513
Robotic agriculture

If you think about global population growth and the need to feed him, then surely farmers must become more efficient in cleaning and production of all crops. In the future robots will be used for most tasks, from seeding and fertilizing.
Seasonal workers on farms — a relic of the past, now the robots will perform their functions — to harvest, to combat insects and weeds.
The farm also drones are used for early identification of fungal diseases, allowing earlier and more successful treatment. The camera equipped drone with GPS will take images of crops with high resolution, providing farmers with a bird's eye that allows us to consider where the culture is healthy, and where in need of care.
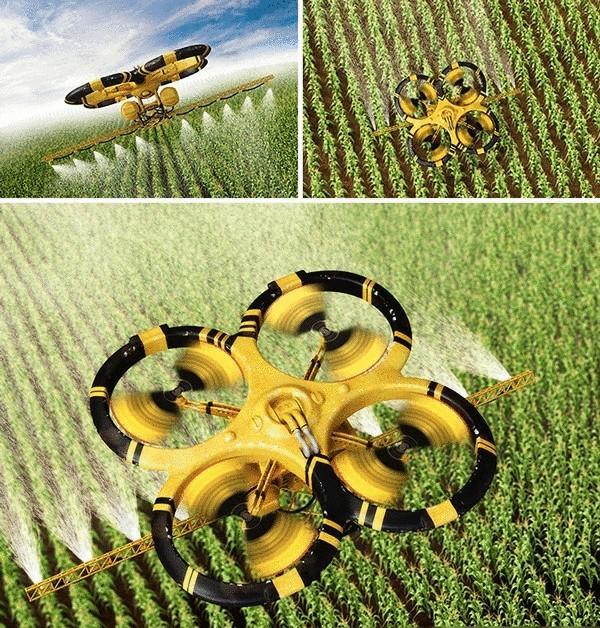
Sometimes during harvest not enough workers. Robots can offer us timely delivery of work at the right time, especially for farms located away from populated areas.
There is no problem with seasonal workers who are hired for harvesting (e.g., strawberries), because such work is very exhausting. During harvest, time is critical, as some crops should be removed quickly. Thus, we need a lot of workers for quite a short period of time that poses a real challenge to maintain employment on a permanent basis.
Commercial farmers have long been trying to develop robots for agricultural labor. In recent years, researchers teach robots to see. If successful, robots will be able to work in the field.
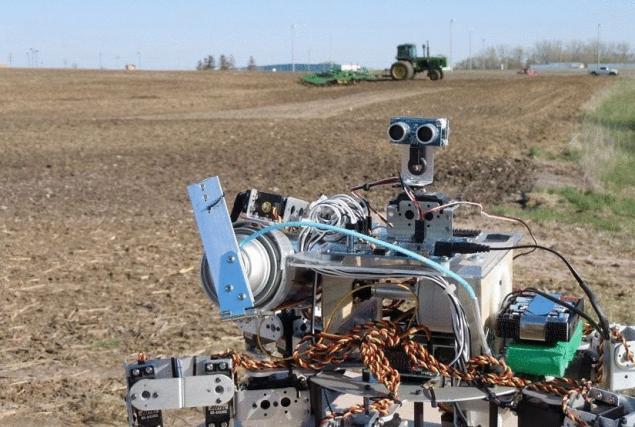
Modern farms already use tractors with automatic steering and dairy farms installed machines that can milk cows. However, the definition of individual fruits or vegetables is much more challenging.
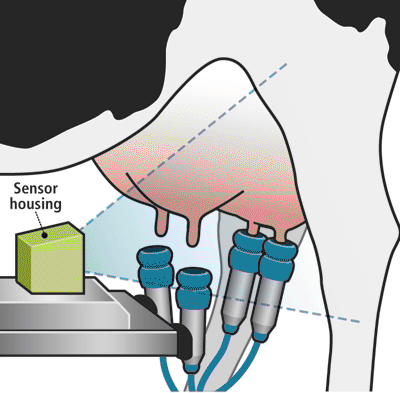
Robotic milking machines are taking on a certain amount of labor of farmers (e.g., feeding and milking cows without human intervention), saving time and labor. Cows decide when they can be milked, and each of them receives personalized service through the clamp with transmitters that show the amount of milk. The transmitter can track the amount of consumed grass by the cow and even then, how many steps she did.
There are no two identical products — each has a unique shape, size and color. Lighting, changing throughout the day and night, contributes to the fact that each fruit or vegetable looks in different conditions in different ways. A green vegetables look like leafy bushes or vines on which they grow.
An example of this problem is cleaning the green beans, because it must be collected young, before the seeds inside of the pod will form lumps. The more you collect, the more it will bear fruit, so the beans need to pluck every 2-3 days. If you leave it to ripen, the vine will not bear any fruit and will shrink.
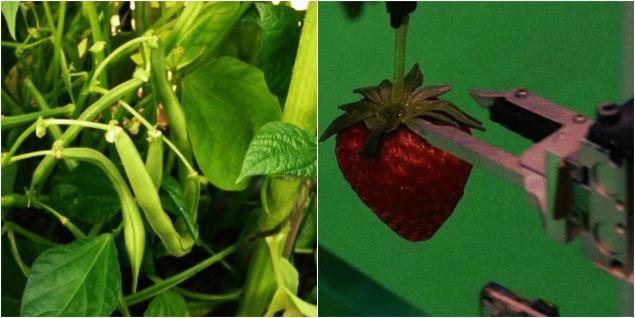
In order to understand the organization within the virtual clutter agricultural environment, researchers working on intelligent sensing systems. Multi-spectral cameras that analyze wavelengths of light reflected from objects can be used to find patterns that will enable the robot to understand what he sees, for example, pepper, regardless of how a vegetable grows.
The robot can then learn from their mistakes and improve during the work. The algorithm will see simple forms, and if a vegetable is partially covered with leaves, will not use the algorithm's full form.
After the robot identificeret the harvest, he would collect it. Thus, there is a need for grasping the tool which will be able to capture products in the right place and pluck her from applying the correct strength and hardness. Researchers are studying the movement of the human hand and using the other set of algorithms trying to repeat it.
Robot to care for lettuce able to weed beds of weeds around the base of the plant. It can also thin out the beds, while to perform the procedure manually it takes about 20 workers.
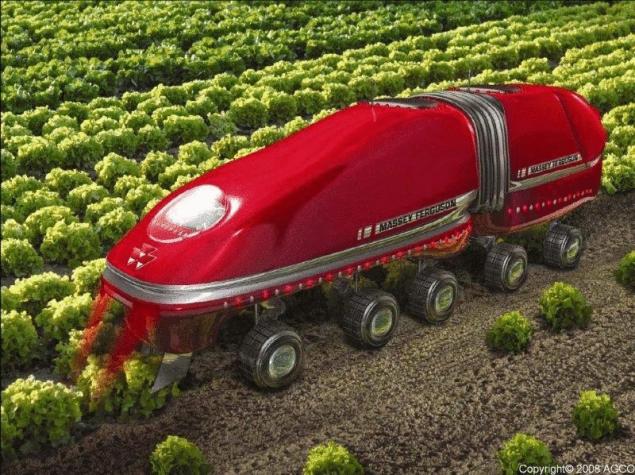
Robot to care for the grapes rolling through the vineyards, trimming the vines, while the other robots that are now under development, will remotely check crops for growth, moisture and signs of disease.
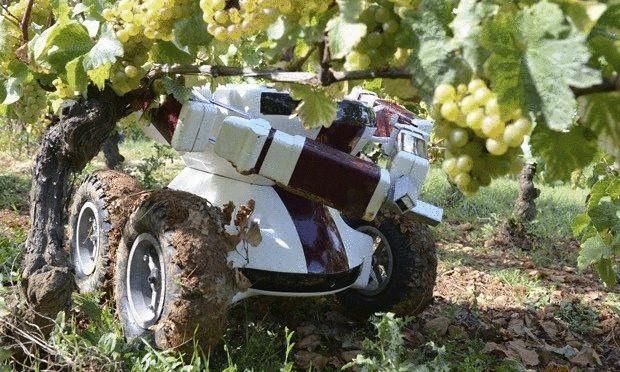
In France there is a new employee of the vineyard with four wheels, two arms and six cameras, prunes 600 vines a day and never out sick. Wall-Ye V. I. N., which is the brainchild of Burgundian inventor Christophe Millot, is one of robots, designed to perform the work in the vineyards.
It performs tasks such as pruning and remove side shoots (removing unproductive young shoots), but also collects important data about the condition and vitality of the soil, fruit and vine.
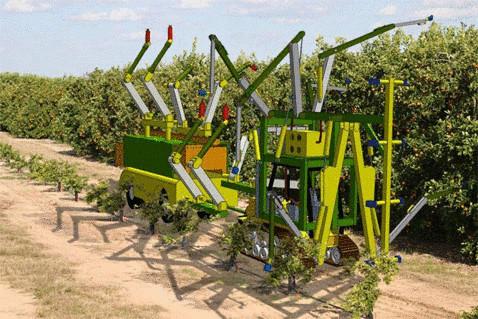
Vision Robotics, a company from San Diego, is working on two robots that will travel through the orchards and pick oranges, apples or other fruits from trees. In a few years these machines will be able to perform time-consuming routine work of picking fruit, for which currently recruited thousands of labor migrants each season.
Two robots will work together as a team. The first will scan the tree and create a 3D-map the location and size of each orange, calculating the best order in which to break the fruit. The second is something like a metal octopus, able to gently touch the fruit. The first robot will be able to scan and send the information to the second processor, to pluck the fruit, and the planned sequence of movements will not give long eight hands running into each other.
In order to feed billions of people around the world, farmers have to use robots. The population growth in America alone is staggering, as it grew by 22.5 percent between 1990 (250 million people) and 2010 (310 million), and the census Bureau expects that by 2050 the numbers will increase to more than 420 million.
If you think about the problem of global population growth and the need to feed this mounting population, farmers must become more efficient in cleaning and production of all crops. In the future robots will be used for most tasks, from seeding to fertilizing and application of chemicals. Process all manually is no longer required. published
Source: www.robo-hunter.com/news/robotizirovannoe-selskoe-hozyaistvo-budushego