413
Coal from beer
The company "Alaskan Brewing Company" decided to reduce the cost of energy and installed at its plant a special oven that can burn the spent grains (the sediment remaining after boiling and extraction of the barley mash). The beer producer has not withheld $ 1.8 million for the acquisition, which allows to meet all the needs of the brewery's electricity.
Alaska has a rich history of brewing. Its origins reach back to the days of the gold rush, when the adventurers "were inspired by" the first beer of local production. Soon, however, the alcohol became excessively popular: the average American per day drink about five pints of hard liquor – instead of "colonial" tea and coffee. And in the beginning of the last century in connection with military sentiments, the authorities decided to save the grain, so supporters of a healthy lifestyle finally succeeded: until 1919 had introduced the "dry law".
Only in 1966 in the United States was fully repealed the ban on beer, whiskey and other "spirits" production. However, years of illicit trade have not been in vain: the lost experience has led to the mediocre quality of the drinks. However, in 1986 a young couple Marcy and Geoff Larson (Marcy and Geoff Larson) found in the archives of the ancient recipes of local brewers and decided to revive these traditions.
It was not too difficult: Jeff is an engineer-chemist and brewer fan, and his wife studied to be an accountant and could not imagine life without excitement and adventure. They combined their skills to open a brewery in the capital of Alaska — Juneau (Juneau). And it has paid off: today is "Alaskan Brewing" produces about 150 000 barrels of beer a year, which are sold in 14 States.
Accumulated wastes in the brewing process, usually go to feed the animals and even added to bread with bran, as in one hundred pounds of dry beer pellet contains approximately 17 pounds of digestible protein. Before "Alaskan Brewing" send spent grains to farmers, although this was a serious problem: in Southeast Alaska there are only 37 agricultural sites, and the brewers are periodically faced with a surplus of grains.
This problem has become more urgent after the in 1995 the brewery was extended. Recyclables had to be sent to buyers from more distant regions, and spend a lot of money on transport of waste because the city does not lead to major highways. In addition, brewer's grain contains a lot of liquid, so before sending, it must be dry, spending extra energy and time. Thus, the net profit from sales was small: for every ton the company has gained $ 60, and of transporting spent $ 30.
So four years ago the management of "Alaskan Brewing" beginning to explore opportunities to use grains on your own object, turning it into a renewable source of energy to reduce costs. After the project has received almost $ 500,000 in the form of subsidies from the Federal rural energy USA, chief engineer Brandon Smith has signed a contract with the company "North Dakota" to create a special recuperative steam boilers.
In the end, "Alaskan Brewing Company"was able to achieve use of spent grain as supplemental fuel: so the recycling became the only source of energy for the brewery. "Beer makes the beer" - joke representatives of the company. But experts believe that the use of the new boiler will reduce the annual expenses of the company for payment of electricity and heat at 70%, which is about $ 450 000 per year.
Source: /users/104
Alaska has a rich history of brewing. Its origins reach back to the days of the gold rush, when the adventurers "were inspired by" the first beer of local production. Soon, however, the alcohol became excessively popular: the average American per day drink about five pints of hard liquor – instead of "colonial" tea and coffee. And in the beginning of the last century in connection with military sentiments, the authorities decided to save the grain, so supporters of a healthy lifestyle finally succeeded: until 1919 had introduced the "dry law".
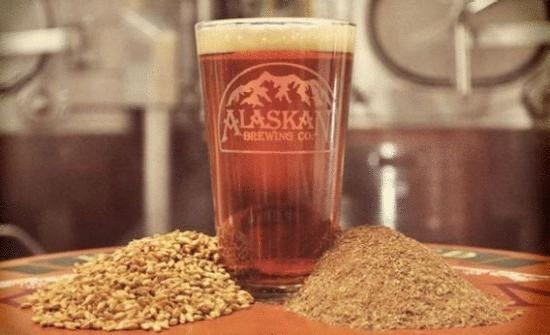
Only in 1966 in the United States was fully repealed the ban on beer, whiskey and other "spirits" production. However, years of illicit trade have not been in vain: the lost experience has led to the mediocre quality of the drinks. However, in 1986 a young couple Marcy and Geoff Larson (Marcy and Geoff Larson) found in the archives of the ancient recipes of local brewers and decided to revive these traditions.
It was not too difficult: Jeff is an engineer-chemist and brewer fan, and his wife studied to be an accountant and could not imagine life without excitement and adventure. They combined their skills to open a brewery in the capital of Alaska — Juneau (Juneau). And it has paid off: today is "Alaskan Brewing" produces about 150 000 barrels of beer a year, which are sold in 14 States.
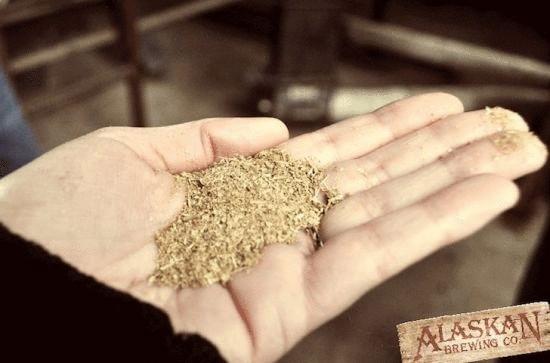
Accumulated wastes in the brewing process, usually go to feed the animals and even added to bread with bran, as in one hundred pounds of dry beer pellet contains approximately 17 pounds of digestible protein. Before "Alaskan Brewing" send spent grains to farmers, although this was a serious problem: in Southeast Alaska there are only 37 agricultural sites, and the brewers are periodically faced with a surplus of grains.
This problem has become more urgent after the in 1995 the brewery was extended. Recyclables had to be sent to buyers from more distant regions, and spend a lot of money on transport of waste because the city does not lead to major highways. In addition, brewer's grain contains a lot of liquid, so before sending, it must be dry, spending extra energy and time. Thus, the net profit from sales was small: for every ton the company has gained $ 60, and of transporting spent $ 30.
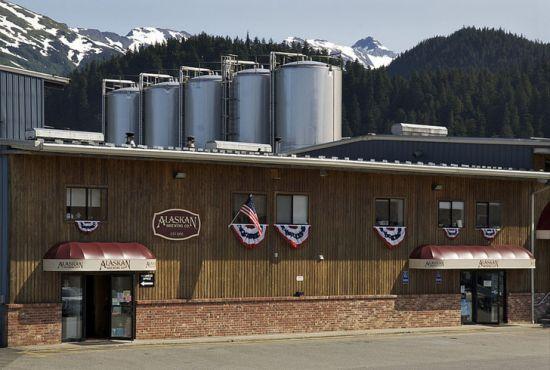
So four years ago the management of "Alaskan Brewing" beginning to explore opportunities to use grains on your own object, turning it into a renewable source of energy to reduce costs. After the project has received almost $ 500,000 in the form of subsidies from the Federal rural energy USA, chief engineer Brandon Smith has signed a contract with the company "North Dakota" to create a special recuperative steam boilers.
In the end, "Alaskan Brewing Company"was able to achieve use of spent grain as supplemental fuel: so the recycling became the only source of energy for the brewery. "Beer makes the beer" - joke representatives of the company. But experts believe that the use of the new boiler will reduce the annual expenses of the company for payment of electricity and heat at 70%, which is about $ 450 000 per year.
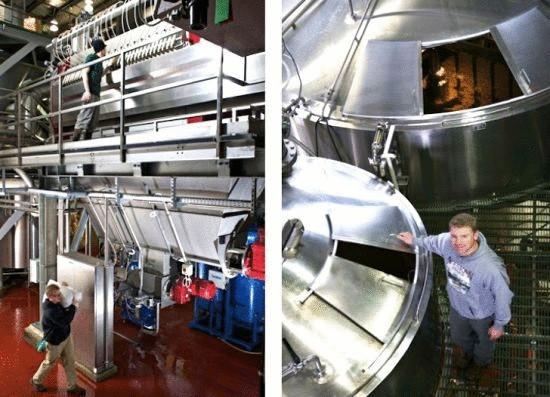
Source: /users/104