983
How are born tires (25 photos)
Bus today - it's so Flawless product, which makes it "by eye" is not possible. At all stages of the production of tires Cordiant big role, automation and computer controls. Already at the first stage of production - in the manufacture of a set of rubber compounds - virtually the entire process is electronically controlled.
In the internal mixer strictly metered components of the future tire - natural and synthetic rubber, carbon black (soot), sulfur. Sometimes the mixing is carried out in several steps, and then the tape has finished rubber mixture is fed into the machine again.
Mixtures are automatic quality control, and then those that successfully qualified leave the warehouse. There are some time "is stored for" and then enter the production of parts, such as rubberized cord hermetic layer frame, a belt, sidewall protector.
For the manufacture of rubberized cord uses a special machine - "creel". It looks very unusual: from a variety of challenges in a number of coils (spool) extend and converge to a single point thread metal wire (steel cord) - something that reminds a harp or a loom. Steel cord is fed to a special extruder in which a wire is pressed into the rubber sheet. Then it is cut to produce the desired part.
Thus obtained rubber-coated wire for special conveyors comes to large coils that are wound and for storage and transportation
The material is very sticky, and to avoid sticking and damage, between the wound layers placed pads
Types of gaskets are different. They are often mistaken for a tire being irregularly shaped
Manufacturers of this smile: "No, to the shape of the future bus we all normally»
Workpiece parts in the shop waiting in the wings until it is assembly step
Factory humor ...
... And orders
Final assembly of the tire takes place on a special machine concern Krupp. On this machine run only two: perezaryadchik and garbage. Perezaryadchik coil inserts into the machine components. Collector ring and put borotovoe on the machine does everything himself: he brings with germosloem Caracas and the side of the workpiece and blows air under the protector with the breaker.
The resulting crude bus runs on automatic checkweighing scales and visual inspection for possible defects.
Thereafter the workpiece are sent to the curing department
The last stage of the production takes place in the hot shop vulcanization. Here, the tire is subjected to hot-heat steam under high pressure. Rubber, carbon black and additives "sintered" together, and on the external and internal surface of the tire with the help of molds applied tread pattern, labels and other technical profiles.
The entire curing process is accompanied by steam and hissing sounds
By acting black "needles" can be seen that the data samples of the mold used for making winter tires
We called vulcanization workshop "chip" of the plant, and even asked to take us here at the end of the show for the second time. Apart from the fact that the process of "birth" of the tire causes interest of the audience, here you can still make wonderful pictures
Work process goes. Very soon these blanks will be familiar to us kind of tires
Despite the prevailing hot weather here, the shop vulcanization not want to leave. Light, the smell of hot rubber and the steam makes this place special
Just "born" tire. More steam. Right now coming next blank. Can be seen from the top of the mold to bring to the tire tread pattern and inscriptions
When the tire is ready, it takes place following harvesting. After 10 minutes, it will provide a bus, we can see every day
Products are ready, tested and delivered to the consumer waits for tests
After the end of the production process occurs test. We have shown this process by the example of aviation tires. In the center of the wheel spins up, simulating the speed of 340 km / h. After dialing the required number of revolutions of the wheel in contact with the bus for a while. There is a friction tire on the wheel - thus simulates the landing of the aircraft. Once the tire is cooled and the cycle is repeated a number of times
Source
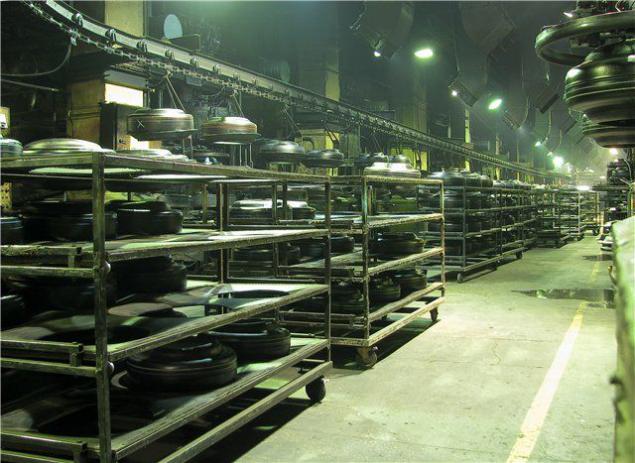
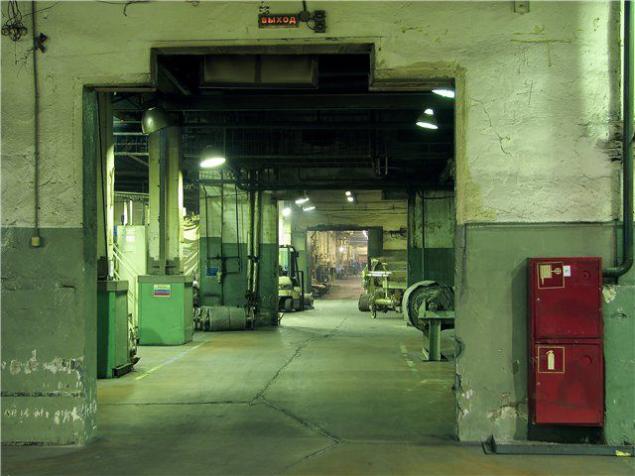
In the internal mixer strictly metered components of the future tire - natural and synthetic rubber, carbon black (soot), sulfur. Sometimes the mixing is carried out in several steps, and then the tape has finished rubber mixture is fed into the machine again.
Mixtures are automatic quality control, and then those that successfully qualified leave the warehouse. There are some time "is stored for" and then enter the production of parts, such as rubberized cord hermetic layer frame, a belt, sidewall protector.
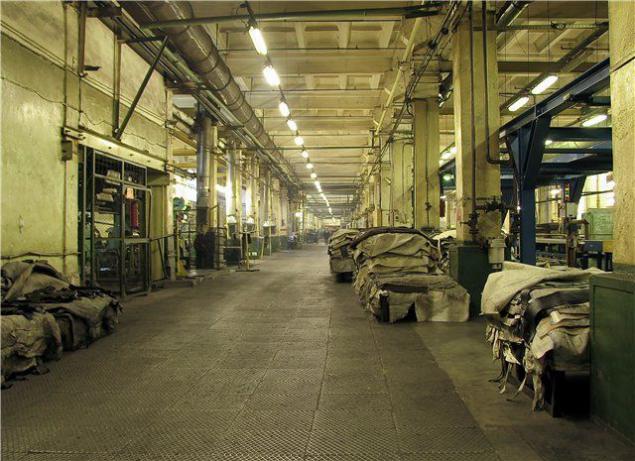
For the manufacture of rubberized cord uses a special machine - "creel". It looks very unusual: from a variety of challenges in a number of coils (spool) extend and converge to a single point thread metal wire (steel cord) - something that reminds a harp or a loom. Steel cord is fed to a special extruder in which a wire is pressed into the rubber sheet. Then it is cut to produce the desired part.
Thus obtained rubber-coated wire for special conveyors comes to large coils that are wound and for storage and transportation
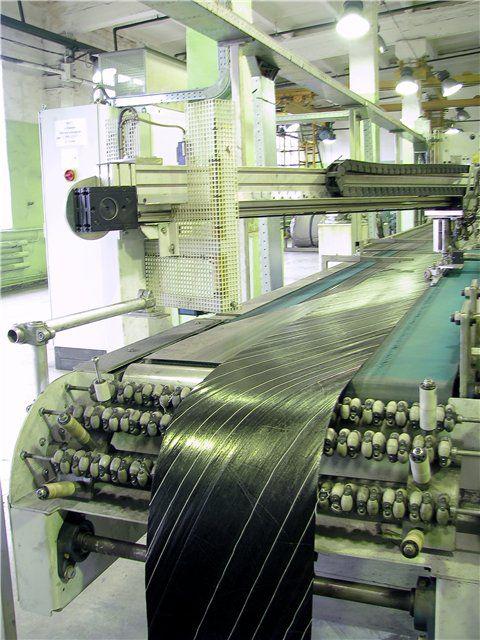
The material is very sticky, and to avoid sticking and damage, between the wound layers placed pads
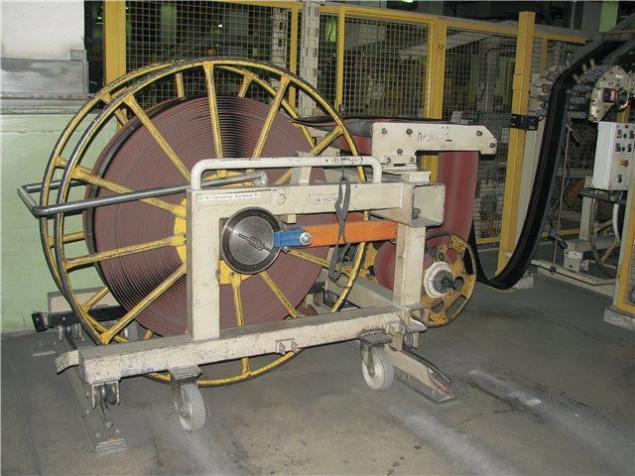
Types of gaskets are different. They are often mistaken for a tire being irregularly shaped
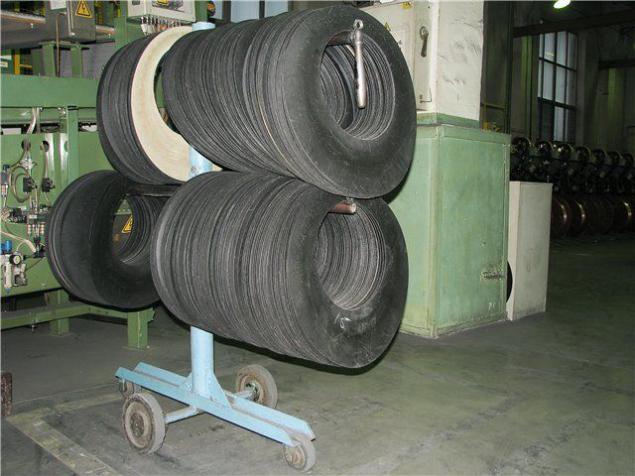
Manufacturers of this smile: "No, to the shape of the future bus we all normally»
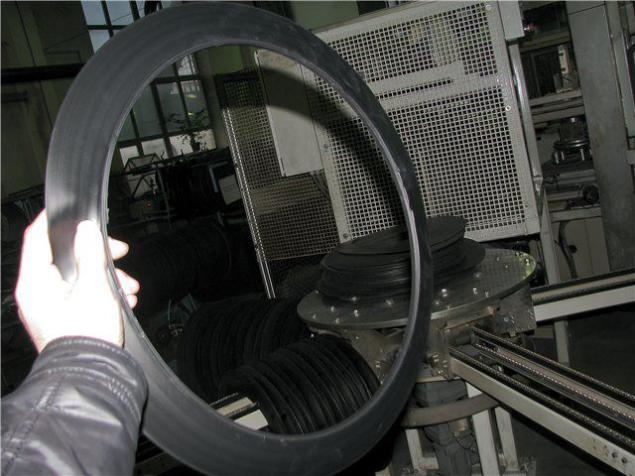
Workpiece parts in the shop waiting in the wings until it is assembly step
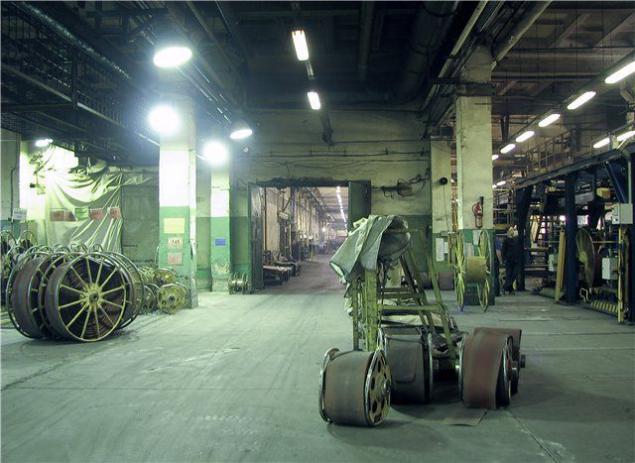
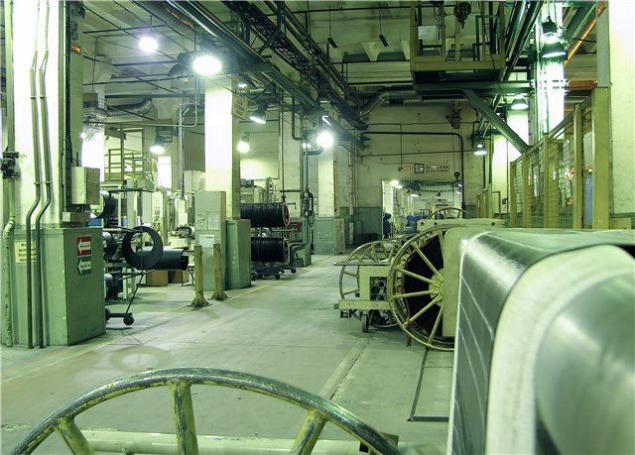
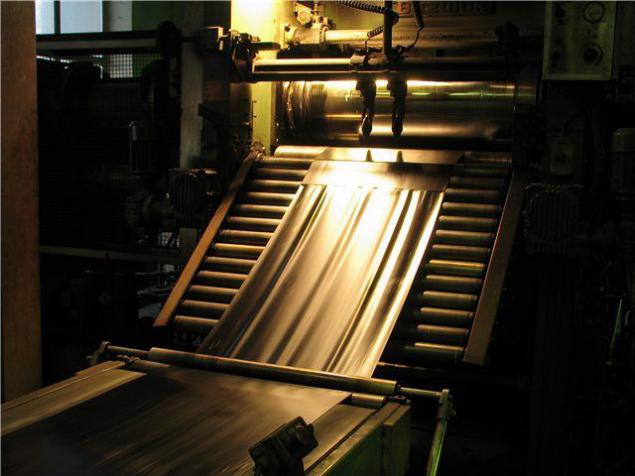
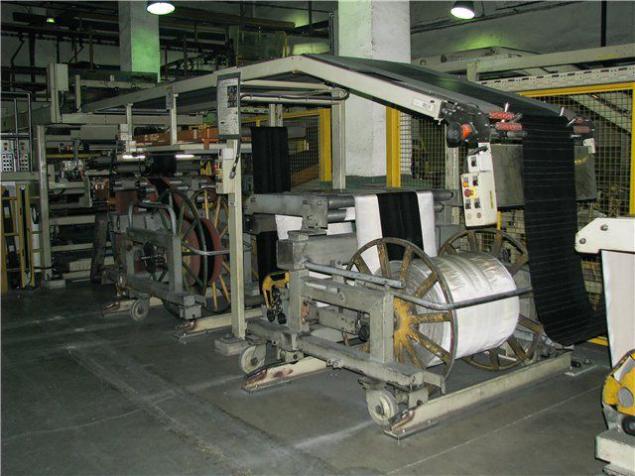
Factory humor ...
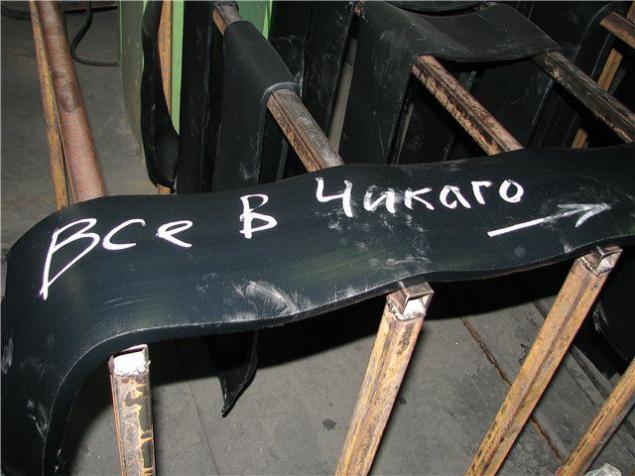
... And orders
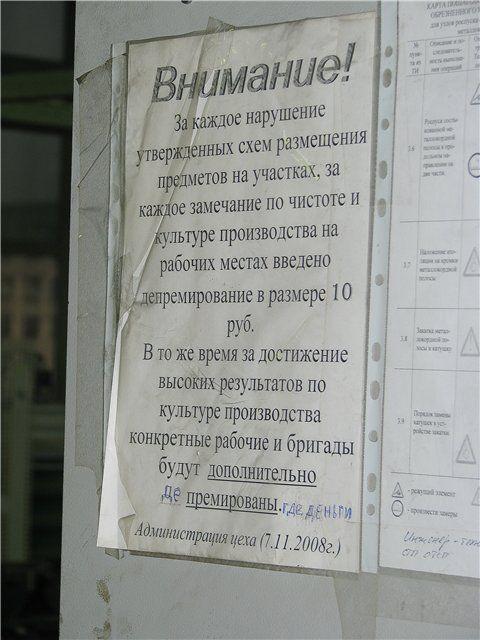
Final assembly of the tire takes place on a special machine concern Krupp. On this machine run only two: perezaryadchik and garbage. Perezaryadchik coil inserts into the machine components. Collector ring and put borotovoe on the machine does everything himself: he brings with germosloem Caracas and the side of the workpiece and blows air under the protector with the breaker.
The resulting crude bus runs on automatic checkweighing scales and visual inspection for possible defects.
Thereafter the workpiece are sent to the curing department
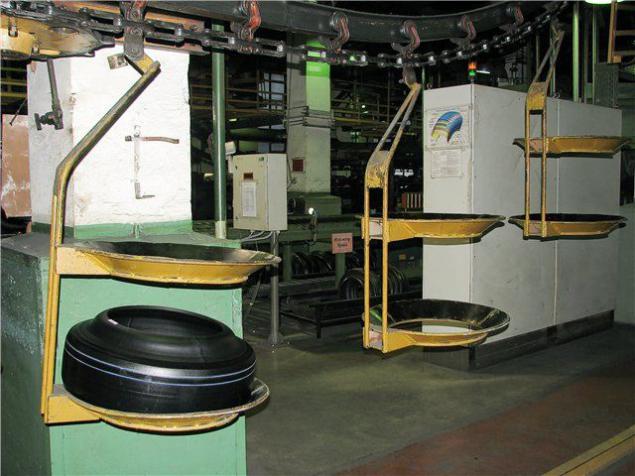
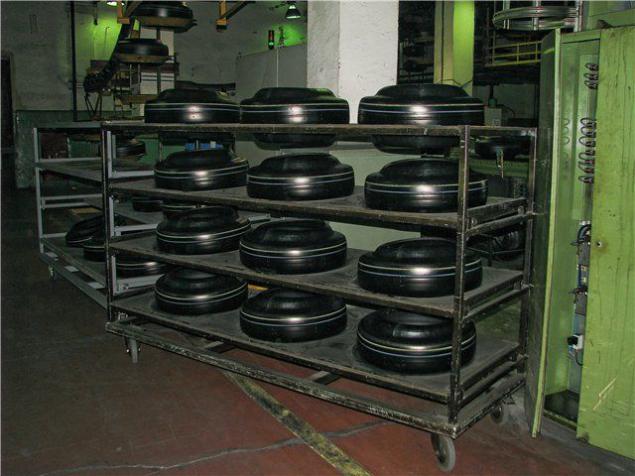
The last stage of the production takes place in the hot shop vulcanization. Here, the tire is subjected to hot-heat steam under high pressure. Rubber, carbon black and additives "sintered" together, and on the external and internal surface of the tire with the help of molds applied tread pattern, labels and other technical profiles.
The entire curing process is accompanied by steam and hissing sounds
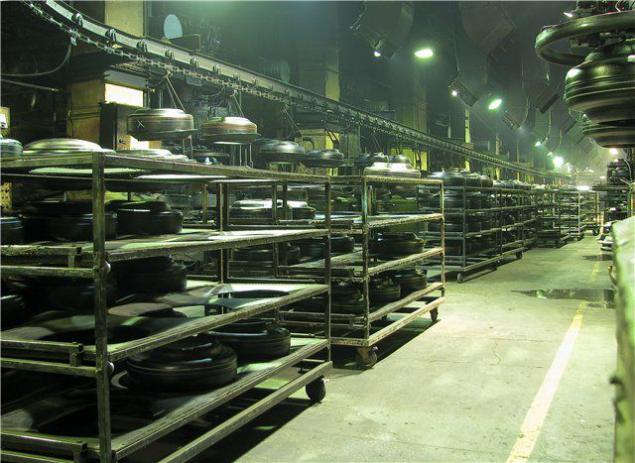
By acting black "needles" can be seen that the data samples of the mold used for making winter tires
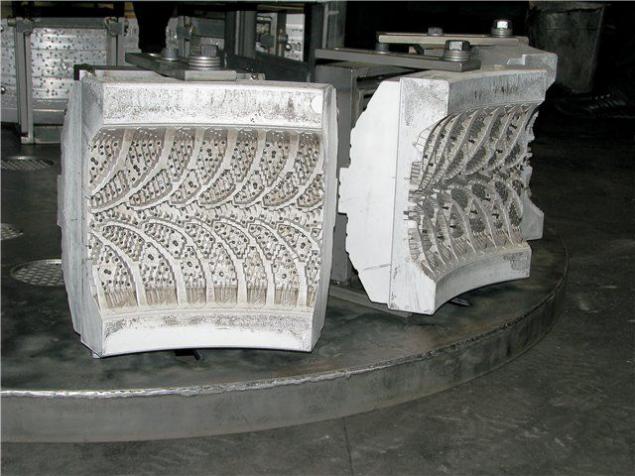
We called vulcanization workshop "chip" of the plant, and even asked to take us here at the end of the show for the second time. Apart from the fact that the process of "birth" of the tire causes interest of the audience, here you can still make wonderful pictures
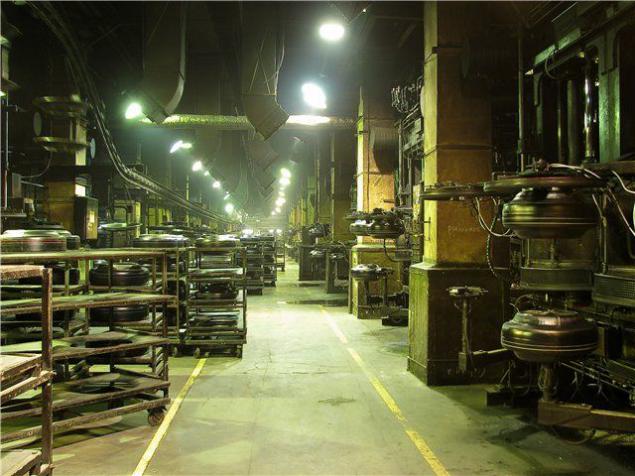
Work process goes. Very soon these blanks will be familiar to us kind of tires
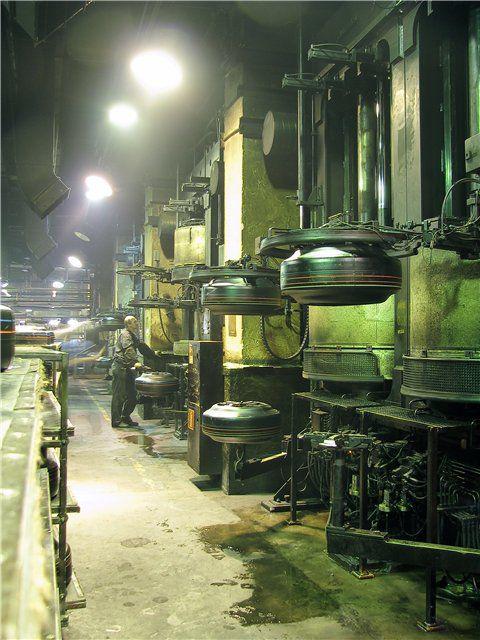
Despite the prevailing hot weather here, the shop vulcanization not want to leave. Light, the smell of hot rubber and the steam makes this place special
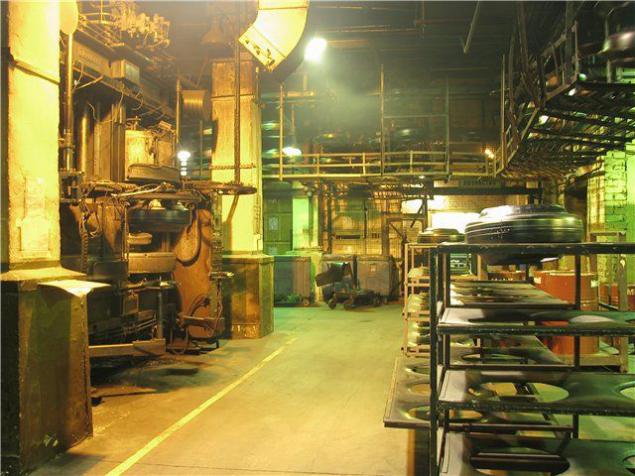
Just "born" tire. More steam. Right now coming next blank. Can be seen from the top of the mold to bring to the tire tread pattern and inscriptions
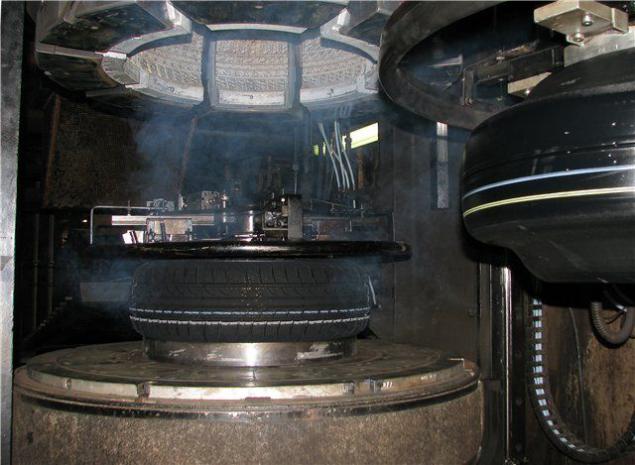
When the tire is ready, it takes place following harvesting. After 10 minutes, it will provide a bus, we can see every day
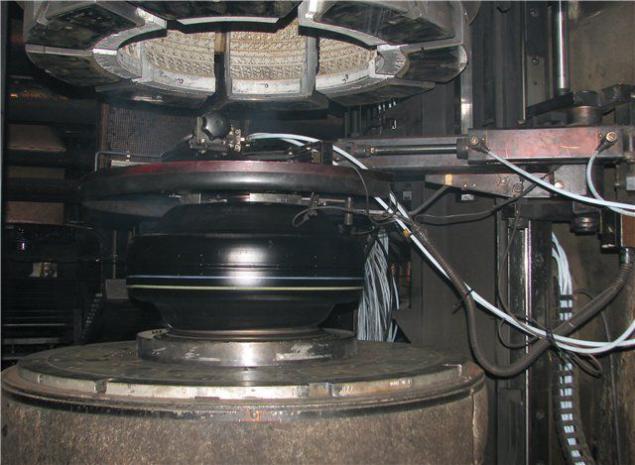
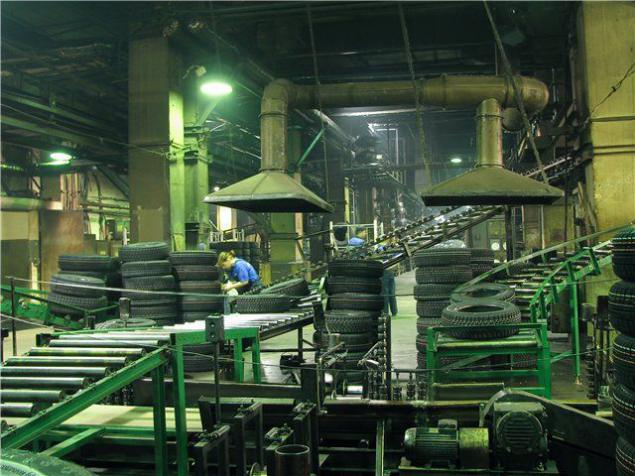
Products are ready, tested and delivered to the consumer waits for tests
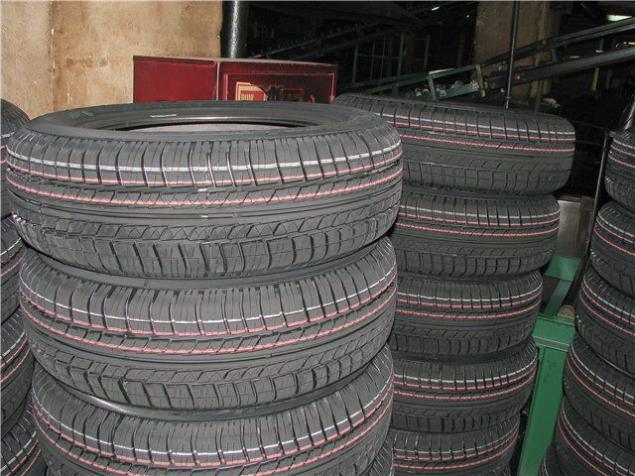
After the end of the production process occurs test. We have shown this process by the example of aviation tires. In the center of the wheel spins up, simulating the speed of 340 km / h. After dialing the required number of revolutions of the wheel in contact with the bus for a while. There is a friction tire on the wheel - thus simulates the landing of the aircraft. Once the tire is cooled and the cycle is repeated a number of times
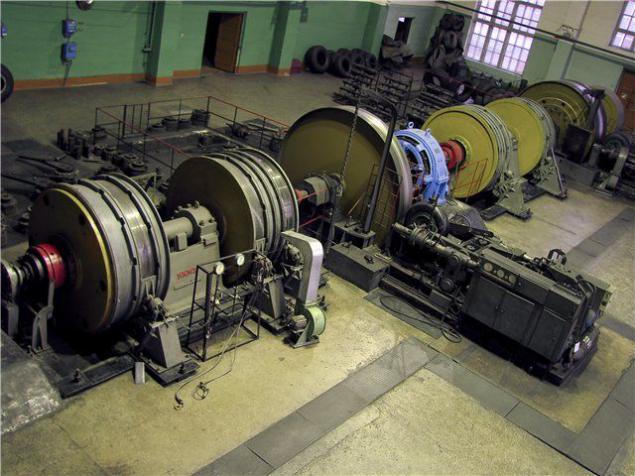
Source