709
My first knife. Hand-forged.
Kitchen knife with his hands. Will 8 photos
My first began with the forging of what I wanted for a long time forged kitchen knife, and even more - to learn how to forge. And with a convenient opportunity he introduced me to a master blacksmith. He forges a long time, 20 years already, but not on a broad sell works. And somehow, a glass of tea, I said that I want the knife and began to ask - Skuy yes Skuy. What they told me: "The hands are? So I go, myself and skuesh! At the same time, and learn.
The Forge is in the courtyard, mountain outdoors, made of stone, clay missed. For blowing - a few different power fans. The most powerful, 5 kW, heats the metal per minute to yellow status. Again, the temperature of the metal - by color, a master in the eye sees, when the metal is hot enough to not "burn" the workpiece, or throw out and start again. I put the fan weaker as 5 pound sledge hammer to pull the shoes in the plane waving paravoznogo valve - quickly tired hands, as well as the workpiece is heated - time to relax your hands.
In mountain burning coal. One tab is enough for about an hour and a half forged. The blank is heated and the process goes on without stopping until completion, the workpiece can not be allowed to cool completely, reheat it may deform, and again the problem of burning carbon.
Arsenal - gloves, tongs, sledge hammers, hammers of different weights. Pull the shoes of heavy sledgehammer, then hammer the blade shape is displayed, it is pulled in place of the blade steel blade fettered by denser blade is attached in place of the cut additional rigidity.
Here is just a process of heating the workpiece:
After the blank is forged - give it to cool. We get here is such a piece of metal is a little like a knife. But dashing the trouble started.
Then, give the approximate shape of the workpiece on sandpaper products. As Smith says: "A friend of the blacksmith - Comrade sandpaper".
Before forged his first knife, looking at the movies, all the time thinking that here is to forge - and received almost the final sword or ax. And only then saw that forging - is shaping properties of the workpiece and by compacting metal and molding it in the right places. And then grind, grind and grind. That shows a gradual shape the future of the knife. Cut off all unnecessary.
After the knife has found form his quenched. In the movie, often we see - forge - and in a barrel. Sh-sh-sh-sh ... and took the finished polished sword. But figushki. The preform will sharpen oh how difficult, and is likely to deform it may bend or twist the screw. Here, after heating to the desired temperature (the master determines again in color), the blade first tsianirovali to increase strength - heat, crumble powder cyanide, beautifully lit, but only work in the mask and in the open air, a pair of highly poisonous cyanide. Then cemented the edge in sealing wax. On cooling to a certain temperature - was lowered into the water. What does the experience - all in color temperature of the metal in the eyes. Skill does not spend on drink. Blade hardened.
The result is such a piece of iron, although not, perhaps this is the blade. Brought in stone form. Lighter to compare the size of the knife.
And then the blade on the sandpaper, but not on a rock, and on the tape of the sanding paper, the common people, "skin", adjusted the shape and sharpened. Why are not carved in stone? A little overexposed and the blade turns blue - overheated blade deteriorates, most likely in these areas is the Jag at work in these places overheat the metal. On the tape of the intense heat does not occur, even if the work takes longer.
Now polish the blade on a felt circle with GOI paste, and get a result here. The wizard offers to make the lining of the horn or wood stabilized - but I would like so. When cutting meat, contrary to fears in his hand does not slip, comfortable grip.
Posted in [mergetime] 1374702408 [/ mergetime]
That has turned out such first knife. Do not lumpy. Thank you for attention!
Source:
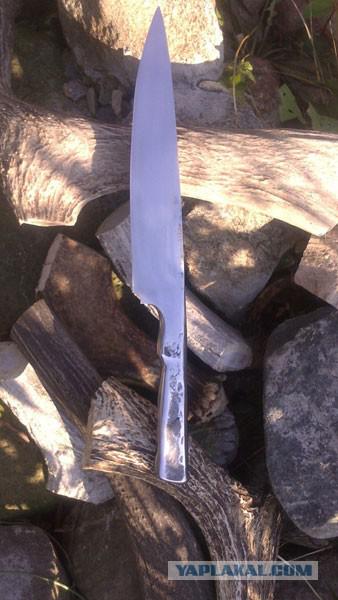
My first began with the forging of what I wanted for a long time forged kitchen knife, and even more - to learn how to forge. And with a convenient opportunity he introduced me to a master blacksmith. He forges a long time, 20 years already, but not on a broad sell works. And somehow, a glass of tea, I said that I want the knife and began to ask - Skuy yes Skuy. What they told me: "The hands are? So I go, myself and skuesh! At the same time, and learn.
The Forge is in the courtyard, mountain outdoors, made of stone, clay missed. For blowing - a few different power fans. The most powerful, 5 kW, heats the metal per minute to yellow status. Again, the temperature of the metal - by color, a master in the eye sees, when the metal is hot enough to not "burn" the workpiece, or throw out and start again. I put the fan weaker as 5 pound sledge hammer to pull the shoes in the plane waving paravoznogo valve - quickly tired hands, as well as the workpiece is heated - time to relax your hands.
In mountain burning coal. One tab is enough for about an hour and a half forged. The blank is heated and the process goes on without stopping until completion, the workpiece can not be allowed to cool completely, reheat it may deform, and again the problem of burning carbon.
Arsenal - gloves, tongs, sledge hammers, hammers of different weights. Pull the shoes of heavy sledgehammer, then hammer the blade shape is displayed, it is pulled in place of the blade steel blade fettered by denser blade is attached in place of the cut additional rigidity.
Here is just a process of heating the workpiece:
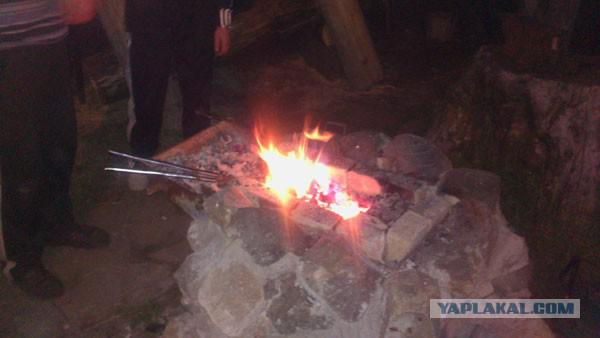
After the blank is forged - give it to cool. We get here is such a piece of metal is a little like a knife. But dashing the trouble started.
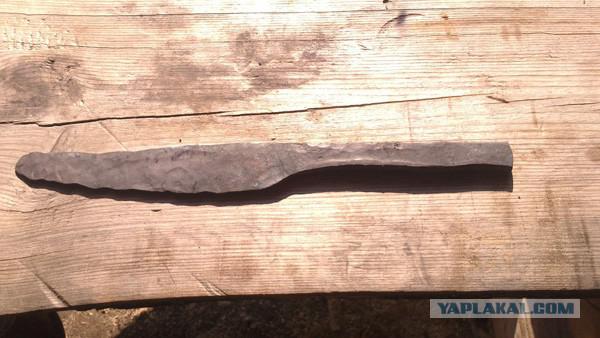
Then, give the approximate shape of the workpiece on sandpaper products. As Smith says: "A friend of the blacksmith - Comrade sandpaper".
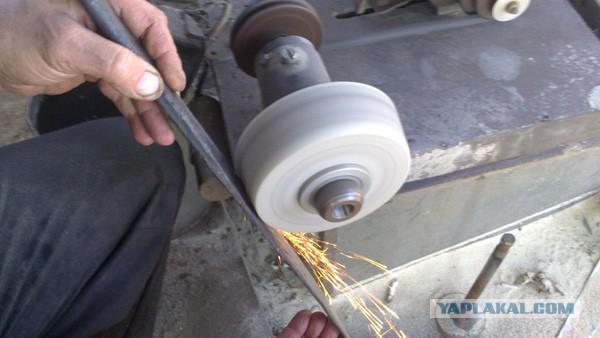
Before forged his first knife, looking at the movies, all the time thinking that here is to forge - and received almost the final sword or ax. And only then saw that forging - is shaping properties of the workpiece and by compacting metal and molding it in the right places. And then grind, grind and grind. That shows a gradual shape the future of the knife. Cut off all unnecessary.
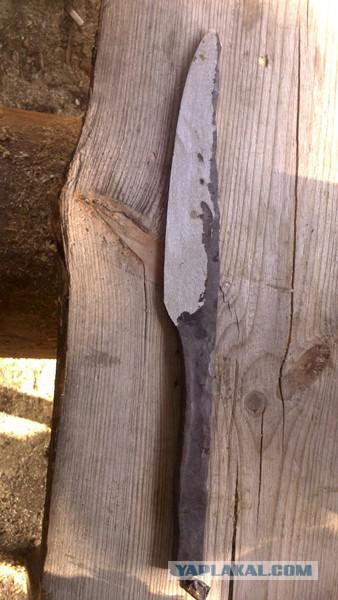
After the knife has found form his quenched. In the movie, often we see - forge - and in a barrel. Sh-sh-sh-sh ... and took the finished polished sword. But figushki. The preform will sharpen oh how difficult, and is likely to deform it may bend or twist the screw. Here, after heating to the desired temperature (the master determines again in color), the blade first tsianirovali to increase strength - heat, crumble powder cyanide, beautifully lit, but only work in the mask and in the open air, a pair of highly poisonous cyanide. Then cemented the edge in sealing wax. On cooling to a certain temperature - was lowered into the water. What does the experience - all in color temperature of the metal in the eyes. Skill does not spend on drink. Blade hardened.
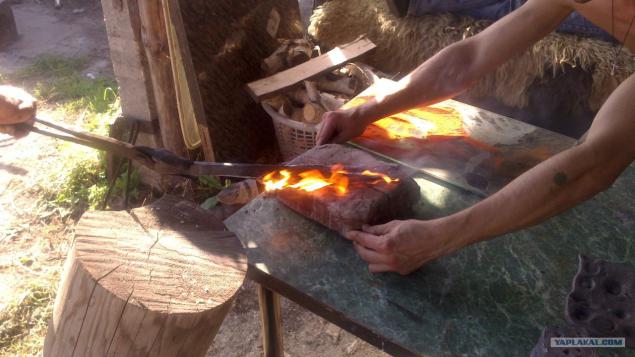
The result is such a piece of iron, although not, perhaps this is the blade. Brought in stone form. Lighter to compare the size of the knife.
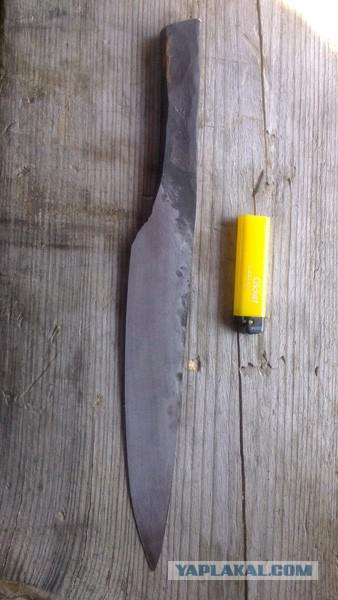
And then the blade on the sandpaper, but not on a rock, and on the tape of the sanding paper, the common people, "skin", adjusted the shape and sharpened. Why are not carved in stone? A little overexposed and the blade turns blue - overheated blade deteriorates, most likely in these areas is the Jag at work in these places overheat the metal. On the tape of the intense heat does not occur, even if the work takes longer.
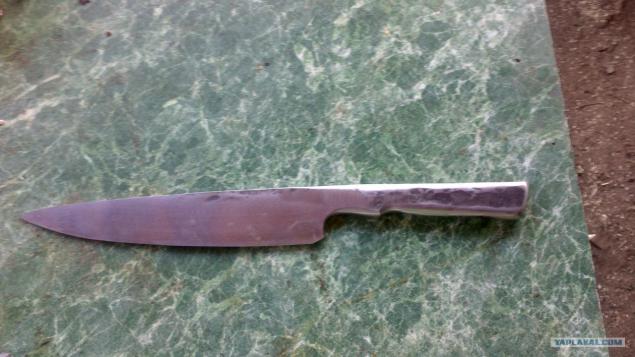
Now polish the blade on a felt circle with GOI paste, and get a result here. The wizard offers to make the lining of the horn or wood stabilized - but I would like so. When cutting meat, contrary to fears in his hand does not slip, comfortable grip.
Posted in [mergetime] 1374702408 [/ mergetime]
That has turned out such first knife. Do not lumpy. Thank you for attention!
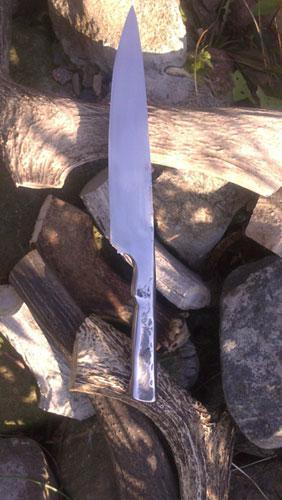
Source: