1214
How do the tube.
On the Internet you can find almost all the information about a particular industry, to learn almost everything. But in the sphere of production reporting lot of white spots, which I personally would like to eliminate. One such topic was suddenly producing tubes for creams and toothpastes. Why all of a sudden? Probably because they do not even thought about the fact that there is such a production as long as I did not offer to remove this report in response to my questions about how to make toothpaste.
76 photos, and text. A source.
2. All starts with this big iron boxes, which are here are aluminum pill.
03
4
From this hopper, which contains blanks for future tubes, they go to the very first section - the press.
5
Here, the high-pressure aluminum tablet tube is stretched almost ready. Everything happens very quickly, the press, we can say from knocks roundels tube. It is noisy, even the floor is shaking under my feet.
6
Tuba comes with a neck on which there is thread - amazing filigree work for the press, which is a fraction of a second makes this piece. Here is cut too much from the tube, so that they were all the same standard length - in the background you can see a box of scraps.
7
Tuba continues its journey further.
8
Here is a blank at this stage.
09
10
A number of tubes lay in boxes, then to report back on the line, if necessary.
11
I look at the tubes, tubes look at me.
12
From the muddy metal tablets obtained such a brilliant contraption.
13
14
A little distracted, but we will continue the tour. Next tubes come here. This annealing furnace in which the billet is subjected to high temperature. This is done so that the metal became softer and the tube could easily crush the hands, squeeze out the contents.
15
Interestingly, while not changing the wall thickness of the tube. As I explained, this process only changes the structure of aluminum.
16
After annealing, the tubes come here. Their inner part is covered with a special varnish.
17
18
Once inside the tube painted, they come down the tape once ad - oven where the paint is polymerized.
19
As you can imagine this is done to ensure that the contents of the tube is not oxidized, and it was useful throughout the life of the product. Lac, which is converted into a polymer absolutely neutral in all respects. As I said, these tubes under the characteristics much better analogues of the laminate, because they are more likely to retain the contents with natural ingredients - at squeezing the contents of the air does not get inside, so - no oxidation.
20
After the polymerization, the inner part of the tube come here in such a drive, which can be several hundred workpieces at a time. This is done in order to stop in the event of one of the line (where the tube is punched) and the other part of the line is not idle.
21
22
In the next step the surface of the tube is covered with white enamel.
23
24
Tubes again, for the third time fall into the furnace, where the enamel is dried.
25
After this white blank falls into the machine, which prints on the surface of the tube a certain pattern. In this case, baby cream. The worker, who monitors the process, before the eyes of lies is such a piece of paper with a sample drawing.
26
Everything here is very fast. Despite the fact that the tube is made pretty much automated process well enough to do everything quickly and efficiently.
27
Barely keep up with the speed to catch the desired frame.
28
29
The line for the production of tubes was bought in the early 90s and works quite well to this day. The machine is capable of applying a pattern of five colors. Here's how: Trees with a certain dip in the stencil with paint tray and tempo disco applied to a certain part of the picture tube. Further, the shaft with another stencil and color does the same thing, and so five times.
30
I found when on the line changed the shafts with the stencil.
31
Now on the line installed other trees to print a drawing for tubes with other products.
32
Before it all properly cleaned and lubricated.
33
Well, a painted tube fired once, the last time to fix the applied pattern.
34
The last operation - bolting to the blank cover.
35
Also all automatic, very quickly.
36
Well, quite a bit of time has passed, and the tube is ready to ensure that its necessary to fill the farm product.
37
38
And in the end all the tubes are rolled at the last stage in this production - packing into boxes.
39
40
But that's not all! Working factory packs up the workpiece from one box to another, I understand that in this way it was easier to use tubes for further production process.
41
Here in the shop is yet another production line of tubes. It is older than the previous one, it more than forty years, but it is working properly. The principle of the manufacture of tubes on the line is not different from what you see above, the only difference is that the lower rate of line and color pattern that can be applied to the tube consists of only three colors.
42
Many areas here, as we see the open, in contrast to the new line.
43
The drive looks different. And in general, this line of Soviet-made, and that - the German, unites them that both are quite effective. By the way, the volume of production at the factory so that these lines have to work around the clock, and nothing cope.
44
Pay attention to the diameter of the tubes - these wider.
45
46
Well, like with aluminum tubami everything is clear, go to the shop where we make the usual laminated tubes.
47
These devices do Bouchon. You ask what is it? Yes, I too was surprised when I heard this word from the master, who told me about the production.
48
And this is only the cap on the tube. The term "Bouchon» (bouchon - cork, France.) Has come from the French language as well as many terms borrowed into Russian language.
49
The machine extrudes hot plastic into the mold: half a minute, and you're done. Bouchon speed extrusion from the mold - 48 pcs. / Min. (Mold - 24 sockets, cycle rate - 20-25 sec.).
50
Scenic waste go back into the manufacturing process of the caps, it turns almost waste-free production.
51
Plastic for Bouchon, by the way - domestic.
52
That is the very mold.
53
There is a new generation, where the plastic is injected into a separate cell, and manages completely without waste.
54
And here is the machine that makes the tube laminate. Modern equipment, takes up very little space, but the manufacturing process of tubes is not as interesting and exciting as opposed to the previous.
55
That's the tape tucked into the machine. You press a button and you're done!
56
Among other things, the production of the factory complies with international quality standards ISO9001. Here, they place their orders, many large manufacturers, including foreign ones, for example, Procter & Gamble, which produced notorious for toothpaste (pictured below). By the end of 2013 commissioned by Procter & Gamble factory producing laminated tubes, is currently being negotiated for their production of aluminum tubes.
57
58
At the same time there are two roll fueled with laminate tubes for blanks, so that if one is over, you can immediately switch to the second.
59
As I said, this laminate is not doing at the factory, he bought in China, it's easier.
60
However, the laminate from which the tube is also not as simple as it seems. In fact, it consists of 5 layers, so that the package was of sufficient quality to be stored for a desired period of a certain product. Try to dissect the package from their toothpaste and tell me what you got).
61
Next, I will not comment, because you will find a video where everything is quite clearly shown.
62
63
64
Well, at the end of the tube folded in a box manually.
65
Laminant provide three production machine.
In this short video you can see how it all happens.
(FLASH MOVIE) 66
The factory is better known other own products (here also produce soap, cosmetics and toothpaste). I remember that my kids had the toothpaste.
67
Well-known children's cream.
68
69
And for adults something.
70
All products tubnogo production immediately checked in the laboratory for leaks, compliance with sanitary norms.
71
Each day is sampled packages (it can be seen that it is including vials), which is thoroughly checked.
72
In general, as you can see what is on the shelves.
73
74
This unit is checked for leaks tubes. The product is fixed in the apparatus, closed part is immersed in water, to another part of the compressed air is blown.
75
76
Well, like it, now you know how your tubes.
I thank the press service of the factory "Freedom" for the opportunity to see this interesting process and production director tubnogo Nikolai Zubkov for an informative tour.
Source:
76 photos, and text. A source.
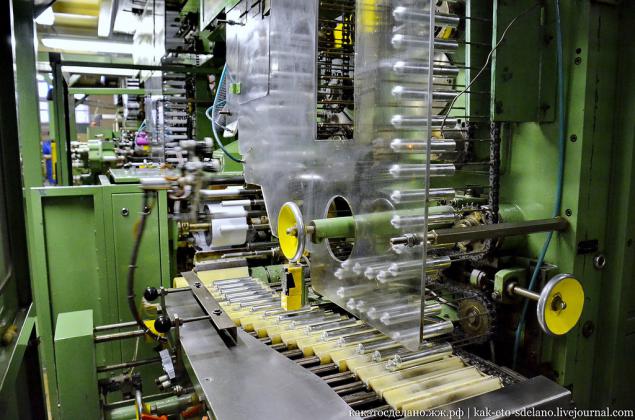
2. All starts with this big iron boxes, which are here are aluminum pill.
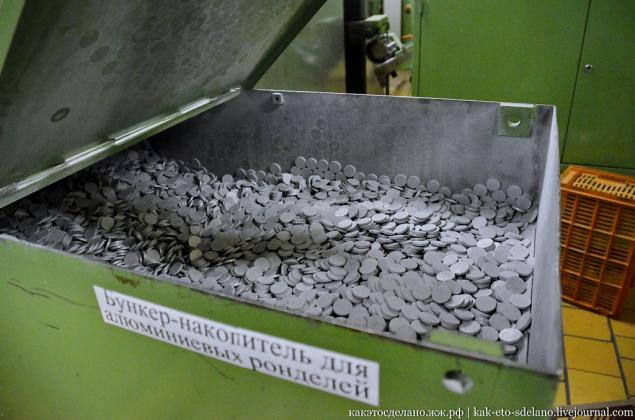
03
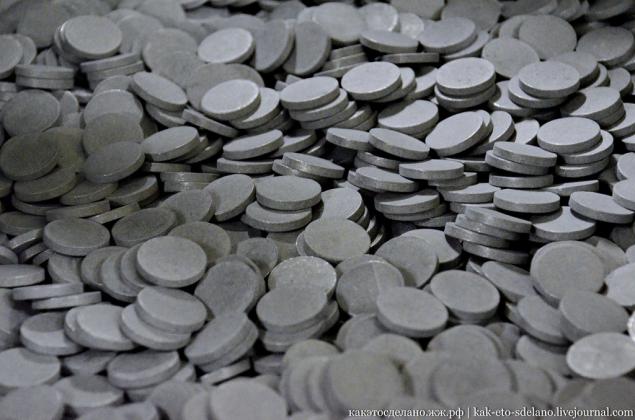
4
From this hopper, which contains blanks for future tubes, they go to the very first section - the press.

5
Here, the high-pressure aluminum tablet tube is stretched almost ready. Everything happens very quickly, the press, we can say from knocks roundels tube. It is noisy, even the floor is shaking under my feet.
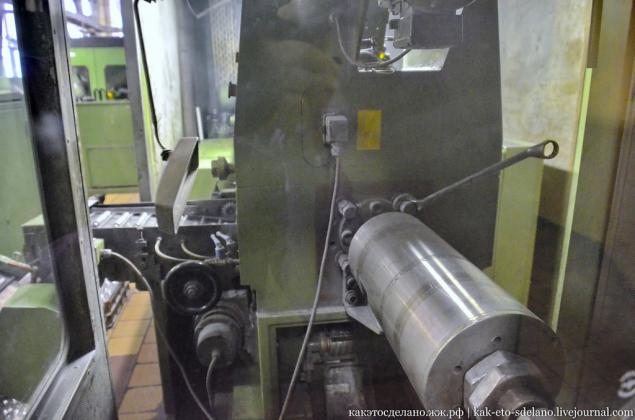
6
Tuba comes with a neck on which there is thread - amazing filigree work for the press, which is a fraction of a second makes this piece. Here is cut too much from the tube, so that they were all the same standard length - in the background you can see a box of scraps.
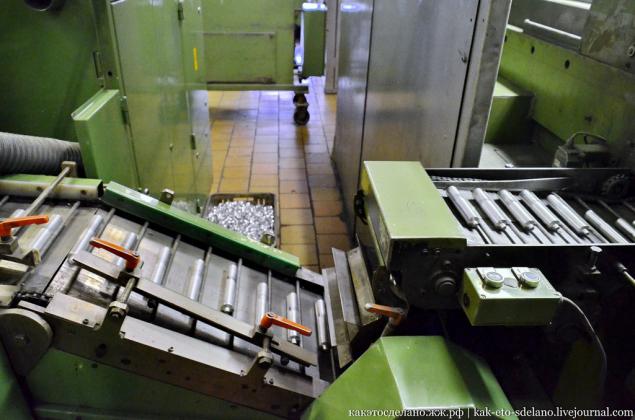
7
Tuba continues its journey further.
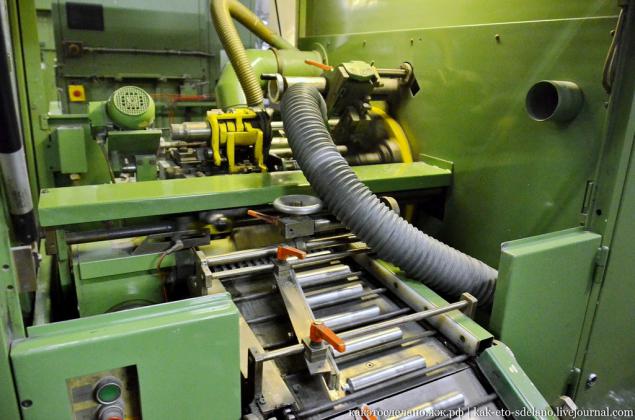
8
Here is a blank at this stage.
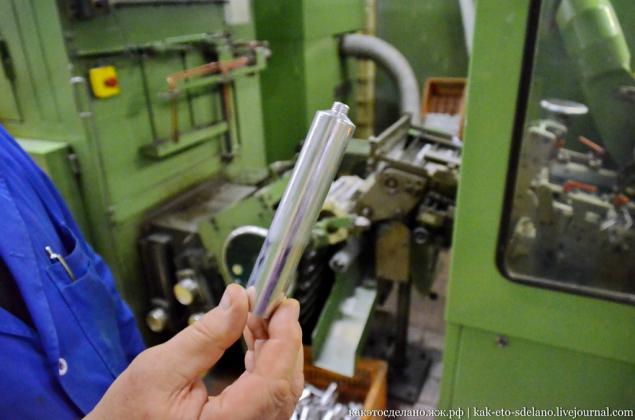
09
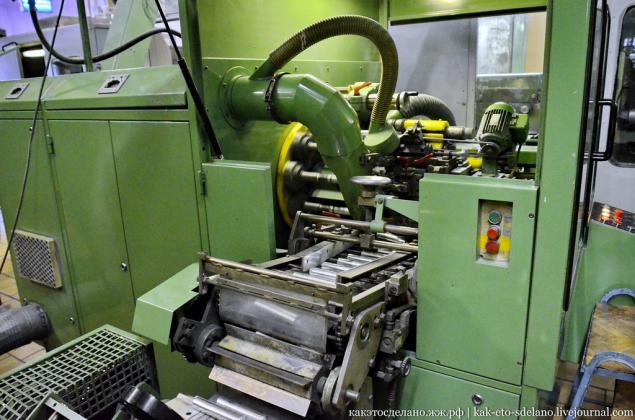
10
A number of tubes lay in boxes, then to report back on the line, if necessary.
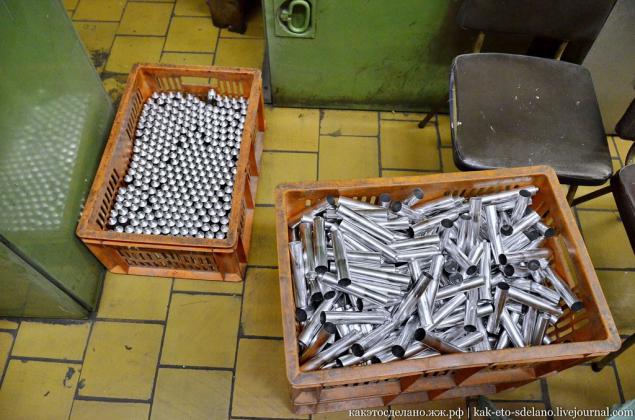
11
I look at the tubes, tubes look at me.
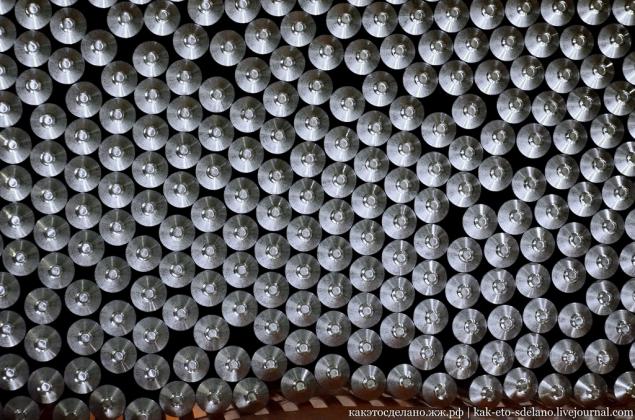
12
From the muddy metal tablets obtained such a brilliant contraption.
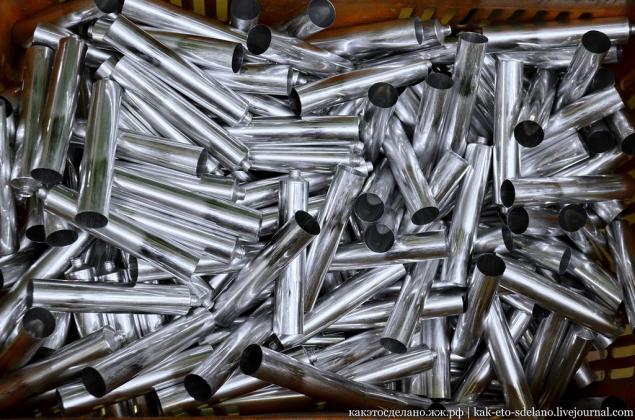
13
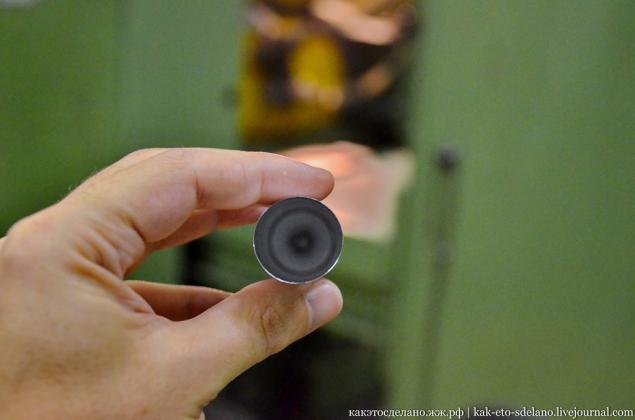
14
A little distracted, but we will continue the tour. Next tubes come here. This annealing furnace in which the billet is subjected to high temperature. This is done so that the metal became softer and the tube could easily crush the hands, squeeze out the contents.
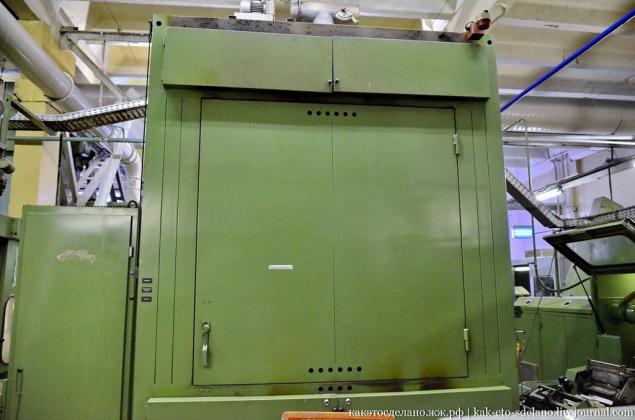
15
Interestingly, while not changing the wall thickness of the tube. As I explained, this process only changes the structure of aluminum.
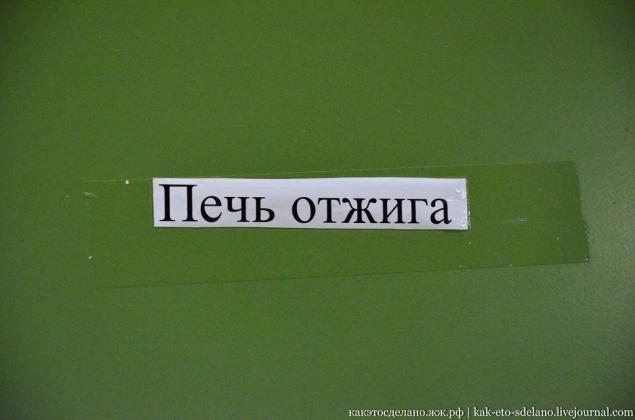
16
After annealing, the tubes come here. Their inner part is covered with a special varnish.
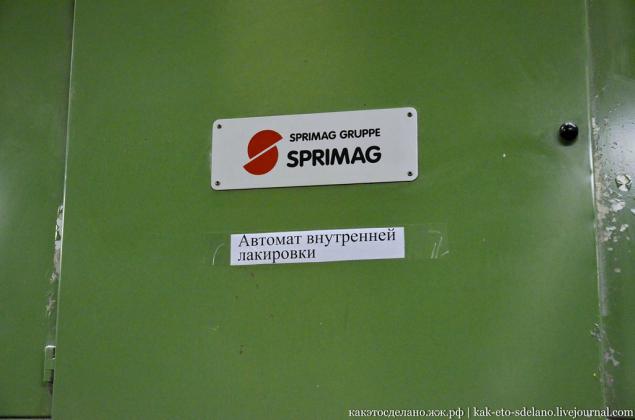
17
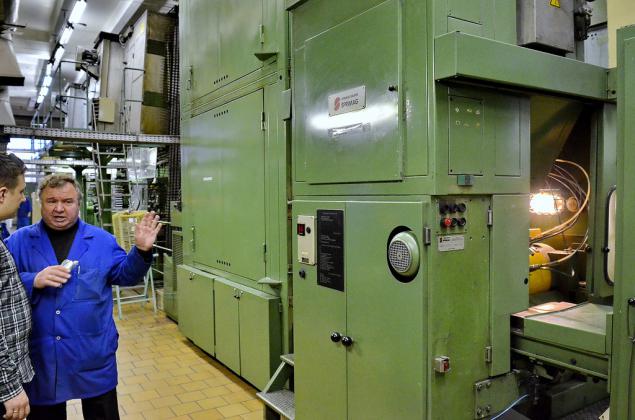
18
Once inside the tube painted, they come down the tape once ad - oven where the paint is polymerized.
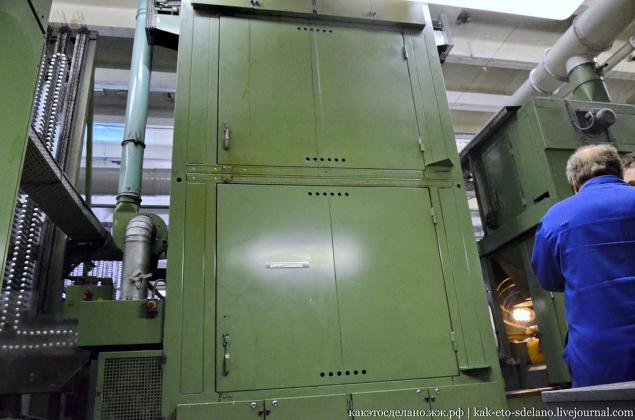
19
As you can imagine this is done to ensure that the contents of the tube is not oxidized, and it was useful throughout the life of the product. Lac, which is converted into a polymer absolutely neutral in all respects. As I said, these tubes under the characteristics much better analogues of the laminate, because they are more likely to retain the contents with natural ingredients - at squeezing the contents of the air does not get inside, so - no oxidation.
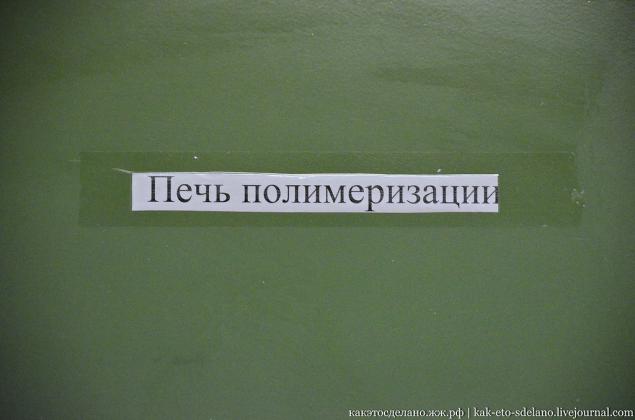
20
After the polymerization, the inner part of the tube come here in such a drive, which can be several hundred workpieces at a time. This is done in order to stop in the event of one of the line (where the tube is punched) and the other part of the line is not idle.
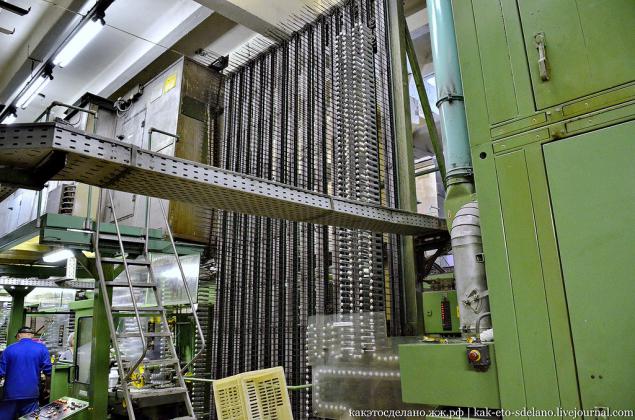
21
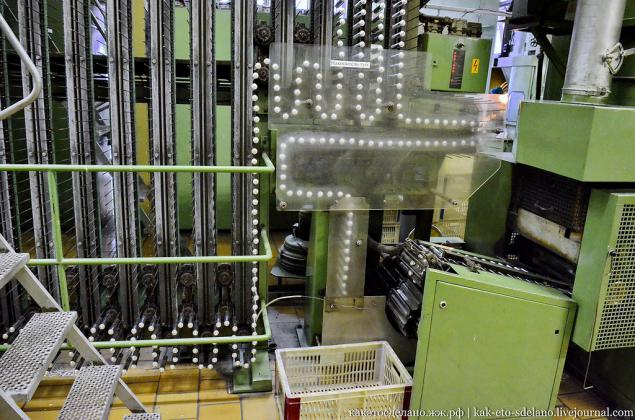
22
In the next step the surface of the tube is covered with white enamel.
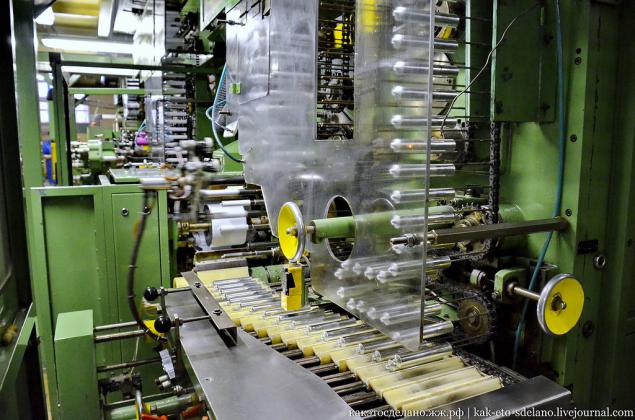
23
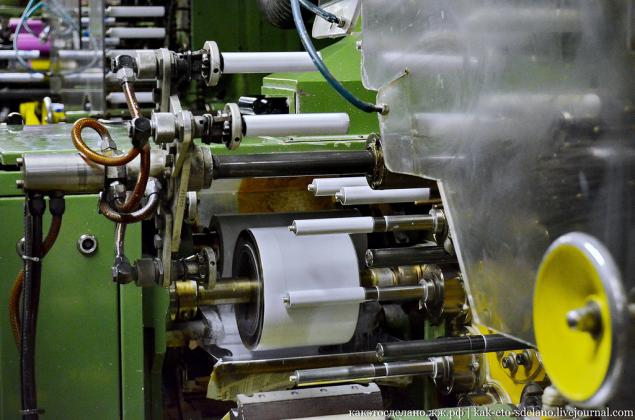
24
Tubes again, for the third time fall into the furnace, where the enamel is dried.
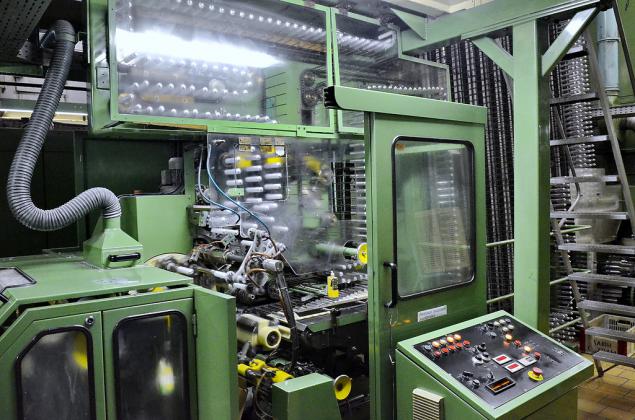
25
After this white blank falls into the machine, which prints on the surface of the tube a certain pattern. In this case, baby cream. The worker, who monitors the process, before the eyes of lies is such a piece of paper with a sample drawing.
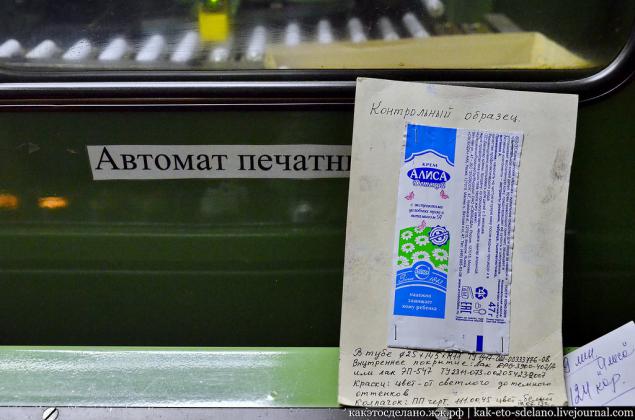
26
Everything here is very fast. Despite the fact that the tube is made pretty much automated process well enough to do everything quickly and efficiently.
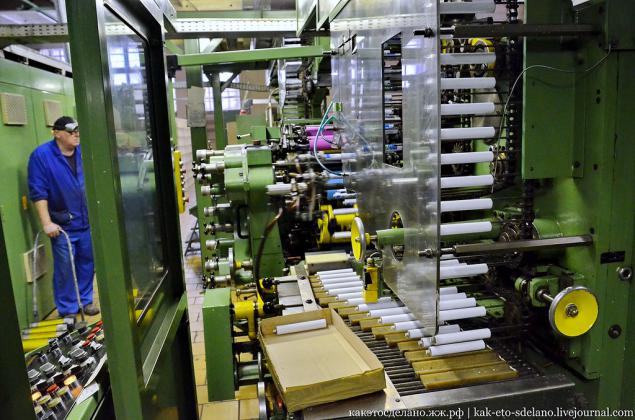
27
Barely keep up with the speed to catch the desired frame.
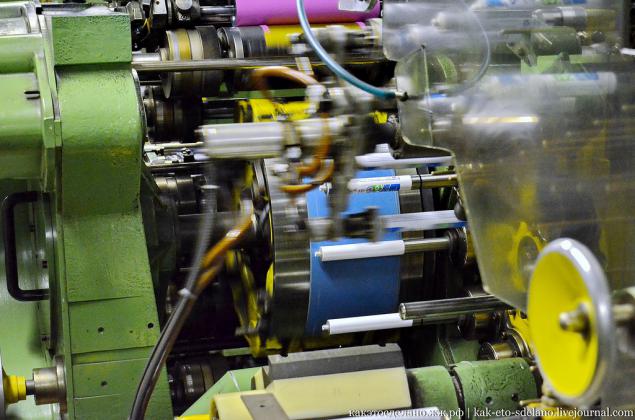
28
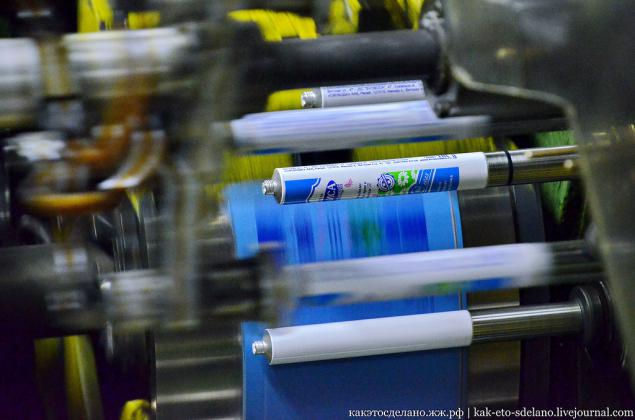
29
The line for the production of tubes was bought in the early 90s and works quite well to this day. The machine is capable of applying a pattern of five colors. Here's how: Trees with a certain dip in the stencil with paint tray and tempo disco applied to a certain part of the picture tube. Further, the shaft with another stencil and color does the same thing, and so five times.
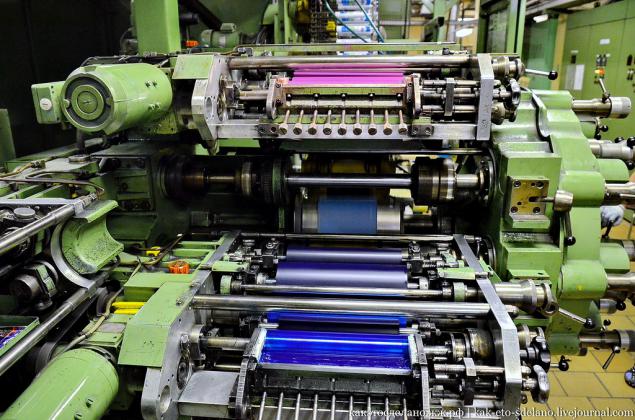
30
I found when on the line changed the shafts with the stencil.

31
Now on the line installed other trees to print a drawing for tubes with other products.
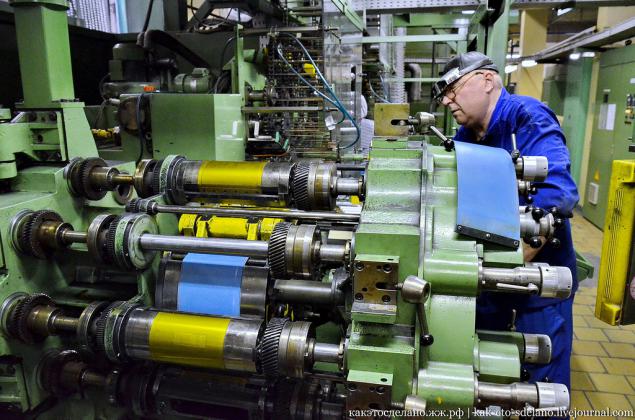
32
Before it all properly cleaned and lubricated.
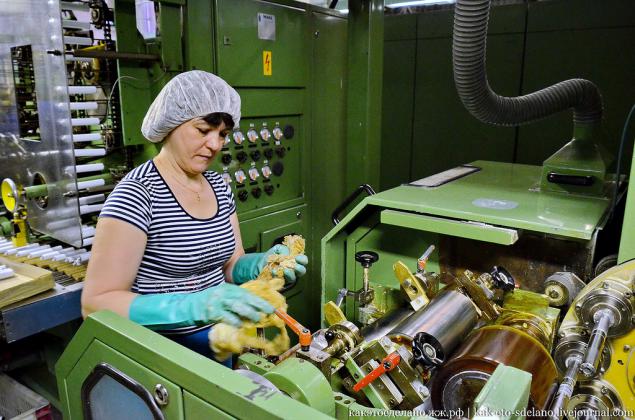
33
Well, a painted tube fired once, the last time to fix the applied pattern.
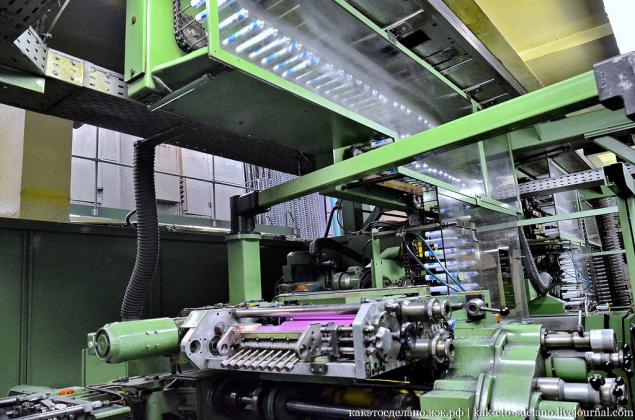
34
The last operation - bolting to the blank cover.
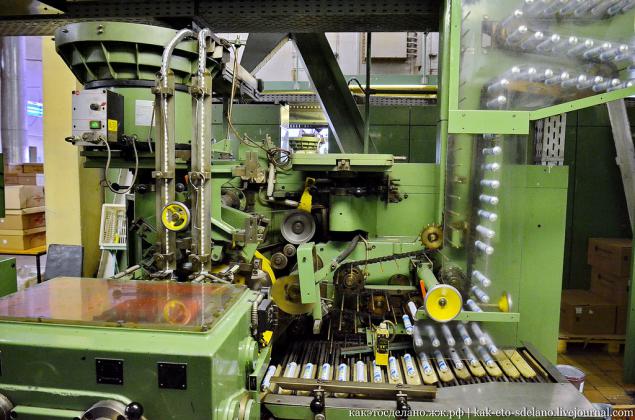
35
Also all automatic, very quickly.
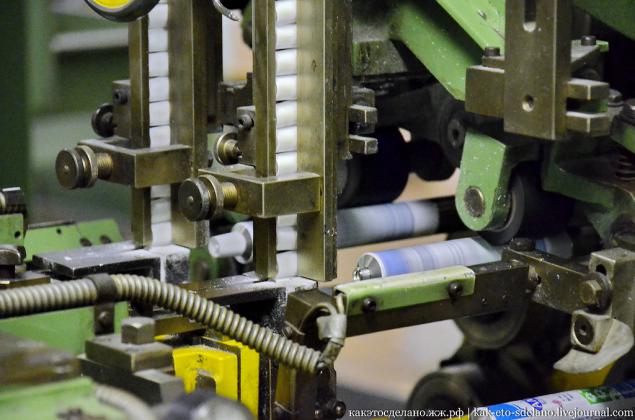
36
Well, quite a bit of time has passed, and the tube is ready to ensure that its necessary to fill the farm product.
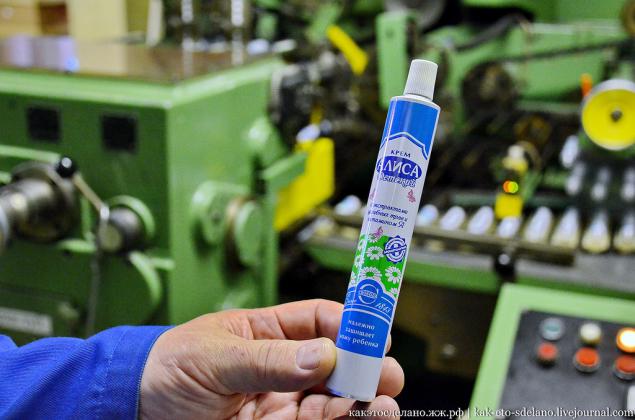
37
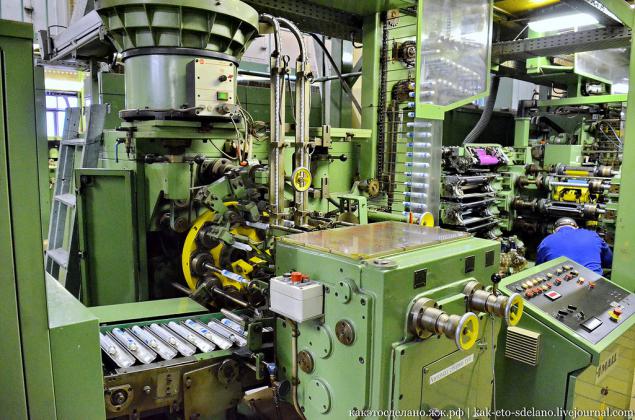
38
And in the end all the tubes are rolled at the last stage in this production - packing into boxes.
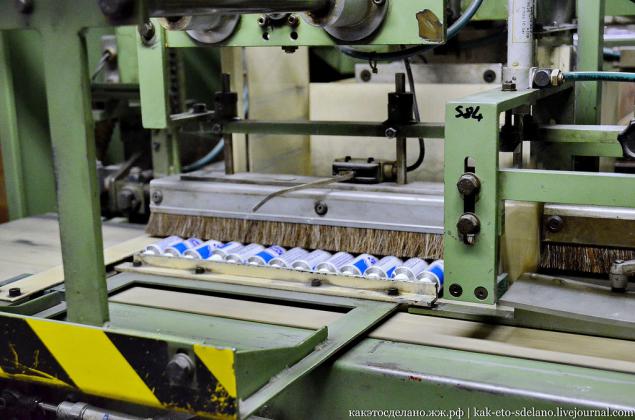
39
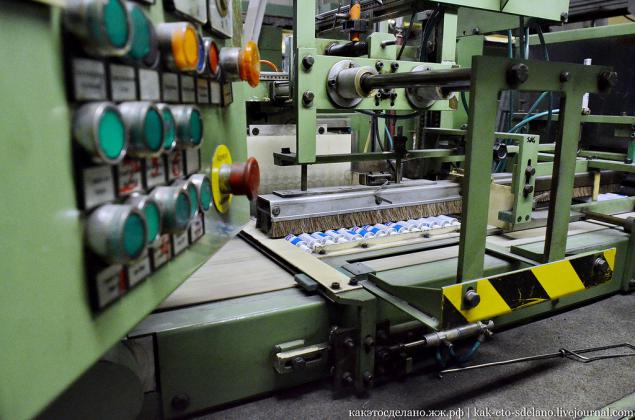
40
But that's not all! Working factory packs up the workpiece from one box to another, I understand that in this way it was easier to use tubes for further production process.
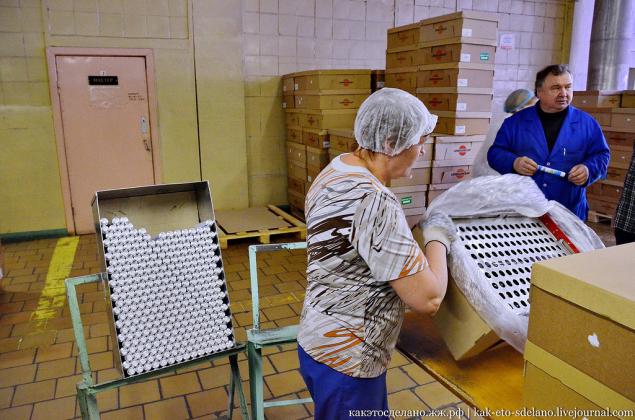
41
Here in the shop is yet another production line of tubes. It is older than the previous one, it more than forty years, but it is working properly. The principle of the manufacture of tubes on the line is not different from what you see above, the only difference is that the lower rate of line and color pattern that can be applied to the tube consists of only three colors.
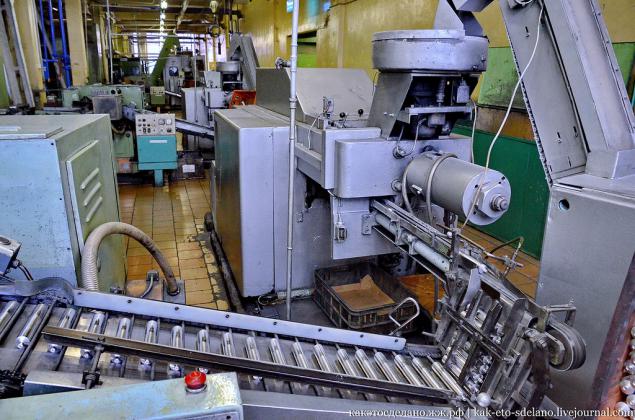
42
Many areas here, as we see the open, in contrast to the new line.
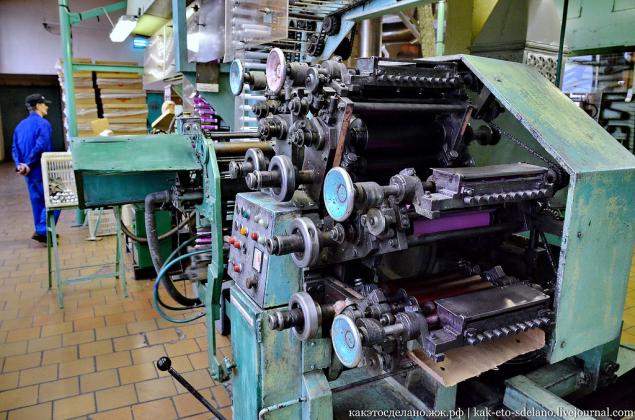
43
The drive looks different. And in general, this line of Soviet-made, and that - the German, unites them that both are quite effective. By the way, the volume of production at the factory so that these lines have to work around the clock, and nothing cope.
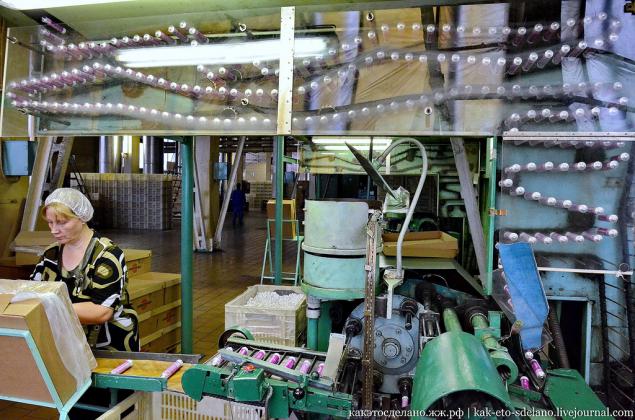
44
Pay attention to the diameter of the tubes - these wider.
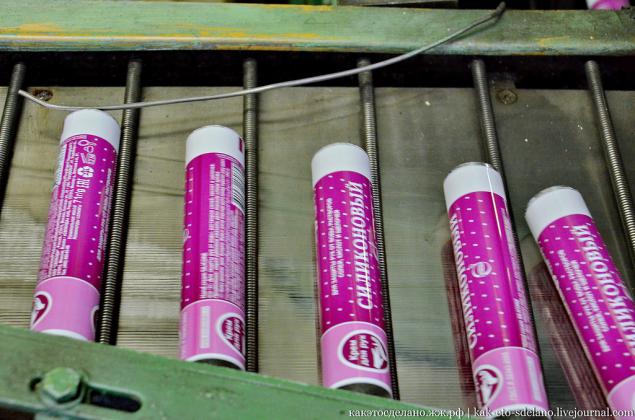
45
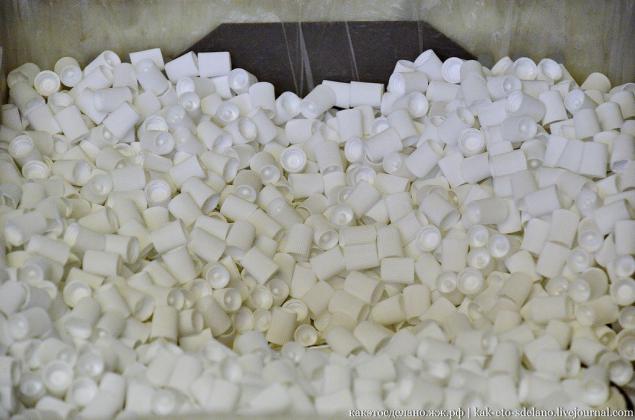
46
Well, like with aluminum tubami everything is clear, go to the shop where we make the usual laminated tubes.
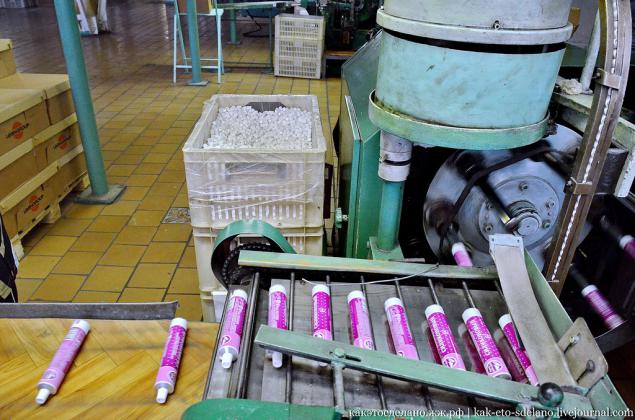
47
These devices do Bouchon. You ask what is it? Yes, I too was surprised when I heard this word from the master, who told me about the production.
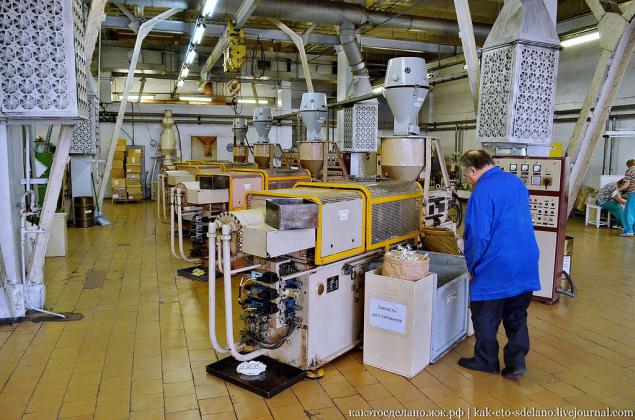
48
And this is only the cap on the tube. The term "Bouchon» (bouchon - cork, France.) Has come from the French language as well as many terms borrowed into Russian language.
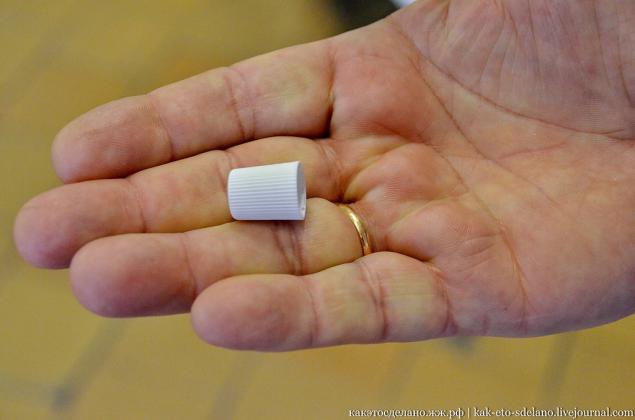
49
The machine extrudes hot plastic into the mold: half a minute, and you're done. Bouchon speed extrusion from the mold - 48 pcs. / Min. (Mold - 24 sockets, cycle rate - 20-25 sec.).
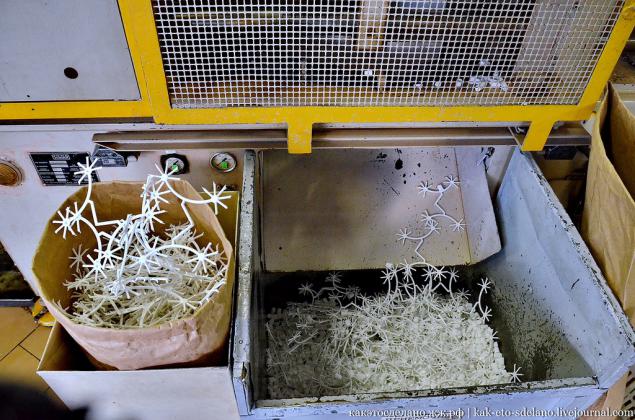
50
Scenic waste go back into the manufacturing process of the caps, it turns almost waste-free production.
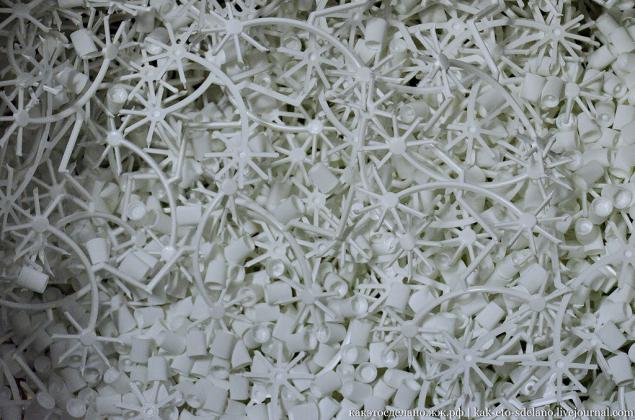
51
Plastic for Bouchon, by the way - domestic.
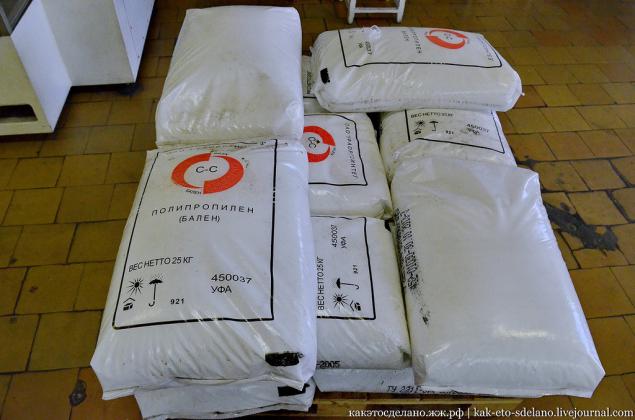
52
That is the very mold.
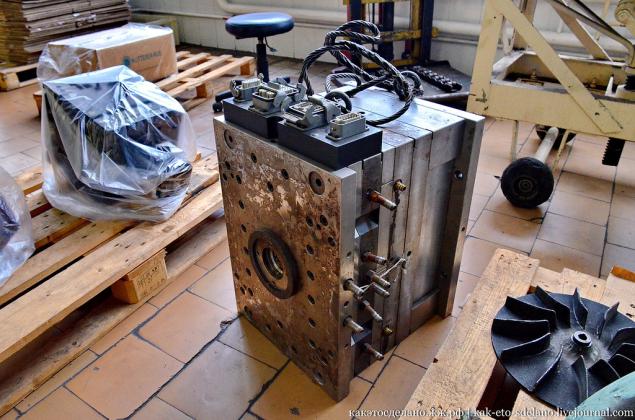
53
There is a new generation, where the plastic is injected into a separate cell, and manages completely without waste.
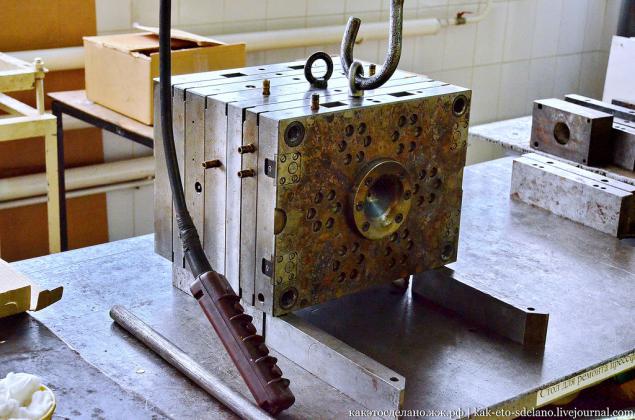
54
And here is the machine that makes the tube laminate. Modern equipment, takes up very little space, but the manufacturing process of tubes is not as interesting and exciting as opposed to the previous.
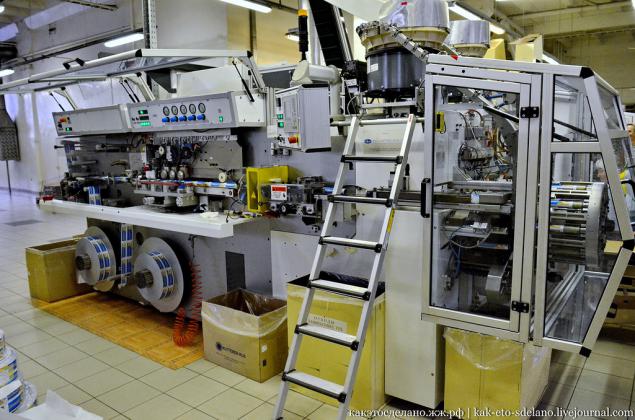
55
That's the tape tucked into the machine. You press a button and you're done!
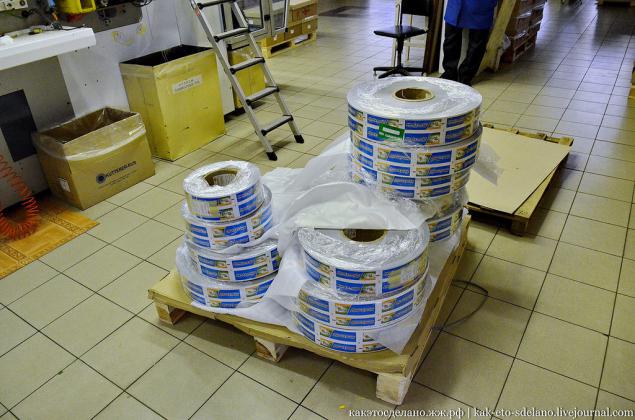
56
Among other things, the production of the factory complies with international quality standards ISO9001. Here, they place their orders, many large manufacturers, including foreign ones, for example, Procter & Gamble, which produced notorious for toothpaste (pictured below). By the end of 2013 commissioned by Procter & Gamble factory producing laminated tubes, is currently being negotiated for their production of aluminum tubes.
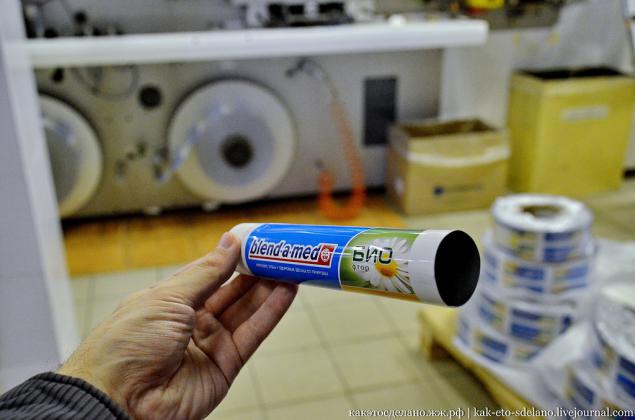
57
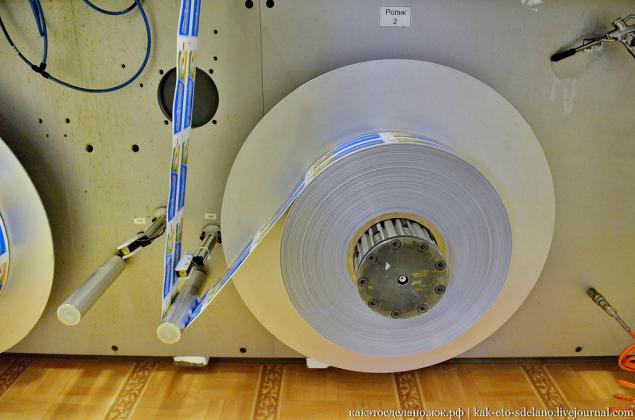
58
At the same time there are two roll fueled with laminate tubes for blanks, so that if one is over, you can immediately switch to the second.
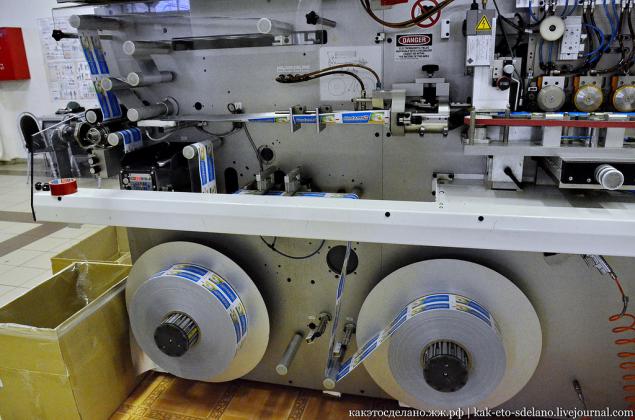
59
As I said, this laminate is not doing at the factory, he bought in China, it's easier.
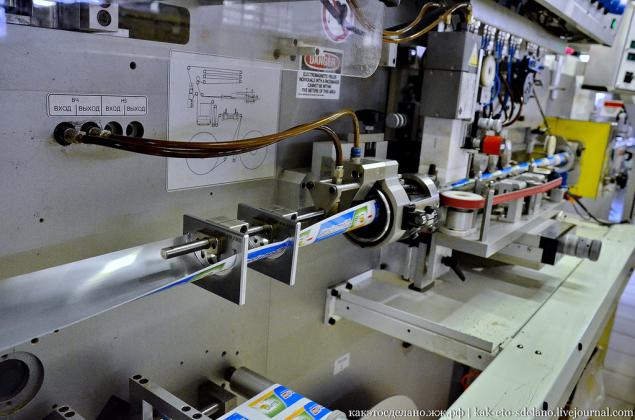
60
However, the laminate from which the tube is also not as simple as it seems. In fact, it consists of 5 layers, so that the package was of sufficient quality to be stored for a desired period of a certain product. Try to dissect the package from their toothpaste and tell me what you got).
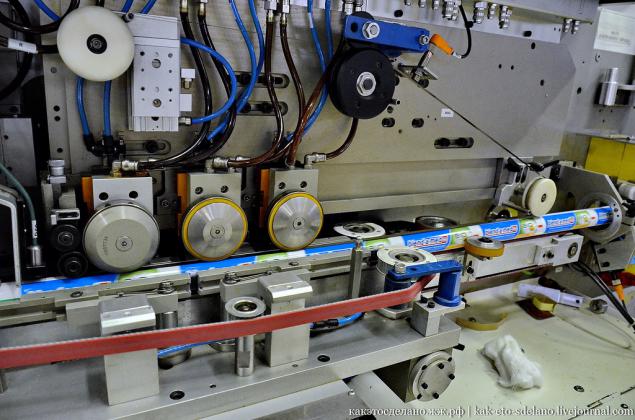
61
Next, I will not comment, because you will find a video where everything is quite clearly shown.
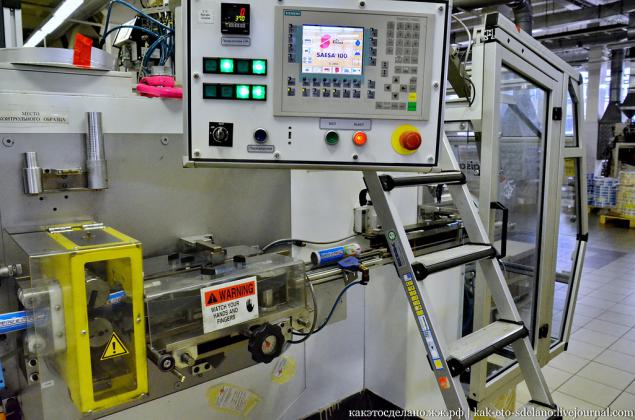
62
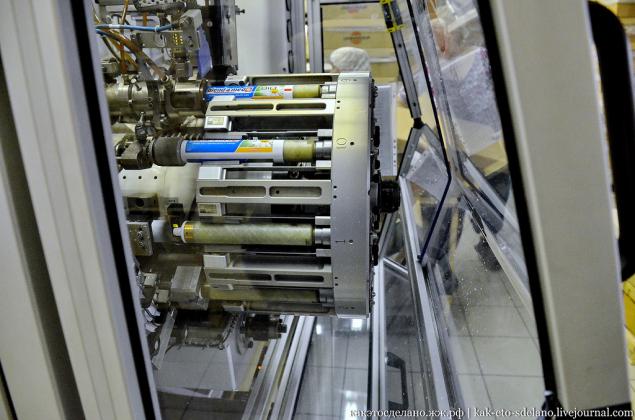
63
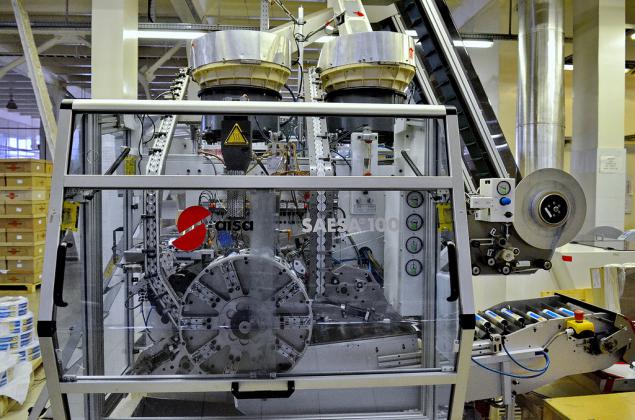
64
Well, at the end of the tube folded in a box manually.
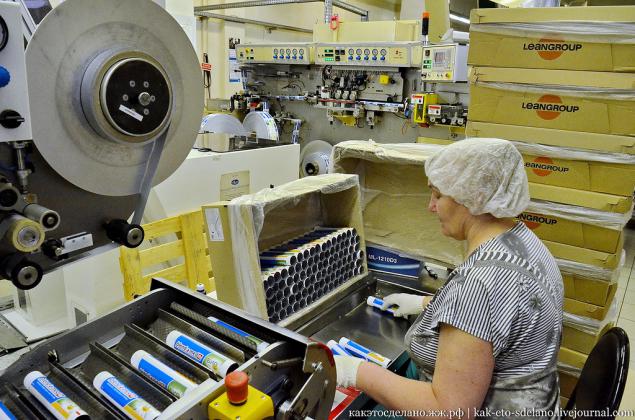
65
Laminant provide three production machine.
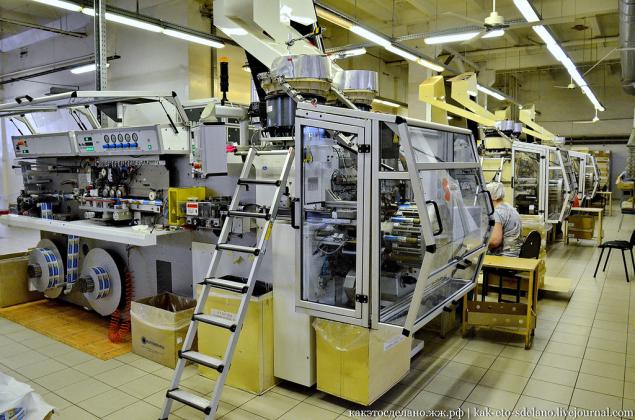
In this short video you can see how it all happens.
(FLASH MOVIE) 66
The factory is better known other own products (here also produce soap, cosmetics and toothpaste). I remember that my kids had the toothpaste.
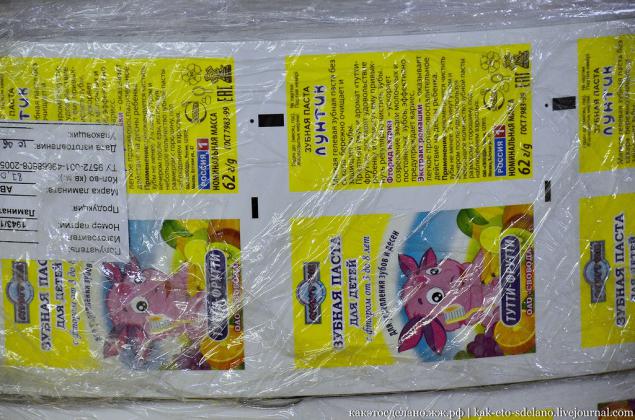
67
Well-known children's cream.
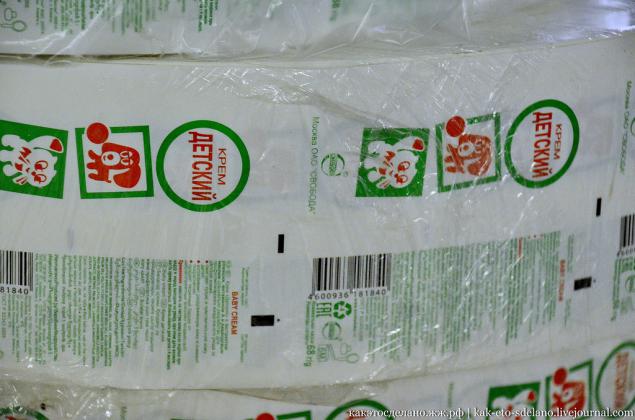
68
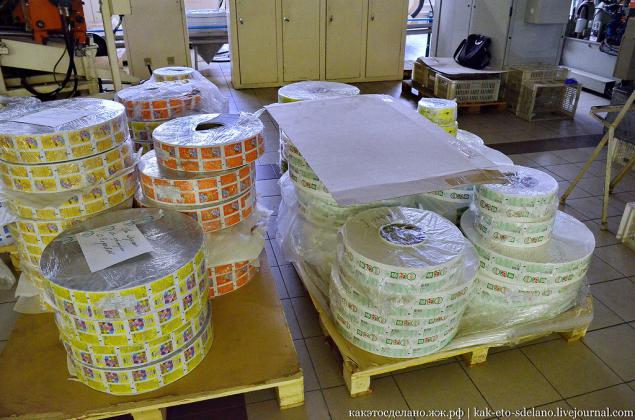
69
And for adults something.
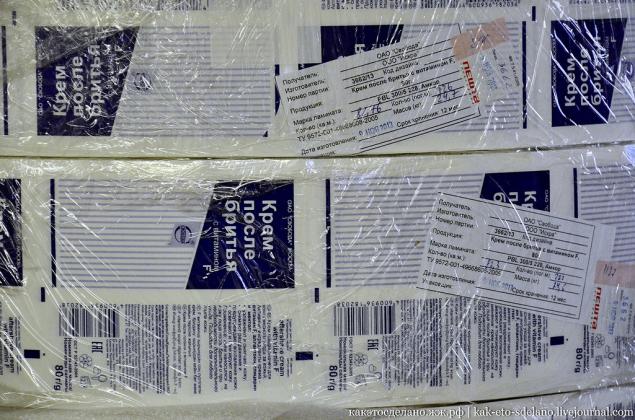
70
All products tubnogo production immediately checked in the laboratory for leaks, compliance with sanitary norms.
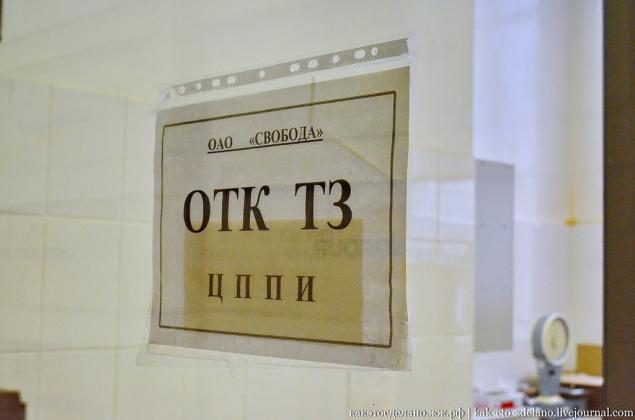
71
Each day is sampled packages (it can be seen that it is including vials), which is thoroughly checked.
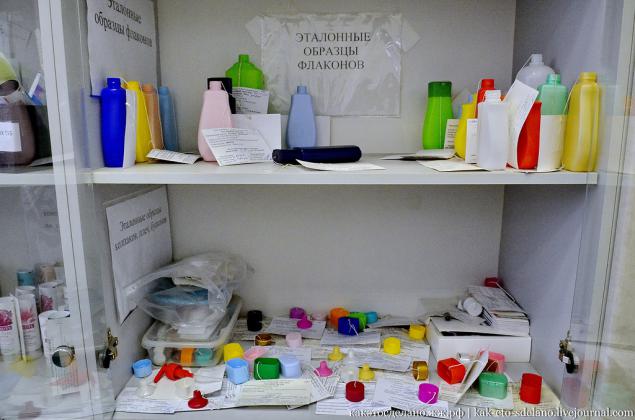
72
In general, as you can see what is on the shelves.
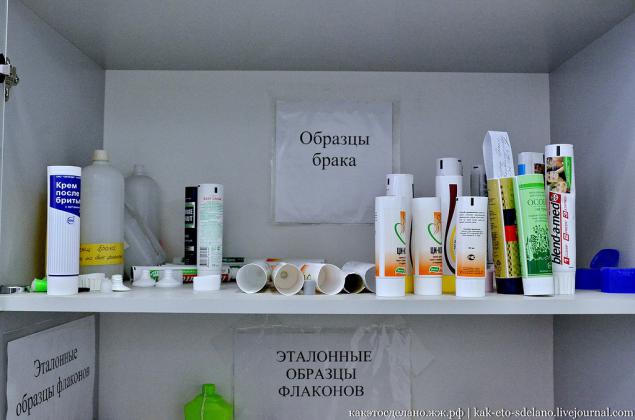
73
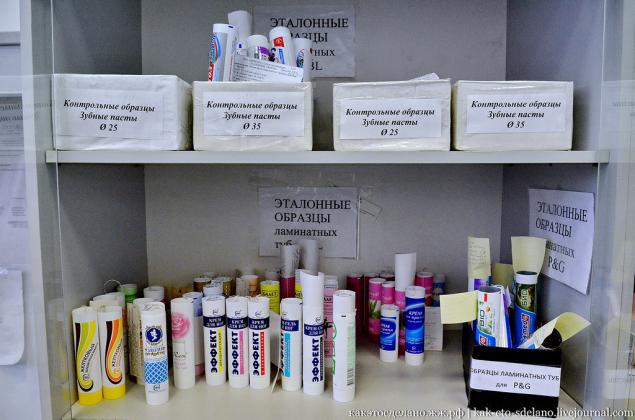
74
This unit is checked for leaks tubes. The product is fixed in the apparatus, closed part is immersed in water, to another part of the compressed air is blown.
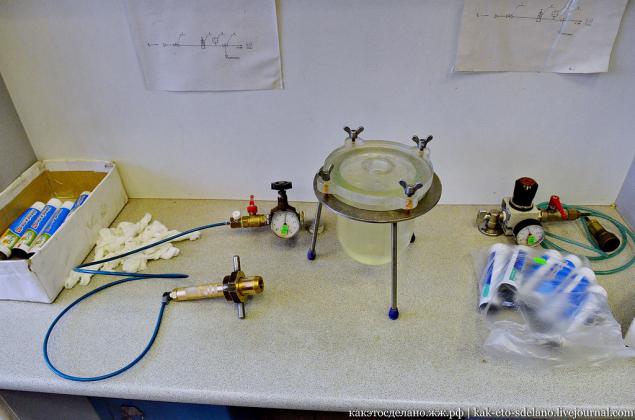
75
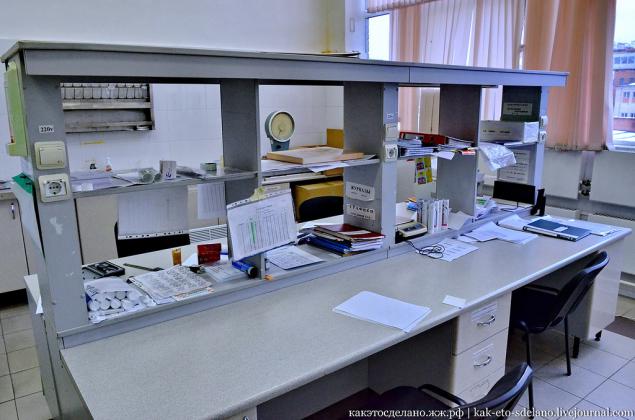
76
Well, like it, now you know how your tubes.
I thank the press service of the factory "Freedom" for the opportunity to see this interesting process and production director tubnogo Nikolai Zubkov for an informative tour.
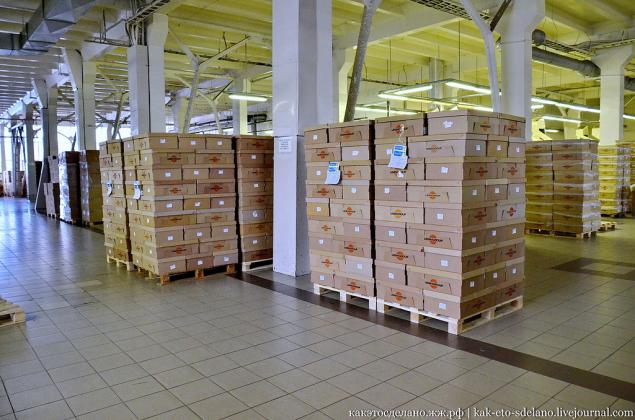
Source: