1109
Birth knife handmade
PL Welcome! Finally he found the time to create the post of a decent size of the case, which I do with my father. I do this in their spare time, while his father is a hobby grew into a business. The thing we have is not very serious, but somewhat complex - production hoz.byt knives for hunting, fishing, hiking, and a collection of cut sausage. First I wanted to describe the process of creating a knife since finished forgings, but immediately decided that this would not be enough for you, so taking time to get to forge one fairly well-known blacksmith Sergei Danilov.
Immediately apologize for ashipki and photo quality, somewhere I removed a file, and somewhere in the phone. The blades and the workpiece may change from time to time in the photo, because it's a long process, put on stream, and remove in a single chronology was difficult. Also in the production are nuances and small trade secrets wizard that ethically I walked in creating photo report.
The knife blade is made of mosaic Damascus. To produce one of a "package", ie the interlayer pattern, using an average of 6 values metal. One blade may be from 1 to N of the number of "packets." On average, they make up packets 5i. The photo blank for the first package, a kind of layered cake of stuck electric welding plates of different brands in different combinations.
It will be about 80 ph and a small video
Then the whole thing is placed in the oven to warm.
Fascinating process ... How nice to look at the fire, water and the like who is working ...
After heating the workpiece sprinkled with brown to forge welding and again placed in the furnace
Next smith conjures the workpiece
The welding process has gone
This procedure is repeated many times, Smith embodies his idea, only he understood only
And again on the hammer, it is necessary to achieve the thickness and shape of the rod
Next smith hand does the unthinkable - spinning metal ...
Stomps him ... cuts, etc. sloit In general, he puts his whole soul, casts from each of its movement depends on the future design and aesthetics of the blade.
Finally, after painstaking work they preform obtained conceived as bars, those "packages". In the photo the result of several days.
Rods are cut into the blade smith chooses their order forms and mentally picture. Smith knows in advance what type of metal is on the cutting edge and takes this into account when combining.
Next, we catch all electric welding as the first photo
The whole cycle repeats itself - warm, borax, and warm up again under the hammer.
Molten metal to its charms ...
Next is the bending of the cutting edge
There is a formation blade
The process is lengthy, time to take a picture of a bird accidentally
It is extraordinarily beautiful, agree
Forging is ready, it is necessary to gradually cool down.
As such, it is a popodaet master, ie my father.
Thickness of about 12mm at it, all you need to grind off the excess. The output will 4+ mm
Master symmetrical grind down all unnecessary
The process is long and nuanced
It looks like "naked" forging a thickness for about 6mm. Picture begins to appear.
Produced primary vzrezka on the butt is already the 5 + mm, 1.5 mm at the tip, the figure is well looked through. The preform is then returned to the blacksmith to heat treatment (termichka, in common). Before termichkoy blacksmith puts its stamp, and the workpiece hardens again falls into the hands of the master.
Blade hardened and with the stigma of a blacksmith. Sorry, the process termichki remove failed because again this is not done in one day
Blade finally "cut up" to the master planned thickness
Then polished on emery tapes, using skin from coarse to very fine grain.
It is necessary to view all the lines, they must be symmetrical and smooth to butt and stinging were "overwhelmed" on any side. Weighed down with the blade in the narrow circles is called "propeller", "screw" itd
Prepare the shaft for soldering pins
Check the thickness of the liner so that it does not exceed the thickness of the blade
Next solder the pin to the shank
Hairpin immediately after soldering
At the same time you need to take pen manufacturer, with what I do well. The large bar thoroughbred wood are cut on the bandsaw-shaped wedges blanks sticks.
Form grinding machine to attach specially presposoblennuyu for this. Do not laugh, but it's a good tool :)
Cut "Spike" for the seat guard
Garda sits in the saddle, which provides robust construction and extra strength
The handle is finished by hand nazhdachkoy
And other tools ...
Garda expands the size of the blade is strictly
Garda should sit like a glove
Slots are not allowed. The mosquito nose will not undermine
Again, I apologize for the quality of a photo, just fotkal file.
We continue to work with wood, master prosverlivet hole for the shank
On both sides of the drills, you should get a smooth through-hole
Fine adjustment is carried out with a file
It is seen as a hole "describes a" form of the shank
The first "fitting." All OK. Forgot to mention that this method of securing the blade to the handle is called "Through tie", it is extremely reliable and is used since the times of the Crusaders.
Look in the preliminary full assembly of all the parts, like everything exactly, the settings are not knocked
Master makes a recess for sharpening the blade
This prevents damage to the heel recess for sharpening the blade
Time to work hard with the blade. It starts with the application of its master stamp. For this he needs a magic wand, heh heh ...
The stigma is ready, Scarlet Flower turned
Two hallmarks closer. Manufacturer forgings for the product top Sergey Danilov, Pozdnyakov and Alexey, the master performing the rest of the work from beginning to end (well, not without my participation of course ^ _ ^).
"Pulling" pattern Damascus steel by electrolysis.
Master collects all again, check all joints and cracks, straightness of lines and correctness geomterii. If something is wrong, it must be corrected.
Protein eyes
In our office has its own atmosphere ...
Master teak oil permeates the hilt.
Pieces of wood soaked, the excess removed
Master Alex drill a hole to fill eboksidnoy resin.
Filled with explosive mixture, after it hardens to disassemble the knife would be virtually impossible
Resin should take absolutely all the free volume of voids should not be.
Inserted Chopik of izyubrinogo horns
Bite off too much
Golden Chopik of izyubryaroga
The finished product is sharpened first pre
Then, on the "water" stone at a certain angle, sharpened for final
The finished product should be Britkov. We spend a little test. Hair Master is on hand with difficulty, sometimes you have to use my
Again, a small test (Life is good) ...
On shooting the finished product came our small friend
Shaved
Source:
Immediately apologize for ashipki and photo quality, somewhere I removed a file, and somewhere in the phone. The blades and the workpiece may change from time to time in the photo, because it's a long process, put on stream, and remove in a single chronology was difficult. Also in the production are nuances and small trade secrets wizard that ethically I walked in creating photo report.
The knife blade is made of mosaic Damascus. To produce one of a "package", ie the interlayer pattern, using an average of 6 values metal. One blade may be from 1 to N of the number of "packets." On average, they make up packets 5i. The photo blank for the first package, a kind of layered cake of stuck electric welding plates of different brands in different combinations.
It will be about 80 ph and a small video
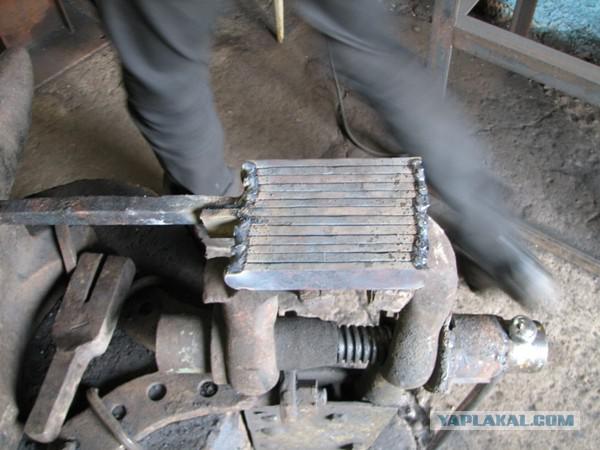
Then the whole thing is placed in the oven to warm.
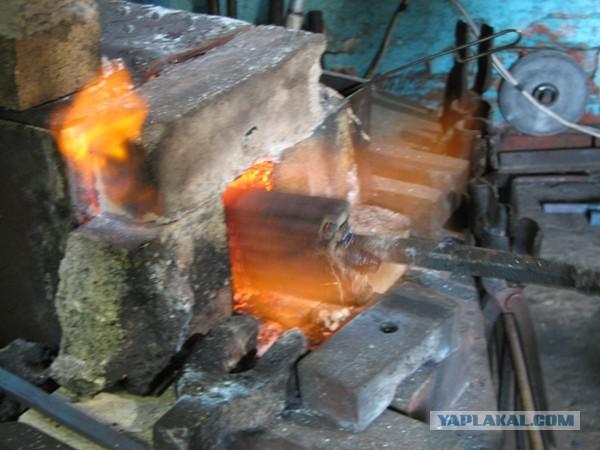
Fascinating process ... How nice to look at the fire, water and the like who is working ...
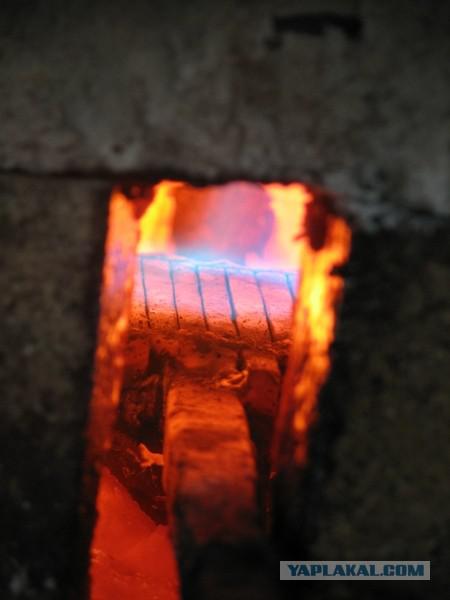
After heating the workpiece sprinkled with brown to forge welding and again placed in the furnace
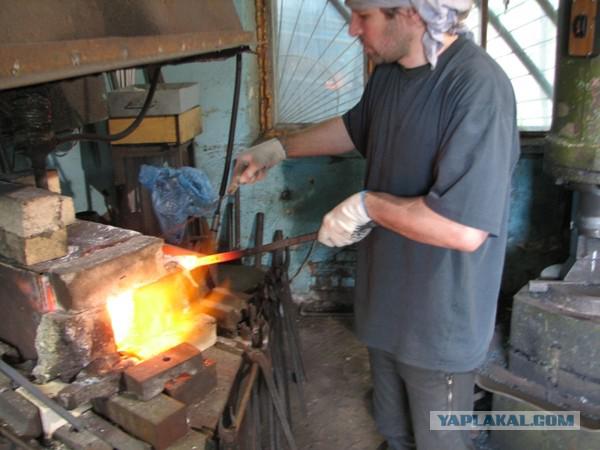
Next smith conjures the workpiece
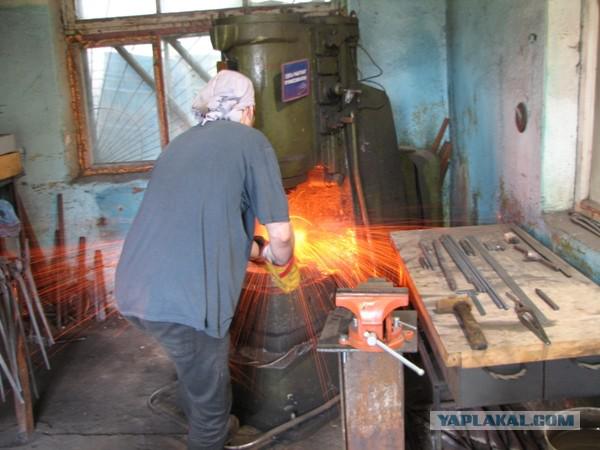
The welding process has gone
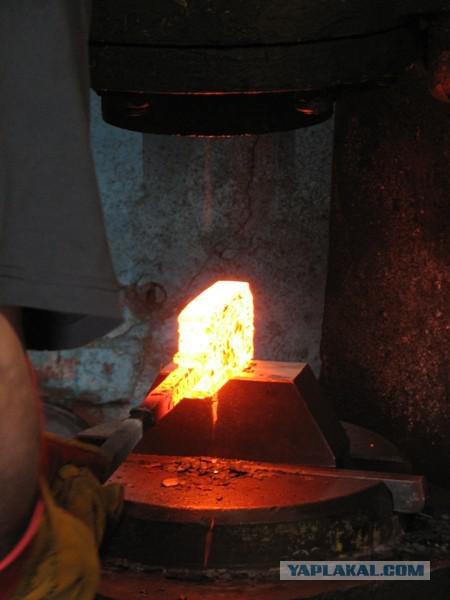
This procedure is repeated many times, Smith embodies his idea, only he understood only
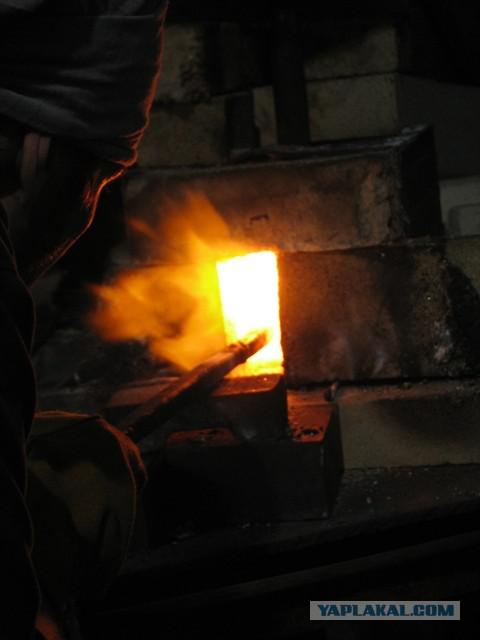
And again on the hammer, it is necessary to achieve the thickness and shape of the rod
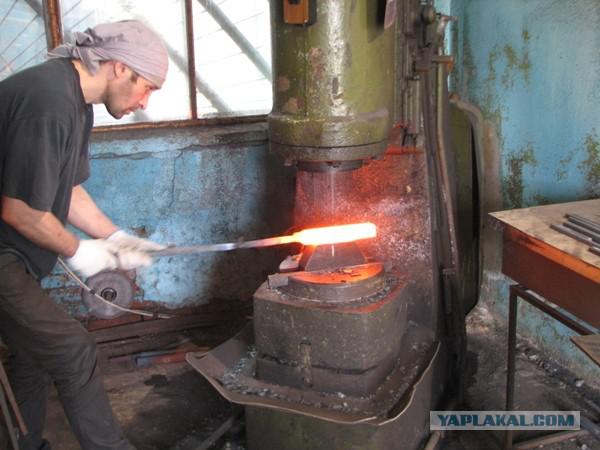
Next smith hand does the unthinkable - spinning metal ...
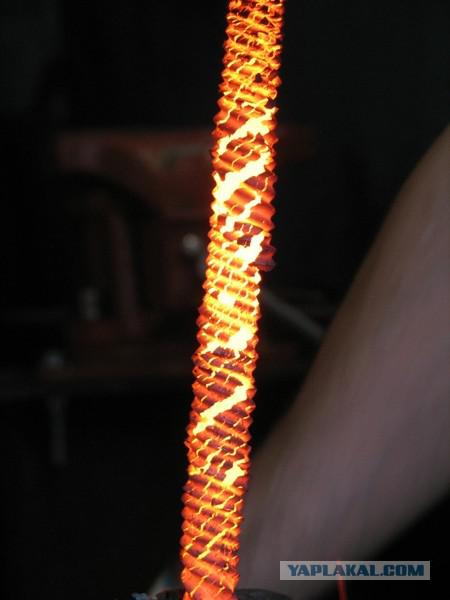
Stomps him ... cuts, etc. sloit In general, he puts his whole soul, casts from each of its movement depends on the future design and aesthetics of the blade.
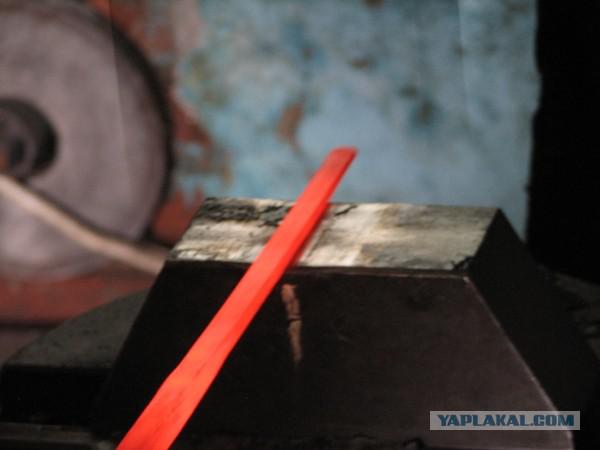
Finally, after painstaking work they preform obtained conceived as bars, those "packages". In the photo the result of several days.
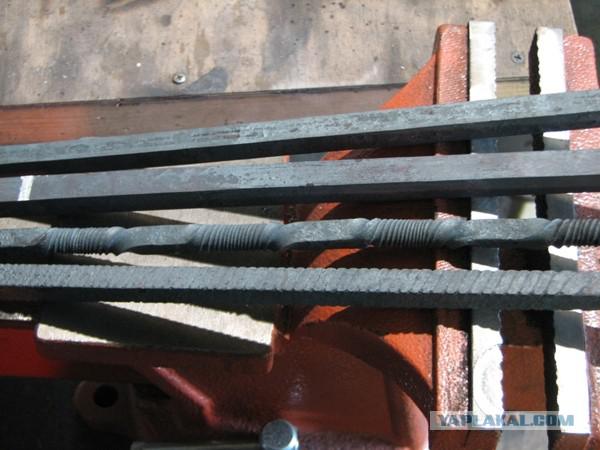
Rods are cut into the blade smith chooses their order forms and mentally picture. Smith knows in advance what type of metal is on the cutting edge and takes this into account when combining.
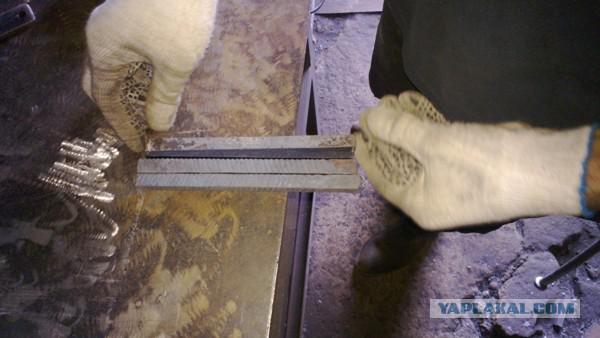
Next, we catch all electric welding as the first photo
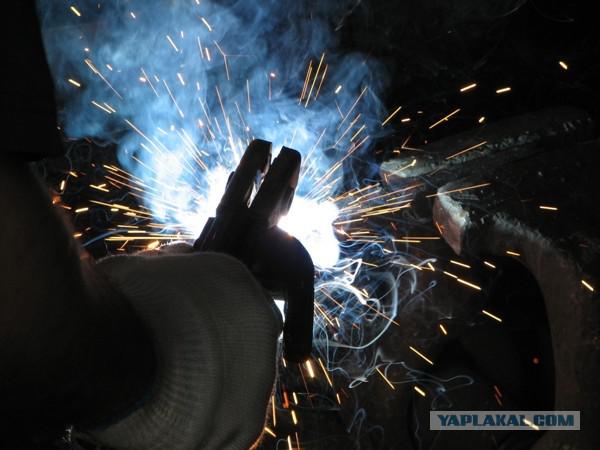
The whole cycle repeats itself - warm, borax, and warm up again under the hammer.
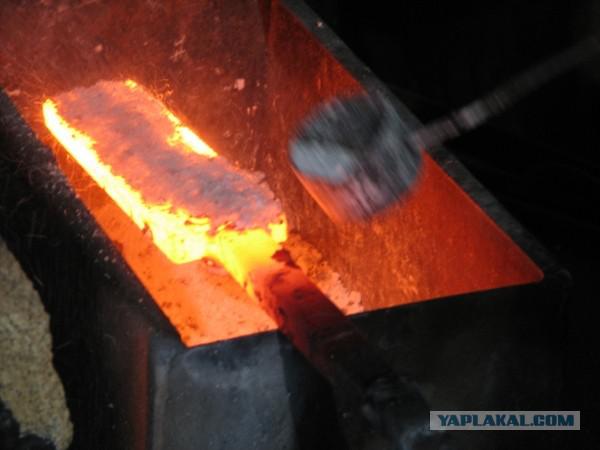
Molten metal to its charms ...
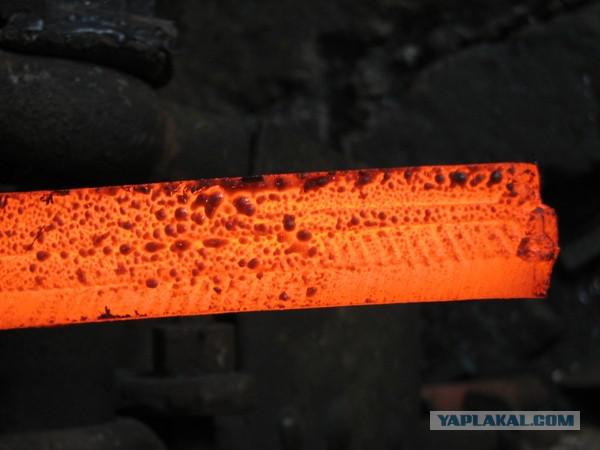
Next is the bending of the cutting edge
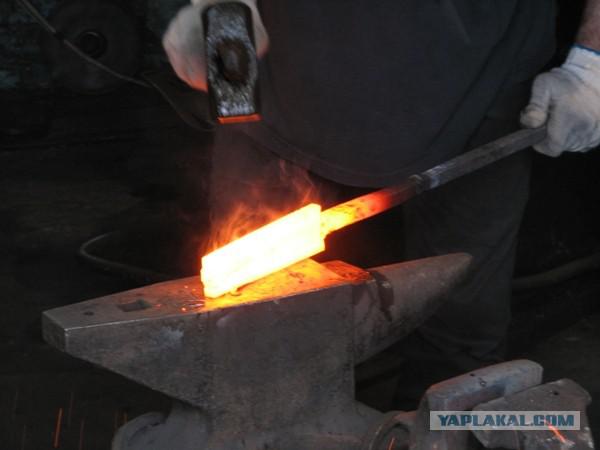
There is a formation blade
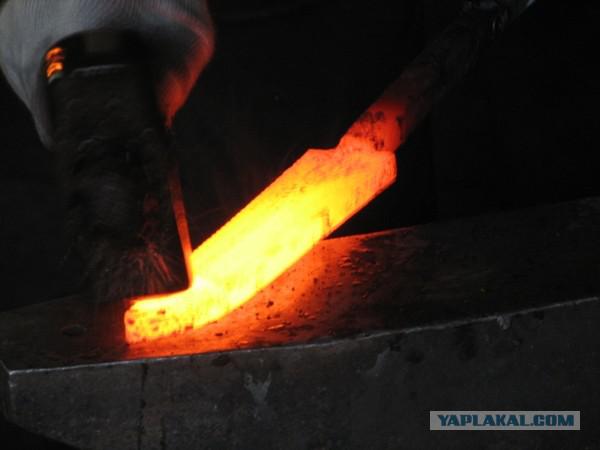
The process is lengthy, time to take a picture of a bird accidentally
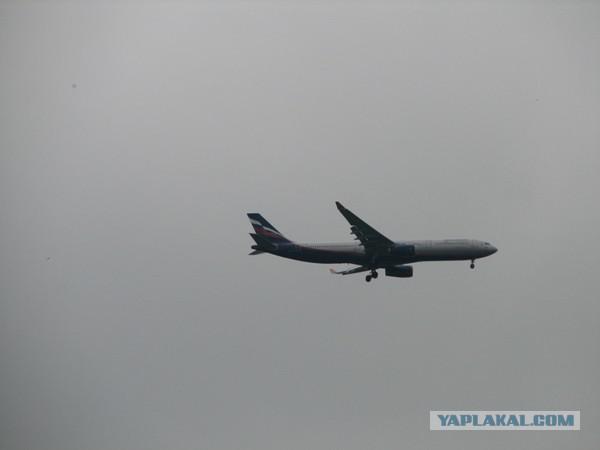
It is extraordinarily beautiful, agree
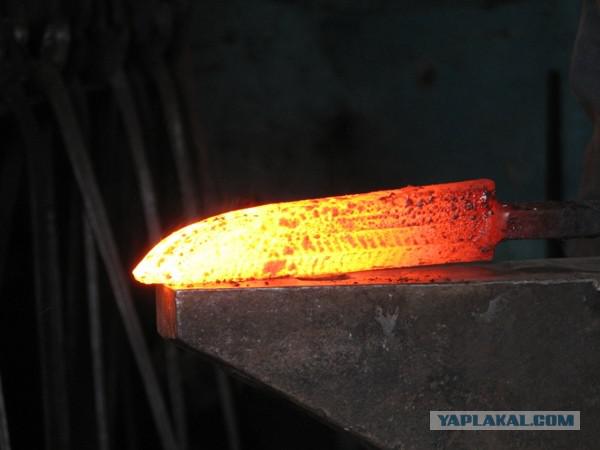
Forging is ready, it is necessary to gradually cool down.
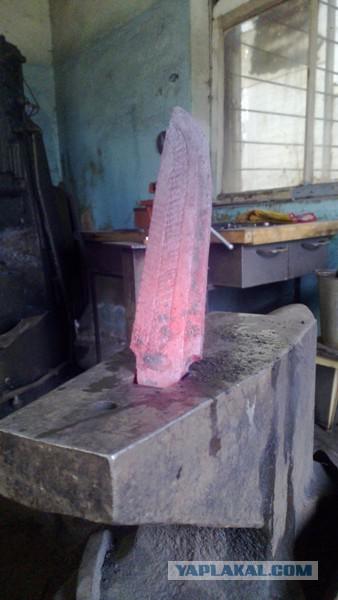
As such, it is a popodaet master, ie my father.
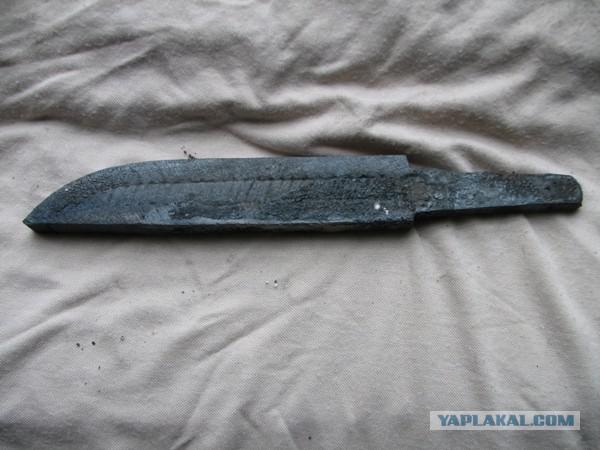
Thickness of about 12mm at it, all you need to grind off the excess. The output will 4+ mm
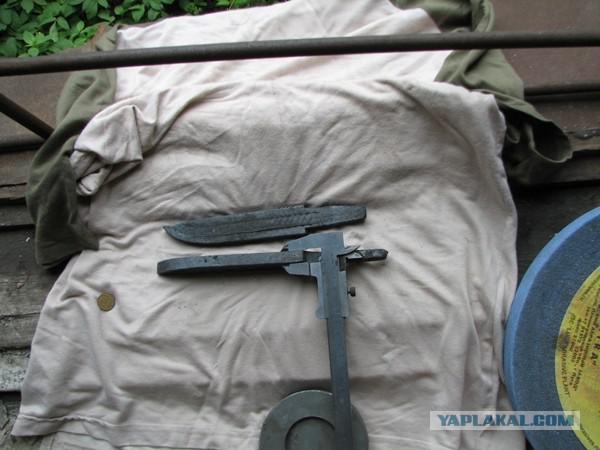
Master symmetrical grind down all unnecessary
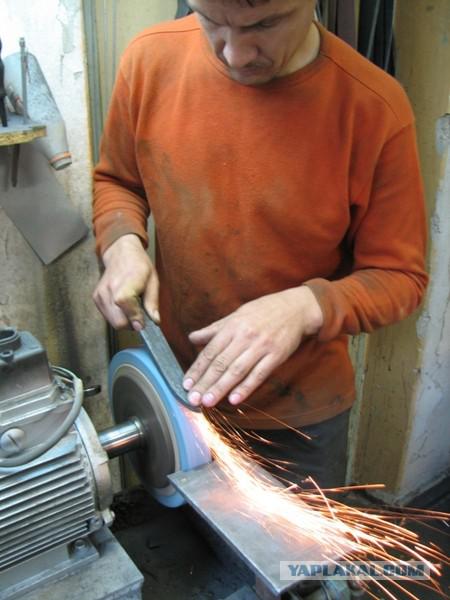
The process is long and nuanced
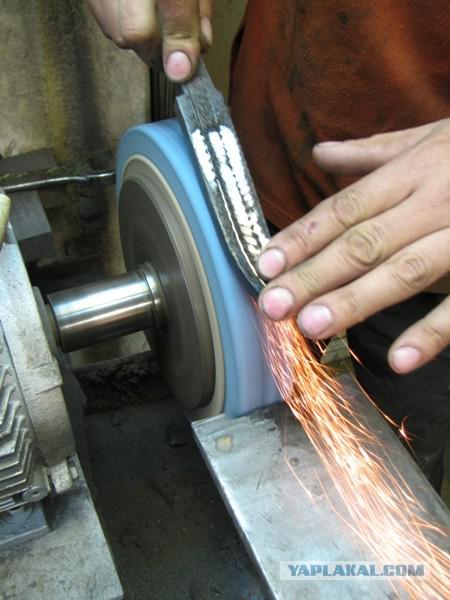
It looks like "naked" forging a thickness for about 6mm. Picture begins to appear.
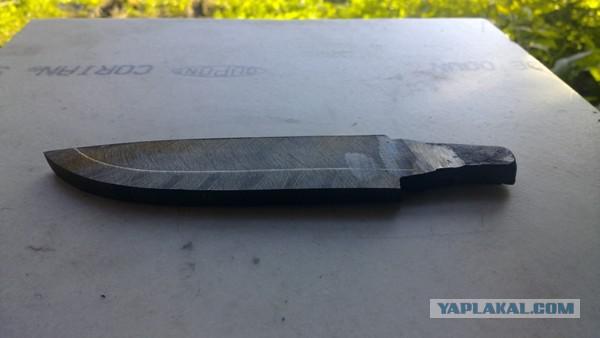
Produced primary vzrezka on the butt is already the 5 + mm, 1.5 mm at the tip, the figure is well looked through. The preform is then returned to the blacksmith to heat treatment (termichka, in common). Before termichkoy blacksmith puts its stamp, and the workpiece hardens again falls into the hands of the master.
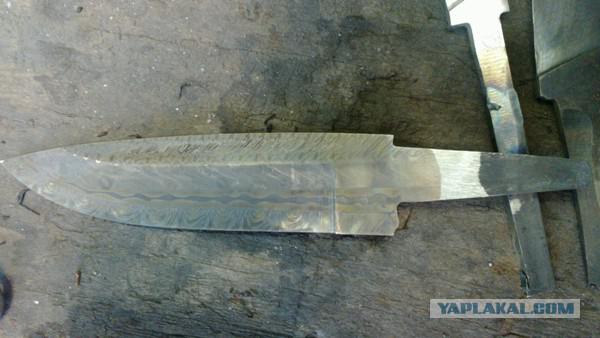
Blade hardened and with the stigma of a blacksmith. Sorry, the process termichki remove failed because again this is not done in one day
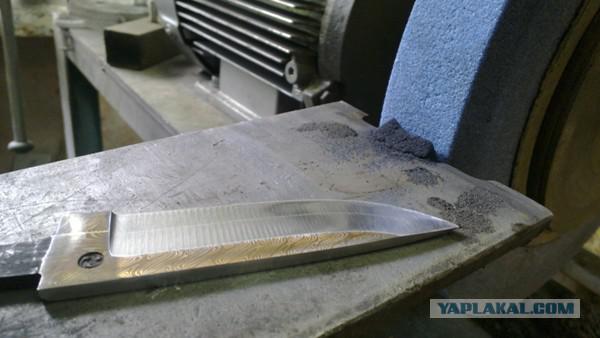
Blade finally "cut up" to the master planned thickness
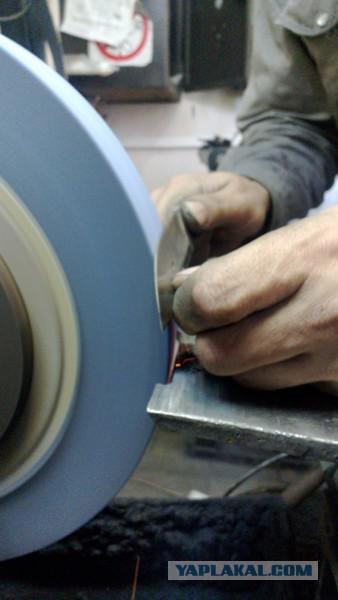
Then polished on emery tapes, using skin from coarse to very fine grain.
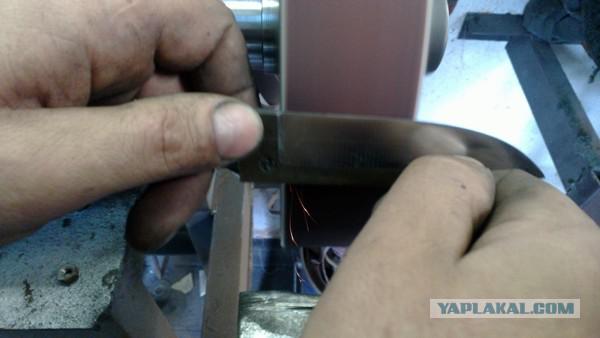
It is necessary to view all the lines, they must be symmetrical and smooth to butt and stinging were "overwhelmed" on any side. Weighed down with the blade in the narrow circles is called "propeller", "screw" itd
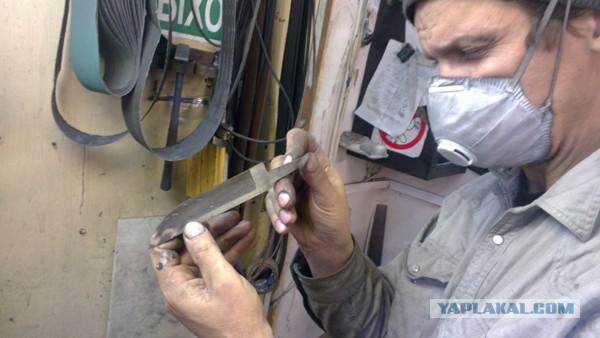
Prepare the shaft for soldering pins
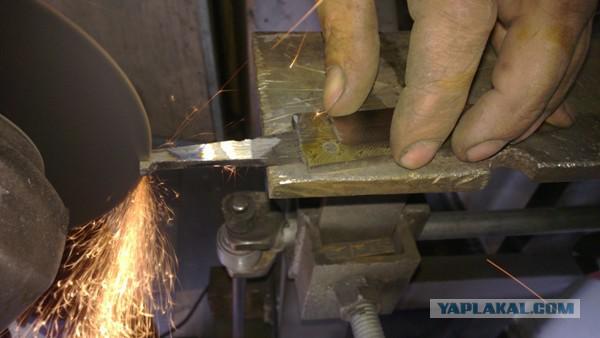
Check the thickness of the liner so that it does not exceed the thickness of the blade
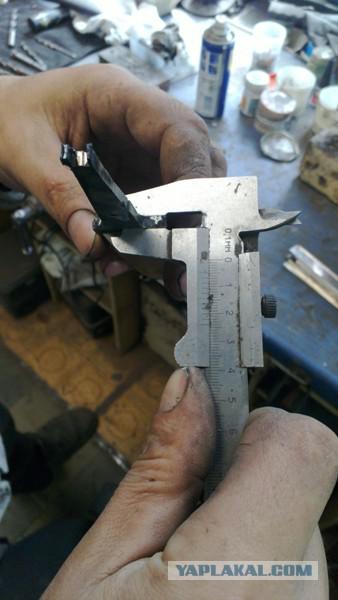
Next solder the pin to the shank
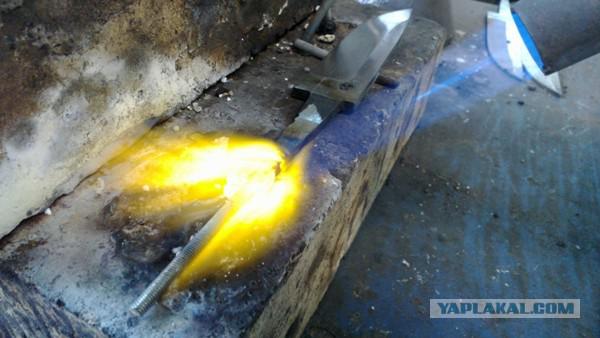
Hairpin immediately after soldering
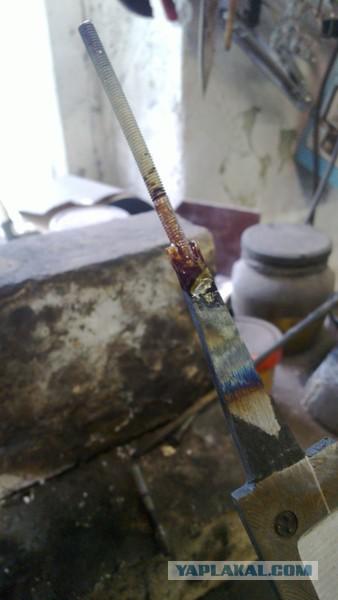
At the same time you need to take pen manufacturer, with what I do well. The large bar thoroughbred wood are cut on the bandsaw-shaped wedges blanks sticks.
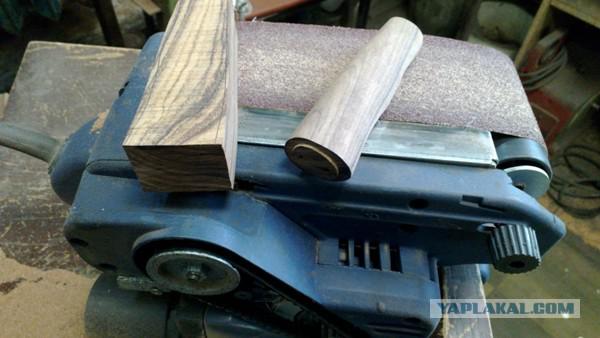
Form grinding machine to attach specially presposoblennuyu for this. Do not laugh, but it's a good tool :)
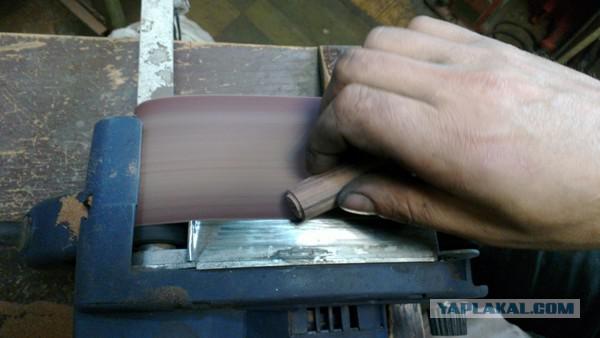
Cut "Spike" for the seat guard
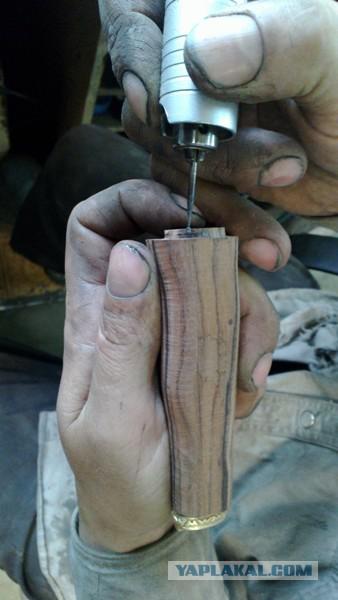
Garda sits in the saddle, which provides robust construction and extra strength
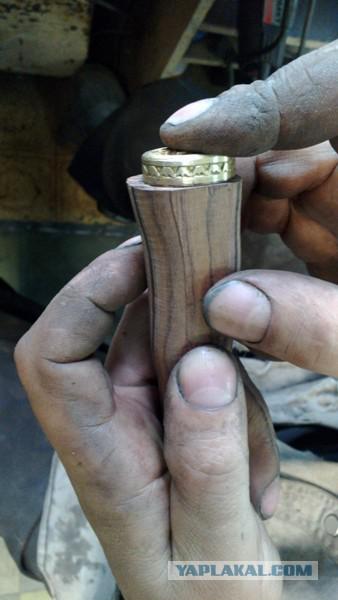
The handle is finished by hand nazhdachkoy
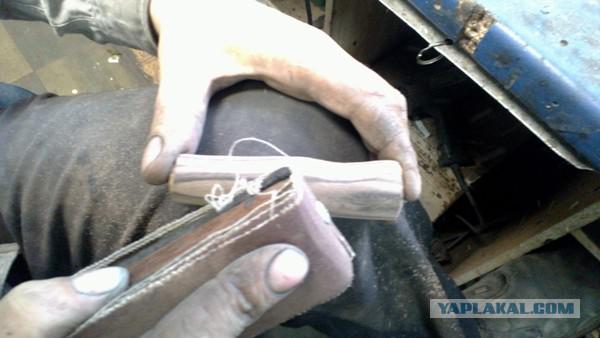
And other tools ...
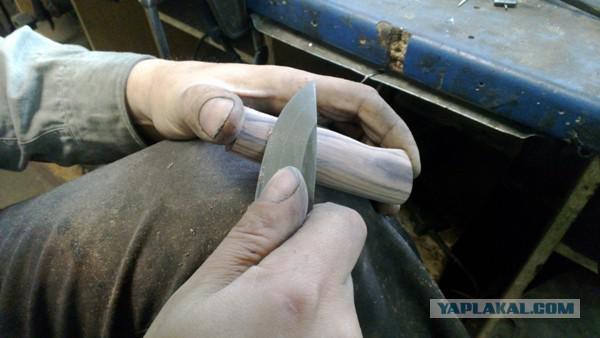
Garda expands the size of the blade is strictly
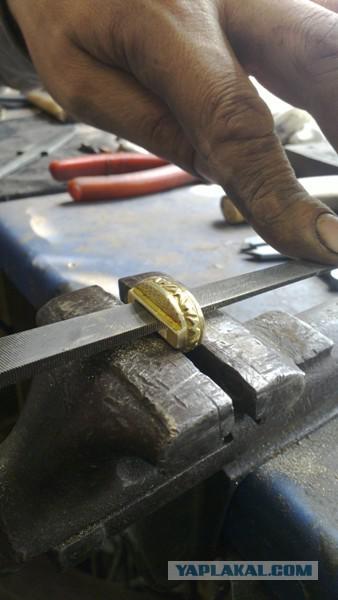
Garda should sit like a glove
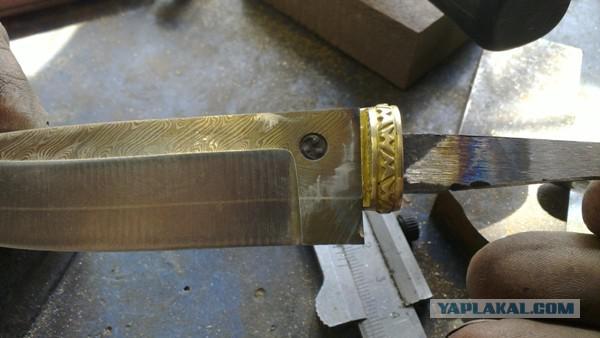
Slots are not allowed. The mosquito nose will not undermine
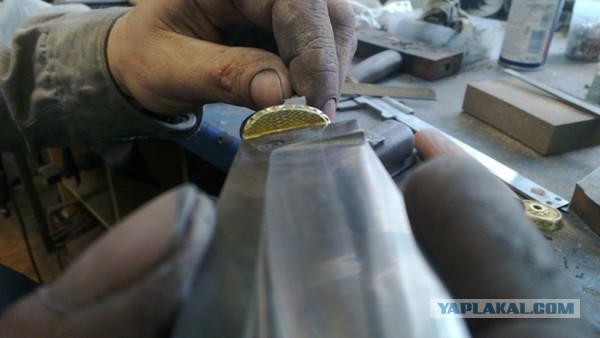
Again, I apologize for the quality of a photo, just fotkal file.
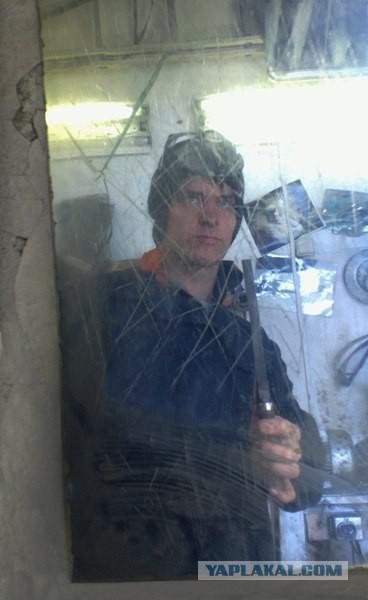
We continue to work with wood, master prosverlivet hole for the shank
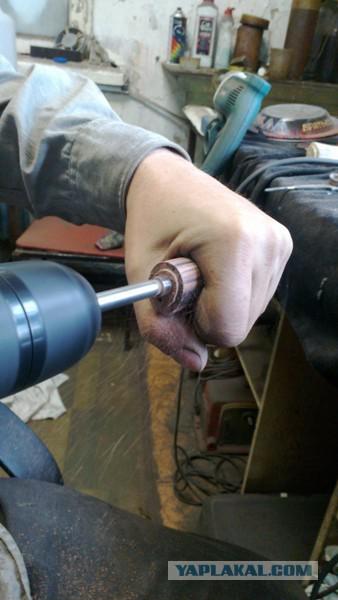
On both sides of the drills, you should get a smooth through-hole
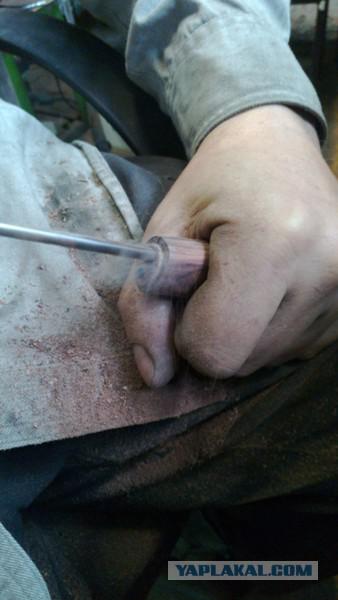
Fine adjustment is carried out with a file
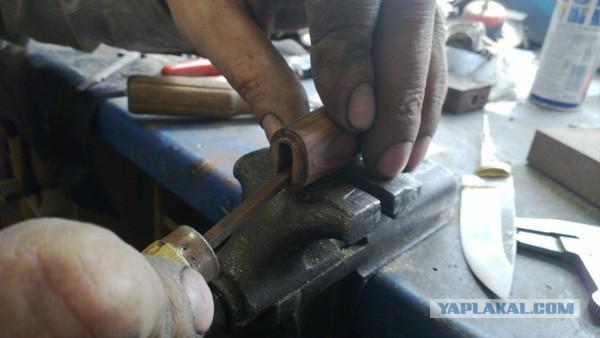
It is seen as a hole "describes a" form of the shank
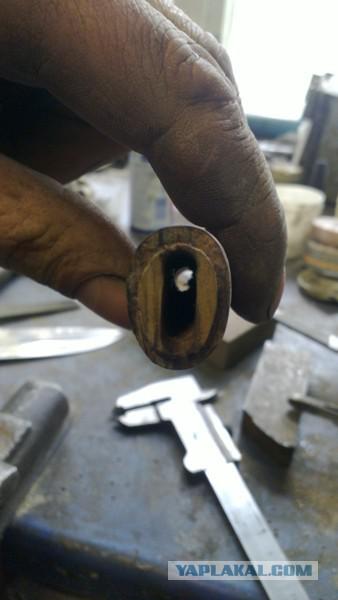
The first "fitting." All OK. Forgot to mention that this method of securing the blade to the handle is called "Through tie", it is extremely reliable and is used since the times of the Crusaders.
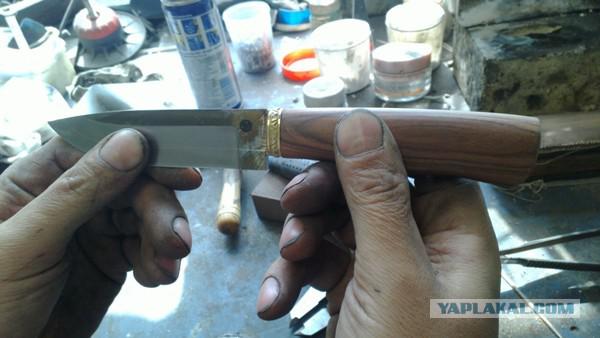
Look in the preliminary full assembly of all the parts, like everything exactly, the settings are not knocked
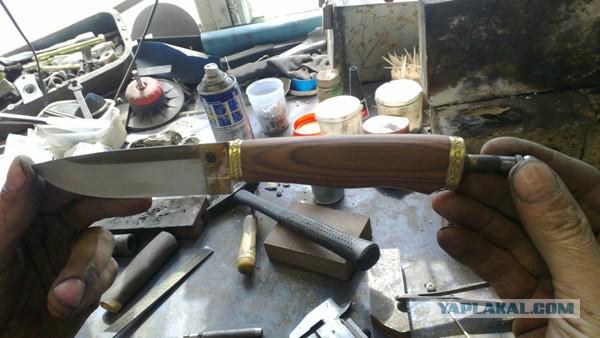
Master makes a recess for sharpening the blade
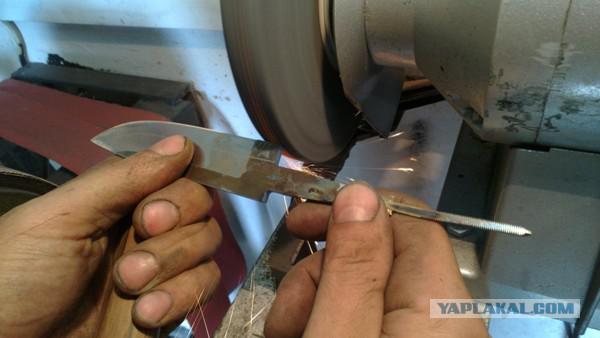
This prevents damage to the heel recess for sharpening the blade
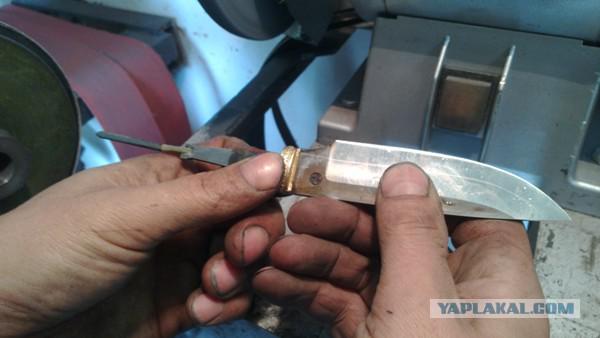
Time to work hard with the blade. It starts with the application of its master stamp. For this he needs a magic wand, heh heh ...
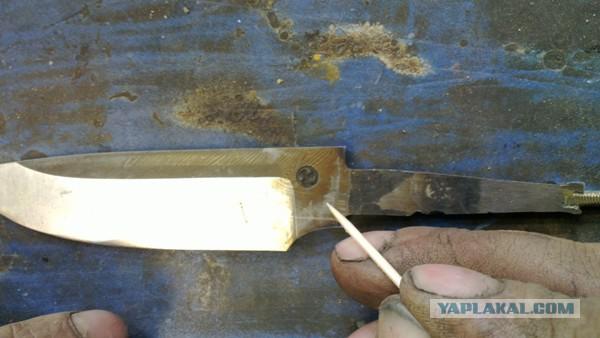
The stigma is ready, Scarlet Flower turned
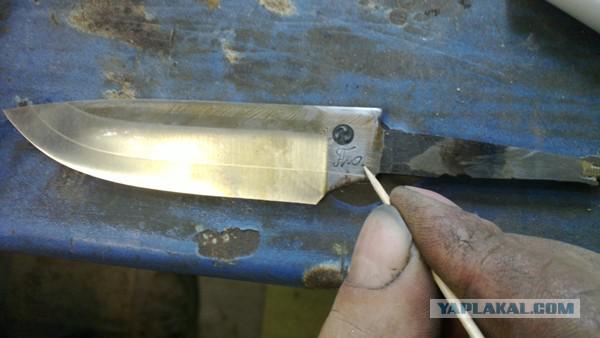
Two hallmarks closer. Manufacturer forgings for the product top Sergey Danilov, Pozdnyakov and Alexey, the master performing the rest of the work from beginning to end (well, not without my participation of course ^ _ ^).
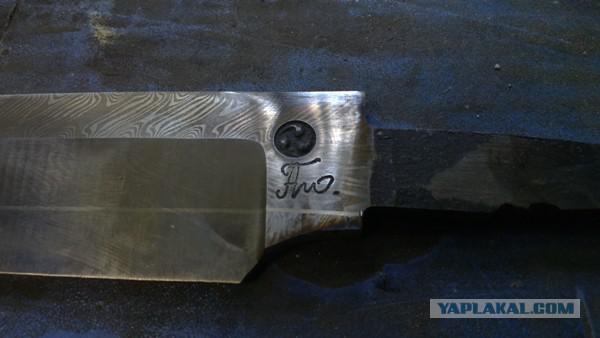
"Pulling" pattern Damascus steel by electrolysis.
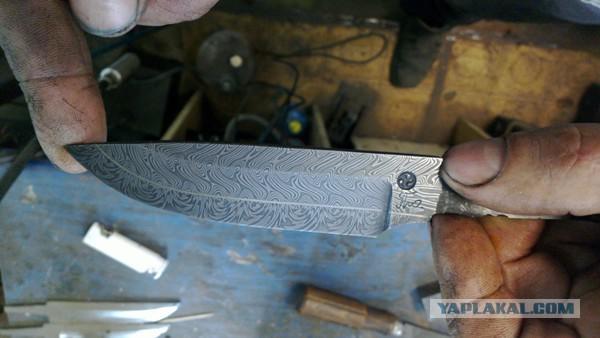
Master collects all again, check all joints and cracks, straightness of lines and correctness geomterii. If something is wrong, it must be corrected.
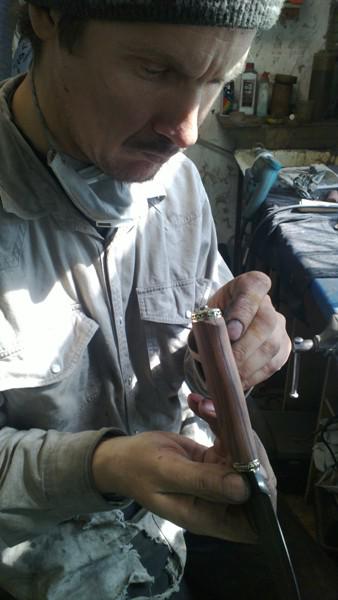
Protein eyes
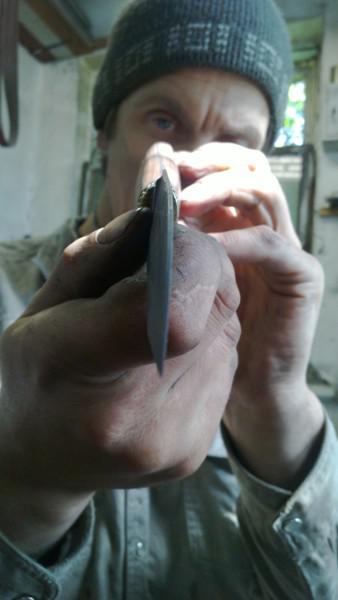
In our office has its own atmosphere ...
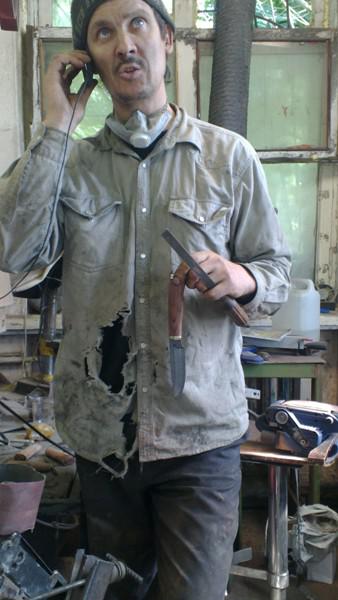
Master teak oil permeates the hilt.

Pieces of wood soaked, the excess removed
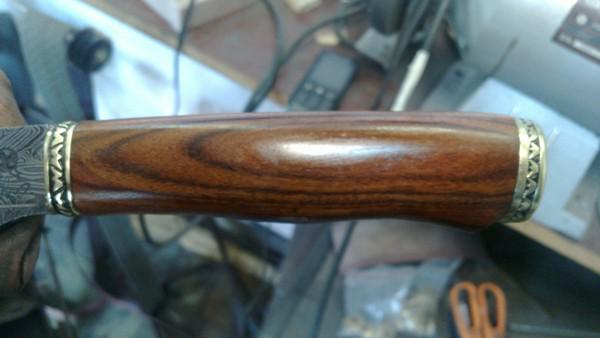
Master Alex drill a hole to fill eboksidnoy resin.
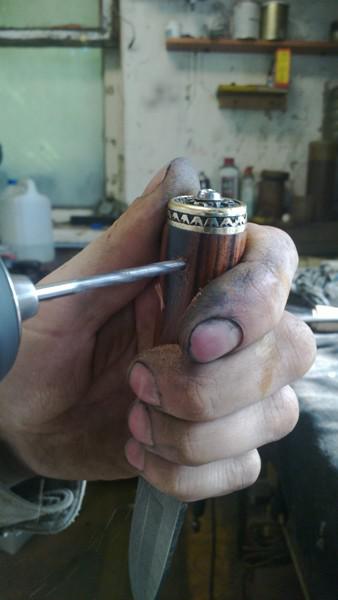
Filled with explosive mixture, after it hardens to disassemble the knife would be virtually impossible
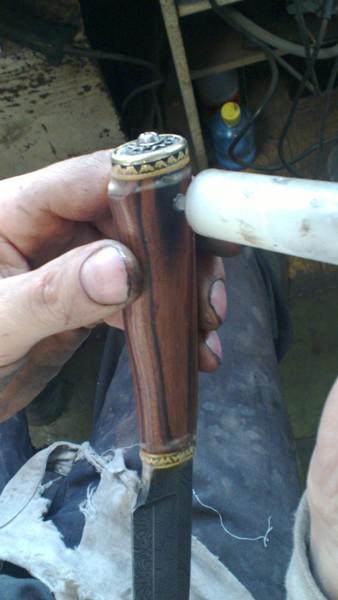
Resin should take absolutely all the free volume of voids should not be.
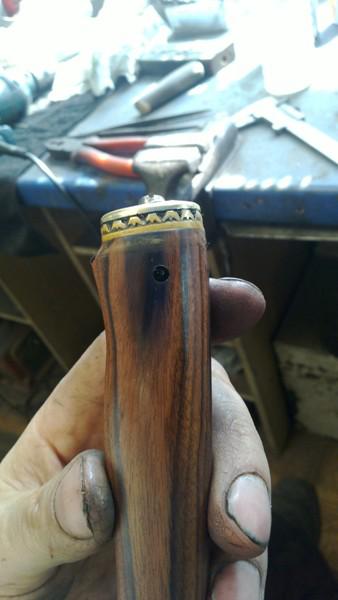
Inserted Chopik of izyubrinogo horns
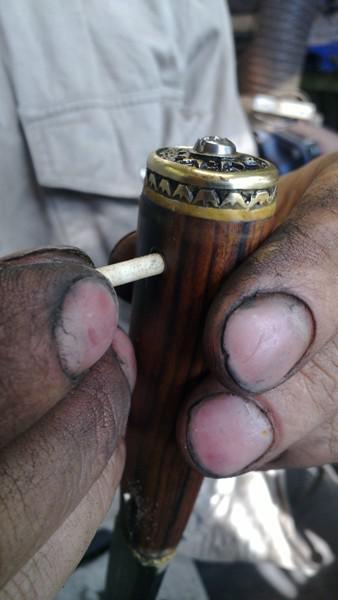
Bite off too much
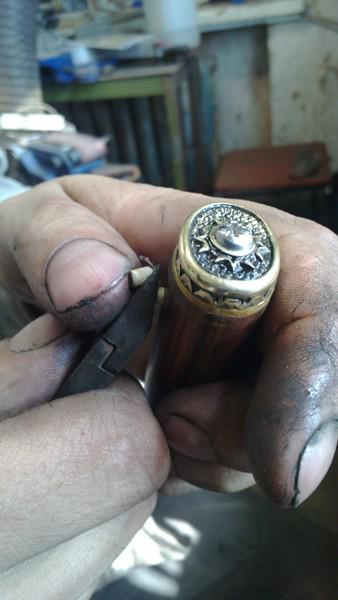
Golden Chopik of izyubryaroga
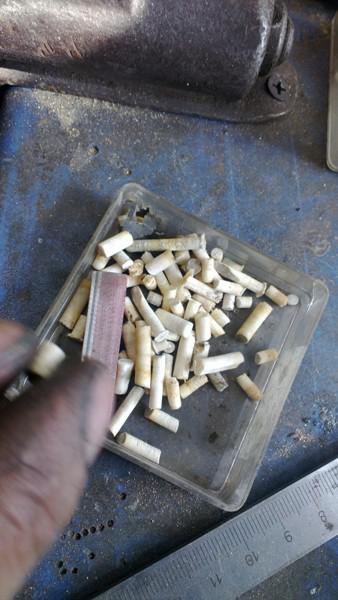
The finished product is sharpened first pre
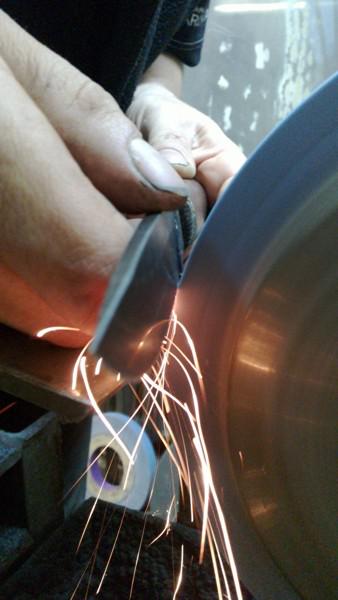
Then, on the "water" stone at a certain angle, sharpened for final
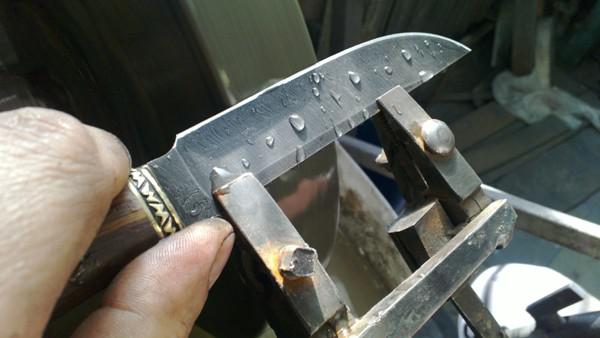
The finished product should be Britkov. We spend a little test. Hair Master is on hand with difficulty, sometimes you have to use my
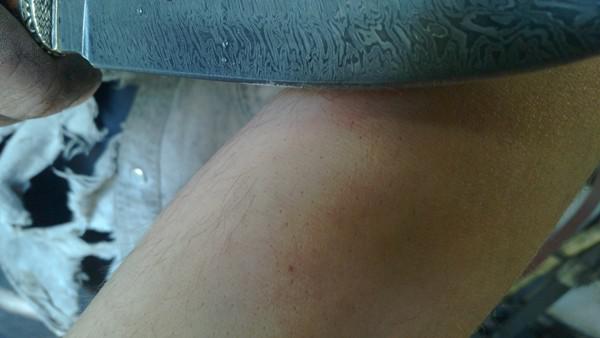
Again, a small test (Life is good) ...
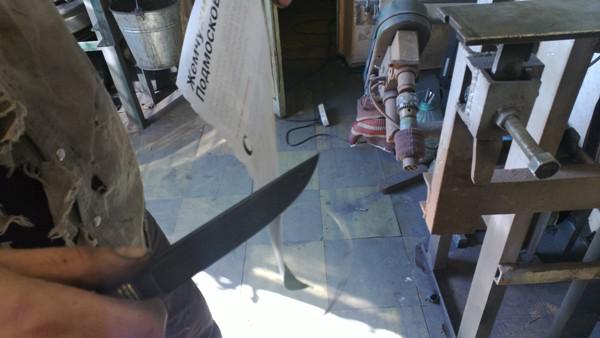
On shooting the finished product came our small friend
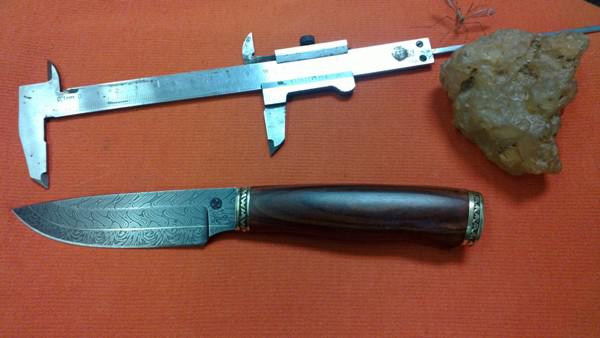
Shaved
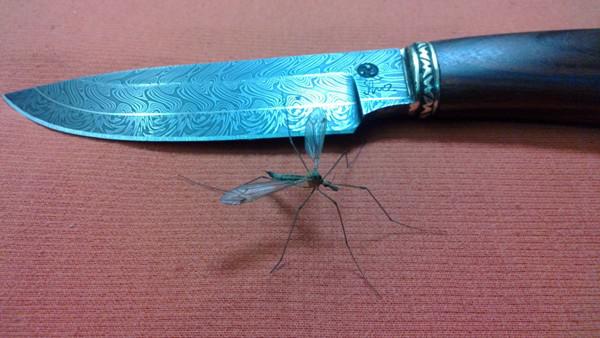
Source: