1052
Modern aluminum production
russos.livejournal.com/905360.html ©
"Kazakhstan Electrolysis Plant" (KEP) - the only aluminum producer in the Republic of Kazakhstan, located in Pavlodar.
It is an industrial enterprise value of $ 900 million represents the largest private investment in Kazakhstan in metallurgy and mining. It produces primary aluminum - aluminum ingots technological purity, weight 20 kg, tied in packages weighing 1080 ± 100 kg.
First, a little history:
In 1854, French scientist Henri Etienne Sainte-Claire Deville, opened way to the industrial production of aluminum, based on extruded aluminum metallic sodium from the double chloride of sodium and aluminum. Over the 36 years of its use, from 1855 to 1890. In a manner St. Clair Deville had received 200 tons of aluminum metal.
In 1856 the factory in Rouen Tissier brothers Deville organized the first industrial plant for the production of aluminum. The cost of 1 kg of aluminum initially equal to 300 francs. After a few years managed to reduce the selling price to 200 francs per 1 kg, but still she remained exceptionally high. Aluminium at this time is used almost as a precious metal for the manufacture of various products.
The modern method of producing was developed independently by American Charles Hall and Frenchman Paul Heroult in 1886. It consists in dissolving alumina in molten cryolite, followed by electrolysis using consumable graphite electrodes or coke. This method of producing electricity is expensive, and therefore proved to be in demand only in the XX century.
For the production of 1 ton of aluminum requires rough 1, 920 tons of alumina, 0, 065 tons of cryolite, 0, 035 tons of aluminum fluoride, 0, 600 tons of anode paste and 17 th. KWh of electricity DC.
SUMMARY aluminum production process is to obtain anhydrous, free from impurities of aluminum oxide (alumina), followed by obtaining metallic aluminum by electrolysis of alumina dissolved in cryolite.
1. For the supply of current to the electrolyte used carbon electrode.
2. For the supply of current to the electrode is used a steel wire (nipple).
3. The electrodes are produced in the anode shop.
4.
5.
6. The plant was built by the Chinese and the Chinese money.
7. Electrolysis shop.
8. The cell is a bath of molten cryolite, a double fluoride of sodium and aluminum, which is dissolved in 3-5% alumina, - floating on a cushion of molten aluminum. Steel tire passing through the hearth of the carbon plates are used for supplying voltage to the cathode and suspended coal bars immersed in molten cryolite, serve as anodes. Operating temperature of the process is close to 950 ° C, well above the melting point of aluminum. Temperature in the electrolytic cell is regulated by changing the gap between the anode and the cathode metal reservoir, which is deposited on the molten aluminum.
9. The current in electrolytic cells is 150 000 A. The operating voltage on the bath 4-5 B. Near the present electrolytic strong electromagnetic field.
10. Space installation on bridge cranes for all manipulations of the cell.
11. cell trough to the horizon.
12. Behind me the same amount and same beside a nearby shop. There groundwork for the construction of more plants.
13. Megaustanovka.
14.
15. Install new electrodes.
16.Ispolzovannye electrodes.
17.Spetsialnaya car anode transport pallet. They are used to transport fresh anodes and anode butts between the anode and assembly department (AMO) and the electrolysis.
18.
19. Foundry.
20. The main equipment of this department - reverberatory furnaces (mixers) with electric heating.
21. "Tea" with aluminum.
22. After the molten aluminum holding furnace for 30-45 minutes at a temperature of about 700 degrees occurs aluminum casting.
23. Give the metal!
24. The filling machine conveyor type.
25. Finished products are packed in pallets of 1,000 kg and is sent to the warehouse. The cost of one pallet 2,600 $
26. A return electrode used in the anode plant.
27.Stalnoy conductor is released from the remnants of the electrode and then goes to the cause.
Everything!)
Source:
"Kazakhstan Electrolysis Plant" (KEP) - the only aluminum producer in the Republic of Kazakhstan, located in Pavlodar.
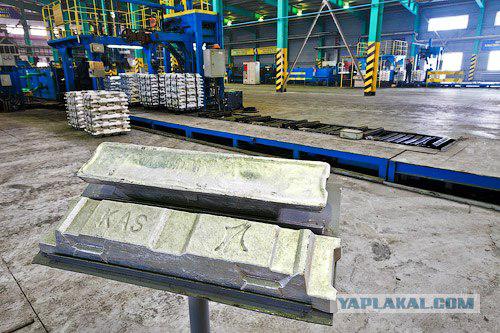
It is an industrial enterprise value of $ 900 million represents the largest private investment in Kazakhstan in metallurgy and mining. It produces primary aluminum - aluminum ingots technological purity, weight 20 kg, tied in packages weighing 1080 ± 100 kg.
First, a little history:
In 1854, French scientist Henri Etienne Sainte-Claire Deville, opened way to the industrial production of aluminum, based on extruded aluminum metallic sodium from the double chloride of sodium and aluminum. Over the 36 years of its use, from 1855 to 1890. In a manner St. Clair Deville had received 200 tons of aluminum metal.
In 1856 the factory in Rouen Tissier brothers Deville organized the first industrial plant for the production of aluminum. The cost of 1 kg of aluminum initially equal to 300 francs. After a few years managed to reduce the selling price to 200 francs per 1 kg, but still she remained exceptionally high. Aluminium at this time is used almost as a precious metal for the manufacture of various products.
The modern method of producing was developed independently by American Charles Hall and Frenchman Paul Heroult in 1886. It consists in dissolving alumina in molten cryolite, followed by electrolysis using consumable graphite electrodes or coke. This method of producing electricity is expensive, and therefore proved to be in demand only in the XX century.
For the production of 1 ton of aluminum requires rough 1, 920 tons of alumina, 0, 065 tons of cryolite, 0, 035 tons of aluminum fluoride, 0, 600 tons of anode paste and 17 th. KWh of electricity DC.
SUMMARY aluminum production process is to obtain anhydrous, free from impurities of aluminum oxide (alumina), followed by obtaining metallic aluminum by electrolysis of alumina dissolved in cryolite.
1. For the supply of current to the electrolyte used carbon electrode.
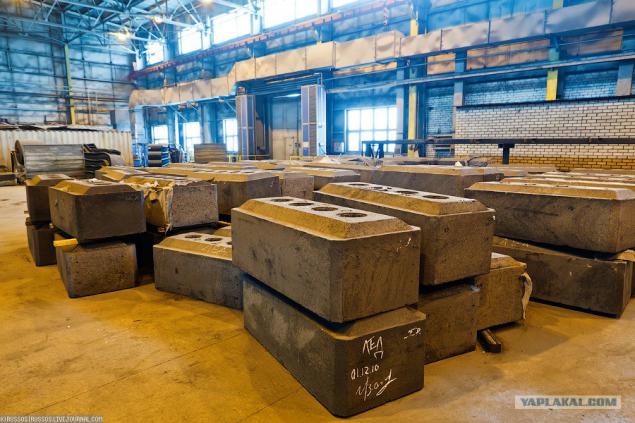
2. For the supply of current to the electrode is used a steel wire (nipple).
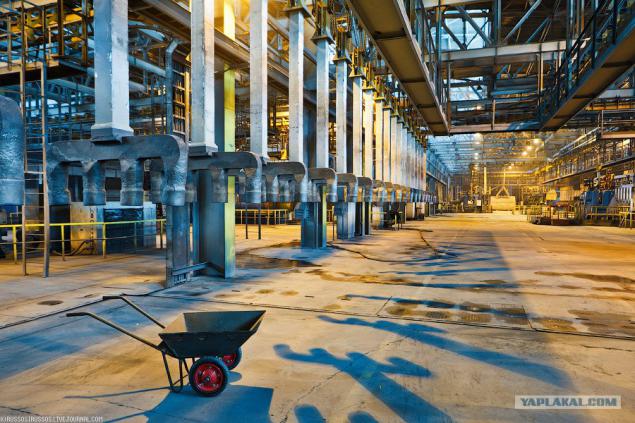
3. The electrodes are produced in the anode shop.
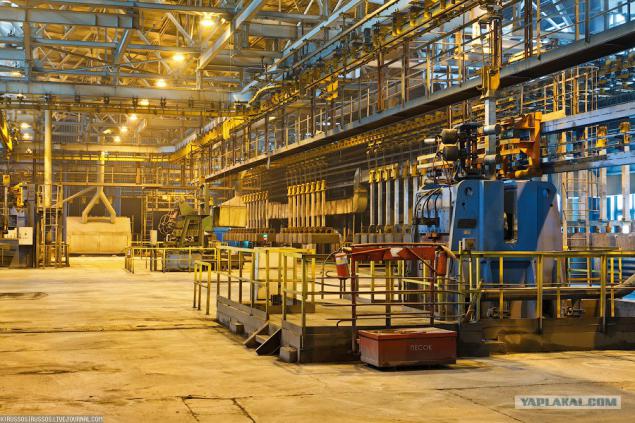
4.
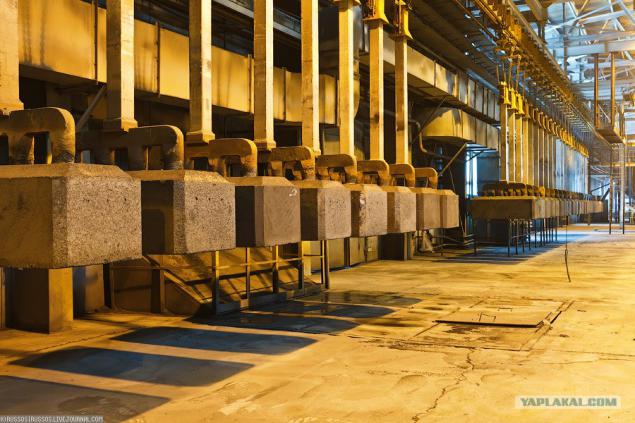
5.
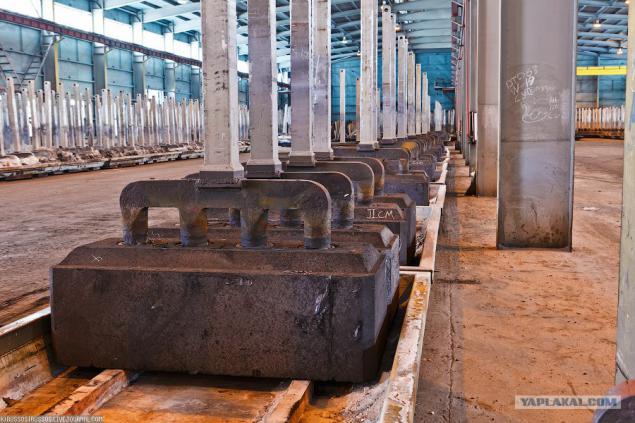
6. The plant was built by the Chinese and the Chinese money.
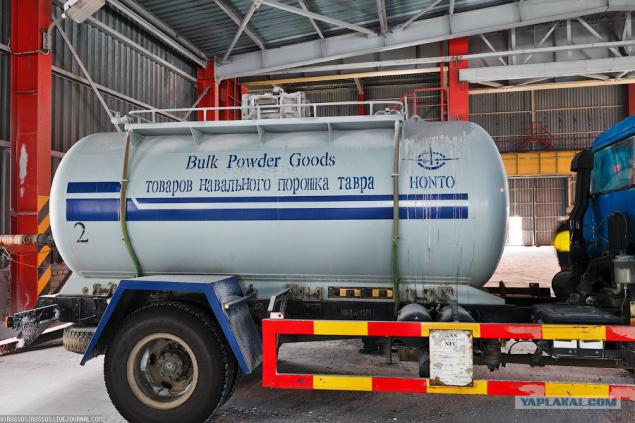
7. Electrolysis shop.
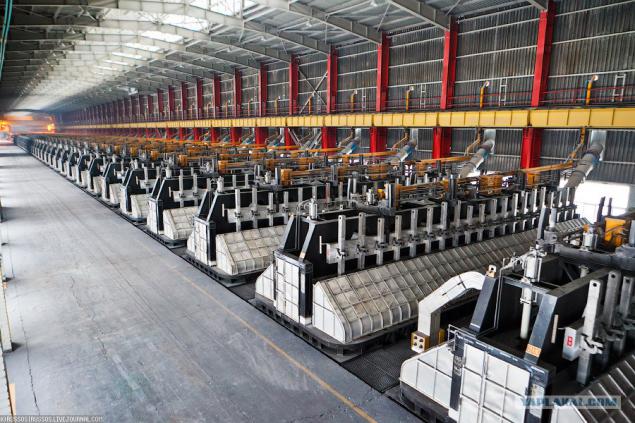
8. The cell is a bath of molten cryolite, a double fluoride of sodium and aluminum, which is dissolved in 3-5% alumina, - floating on a cushion of molten aluminum. Steel tire passing through the hearth of the carbon plates are used for supplying voltage to the cathode and suspended coal bars immersed in molten cryolite, serve as anodes. Operating temperature of the process is close to 950 ° C, well above the melting point of aluminum. Temperature in the electrolytic cell is regulated by changing the gap between the anode and the cathode metal reservoir, which is deposited on the molten aluminum.
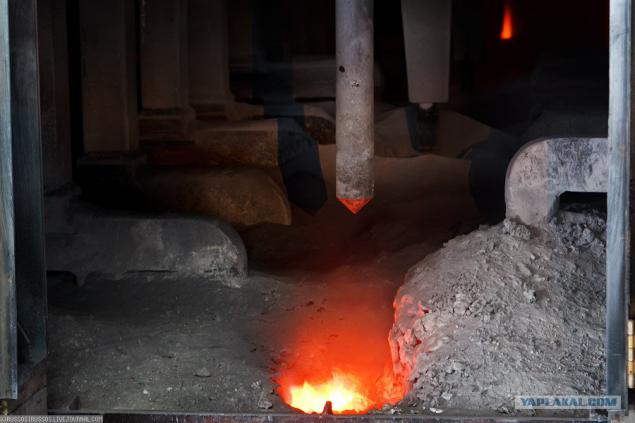
9. The current in electrolytic cells is 150 000 A. The operating voltage on the bath 4-5 B. Near the present electrolytic strong electromagnetic field.
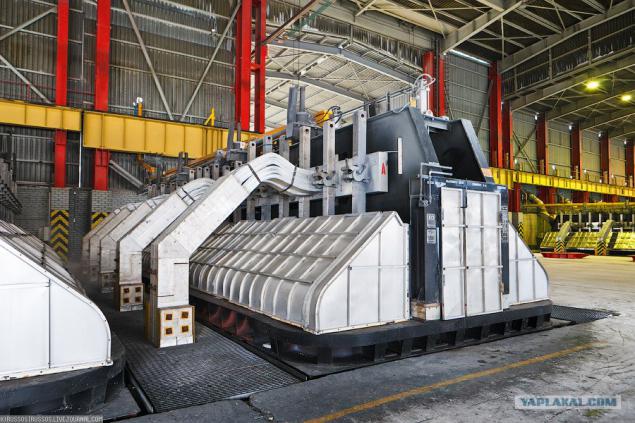
10. Space installation on bridge cranes for all manipulations of the cell.
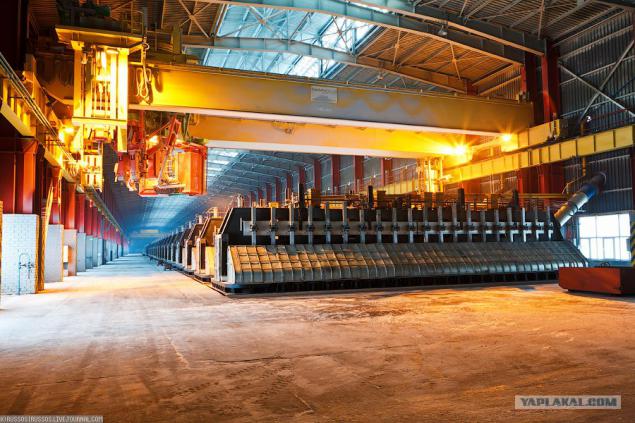
11. cell trough to the horizon.
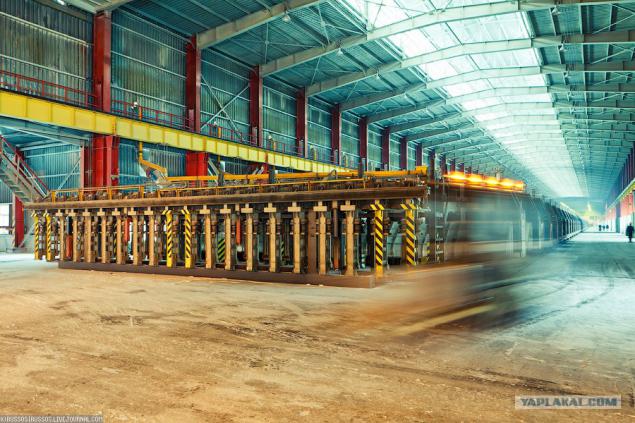
12. Behind me the same amount and same beside a nearby shop. There groundwork for the construction of more plants.
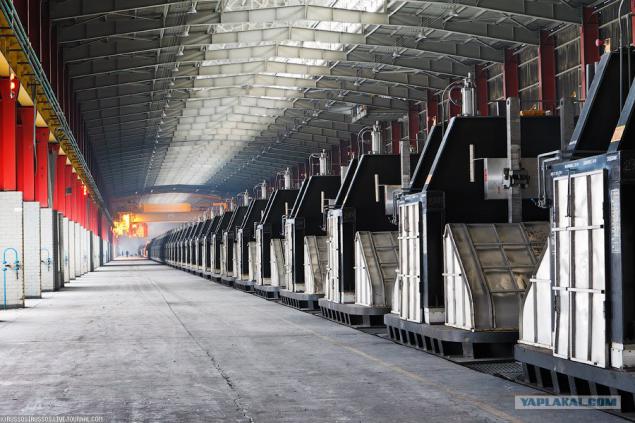
13. Megaustanovka.
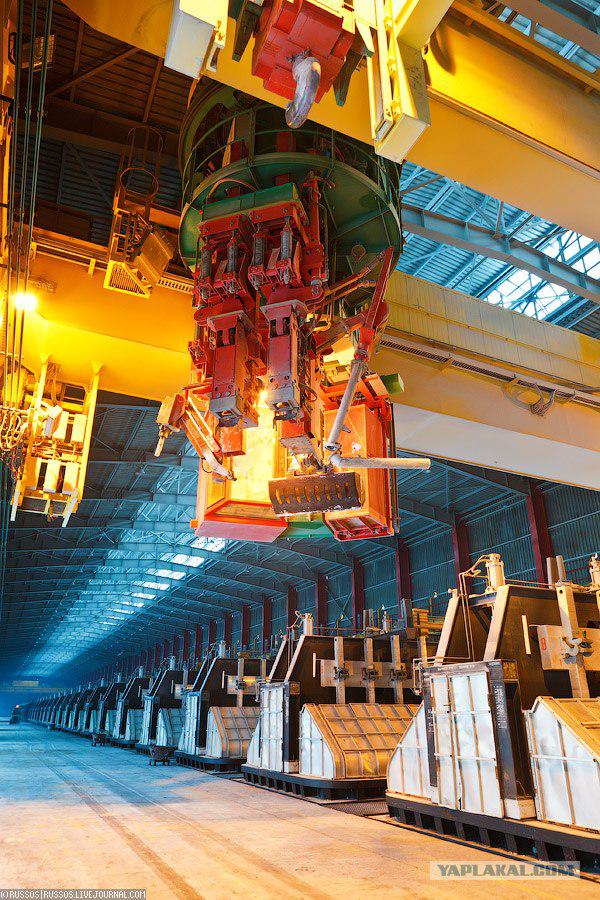
14.
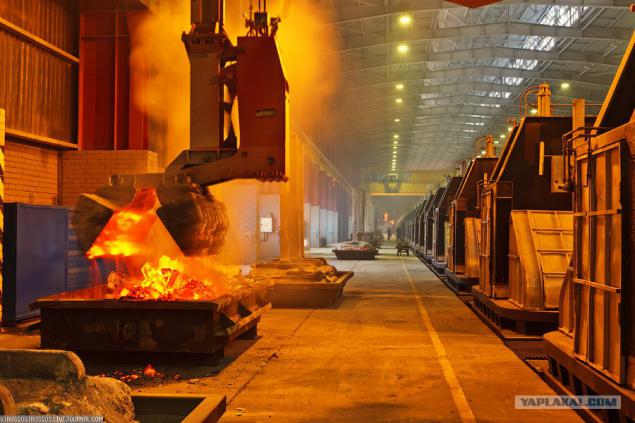
15. Install new electrodes.
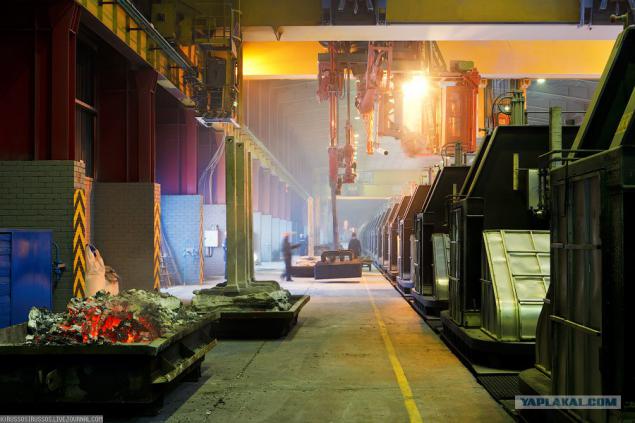
16.Ispolzovannye electrodes.
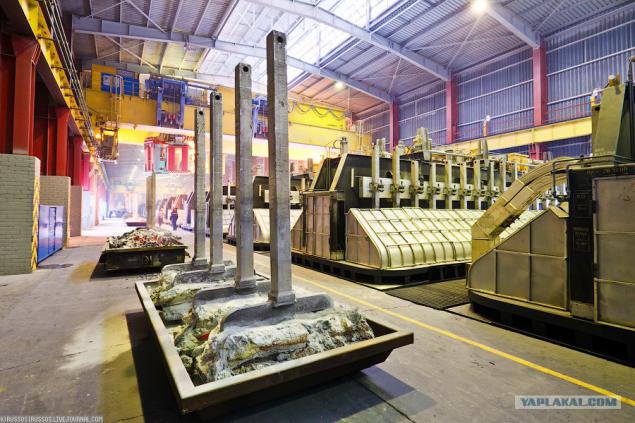
17.Spetsialnaya car anode transport pallet. They are used to transport fresh anodes and anode butts between the anode and assembly department (AMO) and the electrolysis.
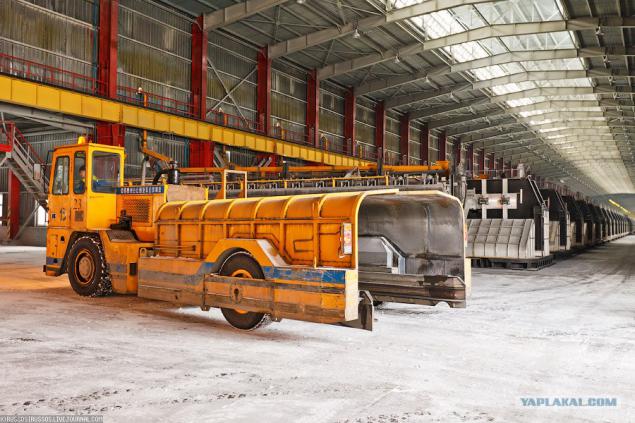
18.
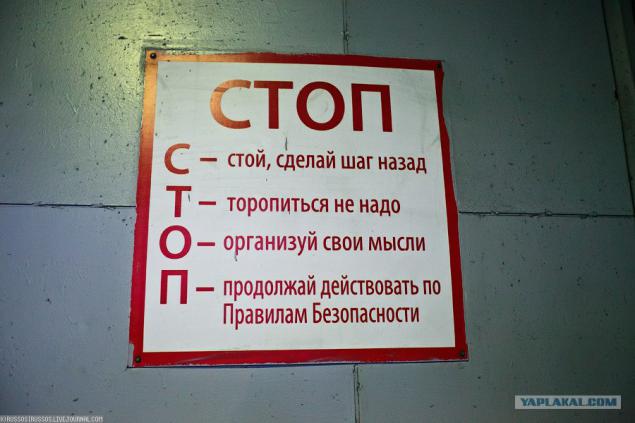
19. Foundry.
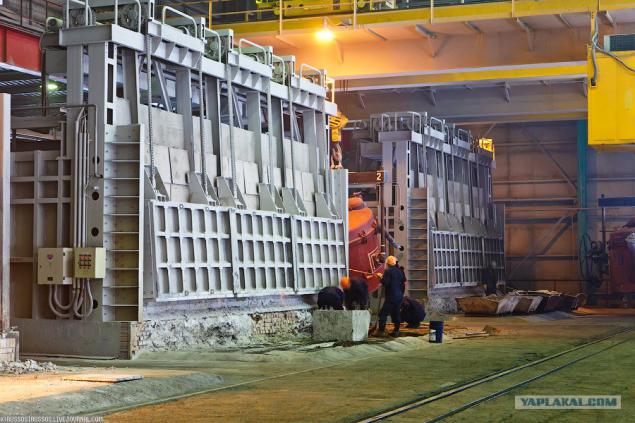
20. The main equipment of this department - reverberatory furnaces (mixers) with electric heating.
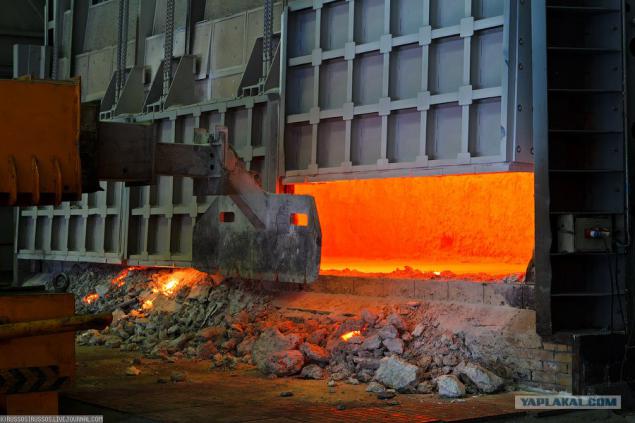
21. "Tea" with aluminum.
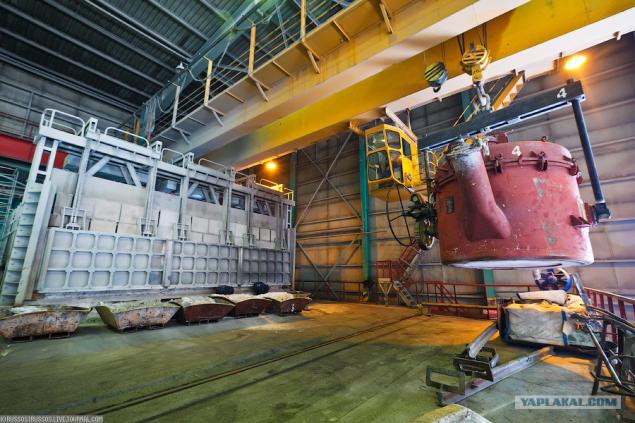
22. After the molten aluminum holding furnace for 30-45 minutes at a temperature of about 700 degrees occurs aluminum casting.
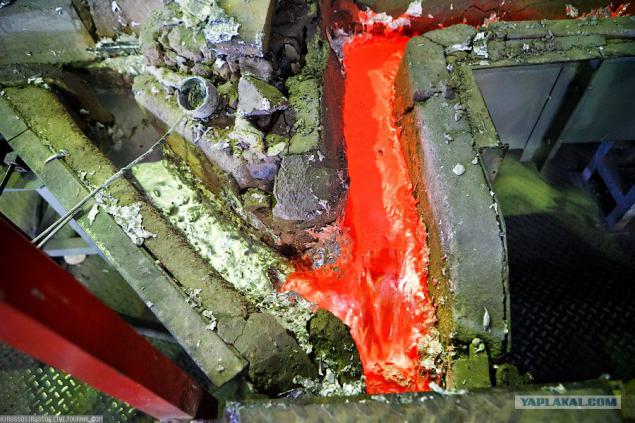
23. Give the metal!
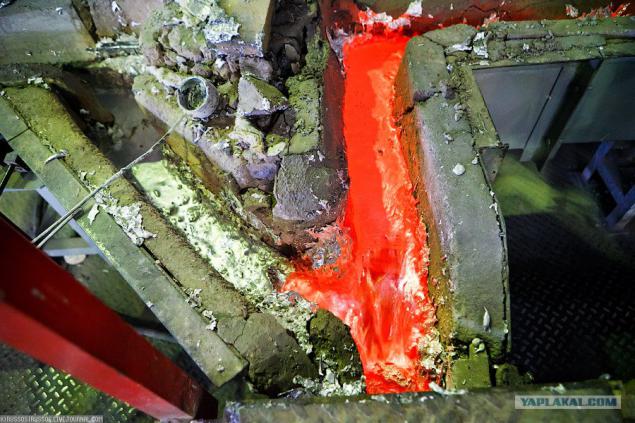
24. The filling machine conveyor type.
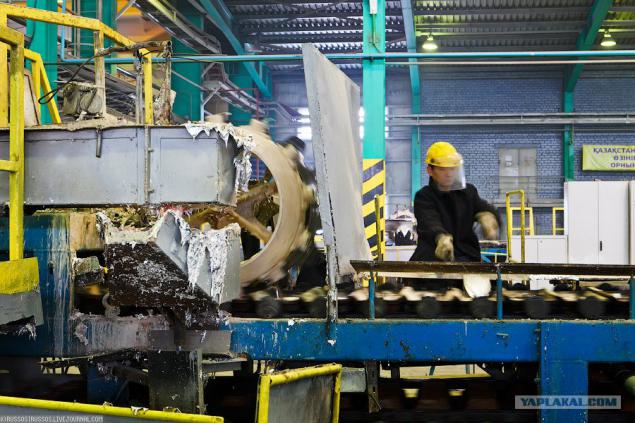
25. Finished products are packed in pallets of 1,000 kg and is sent to the warehouse. The cost of one pallet 2,600 $
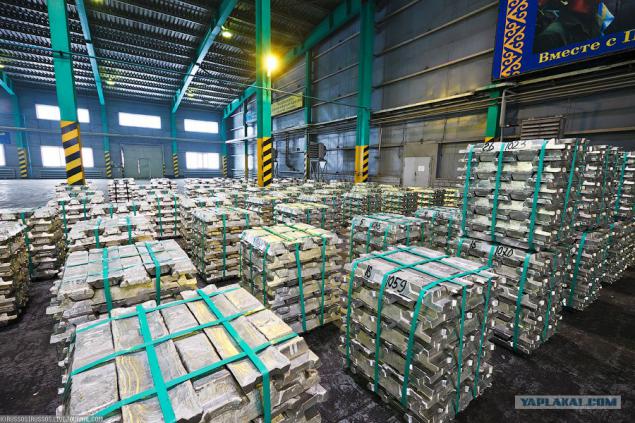
26. A return electrode used in the anode plant.
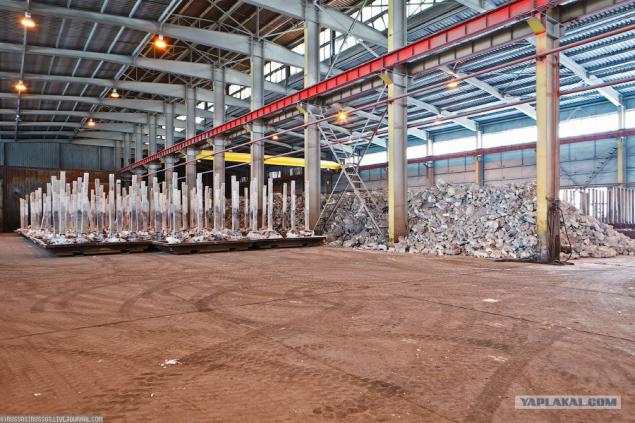
27.Stalnoy conductor is released from the remnants of the electrode and then goes to the cause.
Everything!)
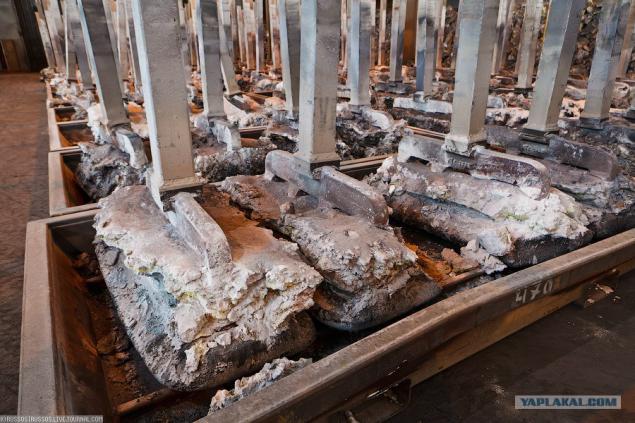
Source: