662
Repair flywheel motor ...
Just write that he intended to post 17 pictures by the way, they are very clickable and can thereby slightly increasing.
Sometimes I think that Yap is high time to open a new chapter ... professional. This is because today the Internet has long ceased to be fun just office workers, here and it turns out that many ordinary laborers also want to share what is in itself and it looks like their real Job. And interestingly, a lot of creative people are showing interest in such topics ... What, for example, is worth at least that's a theme about Diesel, I was wondering.
That is why I decided to create another technocratic subject, in the hope that someone will just curious to know some technical details.
Many years ago, my father used to say to me one piece of advice: "That if you do not study hard, you will be all my life to turn the big key big nut 27 (hz. Why 27?) ... And if you get a good education, then nothing screwdriver lift heavier dick do not have »
Years later, my father had long been dead, and that he is very surprised that he was "the son of" sometimes you have to turn the nuts as much as the size of a 100. (keys there nedetstskie! No rocking simulator does not need to bleat!) At the same time I'm pretty successfully studied every technical disciplines. But something like that happened in life that have to work with large assemblies, and even in a foreign land.
As an example (today completed work) look at the flywheel of marine diesel. Type "one day my work»
According to the established tradition on Yap: this is my first dick knows what position ... but still, please do not hit if it will be boring.
So, with the engine flywheel removed. In general, it is certainly not the biggest ... the diameter of about one meter and a height of 0, 35 m.
From the top of the engine room it has to drag with a few hand 2tonnyh winches, as the weight of the handwheel is 1480 kg.
He will be brought to the shop for repair. Since he has a damper load to compensate for torsional vibrations of the crankshaft of the diesel engine ...
So they brought him into the shop.
Open the lid. We discover the cause of his poor performance. Damper cargo jammed in the flywheel housing, could not rotate.
On the inner surface of the load applied babbitt coating (such as shell bearings of conventional engines.)
Strong teaser on the cover Babbitt was not allowed to rotate freely load. As a lubricant in the flywheel using a silicone gel having a relatively high viscosity, which enables to extinguish the crankshaft rotational jerks.
Under renovation is supposed to dismantle, wash, fix irregularities and then re-assemble and fill the new silicone grease.
Washed from the old grease instructed a staff member about whom it is written by me details HERE HERE Tut
It is a diligent girl who is not afraid zashkvaritsya all sorts of sticky liquids. A silicone grease, this is very sticky and viscous, wash and scour was hard.
So all washed off and wiped dry. At this time, others cleared the teaser on the cargo ...
It's time to collect.
Before you put the goods into the flywheel in its cavity is necessary to first pour about half a kilo here is a lubricant.
It should be noted that almost all of the remaining workers are very inspired at the sight of grease, once started any explicit jokes about the fact that & quot; good to pee yourself a little in reserve in case the cause to his superiors on the carpet for a showdown ... kind of like, with cream, any anal punishment are not afraid of. & quot;
As well as Girl laundered flywheel from an old grease in her address it was also jokes, though my knowledge of a foreign language does not cover many areas, but I will only accept something like "one devchonka- entire two cups of grease .. "The devil knows what they meant ... other folk different mentality.
By the way, she did not take offense, smiled and cut a new gaskets paronite.
So, after brushing the wall cavity of the flywheel slowly lower the load down.
Lubricated and the truth comes gently, even such a huge brutal glands Even with a small warp.
Lowering the flywheel, it is necessary to wait until the grease squeezed out upward by filling chutes. It should be slightly rotate the goods to remove any air from the bottom. (By the way, despite the fact that cargo weighs about 500 kg itself, rotate it in the case, as it turns out, is not difficult. All the same grease-good.)
All this takes time, so you can roll the fool a little, until the bubbles making their way through a viscous fluid.
Here, it is seen as a lubricant starts squeezed up through the supply channels ... (even in sunlight looked nice - a bit sorry that I have no reflex)
Next, put the lid, twisted bolts to 220N \ m and is set for further filling of the reservoir cavity and removal of air. (Reminiscent of pumping the brake system of the car)
The tank I put together an impromptu of adapters for the pipeline. Top connects compressed air and set the pressure of 3-5 atmospheres. For if not to create pressure from above, with such a self-lubricant viscosity zatechet inside, perhaps a month.
So, first, through the drainage holes, begin to emerge large air bubbles.
... Well, then, and a little ...
It seemed to me, it looks beautiful, just like molten glass.
(Sorry, had to withdraw the budget calculator caliper Sony Eriksson, so the macro mode turned out - not so hot.)
Well, like all the collected ...
(it is necessary to carry the flywheel to the dock in another part of the city)
So, after the flywheel dragged back into the engine room on ship-it was time to put it on the engine. Here, too, not everything is simple.
Let me remind you that a piece of iron weighs almost half a ton, and she sits on the shaft at a very hard landing. No sledgehammer will not help. Come to the aid of hydraulic presses. But just the same it is impossible to drive in. Here is some trick. The shaft has a threaded hole for connecting a tube which is fed by a special oil with very high pressure. (Oil on different properties for pressing and pulling out)
Also formed on the shaft a helical groove along which oil is supplied uniformly in the "space between the shaft and the flywheel". When that gap there at all, but there is a transition landing ", negative clearance", ie with interference. That is, it turns out that the high pressure oil as it "stretches" the piece of metal, creating a gap.
To create such pressure "unclamping" used here is a manual pump.
By the way, this black flexible tube few meters long to connect the pump shaft and costs about $ 350. (This I do not ponimayu- for that kind of money?)
Only in this case, it becomes possible to extrude the flywheel using the same hydraulic press, where pressure is applied rather high about 700-800 atmospheres. (This yellow hose)
(Incidentally, according to instructions during operation, take the hands of those compounds of the hose is prohibited because there were times when torn nuts and spray oil cut people hands apart (I was on the course, where we were shown photographs of such damages brush)
. Drive in a flywheel shaft, press "unclamping" is reset, but the effort Joining can only be removed after half an hour.
(visible in the same tube, which costs 300 $)
Of course, there are motors and flywheels are much larger.
But on this ship are four that's such a small diesel engine to run on a single load.
Sfotat rhinestones all difficult, so the shot came here only two of the motor.
In general, I have everything. Thank you for attention.
It is likely that where I wrote incorrectly, because it's not my job to teach ...
Therefore I agree to a healthy criticism.
Source:
Sometimes I think that Yap is high time to open a new chapter ... professional. This is because today the Internet has long ceased to be fun just office workers, here and it turns out that many ordinary laborers also want to share what is in itself and it looks like their real Job. And interestingly, a lot of creative people are showing interest in such topics ... What, for example, is worth at least that's a theme about Diesel, I was wondering.
That is why I decided to create another technocratic subject, in the hope that someone will just curious to know some technical details.
Many years ago, my father used to say to me one piece of advice: "That if you do not study hard, you will be all my life to turn the big key big nut 27 (hz. Why 27?) ... And if you get a good education, then nothing screwdriver lift heavier dick do not have »
Years later, my father had long been dead, and that he is very surprised that he was "the son of" sometimes you have to turn the nuts as much as the size of a 100. (keys there nedetstskie! No rocking simulator does not need to bleat!) At the same time I'm pretty successfully studied every technical disciplines. But something like that happened in life that have to work with large assemblies, and even in a foreign land.
As an example (today completed work) look at the flywheel of marine diesel. Type "one day my work»
According to the established tradition on Yap: this is my first dick knows what position ... but still, please do not hit if it will be boring.
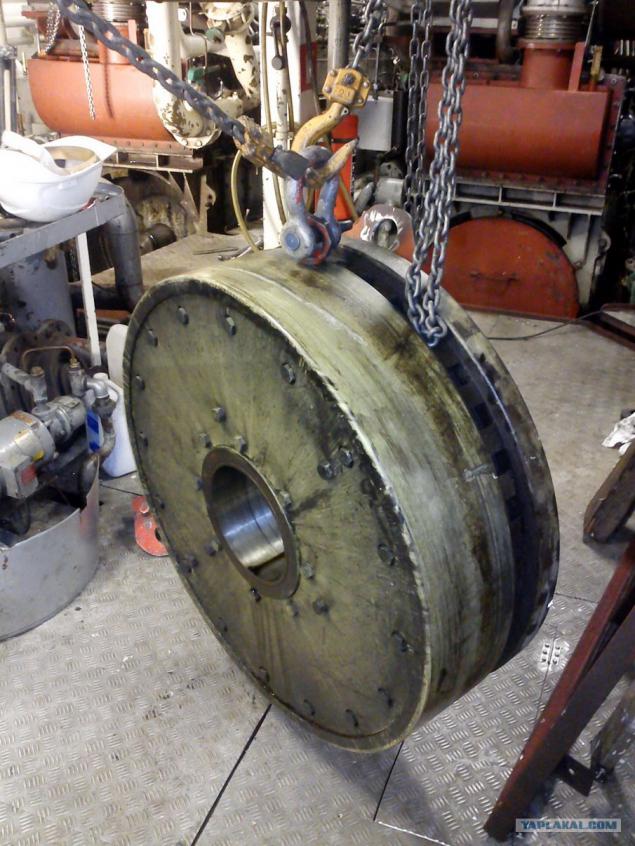
So, with the engine flywheel removed. In general, it is certainly not the biggest ... the diameter of about one meter and a height of 0, 35 m.
From the top of the engine room it has to drag with a few hand 2tonnyh winches, as the weight of the handwheel is 1480 kg.
He will be brought to the shop for repair. Since he has a damper load to compensate for torsional vibrations of the crankshaft of the diesel engine ...
So they brought him into the shop.
Open the lid. We discover the cause of his poor performance. Damper cargo jammed in the flywheel housing, could not rotate.
On the inner surface of the load applied babbitt coating (such as shell bearings of conventional engines.)
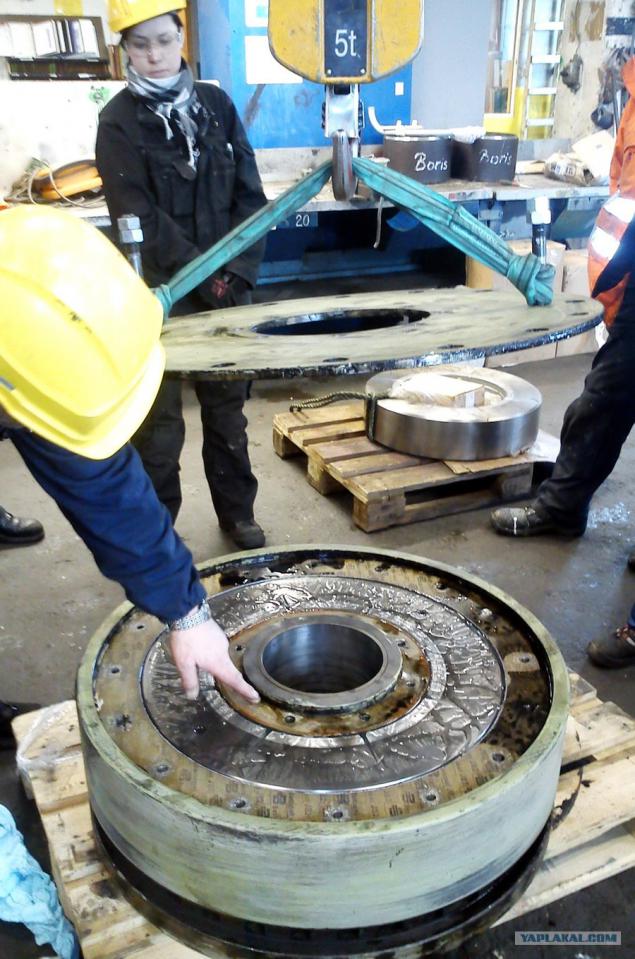
Strong teaser on the cover Babbitt was not allowed to rotate freely load. As a lubricant in the flywheel using a silicone gel having a relatively high viscosity, which enables to extinguish the crankshaft rotational jerks.
Under renovation is supposed to dismantle, wash, fix irregularities and then re-assemble and fill the new silicone grease.
Washed from the old grease instructed a staff member about whom it is written by me details HERE HERE Tut
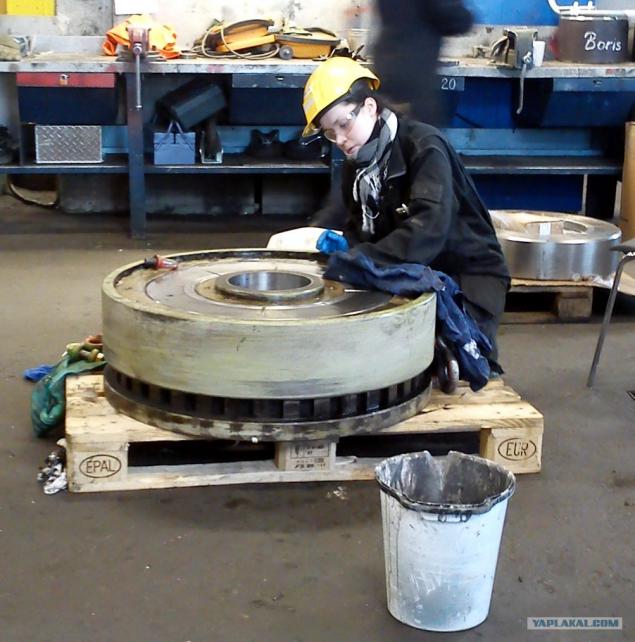
It is a diligent girl who is not afraid zashkvaritsya all sorts of sticky liquids. A silicone grease, this is very sticky and viscous, wash and scour was hard.
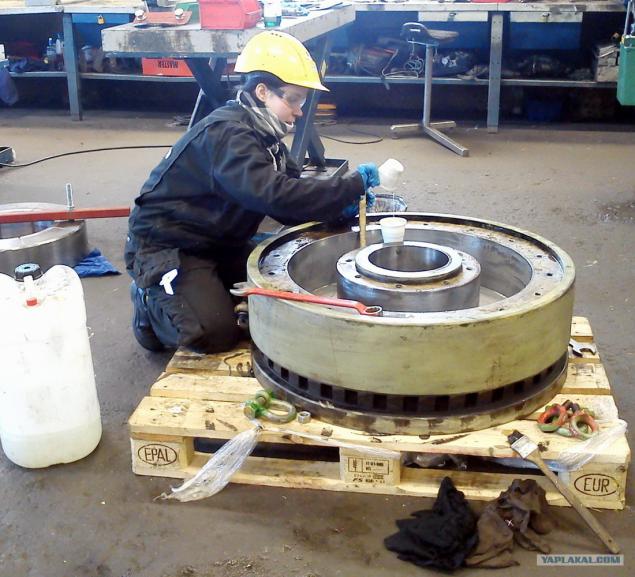
So all washed off and wiped dry. At this time, others cleared the teaser on the cargo ...
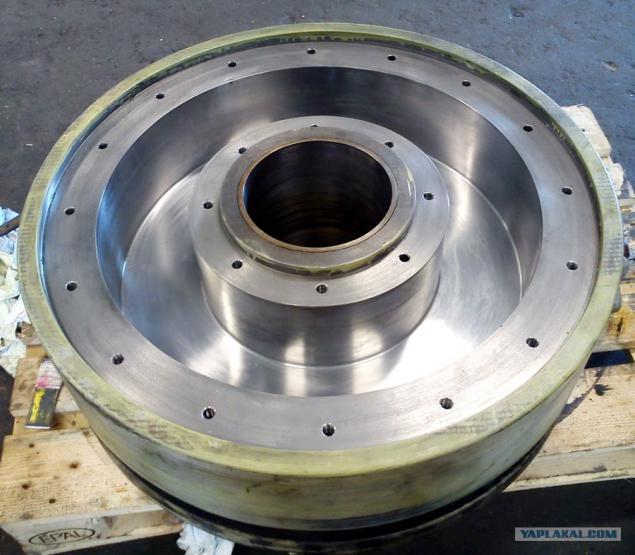
It's time to collect.
Before you put the goods into the flywheel in its cavity is necessary to first pour about half a kilo here is a lubricant.
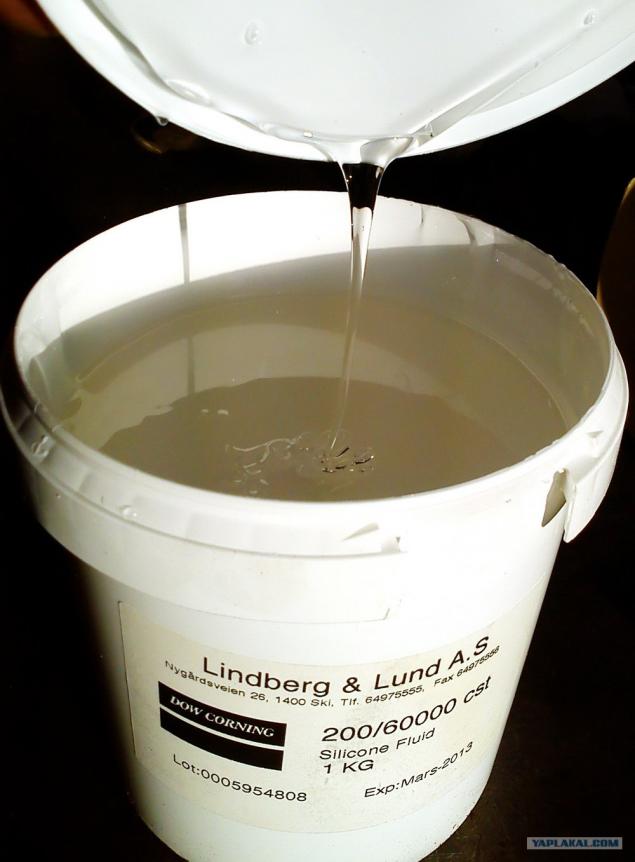
It should be noted that almost all of the remaining workers are very inspired at the sight of grease, once started any explicit jokes about the fact that & quot; good to pee yourself a little in reserve in case the cause to his superiors on the carpet for a showdown ... kind of like, with cream, any anal punishment are not afraid of. & quot;
As well as Girl laundered flywheel from an old grease in her address it was also jokes, though my knowledge of a foreign language does not cover many areas, but I will only accept something like "one devchonka- entire two cups of grease .. "The devil knows what they meant ... other folk different mentality.
By the way, she did not take offense, smiled and cut a new gaskets paronite.
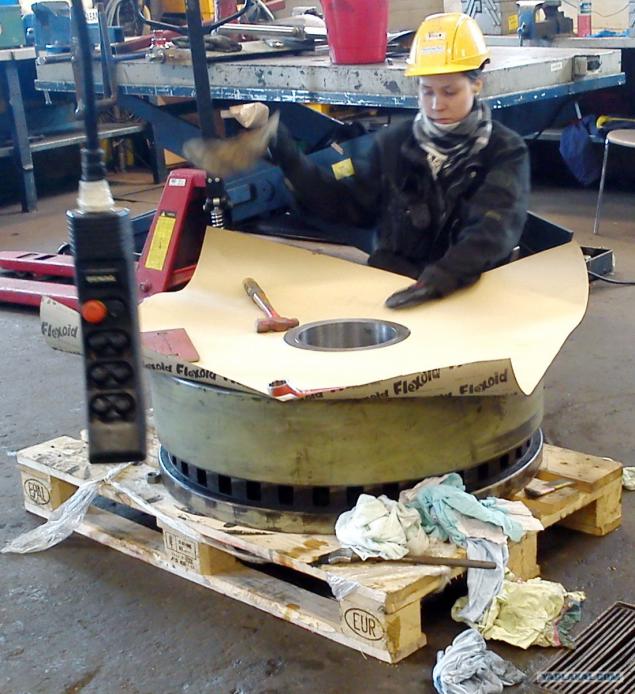
So, after brushing the wall cavity of the flywheel slowly lower the load down.
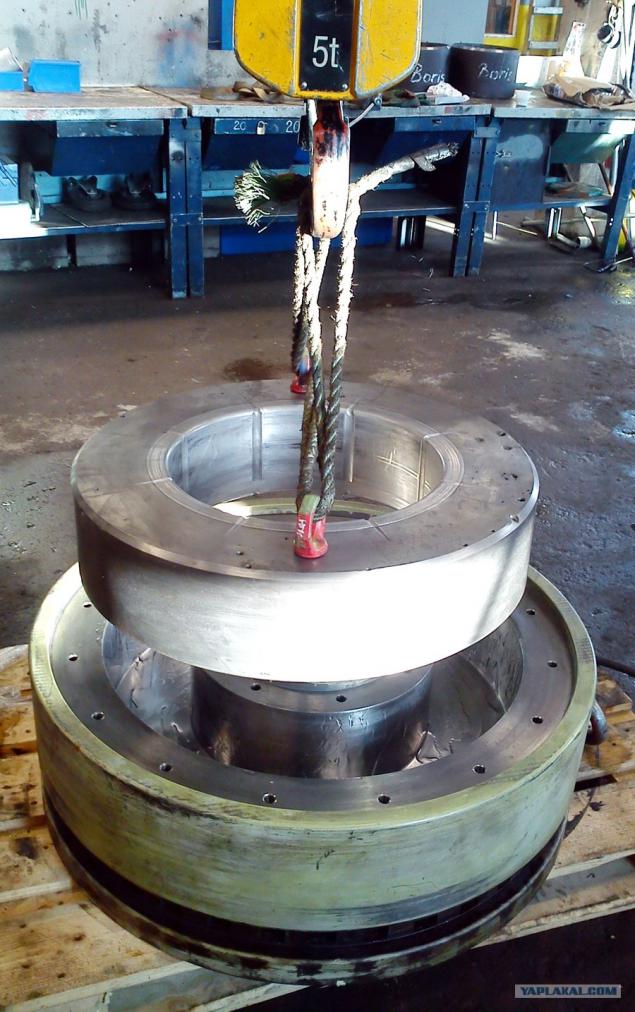
Lubricated and the truth comes gently, even such a huge brutal glands Even with a small warp.
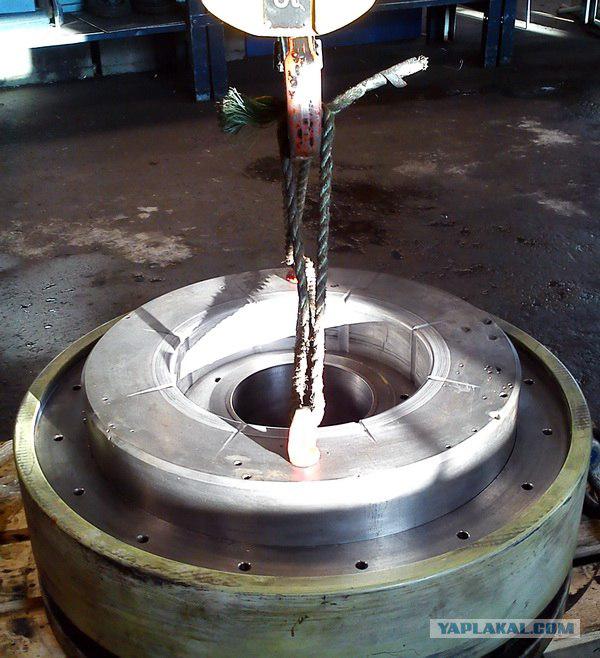
Lowering the flywheel, it is necessary to wait until the grease squeezed out upward by filling chutes. It should be slightly rotate the goods to remove any air from the bottom. (By the way, despite the fact that cargo weighs about 500 kg itself, rotate it in the case, as it turns out, is not difficult. All the same grease-good.)
All this takes time, so you can roll the fool a little, until the bubbles making their way through a viscous fluid.
Here, it is seen as a lubricant starts squeezed up through the supply channels ... (even in sunlight looked nice - a bit sorry that I have no reflex)
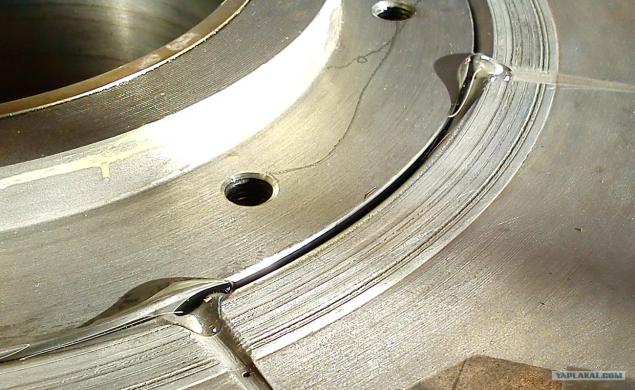
Next, put the lid, twisted bolts to 220N \ m and is set for further filling of the reservoir cavity and removal of air. (Reminiscent of pumping the brake system of the car)
The tank I put together an impromptu of adapters for the pipeline. Top connects compressed air and set the pressure of 3-5 atmospheres. For if not to create pressure from above, with such a self-lubricant viscosity zatechet inside, perhaps a month.
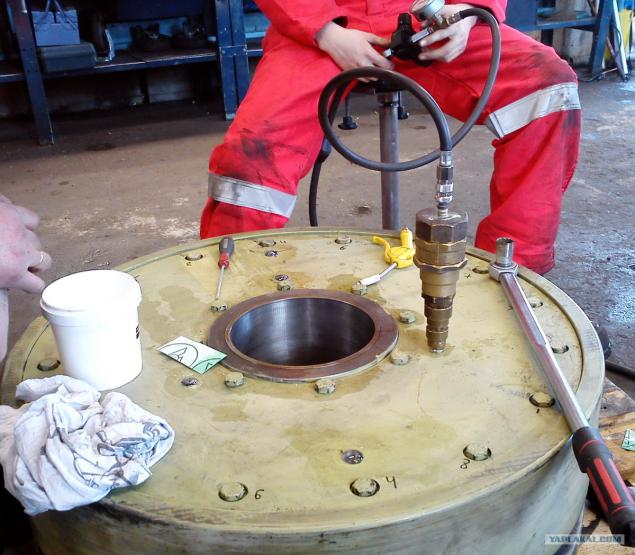
So, first, through the drainage holes, begin to emerge large air bubbles.
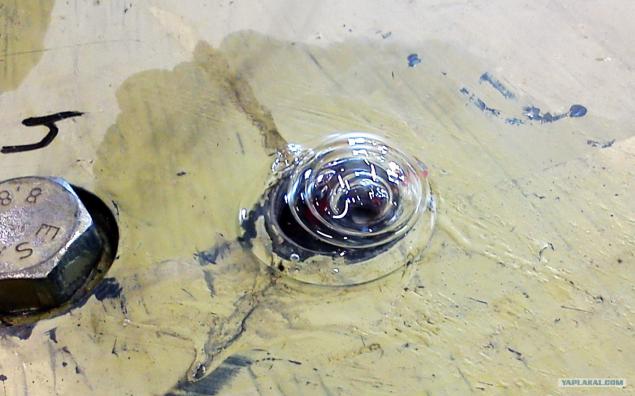
... Well, then, and a little ...
It seemed to me, it looks beautiful, just like molten glass.
(Sorry, had to withdraw the budget calculator caliper Sony Eriksson, so the macro mode turned out - not so hot.)
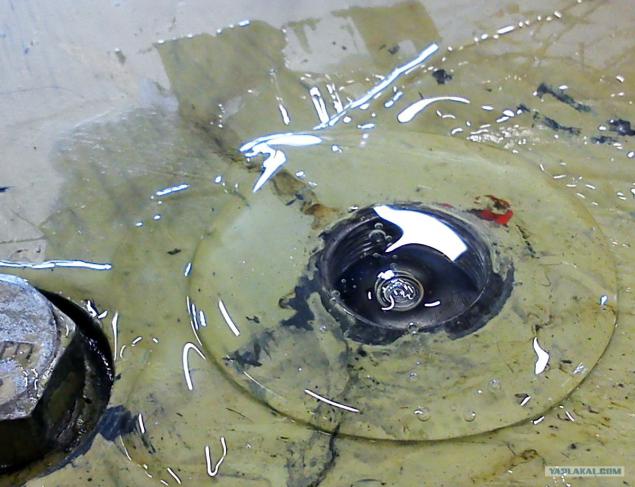
Well, like all the collected ...
(it is necessary to carry the flywheel to the dock in another part of the city)
So, after the flywheel dragged back into the engine room on ship-it was time to put it on the engine. Here, too, not everything is simple.
Let me remind you that a piece of iron weighs almost half a ton, and she sits on the shaft at a very hard landing. No sledgehammer will not help. Come to the aid of hydraulic presses. But just the same it is impossible to drive in. Here is some trick. The shaft has a threaded hole for connecting a tube which is fed by a special oil with very high pressure. (Oil on different properties for pressing and pulling out)
Also formed on the shaft a helical groove along which oil is supplied uniformly in the "space between the shaft and the flywheel". When that gap there at all, but there is a transition landing ", negative clearance", ie with interference. That is, it turns out that the high pressure oil as it "stretches" the piece of metal, creating a gap.
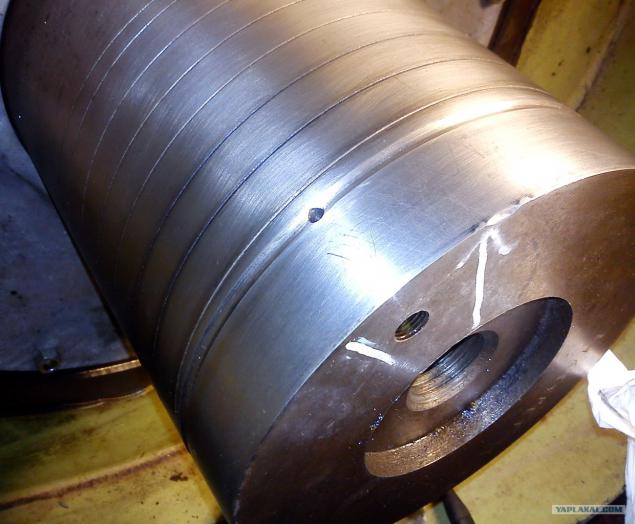
To create such pressure "unclamping" used here is a manual pump.
By the way, this black flexible tube few meters long to connect the pump shaft and costs about $ 350. (This I do not ponimayu- for that kind of money?)
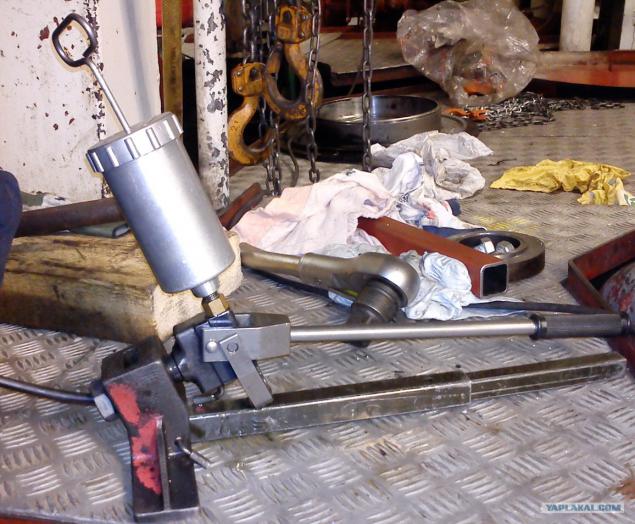
Only in this case, it becomes possible to extrude the flywheel using the same hydraulic press, where pressure is applied rather high about 700-800 atmospheres. (This yellow hose)
(Incidentally, according to instructions during operation, take the hands of those compounds of the hose is prohibited because there were times when torn nuts and spray oil cut people hands apart (I was on the course, where we were shown photographs of such damages brush)
. Drive in a flywheel shaft, press "unclamping" is reset, but the effort Joining can only be removed after half an hour.
(visible in the same tube, which costs 300 $)

Of course, there are motors and flywheels are much larger.
But on this ship are four that's such a small diesel engine to run on a single load.
Sfotat rhinestones all difficult, so the shot came here only two of the motor.
In general, I have everything. Thank you for attention.
It is likely that where I wrote incorrectly, because it's not my job to teach ...
Therefore I agree to a healthy criticism.
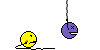
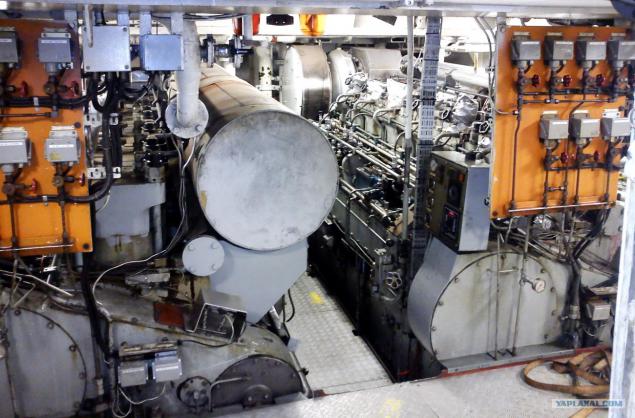
Source: