267
Combined heating boilers: gas-electric or gas-fired
Why choose between different types of energy when you can use several? We will introduce you to hybrid heating equipment: the bases for installing boilers for different types of fuel, the advantages of different combinations, the features of installation and use.
The two main types of hybrid boilers
Manufacturers periodically expand the range of technical means designed to increase the efficiency of heating equipment. However, the main schemes of the device for working on combined fuel are only two:
The difference between boilers with combined and separate furnaces is obvious. On the one hand, the production of single-chamber units implies a lower material intensity, respectively, the weight and dimensions in the end are relatively low. The other side of the coin is negative – it is very difficult to achieve the same high efficiency of burning different types of fuel, in this matter, unification is not beneficial.
The problem is that the heat and composition of combustion products in solid fuels and gases are very different. If using natural gas, it is preferable to increase the area of the heat exchanger and lengthen the path of the flame to absorb heat as efficiently as possible, then in the case of firewood and coal, the situation is somewhat different. The combustion temperature of solid fuel is slightly lower, while the flame length is higher. The power cannot be regulated flexibly, so the heat exchanger is designed with increased reliability instead of energy efficiency. In addition, there is no way to avoid the formation of condensate and soot in large quantities, which greatly and rapidly reduce the rate of heat transfer.
The presence of separate combustion chambers leads to an increase in the cost of equipment of about 30% in comparison with single-top designs. However, this design allows not only to increase the efficiency of combustion, but also makes possible the simultaneous operation of two furnaces. If the operation of a single-chamber bifuel boiler on coal or firewood gas burner is required to remove to exclude its contamination and damage, then in two-step varieties, the inclusion of the gas chamber in the work can occur even without the participation of the operator.
Operating modesThe presence of an electric heater for hybrid boilers is optional. Such an additional heating source is not intended to smooth out interruptions in the supply of fuel or reduce the cost of the thermal power produced. However, TENs are very ergonomic in terms of temperature control, and therefore can be used to accurately heat the coolant without a complex scheme of automation, controlled valves and supercharging.
In most cases, it is important for the consumer to level the disadvantages associated with low gas pressure and its high cost. The main heating occurs due to the combustion of solid fuel, while the gas burner is included in the work only to reach the set temperature. This can be required both because of the low energy intensity of wood, and at times when the next fuel laying is exhausted.
You should know that the most effective scheme of operation is when water from the “reverse” enters the combustion chamber first. There, it is heated exactly to the extent that after passing through a solid fuel furnace, it acquires a precisely specified temperature value. At the same time, the most complete absorption of heat from the most expensive type of fuel occurs. At the same time, the water enters the heat exchanger of the solid fuel chamber already heated, which makes the formation of tar and soda not so intense.
The inclusion of TENs in the work occurs on a slightly different principle. Naturally, if necessary, electric heaters can play the same role as a gas burner. Usually, however, electricity is just a safety net for solid fuel boilers: electric heaters only keep the coolant temperature above freezing point if all the fuel is used up.
Security requirementsDue to the difficulties in organizing the joint work of furnaces, many boilers do not meet safety requirements. This mainly applies to single-storage gas-fired bifuel boilers, for which there are two risk factors.
One of them is the need to manually remove gas equipment. Without proper qualification, the risk of error is very high, and the consequences of sloppy handling of natural gas are well known. Due to the risk of freezing the coolant, reconnection of equipment should be carried out as quickly as possible, but there are no sensible specialists in boiler equipment for a couple of hours.
The second danger lies in the need for periodic changes in the air supply scheme, which differs for different types of fuel. Failures in supercharging can lead to the formation of carbon monoxide in the case of solid fuel or incomplete combustion of natural gas.
To eliminate the dangers of this kind can only be one way - the installation of protective automation. These are primarily household gas analyzers with control of the concentration of carbon monoxide and carbon monoxide, as well as methane, connected to the cut-off valve. Additionally, it is recommended to install a thrust stabilizer on the chimney, it will also not be superfluous to install a fire alarm in the boiler room.
Differences in bindingThe hydraulic binding of boiler equipment and the scheme of wiring of the heating system depends on the type and organization of the heating circuits. The simplest connection scheme is characterized by radiator heating systems with a closed expansion tank. It is mandatory to install a circulation pump and a safety group at the output of the heat exchanger of the solid fuel chamber.
When working a hybrid boiler for heating the warm floor, the risk of water supply of too high temperature should be excluded. The two easiest ways to ensure the correct mode of operation for circuits with a single distribution manifold is to include a three-way valve in the feeding tube that regulates the outflow of excess hot water into the “reverse”.
For systems with several collector nodes of the warm floor, it is recommended to install individual modules of the mix. Built-in forced circulation devices provide the necessary duct with the ability to adjust, while all loops and collector groups operate independently of each other and included in the radiator system.
Preparation of HVS in bifuel boilers can be carried out both in the coil and in the internal boiler. In the latter case, the water supply has a reserve of hot water of the order of 30-40 liters, the heating of which is performed indirectly from the coolant of the heating system, that is, absolutely safe. When organizing the second circuit on a coil of direct heating, the risk of boiling liquid is high, especially when working on solid fuel. It is recommended to install a storage capacity of about 4-5 liters over the boiler for each kilowatt of boiler power with the calculation of the gravitational exchange of fluid between the storage device and the heat exchanger. It is also possible to organize circulation in the water supply system with a sufficiently high length of pipes.
Features of installationBoilers on combined fuel belong to the class of massive and overall heating devices. The mass of boilers for heating residential buildings with an area of 250-300 m2 can reach 500-700 kg. Because of this, a reinforced pedestal is required from reinforced concrete and the lining with refractory materials of walls located closer to one meter to the boiler body.
There are also difficulties with the organization of the chimney. Hybrid boilers, including those with separate furnaces, have a general withdrawal of combustion products with rather strict requirements for the speed of natural traction in the chimney. Guaranteed to avoid problems with the formation of carbon monoxide can be due to the installation of flue fans, or compliance with all requirements for the device vertical segment of the chimney. This mainly concerns a sufficient height of removal (about 2-2.5 meters) above the roof skates of nearby buildings, compliance with the required throughput and the use of composite insulated pipes.
Separately regulated rules of ventilation of the boiler house. Bifuel boilers are installed only in non-residential premises, mainly attached boiler houses without insulation of the enclosing structures. The equipment of leading European manufacturers can be designed for full localization from the internal environment with admission to installation in unattached premises without its own inflow of general ventilation. In this case, air intake is carried out from the street, which has a good effect on energy savings. published
P.S. And remember, just changing our consumption – together we change the world!
Source: //www.rmnt.ru/story/heating/1322042.htm
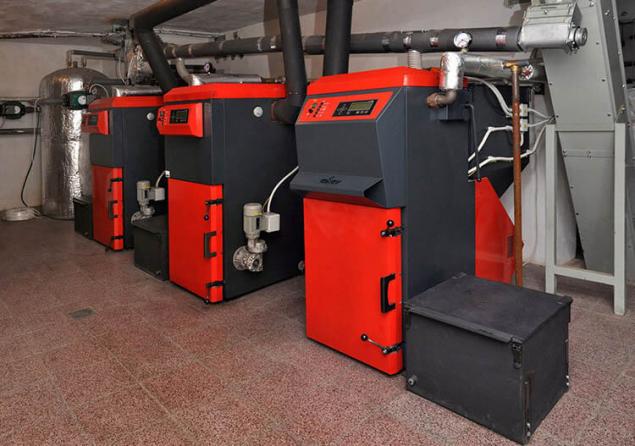
The two main types of hybrid boilers
Manufacturers periodically expand the range of technical means designed to increase the efficiency of heating equipment. However, the main schemes of the device for working on combined fuel are only two:
- boilers with a combined combustion chamber;
- boilers with separate combustion chambers.
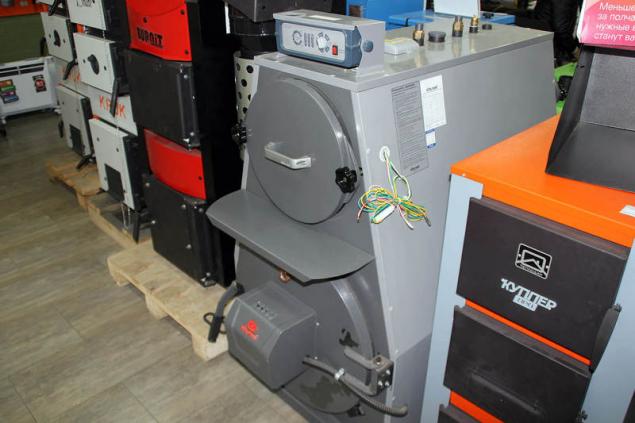
The difference between boilers with combined and separate furnaces is obvious. On the one hand, the production of single-chamber units implies a lower material intensity, respectively, the weight and dimensions in the end are relatively low. The other side of the coin is negative – it is very difficult to achieve the same high efficiency of burning different types of fuel, in this matter, unification is not beneficial.
The problem is that the heat and composition of combustion products in solid fuels and gases are very different. If using natural gas, it is preferable to increase the area of the heat exchanger and lengthen the path of the flame to absorb heat as efficiently as possible, then in the case of firewood and coal, the situation is somewhat different. The combustion temperature of solid fuel is slightly lower, while the flame length is higher. The power cannot be regulated flexibly, so the heat exchanger is designed with increased reliability instead of energy efficiency. In addition, there is no way to avoid the formation of condensate and soot in large quantities, which greatly and rapidly reduce the rate of heat transfer.
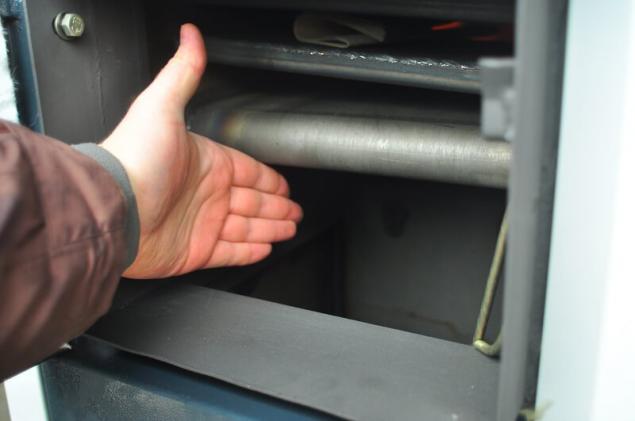
The presence of separate combustion chambers leads to an increase in the cost of equipment of about 30% in comparison with single-top designs. However, this design allows not only to increase the efficiency of combustion, but also makes possible the simultaneous operation of two furnaces. If the operation of a single-chamber bifuel boiler on coal or firewood gas burner is required to remove to exclude its contamination and damage, then in two-step varieties, the inclusion of the gas chamber in the work can occur even without the participation of the operator.
Operating modesThe presence of an electric heater for hybrid boilers is optional. Such an additional heating source is not intended to smooth out interruptions in the supply of fuel or reduce the cost of the thermal power produced. However, TENs are very ergonomic in terms of temperature control, and therefore can be used to accurately heat the coolant without a complex scheme of automation, controlled valves and supercharging.
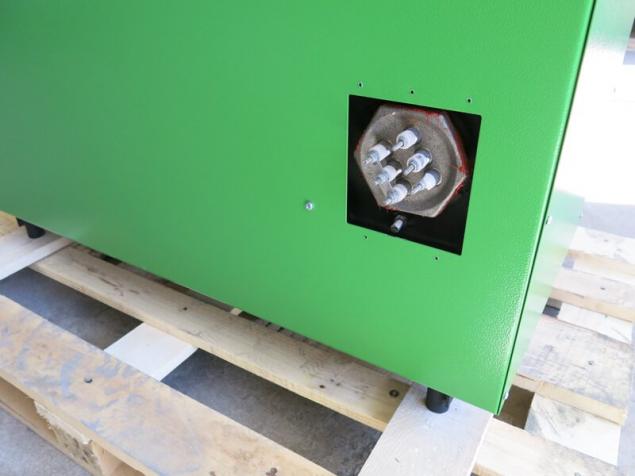
In most cases, it is important for the consumer to level the disadvantages associated with low gas pressure and its high cost. The main heating occurs due to the combustion of solid fuel, while the gas burner is included in the work only to reach the set temperature. This can be required both because of the low energy intensity of wood, and at times when the next fuel laying is exhausted.
You should know that the most effective scheme of operation is when water from the “reverse” enters the combustion chamber first. There, it is heated exactly to the extent that after passing through a solid fuel furnace, it acquires a precisely specified temperature value. At the same time, the most complete absorption of heat from the most expensive type of fuel occurs. At the same time, the water enters the heat exchanger of the solid fuel chamber already heated, which makes the formation of tar and soda not so intense.
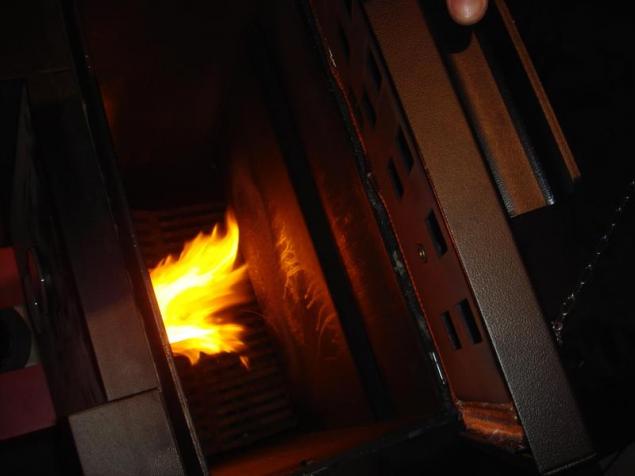
The inclusion of TENs in the work occurs on a slightly different principle. Naturally, if necessary, electric heaters can play the same role as a gas burner. Usually, however, electricity is just a safety net for solid fuel boilers: electric heaters only keep the coolant temperature above freezing point if all the fuel is used up.
Security requirementsDue to the difficulties in organizing the joint work of furnaces, many boilers do not meet safety requirements. This mainly applies to single-storage gas-fired bifuel boilers, for which there are two risk factors.
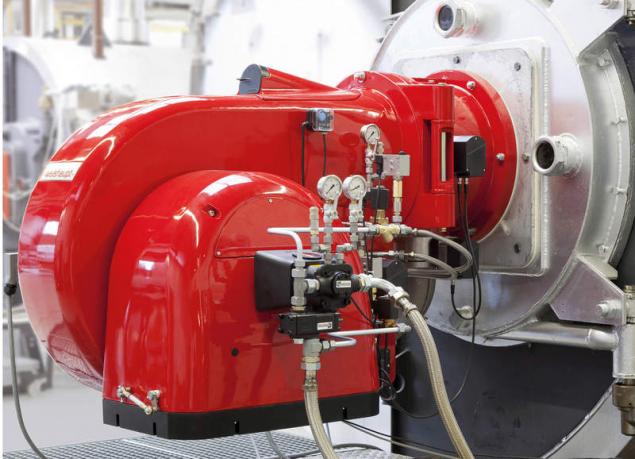
One of them is the need to manually remove gas equipment. Without proper qualification, the risk of error is very high, and the consequences of sloppy handling of natural gas are well known. Due to the risk of freezing the coolant, reconnection of equipment should be carried out as quickly as possible, but there are no sensible specialists in boiler equipment for a couple of hours.
The second danger lies in the need for periodic changes in the air supply scheme, which differs for different types of fuel. Failures in supercharging can lead to the formation of carbon monoxide in the case of solid fuel or incomplete combustion of natural gas.
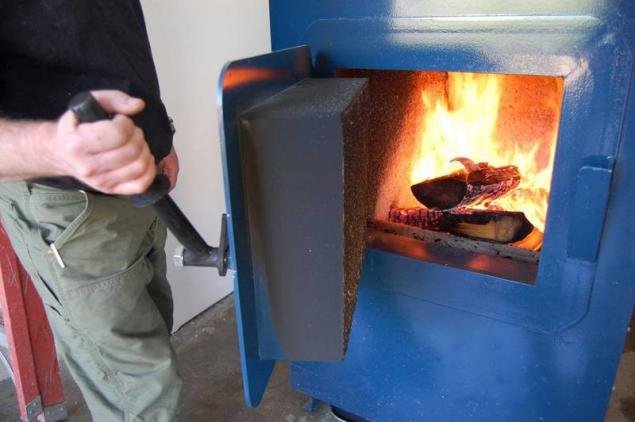
To eliminate the dangers of this kind can only be one way - the installation of protective automation. These are primarily household gas analyzers with control of the concentration of carbon monoxide and carbon monoxide, as well as methane, connected to the cut-off valve. Additionally, it is recommended to install a thrust stabilizer on the chimney, it will also not be superfluous to install a fire alarm in the boiler room.
Differences in bindingThe hydraulic binding of boiler equipment and the scheme of wiring of the heating system depends on the type and organization of the heating circuits. The simplest connection scheme is characterized by radiator heating systems with a closed expansion tank. It is mandatory to install a circulation pump and a safety group at the output of the heat exchanger of the solid fuel chamber.
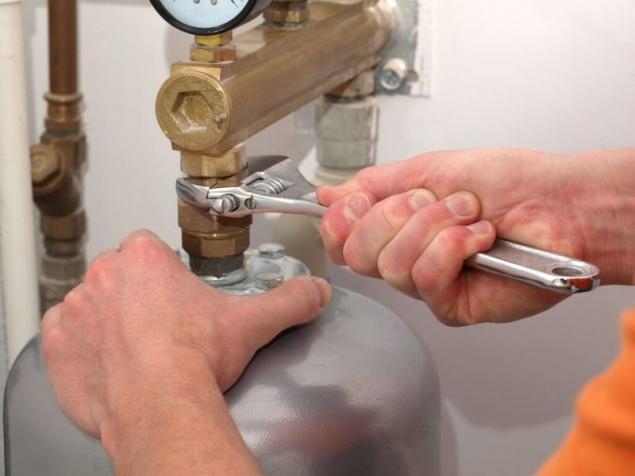
When working a hybrid boiler for heating the warm floor, the risk of water supply of too high temperature should be excluded. The two easiest ways to ensure the correct mode of operation for circuits with a single distribution manifold is to include a three-way valve in the feeding tube that regulates the outflow of excess hot water into the “reverse”.
For systems with several collector nodes of the warm floor, it is recommended to install individual modules of the mix. Built-in forced circulation devices provide the necessary duct with the ability to adjust, while all loops and collector groups operate independently of each other and included in the radiator system.
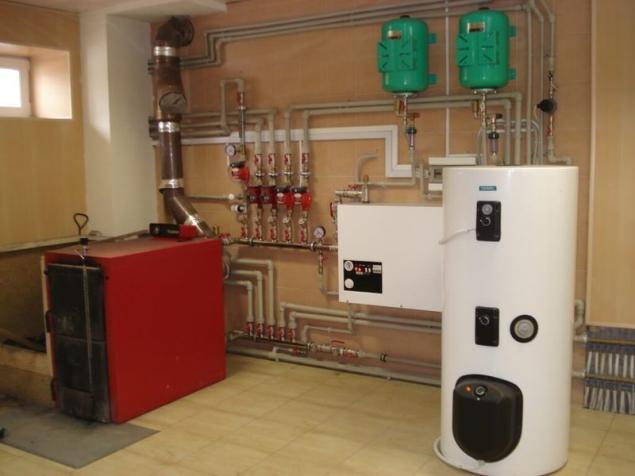
Preparation of HVS in bifuel boilers can be carried out both in the coil and in the internal boiler. In the latter case, the water supply has a reserve of hot water of the order of 30-40 liters, the heating of which is performed indirectly from the coolant of the heating system, that is, absolutely safe. When organizing the second circuit on a coil of direct heating, the risk of boiling liquid is high, especially when working on solid fuel. It is recommended to install a storage capacity of about 4-5 liters over the boiler for each kilowatt of boiler power with the calculation of the gravitational exchange of fluid between the storage device and the heat exchanger. It is also possible to organize circulation in the water supply system with a sufficiently high length of pipes.
Features of installationBoilers on combined fuel belong to the class of massive and overall heating devices. The mass of boilers for heating residential buildings with an area of 250-300 m2 can reach 500-700 kg. Because of this, a reinforced pedestal is required from reinforced concrete and the lining with refractory materials of walls located closer to one meter to the boiler body.
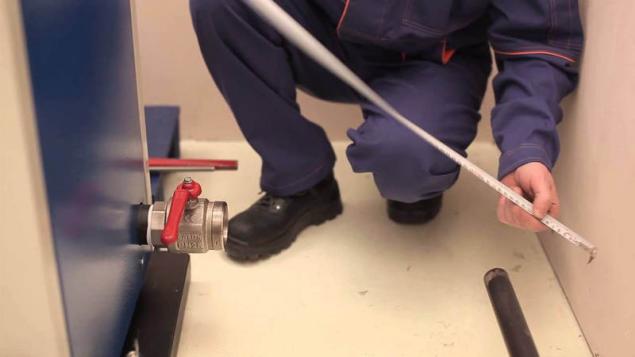
There are also difficulties with the organization of the chimney. Hybrid boilers, including those with separate furnaces, have a general withdrawal of combustion products with rather strict requirements for the speed of natural traction in the chimney. Guaranteed to avoid problems with the formation of carbon monoxide can be due to the installation of flue fans, or compliance with all requirements for the device vertical segment of the chimney. This mainly concerns a sufficient height of removal (about 2-2.5 meters) above the roof skates of nearby buildings, compliance with the required throughput and the use of composite insulated pipes.
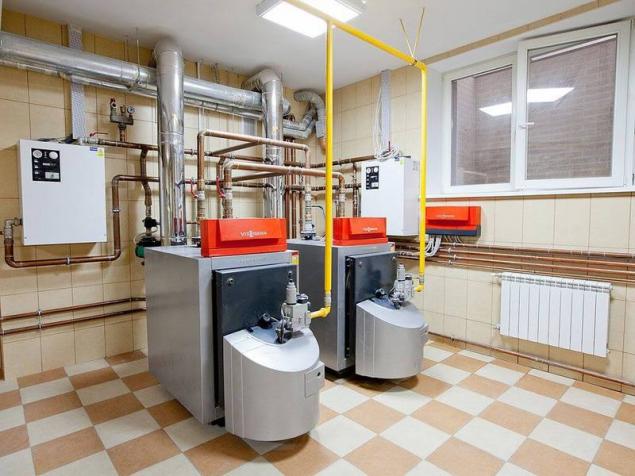
Separately regulated rules of ventilation of the boiler house. Bifuel boilers are installed only in non-residential premises, mainly attached boiler houses without insulation of the enclosing structures. The equipment of leading European manufacturers can be designed for full localization from the internal environment with admission to installation in unattached premises without its own inflow of general ventilation. In this case, air intake is carried out from the street, which has a good effect on energy savings. published
P.S. And remember, just changing our consumption – together we change the world!
Source: //www.rmnt.ru/story/heating/1322042.htm