1245
25 steps, or How to collect batteries
Have you ever looked inside the car batteries? And we decided to look "inside" the production of batteries. The only Belarusian company, which manufactures batteries for cars, is in Pinsk (Belarus) and 75% owned by US corporation Exide. The plant bilingual and build big plans. For example, going to produce batteries for Volkswagen Polo Sedan, which are produced at a factory in Kaluga.
First step. From the warehouse bring a plate "impregnated" special paste (lead oxide additives). They act as conductors. Yellowish color - with a positive charge, greenish-gray - negative. Plates - the major component of the battery, an electrical circuit element. As the filament in the bulb. It determines the amount of paste such important characteristic of the battery as the capacity. A surface area of the plate - starting current.
The thinner plates and more of them, the higher the inrush current. Starter batteries (in Pinsk and only released them) - they have this figure is higher - compared with Arabian horses, traction - with a dray horse.
Pinsk, the company only on the way to the creation of a full cycle of batteries, and now these plates are imported from Poznan, with another plant of the American corporation. "When we will have their own area (unless we rent it), we will be able to expand production. Now our limit - 380 thous. Of batteries per year. The demand in the market of Belarus - 700 thousand. "- Briefly initiates us in case sales manager Anton Uminsky.
The second step. The plates are wrapped in an envelope of a special tape or, more precisely, it makes machine. Wraps - cuts, wraps - cuts ... The goal - to avoid contact of positive and negative electrodes.
The separator tape of porous polyethylene is a bit like rubber, while it is quite thin and has pores. Through them must pass the electrolyte.
The company has automated everything as much as possible. Setting up the equipment carried out by specialists working at the company's European plants. A Breakage Support staff are always on duty. In case of emergency, they are ready to immediately take up the fault. Simple one of the two conveyor belts, even for an hour fraught with the loss of hundreds of euros.
The third step. The pipeline generates a packet from a set of plates - the car alternates them, with a negative charge, then positive, and so on. D.
- Get a pack and there is a battery - it can be anywhere from 10 to 16 plates. In turn, each battery consists of six batteries. Just battery - from 60 to 96 plates, - says Alexander Matvienko, quality manager and one of the old-timers of the enterprise.
The fourth step. At this stage, without human intervention has not been - a marriage bad envelopes. Often the edges uneven cut, skewed. The point, of course, not aesthetics. Remember, we said above about unwanted contact negative and positive plates? Simply remove the potential conflict now. This test, of course, is not limited, but the details below.
The fifth step. If you look closely, on both sides of the package, you can see the metal "tabs" or ears. Ears plus and minus plates are grouped on the opposite sides of the package. Why, it will become clear later.
Now lay the bags in the other car.
Automatic lubricate them with a special solution of the organic acid, which removes the oxide film - lead to better payalsya.
The sixth step. Prior to that, the preparations for the establishment of an electrical circuit in the battery. And now to the main conveyor starts acting - "Bookmarks" -ushki "dip" into the molten lead in a special form (the temperature - 400 degrees Celsius) and immediately cooled with water form. Therefore, clearly visible in the picture pairs.
Near procured lead ingots, which are, in fact, is melted. It looks impressive. To drop a leg - will not find it.
By the way, on the feet of all employees - special shoes (guests give galoshes). In gravity drop leg it protects against injuries, which can be quite severe. And still required glasses and a dust mask. More than four hours in a shop it is prohibited without a mask. All staff are checked on a monthly basis on the content of lead in the body.
The seventh step. Now the future of battery receives a plastic box divided into cells - a candy bar. They, too, are imported from abroad (from Poland and France, where there are several plants of American corporations). An important point: in the inner walls of openings are provided. This is also a reason. About recall them later.
Another machine-tongs gripper inserts monoblock already welded plate packs: first even and then the odd. Like a cassette tape.
Eighth step. But the look of welded ushki- "bookmarks". In the future, they will connect with the neighboring cell special bridge. Also added to the conclusions of "plus" and "minus". At this stage, very clearly visible electrical circuit the battery. As the pages of textbooks on physics.
- The electromotive force of each cell - 2 - continues Alexander Matvienko. - When all six batteries connected as time and will receive the required 12 V battery. It will nourish and radio, and lighting fixtures, and, of course, to give the inrush current to the starter.
The ninth step. As photos are difficult to measure the temperature of the metal. But believe me, it is high. Therefore, future battery sent to a buffer zone, where bridges are cooled. At this time, a voltage of 2 kV being checked for short circuits. It eliminates even potential contact between the negative and positive plates. At this stage, the defective packets still can get and replace. Reveals the same candy bar at a later stage - then incur losses.
- And how do you know that the equipment fails? - Ask.
- In this case there is an advance copy - Alexander puts on the conveyor battery. Red light, and the conveyor "spits" a marriage in a special compartment.
The tenth step. The final phase of the electric circuit. Wire welding plate packs (attention!) Through the very hole in the inner walls of the candy bar. Again, no human intervention! Hiss. Welding takes a couple of seconds. Done!
Before welding
After welding. Pay attention to the deepening in the ears
Eleventh step. The next test is a short-circuit at the same time checked the quality of the welding plate packs. This is the last time when you can look inside the battery.
Occasionally the operator looks at light panel that hangs right in the shop. It is indicated for each pipeline its number of planned to release the battery, and the amount taken. Yes, even at almost US plan to withdraw from the venture will not succeed.
The twelfth step. Gradually the Bank takes a more presentable. Battery gets inside the cover with the conclusions of the "plus" / "minus". More recently, its design was different. Now he is in favor of technological change. In the same case the battery off the assembly line at the other plants under the Exide brand Centra, Exide, Tudor and others.
Thirteenth Step. And now ... the cover is removed to finally welded to the monoblock. It is pressed against the melt plate and press down to the plastic boxes. Again, the process is automated.
All the time we were in the company, it seemed that someone was missing. The shop is almost empty, but the work does not stop there: in the factory only about a hundred people, a minority of which are involved in the production.
Fourteenth step. Soldering terminals "plus" and "minus" (negative - a little thinner). A metal pin (Born) connect with the familiar motorists to "finger", which cling and terminals.
- The battery is no other metals, except lead alloy, - says Alexander Matvienko. - Manual soldering is carried out in order to ensure full contact Bourne and conclusions.
Fifteenth step. Battery check again. At this time, for leaks. The machine inserts a tube into the fill hole and battery takes to the air pressure.
- There are external and internal leaks. In the first case that the electrolyte does not spill on the body did not have microcracks. In the second case, check the reliability of the walls between the cells. This is also important because in violation of the internal leak battery will self-discharge faster - explains Alexander.
Sixteenth step. Put the inner stamp - stamp.
In fact it should be more company than the buyer. In the code, encrypted data, and change some specifications.
For example, "1" means 55-ampere hours, "2" - 60 ampere-hours.
Climb to the platform, which is clearly visible from the main plant. At the end of the day managers planning meeting held here. In all felt the Western approach.
The speaker comes into the circle, outlined on the floor. He is given no more than two minutes. It manages the plant Serb Australian origin - John Nikolic. It almost does not know Russian or Belarusian, so all communication takes place in English.
Seventeenth step. "Dry" batteries are carried in the "wet" department.
There are a lot of barrels, tanks, and workers wear special aprons, gloves, armlets. Aggressive media after all.
Constantly have to deal with dilute sulfuric acid. Yes, here it comes another important stage - in battery electrolyte is poured. It does this machine again. The density of the electrolyte is poured - 1, 26 g per 1 cu. cm.
The operator then inserts the plug and connect the battery cables, connectors - turns the electric circuit, which can be up to 16 batteries.
They asserted no more than an hour. At this time, the electrolyte is absorbed in the plates and the battery is cooled, because the temperature when filling them rises sharply.
The eighteenth step. Batteries are transported to the site of formation.
When you enter, you can feel the characteristic smell of the products of chemical reactions, the habit we even coughed.
Batteries are still assembled in a single chain. But now there is energized. Why?
- This is the formation. If you pour the electrolyte, and to do nothing, it will start undesirable for battery sulfation process, the interaction of lead and acid - explains our attendant. - As a result, crystals are formed, lead sulfate, which subsequently can no longer participate in chemical processes, and the battery will lose some of its capacity. By the way, motorists note: for this reason discharged battery can not be stored for a long time. To avoid this, the battery charge current. For each type designed their programs and algorithms. Depending on the battery capacity process may take 15 to 40 hours.
The nineteenth step. Already formed batteries recycled in the "wet" department. There dozalivayut electrolyte whose level usually decreases slightly. This is due to the fact that during the charging process acid is absorbed in the plate portion goes to electrolysis. On top of regular automatic installation check the level again.
The twentieth step. All procedures were completed with the electrolyte. On the cover of the battery set with special plugs that motorists avoid being sprayed with acid. Precautions, of course, is not superfluous.
Produced here are maintenance-free batteries. This means that at least a year and a half of motorists do not have to look inside yourself battery to measure the density and the electrolyte level. Although there is an opportunity to remove the cover.
Twenty first step. It is necessary to bring marafet. The battery gets into the washing tunnel. It washed away a drop of electrolyte.
Twenty-second step. Stripping conclusions "plus" and "minus". They are beautiful and shiny - so they see the buyer. But it is not only to give a presentable - oxides findings remove the current difficult.
Twenty-third step. Another test - perhaps one of the most important and decisive. Battery check "big" in the current operation. Within two seconds, the battery "take away" the electric current up to 1500 A, the measured voltage across the terminals. The index should be at least 50% of the initial, ie, 6, 0 to 6, 5 V. If below - it's a marriage, and the battery, no matter how hurt comes to parsing controllers.
The controller should find out what the cause of the problem. Then the results of the study fall into the quality of service and technical support - to eliminate defective products in the future. Above the table hang photos of defective items.
Twenty-fourth step. Needle Markers causes another encoding. The first number - the year of issue ("3" refers to 2013th), letter A - a month (in the Latin alphabet: A - January, B - February, C - in March and so on. D.), F - the symbol of the plant (Pinsk enterprise Americans have assigned the letter F), 18 - the number of months, A1 - the designation change. By the way, from this moment the warranty period is counted.
Twenty-fifth step. The final touch. Work wears pad on the findings and places stickers on the body. There is one trick. Stickers are several types, although differences in the batteries - no, go from one conveyor. Products Company Pinsk in Belarus know brand Zubr, while in Russia the same batteries are sold under the brand name Hagen. The famous marketing ploy: when one product is sold under different names.
Stickers - is the last step. When batteries are taken away to the warehouse, and from there - to suppliers.
From myself -All. I would be glad if someone was just as interesting as I do.
Taken from auto.onliner.by
Source:
First step. From the warehouse bring a plate "impregnated" special paste (lead oxide additives). They act as conductors. Yellowish color - with a positive charge, greenish-gray - negative. Plates - the major component of the battery, an electrical circuit element. As the filament in the bulb. It determines the amount of paste such important characteristic of the battery as the capacity. A surface area of the plate - starting current.
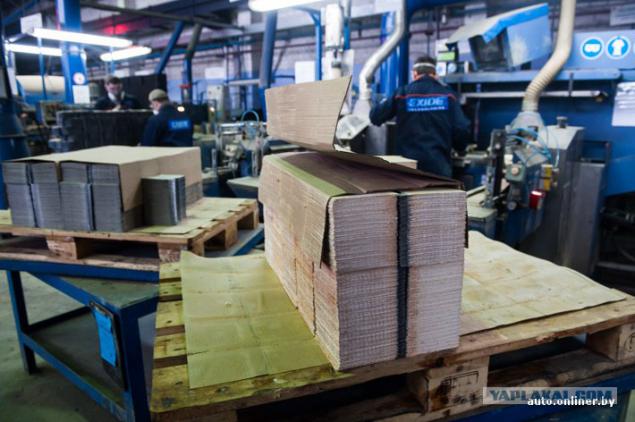
The thinner plates and more of them, the higher the inrush current. Starter batteries (in Pinsk and only released them) - they have this figure is higher - compared with Arabian horses, traction - with a dray horse.
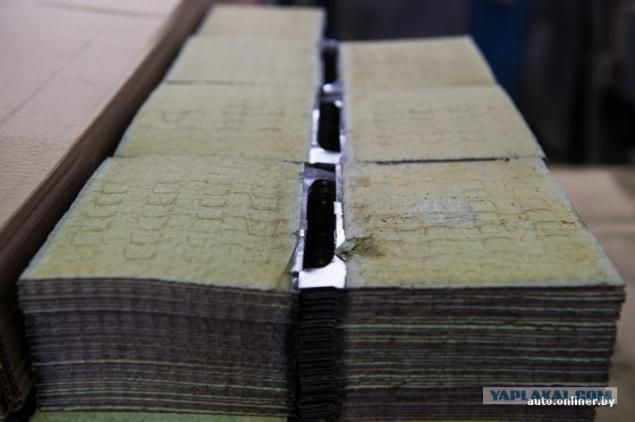
Pinsk, the company only on the way to the creation of a full cycle of batteries, and now these plates are imported from Poznan, with another plant of the American corporation. "When we will have their own area (unless we rent it), we will be able to expand production. Now our limit - 380 thous. Of batteries per year. The demand in the market of Belarus - 700 thousand. "- Briefly initiates us in case sales manager Anton Uminsky.
The second step. The plates are wrapped in an envelope of a special tape or, more precisely, it makes machine. Wraps - cuts, wraps - cuts ... The goal - to avoid contact of positive and negative electrodes.
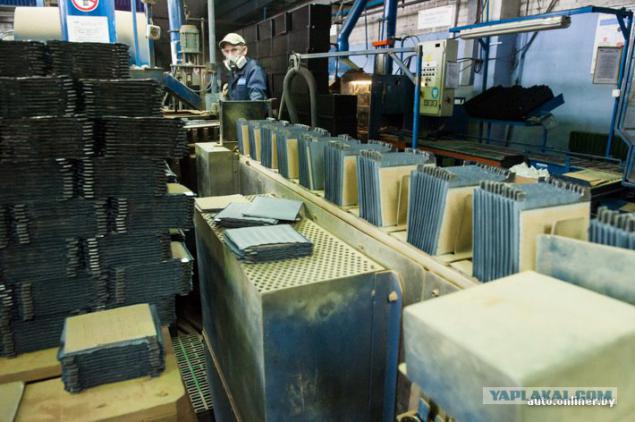
The separator tape of porous polyethylene is a bit like rubber, while it is quite thin and has pores. Through them must pass the electrolyte.
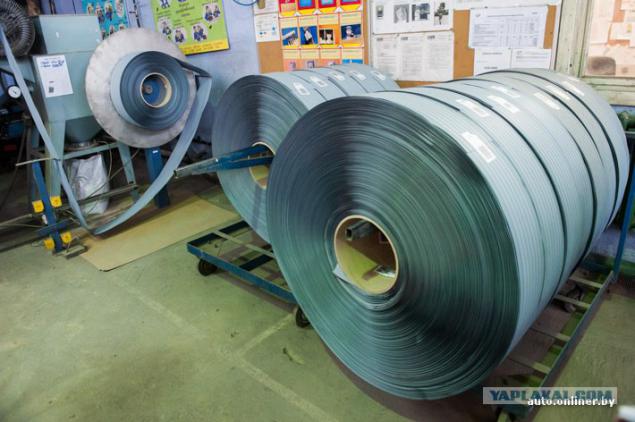
The company has automated everything as much as possible. Setting up the equipment carried out by specialists working at the company's European plants. A Breakage Support staff are always on duty. In case of emergency, they are ready to immediately take up the fault. Simple one of the two conveyor belts, even for an hour fraught with the loss of hundreds of euros.
The third step. The pipeline generates a packet from a set of plates - the car alternates them, with a negative charge, then positive, and so on. D.
- Get a pack and there is a battery - it can be anywhere from 10 to 16 plates. In turn, each battery consists of six batteries. Just battery - from 60 to 96 plates, - says Alexander Matvienko, quality manager and one of the old-timers of the enterprise.
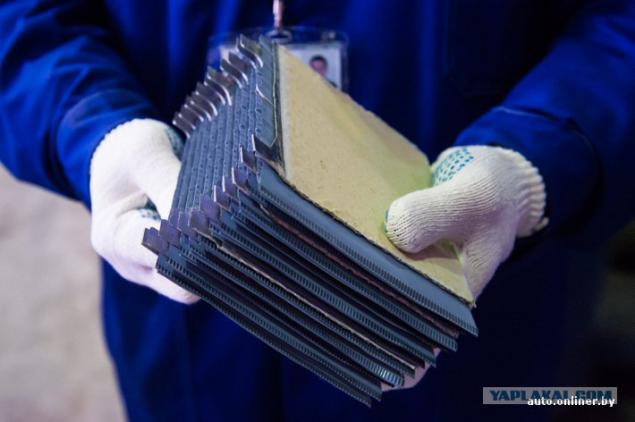
The fourth step. At this stage, without human intervention has not been - a marriage bad envelopes. Often the edges uneven cut, skewed. The point, of course, not aesthetics. Remember, we said above about unwanted contact negative and positive plates? Simply remove the potential conflict now. This test, of course, is not limited, but the details below.
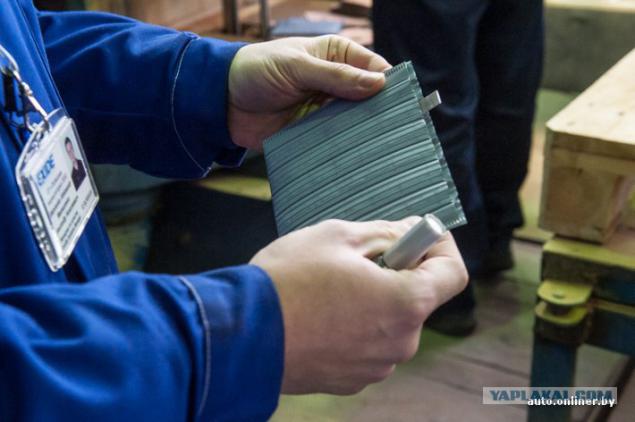
The fifth step. If you look closely, on both sides of the package, you can see the metal "tabs" or ears. Ears plus and minus plates are grouped on the opposite sides of the package. Why, it will become clear later.
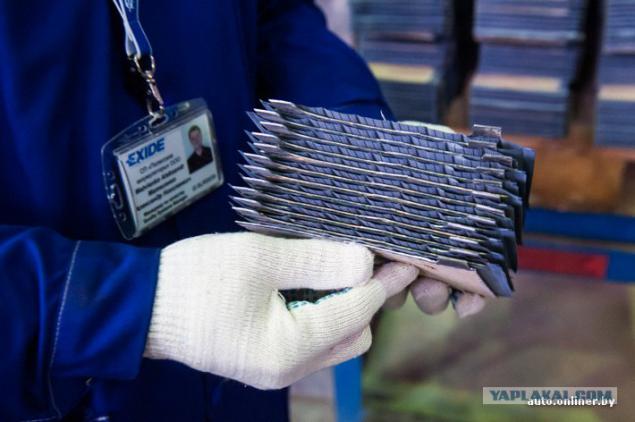
Now lay the bags in the other car.
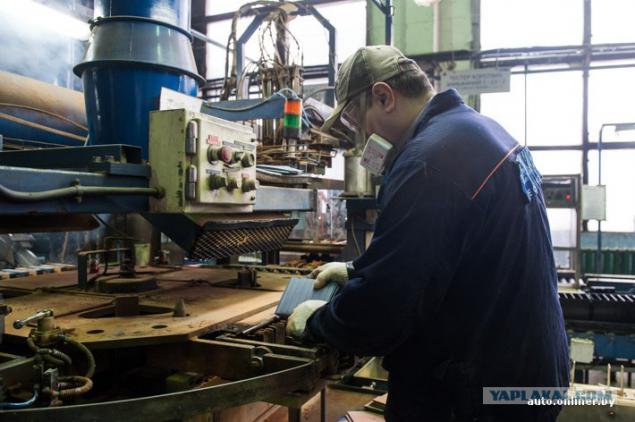
Automatic lubricate them with a special solution of the organic acid, which removes the oxide film - lead to better payalsya.
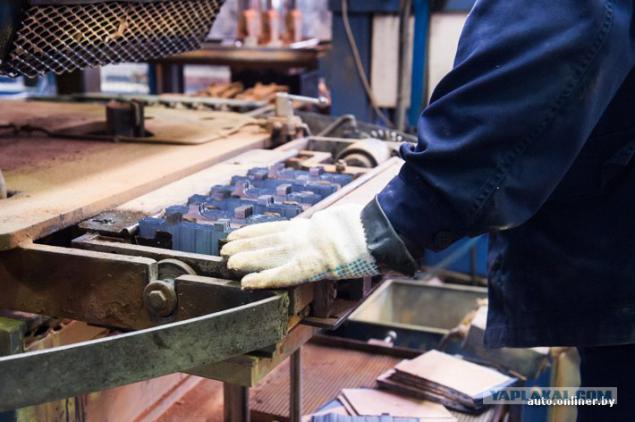
The sixth step. Prior to that, the preparations for the establishment of an electrical circuit in the battery. And now to the main conveyor starts acting - "Bookmarks" -ushki "dip" into the molten lead in a special form (the temperature - 400 degrees Celsius) and immediately cooled with water form. Therefore, clearly visible in the picture pairs.
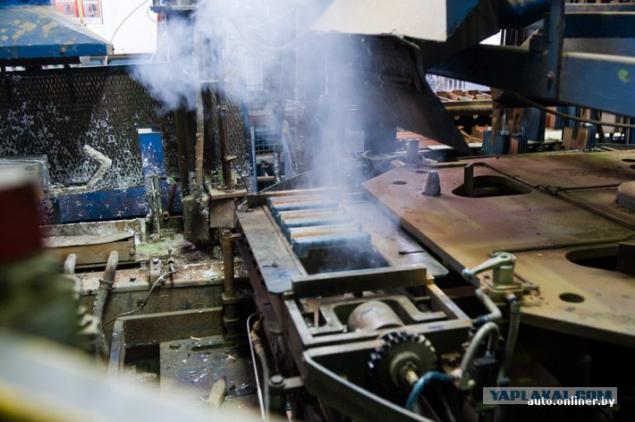
Near procured lead ingots, which are, in fact, is melted. It looks impressive. To drop a leg - will not find it.
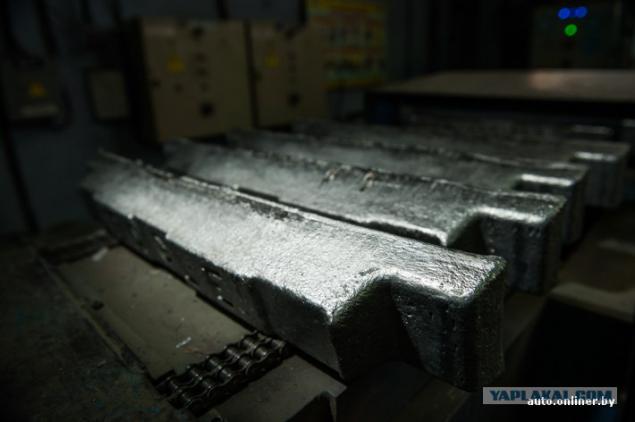
By the way, on the feet of all employees - special shoes (guests give galoshes). In gravity drop leg it protects against injuries, which can be quite severe. And still required glasses and a dust mask. More than four hours in a shop it is prohibited without a mask. All staff are checked on a monthly basis on the content of lead in the body.
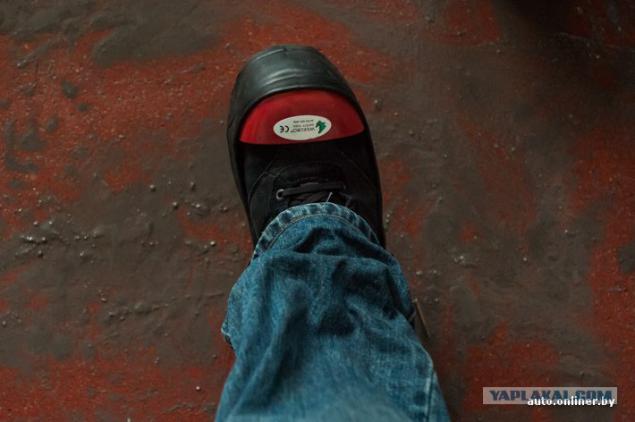
The seventh step. Now the future of battery receives a plastic box divided into cells - a candy bar. They, too, are imported from abroad (from Poland and France, where there are several plants of American corporations). An important point: in the inner walls of openings are provided. This is also a reason. About recall them later.
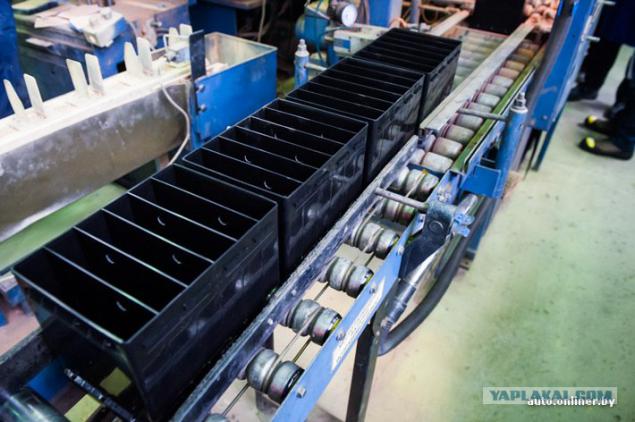
Another machine-tongs gripper inserts monoblock already welded plate packs: first even and then the odd. Like a cassette tape.
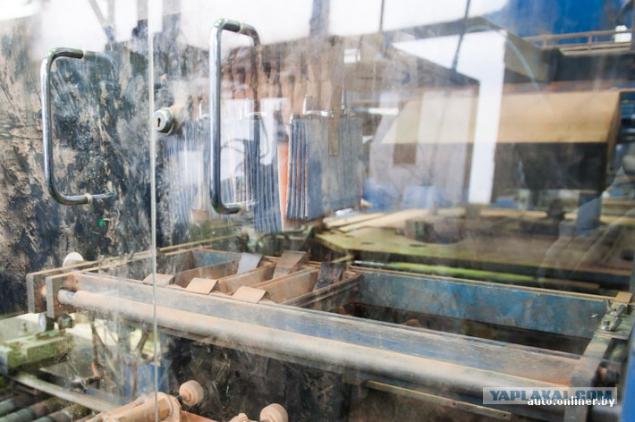
Eighth step. But the look of welded ushki- "bookmarks". In the future, they will connect with the neighboring cell special bridge. Also added to the conclusions of "plus" and "minus". At this stage, very clearly visible electrical circuit the battery. As the pages of textbooks on physics.
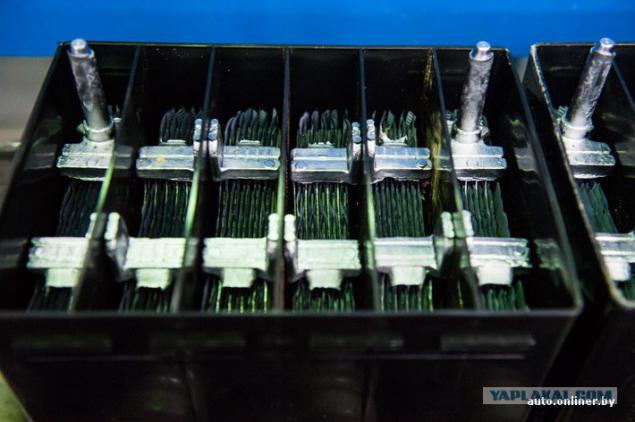
- The electromotive force of each cell - 2 - continues Alexander Matvienko. - When all six batteries connected as time and will receive the required 12 V battery. It will nourish and radio, and lighting fixtures, and, of course, to give the inrush current to the starter.
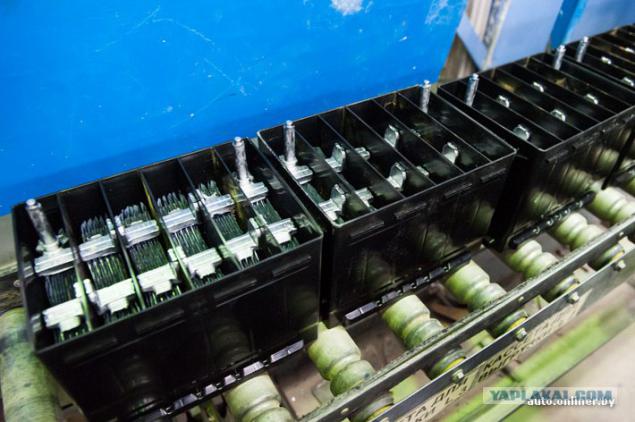
The ninth step. As photos are difficult to measure the temperature of the metal. But believe me, it is high. Therefore, future battery sent to a buffer zone, where bridges are cooled. At this time, a voltage of 2 kV being checked for short circuits. It eliminates even potential contact between the negative and positive plates. At this stage, the defective packets still can get and replace. Reveals the same candy bar at a later stage - then incur losses.
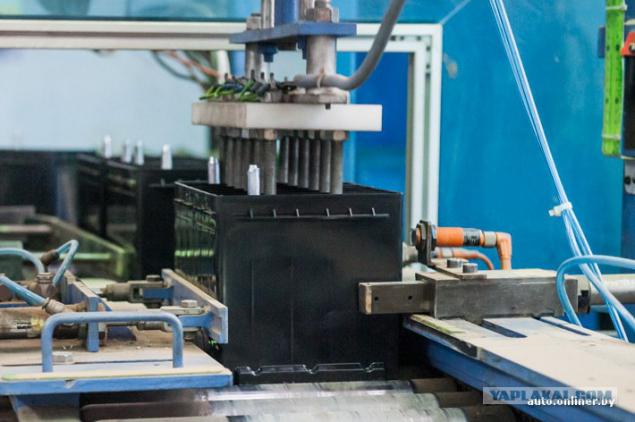
- And how do you know that the equipment fails? - Ask.
- In this case there is an advance copy - Alexander puts on the conveyor battery. Red light, and the conveyor "spits" a marriage in a special compartment.
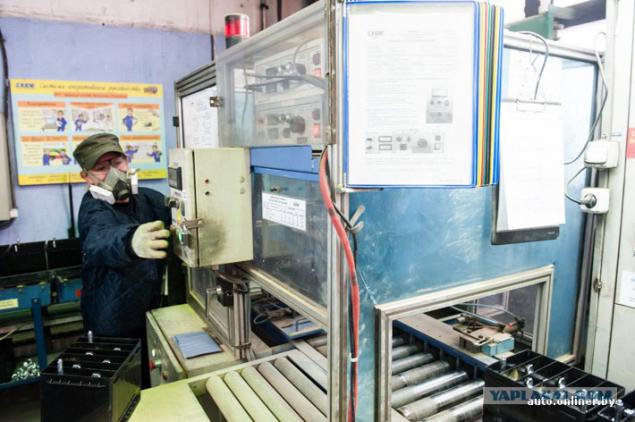
The tenth step. The final phase of the electric circuit. Wire welding plate packs (attention!) Through the very hole in the inner walls of the candy bar. Again, no human intervention! Hiss. Welding takes a couple of seconds. Done!
Before welding
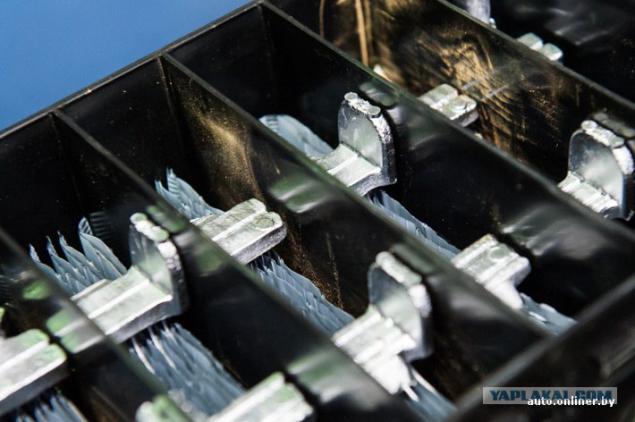
After welding. Pay attention to the deepening in the ears
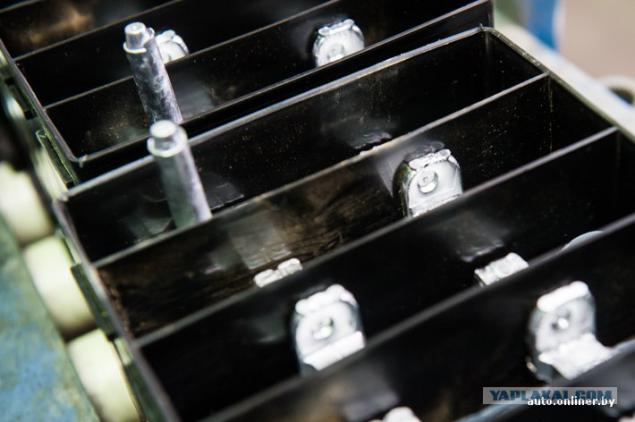
Eleventh step. The next test is a short-circuit at the same time checked the quality of the welding plate packs. This is the last time when you can look inside the battery.
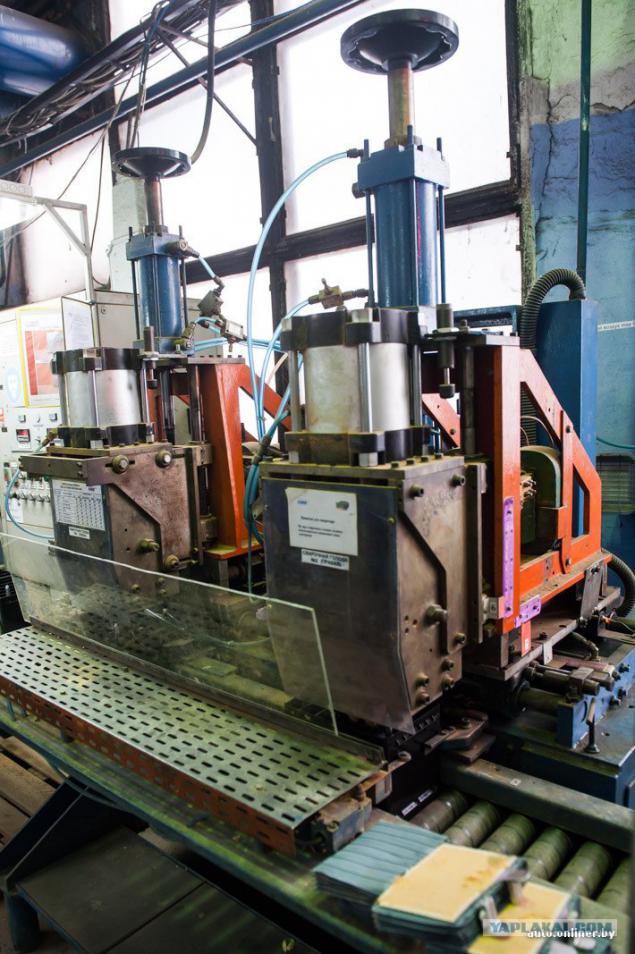
Occasionally the operator looks at light panel that hangs right in the shop. It is indicated for each pipeline its number of planned to release the battery, and the amount taken. Yes, even at almost US plan to withdraw from the venture will not succeed.
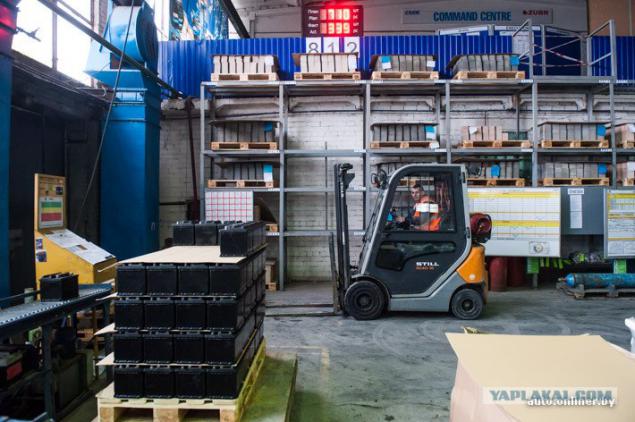
The twelfth step. Gradually the Bank takes a more presentable. Battery gets inside the cover with the conclusions of the "plus" / "minus". More recently, its design was different. Now he is in favor of technological change. In the same case the battery off the assembly line at the other plants under the Exide brand Centra, Exide, Tudor and others.
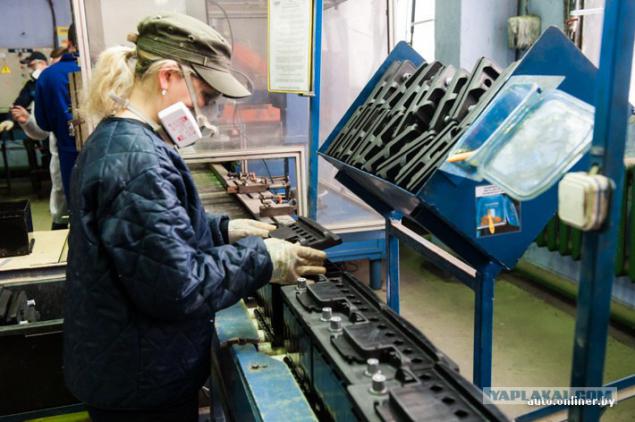
Thirteenth Step. And now ... the cover is removed to finally welded to the monoblock. It is pressed against the melt plate and press down to the plastic boxes. Again, the process is automated.
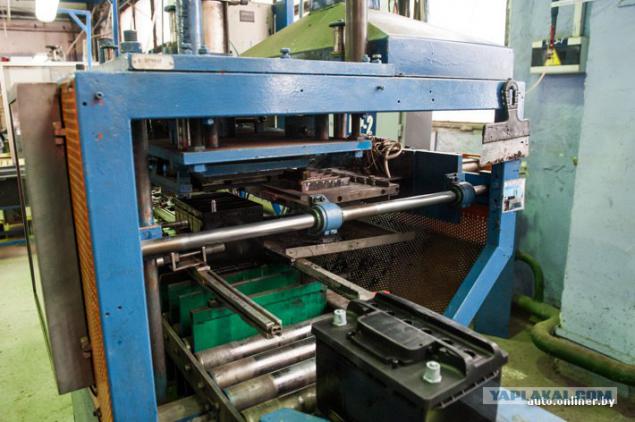
All the time we were in the company, it seemed that someone was missing. The shop is almost empty, but the work does not stop there: in the factory only about a hundred people, a minority of which are involved in the production.
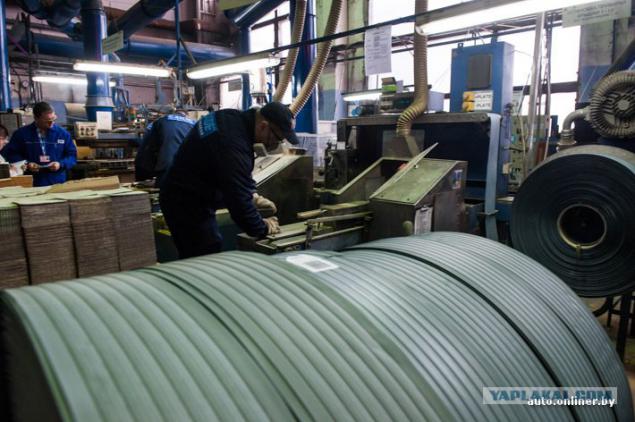
Fourteenth step. Soldering terminals "plus" and "minus" (negative - a little thinner). A metal pin (Born) connect with the familiar motorists to "finger", which cling and terminals.
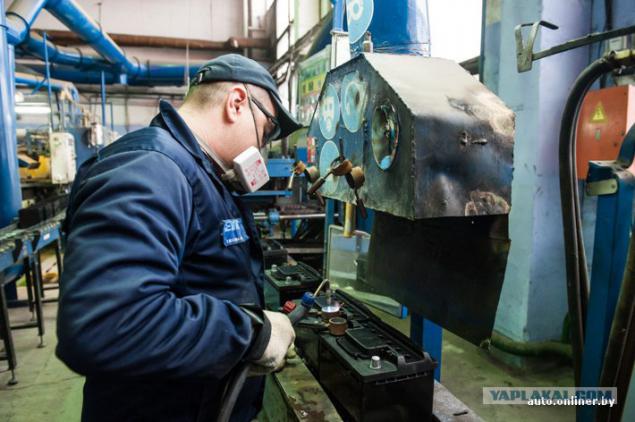
- The battery is no other metals, except lead alloy, - says Alexander Matvienko. - Manual soldering is carried out in order to ensure full contact Bourne and conclusions.
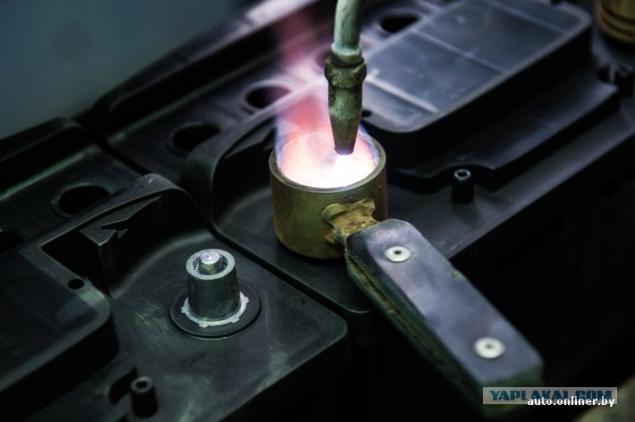
Fifteenth step. Battery check again. At this time, for leaks. The machine inserts a tube into the fill hole and battery takes to the air pressure.

- There are external and internal leaks. In the first case that the electrolyte does not spill on the body did not have microcracks. In the second case, check the reliability of the walls between the cells. This is also important because in violation of the internal leak battery will self-discharge faster - explains Alexander.

Sixteenth step. Put the inner stamp - stamp.
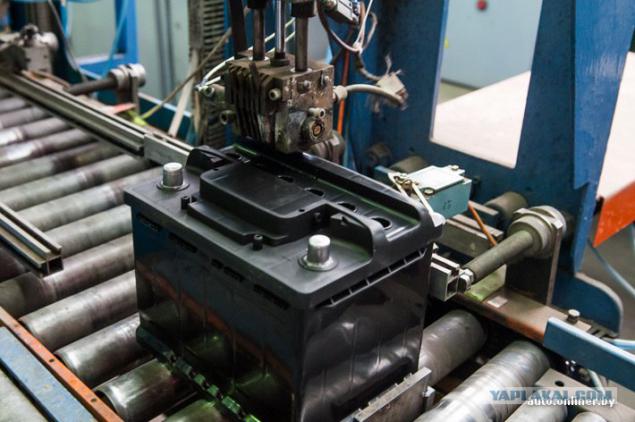
In fact it should be more company than the buyer. In the code, encrypted data, and change some specifications.
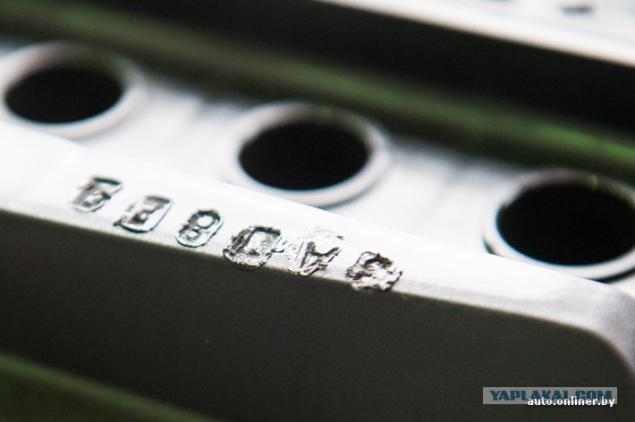
For example, "1" means 55-ampere hours, "2" - 60 ampere-hours.
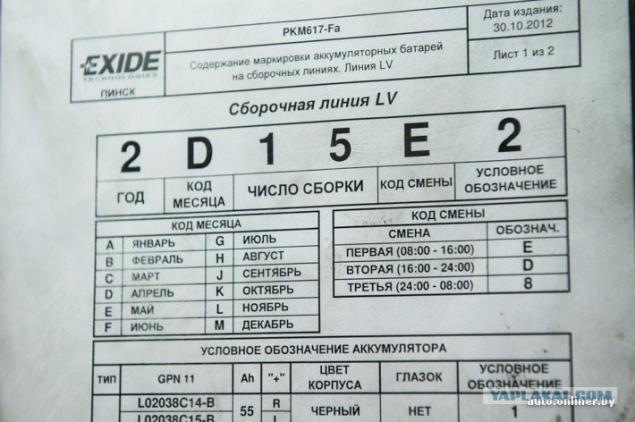
Climb to the platform, which is clearly visible from the main plant. At the end of the day managers planning meeting held here. In all felt the Western approach.
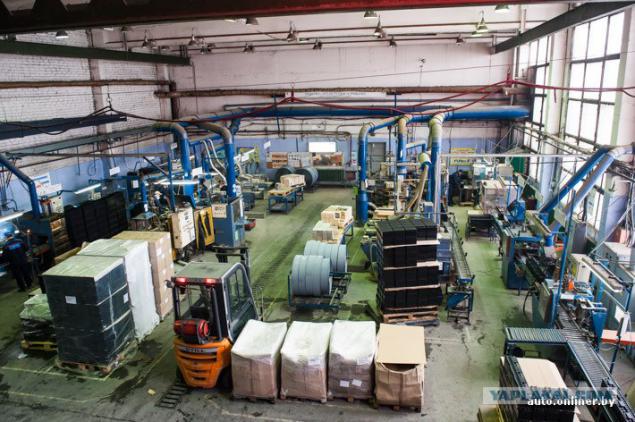
The speaker comes into the circle, outlined on the floor. He is given no more than two minutes. It manages the plant Serb Australian origin - John Nikolic. It almost does not know Russian or Belarusian, so all communication takes place in English.
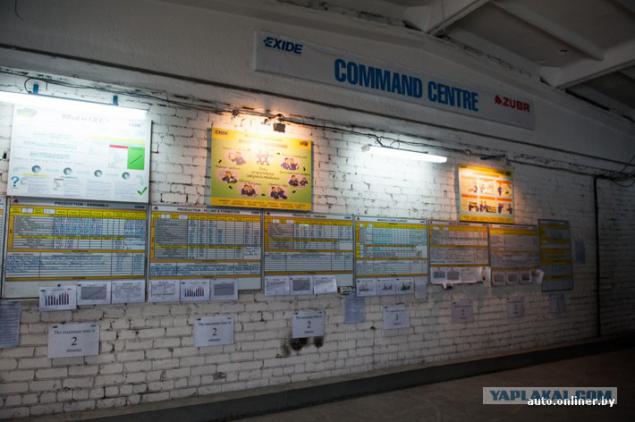
Seventeenth step. "Dry" batteries are carried in the "wet" department.
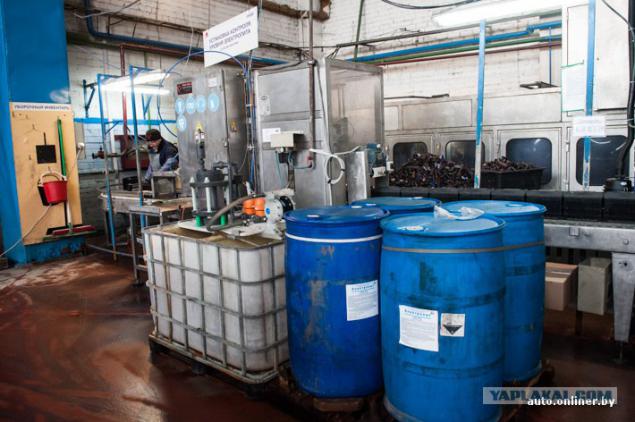
There are a lot of barrels, tanks, and workers wear special aprons, gloves, armlets. Aggressive media after all.
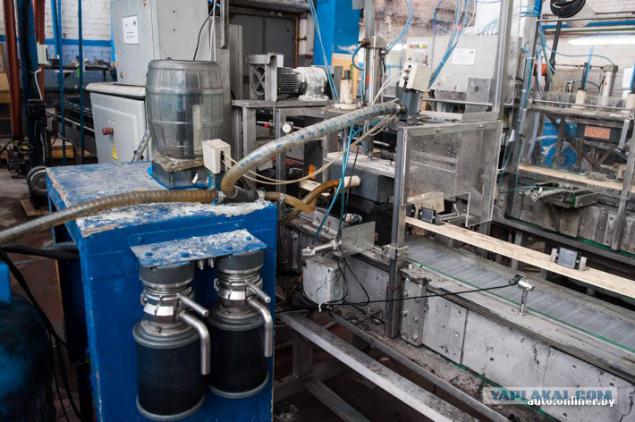
Constantly have to deal with dilute sulfuric acid. Yes, here it comes another important stage - in battery electrolyte is poured. It does this machine again. The density of the electrolyte is poured - 1, 26 g per 1 cu. cm.
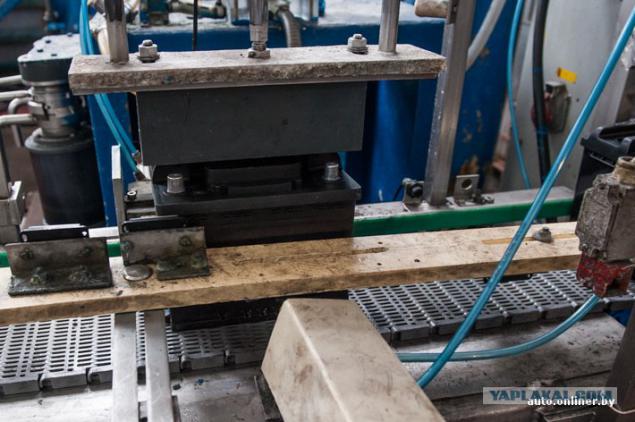
The operator then inserts the plug and connect the battery cables, connectors - turns the electric circuit, which can be up to 16 batteries.
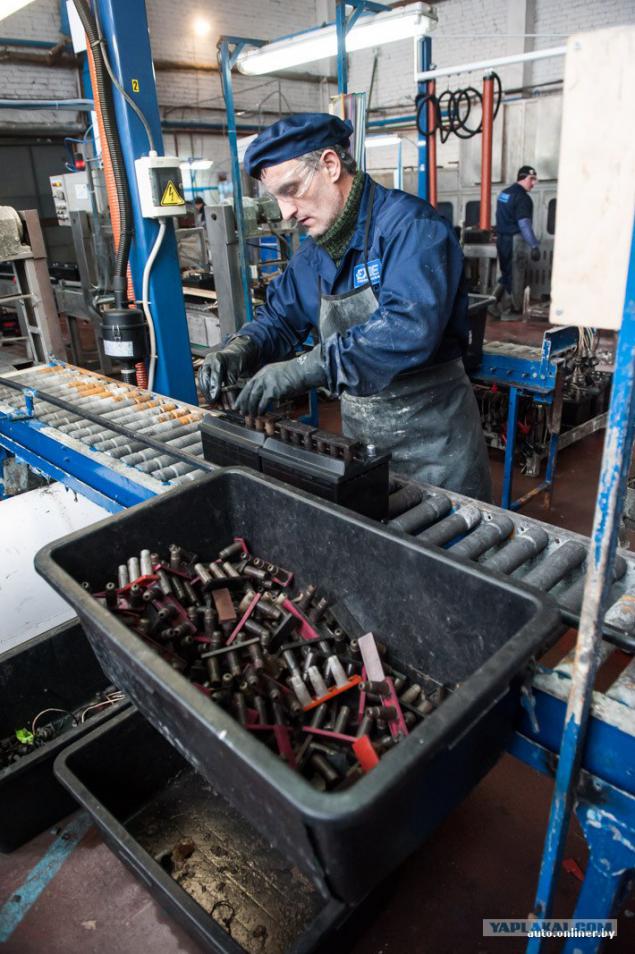
They asserted no more than an hour. At this time, the electrolyte is absorbed in the plates and the battery is cooled, because the temperature when filling them rises sharply.
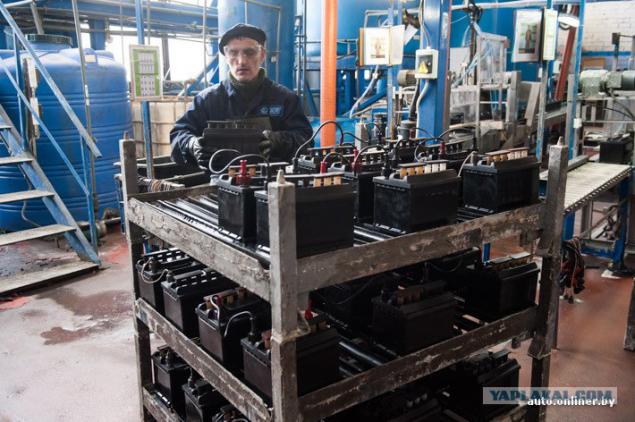
The eighteenth step. Batteries are transported to the site of formation.

When you enter, you can feel the characteristic smell of the products of chemical reactions, the habit we even coughed.
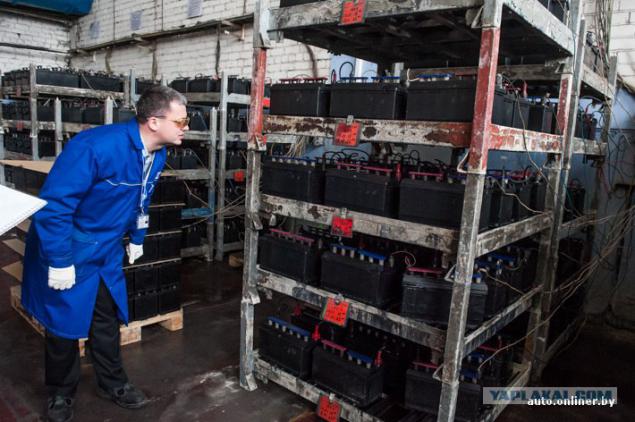
Batteries are still assembled in a single chain. But now there is energized. Why?
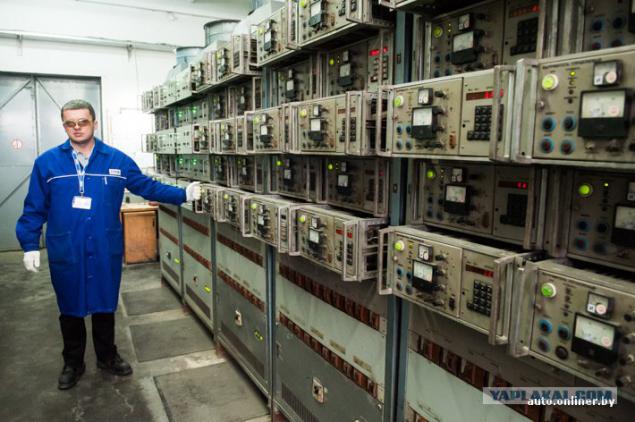
- This is the formation. If you pour the electrolyte, and to do nothing, it will start undesirable for battery sulfation process, the interaction of lead and acid - explains our attendant. - As a result, crystals are formed, lead sulfate, which subsequently can no longer participate in chemical processes, and the battery will lose some of its capacity. By the way, motorists note: for this reason discharged battery can not be stored for a long time. To avoid this, the battery charge current. For each type designed their programs and algorithms. Depending on the battery capacity process may take 15 to 40 hours.
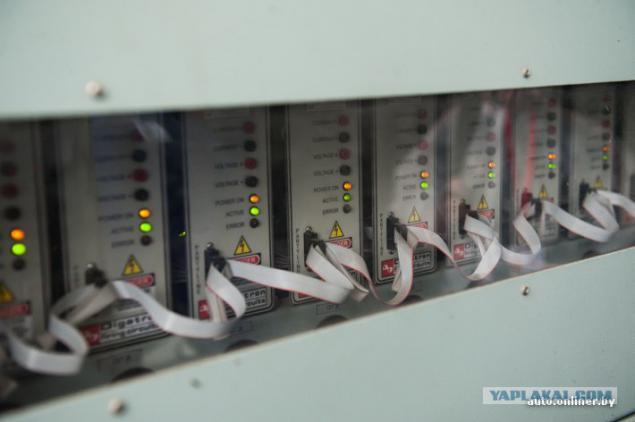
The nineteenth step. Already formed batteries recycled in the "wet" department. There dozalivayut electrolyte whose level usually decreases slightly. This is due to the fact that during the charging process acid is absorbed in the plate portion goes to electrolysis. On top of regular automatic installation check the level again.
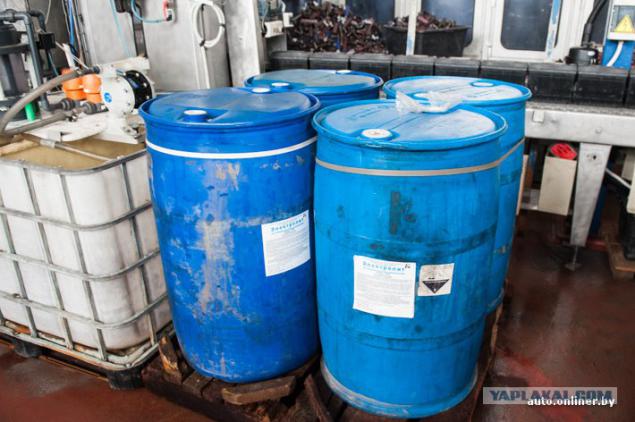
The twentieth step. All procedures were completed with the electrolyte. On the cover of the battery set with special plugs that motorists avoid being sprayed with acid. Precautions, of course, is not superfluous.
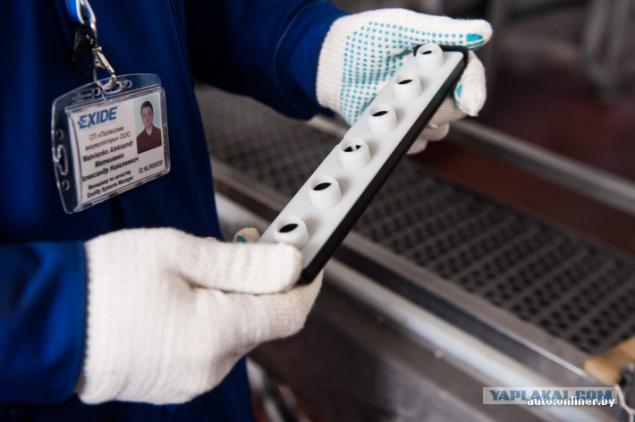
Produced here are maintenance-free batteries. This means that at least a year and a half of motorists do not have to look inside yourself battery to measure the density and the electrolyte level. Although there is an opportunity to remove the cover.
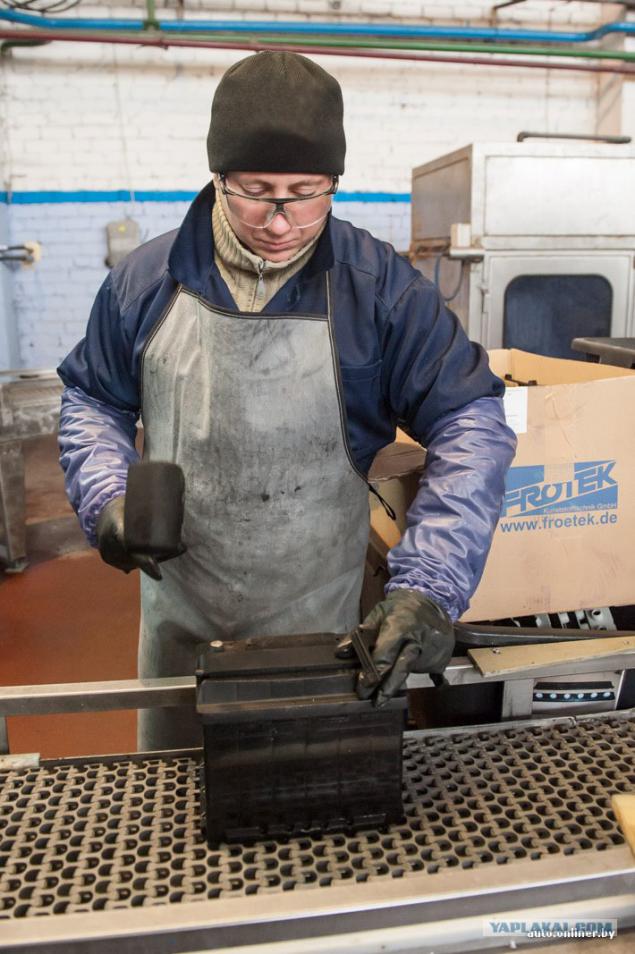
Twenty first step. It is necessary to bring marafet. The battery gets into the washing tunnel. It washed away a drop of electrolyte.
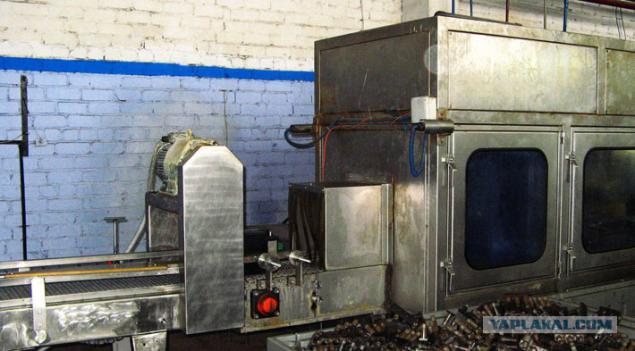
Twenty-second step. Stripping conclusions "plus" and "minus". They are beautiful and shiny - so they see the buyer. But it is not only to give a presentable - oxides findings remove the current difficult.
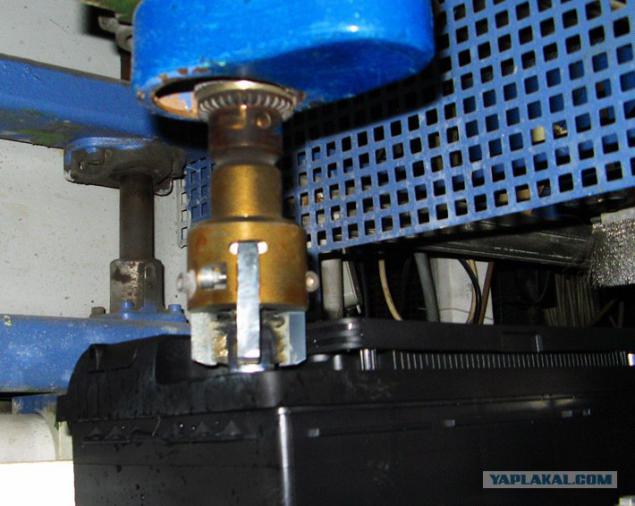
Twenty-third step. Another test - perhaps one of the most important and decisive. Battery check "big" in the current operation. Within two seconds, the battery "take away" the electric current up to 1500 A, the measured voltage across the terminals. The index should be at least 50% of the initial, ie, 6, 0 to 6, 5 V. If below - it's a marriage, and the battery, no matter how hurt comes to parsing controllers.
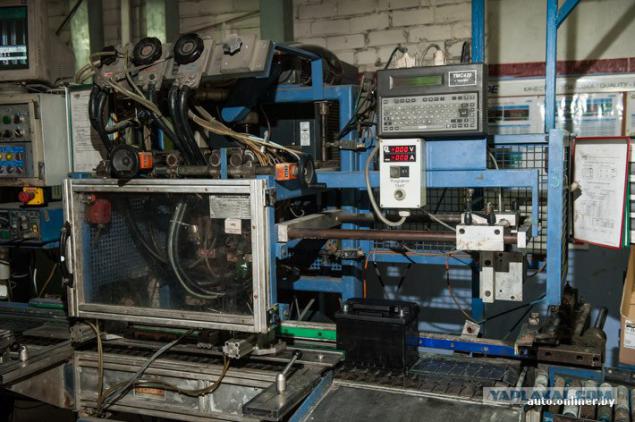
The controller should find out what the cause of the problem. Then the results of the study fall into the quality of service and technical support - to eliminate defective products in the future. Above the table hang photos of defective items.
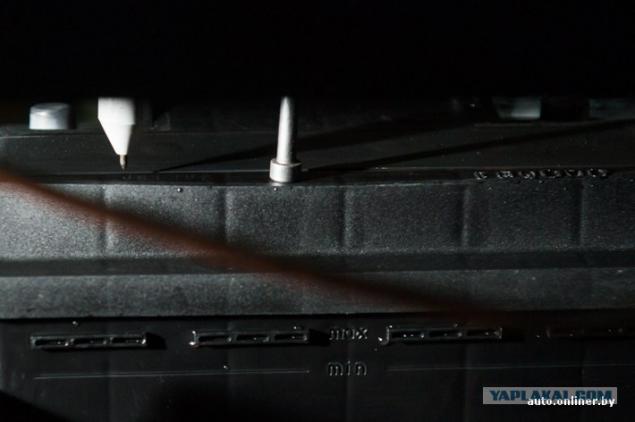
Twenty-fourth step. Needle Markers causes another encoding. The first number - the year of issue ("3" refers to 2013th), letter A - a month (in the Latin alphabet: A - January, B - February, C - in March and so on. D.), F - the symbol of the plant (Pinsk enterprise Americans have assigned the letter F), 18 - the number of months, A1 - the designation change. By the way, from this moment the warranty period is counted.
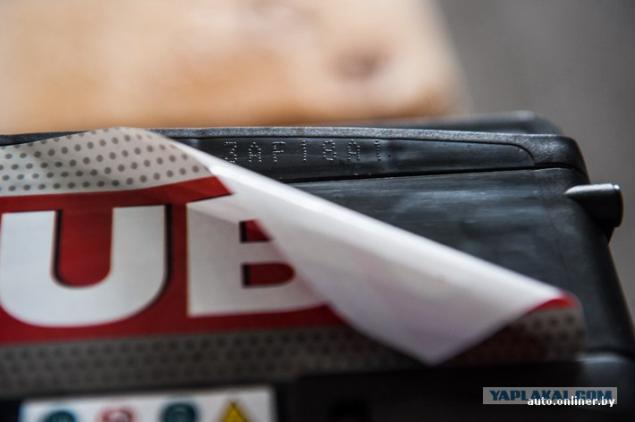
Twenty-fifth step. The final touch. Work wears pad on the findings and places stickers on the body. There is one trick. Stickers are several types, although differences in the batteries - no, go from one conveyor. Products Company Pinsk in Belarus know brand Zubr, while in Russia the same batteries are sold under the brand name Hagen. The famous marketing ploy: when one product is sold under different names.
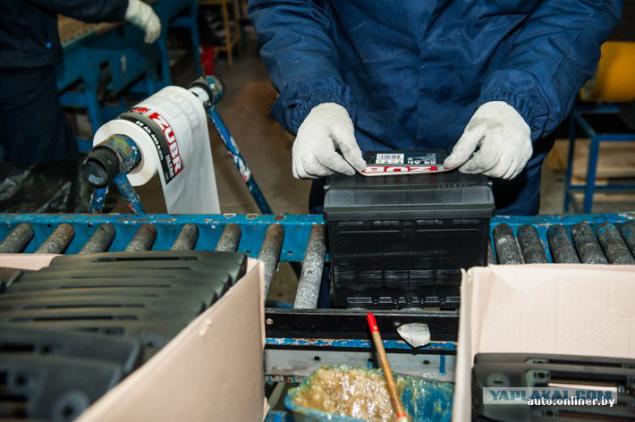
Stickers - is the last step. When batteries are taken away to the warehouse, and from there - to suppliers.
From myself -All. I would be glad if someone was just as interesting as I do.
Taken from auto.onliner.by
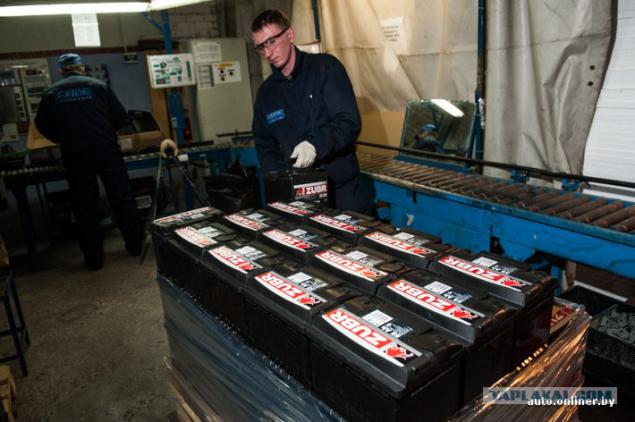
Source: