1203
Engine Clem
Mention of the engine that is the American Richard Clem (Richard Clem) invented, built and successfully used in 1972, is found at many sites dedicated to "free energy". However, almost all of them are a copy of the same article. Perhaps it was the fact that the available information about him is very scanty and fragmentary, and the engine is not what it seems at first glance.
It should be noted that there are many designs that look like the Clem engine, for example, centrifugal engine Igor Vysotsky (he is its author, by the way, this also sure). In fact, these devices use completely different operating principles, and because of their deceptive similarity.
The technical detailsBefore you start considering engine Clem, "sort through" the available information. Below I excerpt from the "canonical" articles, which in varying degrees relate to the technical side of the device.
The "classic" image of the Clem engine. The picture was made under the resolution EGA (640x350), and therefore no correction on modern monitors it looks "flattened". The information in the articleso here's the technical part of the "canonical" articles (for American units of measure in parentheses are metric values, the translation closest to the English original, which substantially changed the description of some moments).
Richard Clem worked with heavy machinery in Dallas. He noticed that certain types of high pressure pumps continued to operate for some time after power has been cut. His curiosity about this phenomenon led to the invention of the motor.... Clem says that... the drivers would only change the eight gallons (about 30 liters) of vegetable oil every 150 thousand miles and never buy any gasoline.The engine weighs about 200 pounds (about 90 kg) and contains vegetable oil at a temperature of 300°F (150°C).Clem said that the used vegetable oil because his motor runs at... the temperature at which water boils and conventional engine oil breaks down. Although he would not disclose details of the device of the engine, its the only additional energy source is a 12-volt battery.It consists of a cone mounted on a horizontal axis. The shaft holding the cone, hollow inside, and the cone has cut therein helical channels. These helical paths along the cone and ending at its base in the form of nozzles (injectors).Liquid is injected into the hollow shaft at pressures in the range 300-500 psig (21-35 kg/cm2), passes through a close spiral channels of the cone and exits through the nozzle. This causes the cone to rotate. The greater the fluid velocity, the faster the rotation of the cone.With increasing speed, fluid is heated, and therefore requires the heat exchanger and the filter. At a certain speed cone begins self-rotation, independent from the engine. The rotation speed of the shaft reaches 1800-2300 rpm.... the motor was tested by Bendix Corporation. The test consisted of attaching the engine to the dynamometer to measure the power on the shaft.The measurements showed that the engine is steadily producing 350 horsepower for 9 days so impressed the engineers at Bendix. They came to the conclusion that the source that could generate all the energy in a CLOSED SYSTEM for such a long time, can only be nuclear.The engine design does not contain non-traditional items, with the exception of the cone with spiral channels and the hollow shaft.When Clem built the first oil engine in 1972, he made a trial trip length of 600 miles (about 1000 km) to El Paso on the motor, which he did on his salary. Before all the shafts and everything bent, he managed to only drive up to Abilene (Google Maps shows the distance along the highway between Dallas and Abilene is 172 miles or 276 km).He explained the failure to the imperfection of the design, too small size of the shaft and using chains instead of gears.Immediately after the inventor was struck by a heart attack and papers were seized, son of the inventor sent the only working model of a machine to a farm near Dallas. There he buried it under 10 feet (3 m) of concrete, and she continued to work at this depth for several years.Here, in General, and all the information Dating back to 1992 — 20 years after the death of the inventor of a heart attack in the same 1972. Later it became known some additional data are as follows.The pump is used as the prototype engine was used for spraying hot, liquid asphalt. The cone was mounted vertically. The heat exchanger was used for cooling. Finally, the latest information about the Clem engine is not mentioned on the cone, but speaks of "seven-pump" and "LNB", "operating like a turbine", and in the photo of the engine showing something similar to the turbine wheel and can not see anything similar on the cone (unless it's hidden inside the "turbines"). The photographs of the car clearly visible two different versions of the engine with longitudinal and transverse orientation of the shaft, but neither one of them have a hint of vertical installation of the cone.
Frankly, the data is not too much — for example, the precise dimensions of the device (this would allow to evaluate the possible diameter of the cone and the resulting centrifugal forces), although given its weight. However, I think that there is quite a lot to try to understand this unusual motor. As for the size of the engine, they may be indirectly evaluated on the basis of the fact that it was placed on the car, apparently, instead of "regular" motor, as the base of the car refers to "Ford Falcon". This model was produced from 1960 until the early 70-ies and was considered a "compact" two-door car.
However, especially before the oil crisis of 1973, the American notion of "compactness" was significantly different from European, so the dimensions of "Ford Falcon" close to the Volga, and not to the "Zaporozhets". And although it should be noted that his engine compartment was possessed of a considerable size, it is unlikely that the engine length exceeded 90 cm, height 70 cm, width — 50 cm, and given the small weight it is possible to assume and a much more compact size. However, the machine depicted on the very famous fuzzy photos, features home-made body, and its size sufficiently densely filled (sorry, what exactly — hard to understand) of the engine compartment close to the specified (as a point of reference for sizing you can use the Richard Clem standing next to the car).
And, of course, be very carefully to treat a possible prototype of the engine was found by Robert Kunz — conical pump for viscous fluids.
Strange descriptionWhen reading the article, you may notice a few features, some of which at first glance seem strange, at least compared to regular automobile engines, and others — at least illogical or even fantastic. However, the analysis of such moments and can provide the key to understanding the operation of the engine. Will list the ones that noticed me.
Unusually small for the declared capacity weight, even if we assume that is dry weight without oil charge (30 liters of oil weigh about 25 kg, and if this mass — working, the share of iron will do no more than 65 kg) and an unusually high ratio of "filling" (about 30 liters) of the weight of the engine (90 kg). For comparison, typically in an automobile engine with a dry weight of about 100 kg is filled with about 4 litres of engine oil and 7-9 liters of coolant (water, antifreeze, etc.). The relatively high operating temperature (150°C). That is not allowed, if required to limit ordinary for automotive cooling systems 80-90°C? Indeed, in this case it would be possible to use standard automotive thermostats and other parts of the cooling system to maintain operating temperature, and as the working fluid could be used motor oil, and maybe even water. High (again according to automotive standards) the oil pressure at the inlet of the cone (20-35 atmospheres). For comparison, the working pressure in the oil system of the conventional engine is from 2 to 8 atmospheres, at high pressures achieved at high speed, opening of the relief valve discharging excess oil back and even reduce its pressure. Do all pump because of the centrifugal force and of themselves can create quite a decent pressure? The article clearly points to the fact that the spiral is not made of tubing, wound on a disc cone and is made in the form of a groove in the cone. But the option with the wound tube would be much easier and smarter, especially in the "garage" conditions of Clem. And even if there was a serious threat of rupture of the tube by centrifugal forces (recall that the speed of rotation, according to the article, do not exceed 2300 rpm), to protect against it is enough to use an external conical protective casing and even a simple counter-wound steel wire. However, the answer to this question is contained in the description of the pump of the prototype. By the way, why do we need the cone — after all, when considering centrifugal engines, we found that from the point of view of hydrodynamics there is no difference not only between the cone and flat coils, and between coils and straight tubes-"horns"? And if you take into account the viscosity of the fluid, the longer its path, the greater will be the friction losses on the walls! Yes, and in the manufacture of engine on my salary it is obvious that the flat spiral cheaper cone — not least because it is less material... by the Way, the photo of the engine Clem no blocks, according to their proportions even remotely similar to the taper on the drawings, including the drawing of pump prototype. In the diagram the heat exchanger placed before the pump, although from the point of view of more effective cooling it is more logical to place it after — after the compression of the working body experiences additional heating. However, this placement has a strong technical justification — improving the thermal operation of the pump, and most importantly, in the heat exchanger the working fluid is at a pressure close to atmospheric! The device for days (and even years) of continuously working in stationary conditions, when installed on the car, broke in less than 300 kilometers, while the failure lay in the fact that "bent the shaft and everything else".
Shaft design only one — the one on which the rotor spins. The cause of his fracture are obviously large load on the horizontal shaft due to gyroscopic effects in cornering and rocking it on the rough roads. The reason can also be twisting forces due to sharp load change — for example, when starting off, but this option is less likely. In addition, the force from the load function only on the other side of the shaft from which power is removed, and the curve of the gyroscopic effects on both of its ends. Probably the first design of the shaft was still horizontal, as in the pump prototype, and vertically the cone could be placed already in the improved model — one that the son of Clem buried on the farm (in my experience that usually about such things think only after something went wrong).
The use of gears instead of a chain drive is unlikely to be the main reason for this rapid breakdown. Indeed, the chain drive gives you not only the tangential (torsional) and normal (bending) stress on the shaft due to the need for chain tensioning, and the use of gears with the corresponding geometry of the teeth of the normal load on the shaft can be almost non-existent. But this factor operates in stationary conditions, and if his influence was great, he inevitably would have happened there.
Since the stated speed of rotation is quite small — about 2000 rpm, compared to about 3000-4000 rpm in conventional engines in "cruising" mode, the cause of the fatal bending of the shaft can only be a very large rotating mass, i.e. the mass of the rotor. Taking into account that the internal combustion engine on the crankshaft still rotates and the flywheel weighing several kilograms and with a diameter of 30 centimeters, with them, and nothing happens, I appreciate the work the weight of the rotor not less than 10 kg, but most likely it weighed more than 20..30 pounds. It is unlikely that Clem, the man is certainly a technically competent, did not understand the importance of reducing the rotating masses and made unduly weighted rotor or deliberately fragile shaft (center hole reduces the strength of the pipe is very low, even if the diameter of the hole will be 3/4 of the diameter of the shaft, its resistance to bending and twisting will be reduced by a quarter). So the question arises: why did Clem such a heavy rotor, especially in contrast to internal combustion engines the flywheel design is not necessary — apparently, it operates continuously and has no "dead spots"? And finally, the most fantastic looks of approval on the work for several years and the engine is under concrete on the three-meter depth, i.e., practically without heat exchange with the external environment. And the most surprising here is not the lack of visible energy source, and maintaining a heat balance. Hardly, hastily burying the engine in the farm, the son of Clem took care of setting up and launching out a powerful system of heat transfer! But if the engine somehow "sucks" heat from the external environment, it will quickly cool the surrounding closed space and simply "freeze" for several, if not minutes, hours. If the device receives energy in some other way (from nuclear processes, the torsion fields, "physical vacuum", etc.), and any substantial part of it is converted to parasitic heat, warming it (at least, this is the inevitable friction losses), the engine will overheat over all margins at about the same time (also a nuclear reactor can operate for years under water and under ground but without the constant intensive cooling it will quickly overheat and explode, as happened at Chernobyl).
Described is possible only in case if the thermal imbalance at idle does not exceed a hundred or two watts, that is, either design is a well balanced combination of heat pump and heat engine or internal energy loss due to friction and other costs are very small, and useless the heat is practically absent (compare the modes of operation at idle and under load from internal combustion engines and electric motors)! A few words about vegetable oilWhy Clem chose vegetable oil? While we do not know due to which engine gets the necessary energy, we can't say whether this optimal choice, and is it possible to improve engine efficiency by selecting as the working fluid is another matter. However, we can analyse the physical properties of vegetable oil and have them in mind, considering the possible principles of operation of this engine.
See what people are saying about the physical properties of vegetable oil cooking sites and forums, because at least some of the details I was able to find only there. Information is not a lot, but the main bit by bit to collect everything you can.
So, at atmospheric pressure the oil does not boil, at least in the classic sense of the word (that is not boiling and splashing do not, of course, if it does not get water from the dish, from food or from the hands of the cooks), but he has three other important temperature points: starting point of chemical decomposition and oxidation not accompanied by significant release of smoke (for many animal oils and fats a 140..160°C, for vegetable is normally 170..190°C), "point of smoke" — when the oil begins to oxidize and decompose with appreciable separation of the products of decomposition ("burning" in the culinary sense — for the vast majority of oils, both animal and vegetable, is 180..210°C), and finally "flash point" — when the overheated oil, remaining liquid, flashes in the open air (for almost all cooking oils, such ignition occurs in the range of 220..240°C).
However, is it true that oil does not boil? Actually this is not true: natural vegetable oil has not been subjected to refining and deep cleaning (and in the days of Clem in mass quantities and the other was not), is a mixture of many factions with different evaporation temperatures, the decomposition and outbreak. Some of them in minimal quantities evaporate already at room temperature, providing the scent of the product. Others begin to evaporate at temperatures around hundreds of degrees Celsius, although during the cooking process this process usually occurs unnoticed and appears only in nasty fatty plaque on the kitchen furniture and the ceiling, which begins to form especially active during intense frying, which corresponds to temperatures between 150°C and above. However, in these processes involved only a tiny fraction of the total amount of oil, and everything else is at atmospheric pressure continues to exist in the liquid state until the temperature of the "flare point".
It should be noted another important property of oil is its relatively high viscosity at room temperature, which decreases rapidly with increasing temperature and at temperatures above 100°C already begins to approach the viscosity of water. On the other hand, when the temperature of the oil does not go sharply into the crystal phase, and relatively smoothly velivet its viscosity until almost solid (but amorphous) state.
A sufficiently high viscosity oil in a cold condition leads to high friction losses when moving along the channels of the rotor and, respectively, causes a rapid heating of the cone, but then as you warm up the oil viscosity very strongly decreases, reducing fluid friction and impeding excessive overheating of the rotor at idle for this reason. An additional advantage of using a vegetable oil — to create an enabling environment for the operation of the parts of the engine to automatically provide lubrication and corrosion protection, although the use of special industrial oils, of course, more efficiently.
In addition, it should be noted that oil well moistens surfaces of most metals, including steel, copper and aluminum alloys, and therefore, the edge layers bordering the channel walls, can effectively engage these walls in the movement, and due to the high viscosity middle layers also willing to follow them.
Why Clem did not use motor or gear oil? Perhaps the fact that unlike the plant, they is a much more homogeneous substance, and they have a boiling temperature substantially above the temperature of decomposition and degradation.
In internal combustion engines and transmissions of high-evaporation oils, and especially boiling it, is very undesirable, so the developers of motor oils specifically trying to reduce the formation of steam throughout the operating temperature range up to 110..120°C. however, they do not involve long working life of the oil at temperatures above 100..110°C, because at temperatures above 110..120°C motor oil deteriorate quickly and lose their properties.
For culinary purposes a relatively high formation of oil vapors is not a limiting factor, and in some cases may even be desirable, but resistance to temperatures from 130..150°C (conventional roasting) to 180..200°C (frying in oil) is a fundamental requirement. Therefore, cooking oil motor is preferable in two cases — if you want the highest possible vaporization or if for some reason the operating temperature can be reduced at least 100°C.
If the engine klema "blame" cavitation with hydraulic shocks, the benefits of the oil before water is undeniable. The fact that the evaporation of water, especially in heated condition, is much higher than that of oil, even hot. As a result, the negative pressure inside the cavitation bubbles will be worse, and "collapse" them to be less sharp than in the case when the pair inside the bubble are virtually absent.
It should be noted that there are many other attempts to explain the operation of this engine. For example, it is necessary to familiarize with the opinion of V. S. Bukreev.
Other engine options klema"Classic" image is not the only design option — there is a version of the engine Clem with a vertical axis of rotation.
Vertical version of the Clem engine during operation (the URL of the original article and the translation of the terms into Russian language added by me).In this embodiment, not only the changed orientation of the axis of rotation, but there are more serious differences — for example, the pump is only used for system startup, and then the oil enters the hollow shaft and further into the cone a rotor-priming. This is a drawing of a noteworthy article by Robert Kunz about the probable prototype of the Clem engine — its Russian translation can be found on a separate page. However, it should be borne in mind that this design in reality, as far as I know Koontz has not been implemented, and the proposed method of regulating the engine speed seems to me to be technically insolvent.
However, there were attempts to make something like the Clem engine in the metal. Here is one of them (apparently domestic) — hydrophore generator "Garuda". Information about the efficiency of this design, I have not.
Another article about the engine, CIBC Jim ray appeared on the website keelynet.com in 2009
Finally, for completeness, we should say a few words about the other liquid structures, using rapid rotation of rotors, turbines or just fluid and supposedly capable of operating "by themselves". Perhaps some of them use the same principles as the engine Clem, but as the working fluid usually is water. Unfortunately, I've met ... online information about them is extremely fragmentary and vague, but you notice that when you start them usually requires a stage of acceleration and warm-up, often very long, and sometimes referred to constraints on minimum sizes. In particular, for water structures, the minimum diameter is usually specified 1..1.5 m (speed in this case is kept secret).
Engine Clem from the point of view of thermodynamicsSpeaking about the Clem engine, it is impossible to ignore thermodynamics and hydrodynamics. Immediately it should be emphasized one very important point. If to seek the cause of the work of the Clem engine in the framework of thermodynamics, heat engine klema's supposed to be cold and to heat the working fluid due to the thermal energy of the environment for this framework to take energy from nowhere else. However, all in one voice say that the heat exchanger was hot and served to cool.
In addition, to recover the heat from the external environment through thermodynamic processes — first of all the adiabatic expansion of a gas (vapor) phase and different heat change of the aggregate States in different conditions — it is necessary to use a working fluid with a good rate of evaporation, as is done in traditional heat pumps. Here inevitably arises the problem of maximum decrease of temperature of "dew point", which requires a very intensive destruction of the expanded cooled vapor from the region of evaporation. But Clem as the optimal working fluid was chosen almost nickipedia oil, rejecting water and other liquids with high evaporation. Therefore, it seems that in General the amount of energy he was not only necessary, but also harmful. In addition, we cannot exclude the possibility that the output channels of the cone was opened not in free space, as shown in the "classical" picture, and in a cell, densely filled with oil — this is another reason why the intense vaporization at the outlet nozzles can not be considered.
However, in this engine will definitely act and thermodynamic processes and compression of the working fluid, and heating it, and wypracowanie through nozzles with sudden pressure drop and cavitation is very likely the evaporation, at least partial. Therefore try to consider the Clem engine from the point of view of thermodynamics and hydrodynamics, and in any case such an analysis would not be amiss, and may show the points that you should pay particularly close attention. However, because at the moment, purely thermodynamic explanation of the operation of the Clem engine (of course, with the violation of the II law of thermodynamics) appear to be untrue, it is on a separate page, and thermodynamic processes have to be considered as playing a secondary role. published
P. S. And remember, only by changing their consumption — together we change the world! ©
Source: //khd2.narod.ru/clem/clem.htm
It should be noted that there are many designs that look like the Clem engine, for example, centrifugal engine Igor Vysotsky (he is its author, by the way, this also sure). In fact, these devices use completely different operating principles, and because of their deceptive similarity.
The technical detailsBefore you start considering engine Clem, "sort through" the available information. Below I excerpt from the "canonical" articles, which in varying degrees relate to the technical side of the device.
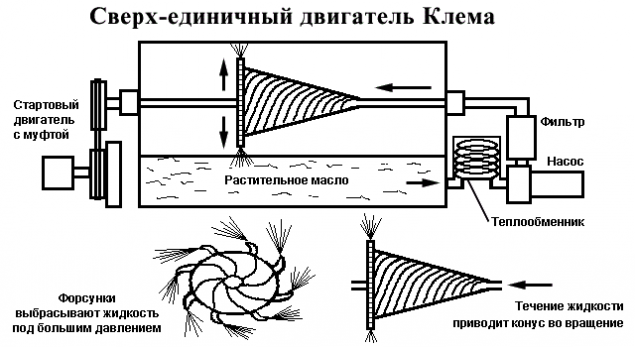
The "classic" image of the Clem engine. The picture was made under the resolution EGA (640x350), and therefore no correction on modern monitors it looks "flattened". The information in the articleso here's the technical part of the "canonical" articles (for American units of measure in parentheses are metric values, the translation closest to the English original, which substantially changed the description of some moments).
Richard Clem worked with heavy machinery in Dallas. He noticed that certain types of high pressure pumps continued to operate for some time after power has been cut. His curiosity about this phenomenon led to the invention of the motor.... Clem says that... the drivers would only change the eight gallons (about 30 liters) of vegetable oil every 150 thousand miles and never buy any gasoline.The engine weighs about 200 pounds (about 90 kg) and contains vegetable oil at a temperature of 300°F (150°C).Clem said that the used vegetable oil because his motor runs at... the temperature at which water boils and conventional engine oil breaks down. Although he would not disclose details of the device of the engine, its the only additional energy source is a 12-volt battery.It consists of a cone mounted on a horizontal axis. The shaft holding the cone, hollow inside, and the cone has cut therein helical channels. These helical paths along the cone and ending at its base in the form of nozzles (injectors).Liquid is injected into the hollow shaft at pressures in the range 300-500 psig (21-35 kg/cm2), passes through a close spiral channels of the cone and exits through the nozzle. This causes the cone to rotate. The greater the fluid velocity, the faster the rotation of the cone.With increasing speed, fluid is heated, and therefore requires the heat exchanger and the filter. At a certain speed cone begins self-rotation, independent from the engine. The rotation speed of the shaft reaches 1800-2300 rpm.... the motor was tested by Bendix Corporation. The test consisted of attaching the engine to the dynamometer to measure the power on the shaft.The measurements showed that the engine is steadily producing 350 horsepower for 9 days so impressed the engineers at Bendix. They came to the conclusion that the source that could generate all the energy in a CLOSED SYSTEM for such a long time, can only be nuclear.The engine design does not contain non-traditional items, with the exception of the cone with spiral channels and the hollow shaft.When Clem built the first oil engine in 1972, he made a trial trip length of 600 miles (about 1000 km) to El Paso on the motor, which he did on his salary. Before all the shafts and everything bent, he managed to only drive up to Abilene (Google Maps shows the distance along the highway between Dallas and Abilene is 172 miles or 276 km).He explained the failure to the imperfection of the design, too small size of the shaft and using chains instead of gears.Immediately after the inventor was struck by a heart attack and papers were seized, son of the inventor sent the only working model of a machine to a farm near Dallas. There he buried it under 10 feet (3 m) of concrete, and she continued to work at this depth for several years.Here, in General, and all the information Dating back to 1992 — 20 years after the death of the inventor of a heart attack in the same 1972. Later it became known some additional data are as follows.The pump is used as the prototype engine was used for spraying hot, liquid asphalt. The cone was mounted vertically. The heat exchanger was used for cooling. Finally, the latest information about the Clem engine is not mentioned on the cone, but speaks of "seven-pump" and "LNB", "operating like a turbine", and in the photo of the engine showing something similar to the turbine wheel and can not see anything similar on the cone (unless it's hidden inside the "turbines"). The photographs of the car clearly visible two different versions of the engine with longitudinal and transverse orientation of the shaft, but neither one of them have a hint of vertical installation of the cone.
Frankly, the data is not too much — for example, the precise dimensions of the device (this would allow to evaluate the possible diameter of the cone and the resulting centrifugal forces), although given its weight. However, I think that there is quite a lot to try to understand this unusual motor. As for the size of the engine, they may be indirectly evaluated on the basis of the fact that it was placed on the car, apparently, instead of "regular" motor, as the base of the car refers to "Ford Falcon". This model was produced from 1960 until the early 70-ies and was considered a "compact" two-door car.
However, especially before the oil crisis of 1973, the American notion of "compactness" was significantly different from European, so the dimensions of "Ford Falcon" close to the Volga, and not to the "Zaporozhets". And although it should be noted that his engine compartment was possessed of a considerable size, it is unlikely that the engine length exceeded 90 cm, height 70 cm, width — 50 cm, and given the small weight it is possible to assume and a much more compact size. However, the machine depicted on the very famous fuzzy photos, features home-made body, and its size sufficiently densely filled (sorry, what exactly — hard to understand) of the engine compartment close to the specified (as a point of reference for sizing you can use the Richard Clem standing next to the car).
And, of course, be very carefully to treat a possible prototype of the engine was found by Robert Kunz — conical pump for viscous fluids.
Strange descriptionWhen reading the article, you may notice a few features, some of which at first glance seem strange, at least compared to regular automobile engines, and others — at least illogical or even fantastic. However, the analysis of such moments and can provide the key to understanding the operation of the engine. Will list the ones that noticed me.
Unusually small for the declared capacity weight, even if we assume that is dry weight without oil charge (30 liters of oil weigh about 25 kg, and if this mass — working, the share of iron will do no more than 65 kg) and an unusually high ratio of "filling" (about 30 liters) of the weight of the engine (90 kg). For comparison, typically in an automobile engine with a dry weight of about 100 kg is filled with about 4 litres of engine oil and 7-9 liters of coolant (water, antifreeze, etc.). The relatively high operating temperature (150°C). That is not allowed, if required to limit ordinary for automotive cooling systems 80-90°C? Indeed, in this case it would be possible to use standard automotive thermostats and other parts of the cooling system to maintain operating temperature, and as the working fluid could be used motor oil, and maybe even water. High (again according to automotive standards) the oil pressure at the inlet of the cone (20-35 atmospheres). For comparison, the working pressure in the oil system of the conventional engine is from 2 to 8 atmospheres, at high pressures achieved at high speed, opening of the relief valve discharging excess oil back and even reduce its pressure. Do all pump because of the centrifugal force and of themselves can create quite a decent pressure? The article clearly points to the fact that the spiral is not made of tubing, wound on a disc cone and is made in the form of a groove in the cone. But the option with the wound tube would be much easier and smarter, especially in the "garage" conditions of Clem. And even if there was a serious threat of rupture of the tube by centrifugal forces (recall that the speed of rotation, according to the article, do not exceed 2300 rpm), to protect against it is enough to use an external conical protective casing and even a simple counter-wound steel wire. However, the answer to this question is contained in the description of the pump of the prototype. By the way, why do we need the cone — after all, when considering centrifugal engines, we found that from the point of view of hydrodynamics there is no difference not only between the cone and flat coils, and between coils and straight tubes-"horns"? And if you take into account the viscosity of the fluid, the longer its path, the greater will be the friction losses on the walls! Yes, and in the manufacture of engine on my salary it is obvious that the flat spiral cheaper cone — not least because it is less material... by the Way, the photo of the engine Clem no blocks, according to their proportions even remotely similar to the taper on the drawings, including the drawing of pump prototype. In the diagram the heat exchanger placed before the pump, although from the point of view of more effective cooling it is more logical to place it after — after the compression of the working body experiences additional heating. However, this placement has a strong technical justification — improving the thermal operation of the pump, and most importantly, in the heat exchanger the working fluid is at a pressure close to atmospheric! The device for days (and even years) of continuously working in stationary conditions, when installed on the car, broke in less than 300 kilometers, while the failure lay in the fact that "bent the shaft and everything else".
Shaft design only one — the one on which the rotor spins. The cause of his fracture are obviously large load on the horizontal shaft due to gyroscopic effects in cornering and rocking it on the rough roads. The reason can also be twisting forces due to sharp load change — for example, when starting off, but this option is less likely. In addition, the force from the load function only on the other side of the shaft from which power is removed, and the curve of the gyroscopic effects on both of its ends. Probably the first design of the shaft was still horizontal, as in the pump prototype, and vertically the cone could be placed already in the improved model — one that the son of Clem buried on the farm (in my experience that usually about such things think only after something went wrong).
The use of gears instead of a chain drive is unlikely to be the main reason for this rapid breakdown. Indeed, the chain drive gives you not only the tangential (torsional) and normal (bending) stress on the shaft due to the need for chain tensioning, and the use of gears with the corresponding geometry of the teeth of the normal load on the shaft can be almost non-existent. But this factor operates in stationary conditions, and if his influence was great, he inevitably would have happened there.
Since the stated speed of rotation is quite small — about 2000 rpm, compared to about 3000-4000 rpm in conventional engines in "cruising" mode, the cause of the fatal bending of the shaft can only be a very large rotating mass, i.e. the mass of the rotor. Taking into account that the internal combustion engine on the crankshaft still rotates and the flywheel weighing several kilograms and with a diameter of 30 centimeters, with them, and nothing happens, I appreciate the work the weight of the rotor not less than 10 kg, but most likely it weighed more than 20..30 pounds. It is unlikely that Clem, the man is certainly a technically competent, did not understand the importance of reducing the rotating masses and made unduly weighted rotor or deliberately fragile shaft (center hole reduces the strength of the pipe is very low, even if the diameter of the hole will be 3/4 of the diameter of the shaft, its resistance to bending and twisting will be reduced by a quarter). So the question arises: why did Clem such a heavy rotor, especially in contrast to internal combustion engines the flywheel design is not necessary — apparently, it operates continuously and has no "dead spots"? And finally, the most fantastic looks of approval on the work for several years and the engine is under concrete on the three-meter depth, i.e., practically without heat exchange with the external environment. And the most surprising here is not the lack of visible energy source, and maintaining a heat balance. Hardly, hastily burying the engine in the farm, the son of Clem took care of setting up and launching out a powerful system of heat transfer! But if the engine somehow "sucks" heat from the external environment, it will quickly cool the surrounding closed space and simply "freeze" for several, if not minutes, hours. If the device receives energy in some other way (from nuclear processes, the torsion fields, "physical vacuum", etc.), and any substantial part of it is converted to parasitic heat, warming it (at least, this is the inevitable friction losses), the engine will overheat over all margins at about the same time (also a nuclear reactor can operate for years under water and under ground but without the constant intensive cooling it will quickly overheat and explode, as happened at Chernobyl).
Described is possible only in case if the thermal imbalance at idle does not exceed a hundred or two watts, that is, either design is a well balanced combination of heat pump and heat engine or internal energy loss due to friction and other costs are very small, and useless the heat is practically absent (compare the modes of operation at idle and under load from internal combustion engines and electric motors)! A few words about vegetable oilWhy Clem chose vegetable oil? While we do not know due to which engine gets the necessary energy, we can't say whether this optimal choice, and is it possible to improve engine efficiency by selecting as the working fluid is another matter. However, we can analyse the physical properties of vegetable oil and have them in mind, considering the possible principles of operation of this engine.
See what people are saying about the physical properties of vegetable oil cooking sites and forums, because at least some of the details I was able to find only there. Information is not a lot, but the main bit by bit to collect everything you can.
So, at atmospheric pressure the oil does not boil, at least in the classic sense of the word (that is not boiling and splashing do not, of course, if it does not get water from the dish, from food or from the hands of the cooks), but he has three other important temperature points: starting point of chemical decomposition and oxidation not accompanied by significant release of smoke (for many animal oils and fats a 140..160°C, for vegetable is normally 170..190°C), "point of smoke" — when the oil begins to oxidize and decompose with appreciable separation of the products of decomposition ("burning" in the culinary sense — for the vast majority of oils, both animal and vegetable, is 180..210°C), and finally "flash point" — when the overheated oil, remaining liquid, flashes in the open air (for almost all cooking oils, such ignition occurs in the range of 220..240°C).
However, is it true that oil does not boil? Actually this is not true: natural vegetable oil has not been subjected to refining and deep cleaning (and in the days of Clem in mass quantities and the other was not), is a mixture of many factions with different evaporation temperatures, the decomposition and outbreak. Some of them in minimal quantities evaporate already at room temperature, providing the scent of the product. Others begin to evaporate at temperatures around hundreds of degrees Celsius, although during the cooking process this process usually occurs unnoticed and appears only in nasty fatty plaque on the kitchen furniture and the ceiling, which begins to form especially active during intense frying, which corresponds to temperatures between 150°C and above. However, in these processes involved only a tiny fraction of the total amount of oil, and everything else is at atmospheric pressure continues to exist in the liquid state until the temperature of the "flare point".
It should be noted another important property of oil is its relatively high viscosity at room temperature, which decreases rapidly with increasing temperature and at temperatures above 100°C already begins to approach the viscosity of water. On the other hand, when the temperature of the oil does not go sharply into the crystal phase, and relatively smoothly velivet its viscosity until almost solid (but amorphous) state.
A sufficiently high viscosity oil in a cold condition leads to high friction losses when moving along the channels of the rotor and, respectively, causes a rapid heating of the cone, but then as you warm up the oil viscosity very strongly decreases, reducing fluid friction and impeding excessive overheating of the rotor at idle for this reason. An additional advantage of using a vegetable oil — to create an enabling environment for the operation of the parts of the engine to automatically provide lubrication and corrosion protection, although the use of special industrial oils, of course, more efficiently.
In addition, it should be noted that oil well moistens surfaces of most metals, including steel, copper and aluminum alloys, and therefore, the edge layers bordering the channel walls, can effectively engage these walls in the movement, and due to the high viscosity middle layers also willing to follow them.
Why Clem did not use motor or gear oil? Perhaps the fact that unlike the plant, they is a much more homogeneous substance, and they have a boiling temperature substantially above the temperature of decomposition and degradation.
In internal combustion engines and transmissions of high-evaporation oils, and especially boiling it, is very undesirable, so the developers of motor oils specifically trying to reduce the formation of steam throughout the operating temperature range up to 110..120°C. however, they do not involve long working life of the oil at temperatures above 100..110°C, because at temperatures above 110..120°C motor oil deteriorate quickly and lose their properties.
For culinary purposes a relatively high formation of oil vapors is not a limiting factor, and in some cases may even be desirable, but resistance to temperatures from 130..150°C (conventional roasting) to 180..200°C (frying in oil) is a fundamental requirement. Therefore, cooking oil motor is preferable in two cases — if you want the highest possible vaporization or if for some reason the operating temperature can be reduced at least 100°C.
If the engine klema "blame" cavitation with hydraulic shocks, the benefits of the oil before water is undeniable. The fact that the evaporation of water, especially in heated condition, is much higher than that of oil, even hot. As a result, the negative pressure inside the cavitation bubbles will be worse, and "collapse" them to be less sharp than in the case when the pair inside the bubble are virtually absent.
It should be noted that there are many other attempts to explain the operation of this engine. For example, it is necessary to familiarize with the opinion of V. S. Bukreev.
Other engine options klema"Classic" image is not the only design option — there is a version of the engine Clem with a vertical axis of rotation.
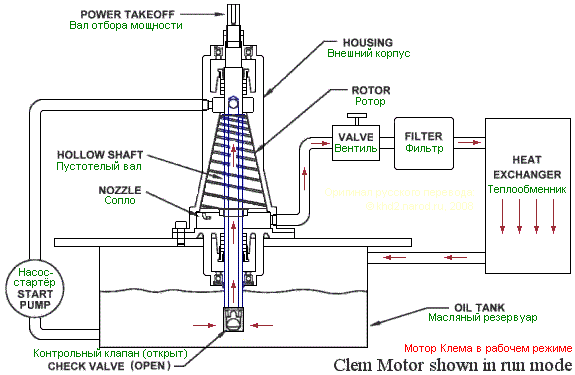
Vertical version of the Clem engine during operation (the URL of the original article and the translation of the terms into Russian language added by me).In this embodiment, not only the changed orientation of the axis of rotation, but there are more serious differences — for example, the pump is only used for system startup, and then the oil enters the hollow shaft and further into the cone a rotor-priming. This is a drawing of a noteworthy article by Robert Kunz about the probable prototype of the Clem engine — its Russian translation can be found on a separate page. However, it should be borne in mind that this design in reality, as far as I know Koontz has not been implemented, and the proposed method of regulating the engine speed seems to me to be technically insolvent.
However, there were attempts to make something like the Clem engine in the metal. Here is one of them (apparently domestic) — hydrophore generator "Garuda". Information about the efficiency of this design, I have not.
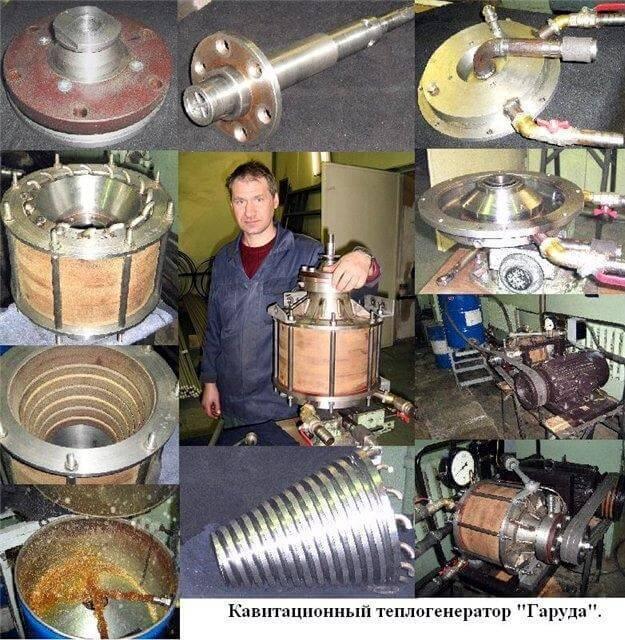
Another article about the engine, CIBC Jim ray appeared on the website keelynet.com in 2009
Finally, for completeness, we should say a few words about the other liquid structures, using rapid rotation of rotors, turbines or just fluid and supposedly capable of operating "by themselves". Perhaps some of them use the same principles as the engine Clem, but as the working fluid usually is water. Unfortunately, I've met ... online information about them is extremely fragmentary and vague, but you notice that when you start them usually requires a stage of acceleration and warm-up, often very long, and sometimes referred to constraints on minimum sizes. In particular, for water structures, the minimum diameter is usually specified 1..1.5 m (speed in this case is kept secret).
Engine Clem from the point of view of thermodynamicsSpeaking about the Clem engine, it is impossible to ignore thermodynamics and hydrodynamics. Immediately it should be emphasized one very important point. If to seek the cause of the work of the Clem engine in the framework of thermodynamics, heat engine klema's supposed to be cold and to heat the working fluid due to the thermal energy of the environment for this framework to take energy from nowhere else. However, all in one voice say that the heat exchanger was hot and served to cool.
In addition, to recover the heat from the external environment through thermodynamic processes — first of all the adiabatic expansion of a gas (vapor) phase and different heat change of the aggregate States in different conditions — it is necessary to use a working fluid with a good rate of evaporation, as is done in traditional heat pumps. Here inevitably arises the problem of maximum decrease of temperature of "dew point", which requires a very intensive destruction of the expanded cooled vapor from the region of evaporation. But Clem as the optimal working fluid was chosen almost nickipedia oil, rejecting water and other liquids with high evaporation. Therefore, it seems that in General the amount of energy he was not only necessary, but also harmful. In addition, we cannot exclude the possibility that the output channels of the cone was opened not in free space, as shown in the "classical" picture, and in a cell, densely filled with oil — this is another reason why the intense vaporization at the outlet nozzles can not be considered.
However, in this engine will definitely act and thermodynamic processes and compression of the working fluid, and heating it, and wypracowanie through nozzles with sudden pressure drop and cavitation is very likely the evaporation, at least partial. Therefore try to consider the Clem engine from the point of view of thermodynamics and hydrodynamics, and in any case such an analysis would not be amiss, and may show the points that you should pay particularly close attention. However, because at the moment, purely thermodynamic explanation of the operation of the Clem engine (of course, with the violation of the II law of thermodynamics) appear to be untrue, it is on a separate page, and thermodynamic processes have to be considered as playing a secondary role. published
P. S. And remember, only by changing their consumption — together we change the world! ©
Source: //khd2.narod.ru/clem/clem.htm
There are things that do not catch up, however quickly fled
How to plaster walls: tips for the beginner