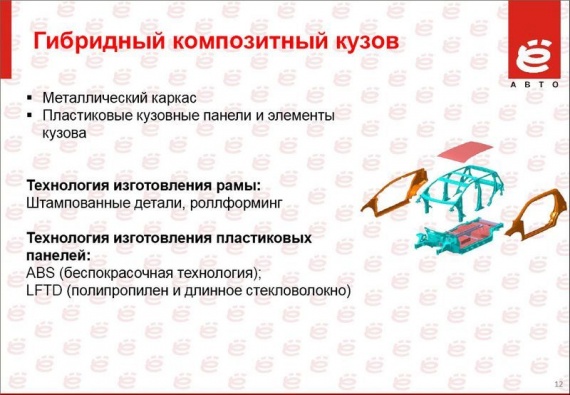
So, the main features of the crossover: the work on the gas and gasoline, low fuel consumption (according to test results, 6 liters per 100 km in the city), light weight (about 1 300 kg), and, of course, mechatronic module. Ginsburg assured that it is no analogues: "I can not say that this is some kind of revolution, but at the moment these units are not available on the world market for sure. This module we are developing in collaboration with a fairly well known company KTM. Develop a long time, since the beginning of the year, these modules are tested at the landfill. For quite a high mileage. Today we can say that it is a finished product, which is already preparing for mass production, and that we will be in this year's show at an exhibition in Crocus-Expo. The module contains a motor, two stage gearbox with differential, control electronics, cooling system. This module weighs less than 50 kilograms. "
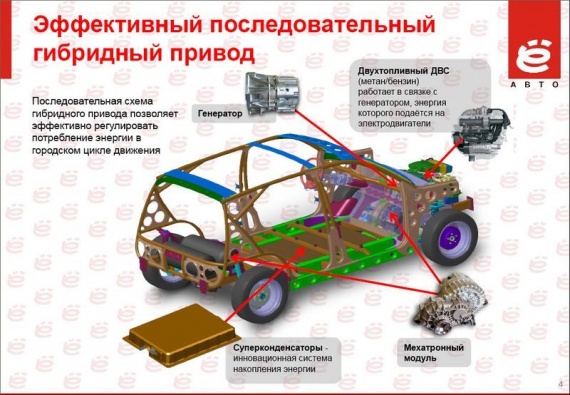
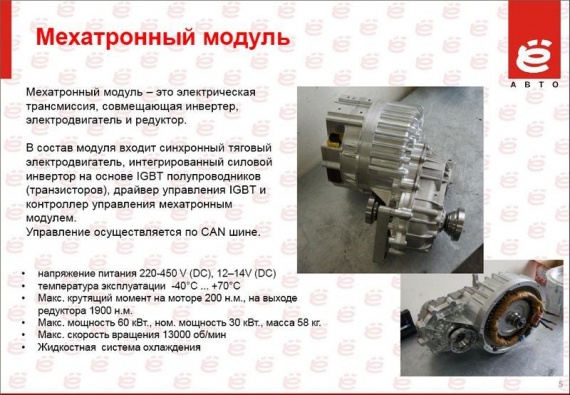
So, on the road ...
Skepticism vanished, had only to pull on a test specimen with the place. It feels like, the car accelerates from zero to 60 km / h in less than 3 seconds, after which, however, should be a certain failure, and after 80 km / h the car accelerates very reluctantly. Anyway, the performance for driving on city commendable. And this despite the fact that the mass of the test body around 300 kg higher than that will be placed on production machines. Bring the car on the line get up to speed 129 km / h (on the straight part of the track is about 3 km long, in the "gas to the floor" position). Rate control innovations for obvious reasons - because of the lack of "native" of the body - is impossible
.
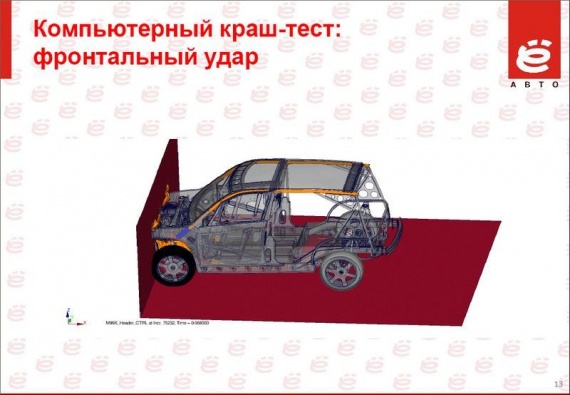
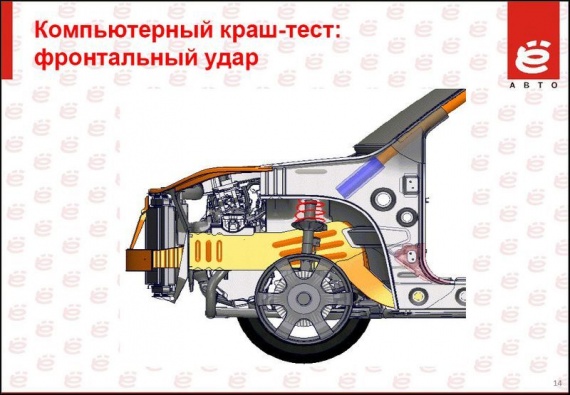
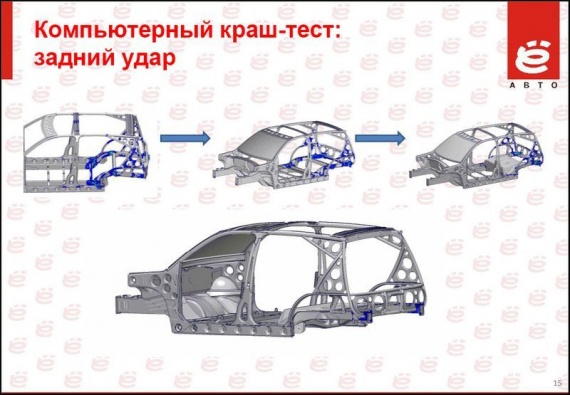
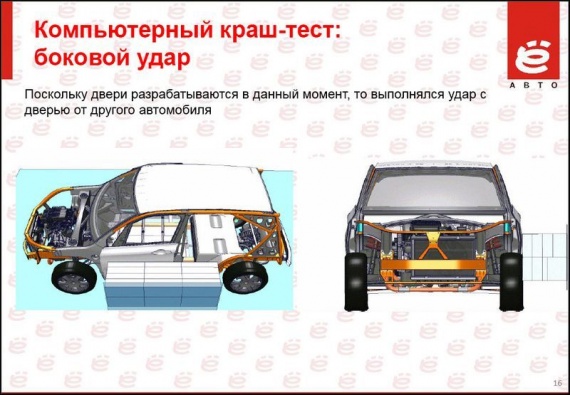
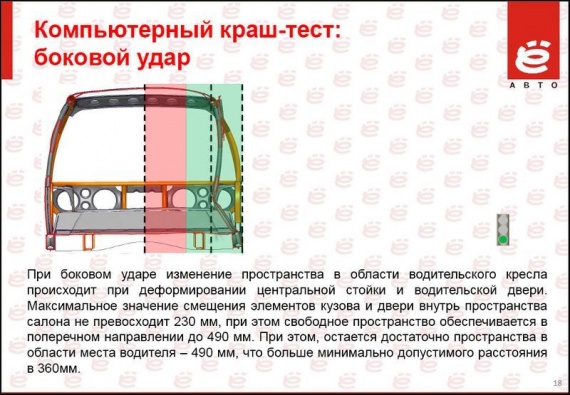
Hold down the speed of around 50 km / h, I was able to pass only on electricity for about 2 km, then turn the engine. Interestingly, it is not connected immediately when sudden acceleration, as in most hybrids: while it is possible, the car accelerates only on electricity. Connecting ICE, by the way, is very sharp. The machine for a split second loses momentum booster, it seems, even the brakes. However, in the second instance, which was made a month later, this process has been going much more smoothly.
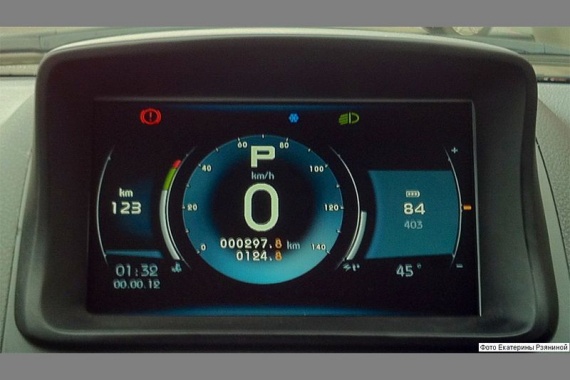
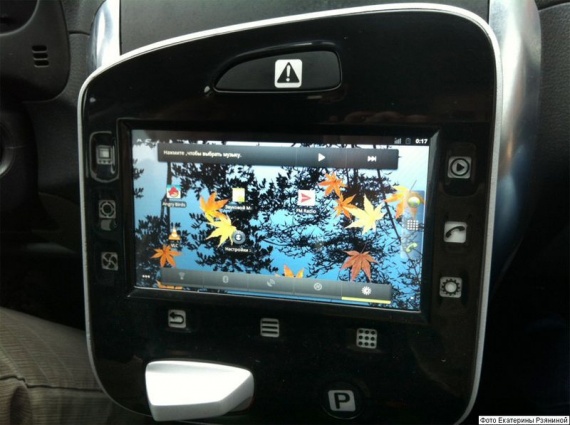
Differ mullahs and interior decoration. If older is only one display, acting as a dashboard (here and speedometer, and a supercapacitor charge information, and other communications), the second and more entertainment, built on the Android system. While the software is still not fully developed, but it is available the radio, and some functionality to "listalkoy" screen in the manner of tablets, and the background is the animation demonstrates the impressive graphics capabilities of the device. Perhaps, after 2 years, when the first serial crossover e-mobility, similar devices will be equipped with most of the cars, but now it looks quite unusual.
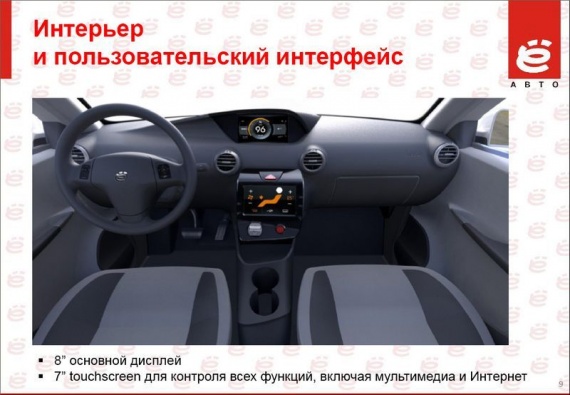
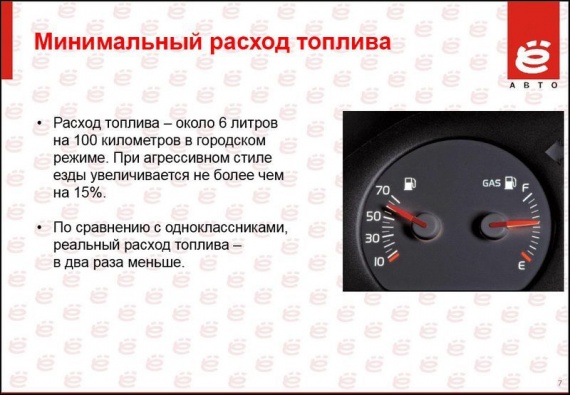
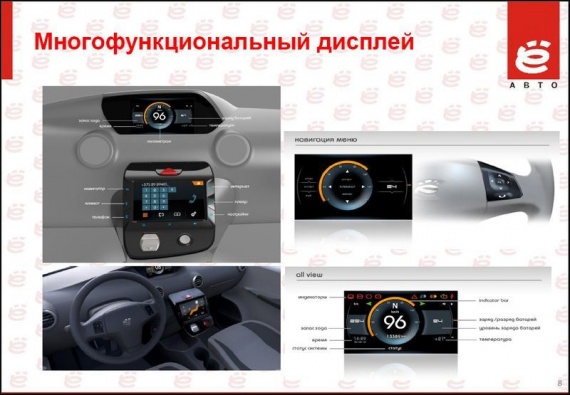
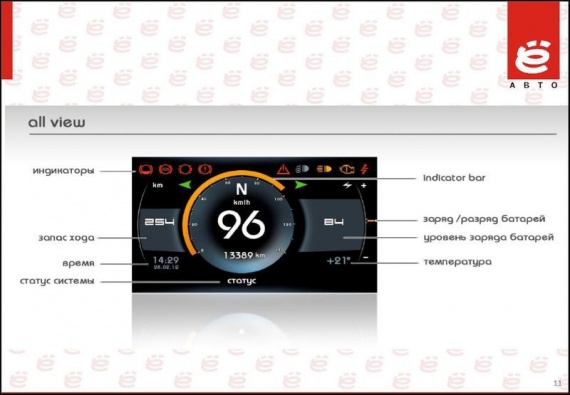
In general, despite the lack of e-mobile body, we were able to confirm one thing: it exists. And this is probably good news. Still to this technological twists to make an attractive body and the normal noise insulation, keep the dynamic performance and fuel consumption at the current level, as well as leave the price on the stated level (400 000) - then a novelty even possible to count on a certain success. And if all that will live up to the assembly line, and does not mutate into a budget cars from the last century, the words of Dmitry Jarota, said in an informal conversation on the way to the track, you will need to carve in granite: "The people who did this damn - them for it
not ashamed. " Source: autonews.ru -