566
Mobile biogas plant to address environmental and energy issues
Every year Russia accumulates 300 million tons of dry equivalent organic waste of 250 million tonnes in agricultural production, 50 million tons in household waste. This waste can be raw material for biogas production. The potential annual amount of the biogas may be up to 90 billion m3.
The biogas product of anaerobic decomposition by microorganisms of organic substances. Calorific value of biogas is 21 to 25 MJ/m3. Depending on the chemical composition of raw materials stands out from 350 to 500 m3 of biogas per 1 ton of organic matter (dry weight).
The author offers a mobile unit for biogas production. The principle of operation is to supply waste or manure using a screw pump and flowing to the reactor, where the process of fermentation of raw materials. While a similar amount of sludge rises from the bottom of the reactor and is pushed into the buffer tank through the outlet pipe.
Fig.1. General view of mobile unified biogas plant.
Fig. 2. Schematic diagram of biogas plant.
1 — housing; 2 — Novozapolyarny; 3 — screw pump with a chopper;
4 — bioreactor; 5 — dry gas tank; 6 — heater; 7 — electric panel; 8 — manure storage.
The advantage of mobile unified biogas plant:
Fig. 3. Design mobile bioreactor.
The bioreactor can be divided into three parts: the upper — crust of large particles that rise with the gas bubbles; medium — liquid and bottom, which accumulate drop down into the sediment grazioplene mass. The reactor is a heated and insulated tank equipped with a mixing device.
In the reactor of live beneficial bacteria that feed on biomass. The waste product of bacteria is biogas. To maintain the life of bacteria requires a supply of food, heated up to 35-40 °C and periodic stirring. The resulting biogas collects in the vault (the tank), then passes the treatment system and is supplied to consumers. The reactor operates without air, sealed and harmless.
The gas system consists of gas distribution pipeline with a shut-off valve, condensate collector, tank, tee, pressure gauge, check valve, filters, CO2, H2S and consumers of biogas (stoves, hot water heaters, hot water boilers, etc.) the System is mounted only after the installation of biogas reactor in the working position.
According to the experimental researches of solid-phase metageneration and calculations of biogas for small farms the necessary volume of the bioreactor is 3.2-3.5 m 3 (1,4-1,6). As the bioreactor used non-stationary horizontal cylindrical body of the trailer, allowing us to quickly move from raw material input to one or more consumers, and to the place of unloading methane effluent, which increases the efficiency of the biogas plant in General. Moving the bioreactor by transport means such as Cars or tractors of various modifications.
Assume the use of optimum pumping equipment — screw screw pump with a chopper (Fig. 4). Helical screw pumps are used for viscous, dense, stringy masses and are suitable for the process of solid phase metageneration when raw humidity of 70-75% 25-40 dynamic viscosity, PA×s density 1250-1400 kg/m3.
Fig. 4. Screw pump with chopper.
Table 1. Specifications of a screw pump with a chopper.
Model
Flow,
m3/h
Pressure,
ATM
Power
kW
Dimensions
Mass, in kg
VN-3-1,0-560
1
6,0-8,0
0,75-2,2
550х540х1110
24
The advantages of a screw pump with a chopper:
The use of more efficient technological process of solid-phase metageneration requires the use of a mechanical mixing device. In view of the rather large dynamic viscosity of the substrate is necessary to apply a mechanical anchor stirrer frame with a maximum viscosity up to 100 PA×s., supplemented by lateral and vertical elements that improves circulation, mix the liquid (Fig. 5).
Fig. 5. A stirring device. Fig. 6. Mechanical anchor stirrer frame.Table 2. Specifications frame anchor stirrer.
The volume of the container
bioreactor, m3
Diameter of stirrer, mm
Rpm
mixer, min-1
Drive power, kW
3,2-3,5
1500
50
11
The advantages of the anchor stirrer frame:
Apparatus with a mechanical mixing device includes a bioreactor, drive, seal, shaft, agitator. The drive shaft and stirrer are connected to a single node, called a mixing device. The drive consists of motor, reducer and drive mounting. A mechanical stirrer is effective for processing heavy substrates with dry matter content (DM) to 35% .
If in the process of biogas production there is a need of mixing the less viscous liquid, the agitator frame is easily converted into anchor stirrer with exclusion from the construction of the transverse members .
The complete bioreactor mixing device for the process of solid phase metageneration is made on the basis of typical mechanical anchor stirrer frame Mr-2-1500-50-11-380V-ST20.
To maintain a mesophilic temperature regime throughout the year, the bioreactor needs to be heated and high-quality heat-waterproofing.
Basic type of heating of the reactor is electric, carried out by means of heating elements or thermolene. For heating the reactor to mesophilic temperatures using electricity an average of 0.4-0.6 kW per 1 m3 of reactor volume.
There are two systems of electrical heating of tanks:
Fig. 7. The heating panel.
Table 3. Technical characteristics of the heating panel.
Working
voltage, V
The output heat power, kW
Consumption current, And
Specific
heat, W/m2
Size
panel, mm
240
2000
8,3
3100
305x2134
In a heating system heating panel includes the following elements:
The outer part of the bioreactor must be insulated with modern and efficient heat-waterproofing coating — rigid polystyrene foamed polyurethane (p=40 kg/m3, λ=0,029 W/m·°C). Method of application — spraying. Due to the excellent adhesion of polyurethane foam to almost any material, the insulating layer does not require additional fastening to the base. Spray polyurethane foam formed by free foaming. Best insulation and strength characteristics are achieved thanks to uniform microscopic acuestate of the resulting material. Of moisture polyurethane foam not afraid, because it is a polymer. From the point of view of waterproofing properties of the material the figure is 99%. However, to increase the lifetime of the material up to 30-40 years, it is necessary to prevent cracking of the foam in contact with direct sunlight by covering it with fiberglass.
Gas collection system for biogas (the collection of the condensate tee and tank) is part of the mobile bioreactor and the gas system of the consumer (piping, valves, pressure gauge, check valve, filters, CO2, H2S) is installed directly at the customer's biogas and connect flexible gas hose with tee fitting of the gas tank.
For small biogas plants it is advisable to apply mechanical pressure regulators. "Dry" gas tank is cheaper and easier to manufacture. Flexible, but inextensible, the capacity of the dry gas tank — easily replaceable in case of wear cheap node. The gas tank is designed as a bellows. Its main function is ensuring stable given output pressure of biogas, and buffering a small instabilities in the production and consumption of biogas.
Thus, for mobile unified biogas plant it is necessary to use practical and economical "dry" gas tank made of plastic or rubber with a given load, to maintain the required pressure in the system user (0,013-0,050 ATM). Optimal design volume of the tank for small biogas plants will be 1m3.
Fig. 8. Gas tank "dry". Fig. 9. The gas system of the consumer. Coarse cleaning of the biogas from carbon dioxide produced by water filters or purification process ethanolamine. Coarse cleaning of the biogas from carbon dioxide allows it to be used for operation of gas burners of stoves and water boilers. Due to the corrosive action of hydrogen sulfide must be removed from biogas before use using the H2S filter.
As a gas pipeline, you can use both steel and plastic pipe resistant to UV sun rays.
Instrumentation used in a biogas plant include a float device, a thermometer for monitoring the level of raw materials and temperature in the bioreactor, as well as a manometer to determine the pressure in the gas system of the consumer.
Source: www.energosovet.ru/bul_stat.php?idd=551
The biogas product of anaerobic decomposition by microorganisms of organic substances. Calorific value of biogas is 21 to 25 MJ/m3. Depending on the chemical composition of raw materials stands out from 350 to 500 m3 of biogas per 1 ton of organic matter (dry weight).
The author offers a mobile unit for biogas production. The principle of operation is to supply waste or manure using a screw pump and flowing to the reactor, where the process of fermentation of raw materials. While a similar amount of sludge rises from the bottom of the reactor and is pushed into the buffer tank through the outlet pipe.
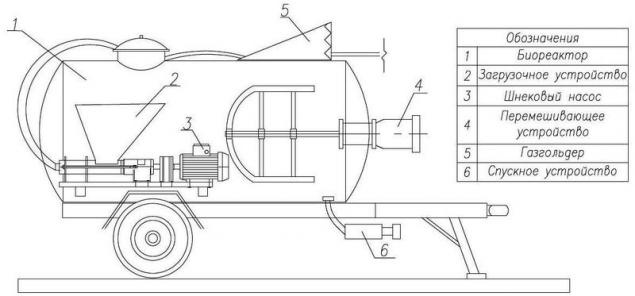
Fig.1. General view of mobile unified biogas plant.
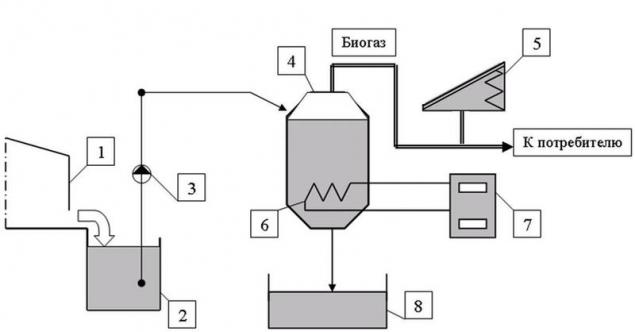
Fig. 2. Schematic diagram of biogas plant.
1 — housing; 2 — Novozapolyarny; 3 — screw pump with a chopper;
4 — bioreactor; 5 — dry gas tank; 6 — heater; 7 — electric panel; 8 — manure storage.
The advantage of mobile unified biogas plant:
- the mobility of the mobile biogas plant;
- intensification of the biogas process, solid phase metageneration;
- effective mixing device;
- automated loading system and grinding;
- modern heating system;
- the quality of the methane effluent;
- small dimensions of the plant.
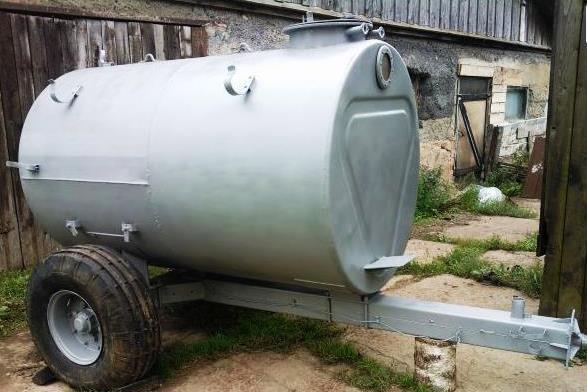
Fig. 3. Design mobile bioreactor.
The bioreactor can be divided into three parts: the upper — crust of large particles that rise with the gas bubbles; medium — liquid and bottom, which accumulate drop down into the sediment grazioplene mass. The reactor is a heated and insulated tank equipped with a mixing device.
In the reactor of live beneficial bacteria that feed on biomass. The waste product of bacteria is biogas. To maintain the life of bacteria requires a supply of food, heated up to 35-40 °C and periodic stirring. The resulting biogas collects in the vault (the tank), then passes the treatment system and is supplied to consumers. The reactor operates without air, sealed and harmless.
The gas system consists of gas distribution pipeline with a shut-off valve, condensate collector, tank, tee, pressure gauge, check valve, filters, CO2, H2S and consumers of biogas (stoves, hot water heaters, hot water boilers, etc.) the System is mounted only after the installation of biogas reactor in the working position.
According to the experimental researches of solid-phase metageneration and calculations of biogas for small farms the necessary volume of the bioreactor is 3.2-3.5 m 3 (1,4-1,6). As the bioreactor used non-stationary horizontal cylindrical body of the trailer, allowing us to quickly move from raw material input to one or more consumers, and to the place of unloading methane effluent, which increases the efficiency of the biogas plant in General. Moving the bioreactor by transport means such as Cars or tractors of various modifications.
Assume the use of optimum pumping equipment — screw screw pump with a chopper (Fig. 4). Helical screw pumps are used for viscous, dense, stringy masses and are suitable for the process of solid phase metageneration when raw humidity of 70-75% 25-40 dynamic viscosity, PA×s density 1250-1400 kg/m3.
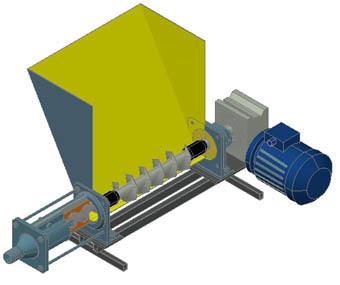
Fig. 4. Screw pump with chopper.
Table 1. Specifications of a screw pump with a chopper.
Model
Flow,
m3/h
Pressure,
ATM
Power
kW
Dimensions
Mass, in kg
VN-3-1,0-560
1
6,0-8,0
0,75-2,2
550х540х1110
24
The advantages of a screw pump with a chopper:
- wear resistant polyurethane stator;
- adjustable stator, which increases the resource of his work;
- hardened rotor steel 25KHGSA;
- screw feeder;
- the hopper for loading of raw materials;
- shaft seal soft seal from Kevlar-Teflon cord;
- flow parts material — steel ST20.
- bunker 30-150.;
- output hose connection or flange.
The use of more efficient technological process of solid-phase metageneration requires the use of a mechanical mixing device. In view of the rather large dynamic viscosity of the substrate is necessary to apply a mechanical anchor stirrer frame with a maximum viscosity up to 100 PA×s., supplemented by lateral and vertical elements that improves circulation, mix the liquid (Fig. 5).
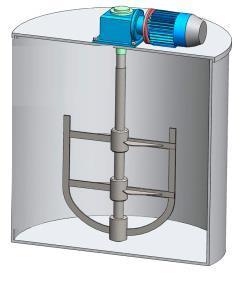
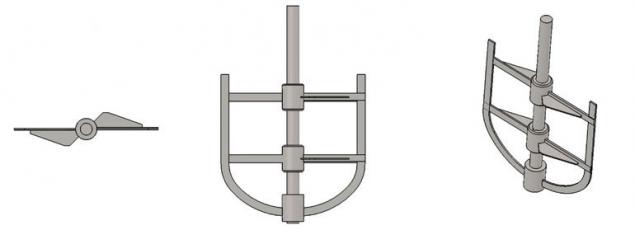
Fig. 5. A stirring device. Fig. 6. Mechanical anchor stirrer frame.Table 2. Specifications frame anchor stirrer.
The volume of the container
bioreactor, m3
Diameter of stirrer, mm
Rpm
mixer, min-1
Drive power, kW
3,2-3,5
1500
50
11
The advantages of the anchor stirrer frame:
- performed mixing heavy and viscous liquids;
- increasing the intensity of heat exchange;
- eliminates the formation of sludge on the walls of the container.
Apparatus with a mechanical mixing device includes a bioreactor, drive, seal, shaft, agitator. The drive shaft and stirrer are connected to a single node, called a mixing device. The drive consists of motor, reducer and drive mounting. A mechanical stirrer is effective for processing heavy substrates with dry matter content (DM) to 35% .
If in the process of biogas production there is a need of mixing the less viscous liquid, the agitator frame is easily converted into anchor stirrer with exclusion from the construction of the transverse members .
The complete bioreactor mixing device for the process of solid phase metageneration is made on the basis of typical mechanical anchor stirrer frame Mr-2-1500-50-11-380V-ST20.
To maintain a mesophilic temperature regime throughout the year, the bioreactor needs to be heated and high-quality heat-waterproofing.
Basic type of heating of the reactor is electric, carried out by means of heating elements or thermolene. For heating the reactor to mesophilic temperatures using electricity an average of 0.4-0.6 kW per 1 m3 of reactor volume.
There are two systems of electrical heating of tanks:
- the system of external heating on the basis of strip heaters, heating cables or panels, which are mounted on the vessel wall of the tank beneath the thermal insulation layer;
- the system of internal heating on the basis of the mortise or immersion heaters.
- ease of installation;
- the maximum contact area;
- the minimum the space occupied by the reactor;
- simple Troubleshooting.
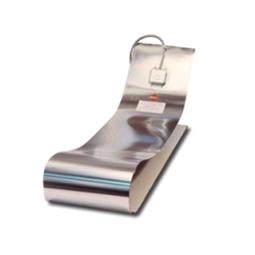
Fig. 7. The heating panel.
Table 3. Technical characteristics of the heating panel.
Working
voltage, V
The output heat power, kW
Consumption current, And
Specific
heat, W/m2
Size
panel, mm
240
2000
8,3
3100
305x2134
In a heating system heating panel includes the following elements:
- high temperature current-carrying conductor;
- limiter thermal protection system;
- protective metal shell;
- heating element of high temperature alloy;
- laminated insulation of high temperature silicone rubber.
The outer part of the bioreactor must be insulated with modern and efficient heat-waterproofing coating — rigid polystyrene foamed polyurethane (p=40 kg/m3, λ=0,029 W/m·°C). Method of application — spraying. Due to the excellent adhesion of polyurethane foam to almost any material, the insulating layer does not require additional fastening to the base. Spray polyurethane foam formed by free foaming. Best insulation and strength characteristics are achieved thanks to uniform microscopic acuestate of the resulting material. Of moisture polyurethane foam not afraid, because it is a polymer. From the point of view of waterproofing properties of the material the figure is 99%. However, to increase the lifetime of the material up to 30-40 years, it is necessary to prevent cracking of the foam in contact with direct sunlight by covering it with fiberglass.
Gas collection system for biogas (the collection of the condensate tee and tank) is part of the mobile bioreactor and the gas system of the consumer (piping, valves, pressure gauge, check valve, filters, CO2, H2S) is installed directly at the customer's biogas and connect flexible gas hose with tee fitting of the gas tank.
For small biogas plants it is advisable to apply mechanical pressure regulators. "Dry" gas tank is cheaper and easier to manufacture. Flexible, but inextensible, the capacity of the dry gas tank — easily replaceable in case of wear cheap node. The gas tank is designed as a bellows. Its main function is ensuring stable given output pressure of biogas, and buffering a small instabilities in the production and consumption of biogas.
Thus, for mobile unified biogas plant it is necessary to use practical and economical "dry" gas tank made of plastic or rubber with a given load, to maintain the required pressure in the system user (0,013-0,050 ATM). Optimal design volume of the tank for small biogas plants will be 1m3.
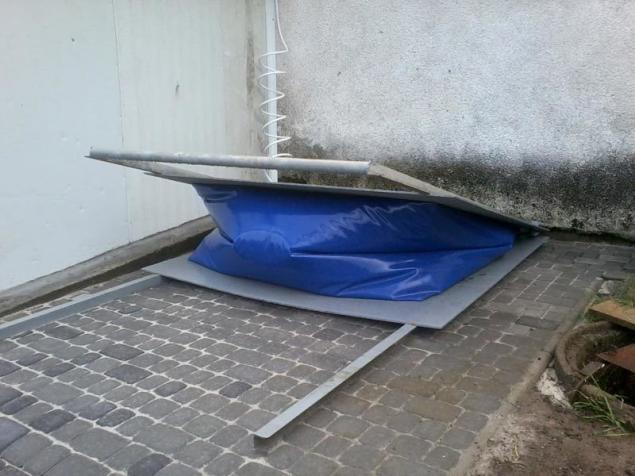
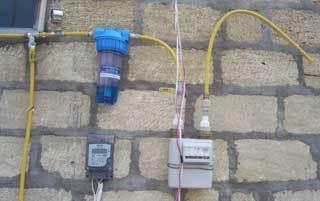
Fig. 8. Gas tank "dry". Fig. 9. The gas system of the consumer. Coarse cleaning of the biogas from carbon dioxide produced by water filters or purification process ethanolamine. Coarse cleaning of the biogas from carbon dioxide allows it to be used for operation of gas burners of stoves and water boilers. Due to the corrosive action of hydrogen sulfide must be removed from biogas before use using the H2S filter.
As a gas pipeline, you can use both steel and plastic pipe resistant to UV sun rays.
Instrumentation used in a biogas plant include a float device, a thermometer for monitoring the level of raw materials and temperature in the bioreactor, as well as a manometer to determine the pressure in the gas system of the consumer.
Source: www.energosovet.ru/bul_stat.php?idd=551
Bike path out of solar panels - a promising future or an extra investment?
Relationship with a strong man: it is necessary to You?