850
How to collect the Nissan Russian! (13 photos)
Representing the Japanese automaker Nissan's run-up to the release of a new model for rossiyskigo market, uncover the secrets of adaptation of its production under the domestic consumer. The Japanese are allowed to get into the holy of holies - manufacturing plants conveyor assembly models Teana and X-Trail, write auto.vesti
X-Trail.
Cars are in discord with the metal body Teana inches unpainted X-Trail. Technological ease of assembly of foreign models is not in doubt, while the training of domestic garbage - the subject of much interest. Outside on the curious tourists looking long building of regular geometric shape. On clean white background with red letters emblazoned the name of world-famous brand Nissan. On the face of the building and its surroundings look sedate and European-kept, but it all inside.
The assembly process
People at the plant perform 90% of the work on the manual assembly and constant control over the quality of products. At the mercy of the robotic technique is given to only 10% of the process of creating cars that include painting cars. Representatives of the Japanese auto giant is currently at the plant near St. Petersburg, Russian localization completely eliminate - the use of domestically produced parts. Without exception, all parts, until the screws and gears, are brought to the village of Kamenka, from Japan as well as China and Thailand. At first glance, the shop internal logistics (strategic management of material flows in the process of procurement, supply, transportation and storage of materials), which deliver imported parts, reminiscent of carefully polished corridors of Finnish furniture warehouses with huge stacks of cardboard boxes. In the warehouse, "cabinets" deftly move the machine-tractor, dragging boxes from place to place. In nearby - Hall for disassembly, all new arrivals by sea parts are tested for quality. Rejected parts flaunt proudly on a large table under the inscription: "Do not use." Parts of the plant have been approved by experts, sent to the packaging of delivery next to the welding shop.
It is in the welding hall there is first a one piece construction from foreign parts, which resembles the skeleton of the car. When the skeleton model, whether Teana and X-Trail, adjusted down to 0, 1 millimeter, becoming more or less recognizable appearance, body parts sent to check welding. According to two people spinning each model with special equipment in order to calculate the slightest error. People engaged in this work, are, according to experts factories, special technical education, someone on probation in Japan. By the way, all employees of the plant before you get to the stage of training workshops held. "Experience in other automotive industry does not have any importance for us, if a man can do or frequently mistaken in those jobs that we give," - said the expert plant personnel training.
Finding error - working body sent back for revision or junk - depending on the ease shortage. The model that has been tested, moves to the paint shop, where her body special robot first applies the ground, and then dries and sends to the grout into the hands of specialists of the plant. People in masks and special suits inspect brushes places that has not reached the "iron hand" of the robot, and to make up for all the work machine. His final color of the frame of the car gets to the next stage pipeline - are engaged in painting robots, but some parts (internal parts of the bonnet, boot lid) them again to finish people. The dried body is sent to the assembly plant, where first of all the factory workers are paving the entire wiring. After that, the next car equipped with heaters and install the front panel. The next stage of the assembly line - assembly and installation of interior attachments engine compartment, further - installation of doors, wheels and seats. The last stage of the assembly line - computer software downloads in a car. Once the car leaves the assembly line, it is tested and sent in a row to their brand new brethren. By the way, a factory work and experts from Japan. Guests from the country of the rising sun, and supervise carefully check all stages of assembly. Foreign experts also help their Russian colleagues to quickly get to the car assembly technology and adapt to the Japanese tradition of production.
According to the workers of the factory, the factory currently operates in order. That is, all Russian automobile assembly, which is similar to the assembly line, already have a buyer. Now the performance of 750 workers of the factory is 8 vehicles per day, despite the fact that for the assembly of a car takes about 40 hours. The company is certainly capable of higher production rates (up to 12 vehicles per day), but while sales of "Russian» Teana and X-Trail does not allow to reach the desired level. Perhaps a new model of Russian assembly will be more budget and pay off, and will contribute to the development of the Japanese branch in Russia.
Rival Ford Focus
On the question of a new model, the director of the production of "Nissan Manufacturing Rus" Dmitry Mikhailov said that the company itself has not decided which model of the Japanese auto giant will enter the following into the Russian pipeline. However, he does not deny that the easiest platform to alter under the current production release Qashqai. Explaining such a scenario, Mikhailov immediately refuted it by saying that Nissan is supposedly not profitable to produce the same model in the same geographic region, as Qashqai has collected in England. "The launch of Qashqai in Russia will not be as effective as one of the main tasks of the new model - the economic benefits for Russian consumers", - said Mikhailov. Nissan and is considering the development of special machines for the Russian market. "The success in Russia Ford Focus, of course, of great interest. With good sales and future development of production activities in this direction are not excluded. But as long as we do not have their own entry-level cars, "- said Dmitry Mikhailov.
Made in Japan
The issue with the Russian localization of "Nissan Manufacturing Rus" is not yet resolved - Now there is not even a screw factory of Russian production in the near future the emergence of Russian auto parts should not wait. "We are negotiating with some suppliers from Russia. Once it is established that the products offered by them responsible for the quality of our needs, we will work with them. While all parts are imported, mostly by sea (containers with item comes three months after the date of order). So it will be as long as their quality, we do not zarekomenduem cars as the Japanese brand product, this time we still have (under the rules of a foreign company have 3 years to reach a 30% of the Russian localization). The release of the new model will be based on the same principle - the first cars will be entirely of the Japanese auto parts. If at the time of its release, we have to cooperate with someone from Russian suppliers, these parts may be in the new model. As long as there are none, "- said Mikhailov. However, an expert from the department of internal logistics of the plant suggested that the first Russian parts may become car seats. According to the engineer Nissan, the company is negotiating with a supplier of car seats, which is already working now Ford. According to some estimates, as high probability that the situation will facilitate the emergence of the Russian market branches of foreign auto parts manufacturers. In cooperation with a number of auto giants, foreign suppliers are already quite closely studying the possibility of working in the Russian market.
Benefit purchase of Nissan Russian assembly is pretty obvious - the final price of the car is expected to be less than the machines of the same model of foreign production. To gain momentum and begin to produce budget cars, Nissan started production with Russian expensive but popular models - Teana and X-Trail. Their success will help the company turn around and gain momentum on the Russian market. "Now everything depends on the economic situation in the Russian market. Sales volume dictates the conditions. Once the company sees that production in Russia - profitable, it will be invested in energy and money. For example, the price of Russian assembly Teana now allows customers to save up to 8% "- summed Dmitry Mikhailov at a news conference after a tour of the factory. The future will show how firmly Nissan will be able to gain a foothold in the Russian car market, but it is now clear that in the case of reducing car prices, customers do not wait long. For Japanese manufacturers offer a guarantee and put their stamp of quality on cars assembled in Russia.
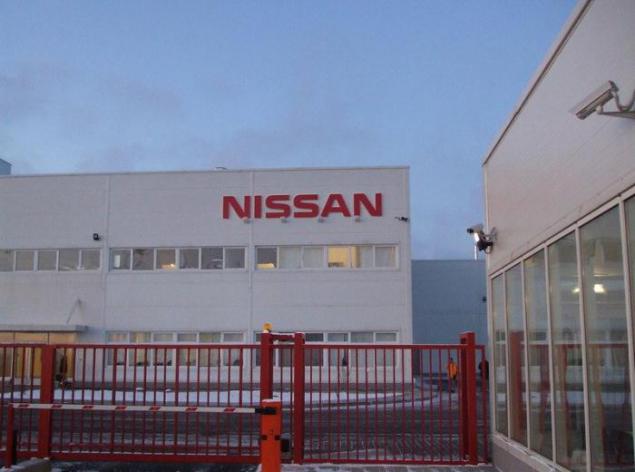
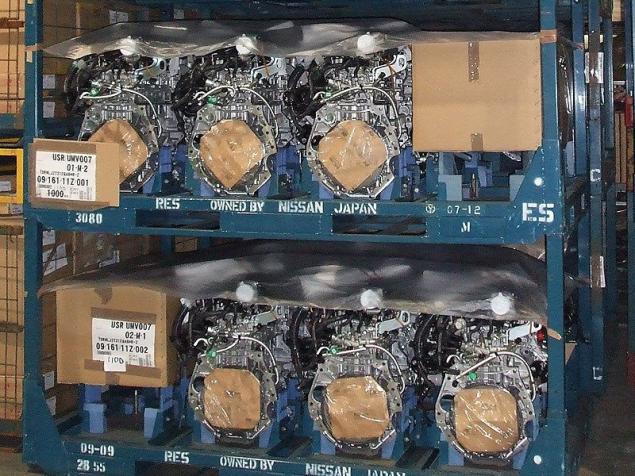
X-Trail.
Cars are in discord with the metal body Teana inches unpainted X-Trail. Technological ease of assembly of foreign models is not in doubt, while the training of domestic garbage - the subject of much interest. Outside on the curious tourists looking long building of regular geometric shape. On clean white background with red letters emblazoned the name of world-famous brand Nissan. On the face of the building and its surroundings look sedate and European-kept, but it all inside.
The assembly process
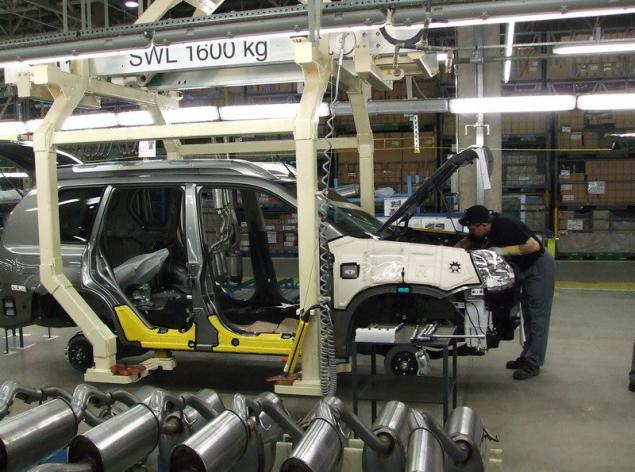
People at the plant perform 90% of the work on the manual assembly and constant control over the quality of products. At the mercy of the robotic technique is given to only 10% of the process of creating cars that include painting cars. Representatives of the Japanese auto giant is currently at the plant near St. Petersburg, Russian localization completely eliminate - the use of domestically produced parts. Without exception, all parts, until the screws and gears, are brought to the village of Kamenka, from Japan as well as China and Thailand. At first glance, the shop internal logistics (strategic management of material flows in the process of procurement, supply, transportation and storage of materials), which deliver imported parts, reminiscent of carefully polished corridors of Finnish furniture warehouses with huge stacks of cardboard boxes. In the warehouse, "cabinets" deftly move the machine-tractor, dragging boxes from place to place. In nearby - Hall for disassembly, all new arrivals by sea parts are tested for quality. Rejected parts flaunt proudly on a large table under the inscription: "Do not use." Parts of the plant have been approved by experts, sent to the packaging of delivery next to the welding shop.
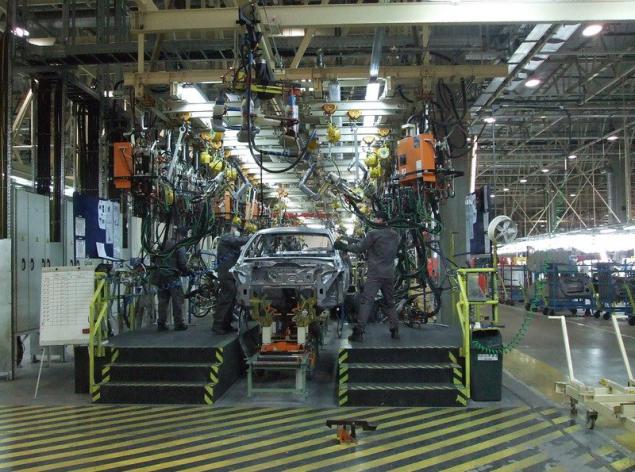
It is in the welding hall there is first a one piece construction from foreign parts, which resembles the skeleton of the car. When the skeleton model, whether Teana and X-Trail, adjusted down to 0, 1 millimeter, becoming more or less recognizable appearance, body parts sent to check welding. According to two people spinning each model with special equipment in order to calculate the slightest error. People engaged in this work, are, according to experts factories, special technical education, someone on probation in Japan. By the way, all employees of the plant before you get to the stage of training workshops held. "Experience in other automotive industry does not have any importance for us, if a man can do or frequently mistaken in those jobs that we give," - said the expert plant personnel training.
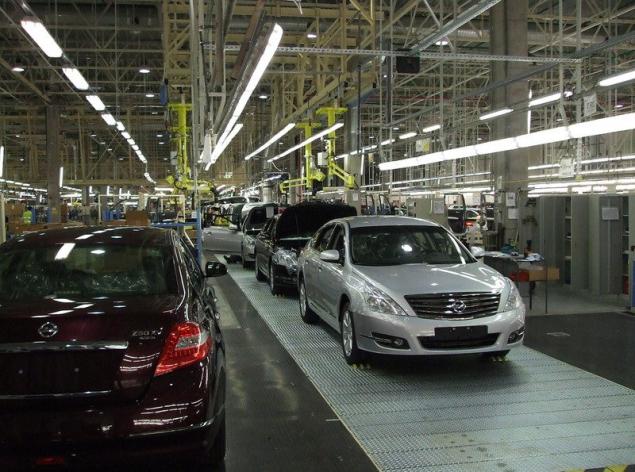
Finding error - working body sent back for revision or junk - depending on the ease shortage. The model that has been tested, moves to the paint shop, where her body special robot first applies the ground, and then dries and sends to the grout into the hands of specialists of the plant. People in masks and special suits inspect brushes places that has not reached the "iron hand" of the robot, and to make up for all the work machine. His final color of the frame of the car gets to the next stage pipeline - are engaged in painting robots, but some parts (internal parts of the bonnet, boot lid) them again to finish people. The dried body is sent to the assembly plant, where first of all the factory workers are paving the entire wiring. After that, the next car equipped with heaters and install the front panel. The next stage of the assembly line - assembly and installation of interior attachments engine compartment, further - installation of doors, wheels and seats. The last stage of the assembly line - computer software downloads in a car. Once the car leaves the assembly line, it is tested and sent in a row to their brand new brethren. By the way, a factory work and experts from Japan. Guests from the country of the rising sun, and supervise carefully check all stages of assembly. Foreign experts also help their Russian colleagues to quickly get to the car assembly technology and adapt to the Japanese tradition of production.
According to the workers of the factory, the factory currently operates in order. That is, all Russian automobile assembly, which is similar to the assembly line, already have a buyer. Now the performance of 750 workers of the factory is 8 vehicles per day, despite the fact that for the assembly of a car takes about 40 hours. The company is certainly capable of higher production rates (up to 12 vehicles per day), but while sales of "Russian» Teana and X-Trail does not allow to reach the desired level. Perhaps a new model of Russian assembly will be more budget and pay off, and will contribute to the development of the Japanese branch in Russia.
Rival Ford Focus
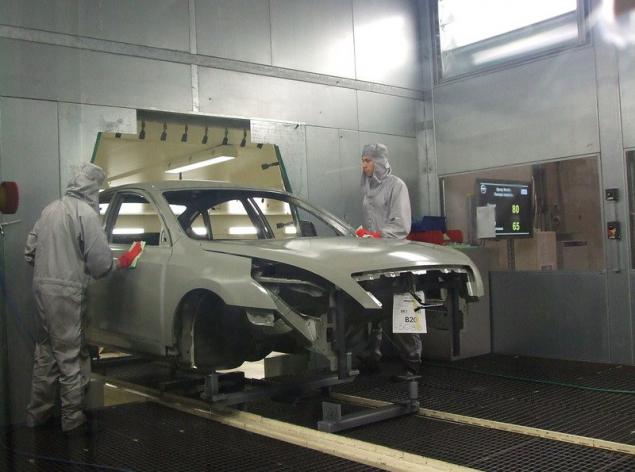
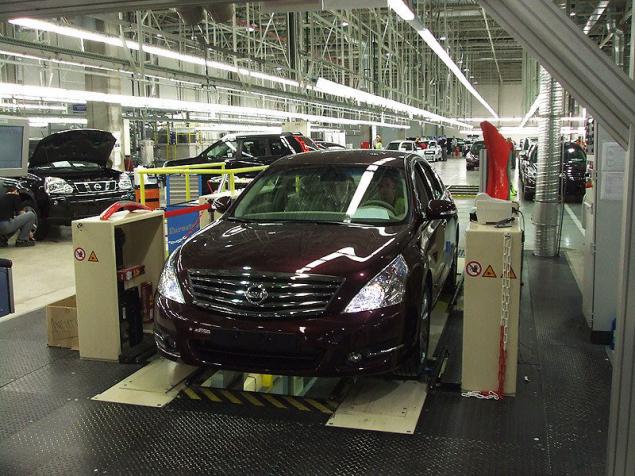
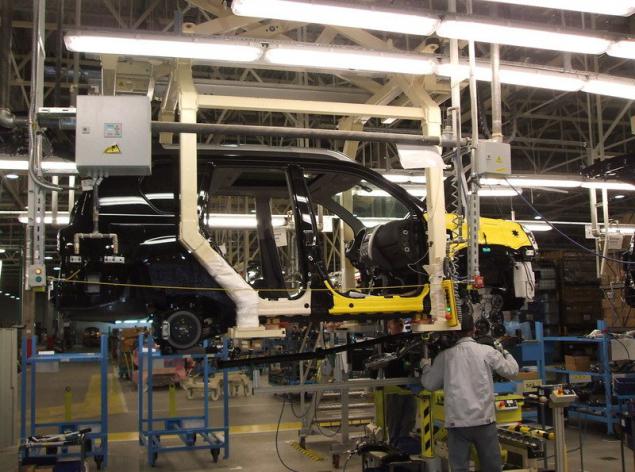
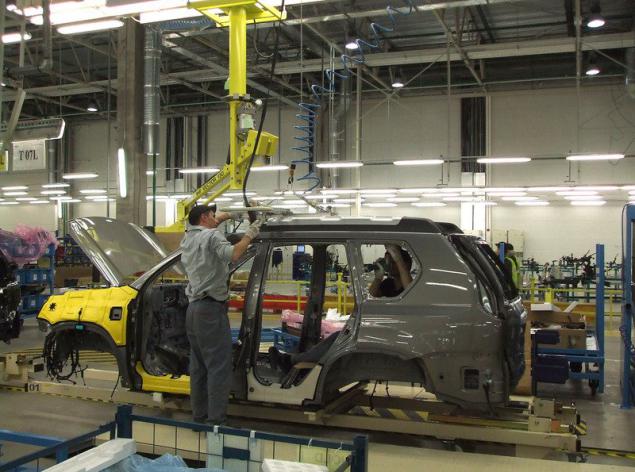
On the question of a new model, the director of the production of "Nissan Manufacturing Rus" Dmitry Mikhailov said that the company itself has not decided which model of the Japanese auto giant will enter the following into the Russian pipeline. However, he does not deny that the easiest platform to alter under the current production release Qashqai. Explaining such a scenario, Mikhailov immediately refuted it by saying that Nissan is supposedly not profitable to produce the same model in the same geographic region, as Qashqai has collected in England. "The launch of Qashqai in Russia will not be as effective as one of the main tasks of the new model - the economic benefits for Russian consumers", - said Mikhailov. Nissan and is considering the development of special machines for the Russian market. "The success in Russia Ford Focus, of course, of great interest. With good sales and future development of production activities in this direction are not excluded. But as long as we do not have their own entry-level cars, "- said Dmitry Mikhailov.
Made in Japan
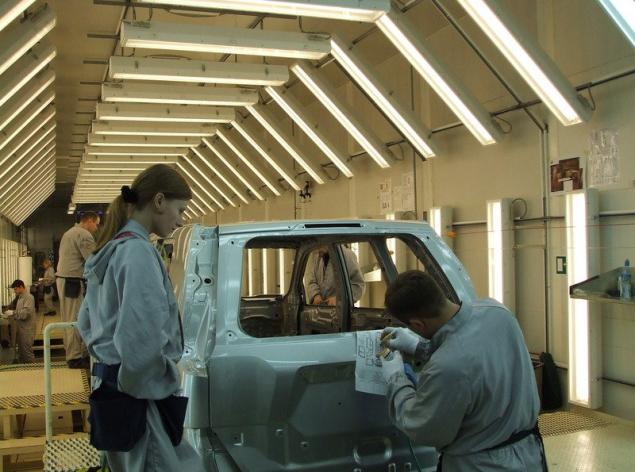
The issue with the Russian localization of "Nissan Manufacturing Rus" is not yet resolved - Now there is not even a screw factory of Russian production in the near future the emergence of Russian auto parts should not wait. "We are negotiating with some suppliers from Russia. Once it is established that the products offered by them responsible for the quality of our needs, we will work with them. While all parts are imported, mostly by sea (containers with item comes three months after the date of order). So it will be as long as their quality, we do not zarekomenduem cars as the Japanese brand product, this time we still have (under the rules of a foreign company have 3 years to reach a 30% of the Russian localization). The release of the new model will be based on the same principle - the first cars will be entirely of the Japanese auto parts. If at the time of its release, we have to cooperate with someone from Russian suppliers, these parts may be in the new model. As long as there are none, "- said Mikhailov. However, an expert from the department of internal logistics of the plant suggested that the first Russian parts may become car seats. According to the engineer Nissan, the company is negotiating with a supplier of car seats, which is already working now Ford. According to some estimates, as high probability that the situation will facilitate the emergence of the Russian market branches of foreign auto parts manufacturers. In cooperation with a number of auto giants, foreign suppliers are already quite closely studying the possibility of working in the Russian market.
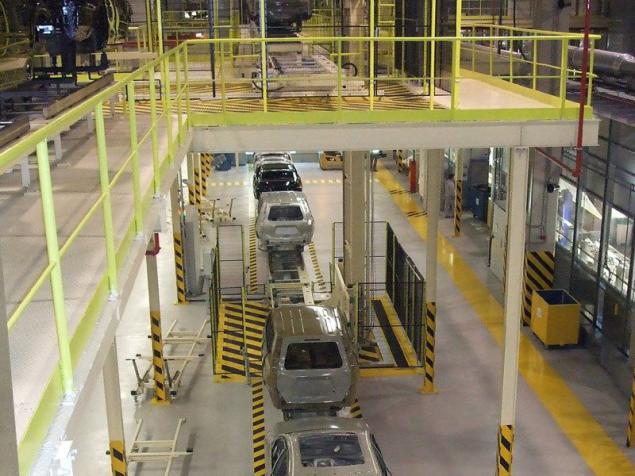
Benefit purchase of Nissan Russian assembly is pretty obvious - the final price of the car is expected to be less than the machines of the same model of foreign production. To gain momentum and begin to produce budget cars, Nissan started production with Russian expensive but popular models - Teana and X-Trail. Their success will help the company turn around and gain momentum on the Russian market. "Now everything depends on the economic situation in the Russian market. Sales volume dictates the conditions. Once the company sees that production in Russia - profitable, it will be invested in energy and money. For example, the price of Russian assembly Teana now allows customers to save up to 8% "- summed Dmitry Mikhailov at a news conference after a tour of the factory. The future will show how firmly Nissan will be able to gain a foothold in the Russian car market, but it is now clear that in the case of reducing car prices, customers do not wait long. For Japanese manufacturers offer a guarantee and put their stamp of quality on cars assembled in Russia.
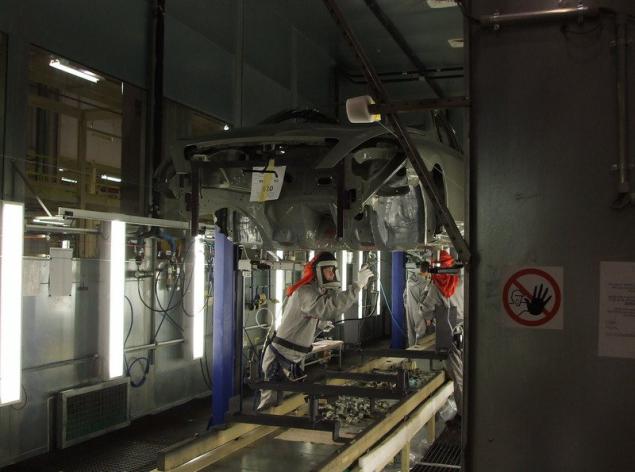
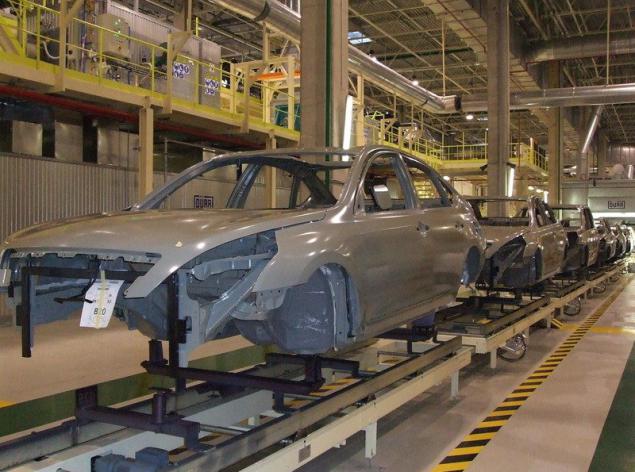