711
Expensive exotics or low-cost "perpetuum mobile"?
Alloys with shape memory effect
Soviet metallurgists G. V. Kurdyumov and L. G. Henderson in 1948 suggested alloy, is endowed with the ability after a significant plastic deformation to restore its original shape when heated to a certain temperature. In 1980 this invention was recognized by the opening and became known as the Kurdyumov effect (effect of restoration of a given configuration or shape memory effect).
This effect is practically reproduced in the following way. The pre-billet of an alloy, e.g. the wire, attach required form. Then it is heated and cooled. After which it straighten. Upon subsequent heating, the wire will take its original configuration.
The mechanism of this phenomenon is not entirely clear. Martensitic reactions are reversible. During heating of the sample, they go in one direction, while cooling the opposite. Occurring during martensitic transformations and physical processes are so complex that experts say "the genetic properties of crystals". Despite the incomplete clarity of the physical mechanism of this phenomenon, it is part of our practical life.
In 1958, was first obtained alloy with effect of shape memory is nitinol. Nitinol is an alloy of Nickel and titanium. It is quite difficult to produce. To achieve the desired transition temperature, the ratio of Nickel and titanium in the alloy must be maintained with high accuracy. This alloy has the phase transitions are above room temperature but below the boiling point of water. If titanium nickelide it possible to dope the iron, the temperature range extends in the range from ambient to the boiling point of liquid nitrogen. The necessary purity of production is ensured through the use of complex vacuum furnaces and auxiliary equipment. Therefore, the widespread use of nitinol is limited by its high cost, and sometimes the inertia of our thinking. But finding ways of reducing the cost of production of nitinol continues. And some firms, for example, "Special metals Corporation" (USA), intend to begin commercial production of nitinol with acceptable commercial value...
The most common applications of nitinol today
In addition to the propulsion, built in the late XX century American banks, others, really embodied in metal "industrial propellers" on the basis of the nitinol actuator in the world press is not marked. Experts know enough of the references (more than 1000 according to various sources) on the patenting of various models of nitinol actuators and propulsion, but the invention is not moved further patent applications.
Robotics stepped a little further using the micron nitinol filaments as electronic muscles. Often, as always, surprised the Japanese. While passing through the nitinol filament weak currents, muscles developing efforts, hundreds of times greater than human.
As auxiliary applications, nitinol is used in a wide range of devices, the designs of which suggest movement caused by heat. So, for example, nitinol is used in devices for fire protection, used for sealing joints in aircraft, submarines and prevent radiation leaks at nuclear power plants. The connections of pipes made from alloys with shape memory effect, with the respective dimensions of the walls, and coupling with a body thickness of only 2 mm can withstand high pressure (in the range of hundreds of atmospheres).
Not far behind from the process industry and space industry. It has developed a "self-extracting" compact antenna, originally on earth, Packed tightly for easy transportation into outer space.
Broad use of nitinol has received and in the medical industry. Today around the world have become well-known bracket systems, used to align the altered occlusion in dentistry. Developed a unique stent for vascular surgery, able to withstand 10 to 20 million cycles "compression-expansion" under the regulations of American FDA and various orthopedic devices, with a dosage correcting load on the affected bone.
The potential application of nitinol
The Electromechanical regulator of the clearance of the car
The problem of the emergency levelling of the car is spread everywhere in the world, in cases when it is necessary to overcome the "difficult" road journey of several kilometers (commuter, road, blurred by rain, for example) and return the height of the clearance "at the same place." Solution pneumatic lifts there, but complaints of their operational fragility also abound. In the alternative, Pneumatics, various companies offer a strut with a mechanical method of lifting (thread nut), but here there is a lot BUT including the same level of rise at uneven wear and tear on the shock towers front and rear, the need to provide access to the nut, by removing the wheels... and manicure, finally.
A solution with a coil of nitinol may be available to any mechanic-welder. Given the episodic nature of the operation of this actuator, the design will last as long as it will last and dampers to replace them. Management in this case, there is a button from the cabin, and the response time is less than 1 min.
Design of household lamps
This patent is based on the international search, which is not found analogues of the use of technology "dual-memory Nickel-titanium alloys" in relation to systems of household lighting.
Attempts to create a ceiling, using the energy of the heating lamps to be deformed decorative elements (petals) have not received serious attention from customers — the manufacturers due to some limitations of the effects (the lamp warms only in the immediate vicinity). In this patent used a different heating principle, special heaters and cost effective heat cables. This approach to the design of the fixture creates an opportunity for wider production sources and directional light flush mount. Light sources that "appear" only when needed (application is medical lighting, automobiles, interior minimalist design, bathrooms, emergency lighting etc.). Considering the frequency of use of these devices (not more than 1-3 times a day), it is possible to provide continuous operation of the nitinol tubes that are running at the limit of the permissible norms of martensitic transformations, without substantially compromising efficiency of the structure (10,000 cycles in 10 years).
The effectiveness of "nitinol actuators"
The high performance of the various actuators made of Nickel-titanium alloys proved a number of major research institutions that studies the processes of the martensitic transformations in various versions of these alloys for over 30 years. For example, according to the conclusions of scientists from the Japanese company Furukawa, adding to the alloy of a minor amount of copper (6%) allows to increase the "useful working stroke of the actuator" up to 30 percent or more. This feature of the Nickel-titanium-copper alloy is now being promoted in robotics. How under this regime reversible deformation — time will tell.
Most professionals from different countries United in the opinion that the plate of titanium-Nickel alloys with an area of 6 cm2 is able to reach the stress with the martensitic-austenitic transformations to 27 tons or, according to some Russian sources, up to 55 tons per square inch of cross section of a part.
Nitinol and electricity
This work of Russian inventors, in my opinion, deserves close attention because of illustrates available to comprehend the process and leads to reflection on the evidence of the use of nitinol as a high performance Electromechanical actuator for generation of electricity. Why electricity? Because the energy spent on heating of metal products, palm-sized dimensions, and the potential work produced by this product after heating are not comparable, even in the case when the rod is heated by an electric source with a power of 5 kW. Moreover, the assurance of a respected state organization FDA (Food and Drug Administration controls in the US quality of food and medical devices), the process of heating-cooling without significant residual strain may last for several million cycles.
Try to start to evaluate the stress at 26.5 tons, in terms of the standard quantities used for the calculations of the various "rotational" structures.
From help:
Kilogram-force (kgf, kgf) is equal to the force that tell the body weight of one kilogram, the acceleration 9,80665 m/S2 (standard acceleration of free fall).
1 KP = 9.80665 Newtons (exactly) ~ 10 N
1 tonf (ton-force) = 103 kg = 9806,65 N
Therefore, in mm2, of Nitinol under strain, according to the authors-developers of the developing shear force is 600 Newtons!
Rod-actuator invented the scissors, when the claimed 26.5 tons generated efforts, develops a little more than 260 000 Newtons.
A lot or a little?
Consider low-speed wind turbine. Suppose that we would like to place in the basement of his house, as a stand-alone "producer" of electricity. Slow speed means no loss in efficiency of power generation, this generator can use the speed of rotation of the rotor shaft from 100 to 600 rpm, instead of 1 500 and 3 000 rpm as the conventional liquid fuel generators. Less speed — less effort spent on the development of this speed. On conviction the developers, the designs on permanent magnets operate up to 20 years or more without replacing parts.
The "home" model 12 kW (made in England-China):
the effective rotor speed 140 rpm;
mass 359 kg;
rotor inertia 1.59 kg m2;
material magnets NdFeB (rare earth neodymium);
a torque of 800 N m.
Of all the introductory specification we are interested in the last one — torque. The moment has the units Newton-meter (N·m).
1 N·m moment of force equal to 1 N, relative to the point located at a distance of 1 m from the line of action of the force.
Let the radius of the "flywheel" of our theoretical torque generator rotor actuator made of nitinol, is 1.2 m. Forces in Newtons, it would seem, abound. But not so simple in the organization of the transfer of translational motion into rotational energy. The point of application of force is unlikely to serve as the periphery of the flywheel, effort will be focused near the center. Assume that the diameter of the axle, where the main applied stress of 50 mm. Therefore, we need to multiply the total force generated by the rod-actuator for a short shoulder radius of the axis — 25mm.
Multiply 260 000 N x 0.015 m = 6 500 N·m.
So produced nitinol rod force, organizing the torque of the rotor is eight times greater than the force required to rotate the generator 12 kW. So a preliminary answer to the question — a lot or a little? That's a lot.
So we do not need.
According to the specification of those British manufacturers, straymouse moment for 30 kW tion of the generator is equal to 31 N·m, and operating torque of the order of 2 500 N·m...
Let us now try to transform the "wonderful power" short movement of the actuator in a smooth, continuous rotation of the rotor of the generator capacity of 30 kW and in the process to understand "what is the cost of heating" nitinol actuator?
It will be only a concept generator with a nitinol actuator, which are based on quite disparate, shared data (including mechanical shear, of course). Therefore, some excessive assumptions and technical inaccuracies I would like to pre-apologize.
We need to:
Nitinol impulse Electromechanical actuator
From the technical description of a hollow nitinol rod thermomechanical shear we recall that the dimensions of the actuator were as follows:
the rod length is 15 cm;
diameter — 4 cm x 2 cm.
Reduce the diameter of the rod in half, so as to cut the metal, we will not, and budge 26.5 tons, in everyday application, no special meaning. The actuator runs in a replaceable cartridge, for easy self-replacement after triggering a certain number of cycles (the diagram below shows a conventionally) once in 20-30 years when the cyclical heating of, say, 5 min. (the Number of cycles in 30 years will be 6 million if round-the-clock operation from 10 million guaranteed many foreign producers).
On the rate of heating and the estimated current is can be judged only indirectly. Direct data we have. There is only a short paragraph, the authors of scissors: "Due to the low temperatures needed for heating the core, the energy source can be, for example, a rechargeable battery, a low-voltage grid, the throttled compressed air, any associated heat exhaust".
The heat capacity of water is 4 200 j, the heat capacity of titanium nickelide only 490 George. But touch base...
Let the estimated capacity of our heating element-spiral, inside reduced nitinol actuator-plate is 5 kW (the power of a standard electric kettle 2 kW and 1 liter of water boil it for 3 min).
We know that the regime of heating and cooling the nitinol actuator +65..+40 - +25°C. And, according to inventors, "... at all temperatures above 40°C it generates stress on unit area of its cross-section equal to 60 kgf/mm2". We do not need to "boil" the body, heating it from 20 to 100°C. moreover, the alloy, in our case, we can not cooling, but only to reduce its temperature to a critical point of the transition martensite-austenite 35-38°C, spraying a refrigerant drip. In this case, the temperature interval of transformations to the point of transition will be even smaller, of the order of 10-15°C. In the engine Banks temperature range was 24°C.
Therefore, we can with a certain degree of confidence to assume that well-organized convection heater will allow you to enter the estimated parameters from 45 seconds to 1 minute. Sparing mode of operation, so to speak. But nevertheless, please be extra time (+2 min), just in case... 5-kilowatt source will heat our actuator 3 min(!) 20-30°C.
Now try to "draw" a stand-alone installation for the production of electricity, placing it aboard average three-storey house with a living area of 300 m2. In the harsh Russian winter home will require at least 0.7-1 kW per 10 m2 of living space. In the end, 21-30 kW to 300 m2.
Let's start with the transformer. It all the power! Here, one might recall the experiments of Pascal with a 4-meter pipe and "torn from the pressure of the water is wide".
Increase the diameter of the pipe at random and hoisted her in the basement like this:
Experience suggests that if the bottom of the tank from the pressure will not fall through the floor, then the piston will assume all the energy Paskaleva pipe, and the situation after heating and cooling the actuator made of nitinol (due to gravity) will look something like this:
Let's stop on this construction of "transformer multiplier" short the efforts of actuator long stroke...
Next to start the process of energy production we will need a launcher standalone heating unit (on the circuit it is not shown). The standard solution for such a case are 2 monocrystalline solar panels 2 x 240 watts mounted on the roof of the house (1800 x 1000 mm each). Will need the usual
Monocrystalline solar panel 240 watts (46, 5.2 A).
Yes, actually, and all... as the batteries we need only occasionally, when starting, charging is a long process and planned (at idle the generator). The sun ever so look out and charge. When running, alternator charging is similar to charging a car battery. Therefore in details to stop on this block will not. There are start-up current and all... As a given...
Now proceed to "build" all together.
Schematic diagram of nitinol-hydraulic-spring-flywheel drive shaft rotation will generatorsof rollicking... actually the drive is quite simple:
Of course, many of the units are shown only schematically (configuration of the actuator, the spiral, the heating element can be successfully replaced by highly efficient direct heating with a supply voltage of 400V and a power of 5 kW, or an infrared heating quartz with high-strength casing, etc.).
But the essence of the plant as a whole reflects, I believe, clearly. Confuses a lot of press, but instead of expensive metal as weighting can be used the filling the sand.
In this case, we are "not confused" short stroke actuator with a reversible strain of 7% — 20% (20% statement of Russian inventors). 7% good. And 20% is even better. In the scheme we have hydraulic press-animator is powerful, but short efforts nitinol actuator that is converted into rotational energy of the shaft of the generator. That is, when the hydraulic press is created win in the force is equal to the ratio of the area of the larger piston to the smaller area. A small compressibility of the fluid provides a practical equality of volumes of liquid passing from the large cylinder into the small.
The area of the small cylinder of 10 cm2. Press dimensions 70 cm x 30 cm according to this ratio, we can win in strength hundreds of times and push into the lumen of the "trunk" of a small cylinder a little less than a liter of fluid.
The cooling system is arranged on the actuator due to the pressure presses on the liquid in the capillary channels inside the package when it is lowered.
Set in the basement of our low speed generator 30 kW.
Mounted the flywheel drive energy nitinol-hydraulic actuator. The hollow disk flywheel has one important feature, it contains within its casing extra battery — spring energy storage.
Now try to imagine what will happen when a powerful but short the effort of the actuator.
Activate the heat. Raise a plate of mass 3 tonnes for 1.5 cm. turn Off heat. Plate starts to fall self-independent, the force of gravity to pressure fluid and to return the actuator to its original starting position. Simultaneously, the press, in its motion down and still cools the actuator.
The motion of the small piston to the left by fluid pressure, gear rack linearly transmits all the energy of the increased fluid pressure of the toothed wheel seated on the axle of the flywheel through a freewheel.
The overrunning clutch engages with the axle and, in turn, transmits the energy of the translational motion of the turns of the elastic springs of the flywheel. In the reverse movement of the overrunning clutch allows the gear rack actuator to move freely without load.
Flywheel mass of 350 kg At the end of the translational movement of the actuator, we transferred a large part of the energy to the flywheel, turning it into a stored elastic force of the spring, the remaining part is consumed on the associated costs of any mechanical transformation. The process is started. As a result, we have a cocked spring of a flywheel and a potential energy of rotation 350-pound steel disk with a radius of 60 cm Flywheel strahovatsya and smoothly begins to rotate, gaining kinetic energy, which will significantly help us in subsequent cycles. In this case, the elastic force in the compressed spring is distributed in such a way that the formula that calculates the radius of application of the main efforts... no longer works. Spring tends to spin the flywheel at the same time over the entire area of the hollow disk, from heavy rim and up to the point of application of force at the radius of the sprocket.
During this period, our actuator can easily regain their strength for the next "breakthrough". Plate, using the forces of gravity and pushed up the coolant will pull it into launch position without excessive pressure, dropping his weight at the end of the movement in special fixtures.
The actuator is resting, and the energy stored in the spring accumulator is gradually released and converted into kinetic energy.
What we have in the end?
Obviously, having after heating the actuator force 3 ton-forces down the slab, is applied through the hydraulics to the hard unstressed spring flywheel for 2 min, we accumulate a tremendous amount of energy to rotate the generator rotor. In the case where the diameter of the sprocket axis equal to 100 mm, and the radius of the applied force, respectively 50 mm, we have roughly 1 500 N·m of torque for our generator. Spring not only creates a reserve for smooth maintaining the torque on those 3 min that are required for the next heating cycle of the actuator (exactly how many depends on the number of turns of the spring and its elasticity), but also increases torque by half due to the redistribution of the point of application of the main efforts.
If we assume that the point of application of force of the combined drive of rotation removed from the center axis 100 mm (which is technically feasible), the torque is 30 000 N x 0.1 m = 3 000 N·m. (plus the elasticity of the springs at the periphery of the flywheel).
When we consider all losses due to friction and other imperfections, depriving the par-3 000 Nm, conventionally, 15%, we will still be 2 550 Nm for belief in the efficiency of the design capacity of 30 kW, so as to overcome the resistance of the magnets of the rotor, we need only 2 300 to 2 500 Nm. The generated electricity will be distributed as follows:
25 kW may be demanded by the consumer; 5 kW will go to support the work of the system (heating actuator).
Moreover, if you go back a little and compare the size of the thermomechanical actuator in the scissors with their effort to develop our ratios, or 3 tons of cargo instead of 26 tons, and only twice reduced the length and width of the actuator, it is possible to assume an even greater optimization of the actuator size for a given production capacity and reduce the intensity of heat.
So, in the end, we have on one side
standalone starter unit on solar energy, costing no more than 150,000 RUB.; compact, long-lived bimetal actuator-an actuator with a heating element, worth up to 30 000 RUB; the generator — 320 000-370 000 RUB depending on the manufacturer; flywheel with a spring 200 000 RUB; support mechanisms ("gravity plate" with the cooling system, etc.) — cost 200 000 RUB total: RUB 930 000 (roughly) 20 years.
On the other hand have already not we are: fellow — the wind turbine 30 kW, 60 without the required batteries will cost about $70 000, the wind turbine of 50 kW is more than $170,000 and so on... (Pay mostly not for the equipment itself, and for mounting an insane amount of metal supporting truss and expensive blades.) So what is "expensive"? Nitinol?
Summaryto Start thinking about "sverkhelastichnosti" this system I would not like. It is only her autonomy and compactness.
And again, I had an initial task to introduce a completely ready solution to the issue on these pages. When publishing his thoughts, the primary motivation was a desire in some way "to move the assemblage point" for a number of creators (and customers, of course) giant windmills, serpentine underwater, "pontoon", "underground" and "space" generators of electricity. Why are these monsters?.. The essence of all processes in a conventional internal combustion engine can be reduced to the banal extension of a substance. A short but powerful effort at expansion. The rest is auxiliary machinery.
Industry famous economical hydraulic tools, developing due to the incompressibility of water is a huge undertaking. It remains only to transform the force into rotation and to store for future use.
Supersize everything, of course, dictated by the desire of developers of large-scale projects to scoop up two handfuls have confused governments, but it is clear that the future of energy is not bulky energy system for many kilometers across the ocean, and the creation of a number of Autonomous centers of production of average power, with the organization capacities of local flows in the event of an accident. In this approach, the Sayano-Shushenskaya effect is simply impossible.
It is likely that somewhere in their thinking about "wind turbine without wind" I made a technical error. But the bottom line is:
The possibility of compact and relatively inexpensive organization of Autonomous electricity production systems for domestic and industrial needs of a particular consumer
Here is a sample specification "Home generator" with the calculated lifetime of equipment 20 years:
That's the whole story... posted
Source: khd2.narod.ru/authors/naygel/nitinol.htm
Soviet metallurgists G. V. Kurdyumov and L. G. Henderson in 1948 suggested alloy, is endowed with the ability after a significant plastic deformation to restore its original shape when heated to a certain temperature. In 1980 this invention was recognized by the opening and became known as the Kurdyumov effect (effect of restoration of a given configuration or shape memory effect).
This effect is practically reproduced in the following way. The pre-billet of an alloy, e.g. the wire, attach required form. Then it is heated and cooled. After which it straighten. Upon subsequent heating, the wire will take its original configuration.
The mechanism of this phenomenon is not entirely clear. Martensitic reactions are reversible. During heating of the sample, they go in one direction, while cooling the opposite. Occurring during martensitic transformations and physical processes are so complex that experts say "the genetic properties of crystals". Despite the incomplete clarity of the physical mechanism of this phenomenon, it is part of our practical life.
In 1958, was first obtained alloy with effect of shape memory is nitinol. Nitinol is an alloy of Nickel and titanium. It is quite difficult to produce. To achieve the desired transition temperature, the ratio of Nickel and titanium in the alloy must be maintained with high accuracy. This alloy has the phase transitions are above room temperature but below the boiling point of water. If titanium nickelide it possible to dope the iron, the temperature range extends in the range from ambient to the boiling point of liquid nitrogen. The necessary purity of production is ensured through the use of complex vacuum furnaces and auxiliary equipment. Therefore, the widespread use of nitinol is limited by its high cost, and sometimes the inertia of our thinking. But finding ways of reducing the cost of production of nitinol continues. And some firms, for example, "Special metals Corporation" (USA), intend to begin commercial production of nitinol with acceptable commercial value...
The most common applications of nitinol today
In addition to the propulsion, built in the late XX century American banks, others, really embodied in metal "industrial propellers" on the basis of the nitinol actuator in the world press is not marked. Experts know enough of the references (more than 1000 according to various sources) on the patenting of various models of nitinol actuators and propulsion, but the invention is not moved further patent applications.
Robotics stepped a little further using the micron nitinol filaments as electronic muscles. Often, as always, surprised the Japanese. While passing through the nitinol filament weak currents, muscles developing efforts, hundreds of times greater than human.
As auxiliary applications, nitinol is used in a wide range of devices, the designs of which suggest movement caused by heat. So, for example, nitinol is used in devices for fire protection, used for sealing joints in aircraft, submarines and prevent radiation leaks at nuclear power plants. The connections of pipes made from alloys with shape memory effect, with the respective dimensions of the walls, and coupling with a body thickness of only 2 mm can withstand high pressure (in the range of hundreds of atmospheres).
Not far behind from the process industry and space industry. It has developed a "self-extracting" compact antenna, originally on earth, Packed tightly for easy transportation into outer space.
Broad use of nitinol has received and in the medical industry. Today around the world have become well-known bracket systems, used to align the altered occlusion in dentistry. Developed a unique stent for vascular surgery, able to withstand 10 to 20 million cycles "compression-expansion" under the regulations of American FDA and various orthopedic devices, with a dosage correcting load on the affected bone.
The potential application of nitinol
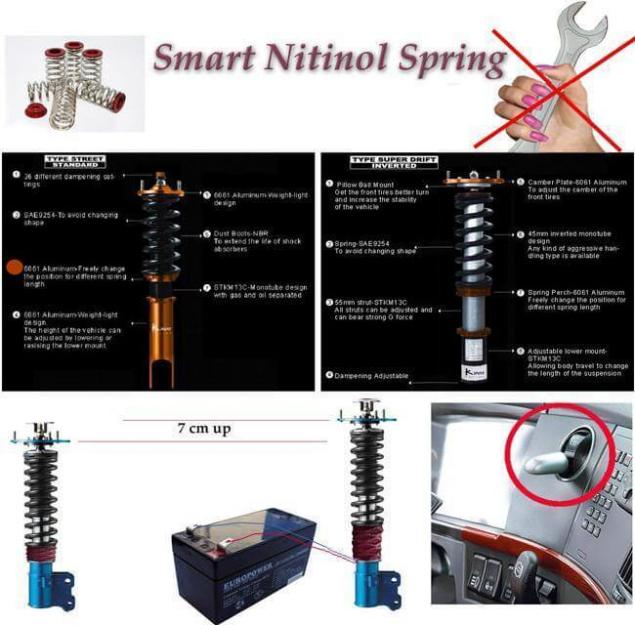
The Electromechanical regulator of the clearance of the car
The problem of the emergency levelling of the car is spread everywhere in the world, in cases when it is necessary to overcome the "difficult" road journey of several kilometers (commuter, road, blurred by rain, for example) and return the height of the clearance "at the same place." Solution pneumatic lifts there, but complaints of their operational fragility also abound. In the alternative, Pneumatics, various companies offer a strut with a mechanical method of lifting (thread nut), but here there is a lot BUT including the same level of rise at uneven wear and tear on the shock towers front and rear, the need to provide access to the nut, by removing the wheels... and manicure, finally.
A solution with a coil of nitinol may be available to any mechanic-welder. Given the episodic nature of the operation of this actuator, the design will last as long as it will last and dampers to replace them. Management in this case, there is a button from the cabin, and the response time is less than 1 min.
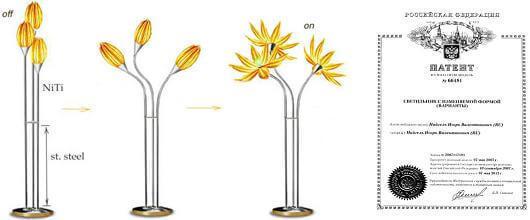
Design of household lamps
This patent is based on the international search, which is not found analogues of the use of technology "dual-memory Nickel-titanium alloys" in relation to systems of household lighting.
Attempts to create a ceiling, using the energy of the heating lamps to be deformed decorative elements (petals) have not received serious attention from customers — the manufacturers due to some limitations of the effects (the lamp warms only in the immediate vicinity). In this patent used a different heating principle, special heaters and cost effective heat cables. This approach to the design of the fixture creates an opportunity for wider production sources and directional light flush mount. Light sources that "appear" only when needed (application is medical lighting, automobiles, interior minimalist design, bathrooms, emergency lighting etc.). Considering the frequency of use of these devices (not more than 1-3 times a day), it is possible to provide continuous operation of the nitinol tubes that are running at the limit of the permissible norms of martensitic transformations, without substantially compromising efficiency of the structure (10,000 cycles in 10 years).
The effectiveness of "nitinol actuators"
The high performance of the various actuators made of Nickel-titanium alloys proved a number of major research institutions that studies the processes of the martensitic transformations in various versions of these alloys for over 30 years. For example, according to the conclusions of scientists from the Japanese company Furukawa, adding to the alloy of a minor amount of copper (6%) allows to increase the "useful working stroke of the actuator" up to 30 percent or more. This feature of the Nickel-titanium-copper alloy is now being promoted in robotics. How under this regime reversible deformation — time will tell.
Most professionals from different countries United in the opinion that the plate of titanium-Nickel alloys with an area of 6 cm2 is able to reach the stress with the martensitic-austenitic transformations to 27 tons or, according to some Russian sources, up to 55 tons per square inch of cross section of a part.
Nitinol and electricity
This work of Russian inventors, in my opinion, deserves close attention because of illustrates available to comprehend the process and leads to reflection on the evidence of the use of nitinol as a high performance Electromechanical actuator for generation of electricity. Why electricity? Because the energy spent on heating of metal products, palm-sized dimensions, and the potential work produced by this product after heating are not comparable, even in the case when the rod is heated by an electric source with a power of 5 kW. Moreover, the assurance of a respected state organization FDA (Food and Drug Administration controls in the US quality of food and medical devices), the process of heating-cooling without significant residual strain may last for several million cycles.
Try to start to evaluate the stress at 26.5 tons, in terms of the standard quantities used for the calculations of the various "rotational" structures.
From help:
Kilogram-force (kgf, kgf) is equal to the force that tell the body weight of one kilogram, the acceleration 9,80665 m/S2 (standard acceleration of free fall).
1 KP = 9.80665 Newtons (exactly) ~ 10 N
1 tonf (ton-force) = 103 kg = 9806,65 N
Therefore, in mm2, of Nitinol under strain, according to the authors-developers of the developing shear force is 600 Newtons!
Rod-actuator invented the scissors, when the claimed 26.5 tons generated efforts, develops a little more than 260 000 Newtons.
A lot or a little?
Consider low-speed wind turbine. Suppose that we would like to place in the basement of his house, as a stand-alone "producer" of electricity. Slow speed means no loss in efficiency of power generation, this generator can use the speed of rotation of the rotor shaft from 100 to 600 rpm, instead of 1 500 and 3 000 rpm as the conventional liquid fuel generators. Less speed — less effort spent on the development of this speed. On conviction the developers, the designs on permanent magnets operate up to 20 years or more without replacing parts.

The "home" model 12 kW (made in England-China):
the effective rotor speed 140 rpm;
mass 359 kg;
rotor inertia 1.59 kg m2;
material magnets NdFeB (rare earth neodymium);
a torque of 800 N m.
Of all the introductory specification we are interested in the last one — torque. The moment has the units Newton-meter (N·m).
1 N·m moment of force equal to 1 N, relative to the point located at a distance of 1 m from the line of action of the force.
Let the radius of the "flywheel" of our theoretical torque generator rotor actuator made of nitinol, is 1.2 m. Forces in Newtons, it would seem, abound. But not so simple in the organization of the transfer of translational motion into rotational energy. The point of application of force is unlikely to serve as the periphery of the flywheel, effort will be focused near the center. Assume that the diameter of the axle, where the main applied stress of 50 mm. Therefore, we need to multiply the total force generated by the rod-actuator for a short shoulder radius of the axis — 25mm.
Multiply 260 000 N x 0.015 m = 6 500 N·m.
So produced nitinol rod force, organizing the torque of the rotor is eight times greater than the force required to rotate the generator 12 kW. So a preliminary answer to the question — a lot or a little? That's a lot.
So we do not need.
According to the specification of those British manufacturers, straymouse moment for 30 kW tion of the generator is equal to 31 N·m, and operating torque of the order of 2 500 N·m...
Let us now try to transform the "wonderful power" short movement of the actuator in a smooth, continuous rotation of the rotor of the generator capacity of 30 kW and in the process to understand "what is the cost of heating" nitinol actuator?
It will be only a concept generator with a nitinol actuator, which are based on quite disparate, shared data (including mechanical shear, of course). Therefore, some excessive assumptions and technical inaccuracies I would like to pre-apologize.
We need to:
- to create highly effective, but simple method of transfer of translational motion into rotation, with a smooth distribution of massive effort, without jerks;
- to ensure the costly actuator the opportunity to work quietly — gently warmed, worked, smoothly cold a c cycle interval 2-5 min;
- starting to create an Autonomous heating system actuator;
- to create a transformer short the efforts of nitinol in a smooth and long motion without significant losses for this kind of transformation;
- create compact self-contained cooling system of the actuator after the heating.
Nitinol impulse Electromechanical actuator
From the technical description of a hollow nitinol rod thermomechanical shear we recall that the dimensions of the actuator were as follows:
the rod length is 15 cm;
diameter — 4 cm x 2 cm.
Reduce the diameter of the rod in half, so as to cut the metal, we will not, and budge 26.5 tons, in everyday application, no special meaning. The actuator runs in a replaceable cartridge, for easy self-replacement after triggering a certain number of cycles (the diagram below shows a conventionally) once in 20-30 years when the cyclical heating of, say, 5 min. (the Number of cycles in 30 years will be 6 million if round-the-clock operation from 10 million guaranteed many foreign producers).
On the rate of heating and the estimated current is can be judged only indirectly. Direct data we have. There is only a short paragraph, the authors of scissors: "Due to the low temperatures needed for heating the core, the energy source can be, for example, a rechargeable battery, a low-voltage grid, the throttled compressed air, any associated heat exhaust".
The heat capacity of water is 4 200 j, the heat capacity of titanium nickelide only 490 George. But touch base...
Let the estimated capacity of our heating element-spiral, inside reduced nitinol actuator-plate is 5 kW (the power of a standard electric kettle 2 kW and 1 liter of water boil it for 3 min).
We know that the regime of heating and cooling the nitinol actuator +65..+40 - +25°C. And, according to inventors, "... at all temperatures above 40°C it generates stress on unit area of its cross-section equal to 60 kgf/mm2". We do not need to "boil" the body, heating it from 20 to 100°C. moreover, the alloy, in our case, we can not cooling, but only to reduce its temperature to a critical point of the transition martensite-austenite 35-38°C, spraying a refrigerant drip. In this case, the temperature interval of transformations to the point of transition will be even smaller, of the order of 10-15°C. In the engine Banks temperature range was 24°C.
Therefore, we can with a certain degree of confidence to assume that well-organized convection heater will allow you to enter the estimated parameters from 45 seconds to 1 minute. Sparing mode of operation, so to speak. But nevertheless, please be extra time (+2 min), just in case... 5-kilowatt source will heat our actuator 3 min(!) 20-30°C.
Now try to "draw" a stand-alone installation for the production of electricity, placing it aboard average three-storey house with a living area of 300 m2. In the harsh Russian winter home will require at least 0.7-1 kW per 10 m2 of living space. In the end, 21-30 kW to 300 m2.
Let's start with the transformer. It all the power! Here, one might recall the experiments of Pascal with a 4-meter pipe and "torn from the pressure of the water is wide".
Increase the diameter of the pipe at random and hoisted her in the basement like this:
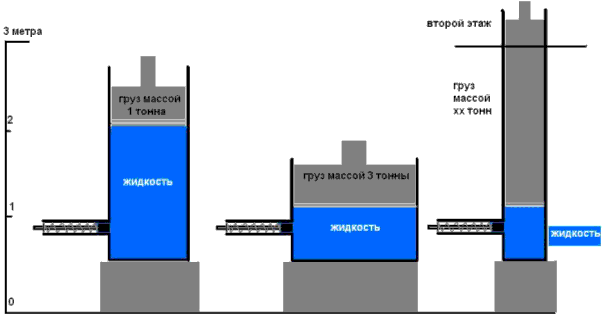
Experience suggests that if the bottom of the tank from the pressure will not fall through the floor, then the piston will assume all the energy Paskaleva pipe, and the situation after heating and cooling the actuator made of nitinol (due to gravity) will look something like this:
Let's stop on this construction of "transformer multiplier" short the efforts of actuator long stroke...
Next to start the process of energy production we will need a launcher standalone heating unit (on the circuit it is not shown). The standard solution for such a case are 2 monocrystalline solar panels 2 x 240 watts mounted on the roof of the house (1800 x 1000 mm each). Will need the usual
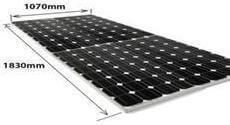
Monocrystalline solar panel 240 watts (46, 5.2 A).
- charge controller
- the inverter 5 kW
- starter battery 2 × 180 Ah...
Yes, actually, and all... as the batteries we need only occasionally, when starting, charging is a long process and planned (at idle the generator). The sun ever so look out and charge. When running, alternator charging is similar to charging a car battery. Therefore in details to stop on this block will not. There are start-up current and all... As a given...
Now proceed to "build" all together.
Schematic diagram of nitinol-hydraulic-spring-flywheel drive shaft rotation will generatorsof rollicking... actually the drive is quite simple:
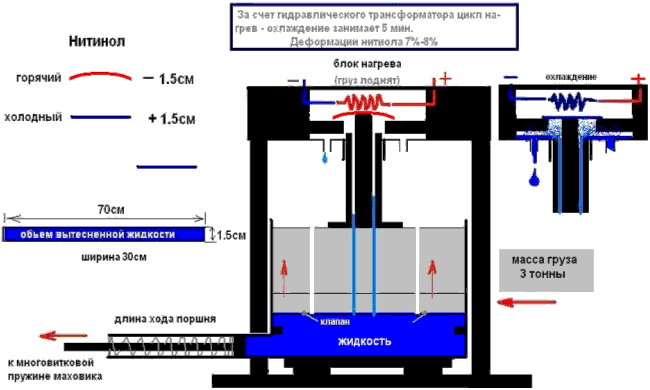
Of course, many of the units are shown only schematically (configuration of the actuator, the spiral, the heating element can be successfully replaced by highly efficient direct heating with a supply voltage of 400V and a power of 5 kW, or an infrared heating quartz with high-strength casing, etc.).
But the essence of the plant as a whole reflects, I believe, clearly. Confuses a lot of press, but instead of expensive metal as weighting can be used the filling the sand.
In this case, we are "not confused" short stroke actuator with a reversible strain of 7% — 20% (20% statement of Russian inventors). 7% good. And 20% is even better. In the scheme we have hydraulic press-animator is powerful, but short efforts nitinol actuator that is converted into rotational energy of the shaft of the generator. That is, when the hydraulic press is created win in the force is equal to the ratio of the area of the larger piston to the smaller area. A small compressibility of the fluid provides a practical equality of volumes of liquid passing from the large cylinder into the small.
The area of the small cylinder of 10 cm2. Press dimensions 70 cm x 30 cm according to this ratio, we can win in strength hundreds of times and push into the lumen of the "trunk" of a small cylinder a little less than a liter of fluid.
The cooling system is arranged on the actuator due to the pressure presses on the liquid in the capillary channels inside the package when it is lowered.
Set in the basement of our low speed generator 30 kW.
Mounted the flywheel drive energy nitinol-hydraulic actuator. The hollow disk flywheel has one important feature, it contains within its casing extra battery — spring energy storage.
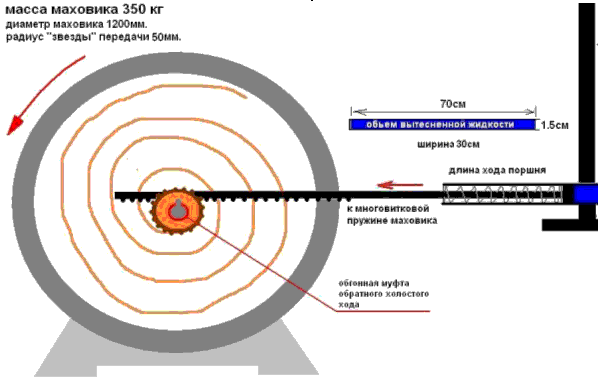
Now try to imagine what will happen when a powerful but short the effort of the actuator.
Activate the heat. Raise a plate of mass 3 tonnes for 1.5 cm. turn Off heat. Plate starts to fall self-independent, the force of gravity to pressure fluid and to return the actuator to its original starting position. Simultaneously, the press, in its motion down and still cools the actuator.
The motion of the small piston to the left by fluid pressure, gear rack linearly transmits all the energy of the increased fluid pressure of the toothed wheel seated on the axle of the flywheel through a freewheel.
The overrunning clutch engages with the axle and, in turn, transmits the energy of the translational motion of the turns of the elastic springs of the flywheel. In the reverse movement of the overrunning clutch allows the gear rack actuator to move freely without load.
Flywheel mass of 350 kg At the end of the translational movement of the actuator, we transferred a large part of the energy to the flywheel, turning it into a stored elastic force of the spring, the remaining part is consumed on the associated costs of any mechanical transformation. The process is started. As a result, we have a cocked spring of a flywheel and a potential energy of rotation 350-pound steel disk with a radius of 60 cm Flywheel strahovatsya and smoothly begins to rotate, gaining kinetic energy, which will significantly help us in subsequent cycles. In this case, the elastic force in the compressed spring is distributed in such a way that the formula that calculates the radius of application of the main efforts... no longer works. Spring tends to spin the flywheel at the same time over the entire area of the hollow disk, from heavy rim and up to the point of application of force at the radius of the sprocket.
During this period, our actuator can easily regain their strength for the next "breakthrough". Plate, using the forces of gravity and pushed up the coolant will pull it into launch position without excessive pressure, dropping his weight at the end of the movement in special fixtures.
The actuator is resting, and the energy stored in the spring accumulator is gradually released and converted into kinetic energy.
What we have in the end?
Obviously, having after heating the actuator force 3 ton-forces down the slab, is applied through the hydraulics to the hard unstressed spring flywheel for 2 min, we accumulate a tremendous amount of energy to rotate the generator rotor. In the case where the diameter of the sprocket axis equal to 100 mm, and the radius of the applied force, respectively 50 mm, we have roughly 1 500 N·m of torque for our generator. Spring not only creates a reserve for smooth maintaining the torque on those 3 min that are required for the next heating cycle of the actuator (exactly how many depends on the number of turns of the spring and its elasticity), but also increases torque by half due to the redistribution of the point of application of the main efforts.
If we assume that the point of application of force of the combined drive of rotation removed from the center axis 100 mm (which is technically feasible), the torque is 30 000 N x 0.1 m = 3 000 N·m. (plus the elasticity of the springs at the periphery of the flywheel).
When we consider all losses due to friction and other imperfections, depriving the par-3 000 Nm, conventionally, 15%, we will still be 2 550 Nm for belief in the efficiency of the design capacity of 30 kW, so as to overcome the resistance of the magnets of the rotor, we need only 2 300 to 2 500 Nm. The generated electricity will be distributed as follows:
25 kW may be demanded by the consumer; 5 kW will go to support the work of the system (heating actuator).
Moreover, if you go back a little and compare the size of the thermomechanical actuator in the scissors with their effort to develop our ratios, or 3 tons of cargo instead of 26 tons, and only twice reduced the length and width of the actuator, it is possible to assume an even greater optimization of the actuator size for a given production capacity and reduce the intensity of heat.
So, in the end, we have on one side
standalone starter unit on solar energy, costing no more than 150,000 RUB.; compact, long-lived bimetal actuator-an actuator with a heating element, worth up to 30 000 RUB; the generator — 320 000-370 000 RUB depending on the manufacturer; flywheel with a spring 200 000 RUB; support mechanisms ("gravity plate" with the cooling system, etc.) — cost 200 000 RUB total: RUB 930 000 (roughly) 20 years.
On the other hand have already not we are: fellow — the wind turbine 30 kW, 60 without the required batteries will cost about $70 000, the wind turbine of 50 kW is more than $170,000 and so on... (Pay mostly not for the equipment itself, and for mounting an insane amount of metal supporting truss and expensive blades.) So what is "expensive"? Nitinol?
Summaryto Start thinking about "sverkhelastichnosti" this system I would not like. It is only her autonomy and compactness.
And again, I had an initial task to introduce a completely ready solution to the issue on these pages. When publishing his thoughts, the primary motivation was a desire in some way "to move the assemblage point" for a number of creators (and customers, of course) giant windmills, serpentine underwater, "pontoon", "underground" and "space" generators of electricity. Why are these monsters?.. The essence of all processes in a conventional internal combustion engine can be reduced to the banal extension of a substance. A short but powerful effort at expansion. The rest is auxiliary machinery.
Industry famous economical hydraulic tools, developing due to the incompressibility of water is a huge undertaking. It remains only to transform the force into rotation and to store for future use.
Supersize everything, of course, dictated by the desire of developers of large-scale projects to scoop up two handfuls have confused governments, but it is clear that the future of energy is not bulky energy system for many kilometers across the ocean, and the creation of a number of Autonomous centers of production of average power, with the organization capacities of local flows in the event of an accident. In this approach, the Sayano-Shushenskaya effect is simply impossible.
It is likely that somewhere in their thinking about "wind turbine without wind" I made a technical error. But the bottom line is:
The possibility of compact and relatively inexpensive organization of Autonomous electricity production systems for domestic and industrial needs of a particular consumer
Here is a sample specification "Home generator" with the calculated lifetime of equipment 20 years:
- slow speed three-phase permanent magnet generator 30 kW;
- output voltage 400 V;
- weight 650 kg;
- the mass of the flywheel 350 kg;
- the diameter of the flywheel 120 cm;
- the rotor speed of 100-120 Rev/min);
- the actuator rotation is nitinol (combo drive);
- the starting source of heating — solar module (kit of 2 panels x 240 W);
- the heating power of the actuator 5 kW (but I believe, however, that not more than 3 kW);
- the heating time is 3 minutes;
- cooling time 2 min;
- the heating temperature of 65-70°C;
- gravity return bar weight 3000 kg.
That's the whole story... posted
Source: khd2.narod.ru/authors/naygel/nitinol.htm