1159
How do Superjet
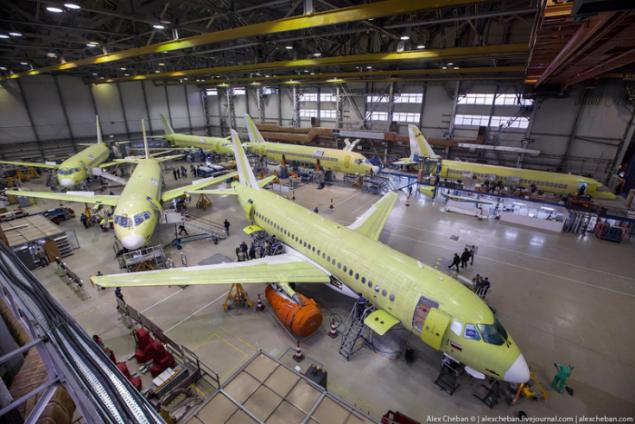
Alexander Cheban writes: "The plane - it's not a car, it is very difficult, we can say," piece "product collected by hand. This is where the hidden fact many doubts and mistrust ordinary escorting.
I think my readers already flew Superjet, well, many flights in one of the six Superjet "UTair" later this year. Today, I suggest you look at the production of this beautiful aircraft. I showed factories "Airbus" in Hamburg and Toulouse plants "Boeing" in Everett and Renton, of course, I was very interested to see how the plane is collected in Russia. Complicated process, where no one has the right to make mistakes, where the multiple control at each stage of assembly. In 2013, collected 25 aircraft, and this year will be collected 40 Superjet! At present, the production cycle is 10 days, in terms of its reduction to seven! »
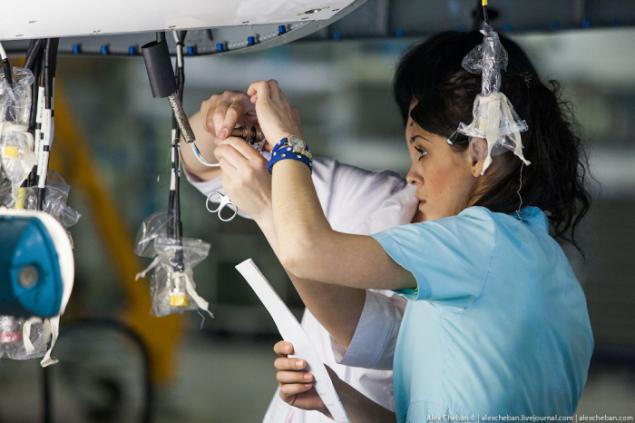
I'll start the story of the production Superjet with a photo essay from the plant in Komsomolsk-on-Amur. Although, of course, it all begins much earlier ...
Production of the aircraft - its final assembly - provides Komsomolsk-on-Amur branch of JSC "Sukhoi Civil Aircraft" (Kanafeh) with the direct participation of other plants in Russia, where the components are made Sukhoi Superjet 100. The finished parts are transmitted in Komsomolsk-on-Amur branch CJSC "Sukhoi Civil Aircraft", where the final assembly of the aircraft.
Manufacture of parts and assembly aggregate sections performed in Novosibirsk, parts of plastics produced in Voronezh. But the first of the major locations where you can see the plane from flying to the assembled fuselage side - it Komsomolsk-on-Amur.
As in "Boeing" or "Airbus", the assembly is carried out according to certain production sites.
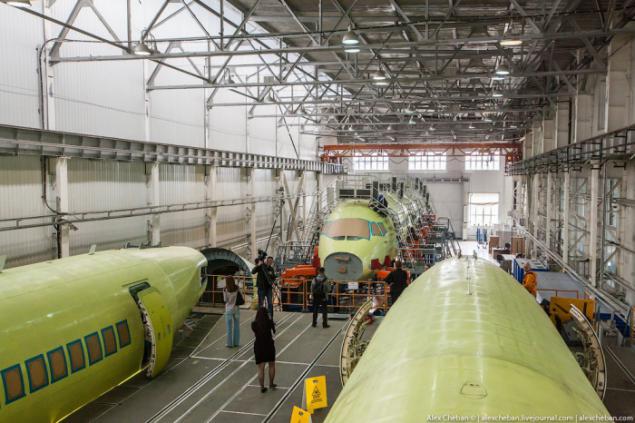
Here is the assembly shop of the fuselage.
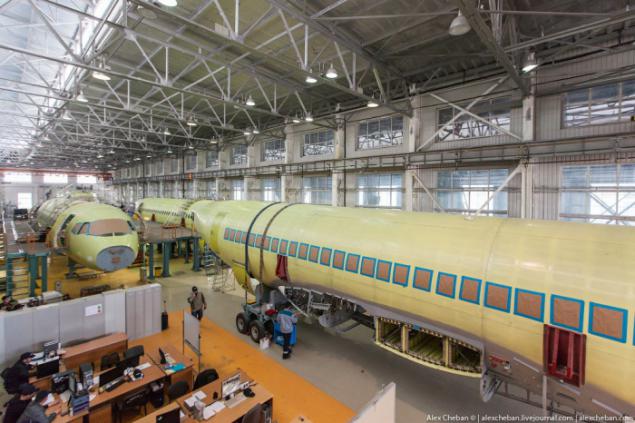
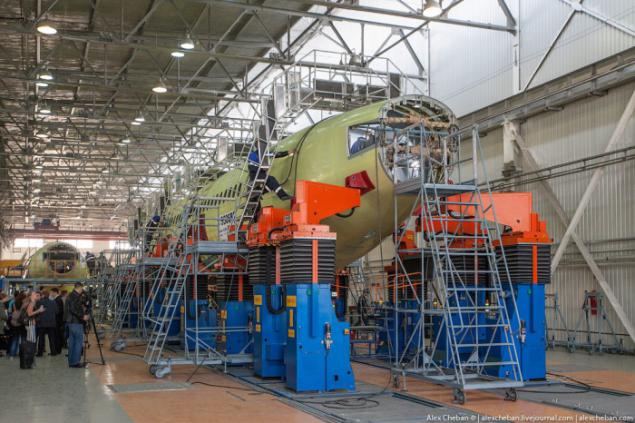
It produces docking bays fuselage mounting racks for radio and electrical equipment.
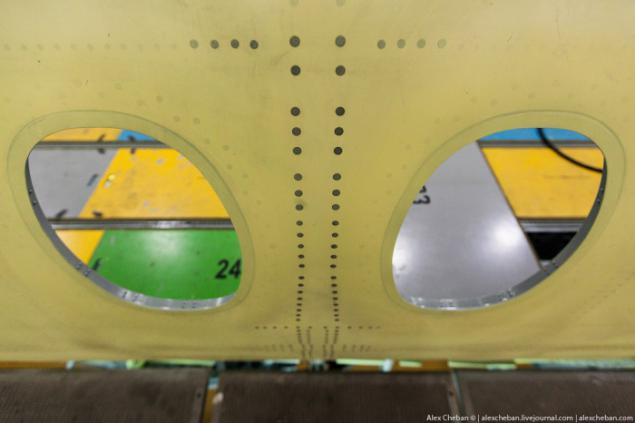
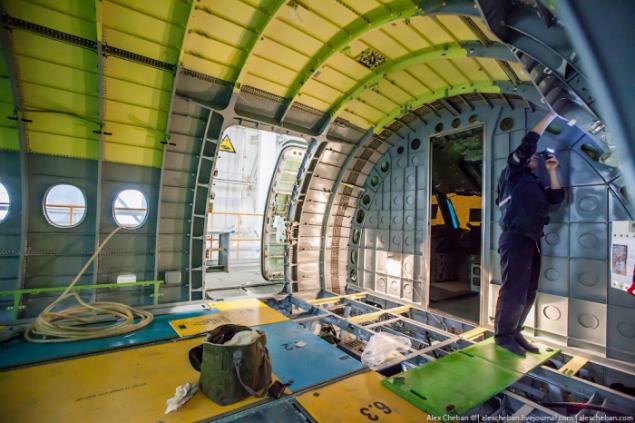
Also, installation floor, storage compartments, doors. Very interesting to see the "evolution" of the aircraft, moving from station to station.
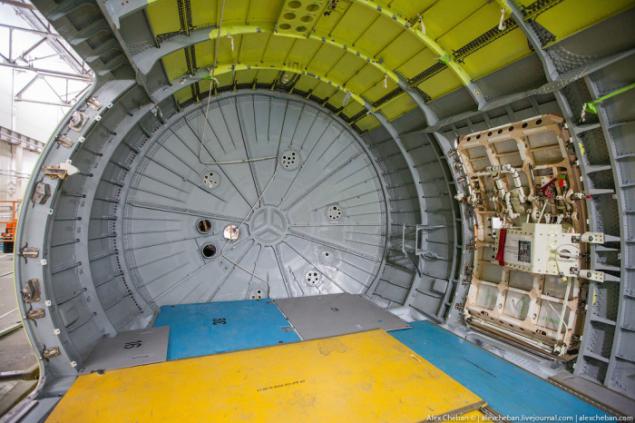
Notice how many items have regular passenger door! Although, of course, it's not normal.
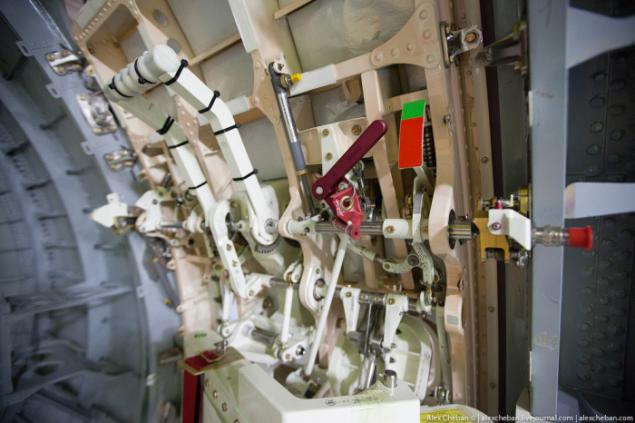
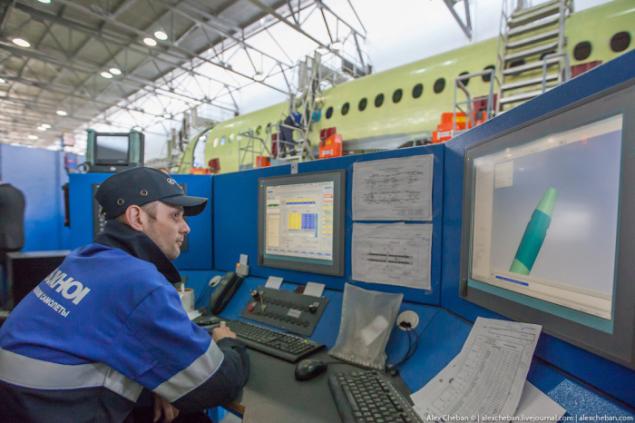
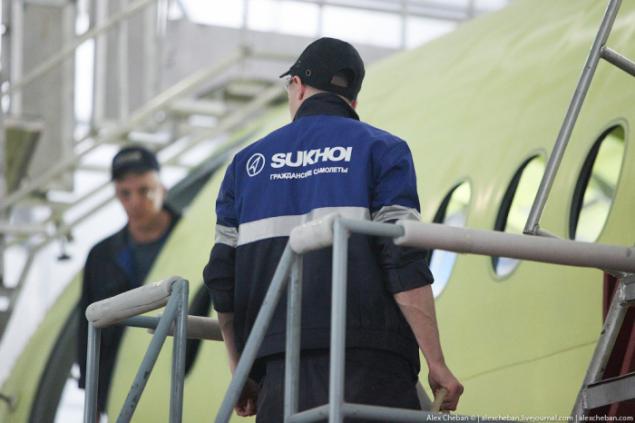
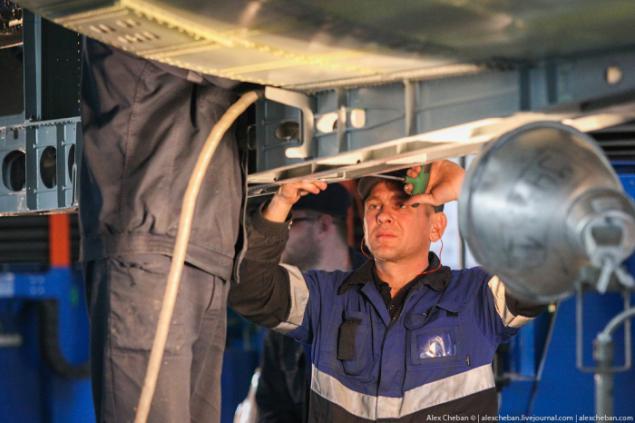
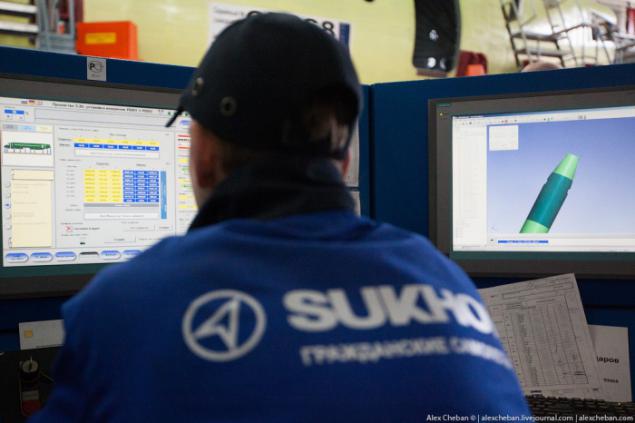
In the assembly shop of the fuselage is made thermal insulation preparation and installation brackets for electrical equipment. Here in this example is very clearly seen "birth" of the cabin.
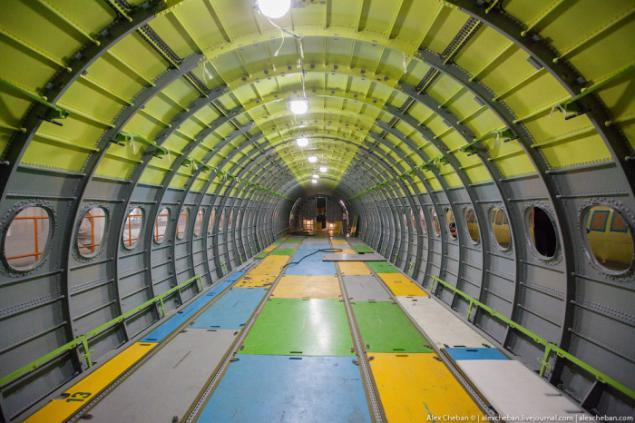
Clean interior and floor installation.
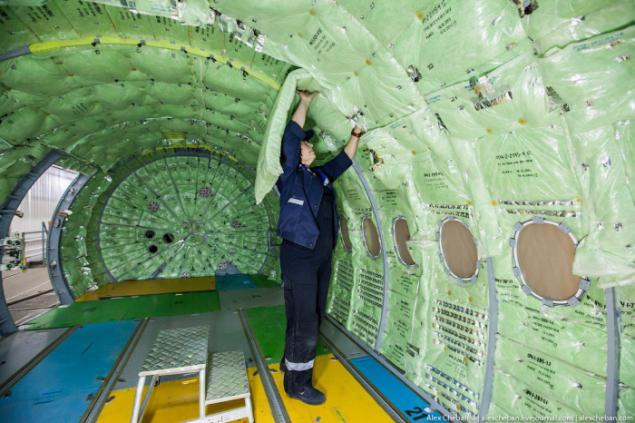
Thermal insulation preparation.
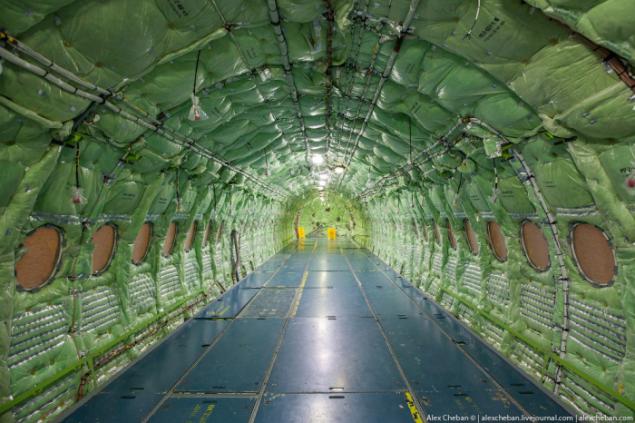
Here I'm getting a little ahead, electric already in place. This frame is made in the final assembly shop.
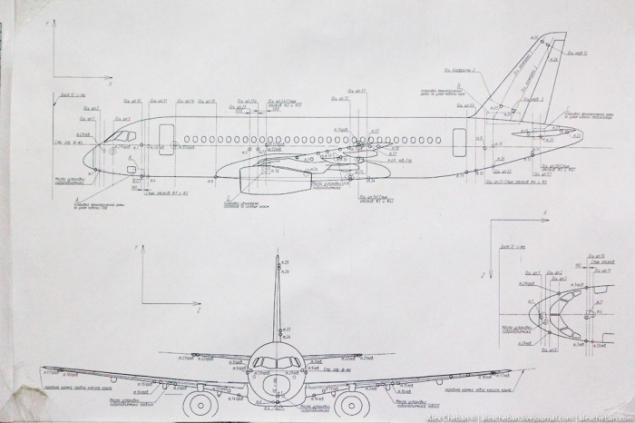
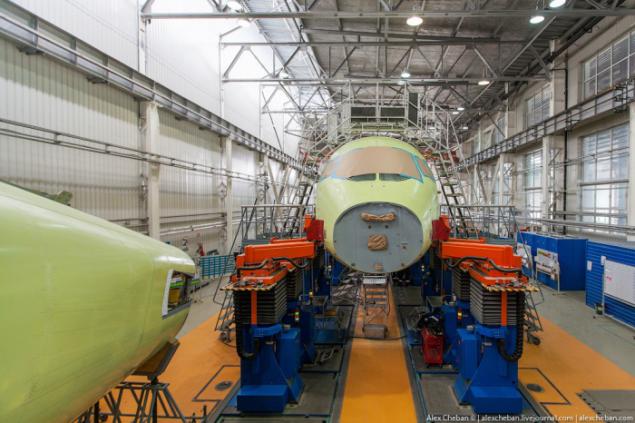
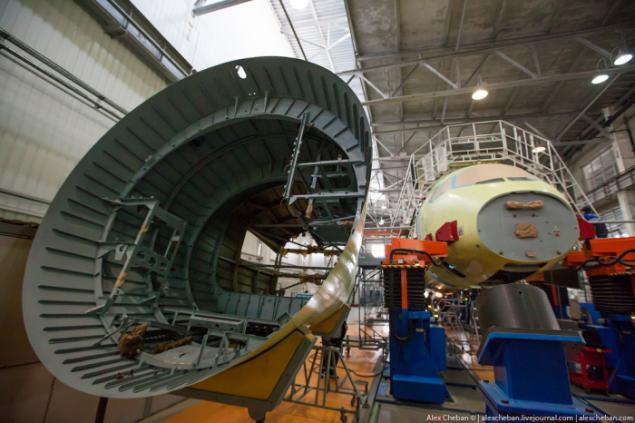
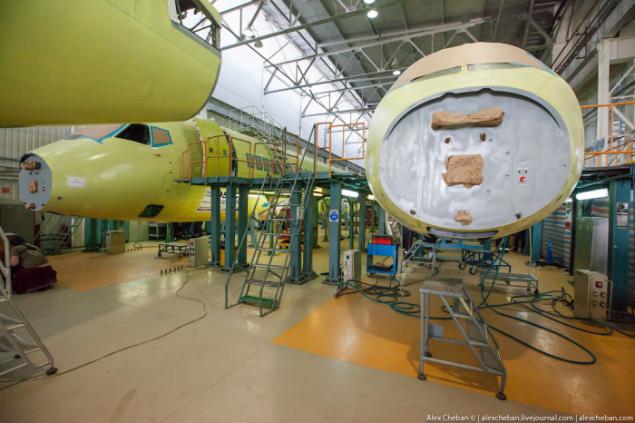
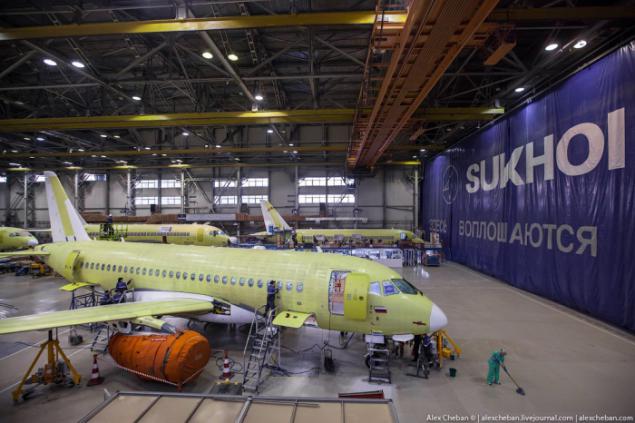
Next we move to a neighboring shop, which is the final assembly shop. Here, the plane moves in seven sections, where transferred to the flight test station.
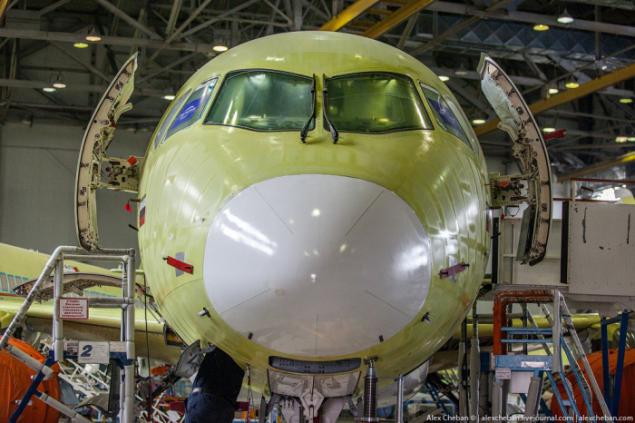
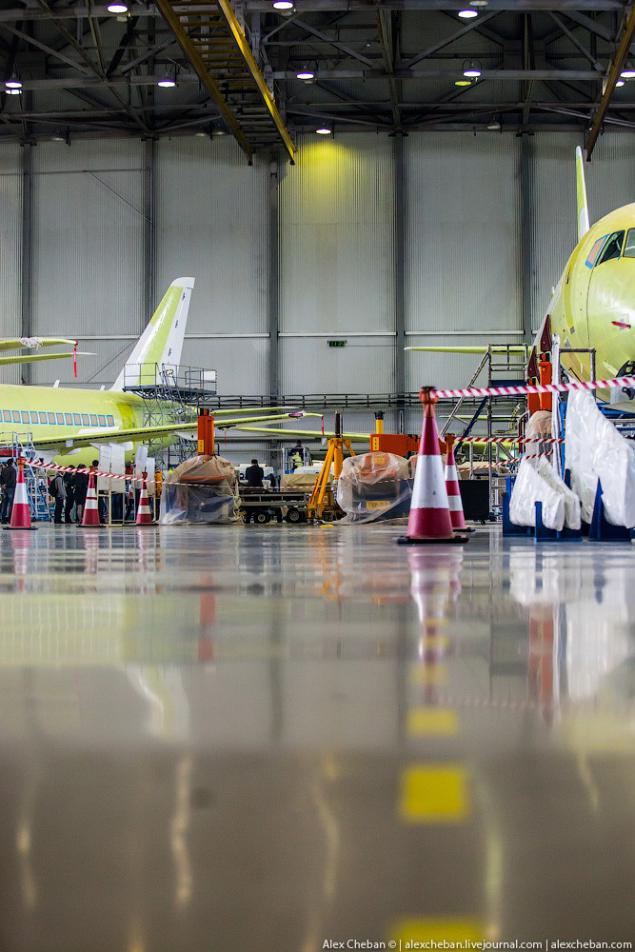
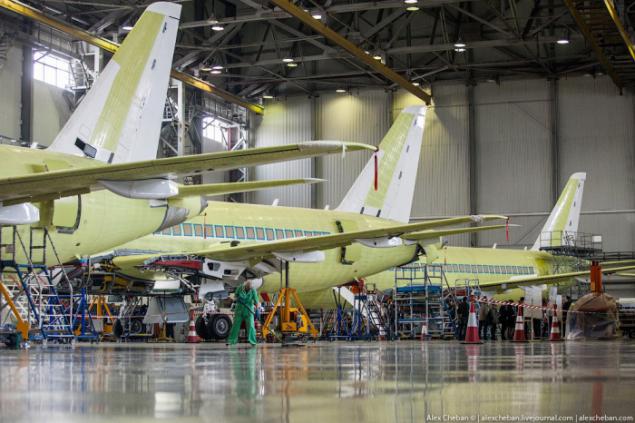
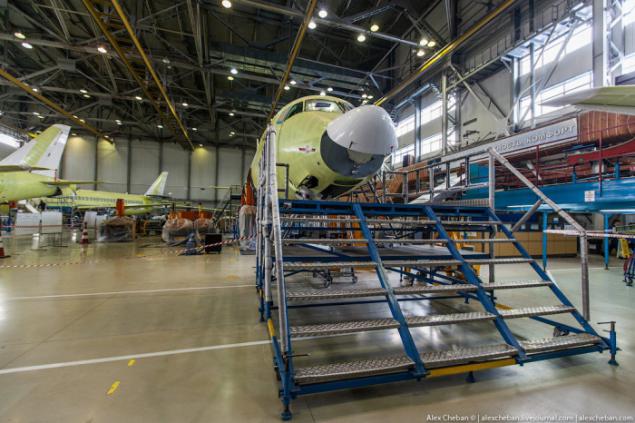
Installation of auxiliary power unit and nose cone.
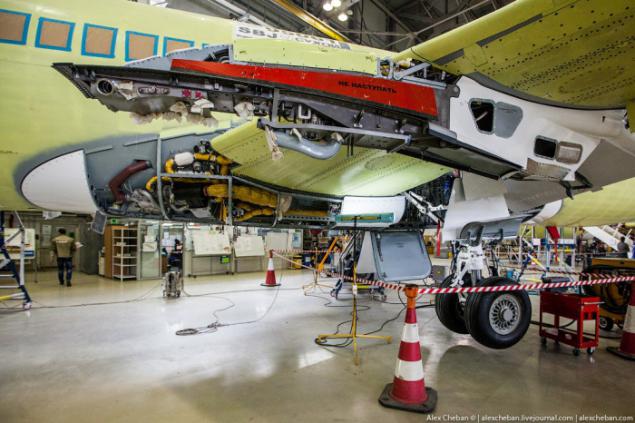
Installation of the front and main landing gear.
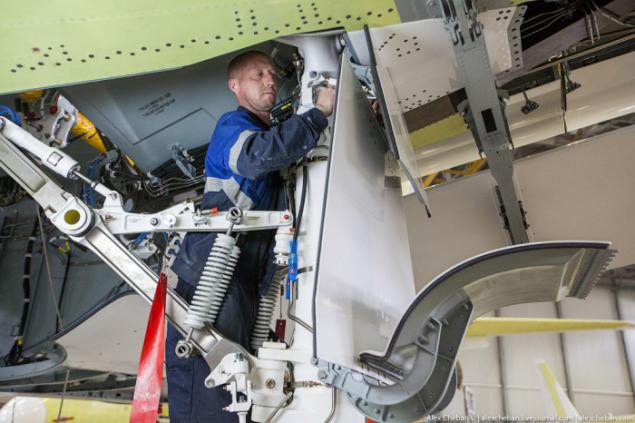
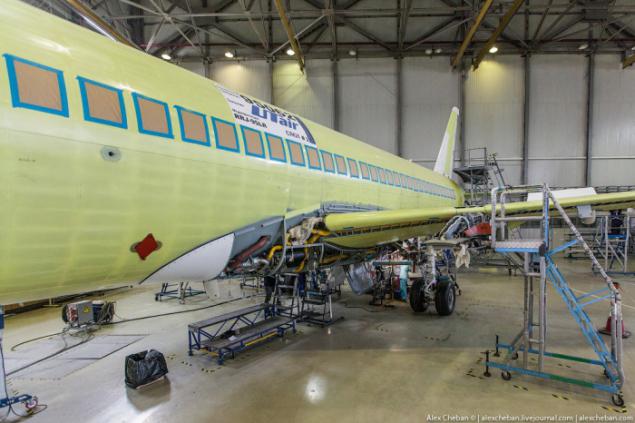
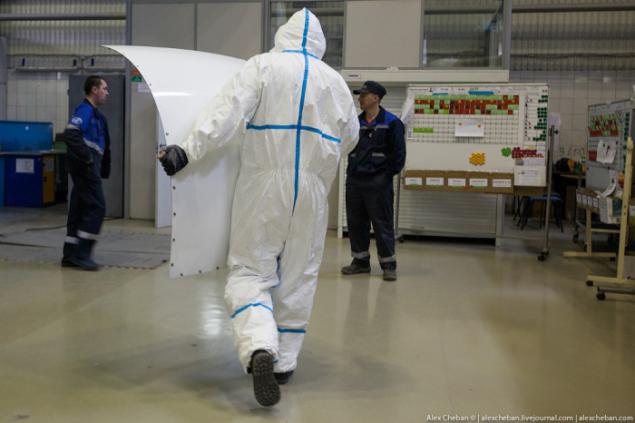
Paint the finished aircraft in the livery of the airline carried in Ulyanovsk or Venice, although some small elements color right here.
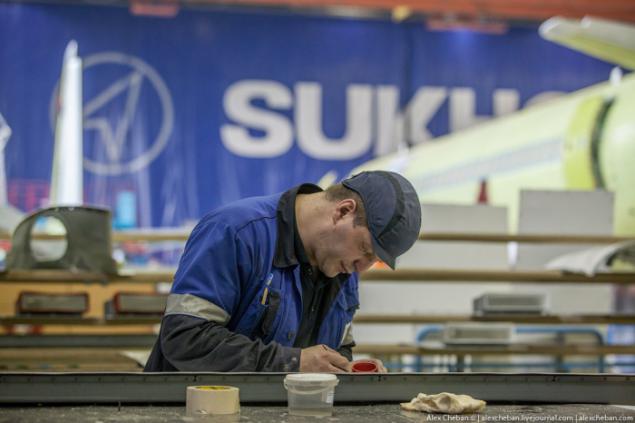
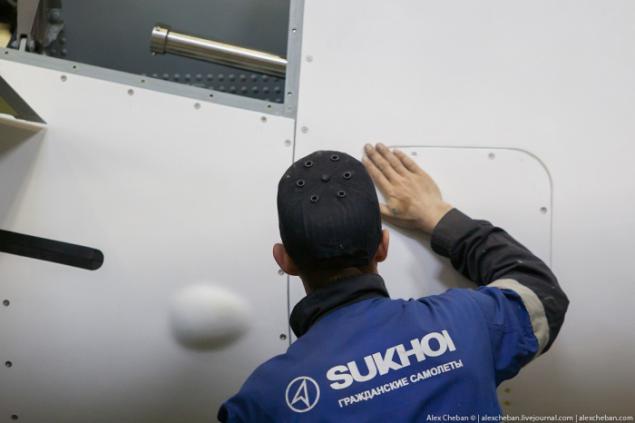
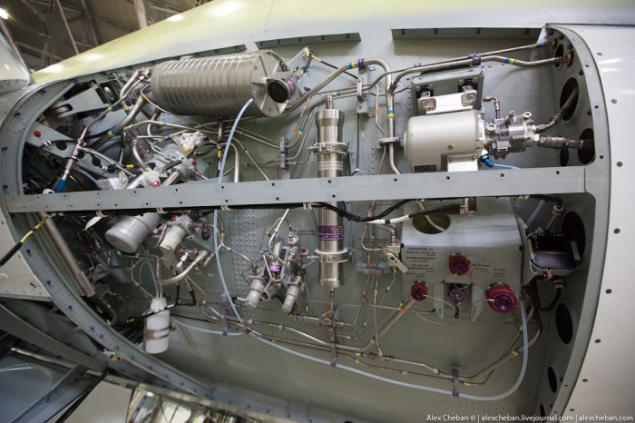
Hydraulic elements ... difficult ?! Harder look only electrical cables! Absolutely all assembly processes are multiple quality control. Each worker is responsible only for your site and a certain list of works.
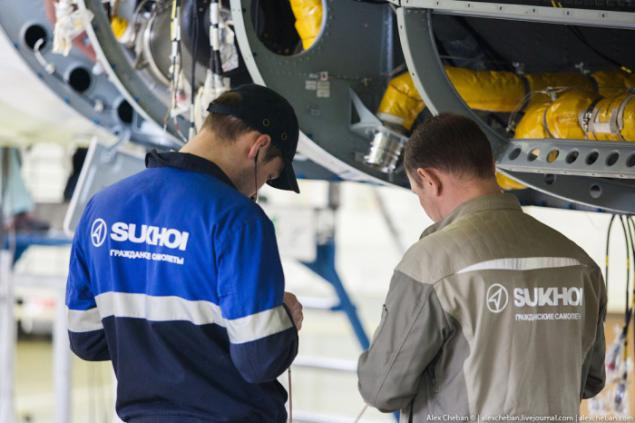
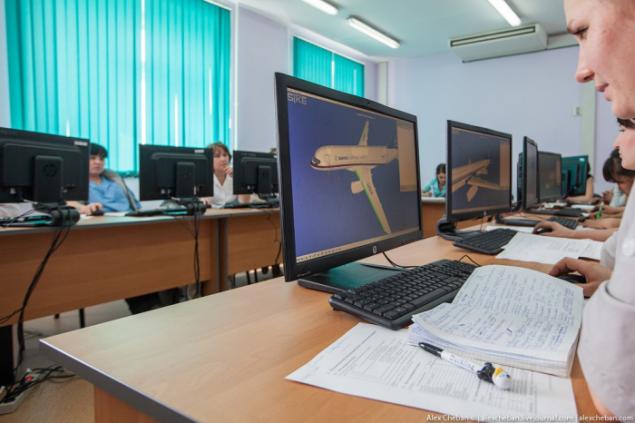
In late 2013 there was introduced a new multimedia teaching system, it works in a nearby building, training and supervision takes place on the job.
All innovations and even quite minor nuances can reduce the build time on the same site, the same way it happens and "Boeing" with the "Airbus". Superjet still a very young project, so every achievement in the production process - a small feat.
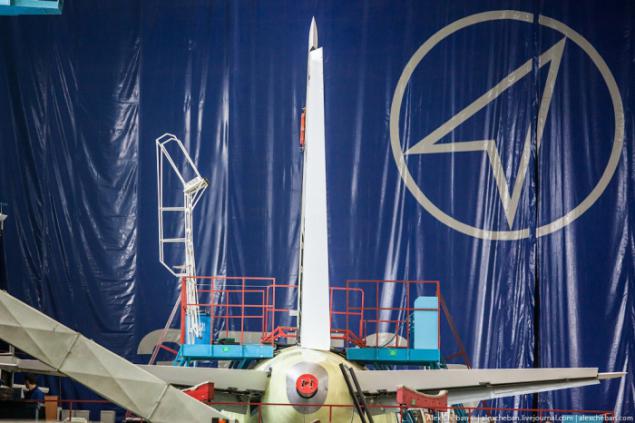
Assembling the plane - this is not a car assembly line, it is - the people. At each stage of our group was accompanied by engineers and department heads, you would have seen their enthusiasm and energy! And what girls working here!
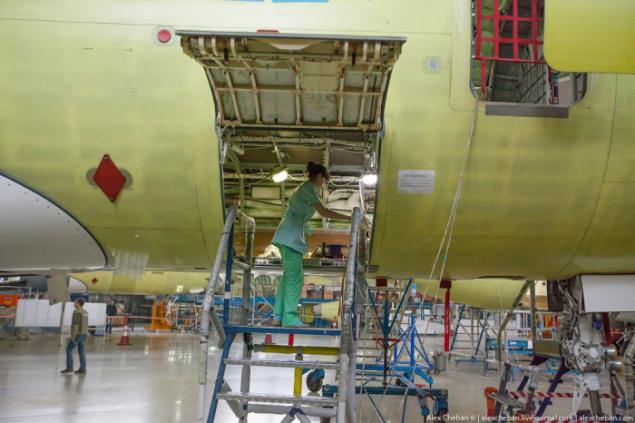
Installation of the elements of the luggage compartment in the process ...
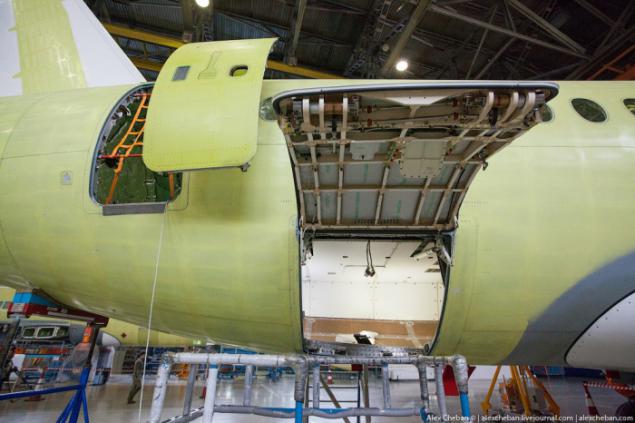
... And after its completion.
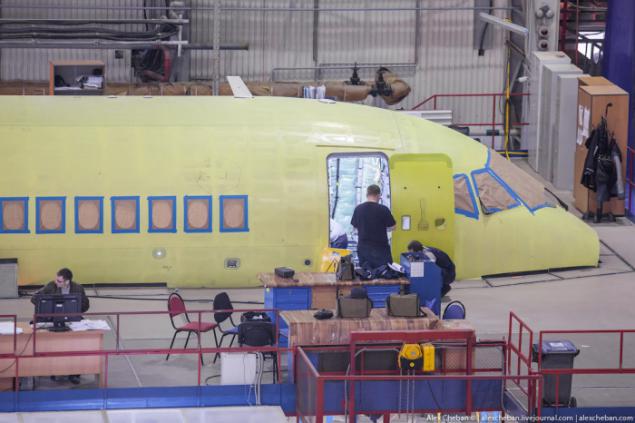
On the last section checks the operation of the chassis, the preparation of the aircraft for delivery under the current installation of equipment units.
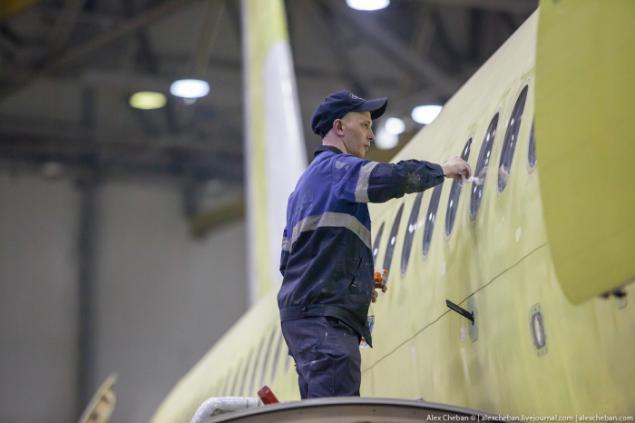
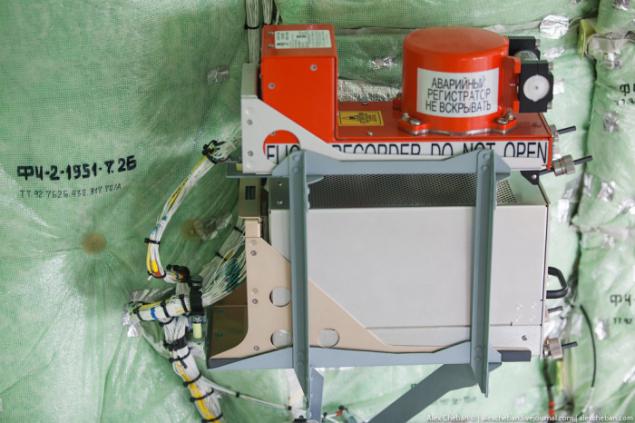
But looks like a crash recorder or "black box" in the language of the layman. And he's not black.
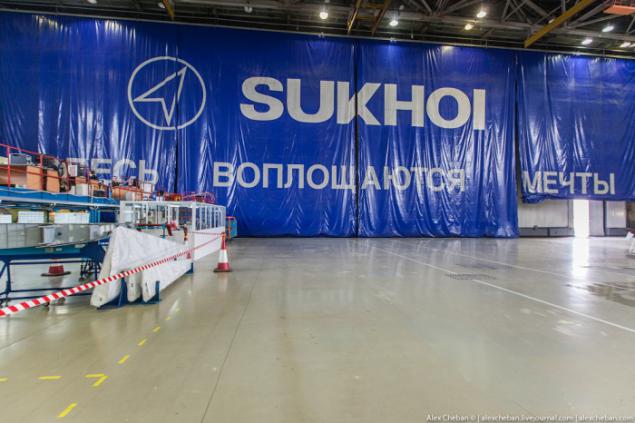
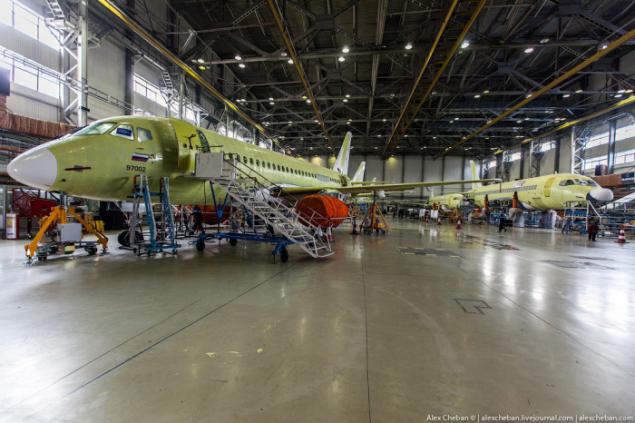
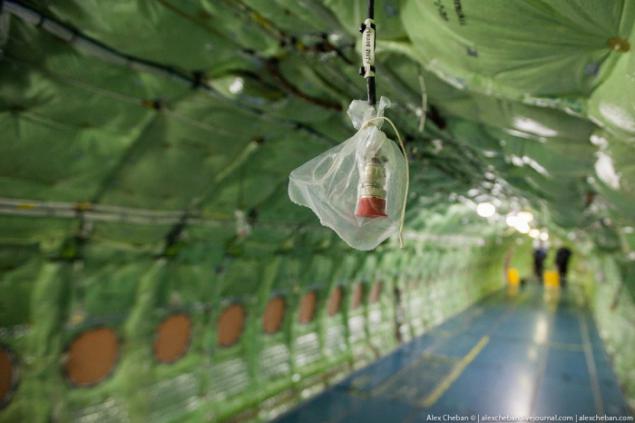
In separate report, I'll show booth Superjet at different stations assembly and in the final version.
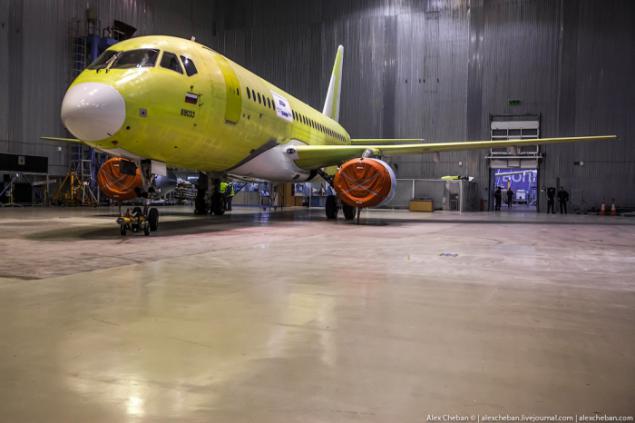
Aircraft is assembled! At this point, it is transferred to the stage of flight performance tests. Usually, each new flight program consists of eight aircraft flight, during which there is air in the test systems.
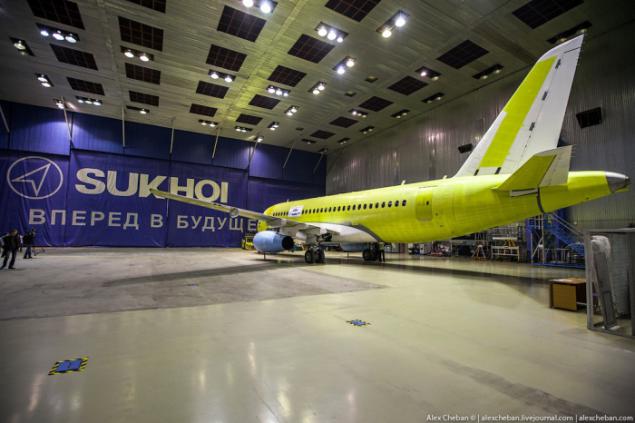
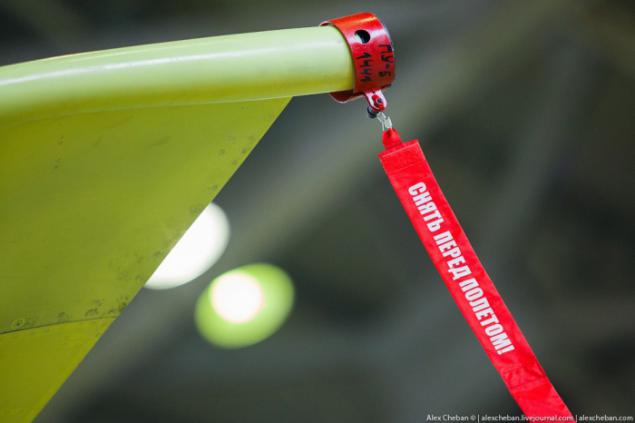
A little unusual to see «Remove before flight» in Russian.
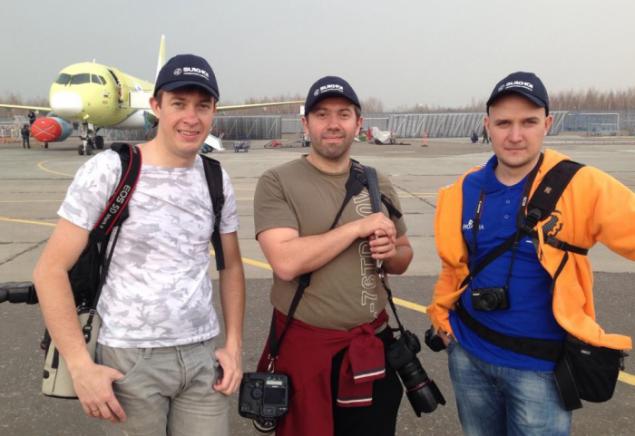
Well, where do in the report without serious guys ?! icon smile How do Superjet: Komsomolsk-on-Amur, Viktor Borisov, Leonid and I Faerberg.
To date (as of May 2014) Airlines delivered more than thirty aircraft, which flew about 29,000 commercial flights a total duration of more than 42 million flight hours.
Well, then there are two ways in brand new freshly aircraft.
If the customer is an Italian SuperJet International, which currently supplies the aircraft for the Mexican InterJet, then assembled in Komsomolsk-on-Amur go overboard once in Zhukovsky, where flights to Venice for the installation of interior and painting. There he will be transferred to the customer.
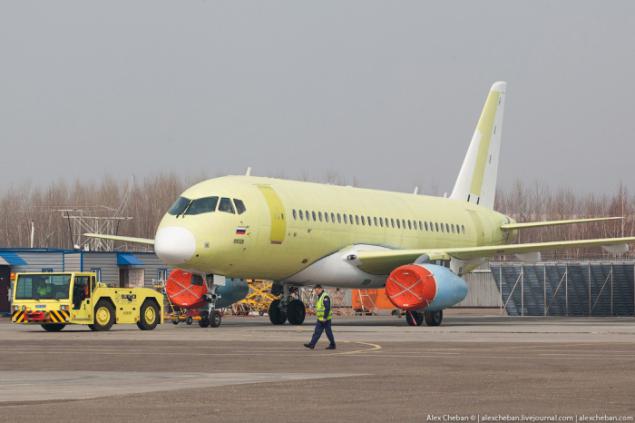
If the aircraft is intended for other customers, the Komsomolsk SSJ100 flies to Ulyanovsk for the installation of interior and paint in the colors of the airline, the aircraft flies out ready to Zhukovsky for transmission customers, including and "UTair". Of Zhukovsky is the second part of the report.
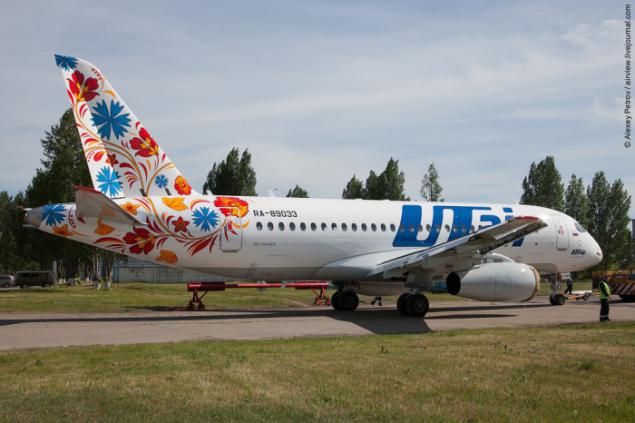
I have already shown before, here is a fun and summer Superjet the "UTair" was released in Ulyanovsk.
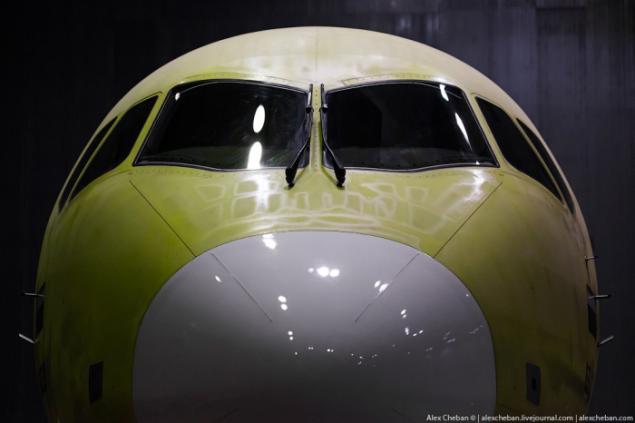
Many thanks to the press service of "UTair" and the GSS and personally Elena Galanova and Marina Motor!
©