726
MINI - Plant in Oxford (24 photos)
Capital Oxfordshire known not only in the presence of the oldest university in the English-speaking world. There also collect cars throughout its history connected with the history of Great Britain. 4,500 workers produce every week on the road all over the world 3500 legendary cars badged MINI. Here in Oxford, is one of the most modern and technically advanced car factories in the world, in which BMW Group for nine years has invested about 380 million. Pounds. Here we, a group of journalists from different countries who came to the festival MINI United, brought on a tour to show how to see the light of these cars.
Now, in an area of 40,000 square meters assembly of automobile bodies involved 230 industrial robots.
The accuracy of the assembly of parts of the body such robots - 0.05 mm.
During the build quality ensures a special team. Corrected deficiencies found here, next to the assembly site.
Master brought one of the bodies to their workplace and begins to deal with it.
Unfortunately, we did not have time to visit The Paintshop -
shop body painting, occupying, as they say, an area equal to 12 football fields.
Instead, it took us directly to the assembly line. On this site the body is prepared for paint work, hanging on him all the necessary parts.
With this arrangement, for example, put on a body model MINI Clubman rear door. The MINI depending on the configuration consists of approximately 2,500 internal and external Beams.
I really liked the working environment at the factory. The people working there cheerful, friendly, the camera does not turn away, likes to joke.
In such circumstances, shoot - a pleasure. Sorry, did not have much time.
Well, the rear doors on Klabmene in place. This "family" Quintuple model plant began producing in 2007
It is longer than the classic MINI body 80 mm.
This is the beginning of the final assembly of the car: colored body, moving slowly in the shop, cluttered with details, turning into a real MINI.
We came when the factory finish work second shift and started third, night. Girl and worked his going home.
During a shift change conveyor stops. Masters simply replace each other.
Coming to work with a partner removes tool belt while he is still working.
Changed and the new shift started work.
The assembly is extremely mechanized, but there are some operations that are performed manually, mostly women.
Brought windshields.
Here are preparing the engine to the transmission and front axle to be installed inside the body.
I had not even noticed the engine was at the right place. Moreover, everything is calm, somehow, even with the lazy, leisurely.
Here MINI gets its wheels.
It is said that two absolutely identical MINI on the line is not seen. On each machine hangs a piece of paper with barcodes and when another car pulls up to the new site, the master reads the barcode scanner and it puts on the body that need this particular car.
Finals getting closer. The machine itself has wheels on the ground, the assembly is nearing its end.
Finally, in the new car gets its first driver.
Starter dry clicks several times and distributed under the hood low sound of the engine. The car was born.
Let's go!
drugoi

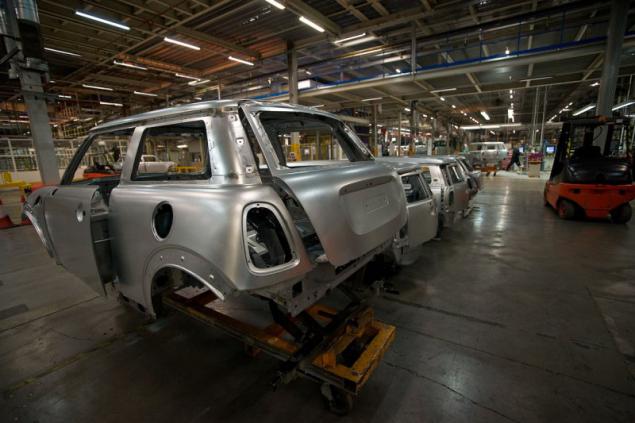
Now, in an area of 40,000 square meters assembly of automobile bodies involved 230 industrial robots.
The accuracy of the assembly of parts of the body such robots - 0.05 mm.
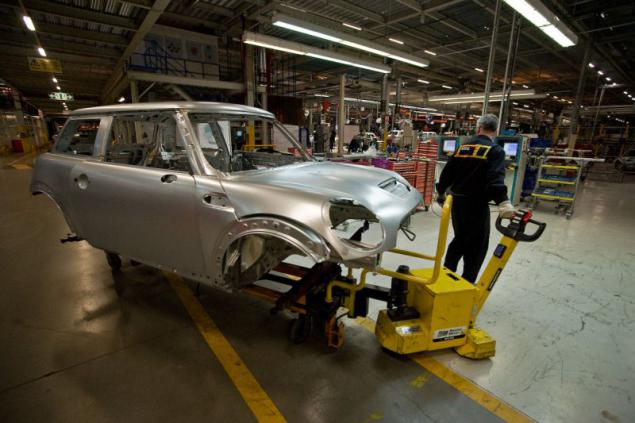
During the build quality ensures a special team. Corrected deficiencies found here, next to the assembly site.
Master brought one of the bodies to their workplace and begins to deal with it.
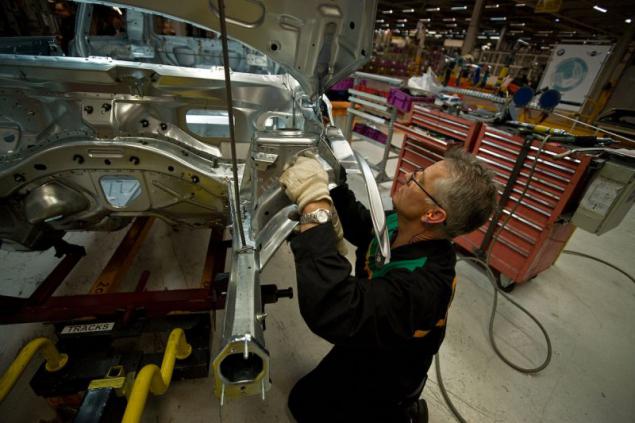
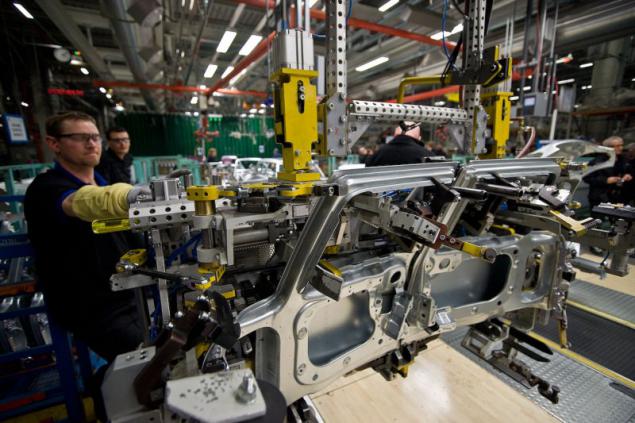
Unfortunately, we did not have time to visit The Paintshop -
shop body painting, occupying, as they say, an area equal to 12 football fields.
Instead, it took us directly to the assembly line. On this site the body is prepared for paint work, hanging on him all the necessary parts.
With this arrangement, for example, put on a body model MINI Clubman rear door. The MINI depending on the configuration consists of approximately 2,500 internal and external Beams.
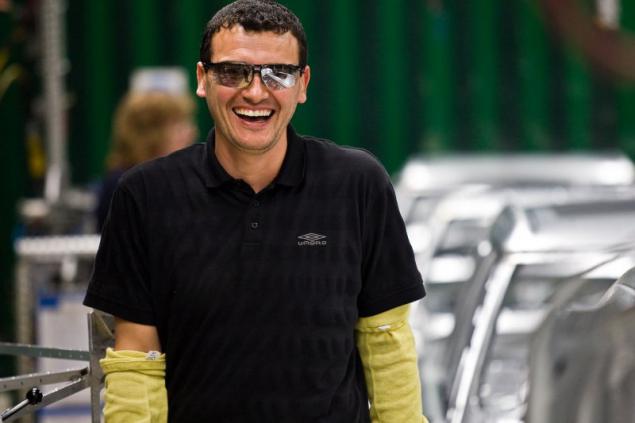
I really liked the working environment at the factory. The people working there cheerful, friendly, the camera does not turn away, likes to joke.
In such circumstances, shoot - a pleasure. Sorry, did not have much time.
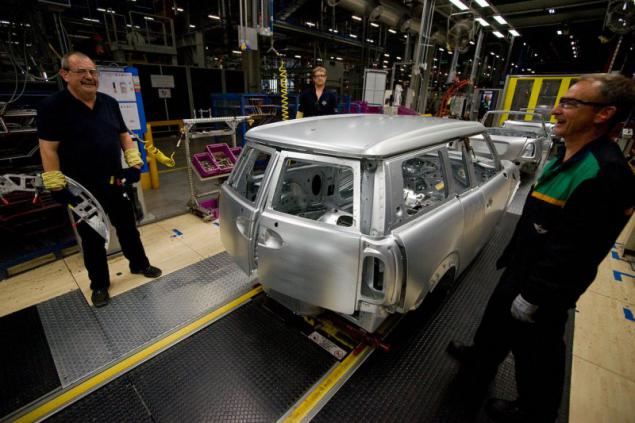
Well, the rear doors on Klabmene in place. This "family" Quintuple model plant began producing in 2007
It is longer than the classic MINI body 80 mm.
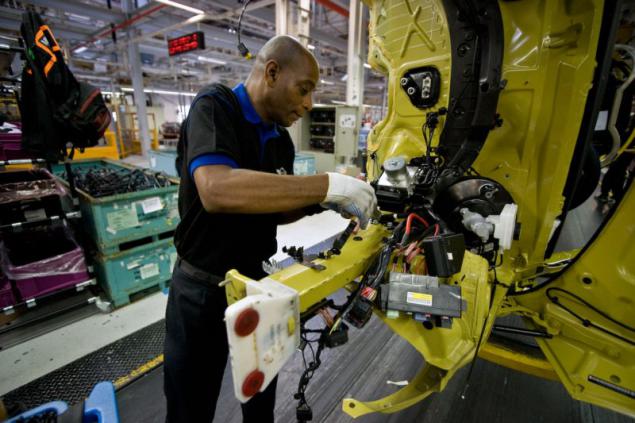
This is the beginning of the final assembly of the car: colored body, moving slowly in the shop, cluttered with details, turning into a real MINI.
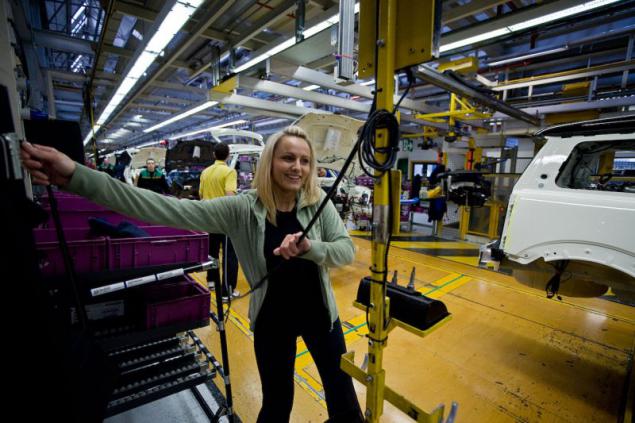
We came when the factory finish work second shift and started third, night. Girl and worked his going home.

During a shift change conveyor stops. Masters simply replace each other.
Coming to work with a partner removes tool belt while he is still working.
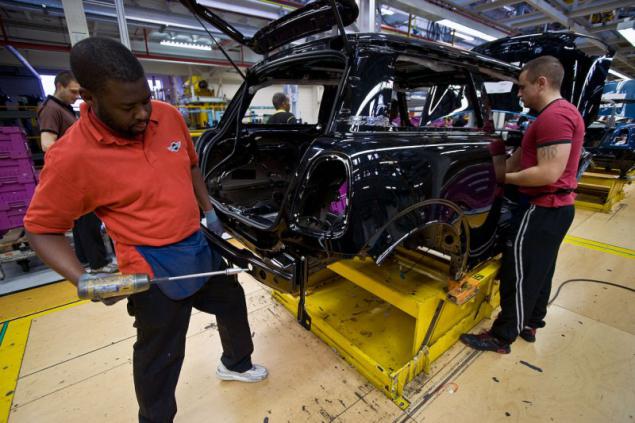
Changed and the new shift started work.
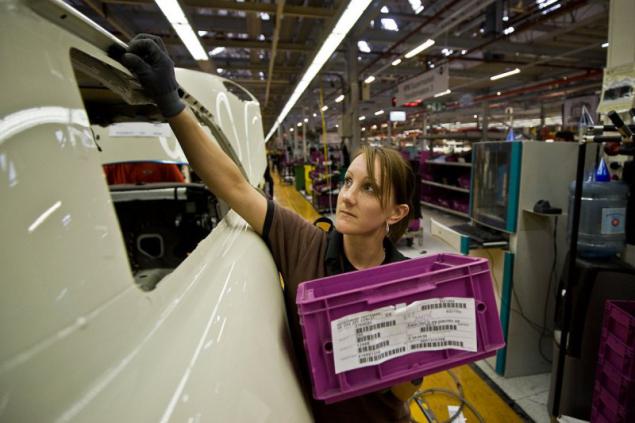
The assembly is extremely mechanized, but there are some operations that are performed manually, mostly women.
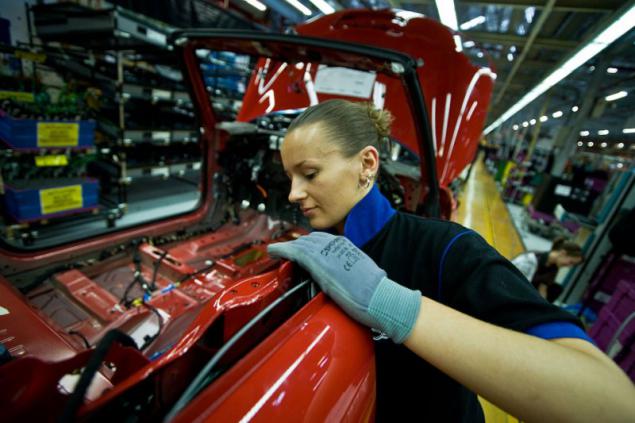
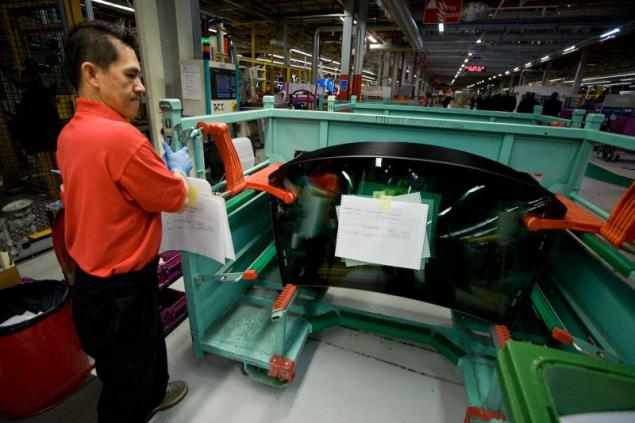
Brought windshields.
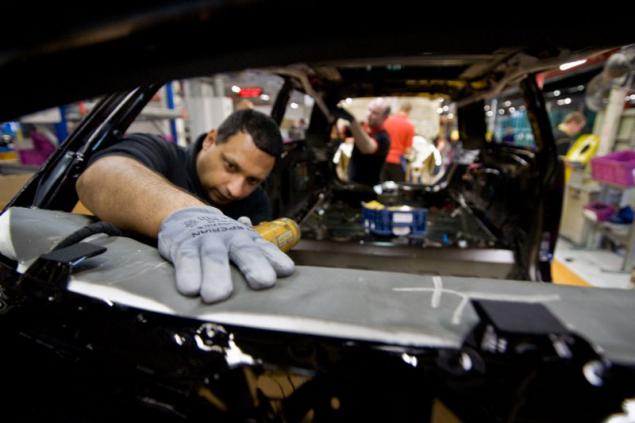
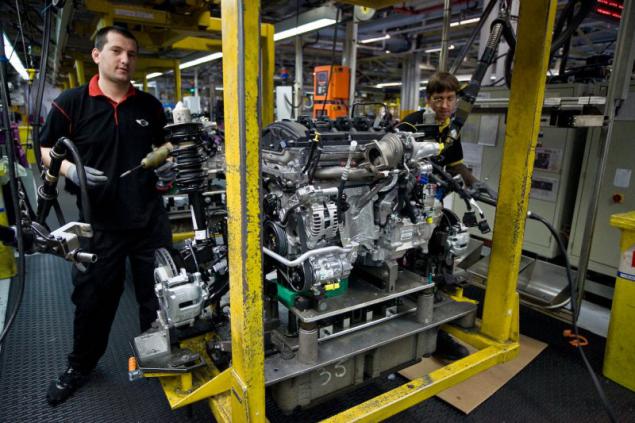
Here are preparing the engine to the transmission and front axle to be installed inside the body.
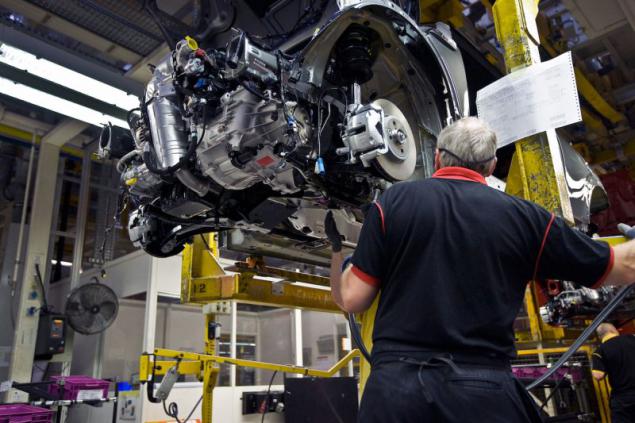
I had not even noticed the engine was at the right place. Moreover, everything is calm, somehow, even with the lazy, leisurely.

Here MINI gets its wheels.
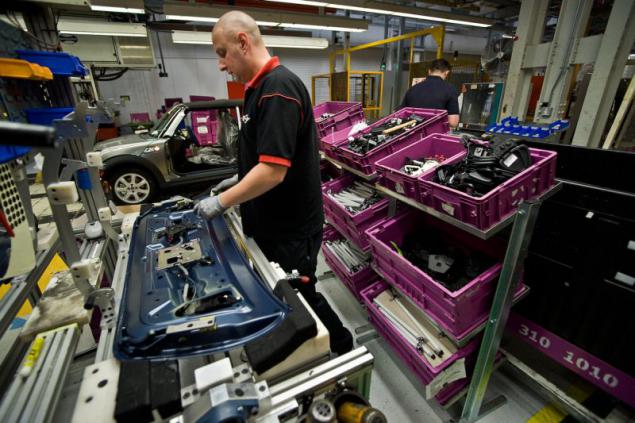
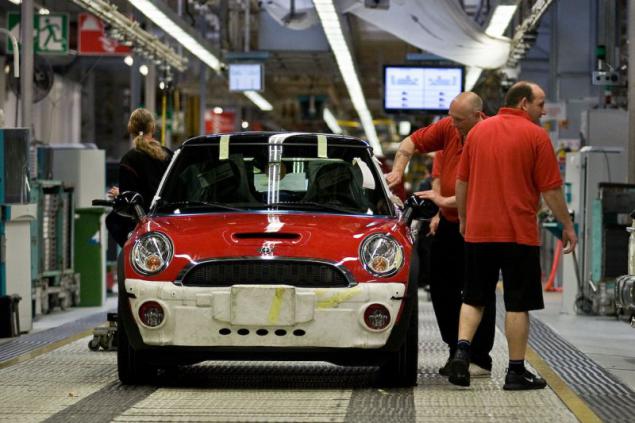
It is said that two absolutely identical MINI on the line is not seen. On each machine hangs a piece of paper with barcodes and when another car pulls up to the new site, the master reads the barcode scanner and it puts on the body that need this particular car.
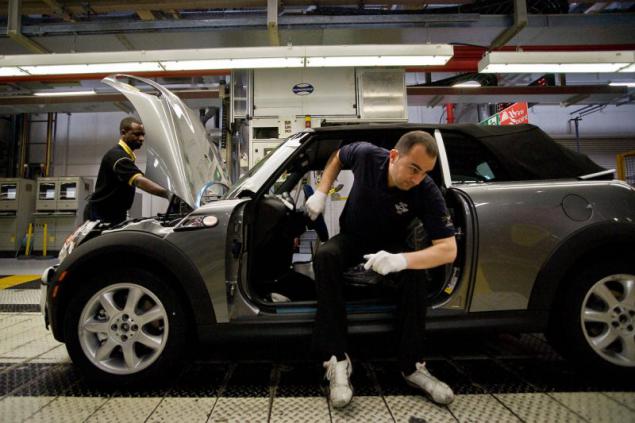
Finals getting closer. The machine itself has wheels on the ground, the assembly is nearing its end.

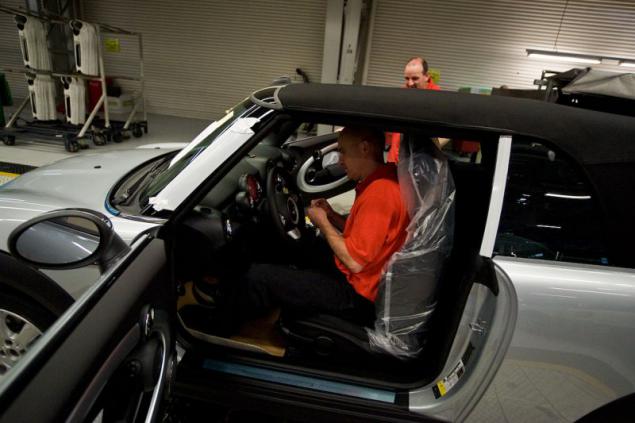
Finally, in the new car gets its first driver.
Starter dry clicks several times and distributed under the hood low sound of the engine. The car was born.
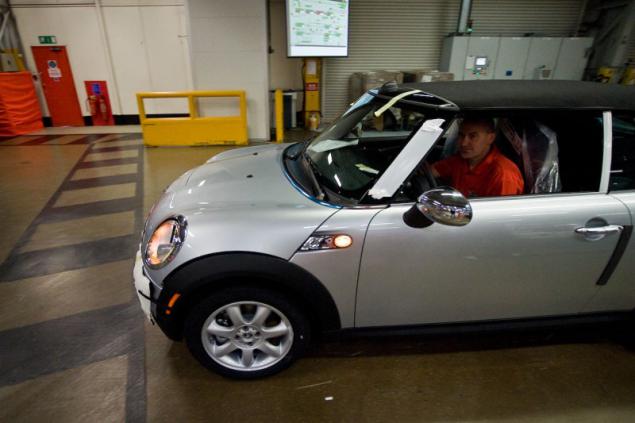
Let's go!
drugoi